硅烷偶联剂的使用方法
偶联剂的使用方法

偶联剂的使用方法
1、使用我公司DB-550对粉体进行表面处理,效果比较好。
2、使用悬式搅拌器,在搅拌过程中将温度升到80度左右,将粉体干燥后,自然冷却
3、采用喷雾式加入偶联剂。
4、偶联剂用水稀释,稀释比例为整个粉体质量的1%-5%。
硅烷偶联剂的使用方法
⑴表面预处理法将硅烷偶联剂配成0.5~1%浓度的稀溶液,使用时只需在清洁的被粘表面涂上薄薄的一层,干燥后即可上胶。
所用溶剂多为水、醇、或水醇混合物,并以不含氟离子的水及价廉无毒的乙醇、异丙醇为宜。
除氨烃基硅烷外,由其它硅烷偶联剂配制的溶液均需加入醋酸作水解催化剂,并将pH值调至3.5~5.5。
长链烷基及苯基硅烷由于稳定性较差,不宜配成水溶液使用。
氯硅烷及乙酰氧基硅烷水解过程中伴随有严重的缩合反应,也不宜配成水溶液或水醇溶液使用,而多配成醇溶液使用。
水溶性较差的硅烷偶联剂,可先加入0.1~0.2%(质量分数)的非离子型表面活性剂,然后再加水加工成水乳液使用。
⑵迁移法将硅烷偶联剂直接加入到胶粘剂组分中,一般加入量为基体树脂量的1~5%。
涂胶后依靠分子的扩散作用,偶联剂分子迁移到粘接界面处产生偶联作用。
对于需要固化的胶粘剂,涂胶后需放置一段时间再进行固化,以使偶联剂完成迁移过程,方能获得较好的效果。
实际使用时,偶联剂常常在表面形成一个沉积层,但真正起作用的只是单分子层,因此,偶联剂用量不必过多。
硅烷偶联剂处理粉体工艺

硅烷偶联剂处理粉体工艺主要包括以下步骤:
1.将硅烷偶联剂加入到适当的稀释液和助剂中,混合配成处理液。
2.将需要处理的粉体(如石英粉、二氧化硅粉体等)加入到反应釜或反应罐中。
3.将处理液喷洒到粉体上,并进行加热反应或浸泡。
4.反应一定时间后,将粉体进行脱水处理,如使用高速搅拌、加热烘干等方法。
通过硅烷偶联剂处理,可以改善粉体的表面性能,提高其与高聚物或树脂等材料的相容性和亲和力,使其更均匀地分散在基体中,从而提高填充体系的强度、模量等性能。
这种处理工艺在塑料、橡胶、电线电缆、医药、涂料、油漆、日用化工等行业中得到广泛应用。
以上信息仅供参考,具体的处理工艺可能因粉体种类、硅烷偶联剂种类和工艺条件等因素而有所不同。
建议在实际应用中,根据具体情况选择合适的处理工艺和参数。
kh560硅烷偶联剂使用方法
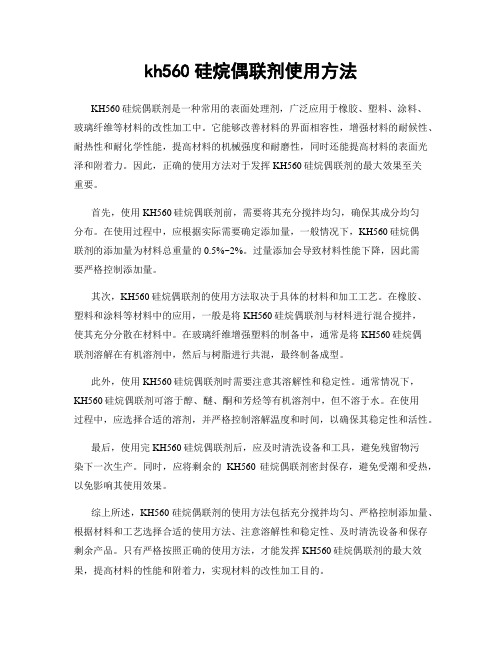
kh560硅烷偶联剂使用方法KH560硅烷偶联剂是一种常用的表面处理剂,广泛应用于橡胶、塑料、涂料、玻璃纤维等材料的改性加工中。
它能够改善材料的界面相容性,增强材料的耐候性、耐热性和耐化学性能,提高材料的机械强度和耐磨性,同时还能提高材料的表面光泽和附着力。
因此,正确的使用方法对于发挥KH560硅烷偶联剂的最大效果至关重要。
首先,使用KH560硅烷偶联剂前,需要将其充分搅拌均匀,确保其成分均匀分布。
在使用过程中,应根据实际需要确定添加量,一般情况下,KH560硅烷偶联剂的添加量为材料总重量的0.5%~2%。
过量添加会导致材料性能下降,因此需要严格控制添加量。
其次,KH560硅烷偶联剂的使用方法取决于具体的材料和加工工艺。
