振动切削
超声椭圆振动切削

超声椭圆振动切削
1.工作原理
超声振动切削从微观上看是一种脉冲切削。
在一个振动周期中,的有效切削时间很短,大于80%时间的里与工件、切屑完全分离。
与工件、切屑断续接触,这就使得所受到的摩擦变小,所产生的热量大大减少,切削力显著下降,避免了普通切削时的“让刀”现象,并且不产生积屑瘤。
利用这种振动切削,在普通机床上就可以进行精密加工,圆度、圆柱度、平面度、平行度、直线度等形位公差主要取决于机床主轴及导轨精度,最高可达到接近零误差,使以车代磨、以钻代铰、以铣代磨成为可能。
与高速硬切削相比,不需要高的机床刚性,并且不破坏工件表面金相组织。
在曲线轮廓零件的精加工中,可以借助数控车床、加工中心等进行仿形加工,可以节约高昂的数控磨床购置费用。
2.性能指标
2.1切削力小,约为普通切削力的1/3-1/10。
2.2加工精度高,主要取决于所用机床精度,所加工工件形位公差几乎可接近机床相关精度。
2.3切削温度低,工件保持室温状态。
2.4不产生积屑瘤,工件变形小,没有毛刺。
2.5切削表面粗糙度低,可接近理论粗糙度值,最高可达Ra0.2以下。
2.6被加工零件的“刚性化”,即与普通切削相比,相当于工件刚性提高。
2.7加工过程稳定,能有效消除颤振。
2.8切削液的冷却、润滑作用提高。
2.9耐用度呈几倍到几十倍提高。
2.10被加工表面呈压应力状态,零件疲劳强度、耐磨性、耐腐蚀性提高。
2.11切削后的工件表面呈彩虹效果。
振动切削加工技术

振动切削加工技术姓名:宋大同班级:机械工程1105班学号:113085201149摘要:振动切削加工技术是机械振动有利一面的应用,这是一种优于普通切削的新技术,是先进制造方法的重要组成部分。
本文通过振动切削与普通切削的对比,分析了振动切削的原理、特点、工艺效果及在切削过程中的作用。
同时论述了振动切削加工技术在工业中的具体应用和仍需解决的问题。
关键词:振动切削低频振动超声振动工艺效果应用机械振动同许多事物一样具有两面性,有其不利的一面,也有其有利的一面。
振动切削加工技术就是机械振动有利一面的应用。
振动切削加工是20 世纪60 年代发展起来的一种先进制造技术,它通过在常规的切削刀具上施加高频振动,使刀具和工件发生间断性的接触,从而使传统切削模式发生了根本性的变化。
振动切削改变了工件与刀具之间的时间与空间的分配,从而改变了切削加工机理,达到了减小切削力和切削热,并且提高加工质量和效率的目的。
由于其在一定范围内能够有效地解决难切削材料的加工及其精密切削加工方面的问题,因而越来越引起人们的重视。
1.普通切削与振动切削在普通切削中,切削是靠刀具与工件的相对运动来完成的。
切屑与已加工表面的形成过程,本质上是工件材料受到刀具的挤压,产生弹性变形和塑性变形,使切屑与母体分离的过程。
在这种刀具始终不离开切削的普通切削中,刀具的作用包括两个方面:一个是刀刃的作用,一个是形成刀刃的刀面的作用。
由于刀刃与被切削物接触处局部压力很大,从而使被切物分离。
刀面则在切削的同时撑挤被切物,促进这种分离。
普通切削中,伴随着切屑的形成,由于切屑与刀具之间的挤压和摩擦作用,将不可避免产生较大的切削力,较高的切削温度,使刀具磨损和产生切削振动等有害现象。
基于这种思想,产生了一种新的切削方法——振动切削。
振动切削即通过在切削刀具上施加某种有规律的可控的振动,使切削速度、切削深度产生周期性的改变,从而得到特殊的切削效果的方法。
振动切削改变了工具和被加工材料之间的空间与时间存在条件,从而改变了加工机理,达到减小切削力、切削热,提高加工质量和效率的目的。
金属切削中的振动现象对刀具磨损的影响

金属切削中的振动现象对刀具磨损的影响切削加工是一种常见的金属加工方法,其通过通过刀具对工件进行削除材料的过程。
