振动辅助切削加工技术研究现状
低频、超低频振动计量技术的研究与展望
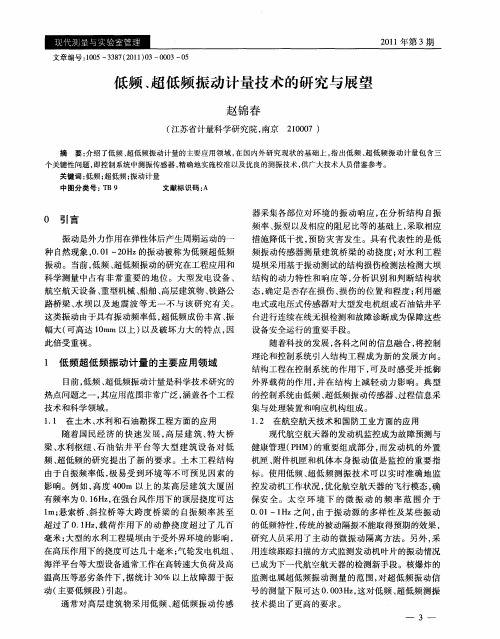
随着国民经济的快速发 展 , 高层 建筑 、 特大 桥 梁、 水利枢纽 、 油钻井平 台等大型建筑设 备对低 石
频、 超低 频 的研 究 提 出 了 新 的要 求 。土 木 工程 结 构 由于 自振频 率低 , 易 受 到 环 境 等 不 可 预 见 因素 的 极 影 响 。例 如 , 度 40 以上 的某 高 层 建 筑 大 厦 固 高 0m 有频 率 为 0 1H , 强 台风 作用 下 的顶 层挠 度 可达 .6 z在
结 构工 程在 控 制系 统 的 作 用下 , 可及 时感 受 并 抵 御 外 界载 荷 的作 用 , 在结 构 上减 轻 动 力 影 响 。典 型 并
幅大 ( 可高达 1r 0 m以上 ) a 以及破坏力大 的特点 , 因
此 倍 受重 视 。
1 低频 超低 频振动计量 的主要应用领域
航空航天设备 、 重型机械 、 船舶 、 高层建筑物 、 铁路公 路 桥 梁 、 坝 以 及 地 震 波 等无 一 不 与 该 研 究 有 关 。 水
这 类 振动 由于具有 振 动频率 低 , 超低 频成 份 丰富 、 振
态, 确定是否存在损伤、 损伤的位置和程度 ; 利用磁 电式或电压式传感器对大型发 电机组或石油钻井平 台进行连续在线无损检测和故障诊断成为保障这些 设 备安 全运 行 的重要 手 段 。 随着科技的发展 , 各科之问的信息融合 , 将控制 理论和控制系统引入结构工程成为新 的发展方向。
加速 度 两个研 究方 向 已成 为振 动计量 急待 研究解 决
的新 课题 。
带之间, 蒙受地震灾害比较深重 , 据统计 2 世纪因破 0 坏性地震, 在我国造成死亡人数约 6 0万, 使人民生命 财产遭受 了惨 痛 的损失 。西 气东 输 、 南水 北 调 、 峡 三
轴向超声振动辅助磨削的磨削力建模_唐进元

Modeling on Grinding Force Assisted with Axial Ultrasonic Vibration
TANG Jinyuan ZHOU Weihua HUANG Yulin
(State Key Laboratory of High Performance Complex Manufacturing, Central South University, Changsha 410083)
1
轴向超声振动下单颗磨粒的运动 特性分析
图 1 为轴向超声振动辅助磨削的运动模型图,
从图 1 可以看出,砂轮上的单颗磨粒的运动由绕砂 轮轴线做等速圆周运动、相对于工件做等速平移运 动以及沿砂轮轴向的高频振动合成。
图1
轴向超声振动辅助磨削运动模型
图 2 为轴向超声振动下,单颗磨粒的运动轨 迹图。
图2
轴向超声振动下单颗磨粒的运动轨迹图
摘要:以单颗磨粒为对象,分析轴向超声振动下磨粒的运动特性。在此基础上,将磨削力分为切屑变形力和摩擦力两部分, 分别分析了轴向超声振动对切屑变形力和摩擦力的影响。在切屑变形力方面,轴向超声振动改变了磨粒运动方向与主切削方 向间的夹角;在摩擦力方面,轴向超声振动降低了磨粒与工件间的摩擦因数。基于此建立了轴向超声振动辅助磨削的磨削力 模型。 通过对 21NiCrMo5H 进行了轴向超声振动辅助磨削的磨削力试验, 确定了模型中的常数, 并验证了所建模型的正确性。 建立的磨削力模型是轴向超声振动辅助磨削的磨削力预测的一种有效方法, 对轴向超声振动辅助磨削机理的认识具有较大意 义。 关键词:轴向超声振动;磨削力建模;切屑变形力;摩擦力;磨削力预测 中图分类号:TG58
