注塑成型工艺与模具设计word文档
《塑料成型工艺及模具设计》课程设计指导书word资料10页

《塑料成型工艺及模具设计》课程设计指导书(一)塑料模具课程设计的目的塑料模具课程设计是《塑料成型工艺与模具设计》课程中的最后一个实践性教学环节,也是一次对学生进行比较全面的塑料模具设计的训练,其目的是:(1)通过模具课程设计,要求学生综合应用《塑料成型工艺与模具设计》及其他相关课程的基本知识来解决工程实际中的具体设计问题,以进一步巩固和深化所学课程的知识。
(2)通过模具课程设计,学生进行了一次较为完整的塑料模具设计的实际训练,使学生初步掌握塑料模具设计的内容、步骤和基本方法,进一步提高学生的结构设计能力和独立工作能力,为毕业设计和今后从事模具设计与制造工作奠定基础。
(3)通过模具课程设计,提高学生查阅技术资料和手册的能力,熟悉并正确应用有关的技术标准。
(4)通过模具课程设计,培养学生认真负责、踏实细致的工作作风和严谨的科学态度,强化学生的质量意识和时间观念,使学生初步形成从业的基本素职。
(二)课程设计的任务塑件形状:以盖状零件为例设计注塑模具,塑件形状、尺寸、公差等自行拟定。
例如:塑件说明:塑件材料为ABS。
采用注射成型,进行大批量生产,以满足日常生活用品的需要。
技术要求:1、壁厚均匀;2、塑件不允许有裂纹和变形缺陷;3、脱模斜度30'~1°;4、模具结构设计要求:根据塑件大小设计成多型腔或单型腔模具。
课程设计任务要求:要求在规定的时间内完成如下任务:(1)绘制塑料制件图一张(A4)(手工绘图,或用计算机绘图)(2)绘制塑料注射模装配图一张(A2及以上,根据塑件尺寸自行选择,及以细节表达清晰为准)(必须手工绘图)(3)绘制模具零件工作图2~3张(手工绘图,或用计算机绘图)(4)编写设计说明书一份(要求设计过程详细,图文并茂)注意:图纸的线形、标注、公差等严格按照机制绘图标准执行。
(三)塑料注射模具设计步骤(仅供参考,可自行安排)1.塑件成型工艺分析(1)塑件成型特性的分析根据塑件图中标明的塑料品种,分析该塑料的使用性能及成型性能;查阅该塑料的比重、比容、收缩率及流动性等特性。
塑料成型工艺与模具设计 电子文档 学习情境4

学习情境4:塑件注射成型工艺参数的选用项目内容·塑件注射成型工艺参数的选用学习目标·了解塑件注射成型工艺·查表选用塑件的注射成型工艺参数能力目标·能查表选用塑件的注射成型工艺参数主要知识点·塑件注射成型工艺·塑件注射成型工艺参数一、任务引入图4-1所示塑料线圈骨架,材质为ABS, 采用塑料精度MT5级,生产批量1万件。
请拟定该塑件的成型工艺方案、选定参数。
(一)注射成型原理和特点·注射成型是热塑性塑料制品生产的一种重要方式。
注射成型又称注塑成型。
到目前为止,除氟塑料外,几乎所有的热塑性塑料都可以用注射成型方法生产塑件。
注射成型现在不但用于热塑性塑料的成型,而且已成功应用于热固性塑料的成型。
·注射成型主要通过注射机和模具来实现。
注射机种类很多,但其基本作用有两个:其一是加热熔融塑料,使其达到粘流状态;其二是对粘流态的塑料施加高压,使其射入模具型腔内。
·根据使用的注射机类型的不同,注射成型可分为柱塞式注射机和螺杆式注射机注射成型。
柱塞式注射机结构简单,但注射成型中一般存在塑化不均匀、注射压图4-1 塑料线圈骨架简图力损失大、注射量小(一般在60g以下)和塑料流动状态不太理想、料筒清理较困难等方面的缺陷,所以柱塞式注射机正被螺杆式注射机所替代。
图4-2螺杆式注射机注射成型工作循环,如图4-3所示。
图4-3·与柱塞式注射机注射成型相比较,螺杆式注射机注射成型由于螺杆的剪切作用,塑料混合均匀,塑化效果好,改善了成型工艺,提高了塑件质量。
同时扩大了注射成型塑料品种的范围和最大注射量。
因此,对于热敏性和流动性差的塑料和大、中型塑件,一般可用移动螺杆式注射机成型。