然而,在金属切削中,振动现象常常会对刀具产生负面影响,导致刀具的磨损加剧。
本文将讨论振动现象对刀具磨损的影响,并探讨可能的解决方案。
首先,振动现象在金属切削过程中可能引起刀具的不均匀磨损。
振动会导致刀具与工件之间的相对运动受到干扰,使得刀具无法均匀地接触工件表面。
当刀具在振动状态下工作时,刀具的切削力和切削温度会发生变化。
这种不均匀的切削力分布将导致刀具表面的磨损不均匀,使刀具的寿命大大缩短。
其次,振动还可能引起刀具的疲劳破裂。
由于振动会导致刀具产生应力集中,这些应力集中区域容易形成裂纹。
随着切削过程的持续,裂纹将逐渐扩展并最终导致刀具的疲劳破裂。
疲劳破裂会导致刀具的可用寿命大大降低,并且对于高强度材料的切削加工来说尤其严重。
另外,振动还会对切削表面质量产生负面影响。
振动导致切削力的不稳定变化,这将导致切削表面产生不规则的纹理和凹凸不平的表面。
对于需要高精度加工的工件来说,这种表面质量的损坏是无法容忍的。
那么,如何减轻振动现象对刀具磨损的影响呢?首先,优化切削条件是减轻振动现象的关键。
合适的切削速度、进给量和切削深度能够减少切削力的变化,从而降低振动的程度。
此外,选择合适的刀具材料和几何形状也能够减轻振动现象对刀具磨损的影响。
采用具有抗振动能力的刀具材料,如硬质合金,以及刀具几何形状设计上的优化,可以显著降低刀具的磨损。
其次,刀具的装夹和刀具路径的设计也是减轻振动现象的重要因素。
正确的刀具装夹能够减少刀具的振动,并提高切削稳定性。
同时,针对工件和刀具的几何形状特点,设计合理的切削路径也能够减轻振动现象的产生。
采用合理的路径能够平衡切削力,降低振动的风险。
最后,使用先进的切削工具和技术也是减轻振动现象的有效手段。
近年来,先进的切削工具如超硬刀具和复合刀具的发展为减轻振动带来了新的解决方案。
切削振动产生原因和解决

细长杆立铣刀铣削深型腔时 常采用插铣方法
插铣就是刀具象钻头一样轴向 进刀,当铣削深的型腔时,通 常长杆的悬伸大于3倍的刀杆 直径,我们推荐使用轴向进刀 的插铣方法,但是立铣刀刀片 刃口有一定的径向切削刃,刀 具供应商有技术资料证明此刀 具在插铣时的最大吃刀宽度 PlungeMill是专门用于模具和 航空工业的大直径插铣刀,它 最大的特点是高效率和超大切 宽,通常用于大型深腔模具的 开粗。
切削振动的原因
刀具在切削工件时发生振动需要有下面三 个条件同时存在: 第一是包括刀具在内的工艺系统刚性不足 导致其固有频率低, 第二是切削产生了一个足够大的外激力, 第三是这个外激力的频率与工艺系统的固 有频率相同随即产生共振
分清自激振动和强迫振动
。
刀具振动实际应该叫“切削振动,通常发生在长悬臂刀杆的镗削和铣削,薄 壁件的切削加工,细长杆的车削等等。当环保做为车间考核的标准时,高速 钻削产生的高频啸叫也和振动噪音一起列为技术公害。 切削振动顾名思义只有在刀具进行切削时才产生,如果振动来自非切削因素 如不稳定的机床地基,机床丝杠的间隙,主轴轴承的损坏甚至几百米以外火 车的经过而产生的震动我们叫做强迫振动,这种振动不伴随噪音而非我们讨 论的话题。 切削振动产生噪音,但噪音并不是全由切削振动引起发生,机夹刀片铣刀在 100米以上的切削速度每齿走刀在0.1毫米以上铣削3毫米的切深,即便是铣削 灰口铸铁也会产生接近90分贝的噪音,而低频切削振动噪音常低于此值。 切削振动是自激振动是一种正弦波振动,除了用专业仪器测量振频与波长外 ,最明显的是工件被加工表面有振纹。
薄壁工件的铣削加工