在轴向超声振动中超声振动作用下的摩擦力与没添加超声振动下的摩擦力之比为19将式16和17代入12中并乘以磨削接触区2023磨削力模型根据以上的分析可以得出轴向超声振动辅助磨削的磨削力模型如式21所示sincoscoscoscossin21由于超声振动的添加使得磨削力随时间呈现周期性的变化因此一个周期内的平均磨削力可以表示为ncncacaccb则超声振动辅助磨削加工的磨削力模型第52卷第15期期188fafa为常数通过试验数据确定
机械振动-精密深孔镗削中镗杆振动问题

北方工业大学科目机械振动-精密深孔镗削中镗杆振动问题学院机电工程学院专业班级机研-12学生姓名指导教师撰写日期:2012年12月12日摘要在机械制造业中,一般规定孔深L 与孔径d 之比大于5,即L/d>5 的孔称为深孔。
深孔加工是处于封闭或半封闭状态下进行的,不能直接观察到刀具的切削情况;且受孔径尺寸限制,刀具直径小,悬伸长,刚性差;切屑不易排出,切削热不易传散,因此深孔加工一直是金属切削领域内公认的技术难题。
而对于两端孔径小,中间孔径大的瓶腔深孔加工则难度更大,除了存在上述一般深孔加工的问题外,还要求实现镗刀块的伸出、夹紧、松开、缩回等动作,且受入口直径的限制,镗杆的刚性问题及振动问题变得更加尖锐。
因此精密小深孔加工技术的研究在理论和实践上都具有重要意义。
经过深孔镗削过程中的自激振动分析、深孔镗杆进行了静力学和动力学理论分析、对深孔镗杆进行ANSYS分析、深孔镗杆的模态分析,有一些减小振动的方法可以利用,如合理选择刀具几何形状、提高工艺系统的抗振性、采用减振装置、合理调整振型的刚度比、超声波方法、镗杆结构优化、智能镗杆颤振监测实验系统、镗削振动主动控制、设计辅助结构等方法等等。
关键词:深孔;镗削;减振目录目录 (3)1机械振动概况 (4)1.1机械振动对机械加工的影响 (4)1.2深孔加工的振动问题 (4)2精密振动切削工艺中的振动问题 (4)2.1项目简介 (4)2.1.1项目中的振动 (4)2.1.2项目镗削工序的振动分析 (4)3深孔镗削过程中的振动分析 (6)3.1深孔镗削过程中的自激振动 (6)3.2深孔镗杆进行了静力学和动力学理论分析 (7)3.3对深孔镗杆进行ANSYS分析 (9)3.4深孔镗杆的模态分析 (10)4减小深孔镗削中振动的方法 (11)4.1概述 (11)4.2超声波方法 (11)4.3镗杆结构优化 (13)4.4智能镗杆颤振监测实验系统 (13)4.5镗削振动主动控制 (14)4.6深孔镗削加减振措施后效果 (15)5.总结 (15)参考文献 (16)1机械振动概况1.1机械振动对机械加工的影响在机械加工过程中,工艺系统的振动会破坏刀具与工件之间正常的运动轨迹,给机械加工带来较大的危害,具体表现在以下几个方面:①影响加工表面质量,频率低时产生波纹,频率高时产生微观不平度;②降低生产效率,加工中的振动制约了切削用量的提高,严重时甚至使切削不能正常进行;③缩短刀具、机床等的使用寿命;④振动产生的噪声污染了环境。
激光加热辅助切削加工技术研究进展

激光加热辅助切削加工技术研究进展张迎信;安立宝【摘要】This paper reviews the recent research progress on laser assisted machining technology. On the experimental research aspect, the technical characteristics of various processes including laser assisted