在橡胶、塑料和涂料等材料中的应用,一般是将KH560硅烷偶联剂与材料进行混合搅拌,使其充分分散在材料中。
在玻璃纤维增强塑料的制备中,通常是将KH560硅烷偶联剂溶解在有机溶剂中,然后与树脂进行共混,最终制备成型。
此外,使用KH560硅烷偶联剂时需要注意其溶解性和稳定性。
通常情况下,KH560硅烷偶联剂可溶于醇、醚、酮和芳烃等有机溶剂中,但不溶于水。
在使用过程中,应选择合适的溶剂,并严格控制溶解温度和时间,以确保其稳定性和活性。
最后,使用完KH560硅烷偶联剂后,应及时清洗设备和工具,避免残留物污染下一次生产。
同时,应将剩余的KH560硅烷偶联剂密封保存,避免受潮和受热,以免影响其使用效果。
综上所述,KH560硅烷偶联剂的使用方法包括充分搅拌均匀、严格控制添加量、根据材料和工艺选择合适的使用方法、注意溶解性和稳定性、及时清洗设备和保存剩余产品。
只有严格按照正确的使用方法,才能发挥KH560硅烷偶联剂的最大效果,提高材料的性能和附着力,实现材料的改性加工目的。
硅烷偶联剂使用方法
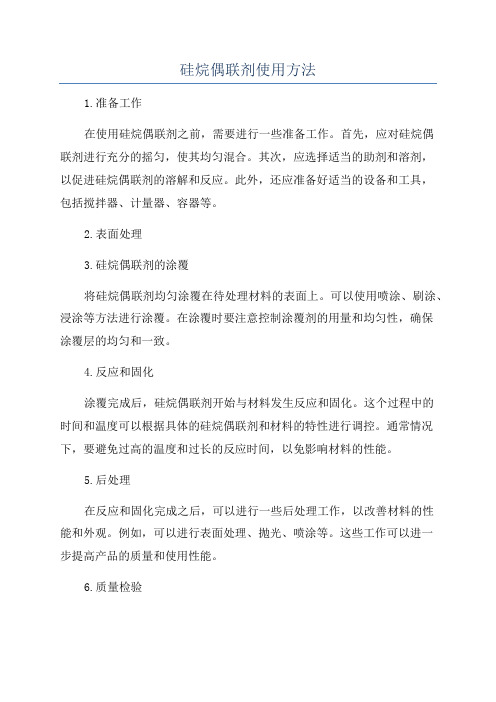
硅烷偶联剂使用方法
1.准备工作
在使用硅烷偶联剂之前,需要进行一些准备工作。
首先,应对硅烷偶
联剂进行充分的摇匀,使其均匀混合。
其次,应选择适当的助剂和溶剂,
以促进硅烷偶联剂的溶解和反应。
此外,还应准备好适当的设备和工具,
包括搅拌器、计量器、容器等。
2.表面处理
3.硅烷偶联剂的涂覆
将硅烷偶联剂均匀涂覆在待处理材料的表面上。
可以使用喷涂、刷涂、浸涂等方法进行涂覆。
在涂覆时要注意控制涂覆剂的用量和均匀性,确保
涂覆层的均匀和一致。
4.反应和固化
涂覆完成后,硅烷偶联剂开始与材料发生反应和固化。
这个过程中的
时间和温度可以根据具体的硅烷偶联剂和材料的特性进行调控。
通常情况下,要避免过高的温度和过长的反应时间,以免影响材料的性能。
5.后处理
在反应和固化完成之后,可以进行一些后处理工作,以改善材料的性
能和外观。
例如,可以进行表面处理、抛光、喷涂等。
这些工作可以进一
步提高产品的质量和使用性能。
6.质量检验
最后,应对材料进行质量检验,以确保产品符合要求。
可以使用物理
性能测试、化学分析、显微镜观察等方法进行检验。
根据检验结果进行调
整和改进,以提高产品的质量和使用效果。
总结:
硅烷偶联剂的使用方法包括准备工作、表面处理、涂覆、反应和固化、后处理以及质量检验等。
通过正确操作和控制,可以提高材料的性能和产
品质量。
然而,不同的硅烷偶联剂和材料可能有不同的要求和操作方式,
因此在使用之前应根据具体情况进行试验和调整。
硅烷偶联剂的使用说明
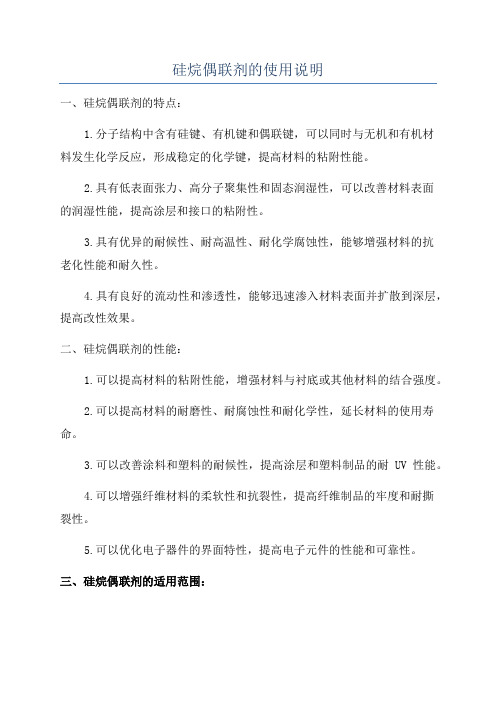
硅烷偶联剂的使用说明一、硅烷偶联剂的特点:1.分子结构中含有硅键、有机键和偶联键,可以同时与无机和有机材料发生化学反应,形成稳定的化学键,提高材料的粘附性能。
2.具有低表面张力、高分子聚集性和固态润湿性,可以改善材料表面的润湿性能,提高涂层和接口的粘附性。
3.具有优异的耐候性、耐高温性、耐化学腐蚀性,能够增强材料的抗老化性能和耐久性。
4.具有良好的流动性和渗透性,能够迅速渗入材料表面并扩散到深层,提高改性效果。