薄壁工件铣削发生振动的原因完全来自于工件,这种工件被叫做箱式或者 碗式零件(box like or bowl like shape workpiece),由于振动来自于工件本身 ,那么技术人员各显神通,国外在处理这类零件的铣削加工主要以改善工 件夹持为主,例如增加合适的辅助支撑点,在夹具和机床工作台面之间加 装一层木板,用粗大的橡皮条或者弹簧勒在壳体的外面,在箱体内部充满 湿沙子等等,奇思妙想不一而足。在铣削薄腹板时,推荐使用90度面铣刀 以减小对腹板的轴向切削力。
切削振动的三个分类
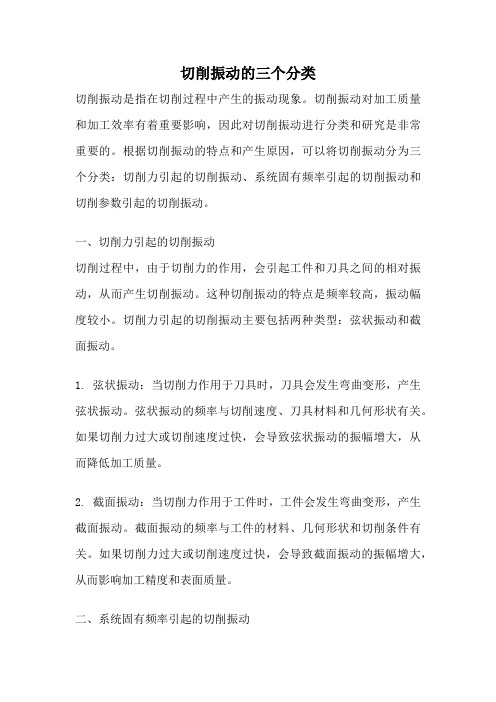
切削振动的三个分类切削振动是指在切削过程中产生的振动现象。
切削振动对加工质量和加工效率有着重要影响,因此对切削振动进行分类和研究是非常重要的。
根据切削振动的特点和产生原因,可以将切削振动分为三个分类:切削力引起的切削振动、系统固有频率引起的切削振动和切削参数引起的切削振动。
一、切削力引起的切削振动切削过程中,由于切削力的作用,会引起工件和刀具之间的相对振动,从而产生切削振动。
这种切削振动的特点是频率较高,振动幅度较小。
切削力引起的切削振动主要包括两种类型:弦状振动和截面振动。
1. 弦状振动:当切削力作用于刀具时,刀具会发生弯曲变形,产生弦状振动。
弦状振动的频率与切削速度、刀具材料和几何形状有关。
如果切削力过大或切削速度过快,会导致弦状振动的振幅增大,从而降低加工质量。
2. 截面振动:当切削力作用于工件时,工件会发生弯曲变形,产生截面振动。
截面振动的频率与工件的材料、几何形状和切削条件有关。
如果切削力过大或切削速度过快,会导致截面振动的振幅增大,从而影响加工精度和表面质量。
二、系统固有频率引起的切削振动系统固有频率是指切削系统在没有外界刺激下自然振动的频率。
当切削系统的激励频率与系统固有频率接近或相等时,就会引起共振现象,从而产生较大的切削振动。
系统固有频率引起的切削振动主要包括两种类型:共振振动和强迫振动。
1. 共振振动:当切削系统的激励频率与系统固有频率接近或相等时,就会引起共振振动。
共振振动的特点是振幅较大,对加工质量和加工效率有着较大影响。
为了避免共振振动的发生,需要合理选择切削参数,并采取减振措施,如增加刚度或增加阻尼。
2. 强迫振动:当切削系统的激励频率与系统固有频率不完全匹配时,就会引起强迫振动。
强迫振动的特点是振幅较小,但会对加工表面质量产生一定影响。
为了减小强迫振动的影响,需要合理选择切削参数,并采取减振措施,如增加刚度或增加阻尼。
三、切削参数引起的切削振动切削参数是指切削过程中与切削力和振动有关的参数,包括切削速度、进给量和切削深度等。
振动刀工作原理

振动刀工作原理
振动刀是一种常用于木工、金属加工等行业的工具,其工作原理是利用高速振动来实现切削或切割材料的目的。
振动刀通常由电机、振动装置和刀具组成,通过电机驱动振动装置产生高频振动,从而使刀具在工件表面产生切削作用。
振动刀的工作原理可以简单分为以下几个步骤:
1. 电机驱动振动装置:振动刀的核心部件是振动装置,它通常由电机和振动机构组成。
电机通过传动装置驱动振动机构产生高频振动,将振动传递给刀具。
2. 刀具与工件接触:在振动刀工作时,刀具被安装在振动机构上,与待加工的工件表面接触。
振动刀的高频振动使刀具在工件表面产生快速的来回运动,从而实现切削或切割作用。
3. 切削材料:当刀具在工件表面振动时,切削刃与工件接触,通过振动的作用力将工件材料分离或切割。
由于振动刀的高频振动,切削作用更为精细、快速,能够实现高效加工。
4. 调节振动频率和幅度:振动刀的工作效果与振动频率和振动幅度密切相关。
通过调节电机的转速和振动机构的设计,可以实现不同频率和幅度的振动,以适应不同材料和加工要求。
振动刀的工作原理简单而有效,能够实现高效、精确的加工效果。
在木工、金属加工等行业广泛应用,成为生产制造中重要的工具之一。
