渗氮、渗碳工艺
渗碳与渗氮的区别

钢的渗碳和渗氮钢的渗碳---就是将低碳钢在富碳的介质中加热到高温(一般为900--950C),使活性碳原子渗入钢的表面,以获得高碳的渗层组织。
随后经淬火和低温回火,使表面具有高的硬度、耐磨性及疲劳抗力,而心部仍保持足够的强度和韧性。
渗碳钢的化学成分特点(1)渗碳钢的含碳量一般都在0.15--0.25%范围内,对于重载的渗碳体,可以提高到0.25--0.30%,以使心部在淬火及低温回火后仍具有足够的塑性和韧性。
但含碳量不能太低,否则就不能保证一定的强度。
(2)合金元素在渗碳钢中的作用是提高淬透性,细化晶粒,强化固溶体,影响渗层中的含碳量、渗层厚度及组织。
在渗碳钢中通常加入的合金元素有锰、铬、镍、钼、钨、钒、硼等。
常用渗碳钢可以分碳素渗碳钢和合金渗碳钢两大类。
(1)碳素渗碳钢中,用得最多的是15和20钢,它们经渗碳和热处理后表面硬度可达56--62HRC。
但由于淬透性较低,只适用于心部强度要求不高、受力小、承受磨损的小型零件,如轴套、链条等。
(2)低合金渗碳钢如20Cr、20Cr2MnVB、20Mn2TiB等,其渗透性和心部强度均较碳素渗碳钢高,可用于制造一般机械中的较为重要的渗碳件,如汽车、拖拉机中的齿轮、活塞销等。
(3)中合金渗碳钢如20Cr2Ni4、18Cr2N4W、15Si3MoWV等,由于具有很高的淬透性和较高的强度及韧性,主要用以制造截面较大、承载较重、受力复杂的零件,如航空发动机的齿轮、轴等。
固体渗碳;液体渗碳;气体渗碳---渗碳温度为900--950C,表面层w(碳)为0.8--1.2%,层深为0.5--2.0mm。
渗碳后的热处理---渗碳工件实际上应看作是由一种表面与中心含量相差悬殊码复合材料。
渗碳只能改变工件表面的含碳量,而其表面以及心部的最终强化则必须经过适当的热处理才能实现。
渗碳后的工件均需进行淬火和低温回火。
淬火的目的是使在表面形成高碳马氏体或高碳马氏体和细粒状碳化物组织。
渗氮渗碳工艺
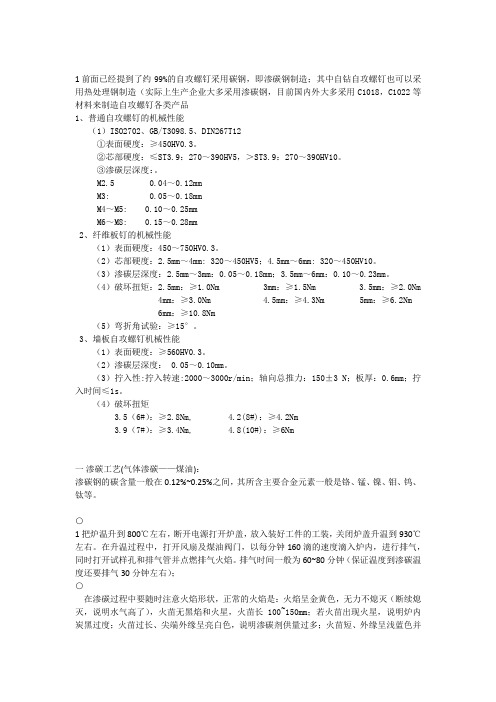
1 前面已经提到了约99%的自攻螺钉采用碳钢,即渗碳钢制造;其中自钻自攻螺钉也可以采用热处理钢制造(实际上生产企业大多采用渗碳钢,目前国内外大多采用C1018,C1022等材料来制造自攻螺钉各类产品1、普通自攻螺钉的机械性能(1)ISO2702、GB/T3098.5、DIN267T12①表面硬度:≥450HV0.3。
②芯部硬度:≤ST3.9:270~390HV5,>ST3.9:270~390HV10。
③渗碳层深度:。
M2.5 0.04~0.12mmM3: 0.05~0.18mmM4~M5: 0.10~0.25mmM6~M8: 0.15~0.28mm2、纤维板钉的机械性能(1)表面硬度:450~750HV0.3。
(2)芯部硬度:2.5mm~4mm: 320~450HV5;4.5mm~6mm: 320~450HV10。