二、硅烷偶联剂的性能:1.可以提高材料的粘附性能,增强材料与衬底或其他材料的结合强度。
2.可以提高材料的耐磨性、耐腐蚀性和耐化学性,延长材料的使用寿命。
3.可以改善涂料和塑料的耐候性,提高涂层和塑料制品的耐UV性能。
4.可以增强纤维材料的柔软性和抗裂性,提高纤维制品的牢度和耐撕裂性。
5.可以优化电子器件的界面特性,提高电子元件的性能和可靠性。
三、硅烷偶联剂的适用范围:1.涂料方面:可用于增强涂料的附着力,改善涂膜的耐候性和耐化学性。
适用于金属涂料、木器涂料、玻璃涂料等各种涂料体系。
2.塑料方面:可用于增强塑料制品的附着力和耐候性,改善塑料制品的表面光洁度和耐划伤性。
适用于聚丙烯、聚氯乙烯、聚酰胺等常见塑料材料。
3.橡胶方面:可用于提高橡胶制品的耐磨性和耐老化性,改善橡胶制品的硬度和强度。
适用于天然橡胶、丁苯橡胶、氯丁橡胶等各种橡胶材料。
4.纤维方面:可用于提高纤维制品的柔软性和抗裂性,改善纤维制品的牢度和耐洗涤性。
适用于棉纤维、涤纶纤维、尼龙纤维等各种纤维材料。
5.电子器件方面:可用于优化电子元件的界面特性,提高电子元件的性能和可靠性。
适用于半导体材料、玻璃基板等电子器件的制造与改性。
四、硅烷偶联剂的使用注意事项:1.在使用硅烷偶联剂前,请先进行必要的实验和测试,以确定最佳用量和适用范围。
2.在使用硅烷偶联剂时,请使用适当的防护措施,避免接触皮肤和眼睛,并保持良好的通风环境。
3.硅烷偶联剂一般为液体或溶液,应储存在密封的容器中,在避光、低温干燥的环境中保存。
硅烷偶联剂使用方法
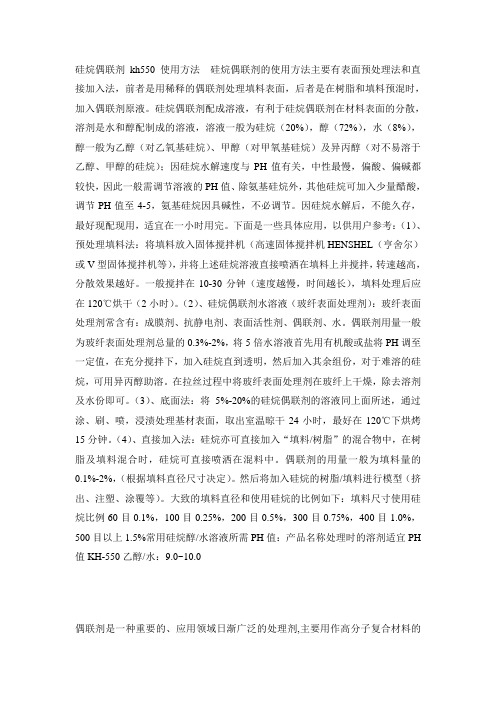
硅烷偶联剂kh550使用方法硅烷偶联剂的使用方法主要有表面预处理法和直接加入法,前者是用稀释的偶联剂处理填料表面,后者是在树脂和填料预混时,加入偶联剂原液。
硅烷偶联剂配成溶液,有利于硅烷偶联剂在材料表面的分散,溶剂是水和醇配制成的溶液,溶液一般为硅烷(20%),醇(72%),水(8%),醇一般为乙醇(对乙氧基硅烷)、甲醇(对甲氧基硅烷)及异丙醇(对不易溶于乙醇、甲醇的硅烷);因硅烷水解速度与PH值有关,中性最慢,偏酸、偏碱都较快,因此一般需调节溶液的PH值、除氨基硅烷外,其他硅烷可加入少量醋酸,调节PH值至4-5,氨基硅烷因具碱性,不必调节。
因硅烷水解后,不能久存,最好现配现用,适宜在一小时用完。
下面是一些具体应用,以供用户参考:(1)、预处理填料法:将填料放入固体搅拌机(高速固体搅拌机HENSHEL(亨舍尔)或V型固体搅拌机等),并将上述硅烷溶液直接喷洒在填料上并搅拌,转速越高,分散效果越好。
一般搅拌在10-30分钟(速度越慢,时间越长),填料处理后应在120℃烘干(2小时)。
(2)、硅烷偶联剂水溶液(玻纤表面处理剂):玻纤表面处理剂常含有:成膜剂、抗静电剂、表面活性剂、偶联剂、水。
偶联剂用量一般为玻纤表面处理剂总量的0.3%-2%,将5倍水溶液首先用有机酸或盐将PH调至一定值,在充分搅拌下,加入硅烷直到透明,然后加入其余组份,对于难溶的硅烷,可用异丙醇助溶。
在拉丝过程中将玻纤表面处理剂在玻纤上干燥,除去溶剂及水份即可。