·注射成型周期短,生产率高,可采用微机控制,容易实现自动化生产。
·注射成型能成型形状复杂、尺寸精确、带有金属或非金属嵌件制件。
·但是,注射成型模具结构复杂,成型设备昂贵,生产成本高,不适于单件小批量塑件生产。
(完整word版)《塑料成型工艺与模具设计》(上册)电子教案完全版

JSZ024-1广东省高级技工学校教案本授课日期:2009年09月~2010年01月课程名称:《塑料成型工艺与模具设计》(上册)授课班级:高模33、34班授课教师:汪立胜课题:§1 绪论【组织教学】【讲授新课】§1 绪论一、塑料成型在塑料工业中的地位(一)塑料工业的生产过程塑料工业包含塑料生产和塑料制品生产两个系统。
(二)塑料制品生产及塑料成型的重要性1、塑料制品生产的组成(1)预处理;(2)塑料的成型;(3)机械加工;(4)修饰;(5)装配。
2、模塑成型的种类(1)注塑成型;(2)压制成型;(3)压铸成型;(4)中空吹塑成型;(5)挤出成型;(6)喷射成型等.二、四大工业材料1、钢材2、木材(纤维素类)3、水泥(硅酸盐类)4、塑料三、塑料与金属材料相比较,有以下的优点1、质轻(密度小)2、比强度、比刚度高3、耐腐蚀4、绝缘性好5、易着色6、制品可加工成任意形状(易成型加工)7、生产率高,价格低,应用广泛四、塑料模塑成型技术的发展动向(一)要加深工艺理论的研究;(二)要实现成型设备和模具生产的高效率、自动化;(三)模具要向超大型、微型、高精度方向发展;(四)要发展高寿命和简易经济模具;(五)模具制造先进设备及先进工艺;(六)要实现模具的标准化与专业化生产;(七)要发展和应用模具CAD/CAM/CAE技术。
CAD-——-——- Computer Aided Design (计算机辅助设计)CAM-—----—Computer Aided Manufacture (计算机辅助制造)CAE—-—-—-—Computer Aided Engineering (计算机辅助工程)五、模具的定义用特定的外形去成型具有特定形状、尺寸、大小的制品的工具称之为模具。
六、模具工业在国民经济中的重要性1、模具是“效益放大器”。
2、美国工业界认为:模具工业是美国工业的基石。
3、日本:模具是促进社会繁荣富裕的动力。
注塑工艺与模具设计
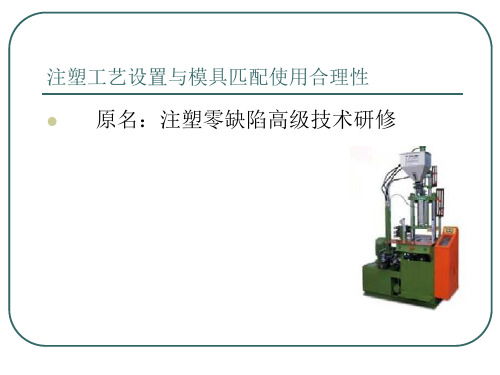
当塑料进入行腔后会形成流动波前,在中 心地方旳流动快,在接近模壁旳地方流动 慢。因为流动速度不同产生剪切,从而造 成分子排向。
注塑工艺基础
进料点
流动性快
模具冷料 井
先冷却, 流动 性慢
注塑工艺基础
压力怎样影响产品构造及外观 压力会使分子紧靠在一起,收缩性变小,
45P
黄色
45P
白色
45P
红色
45P
透明LDPE
温度范围 成型压力(KGF/CM) (℃) 总压 一次压 二次压
155-180 80-100 35-55 5-30 155-180 80-100 35-55 5-30 155-180 80-100 35-55 5-30
155-180 80-100 35-55 5-30 155-180 80-100 35-55 5-30 155-180 80-100 35-55 5-30 155-185 80-100 35-55 5-30 155-185 80-100 40-60 10-35 155-180 80-100 40-60 10-35 150-180 80-100 40-60 10-35 140-175 80-100 40-60 10-35 140-175 80-100 40-60 10-35 155-185 80-100 35-55 5-30 150-180 80-100 30-50 10-30 140-175 80-100 30-50 10-30 150-180 80-100 30-50 10-30 125-150 80-100 10-35 0-10