(3)渗碳层深度:2.5mm~3mm:0.05~0.18mm;3.5mm~6mm:0.10~0.23mm。
(4)破坏扭矩:2.5mm:≥1.0Nm 3mm:≥1.5Nm 3.5mm:≥2.0Nm 4mm:≥3.0Nm 4.5mm:≥4.3Nm 5mm:≥6.2Nm6mm:≥10.8Nm(5)弯折角试验:≥15°。
3、墙板自攻螺钉机械性能(1)表面硬度:≥560HV0.3。
(2)渗碳层深度: 0.05~0.10mm。
(3)拧入性:拧入转速:2000~3000r/min;轴向总推力:150±3 N;板厚:0.6mm;拧入时间≤1s。
(4)破坏扭矩3.5(6#):≥2.8Nm,4.2(8#):≥4.2Nm3.9(7#):≥3.4Nm,4.8(10#):≥6Nm一渗碳工艺(气体渗碳——煤油):渗碳钢的碳含量一般在0.12%~0.25%之间,其所含主要合金元素一般是铬、锰、镍、钼、钨、钛等。
○1 把炉温升到800℃左右,断开电源打开炉盖,放入装好工件的工装,关闭炉盖升温到930℃左右。
渗氮 渗碳 碳氮共渗

渗氮渗碳碳氮共渗碳氮共渗是一种常见的表面处理技术,通过渗碳和渗氮来改善材料的硬度和耐磨性。
本文将对渗氮、渗碳和碳氮共渗的原理、应用和工艺进行详细介绍。
一、渗氮渗氮是将氮原子渗入材料表面形成氮化物层的过程。
氮原子通过高温处理和氮气氛的作用,渗透到材料表面并与材料中的元素反应,形成硬质氮化物层。
这一薄层氮化物层不仅能提高材料的硬度和抗磨损性能,还能改善材料的耐腐蚀性。
渗氮的主要应用领域包括机械制造、汽车工业、航空航天等。
在机械制造中,渗氮可以增加零件的硬度和耐磨性,延长使用寿命;在汽车工业中,渗氮可以提高引擎零件的耐磨性和抗腐蚀性能;在航空航天领域,渗氮可以增强航空发动机部件的耐高温和耐磨性能。
渗氮的工艺流程一般包括清洗件表面、装配件和炉内预处理、渗氮和回火处理等步骤。
渗氮一般采用封闭式和开放式两种方式进行,根据具体应用需求可以选择合适的渗氮工艺。
二、渗碳渗碳是将碳原子渗入材料表面形成碳化物层的过程。
碳原子通过高温处理和含有碳气体的氛围,渗透到材料表面并在表面与材料中的元素反应,形成硬质碳化物层。
渗碳技术不仅能提升材料的硬度和耐磨性,还可以改善材料的断裂韧性和抗腐蚀性。
渗碳广泛应用于机械零件、钢铁制品等领域。
渗碳后的材料表面硬度高、耐磨性好,适用于制作耐磨零件,如轴承、齿轮等;同时碳化层的外表面与空气隔绝,降低了材料的腐蚀速率,提高了零件的使用寿命。
渗碳的工艺流程包括预处理、渗碳、淬火和回火等。
渗碳一般采用气体渗碳和液体渗碳两种方式进行,具体工艺参数可以根据材料的要求进行选择。
三、碳氮共渗碳氮共渗是将碳原子和氮原子同时渗入材料表面形成碳氮共渗层的过程。
碳氮共渗通过碳氮共渗剂和高温处理,使碳原子和氮原子分别与材料中的元素发生反应,形成硬质碳氮化物层。
碳氮共渗能够同时获得渗碳和渗氮的特性,提高材料的硬度、耐磨性和抗腐蚀性。
碳氮共渗广泛应用于汽车工业、航空航天等领域。