(3)、底面法:将5%-20%的硅烷偶联剂的溶液同上面所述,通过涂、刷、喷,浸渍处理基材表面,取出室温晾干24小时,最好在120℃下烘烤15分钟。
(4)、直接加入法:硅烷亦可直接加入“填料/树脂”的混合物中,在树脂及填料混合时,硅烷可直接喷洒在混料中。
偶联剂的用量一般为填料量的0.1%-2%,(根据填料直径尺寸决定)。
然后将加入硅烷的树脂/填料进行模型(挤出、注塑、涂覆等)。
大致的填料直径和使用硅烷的比例如下:填料尺寸使用硅烷比例60目0.1%,100目0.25%,200目0.5%,300目0.75%,400目1.0%,500目以上1.5%常用硅烷醇/水溶液所需PH值:产品名称处理时的溶剂适宜PH 值KH-550乙醇/水:9.0~10.0偶联剂是一种重要的、应用领域日渐广泛的处理剂,主要用作高分子复合材料的助剂。
硅烷偶联剂的使用方法

硅烷偶联剂的使用方法硅烷偶联剂是一种重要的有机硅化合物,具有良好的耐热性、耐候性、电绝缘性等特点,广泛应用于涂料、塑料、橡胶、纺织品、电子材料等工业领域。
硅烷偶联剂的主要作用是在有机基质与无机基质之间建立稳定的界面结合,以提高复合材料的性能。
1.表面处理:在使用硅烷偶联剂之前,需要对基质表面进行预处理。
一般来说,基质表面应保持干燥、无油污和灰尘,以保证硅烷偶联剂能够充分与基质表面接触。
2.稀释:将硅烷偶联剂与有机溶剂按照一定比例混合并搅拌均匀。
这样可以方便硅烷偶联剂的涂布和扩散,提高接触面积,增加反应效果。
3.涂布:采用刷涂、喷涂、浸渍等方法将稀释后的硅烷偶联剂涂覆在基质表面。
刷涂适用于较小面积和精细加工的部件,而喷涂适用于较大面积和批量生产。
浸渍则适用于对材料要求不高的产品。
4.干燥和烘烤:涂布后,将基质置于空气中自然干燥,或者采用加热烘烤的方式促进硅烷偶联剂与基质的反应。
根据硅烷偶联剂的不同,烘烤温度和时间也有所区别,一般在100摄氏度以上热处理。
5.储存和使用:硅烷偶联剂在储存和使用过程中需要注意防潮、密封和避免高温。
一般应存放在阴凉干燥处,避免与空气中的水分接触。
而按照应用领域的不同,硅烷偶联剂的使用方法还有一些特别的要点:1.对于涂料,硅烷偶联剂可以用作附着力促进剂。
在一般的处理方法后,与涂料配方中的颜料、填料和树脂一起混合使用,提高涂层与底材之间的粘结性能。
2.对于塑料,硅烷偶联剂可以作为改性剂。
一般是将硅烷偶联剂与塑料原料一同加入到挤出机或注塑机中进行加工。
硅烷偶联剂会与塑料颗粒发生反应,在塑料表面形成一层致密的硅氧化物覆盖层,提高塑料的强度、硬度和耐热性能。
3.对于橡胶,硅烷偶联剂可以作为增强剂。
硅烷偶联剂与填充剂如炭黑颗粒反应生成硅氧化物覆盖层,提高填充剂与橡胶的相容性和分散性,从而改善橡胶的拉伸性能、耐磨性和耐候性。
4.对于纺织品,硅烷偶联剂可以作为阻燃剂。
硅烷偶联剂可以通过反应或吸附等方式降低纺织品的可燃性,提高纤维的防火性能,延缓燃烧速度,减少烟雾和有害气体的产生。
硅烷偶联剂使用方法

硅烷偶联剂是由硅氯仿(HSiCl3)和带有反应性基团的不饱和烯烃在铂氯酸催化下加成,再经醇解而得。
硅烷偶联剂实质上是一类具有有机官能团的硅烷,在其分子中同时具有能和无机质材料(如玻璃、硅砂、金属等)化学结合的反应基团及与有机质材料(合成树脂等)化学结合的反应基团。