turning, milling, drilling, and grinding have been summarized, and the effects of laser and cutting parameters on machining quality have been stated. Investigations show that properly increasing laser power and decreasing cutting speed and feed rate within limits is propitious to fully soften the workpiece material in the cutting zone, and therefore improves the machinability of the workpiece material and enhances the machining efficiency and quality. Current simulation research on laser assisted machining is mainly focused on the cutting temperature field and machining process. By establishing the model of temperature field, the best temperature range for removing workpiece material can be predicted and the cutting parameters can be optimized. Cutting process simulation discusses the influence of physical quantities in machining such as stress, strain, and temperature, providing a basis for controlling the quality of the machined surface in real operations. In the future, the study on machining mechanism, processing techniques and simulation for optimization should be strengthened, and the data base for laser assisted machining processes should be found, in order to promote the industrial application of the technology.%综述近年来激光加热辅助切削加工技术的研究进展.在实验研究方面,总结了激光加热辅助车削、铣削、钻削、磨削等不同工艺过程的加工特点,阐述了激光参数和切削参数对加工质量的影响.研究表明:在一定范围内,适当提高激光功率、降低切削速率、减小进给量有利于切削区材料的充分软化,可改善工件材料的切削加工性,提高加工效率和加工质量.目前,激光加热辅助切削加工仿真研究主要集中在切削温度场与切削过程仿真.通过建立温度场模型,可预测材料去除最优温度范围,优化加工工艺参数.切削过程仿真探讨应力、应变、温度等物理量的影响,为实际加工中控制零件表面质量提供了依据.后续工作应进一步加强在加工机理、加工工艺、仿真优化等方面的研究,建立完善的激光加热辅助切削加工数据库,以促进该技术的工业应用.