在汽车工业中,碳氮共渗可以提高零部件的硬度和耐磨性,同时还可以提高零部件的抗磨损能力和抗腐蚀性;在航空航天领域,碳氮共渗可以增强发动机部件的抗高温性能和抗腐蚀能力。
化学热处理方法

化学热处理方法
化学热处理是一种在工件表面涂覆化学物质并利用化学反应来
改善工件材料的热处理工艺。
以下是常见的化学热处理方法:
1. 渗碳:在工件表面涂覆碳素墨水,并在高温下加热,碳素墨水
会将碳元素渗入工件表面,形成渗碳层。
这种热处理方法可以用于制作高强度、高硬度的零部件。
2. 渗氮:在工件表面涂覆氮化墨水,并在高温下加热,氮化墨水
会使工件表面形成氮化层,提高工件的耐磨性和耐腐蚀性。
这种热处理方法可以用于制作耐磨、耐腐蚀的零部件。
3. 硬化:在工件表面涂覆硬化剂,并在高温下加热,硬化剂会在
工件表面形成坚硬的硬化层,提高工件的强度和硬度。
这种热处理方法可以用于制作高强度、高硬度的零部件。
4. 氧化:在工件表面涂覆氧化剂,并在高温下加热,氧化剂会在
工件表面形成氧化层,提高工件的耐腐蚀性。
这种热处理方法可以用于制作耐蚀的零部件。
5. 电镀:在工件表面涂覆电镀剂,并在高温下加热,电镀剂将工
件表面形成电镀层,提高工件的耐腐蚀性和耐磨性。
这种热处理方法可以用于制作需要耐腐蚀性和耐磨性的零部件。
化学热处理方法的应用范围非常广泛,可以用于制作各种零部件,如汽车发动机零件、航空航天部件、机械零件等。
最全的渗碳和渗氮区别整理表格
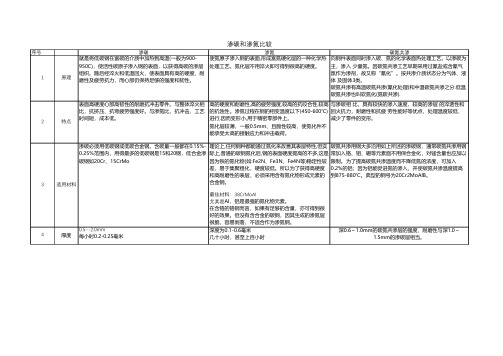
序号渗碳和渗氮比较12特点表面高硬度心部高韧性的耐磨抗冲击零件。
与整体淬火相比,抗挤压、抗弯疲劳强度好。
与渗氮比,抗冲击,工艺时间短,成本低。
高的硬度和耐磨性,高的疲劳强度,较高的抗咬合性,较高的抗蚀性。
渗氮过程在钢的相变温度以下(450-600℃)进行,因而变形小,用于精密零部件上。
氮化层较薄,一般0.5mm、且脆性较高,使氮化件不能承受太高的接触应力和冲击载荷。
渗碳渗氮就是将低碳钢在富碳的介质中加热到高温(一般为900-950C),使活性碳原子渗入钢的表面,以获得高碳的渗层组织。
随后经淬火和低温回火,使表面具有高的硬度、耐磨性及疲劳抗力,而心部仍保持足够的强度和韧性。
使氮原子渗入钢的表面,形成富氮硬化层的一种化学热处理工艺。
氮化层不用淬火即可得到很高的硬度。
原理碳氮共渗向钢件表面同时渗入碳、氮的化学表面热处理工艺。
以渗碳为主,渗入 少量氮。
因碳氮共渗工艺早期采用过氰盐或含氰气氛作为渗剂,故又称“氰化”。
按共渗介质状态分为气体、液体 及固体3类。
碳氮共渗有高温碳氮共渗(氰化处理)和中温碳氮共渗之分.低温碳氮共渗也叫软氮化(氮碳共渗).与渗碳相 比,具有较快的渗入速度,较高的渗层 的淬透性和回火抗力,耐磨性和抗疲 劳性能好等优点,处理温度较低,减少了零件的变形。
3适用材料渗碳必须用低碳钢或低碳合金钢。