通式如图,此处,n=0~3;X-可水解的基团;Y一有机官能团,能与树脂起反应。
X 通常是氯基、甲氧基、乙氧基、甲氧基乙氧基、乙酰氧基等,这些基团水解时即生成硅醇(Si(OH)3),而与无机物质结合,形成硅氧烷。
Y是乙烯基、氨基、环氧基、甲基丙烯酰氧基、巯基或脲基。
这些反应基可与有机物质反应而结合。
因此,通过使用硅烷偶联剂,可在无机物质和有机物质的界面之间架起"分子桥",把两种性质悬殊的材料连接在一起提高复合材料的性能和增加粘接强度的作用。
硅烷偶联剂的这一特性最早应用于玻璃纤维增强塑料(玻璃钢)上,作玻璃纤维的表面处理剂,使玻璃钢的机械性能、电学性能和抗老化性能得到很大的提高,在玻璃钢工业中的重要性早已得到公认。
目前,硅烷偶联剂的用途已从玻璃纤维增强塑料(FRP)扩大到玻璃纤维增强热塑性塑料(FRTP)用的玻璃纤维表面处理剂、无机填充物的表面处理剂以及密封剂、树脂混凝土、水交联性聚乙烯、树脂封装材料、壳型造型、轮胎、带、涂料、胶粘剂、研磨材料(磨石)及其它的表面处理剂。
在硅烷偶联剂这两类性能互异的基团中,以Y基团最重要、它对制品性能影响很大,起决定偶联剂的性能作用。
只有当Y基团能和对应的树脂起反应,才能使复合材料的强度提高。
一般要求Y基团要与树脂相容并能起偶联反应。
编辑本段|回到顶部应用领域硅烷偶联剂的应用大致可归纳为三个方面:(一)用于玻璃纤维的表面处理,能改善玻璃纤维和树脂的粘合性能,大大提高玻璃纤维增强复合材料的强度、电气、抗水、抗气候等性能,即使在湿态时,它对复合材料机械性能的提高,效果也十分显著。
目前,在玻璃纤维中使用硅烷偶联剂已相当普遍,用于这一方面的硅烷偶联剂约占其消耗总量的50%,其中用得较多的品种是乙烯基硅烷、氨基硅烷、甲基丙烯酰氧基硅烷等。
- 1、下载文档前请自行甄别文档内容的完整性,平台不提供额外的编辑、内容补充、找答案等附加服务。
- 2、"仅部分预览"的文档,不可在线预览部分如存在完整性等问题,可反馈申请退款(可完整预览的文档不适用该条件!)。
- 3、如文档侵犯您的权益,请联系客服反馈,我们会尽快为您处理(人工客服工作时间:9:00-18:30)。
一、选用硅烷偶联剂的一般原则已知,硅烷偶联剂的水解速度取于硅能团Si-X ,而与有机聚合物的反应活性则取于碳官能团C-丫。
因此,对于不同基材或处理对象,选择适用的硅烷偶联剂至关重要。
选择的方法主要通过试验预选,并应在既有经验或规律的基础上进行。
例如,在一般情况下,不饱和聚酯多选用含CH2=CMeC、OOVi 及CH2-CHOCH-2O 的硅烷偶联剂;环氧树脂多选用含CH2- CHCH2及H2N-硅烷偶联剂;酚醛树脂多选用含H2N-及H2NC0NH硅烷偶联剂;聚烯烃选用乙烯基硅烷;使用硫黄硫化的橡胶则多选用烃基硅烷等。
由于异种材料间的黏接可度受到一系列因素的影响,诸如润湿、表面能、界面层及极性吸附、酸碱的作用、互穿网络及共价键反应等。
因而,光靠试验预选有时还不够精确,还需综合考虑材料的组成及其对硅烷偶联剂反应的敏感度等。
为了提高水解稳定性及降低改性成本,硅烷偶联剂中可掺入三烃基硅烷使用;对于难黏材料,还可将硅烷偶联剂交联的聚合物共用。