处理缩孔及缩水问题需对胶料加以烘烤,根据 实际情况设定温度至少烘烤2个小时以上,料斗 最佳保持饱满;适量加大背压,让螺杆释放出 多出旳空气;
塑料成型工艺与注射模具设计 (4)

2
相关知识点
(2)嵌件 的预热
为了满足装配和使用强度的要求,塑件内经常要嵌入金属嵌 件。由于金属和塑料收缩率相差较大,因而在塑件冷却时,嵌 件周围产生较大的内应力,导致嵌件周围塑料层强度下降和出 现裂纹。因此,成型前应对金属嵌件进行预热,以降低它与塑 料熔体的温差,减小内应力。
2
相关知识点
(3)料筒 的清洗
2
相关知识点
螺杆式注射机注射成型工作循环,如图4-3所示。
图4-3
2
相关知识点
与柱塞式注射机注射成型相比 较,螺杆式注射机注射成型由于 螺杆的剪切作用,塑料混合均匀, 塑化效果好,改善了成型工艺, 提高了塑件质量。同时扩大了注 射成型塑料品种的范围和最大注 射量。因此,对于热敏性和流动 性差的塑料和大、中型塑件,一 般可用移动螺杆式注射机成型。
2
相关知识点
当残余压力为正值时,脱模比较困 难,塑件容易被刮伤甚至破裂;当残 余压力为负值时,塑件表面易出现凹 陷或内部有真空泡。因此,只有残余 庄力接近为零时.脱模较顺利,而且 可获得较满意的塑件。 ◆塑件的冷却速率应适中,冷却速率 过快或模温不均匀,都会导致冷却不 均和收缩的不一致,使塑件内部产生 内应力,出现翘曲变形。
2
相关知识点
完整的注射过程包括加料、塑化、 注射、保压、冷却和脱模等几个阶段。 (1)加料 将粉状或粒状的塑料加入注射机料 斗,由柱塞或螺杆带入料筒内加热。 (2)塑化 成型塑料在注射机料筒内经加热、 压实以及混料等作用,由松散的粉状 颗粒或粒状的固态转变为连续的均匀 塑化熔体的过程。对塑化的要求是: 在规定的时间内塑化出足够数量的熔 融塑料;塑料熔体进入模具型腔内之 前应达到规定的成型温度,而且熔体 各点温度应均匀一致,避免局部温度 过低或温度过高。
塑料成型工艺与注射模具设计 (1)

1
了解塑料与塑料模 具工业的发展现状
塑料成型工艺与注射模具设计
学习情境一
项目内容 塑料与塑料模具工业的发展现状
学习目标
了解塑料工业的发展现状 了解塑料成型模具的发展趋势
了解《塑件成型方案拟定与 模具设计》课程地位、学习 目标、学习方法
学习情境一
能力目标
通过在互联网、图书馆查阅资 料,撰写有关塑料与塑料模具 工业发展现状的调研报告。
现代模具工业有“不衰亡工业” 之称,美国工业界认为“模具 工业是工业的基石”,日本则 认为“模具是人类进入富裕社 会的原动力”还有人认为模具 是“效益放大器”,用模具生 产出的产品价值,往往是模具 价值的几十倍,上千倍。
Hale Waihona Puke 由于模具对社会生产和国民经济 的巨大推动作用和自身的高附加 值,世界模具市场发展较快,当 前全球模具工业的产值已经达到 600亿~650亿美元,是机床工 业产值的两倍。 我国塑料模具从起步到现在,水 平有了较大提高。在大型模具方 面已能生产48英寸大屏幕彩电塑 壳注射模具、6.5Kg 大容量洗衣 机全套塑料模具以及汽车保险杠 和整体仪表板等塑料模具
以生产家用电器的企业为代表, 陆续引进了相当数量的 CAD/CAM系统,如美国EDS的 UGⅡ、美国CV公司的CADS5、 英国Deltacam公司的DOCT5、 日本HZS公司的CRADE、以色 列公司的Cimatron、美国 Parametric Technology公司的 Pro/Emgineer、美国AC-Tech 公司的C-Mold及澳大利亚 Moldflow公司的MPA塑模分析 软件等。