含碳量一般都在0.15%-0.25%范围内,用得最多的低碳钢是15和20钢,低合金渗碳钢如20Cr、15CrMo理论上,任何钢种都能通过氮化来改善其表层特性,但实际上,普通的碳钢氮化后,钢的表面硬度提高的不多,这是因为铁的氮化物(如:Fe2N、Fe3N、Fe4N等)稳定性较差,易于集聚粗化,硬度较低。
所以为了获得高硬度和高耐磨性的表层,必须采用含有氮化物形成元素的合金钢。
最佳材料:38CrMoAl尤其是AI,铝是最强的氮化物元素。
在含铬的铬钢而言,如果有足够的含量,亦可得到很好的效果。
但没有含合金的碳钢,因其生成的渗氮层很脆,容易剥落,不适合作为渗氮钢。
渗碳与渗氮的区别
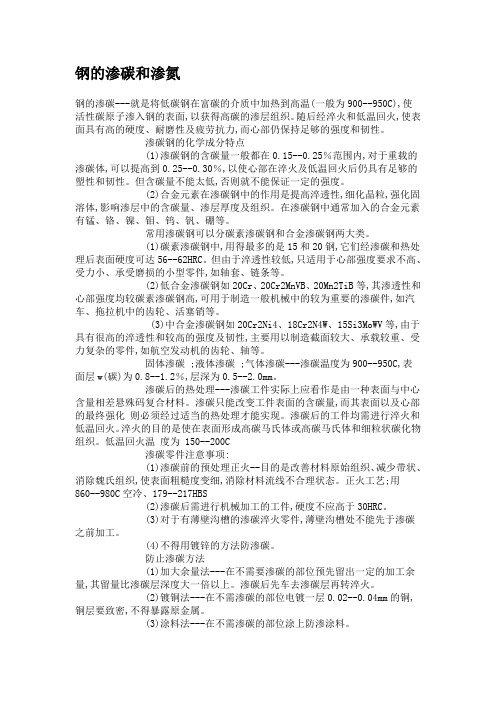
钢的渗碳和渗氮钢的渗碳---就是将低碳钢在富碳的介质中加热到高温(一般为900--950C),使活性碳原子渗入钢的表面,以获得高碳的渗层组织。
随后经淬火和低温回火,使表面具有高的硬度、耐磨性及疲劳抗力,而心部仍保持足够的强度和韧性。
渗碳钢的化学成分特点(1)渗碳钢的含碳量一般都在0.15--0.25%范围内,对于重载的渗碳体,可以提高到0.25--0.30%,以使心部在淬火及低温回火后仍具有足够的塑性和韧性。
但含碳量不能太低,否则就不能保证一定的强度。
(2)合金元素在渗碳钢中的作用是提高淬透性,细化晶粒,强化固溶体,影响渗层中的含碳量、渗层厚度及组织。
在渗碳钢中通常加入的合金元素有锰、铬、镍、钼、钨、钒、硼等。
常用渗碳钢可以分碳素渗碳钢和合金渗碳钢两大类。
(1)碳素渗碳钢中,用得最多的是15和20钢,它们经渗碳和热处理后表面硬度可达56--62HRC。
但由于淬透性较低,只适用于心部强度要求不高、受力小、承受磨损的小型零件,如轴套、链条等。
(2)低合金渗碳钢如20Cr、20Cr2MnVB、20Mn2TiB等,其渗透性和心部强度均较碳素渗碳钢高,可用于制造一般机械中的较为重要的渗碳件,如汽车、拖拉机中的齿轮、活塞销等。
(3)中合金渗碳钢如20Cr2Ni4、18Cr2N4W、15Si3MoWV等,由于具有很高的淬透性和较高的强度及韧性,主要用以制造截面较大、承载较重、受力复杂的零件,如航空发动机的齿轮、轴等。
固体渗碳 ;液体渗碳 ;气体渗碳---渗碳温度为900--950C,表面层w(碳)为0.8--1.2%,层深为0.5--2.0mm。
渗碳后的热处理---渗碳工件实际上应看作是由一种表面与中心含量相差悬殊码复合材料。
渗碳只能改变工件表面的含碳量,而其表面以及心部的最终强化则必须经过适当的热处理才能实现。
渗碳后的工件均需进行淬火和低温回火。
淬火的目的是使在表面形成高碳马氏体或高碳马氏体和细粒状碳化物组织。
渗碳和渗氮的新概念及其实际运用
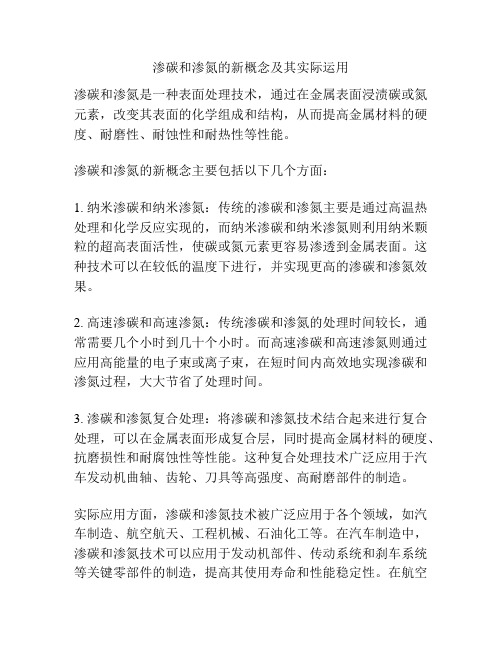
渗碳和渗氮的新概念及其实际运用
渗碳和渗氮是一种表面处理技术,通过在金属表面浸渍碳或氮元素,改变其表面的化学组成和结构,从而提高金属材料的硬度、耐磨性、耐蚀性和耐热性等性能。
渗碳和渗氮的新概念主要包括以下几个方面:
1. 纳米渗碳和纳米渗氮:传统的渗碳和渗氮主要是通过高温热处理和化学反应实现的,而纳米渗碳和纳米渗氮则利用纳米颗粒的超高表面活性,使碳或氮元素更容易渗透到金属表面。
这种技术可以在较低的温度下进行,并实现更高的渗碳和渗氮效果。
2. 高速渗碳和高速渗氮:传统渗碳和渗氮的处理时间较长,通常需要几个小时到几十个小时。
而高速渗碳和高速渗氮则通过应用高能量的电子束或离子束,在短时间内高效地实现渗碳和渗氮过程,大大节省了处理时间。
3. 渗碳和渗氮复合处理:将渗碳和渗氮技术结合起来进行复合处理,可以在金属表面形成复合层,同时提高金属材料的硬度、抗磨损性和耐腐蚀性等性能。
这种复合处理技术广泛应用于汽车发动机曲轴、齿轮、刀具等高强度、高耐磨部件的制造。
实际应用方面,渗碳和渗氮技术被广泛应用于各个领域,如汽车制造、航空航天、工程机械、石油化工等。
在汽车制造中,渗碳和渗氮技术可以应用于发动机部件、传动系统和刹车系统等关键零部件的制造,提高其使用寿命和性能稳定性。
在航空
航天领域,渗碳和渗氮技术可以应用于航空发动机涡轮叶片、导向叶片等高温部件的制造,提高其耐热性和耐腐蚀性。
总之,渗碳和渗氮的新概念和实际运用不断拓展着金属材料表面处理的领域,为各个行业提供了更高性能的金属材料解决方案。
渗氮、渗碳工艺与操作过程

一渗碳工艺(气体渗碳——煤油):渗碳钢的碳含量一般在0.12%~0.25%之间,其所含主要合金元素一般是铬、锰、镍、钼、钨、钛等。
○1把炉温升到800℃左右,断开电源打开炉盖,放入装好工件的工装,关闭炉盖升温到930℃左右。
在升温过程中,打开风扇及煤油阀门,以每分钟160滴的速度滴入炉内,进行排气,同时打开试样孔和排气管并点燃排气火焰。
排气时间一般为60~80分钟(保证温度到渗碳温度还要排气30分钟左右);○2当火焰为鸡蛋黄颜色时开始强渗了,此时要加大煤油的滴量,按每分钟180~200滴。
在强渗时就可用放入试棒(含碳量少的材料,尺寸Ф8×100mm),关闭试样孔,炉压保持在6~10格——渗层深炉压取高值。
渗碳速度一般按0.15~0.2mm/h来计算,如要渗层深度为0.8~1.2mm,则强渗时间为6小时,提前在强渗设定时间结束前半小时,取出试棒,观察渗层深度(试棒渗层深度一般为工件的一半,这边渗层深度靠操作工的肉眼加经验判断),深度够在强渗结束就可以开始扩散,否则增加强渗时间;○3扩散期温度不变,减少煤油滴量,按每分钟100滴,一般扩散时间为60~90分钟,作用是均匀工件表层的碳溶度;○4扩散期结束开始降温,此时断开加热器,降温到810℃左右,并在此温度保温10~20分钟。
降温期减少煤油滴量,按每分钟60滴。
保温结束时断开加热器,关闭风扇,打开炉盖,用行车吊起工装,垂直进入温度为50~70℃的油中冷却,冷却时上下左右轻轻摇动工装,一般冷却时间为10~20分钟左右,吊起工装时也要注意工件出油的温度。
○5冷却好的工件要在半个小时之内(防止工件开裂)进行低温回火,温度一般在160~190℃(由硬度要求而定),保温时间2小时左右出炉空冷。