硅烷偶联剂用作增黏剂时,主要是通过与聚合物生成化学键、氢键;润湿及表面能效应;改善聚合物结晶性、酸碱反应以及互穿聚合物网络的生成等而实现的。
增黏主要围绕 3 种体系:即(1)无机材料对有机材料;(2)无机材料对无机材料;(3)有机材料对有机材料。
对于第一种黏接,通常要求将无机材料黏接到聚合物上,故需优先考虑硅烷偶联剂中丫与聚合物所含官能团的反应活性;后两种属于同类型材料间的黏接,故硅烷偶联剂自身的反亲水型聚合物以及无机材料要求增黏时所选用的硅烷偶联剂。
二、使用方法如同前述,硅烷偶联剂的主要应用领域之一是处理有机聚合物使用的无机填料。
后者经硅烷偶联剂处理,即可将其亲水性表面转变成亲有机表面,既可避免体系中粒子集结及聚合物急剧稠化,还可提高有机聚合物对补强填料的润湿性,通过碳官能硅烷还可使补强填料与聚合物实现牢固键合。
但是,硅烷偶联剂的使用效果,还与硅烷偶联剂的种类及用量、基材的特征、树脂或聚合物的性质以及应用的场合、方法及条件等有关。
本节侧重介绍硅烷偶联剂的两种使用方法,即表面处理法及整体掺混法。
前法是用硅烷偶联剂稀溶液处理基体表面;后法是将硅烷偶联剂原液或溶液,直接加入由聚合物及填料配成的混合物中,因而特别适用于需要搅拌混合的物料体系。
1、硅烷偶联剂用量计算被处理物(基体)单位比表面积所占的反应活性点数目以及硅烷偶联剂覆盖表面的厚度是决定基体表面硅基化所需偶联剂用量的关键因素。
为获得单分子层覆盖,需先测定基体的Si—OH含量。
已知,多数硅质基体的Si —OH含是来4-12 个/卩叭因而均匀分布时,1mol硅烷偶联剂可覆盖约7500m2的基体。
具有多个可水解基团的硅烷偶联剂,由于自身缩合反应,多少要影响计算的准确性。
若使用丫3SiX处理基体,则可得到与计算值一致的单分子层覆盖。
但因丫3SiX价昂,且覆盖耐水解性差,故无实用价值。
此外,基体表面的Si-OH数,也随加热条件而变化。
例如,常态下Si —OH数为5.3个/卩川硅质基体,经在400C或800C 下加热处理后,则Si —OH值可相应降为2.6个/卩卅或V 1个/卩讥反之,使用湿热盐酸处理基体,则可得到高Si —OH含量;使用碱性洗涤剂处理基体表面,则可形成硅醇阴离子。
硅烷偶联剂的可润湿面积(WS,是指ig硅烷偶联剂的溶液所能覆盖基体的面积(卅/g )。
若将其与含硅基体的表面积值(卅/g)关连, 即可计算出单分子层覆盖所需的硅烷偶联剂用量。
以处理填料为例,填料表面形成单分子层覆盖所需的硅烷偶联剂W(g )与填料的表面积S(tf /g )及其质量成正比,而与硅烷的可润湿面积WS(tf /g,可由表1查得)成反比。
据此,得到硅烷偶联剂用量的计算公式如下:硅烷用量(g)=某些常见填料的表面(S)值示于表 1 。
表1常见填料的比表面积(S)填料E- 玻璃纤维石英粉高岭土黏土滑石粉硅藻土硅酸钙气相法白炭黑S/ m2 .g-1 0.1-0.21-27 7 7 1.0-3.5 2.6150-250此外,使用硅烷偶联剂处理填料时,还需测定填料含水量是否能满足硅烷偶联剂水解反应的需要。
表2 列出某些硅烷偶联剂水解反应所需的最低水量。