振动刀的发展也在不断完善和创新,以适应不同材料和加工需求,提高加工效率和质量。
总的来说,振动刀的工作原理是利用高频振动实现切削或切割材料的目的,通过电机驱动振动机构产生振动,刀具与工件接触产生切削作用,实现高效加工。
振动刀在工业生产中发挥着重要作用,不断推动生产制造技术的进步和发展。
切削振动的产生及解决

使用锋利的刀片来降低切削力
非涂层刀片通常比涂层刀片 要锋利 即便是涂层刀片,物理涂层 (PVD))也比化学涂层( CVD或MTCVD)刃口要锋利 判断刃口的锋利度可以从它 在指甲盖上是否划出成形的 屑来判断
刃口的钝化半径通 常在35u到75u之间
切深一定时使用小的刀尖圆弧半径
比如刀片的刀尖角为0.8mm不变时 ,随着刀片切深的增加,细长的镗 刀或铣刀杆振动倾向在切深ap和刀 尖圆弧半径(r=0.8mm)相等时最 大,当切深ap大于刀尖半径r后, 刀杆的振动反而被抑制 图中的∆R代表镗杆的弹变,可以 看出当切深ap与等于刀尖圆弧半径 时弹变最大,而且随着切深增加弹 变不会再增加反而开始减小,因为 径向切削力FCN在ap=r时最大,ap 再增加只会增加轴向抗力,而轴向 抗力不是细长刀杆产生振动弹变的 原因,反过来还会使刀杆保持稳定 。
使用正前角和大后角的刀片 配以轻快的断屑槽。 配以轻快的断屑槽。 pos. neg..
这样的刀片在镗削或铣削中的切削楔入角最小,切 削当然轻快。在车削与镗削中,7度和11度后角是 最常见的刀片,刀片为螺钉夹持的最多,在20毫米 以下的孔镗削中,即便不存在振动问题大家也通常 选择11度后角的刀片,例如山特维克可乐满的 TPMT,DPMT,VCEX的刀片(V型刀片后角为7度或 11度)。后角以7或11度后角刀片为主要推荐,因 为它们是ISO标准刀片,不同厂家的刀片可以互换 车刀片适用于镗削加工,现代机夹车刀片按照粗精 加工分为不同的短屑槽槽型,比如像可乐满刀片槽 型PF,KM,MF,KR等,其中的第二位表示刀片适合的 加工,F表示Finishing为精加工,这是适合做减振 镗削的刀片,当然刀片应该配以刃口耐冲击的材质 才可以,比如PF-4025,PF-4035,WK-4025等等。
振动切削加工技术

• 振动切削的分类
按振动质量:自激振动切削和强迫振动切削
按刀具振动方向:吃刀抗力方向、进给抗力 方向、主切削方向 按所加频率:高频振动和低频振动
• 普通切削与振动切削的对比
-------普通切削中,切削靠刀具与工具的相对 运动来完成。产生较大切削力,使刀具磨损、 产生切削振动的有害现象。 --------振动切削中,在切削刀具上施加某种有 规律的可控的振动,使切削速度、切削深度 产生周期性的改变,从而使切削力减小、切 削热降低。
• 振动切削的特点
1、切削力大大减小 2、切削温度明显降低 3、切削液的作用得到了充分发挥 4、可提高刀具使用寿命 5、可控制切屑的形状和大小 6、提高加工精度和表面质量 7、可提高已加工表面的耐磨性和耐蚀性
• 振动切削技术的应用
1、难切削材料的加工。如:不锈钢、钛合金、 陶瓷、玻璃等采用超声振动切削来大大降低加 工难度;加工石墨与氧化铝等材料只有采用超 声振动才能产生微粒式的切削分离得到整齐的 加工表面
金刚石刀具可以切削含铁工件
振动切削加工技术
振动加工技术是从20世纪60年代发展起来的 一种优于普通切削的先进的制造技术。
• 它通过在常规的切削刀具上施加高 频振动,使刀具和工件发生间断性 的接触。改变了工件与刀具之间的 时间与空间分配,从而改变了切削 加工机理达到了减小切削力和切削 热并提高加工质量和效率的目的。
2、难加工零件的切削加工
如易弯曲变形的细长杆类零件、薄壁零件、排屑断屑比较困难的切削加工 如用于钻孔、饺孔、攻丝、拉削等
Thank you!