【期刊名称】《航空材料学报》【年(卷),期】2018(038)002【总页数】9页(P77-85)【关键词】激光加热辅助切削;加工;实验;仿真;参数;温度场;研究【作者】张迎信;安立宝【作者单位】华北理工大学机械工程学院,河北唐山 063210;华北理工大学机械工程学院,河北唐山 063210【正文语种】中文【中图分类】TG665近年来,工程陶瓷、复合材料、高温合金、钛合金等先进工程材料因其具有强度高、耐磨损、抗腐蚀、热稳定性好等优良特性,在机械、化工、航空航天、核工业等领域获得了广泛应用[1-3]。
刀具设计减震原理及应用

刀具设计减震原理及应用刀具设计中的减震原理及应用涉及到刀具的结构、材料选择和使用环境等方面。
有效的减震设计可以减轻刀具振动对切削质量、刀具寿命和机床精度的不利影响,提高切削效率和加工质量。
下面将从刀具结构设计、材料选择和减震应用方面进行详细阐述。
刀具结构设计是减震设计的基础。
优秀的刀具结构设计可以减少切削振动,降低切削力和切削温度,提高切削稳定性和加工精度。
常见的刀具结构设计包括刀柄结构、刀片结构和切削辅助装置。
刀柄结构是刀具振动传递的关键部位之一。
在刀柄设计中,常采用独立刀柄和整体刀柄两种结构形式。
独立刀柄结构可以通过调整刀柄材料和形状来改变刀具的振动特性,减少刀具振动。
整体刀柄结构则可以提高刀具的刚度和稳定性,减弱切削振动。
此外,刀柄还可以采用中空结构,通过填充流体或填充刚性材料来减小切削振动。
刀片结构是刀具减震设计的另一个关键点。
刀片结构的合理设计可以降低切削振动和切削力,提高切削效率和切削质量。
常见的刀片结构设计包括面刀片、侧刀片和刀片吊形式。
面刀片结构适用于切削力较大的情况,它具有较大的刀片刚度和稳定性,可以减小切削振动。
侧刀片结构适用于切削力较小的情况,它具有较小的刀片刚度和稳定性,可以减轻切削振动。
刀片吊形式是通过刀片系统的吊装设计来实现减震效果,通过刀片的柔性悬挂减小切削振动。
切削辅助装置是减震设计的重要手段之一。
切削辅助装置可以采用振动切削刀具、自激振动切削刀具、振动刀具切削等方式来减小切削振动和提高加工精度。
振动切削刀具是通过引入激振器来实现刀具振动的方式,通过调节激振频率和振幅来减小切削振动。
自激振动切削刀具是通过刀片系统自身的刚度和阻尼来实现振动切削,通过调节刀片系统的阻尼比和频率来减小切削振动。
振动刀具切削是通过刀具振动产生波纹切削的方式来减小切削振动。
刀具材料的选择也是减震设计的重要因素之一。
材料的刚度和阻尼是减震设计的关键要素。
刚度高的材料可以提高刀具的刚度和稳定性,减小切削振动;阻尼大的材料可以吸收和消散切削振动的能量,减小切削振动。
振动压路机与振动压实的前沿技术
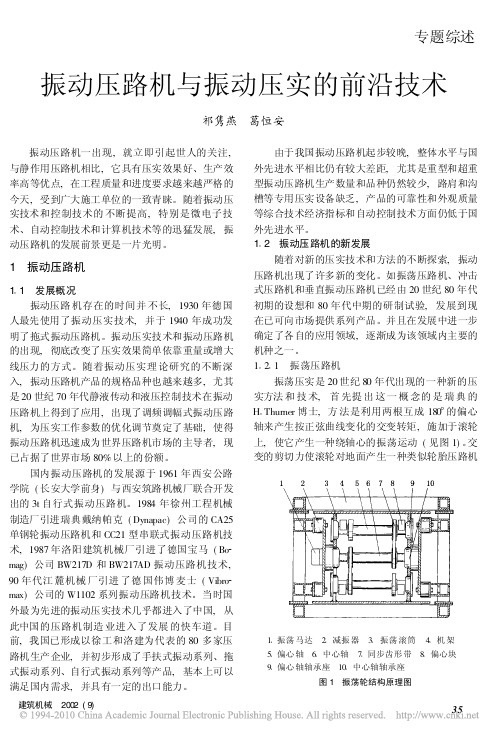
振动压路机与振动压实的前沿技术祁隽燕 葛恒安振动压路机一出现,就立即引起世人的关注,与静作用压路机相比,它具有压实效果好、生产效率高等优点,在工程质量和进度要求越来越严格的今天,受到广大施工单位的一致青睐。
随着振动压实技术和控制技术的不断提高,特别是微电子技术、自动控制技术和计算机技术等的迅猛发展,振动压路机的发展前景更是一片光明。
1 振动压路机1 1 发展概况振动压路机存在的时间并不长,1930年德国人最先使用了振动压实技术,并于1940年成功发明了拖式振动压路机。
振动压实技术和振动压路机的出现,彻底改变了压实效果简单依靠重量或增大线压力的方式。
随着振动压实理论研究的不断深入,振动压路机产品的规格品种也越来越多,尤其是20世纪70年代静液传动和液压控制技术在振动压路机上得到了应用,出现了调频调幅式振动压路机,为压实工作参数的优化调节奠定了基础,使得振动压路机迅速成为世界压路机市场的主导者,现已占据了世界市场80%以上的份额。