表 2 硅烷水解反应所需的最低水量硅烷偶联剂水解1g 硅烷需水量/gCIC3H6Si(OMe)3 0.27CH2-CHOCH2OC3H6Si(OMe)3 0.23ViSi(OEt)3 0.28ViSi(OC2H4OMe)3 0.19HSC3H6Si(OMe)3 0.28CH2=CMeCOOC3H6Si(OMe)3 0.22H2NC3H6Si(OEt)3 0.25倘若不掌握填料的比表面积,则可先用1%(质量分数)浓度的硅烷偶联剂溶液处理填料,同时改变浓度进行对比,以确定适用的浓度。
2、表面处理法此法系通过硅烷偶联剂将无机物与聚合物两界面连结在一起,以获得最佳的润湿值与分散性。
表面处理法需将硅烷偶联剂酸成稀溶液,以利与被处理表面进行充分接触。
所用溶剂多为水、醇或水醇混合物,并以不含氟离子的水及价廉无毒的乙醇、异丙醇为宜。
除氨烃基硅烷外,由其他硅烷配制的溶液均需加入醋酸作水解催化剂,并将pH值调至3.5-5.5。
长链烷基及苯基硅烷由于稳定性较差,不宜配成水溶液使用。
氯硅烷及乙酰氧硅烷水解过程中,将伴随严重的缩合反应,也不适于制成水溶液或水醇溶液使用。
对于水溶性较差的硅烷偶联剂,可先加入0.1%-0.2%(质量分数)的非离子型表面活性剂,而后再加水加工成水乳液使用。
为了提高产品的水解稳定性的经济效益,硅烷偶联剂中还可掺入一定比例的非碳官能硅烷。
处理难黏材料时,可使用混合硅烷偶联剂或配合使用碳官能硅氧烷。
配好处理液后,可通过浸渍、喷雾或刷涂等方法处理。
一般说,块状材料、粒状物料及玻璃纤维等多用浸渍法处理;粉末物料多采用喷雾法处理;基体表面需要整体涂层的,则采用刷涂法处理。
下面介绍几种具体的处理方法。
(一)使用硅烷偶联剂醇-水溶液处理法此法工艺简便,首先由95%勺EtOH及5%勺H2O配成醇—水溶液,加入AcOH使pH为4.5-5.5 。
搅拌下加入硅尝偶联剂使浓度达2%水解5min后,即生成含Si —OH 的水解物。
当用其处理玻璃板时,可在稍许搅动下浸入1-2min,取出并浸入EtOH中漂洗2次,晾干后,移入110C的烘箱中烘干5-10min,或在室温及相对湿度v 60%条件下干燥24h,即可得产物。
如果使用氨烃基硅烷偶联剂,则不必加HOA。
但醇-水溶液处理法不适用于氯硅烷型偶联剂,后者将在醇水溶液中发生聚合反应。
当使用2%浓度的三官能度硅烷偶联剂溶液处理时,得到的多为3-8 分子厚的涂层。
二)使用硅烷偶联剂水溶液处理工业上处理玻璃纤维大多采用此法。
具体工艺是先将烷氧基硅烷偶联剂溶于水中,将其配成0.5%-2.0%的溶液。
对于溶解性较差的硅烷,可事先在水中加入0.1% 非离子型表面活性剂配制成水乳液,再加入AcOH 将pH调至5.5。
然后,采用喷雾或浸渍法处理玻璃纤维。
取出后在110-120C下固化20-30min,即得产品。
由于硅烷偶联剂水溶液的稳定性相差很大,如简单的烷基烷氧基硅烷水溶液仅能稳定数小时,而氨烃硅烷水溶液可稳定几周。
由于长链烷基及芳基硅烷水溶液仅能稳定数小时,而氨烃硅水溶液可稳定几周。
由于长链烷基及世基硅烷的溶解度参数低,故不能使用此法。
配制硅烷水溶液时,无需使用去离子水,但不能使用含所氟离子的水。
三)使用硅烷偶联剂—有机溶剂配成的溶液处理使有硅烷偶联剂溶液处理基体时,一般多选用喷雾法。