- 1、下载文档前请自行甄别文档内容的完整性,平台不提供额外的编辑、内容补充、找答案等附加服务。
- 2、"仅部分预览"的文档,不可在线预览部分如存在完整性等问题,可反馈申请退款(可完整预览的文档不适用该条件!)。
- 3、如文档侵犯您的权益,请联系客服反馈,我们会尽快为您处理(人工客服工作时间:9:00-18:30)。
汽车发动机的曲轴在工作时会发生 扭振现象,其内因是曲轴不仅自身 具有惯性,而且还有弹性,由此确 定了曲轴本身固有的自由扭转特性, 而其外因则是作用在曲轴上周期性 变化时的激振力矩,例如:大爆发 的活塞惯性力、曲柄连杆机构的惯 性力和重力、附件的不规则阻力矩 和外界作用力,这些力矩是曲轴产生扭振的能量来源,只 要机器运行,这些激振力矩就存在强迫扭振就持续发生, 使得轴在运转时产生剧烈振动。
角动,音律同矣”;成书于公元2~5世纪的《犹太法典》第二章
也描述一种共振象,“公鸡把头伸进空的玻璃容器内啼鸣致使容 器破碎”。
战国初期为了防御敌国的地道战术在《墨子.备学篇》记载 了一种防御方式 ,守军在城内沿城墙根约每隔6米挖一口井。 深约3米左右。让陶工烧制坛子,有耳朵灵敏的人日夜值班,
并将耳朵贴在坛口侦听。如果敌人正在挖地道,通过坛中的
●恶化飞机和车船的乘载条件,等等。
地震,群灾之 首。强烈的破坏性 地震瞬间将房屋、 桥梁、水坝等建筑 物摧毁,直接给人 类造成巨大的灾难, 还会诱发水灾、火 灾、海啸、有毒物 质及放射性物质泄 漏等次生灾害。
印度洋强震引发海啸席卷南亚东南亚
建造结构振动台模型试验
一种吸声型的声屏障结构
利用声屏障将声源 和保护目标隔开
曲轴的破坏
曲轴按照激振的频率进行强制振动,当激振
频率与曲轴本身的固有频率相同时,就会产生共
振。当扭振应力超过轴系所能承受的应力时,曲
轴将产生断裂。
防止曲轴破坏的解决办法
在设计新型的内燃机过程中,就应注意设计方案和设计参
数的选择,不要使所设计的内燃机工作在临界转速内,必要 时可以通过改变曲轴的刚度、各个转动系统的转动惯量等 设计参数,以及采用内磨擦较大的材料(如球墨铸铁)来制做
机械振动,是指物体 ( 系 ) 在平衡位置 (或平均位置)附近来回往复的运动。
●引起噪声污染; ●影响精密仪器设备的功能,降低机械加 工的精度和光洁度; ●消耗机械系统的能量,降低机器效率; ●使结构系统发生大变形而破坏,甚至造 成灾难性的事故,有些桥梁等建筑物就是 由于振动而塌毁; ●机翼的颤振、机轮的摆振和航空发动机 的异常振动,曾多次造成飞行事故;
利、土木、建筑、建材、铁路、公路交通、轻工、食品和谷物加
工、农田耕作以及在人类日常生活过程中。
振动切削
振动切削加工是在刀具或工件上附加一定可控的振动,使加
工过程变为间断、瞬间、往复的微观断续切削过程。振动切削
方法首先由日本宇都宫大学的隈部淳一郎教授于60年代提出的。 目前,在日本、中国、俄罗斯、德国、韩国、印度、美国、奥 地利、英国等开展了广泛的研究与生产应用。
曲轴,从而改变整个轴系的自振频率,避免内燃机在工作转
速范围内产生共振。当采取一定的措施后还不能解决问题, 最常用的办法就是在曲轴自由端安装减振器。
振动的利用
“振动利用工程学” 是20世纪后半期逐渐形成和发展起来的 一门新学科,振动利用工程的发展使世人瞩目。就振动机械来说, 目前已成功应用于工矿企业中的振动机器已发展到数百种之多, 在许多部门,如采矿、冶金、煤炭、石油化工、机械、电力、水
振动切削原理