在渗碳过程中要随时注意火焰形状,正常的火焰是:火焰呈金黄色,无力不熄灭(断续熄灭,说明水气高了),火苗无黑焰和火星,火苗长100~150mm;若火苗出现火星,说明炉内炭黑过度;火苗过长、尖端外缘呈亮白色,说明渗碳剂供量过多;火苗短、外缘呈浅蓝色并有透明,说明渗碳剂供量不足或炉子漏气。
- 1、下载文档前请自行甄别文档内容的完整性,平台不提供额外的编辑、内容补充、找答案等附加服务。
- 2、"仅部分预览"的文档,不可在线预览部分如存在完整性等问题,可反馈申请退款(可完整预览的文档不适用该条件!)。
- 3、如文档侵犯您的权益,请联系客服反馈,我们会尽快为您处理(人工客服工作时间:9:00-18:30)。
1?前面已经提到了约99%的自攻螺钉采用碳钢,即渗碳钢制造;其中自钻自攻螺钉也可以采用热处理钢制造(实际上生产企业大多采用渗碳钢,目前国内外大多采用C1018,C1022等材料来制造自攻螺钉各类产品
1、普通自攻螺钉的机械性能
(1)ISO2702、GB/T3098.5、DIN267T12
①表面硬度:≥450HV0.3。
②芯部硬度:≤ST3.9:270~390HV5,>ST3.9:270~390HV10。
③渗碳层深度:。
M2.5 0.04~0.12mm
M3: 0.05~0.18mm
M4~M5: 0.10~0.25mm
M6~M8: 0.15~0.28mm
2、纤维板钉的机械性能
(1)表面硬度:450~750HV0.3。
(2)芯部硬度:2.5mm~4mm: 320~450HV5;4.5mm~6mm: 320~450HV10。
(3)渗碳层深度:2.5mm~3mm:0.05~0.18mm;3.5mm~6mm:0.10~0.23mm。
(4)破坏扭矩:2.5mm:≥1.0Nm 3mm:≥1.5Nm 3.5mm:≥2.0Nm 4mm:≥3.0Nm 4.5mm:≥4.3Nm 5mm:≥6.2Nm
6mm:≥10.8Nm
(5)弯折角试验:≥15°。
3、墙板自攻螺钉机械性能
(1)表面硬度:≥560HV0.3。
(2)渗碳层深度: 0.05~0.10mm。
(3)拧入性:拧入转速:2000~3000r/min;轴向总推力:150±3 N;板厚:0.6mm;拧入时间≤1s。
(4)破坏扭矩
3.5(6#):≥2.8Nm,
4.2(8#):≥4.2Nm
3.9(7#):≥3.4Nm,
4.8(10#):≥6Nm
一?渗碳工艺(气体渗碳——煤油):?
渗碳钢的碳含量一般在0.12%~0.25%之间,其所含主要合金元素一般是铬、锰、镍、钼、钨、钛等。
?
○
1?把炉温升到800℃左右,断开电源打开炉盖,放入装好工件的工装,关闭炉盖升温到930℃左右。
在升温过程中,打开风扇及煤油阀门,以每分钟160滴的速度滴入炉内,进行排气,同时打开试样孔和排气管并点燃排气火焰。
排气时间一般为60~80分钟(保证温度到渗碳温度还要排气30分钟左右);?