处理前,需掌握硅烷用量及填料的含水量。
将偶联剂先配制成25%的醇溶液,而后将填料置入高速混合器内,在搅拌下泵入呈细雾状的硅烷偶联剂溶液,硅烷偶联剂的用量约为填料质量的0.2%—1.5%,处理20min即可结束,随后用动态干燥法干燥之。
除醇外,还可使用酮、酯及烃类作溶剂,并配制成1%-5%(质量分数)的浓度。
为使硅烷偶联剂进行水解或部分水解,溶剂中还需加入少量水,甚至还可加入少许HOAC乍水解催化剂,而后将待处理物料在搅拌下加入溶液中处瑼,再经过滤,及在80-120C 下干燥固化数分钟,即可得产品。
采用喷雾法处理粉末填料,还可使用硅烷偶联剂原液或其水解物溶液。
当处理金属、玻璃及陶瓷时,宜使0.5%-2.0% (质量分数)浓度的硅烷偶联剂醇溶液,并采用浸渍、喷雾及刷涂等方法处理,根据基材的处形及性能,既可随即干燥固化,也可在80-180C下保持1-5min达到干燥固化。
四)使用硅烷偶联剂水解物处理即先将硅烷通过控制水解制成水解物而用作表面处理剂。
此法可获得比纯硅烷溶液更佳的处理效果。
它无需进一步水解,即可干燥固化。
3、整体掺混法整体掺混法是在填料加入前,将硅烷偶联剂原液混入树脂或聚合物内。
因而,要求树脂或聚合物不得过早与硅烷偶联剂反应,以免降低其增黏效果。
此外,物料固化前,硅烷偶联剂必须从聚合物迁移到填料表面,随后完成水解缩合反应。
为此,可加入金属羧酸酯作催化剂,以加速水解缩合反应。
此法对于宜使用硅烷偶剂表面处理的填料,或在成型前树脂及填料需经混匀搅拌处理的体系,尤为方便有效,还可克服填料表面处理法的某些缺点。
有人使用各种树脂对比了掺混法及表面处理法的优缺点。
认为:在大多数情况下,掺混法效果亚于表面处理法。
掺混法的作用过程是硅烷偶剂从树脂迁移到纤维或填料表面,并过而与填料表面作用。
因此,硅烷偶联掺入树脂后,须放置一段时间,以完成迁移过程,而后再进行固化,方能获得较佳的效果。
还从理论上推测,硅烷偶联剂分子迁移到填料表面的理,仅相当于填料表面生成单分子层的量,故硅烷偶联剂用量仅需树脂质量的0.5%-1.0%。
还需指出,在复合材料配方中,当使用与填料表面相容性好、且摩尔质量较低的添加剂,则要特别注意投料顺序,即先加入硅烷偶联剂,而后加入添加剂,才能获得较佳的结果。
硅烷偶联剂是重要的、应用日渐广泛的处理剂之一。
它最初作为FPR玻璃纤的处理剂而开发的。
其后,随着新化合物的研制,逐渐在各个领域获得应用。
现在,硅烷偶联剂基本上适用于所有无机材料和有机材料的表面,下面主要介绍硅偶联剂及其在复合材料中应用。
1硅烷偶联剂硅烷偶联剂是以下式所表示的一类有机硅化合物,其特点是分子中具有 2 种以上不同的反应基团。
通式:Y—R—Si —X3R:烷基或芳基;X:甲氧基、乙氧基、氯基等;Y:有机反应基(乙烯基、环氧基、氨基、巯基等)。
X所表示的水解性基团能与有机材料化学结合,故硅烷偶联剂在无机材料和有机材料的界面起着桥梁作用,因而被广泛用于复合材料的改性。
目前,国内外硅烷偶联剂品种繁多,常用的见表 1 所列。
2 在复合材料中的作用机理人们对其作用机理已进行了相当多的研究,提出了各种理论,但至今无完整统的认识。