国内振动压路机的发展源于1961年西安公路学院(长安大学前身)与西安筑路机械厂联合开发出的3t自行式振动压路机。
1984年徐州工程机械制造厂引进瑞典戴纳帕克(Dynapac)公司的CA25单钢轮振动压路机和CC21型串联式振动压路机技术,1987年洛阳建筑机械厂引进了德国宝马(Bo mag)公司BW217D和BW217AD振动压路机技术, 90年代江麓机械厂引进了德国伟博麦士(Vibro max)公司的W1102系列振动压路机技术。
当时国外最为先进的振动压实技术几乎都进入了中国,从此中国的压路机制造业进入了发展的快车道。
目前,我国已形成以徐工和洛建为代表的80多家压路机生产企业,并初步形成了手扶式振动系列、拖式振动系列、自行式振动系列等产品,基本上可以满足国内需求,并具有一定的出口能力。
由于我国振动压路机起步较晚,整体水平与国外先进水平相比仍有较大差距,尤其是重型和超重型振动压路机生产数量和品种仍然较少,路肩和沟槽等专用压实设备缺乏,产品的可靠性和外观质量等综合技术经济指标和自动控制技术方面仍低于国外先进水平。
超声振动超精密车削Ti6Al4V的表面质量研究

超声振动超精密车削Ti6Al4V的表面质量研究李东炜;梁忠伟;孔早慧【期刊名称】《机床与液压》【年(卷),期】2024(52)2【摘要】为研究超声振动辅助超精密车削Ti6Al4V切削性能,使用Son-x公司的UTS one设备使单晶金刚石刀具在切削方向振动,使用350FG摩尔Nanotech 4轴机床进行加工,采用四因素三水平正交试验,试验因素为切削速度、切削深度、进给速度和刀具振幅,切削力、表面粗糙度为评价指标。
采用Zygo的Nexview 8050三维光学表面轮廓仪测量表面粗糙度;采用Kistler 9256B三相测力仪测量主切削力、进给抗力、切深抗力;采用日立TM3000扫描电镜对切屑进行观察。
结果表明:切削速度对表面粗糙度和切削力的影响最大,切削深度和刀具振幅影响次之,进给速度对表面粗糙度和切削力均无显著影响;提高刀具振幅从总体趋势上可以降低切削力和表面粗糙度;随着切削速度的提高,即使切削速度远低于传统公式中计算出来的临界切削速度,切屑也会从平整带状变为两侧呈规律性锯齿状的带状,进而成为散裂状并且中间出现裂纹的切屑,在刀具振幅下降的过程中,以上现象更为明显。
【总页数】5页(P57-61)【作者】李东炜;梁忠伟;孔早慧【作者单位】广州大学机械与电气工程学院;香港理工大学机械工程学系【正文语种】中文【中图分类】TG519.3【相关文献】1.SiCp/Al复合材料超精密车削表面质量的影响因素2.超精密车削表面质量影响因素及发展趋势研究3.超声振动车削W-Fe-Ni表面质量及其形貌特征研究4.Al6061超精密车削工艺参数与表面质量关联性研究5.三维超声振动辅助车削减摩特性与表面质量的实验研究因版权原因,仅展示原文概要,查看原文内容请购买。
机械加工过程中振动的影响2

3、振动对工件表面质量的影响及其控制3。
1振动对工件表面质量的影响机械加工中产生的振动,一般说来是一种破坏正常切削过程的有害现象。
各种切削和磨削过程都可能发生振动,当速度高、切削金属量大时常会产生较强烈的振动。
切削过程中的振动,会影响加工质量和生产率,严重时甚至会使切削不能继续进行,因此通常都是对切削加工不利的,主要表现在以下几个方面。
(1)影响加工的表而粗糙度。
振动频率低时会产生波度,频率高时会产生微观不平度。
(2)影响生产率.加工中产生振动,会限制切削用量的进一步提高,严重时甚至会使切削不能继续进行。