○
在渗碳过程中要随时注意火焰形状,正常的火焰是:火焰呈金黄色,无力不熄灭(断续熄灭,说明水气高了),火苗无黑焰和火星,火苗长100~150mm;若火苗出现火星,说明炉内炭黑过度;火苗过长、尖端外缘呈亮白色,说明渗碳剂供量过多;火苗短、外缘呈浅蓝色并有透明,说明渗碳剂供量不足或炉子漏气。
渗碳工艺曲线说明如下:?
赶气:其目的是赶走炉内空气,使炉内空气恢复到工艺规定的碳势气氛。
?保温:其目的是使炉内工件温度均匀。
保温时间一般是40min到1h。
? 渗碳温度和渗碳时间:渗碳温度一般为
900~940℃,渗碳时间应根据要求的渗碳层深度确定,它与渗碳温度、炉内气氛的碳势及工件特征等因素有关。
? 渗碳剂的选择及应用:采用滴注式渗碳时,可根据生产厂条件选择渗碳剂。
选用普通煤油作渗碳剂,炉内碳黑较多。
选用航空煤油,不易产生碳黑,甲醇作载气,煤油作富化气,炉内碳黑较少。
用甲醇作载气,丙酮或醋酸乙醋作富化气,炉内碳黑则更少,可进行气氛的碳势控制。
渗碳剂用量根据工件装载量和表面积大小等因素进行调整。
2?当火焰为鸡蛋黄颜色时开始强渗了,此时要加大煤油的滴量,按每分钟180~200滴。
在强渗时就可用放入试棒(含碳量少的材料,尺寸Ф8×100mm),关闭试样孔,炉压保持在6~10格——渗层深炉压取高值。
渗碳速度一般按0.15~0.2mm/h来计算,如要渗层深度为0.8~1.2mm,则强渗时间为6小时,提前在强渗设定时间结束前半小时,取出试棒,观察渗层深度(试棒渗层深度一般为工件的一半,这边渗层深度靠操作工的肉眼加经验判断),深度够在强渗结束就可以开始扩散,否则增加强渗时间;?
○3?扩散期温度不变,减少煤油滴量,按每分钟100滴,一般扩散时间为60~90分钟,
作用是均匀工件表层的碳溶度;?
○
4?扩散期结束开始降温,此时断开加热器,降温到810℃左右,并在此温度保温10~20分钟。
降温期减少煤油滴量,按每分钟60滴。
保温结束时断开加热器,关闭风扇,打开炉盖,用行车吊起工装,垂直进入温度为50~70℃的油中冷却,冷却时上下左右轻轻摇动工装,一般冷却时间为10~20分钟左右,吊起工装时也要注意工件出油的温度。
?
○
5冷却好的工件要在半个小时之内(防止工件开裂)进行低温回火,温度一般在160~190℃(由硬度要求而定),保温时间2小时左右出炉空冷。
?
???在渗碳过程中要随时注意火焰形状,正常的火焰是:火焰呈金黄色,无力不熄灭(断续熄灭,说明水气高了),火苗无黑焰和火星,火苗长100~150mm;若火苗出现火星,说明炉内炭黑过度;火苗过长、尖端外缘呈亮白色,说明渗碳剂供量过多;火苗短、外缘呈浅蓝色并有透明,说明渗碳剂供量不足或炉子漏气。
??
?渗碳过程:煤油→滴量管→罐内→U型管→排气管
?2?
当液滴直径分别为3、3.5及4mm,滴速皆为200滴/分钟,计算结果表明其流量分别为2.82、4.5及6.72毫升/分,相当于1:1.6:2.4。
一般以每100平方厘米的渗碳面积滴入1.0~1.2cm3/h 的渗碳剂为宜。
??气体渗碳工艺:?
1,加氨渗碳,在渗碳气体中通入一部分氨气,可以收到良好的效果。
一方面由于通入氨可以减少碳黑的形成,另一方面由于NH3分解产生的氮可以加快碳原子的吸收和扩散,缩短渗碳时间。
一般是在井式气体渗碳炉的滴管上装一分管,通入2.5~5%的氨即可;?