目前,中国塑料制品行业规 模以上企业近万家,其中24 家企业的年销售收入超过10 亿元。从地区分布来看,广 东、浙江、江苏3省占领了塑 料制品产量的“半壁江山”。
注塑模具设计说明书
注塑模具设计说明书注塑模具设计说明书1.引言本文档旨在为注塑模具的设计提供详细指导和说明。
注塑模具是在注塑成型过程中必备的工具,准确的设计和制造对于生产高质量的注塑制品至关重要。
2.模具设计概述2.1 模具类型及用途2.2 模具材料选择2.3 模具尺寸和形状设定2.4 模具结构设计2.5 模具配件选择与设计3.模具主要零部件设计3.1 模具基板设计3.2 模具腔体与芯腔设计3.3 模具导向系统设计3.4 模具冷却系统设计3.5 模具强度校核3.6 模具表面处理4.注塑模具设计考虑因素4.1 塑料材料特性4.2 注塑工艺要求4.3 产品设计要求4.4 模具制造成本和周期5.模具设计流程5.1 需求分析与规划5.2 初始设计与草图5.3 详细设计与模拟分析5.4 模具制造与加工5.5 模具调试与试模5.6 模具验收和交付6.模具设计的注意事项6.1 常见设计错误与避免方法6.2 模具装配和拆卸注意事项6.3 模具维护与保养7.附件本文档涉及以下附件:- 附件1:注塑模具设计草图- 附件2:注塑模具3D模型文件- 附件3:模具设计分析报告8.法律名词及注释本文所涉及的法律名词及其相应注释如下:- 法律名词1:注塑成型工艺注释:指利用注塑设备将塑料加热并溶化,然后将熔融塑料注入模具腔中,并通过冷却固化成型的工艺。
- 法律名词2:模具基板注释:指注塑模具的基础组件,用于固定和支撑模具的其他部件,具有足够的强度和稳定性。
- 法律名词3:模具腔体与芯腔注释:模具腔体为模具中用于成型制品外形的部分,芯腔为模具中用于成型制品内部结构的部分。
9.结束语本文档详细介绍了注塑模具设计的各个方面。
通过遵循本文档中的指导和说明,设计师可以制定出高质量的注塑模具并实现优秀的注塑成型工艺。
模具设计与制造及注塑成型生产工艺流程
模具设计与制造及注塑成型生产工艺流程下载提示:该文档是本店铺精心编制而成的,希望大家下载后,能够帮助大家解决实际问题。
文档下载后可定制修改,请根据实际需要进行调整和使用,谢谢!本店铺为大家提供各种类型的实用资料,如教育随笔、日记赏析、句子摘抄、古诗大全、经典美文、话题作文、工作总结、词语解析、文案摘录、其他资料等等,想了解不同资料格式和写法,敬请关注!Download tips: This document is carefully compiled by this editor. I hope that after you download it, it can help you solve practical problems. The document can be customized and modified after downloading, please adjust and use it according to actual needs, thank you! In addition, this shop provides you with various types of practical materials, such as educational essays, diary appreciation, sentence excerpts, ancient poems, classic articles, topic composition, work summary, word parsing, copy excerpts, other materials and so on, want to know different data formats and writing methods, please pay attention!1. 模具设计。