(3)影响刀具寿命。
切削过程中的振动可能使刀尖刀刃崩碎,特别是韧性差的刀具材料,如硬质合金、陶瓷等,要注意消振问题.(4)对机床、夹具等不利。
振动使机床、夹具等的零件连接部分松动,间隙增大,刚度和精度降低,同时使用寿命缩短.此外,强烈的振动及伴随而来的噪声,还会污染环境,危省操作者的身心健康。
对于精密零件的精密加工和超精密加工,其尺寸精度要求多小于m1μ,表面粗糙度值m.0以下,而且不允许出现波纹.因此,在切削过程中哪怕出现极Raμ02其微小的振动,也会导致被加工零件达不到设计的质量要求.振动对机械加工有不利的一面,但又可以利用振动来更好地切削,如振动磨削、振动研抛、超声波加工等都是利用振动来提高表面质量或生产率的.机械加工中产生的振动,根据其产生的原因,大体可分为自由振动、强迫振动和自激振动三大类,如图1所示.图1 切削加工中振动的类型3.2自由振动自由振动是当系统所受的外界干扰力去除后系统本身的衰减振动。
由于工艺系统受一些偶然因素的作用(如外界传来的冲击力、机床传动系统中产生的非周期性冲击力、加工材料的局部硬点等引起的冲击力等),系统的平衡被破坏,只靠其弹性恢复力来维持的振动属于自由振动。
在机械加工中,自由振动是最简单的振动,所占振动比率仅5%左右。
振动的频率就是系统的固有频率。
由于工艺系统的阻尼作用,这类振动会很快衰减。
- 1、下载文档前请自行甄别文档内容的完整性,平台不提供额外的编辑、内容补充、找答案等附加服务。
- 2、"仅部分预览"的文档,不可在线预览部分如存在完整性等问题,可反馈申请退款(可完整预览的文档不适用该条件!)。
- 3、如文档侵犯您的权益,请联系客服反馈,我们会尽快为您处理(人工客服工作时间:9:00-18:30)。
Jun.2015 Hydromechatronics Engineering Vo1.43 NO.12 Hydromechatronics Engineering http://jdy.qks.cqut.edu.ca E-mail:jdygcyw@126.com
Research status of the vi bration assisted machining(VAM)technology ng—qi LI ,Dong YU,Tao SUN (Harbin Imtit ̄e ofTechnology,Harbin 150001,China) Abstract:With the constantly development of precision and ultra・precision machining technology,the vibration assisted machining(VAM)technology applied to the precision and ultra-precision machining has become an inev。 itable trend.This paper combines the domestic and foreign researchers’achievements and introduces the basic principle of uhrasonic vibration assisted cutting technology.Finally,the advantages and research status of the ul- trasonic vibration assisted cutting technology is summarized at the end of paper.