2,煤油(或丙醇)+甲醇的分段渗碳,根据渗碳过程中不同阶段及不同渗剂的性能特点,联合使用煤油(或丙醇)+甲醇进行分段渗碳,在渗碳的不同阶段采用不同的渗剂和滴量。
? ??由于甲醇裂解温度低,产气量大以及不易形成碳黑,所以在排气阶段的前期(900℃以下),单独滴入甲醇,以尽快排除炉内的空气。
在炉温高于900℃后,煤油已能充分热解,在正常滴量下也不致形成大量的碳黑,为了更快的恢复炉气活性,改滴煤油,继续排气。
保温期可以减少煤油滴量(分解吸收平衡及避免形成碳黑),扩散过程总是慢于吸收过程的特点以及为了降低表层碳浓度,再进一步减少煤油滴量。
到降温期预冷时,只要维持炉内还原气氛即可,因此又停滴煤油,改滴少量甲醇。
?此工艺渗剂耗量小,生产周期短,而且表面含碳量也比较理想(0.8%~1.1%)和渗层中碳浓度分布也较均匀。
?
3,滴注式可控气氛渗碳,是利用有机液体直接滴入炉罐而进行碳势控制的渗碳工艺,它同时向炉内滴入两种不同的有机液体。
一种产生稀释气体,起到冲淡作用;另一种产生富化气,
起渗碳作用。
???通常选用甲醇(CH3OH)产生稀释气体。
甲醇在800℃时就能充分分解,为了防止零件氧化,在650℃时就可用向炉内滴注。
作用是渗碳初期排气,渗碳阶段维持炉内正压,并构成恒定的炉气成分。
一般采用醇(甲醇、乙醇)类或酯(乙酸乙酯、醋酸乙酯)作为渗碳剂。
国内一些单位用丙酮或煤油作为渗碳剂进行滴控也取得满意的效果。
??滴注式可控气体渗碳可以获得高质量的渗碳层,表面光洁,碳势可控,又具有井式炉气体渗碳法的经济性和简便性。
?
二?渗氮工艺过程(气体渗氮——液氨):?
炉罐用1Cr18Ni9Ti等不锈耐热钢做的,这种渗氮罐使用一段时间后,其表面往往会对氨的分解起到催化作用,加大氨的分解率,甚至发展到无法控制。
因此在使用一段时期后,把渗氮罐加热到800℃以上保温3~4小
时或650℃保温6小时进行退氮处理,处理后又可恢复正常使用。
?1),渗氮前的设备准备及检查?1,清理氮化管,?2,清理管道,?2),渗氮工件的准备?
1,非渗氮面的防护,镀层或涂料,镀层一般是镀锡,涂料是水玻璃和石墨粉的混合物,? 2,工件表面的清洗,先用棉布擦干净,再用汽油洗,最后用棉布把工件擦干净;?3,工夹具的准备,也要干净、无油垢和铁锈,铁丝也要去除表面的镀锡层?4,工件的装炉,洗好的工件在2小时内装炉,工件的高度不能超过排气管的高度,试样也要一起放进去?
5,升温,封炉盖进行升温,有风扇的开风扇并同氨气。
氨气流量控制在0.2~0.3m3/小时或0.4~0.5m3/小时,使进气压力保持在20~40mm油柱。
然后炉温升到200~250度,保温1~3小时进行排气,用氨气将罐内和管道中的空气排除干净。
当罐内空气小于5%或氨气分解率为零时,才允许继续升温。
这时可以降低氨气流量,保持罐内正压,使工件不被氧化即可;? ??当炉温升到450度左右时,控制升温速度,不要过快,以免造成保温初期的超温。
同时加大氨气流量,使氨气分解率控制在工艺规定的下限。
这样到达温度后,氨气分解率就会保持在要求分为内,可以加快渗氮速度。
在到温前5~10度或到温初期,校正温度。
渗氮温度以罐内温度为准;?6,保温,?
??渗氮罐内到达温度后,进入保温阶段。
这时根据工艺规范要求调节氨流量,并保持温度和氨气分解率的正确和稳定。
保温初期当测得分解率在要求范围内时,记下此时的进气和排气压力,并在整个过程中尽量保持压力不变。
同时每隔半小时或一小时测量氨气分解率一次;? ?此外还要经常观察炉温控制系统和风扇运转是否正常,进气及排气压力是否稳定。