在注塑成型生产过程中,模具设计是至关重要的一环。
塑料成型工艺和模具设计课程设计说明书
塑料成型工艺和模具设计课程设计说明书设计课题_________________________________________ 系部现代制造工程系专业模具设计和制造班级学生姓名指导教师2012 年 5 月18 日塑料成型工艺和模具设计任务书_现代制造工程_系_模具设计和制造_专业__________班姓名__________一、设计课题_________________________________________二、设计工作自_2012_年5月_14_日起至_2012_年5月_18_日三、设计进行地点:___CAD/CAM机房______________四、课程设计的内容要求:1.对教师指定的塑料件进行工艺设计,包括塑件成型工艺分析、分型面及浇注系统的确定、塑料模具设计的方案论证、主要零部件的设计计算、注射机有关参数的校核;2.完成一套塑料模的设计,包括确定模具结构尺寸、绘制该塑料模的总装配图和主要零件图;3. 编写设计计算说明书(20~25页)。
第一章塑件工艺分析1、塑件的原始材料分析该材料为丙烯腈-丁二烯-苯乙烯共聚物(ABS塑料)ABS是由丙烯腈、丁二烯和苯乙烯三种化学单体合成,收缩率为0.3%~0.8% 。
ABS无毒、无味、呈微黄色,成型的塑件有较好的光泽。
从使用性能上看,该塑料具有极好的抗冲击强度,有良好的机械强度和一定的耐磨性、耐寒性、耐油性、耐水性、化学稳定性和电气性能。
从成型性能上看,该塑料在升温时粘度增高,所以成型压力较高,故塑件上的脱模斜度宜稍大;ABS易吸水,成型加工前应进行干燥处理;ABS易产生熔接痕,模具设计时应注意尽量减少浇注系统对料流的阻力;在正常的成型条件下,壁厚、熔料温度对收缩率影响极小。
在要求塑件精度高时,模具温度可控制在50~60℃,而在强调塑件光泽和耐热时,模具温度应控制在60~80℃。
2、塑件的结构、尺寸精度及表面质量分析1、结构分析从零件图上分析,该零件总体形状为回转体,在一个直径为38mm高为17mm的圆柱中间有一个直径为16mm高为11mm和一个直径为19mm高为6mm的台阶孔,然后留壁厚为 1.5mm。
注塑模具工艺文件
版本号V1.0注塑成型工艺编制:唐2021年2月目录1.工艺流程.......................................................3.1.1填充阶段1.2保压阶段1.3冷却阶段1.4脱模阶段2.工艺参数.......................................................6.2.1注塑压力2.2注塑时间2.3注塑温度2.4保压压力、时间2.5螺杆背压3.注塑机...........................................................7.3.1卧式注塑机3.2立式注塑机3.3双色注塑机4.注塑模具......................................................10.4.1模具类型4.2注塑模具基本结构1.工艺流程注塑成型工艺过程主要包括合模——填充——保压——冷却——开模——脱模等6个阶段。
这6个阶段直接决定着制品的成型质量,而且这6个阶段是一个完整的连续过程。
1.1填充阶段填充是整个注塑循环过程中的第一步,时间从模具闭合开始注塑算起,到模具型腔填充到大约95%为止。
理论上,填充时间越短,成型效率越高;但是在实际生产中,成型时间(或注塑速度)要受到很多条件的制约。
(1)高速填充。
高速填充时剪切率较高,塑料由于剪切变稀的作用而存在粘度下降的情形,使整体流动阻力降低;局部的粘滞加热影响也会使固化层厚度变薄。