Key words:Vibration assisted cutting,Ultrasonic assisted cutting,Precision and ultra‘precision machining doi:10.3969/j.issn.1001-3881.2015.12.001 Document code:A CLC number:TG1 15.6+3
1 Brief introduction Turning is a machining process that uses the cutting tool’s sharp edge to remove the surface thin layer, then a cylindrical surface is formed.This technology has been used in cutting various types of metal materi— als for centuries.With the development of science and technology,the demands for advanced cutting technol- ogy handling difficult machining problems are in— creased at the same time[1].There are great benefits and potential in ultra—precise machining of steel with single crystal diamond cutter.But the diamond is USU- ally limited to process thenon—ferrous metals,some of the crystals and ductile materials,the adsorption be- tween carbon(diamond)and iron(workpiece)will lead to excessive wear of the cutting tool[2].The in— vention of the ultrasonic vibration cutting technology provides a solution for the above—mentionedproblems. The ultrasonic vibration cutting technology is proposed by the Japanese scholar Kumabe Junichiro in the 1950s.Ultrasonic vibration cutting overlaps regular ul— trasonic vibration on the cutting tool or workpiece, and makes the tool or workpiece vibrate periodically. Received 4 November 2014;revised 26 February 2015; accepted 5 March 2015 ¥Corresponding author:Zeng—qiang LI.Professor E—mail:zqlee@hit.edu.en It is a new technology which combines and ultrasonic cutting technologies[3]. the ordinary With the constantly development and mature of pre- cision and ultra—precision processing technology,the vibration assisted cutting technology applied to the precision and ultra—precision machining has become an inevitable trend.After studied for many years,numer- OUS domestic and foreign experts found that ultrasonic vibration cutting has significant advantages as con— pared with ordinary cutting,such as smaller cutting force,better surface quality and longer tool life. Therefore,the development of ultrasonic vibration cut— ting technology has attracted the attention of scientists all over the world. Japan is the first country to study ultrasonic machi— ning technology.In terms of the research depth and width or the practical application effects,Japan is the leader in this field.In Japan.the research on vibra. tion cutting and ultrasonic grinding has become con- siderably intensive in the 1970s.There were two of the most authoritative and most representative scholars. One is Shimakawa Jungxianat Chuo University.anoth— er is Kumabe Junichiro at Utsunomiya University.who put forward the theory of vibration cutting system in 1956 and published a number of papers.He is the first expert successfully applying the vibration cutting theory to turning,planning,milling,drilling,boring, reaming,broaching,grinding,screw thread machi— ning,gear machining,polishing,honing,stretching, 2 Zeng-qiang LI,et a1. squeezing and other processing fields,and all of these had promoted the worJdwide researches and populari— zation of ultrasonic vibration cutting.The ultrasonic elliptical vibration cutting technology was put forward by Japanese scholar in the 1990s.The basic principle is based on the traditional ultrasonic vibration cutting. It adds a simple harmonic vibration toward the direc- tion of chip flow.Two orthogonal simple harmonic vi— bration make the cutting tool’s motion into an elliptic trajectory,thus it could realize the elliptical vibration cutting on workpiece. At the end of 1950s and early 1960s,the former So- viet Union began to study ultrasonic vibration cutting and published many valuable papers.The ultrasonic vibration cutting was applied to the practical process— ing of ultrasonic turning,grinding,finishing and com— posite processing,and it achieved considerable eco— nomic benefits.A discussion held in the former Soviet Union in 1973,confirmed the economic effects and practical values of ultrasonic machining,which promo— ted the popularization of this new technology in this country.America started the research on the uhrason— ic vibration cutting since 1960s.However,the quality of the designed and manufactured acoustic vibration system,transducer and generator is disillusionary due to the immature ultrasonic machining technology.In the middle of the 1970s,American begun to use the ultrasonic drilling center hole,finishing machining, grinding and welding.Other countries like German, Britain,Singapore and South Korea have also made a— bundant Ilesearches on the ultrasonic vibration’s ma- chining mechanism and industrial application,and published many valuable papers. In China,research on ultrasonic machining began at the end of the 1950s,but the research of the ultra— sonic generator,transducer,acoustic vibration system COOls down quickly due to the lack of reasonable or— ganization and sustaining researches.In the 1970s. Harbin Institute of Technology has applied the ultra— sonic turning to the airborne aluminum slender axis, and achieved excellent cutting effects,which still lacks enough summaries and studies in—depth l 4 J. Until the late 1990s,because of the urgent demands of vibration cutting technology from national defense, aerospace and other fields,ultrasonic vibration cutting technology became the resealx3h hot topic ofChinese scholars again.In this period,the Beihang University achiered a series of technological breakthroughs.At present,China has made lots of valuable achievements in the machining of materials difficult to cut or diffi— cult to break and remove chip[5].