振动切削理论是在切削过程中加入了超声振动。由工业金刚石颗粒 制成的铣刀、钻头或砂轮,在加工过程中对零件表面进行20000次/秒的 连续敲击,即使是高硬材料,在如此高频的振动敲击下,一个很小的切削 力也可将其瓦解。振动切削机床的进给力还是很大的,因此在振幅的最高 点,附在刀具上的金刚石颗粒以撞击方式将零件表面材料以微小颗粒形式 分离出来。
①生产率高,特别对于难加工材料,
生产率比普通钻削高2~3倍; ②不需退刀排屑,易实现机械化; ③加工精度和表面质量的很大提高, 表面粗糙度值可达Ra0.8μm,而且不
出现毛刺;
④可降低切削温度。
超声诊断仪产生超声,并发射到人体内,在 组织中传播,遇到正常与有疾病的组织时,便会 产生反射与散射,仪器接到这种信号后,加以处 理,显示为波形、曲线或图像等,就可以供医生 做判断组织或器官健康与否的依据。
车载火炮稳定系统
振动引起的转子系统破坏
如果在加工时有强迫振动,又称为激励振动,它是由周期变 化的激振力所引起的,例如主轴回转不平衡、电机振动、传 动部件有缺陷,以及周围有振动源通过地基传给加工设备的 振动等,都会产生振纹。电机是主要动力源,也是振动源, 电机的振动对加工的影响很大。
声音就能觉察。这种方法不仅能判断敌人否在挖洞,还能从 不同的坛口的声音确定声源方向。即地道的大致方位。这个
方法很有振动学理论根据。因为敌人挖地道的声波经同地下
传到坛子,坛子内空气柱发生共鸣,再引起坛口蒙皮的振动, 因此声音就大了
在振动力学研究兴起之前,有两个典型的振动问题引起注 意,即弦线振动和单摆摆动。弦线振动是无穷多自由度连 续系统的振动,单摆摆动是单自由度离散系统的振动,振幅 不大时都可认为是线性的.单摆振动比较简单,对后来线性 振动的发展影响不大。 1678年Hooke提出弹性定律,建立了弹性体变形与恢复 力间的线性关系,引入了振动系统的基本组成部分——弹 簧,1678年,Newton在其划时代的《自然哲学之数学 原理》中建立了运动变化与受力间的关系,使振动问题的 动力学研究成为可能,他也定义了振动系统的另一基本组 成部分——质量,假设了介质阻力与速度及速度平方成正 比,形成阻尼概念的雏形。
机械振动的发展历史
振动带来的危害及其控制
振动的利用
振动是在日常生活和工程实际
中普遍存在的一种现象,也是整 个力学中最重要的研究领域之一。
人类对振动现象的认识有悠久的历史,早在公元前6世
纪,Pythagoras发现了较短的弦发出较高的音,将弦长缩短一半 可发出高一音阶的音符,战国时期的古人已定量地总结出弦线 发音与长度的关系,将基音弦长分为三等份,减去或增加一份可 确定相隔五度音程的各个音,公元前6世纪成书的《旧约・约 书亚记》记载共振现象,城墙在齐声呐喊中塌陷;成书于战国时 期的《庄子・徐无鬼》更明确记载了共振现象“鼓宫宫动,鼓角
限制有害的振动,利用有益的振动
谢谢观看Βιβλιοθήκη 因振动切削机理与普通切削不同,使其具有如下现象 及效果。
1)切削抗力显著降低。
2)加工精度明显提高。
3)切削温度显著降低。
4)切削过程比较顺利。 5)加工表面质量可以得到改善
采用刀具振动孔加工
超声纵振孔加工又可分为刀具振动和工件振动两类。虽然振动体不同,
但它们刀具与工件的相对振动都是轴向的,因此加工效果基本一致。超声 纵振孔加工的主要特点有:
高架桥上的吸声 与隔振组合屏障
高架桥上的吸声屏障
在坦克炮塔内,陀螺仪、加速度计及角度 传感器不断地测定各种运动载荷,车载计算机 根据这些信息计算并发出抵消这些运动的控制 指令,通过伺服系统使炮塔相对于底盘水平转 动、火炮相对于炮塔高低俯仰,从而使坦克即 使在不断颠簸的运动中也能将火炮准确地对准 目标。