因此在流动控制阶段,填充行为往往取决于待填充的体积大小。
即在流动控制阶段,由于高速填充,熔体的剪切变稀效果往往很大,而薄壁的冷却作用并不明显,于是速率的效用占了上风。
(2)低速填充。
热传导控制低速填充时,剪切率较低,局部粘度较高,流动阻力较大。
由于热塑料补充速率较慢,流动较为缓慢,使热传导效应较为明显,热量迅速为冷模壁带走。
加上较少量的粘滞加热现象,固化层厚度较厚,又进一步增加壁部较薄处的流动阻力。
- 1、下载文档前请自行甄别文档内容的完整性,平台不提供额外的编辑、内容补充、找答案等附加服务。
- 2、"仅部分预览"的文档,不可在线预览部分如存在完整性等问题,可反馈申请退款(可完整预览的文档不适用该条件!)。
- 3、如文档侵犯您的权益,请联系客服反馈,我们会尽快为您处理(人工客服工作时间:9:00-18:30)。
1最小壁厚满足条件:具有足够的强度;脱模时能经受脱模机构的冲击还和震荡;装配时能承受紧固力。
壁厚过小,会造成填充阻力增大;壁厚过大,不仅浪费材料,还延长冷却时间。
一般而言,在满足适应条件的前提下,制件壁厚尽可能取小些。
2壁厚设计的另一基本原则:同一塑件壁厚尽可能均匀一致。
否则会因冷却和固化速率不均产生附加内应力,引起翘曲变形,热塑性塑料会在壁厚处产生锁孔;热固性塑料则会因未充分固化而鼓包或因交联度不一致而造成性能差异。
为消除壁厚不均匀,设计时可考虑将壁厚部分挖空或在壁面交界处采用适当的半径过度以缓解厚薄部分的突然变化。
设置加强筋的目的:在不增加壁厚的情况下,达到提高制件的刚强度,避免翘曲变形。
沿着料流方向的加强筋还能改善成型时的塑料熔体的流动性,避免气泡、缩孔和凹陷等缺陷的形成。
3加强筋设计时注意:加强筋不宜过厚,b=(0.4~0.8)t,否则其对应壁上会容易产生凹陷;加强筋设计不应过高,h≤3t,否则,在较大弯矩或冲击负荷作用下受力破坏;加强筋必须有足够的斜度,加强筋的顶部为圆角,底部也应呈圆弧过渡。
加强筋布置应考虑:加强筋的方向尽量与熔体充模方向一致,以避免熔体流动干扰、影响成型质量;加强筋的设置应避免或减少塑料局部集中,否则会产生缩孔、气泡等缺陷。
除了采用加强筋外,对于薄壁容器或壳类件可以适当改变起结构或形状,也能达到提高其刚强度和防止变形的目的。
4圆角:带有尖角的塑件在成型时,往往会在尖角处产生局部应力集中,在受力或冲击震动下会发生开裂或破裂。
采用圆弧过渡首先可增加塑件的美观程度,其次可增加塑件的强度,也大大改善充模流动特性。
另外,塑件的圆角对应与模具也呈圆角,这样既增加模具的坚固性,在一定程度上也减少模具热处理时因应力集中而导致开裂情况的出现。
理想的内圆角半径为壁厚的1/3。
通常,塑件内壁圆角半径是壁厚的一半,外壁圆角半径为壁厚的1.5倍,一般圆角半径不小于0.5mm,壁厚不等的两壁转角可按平均壁厚确定内、外圆角半径。
5分型面选择原则:分型面应选在塑件外形最大轮廓处;应尽量减少塑件在分型面上的投影面积,注塑机都规定其相应模具所允许的最大成型面积及额定锁模力,注塑成型过程中,当塑件(包括浇注系统)在分型面上的投影面积超过允许的最大成型面积时,会出现涨模溢料现象,这时注塑成型所需的合模力也会超出额定锁模力;考虑排气效果;保证塑件的形状与尺寸精度要求;满足塑件的外观质量要求;应尽可能使塑件在开模后留在动模一侧;对侧向抽芯的影响,应以浅的侧向凹孔或短的侧向凸台作为抽芯方向,将较深的凹孔或较高的凸台放置在开模方向,并尽可能把侧向抽芯机构放置在动模一侧;便于模具的加工制造6浇注系统设计原则:压力损失小;温差小;主流道设计:喷嘴窝球面半径SR=喷嘴球面半径+(0.5~1)mm分流道设计:分流道的长度要尽可能短,且少弯折,便于注塑成型过程中最经济地使用原料和注塑机的能耗,减少压力损失和热量损失,较长的分流道还需要在末端设置冷料穴。
分流道布置形式应遵循:排列紧凑,缩小模具版面尺寸;流程尽量短,锁模力力求平衡。
7浇口的设计:直接浇口:塑料熔体直接由主流道进入型腔,因而具有流动阻力小,料流速率快及补缩时间长的特点,但注塑压力直接作用在塑件上,容易在进塑处产生较大的残余应力而导致塑件翘曲变形,浇口痕迹也较明显。
大都用于注塑成型大型壁厚,长流程、深型腔的塑件以及一些高黏度塑料,多用与多型腔模具。
侧浇口:用于中小型塑件的多型腔模具,且对各种塑料的成型适应性均较强;但有浇口痕迹存在,会形成熔接痕、缩孔、气孔等缺陷,且注射压力损失大,多深型腔塑件排气不便。
浇口长度越长,浇口上的压力降越大;浇口的厚度越厚,浇口封闭时间越长;浇口宽度越宽,流动阻力越小。
扇形浇口:采用扇形浇口,可使塑料熔体在宽度方向上的流动得到更均匀的分配,塑件的内应力较小;且对消除浇口附近的缺陷有较好的效果,因此适用于成型薄片状塑件及扁平塑件,但浇口痕迹较明显,且去除较困难。
环形浇口:成型圆筒件,开设在塑件外侧。
塑料熔体在充模时进料均匀,各处料流速率大致相同,模腔内空气容易排出,避免了侧浇口容易在塑件上产生熔接痕,但浇口去除较难,浇口痕迹明显。
盘形浇口:类似于环形浇口,浇口开设在塑件内侧。
轮辐浇口:浇口尺寸与侧浇口类似,凝料易去除用料少,塑件容易产生多条熔接痕降低塑件的强度。
点浇口:浇口前后两端存在较大的压力差,能有效地增大塑料熔体的剪切速率并产生较大的剪切热;从而使熔体表面黏度下降,流动性增加,利于填充。
有利于成型薄壁塑件以及表观黏度随剪切速率变化敏感改变的塑料,不利于成型了流动性差及热敏性塑料,也不利于成型平薄易变形及形状复杂的塑件。
采用点浇口的模具,已取得浇注系统的平衡,也有利于自动化操作,但压力损失大,浇口凝料脱模需在定模部分另加一个分型面,塑件浇口残留痕迹小,但收缩大、易变形。
潜伏浇口:由点浇口演变而来。
8浇口位置的选择:尽量缩短流动距离;浇口应开设在塑件壁最厚处;尽量减少或避免熔接痕;应有利于型腔气体排出;考虑分子定向的影响;避免产生喷射和蠕动;不在塑件承受弯曲或冲击载荷的部位设置浇口;浇口位置选择注意塑件外观质量。
浇注系统的平衡:布局与分流道的平衡、浇口平衡(自然平衡、人工平衡)。
9冷料穴:一般开设在主流道对面的动模板上。
拉料杆:Z字形为最常见。
倒锥形、环形槽形适用于弹性较好的软质塑料;球头、菌形头适用于推板脱模,弹性较好的塑料;分流锥形适用各种塑料,适用于中间有空是塑件而又采用直接浇口或抓形浇口形式10合模导向机构:保证动、定模或上、下模合模时,正确定位和导向的装置。
具体作用:导向作用,合模时,首先是导向零件接触,引导动、定模或上、下模准确闭合,避免型芯先进入型腔造成零件损坏。
定位作用,模具闭合后,保证动、定模位置正确,保证型腔的形状和尺寸精度;导向机构在模具装配过程中也起了定位作用,便于装配和调整承受一定的侧向压力,塑料熔体在充型过程中可能产生单向侧压力,或者由于成型设备精度低的影响,是导柱承受一定的侧向压力,一保证模具的正常工作。
若侧压力很大时,不能单靠导柱来承担,需增设锥面定位机构。
推杆、推管、推板的适用范围推杆推出机构由于设置推杆位置的自由度较大,因而推杆推出机构是最常用的推出机构。
不宜用在脱模力大的筒形和箱型塑件的脱模。
推管推出机构中心有孔的圆形套类零件,通常使用推管推出机构。
图4-77(课本p95)所示为推管推出机构的结构,(a)是型芯固定在模具底板上的形式,这种结构型芯较长,常用在推出距离不大的场合;(b)用方销将型芯固定在动模板上,推管在方销的位置处开槽,推出时让开方销,推管与方销的配合采用H8/f7或H8/f8;(c)为推管在模板内滑动的形式,这种结构适宜模板厚度较大的模具,型芯和推管都较短。
推板推出机构推板推出机构主要适用于塑件内孔为圆形或其他简单形状的场合。
4.8 侧向分型抽芯机构设计4.8.3斜导柱侧向分型抽芯机构由图4-103(课本107页)可看出,斜导柱侧向分型抽芯机构主要由斜导柱、楔紧块、侧型腔或型芯滑块、导滑槽、侧型芯以及定距限位装置等组成。
4.8.3.5斜导柱侧向分型抽芯机构的结构形式安装形式(课本P115——118)4.8.5弯销侧向分型抽芯机构弯销与斜导柱的区别弯销侧向分型抽芯机构的工作原理和斜导柱侧向分型抽芯机构相似,所不同的是在结构上以矩形截面的弯销代替了斜导柱,因此弯销侧向分型抽芯机构仍让离不开滑块的导滑,注塑时侧型芯的锁紧和侧抽芯结束时滑块的定位这三大要素。
4.9温度调节系统设计模具温度对塑件成型的影响(1)模具温度对塑件质量的影响模温过低,熔体流动性差,塑件轮廓不清晰,甚至充不满型腔或形成熔接痕,塑件表面无光泽,缺陷多,力学性能降低。
热固性塑料因固化程度不足,造成塑件的物理、化学和力学性能降低;热塑性塑料因充模速率不高,造成塑件内应力增大,易引起翘曲变形或应力开裂。
模温过高,成型收缩率大,脱模和脱模后塑件变形大,并易造成溢料和粘模。
热固性塑料因“过熟”,会导致变色发脆、强度低等缺陷。
模具温度不均匀,型芯和型腔温度差过大、塑件收缩不均匀,导致塑件翘曲变形,影响塑件的形状及尺寸精度。
模具温度波动对塑件的收缩率、尺寸稳定性、力学性能、变形、应力开裂和表面质量等均有影响。
(2)模具温度对模塑周期的影响塑料注射成型过程中,注射时间约占成型周期的5%,冷却时间约占80%,推出(脱模)时间约占15%。
由此可见,缩短模塑周期关键在于缩短冷却固化时间,可通过调节塑料和模具的温差。
因而在保证塑件质量和成型工艺顺利进行的前提下,降低模具温度有利于缩短冷却时间,也就是缩短模塑周期,从而提高塑料成型的生产效率。
冷却系统设计冷却系统设计原则①冷却水道应尽量多、截面尺寸应尽量大②冷却水道至型腔表面距离应尽量相等③浇口处加强冷却④冷却水道出、入口温差应尽量小此外,冷却水道的设计还必须尽量避免接近塑件的熔接部位,以避免产生熔接痕,降低塑件强度。
4.10热流道注塑模具热流道模具按使流道内塑料保持熔融状态的方法分为绝热流道注塑模和加热流道注塑模两种。
(1)绝热流道绝热流道注塑模将主流道和分流道截面尺寸设计的很大,利用塑料与流道壁接触处形成冷凝层的绝热保温作用,使流道中心部位的塑料始终保持熔融流动状态,在注射压力作用下,熔融料通过流道顺利的进入型腔,从而满足连续注射的要求。
①绝热主流道绝热主流道又称井式喷嘴,是结构最简单的绝热流道,适用于单型腔注塑模。
②绝热分流道绝热分流道又称多型腔绝热流道,有直接浇口式和点浇口式两种类型。
(2)加热流道加热流道是在流道内或留到附近设置加热器,利用加热的方法使注射机喷嘴到浇口之间的浇注系统处于高温状态,从而让浇注系统内的塑料在生产过程中一直保持熔融状态。
①延伸喷嘴延伸喷嘴是一种最简单的加热流道,它是将普通喷嘴加长以后能与模具上浇口部位直接接触的一种特别喷嘴,其自身也可安装加热器,以便补偿喷嘴延长之后的散热量,或在特殊要求下使其温度高于料筒温度。
延伸喷嘴只适于单腔模具结构,②多型腔加热流道这类模具的结构形式很多,但大概可归纳为外加热式和内加热式两大类③阀式浇口热流道使用热流道注塑模成型黏度很低的塑料时,为了避免产生流延和拉丝现象,可采用阀式浇口。
热流道系统组成热流道板:其主要任务是恒温地将熔体从主流道送入各个单独喷嘴,在熔体传送过程中熔体的压力降尽可能减小,并不允许材料降解。
通常热流道板的形式有:一字型,H型,Y型,十字型。
喷嘴:将熔体从热流道板送入模具型腔,带有开放式,针阀式等喷嘴。
加热元件:保证流道内熔体一直处于熔融状态,常用有加热棒,加热圈,管式加热器及螺旋式加热器等。
温控器:精确控制温度,常用有通断式,比例控制,新型智能化控制器。