零部件物料清单和供应商明细表
物料清单与零件明细表的区别

详细程度不同
物料清单更注重产品的整体结构, 相对较为概括,而零件明细表更 加详细,列出了每个零件的具体 信息。
05
实例对比分析
物料清单实例
01
02
03
物料清单实例1
一个简单的电脑组装物料 清单,包括CPU、内存、 硬盘、主板、电源等主要 组件。
物料清单实例2
一个家具制造的物料清单, 包括木材、油漆、钉子、 胶水等原材料以及各种零 部件。
3
物料清单不仅包含原材料和组件,还可能包含间 接材料和耗材,而零件明细表主要关注产品组成 的具体零件。
04
编制方法与流程
物料清单的编制方法与流程
确定产品结构
明确产品的组成,将产品分解为若干个组件 或零件。
收集数据
收集各组件或零件的详细信息,包括名称、 规格、数量、材料等。
编制物料清单
根据产品结构和收集的数据,按照一定的格 式和要求,编制出物料清单。
物料清单是生产计划、采购、库存管理以及产品追溯等环节的重要依据,是制造业中不可或缺的基础 数据。
零件明细表的定义
零件明细表(Part List)是详细列出 制造一个完整产品所需的所有零件的 清单。它通常包括每个零件的名称、 规格、数量、供应商信息等。
零件明细表主要用于采购、库存管理 和生产过程中的零件管理,以确保生 产所需的零件都已到位且数量正确。
在产品的生命周期中,维护和维修是必不可少的环节。零件明细表提供
了产品的详细组成信息,帮助维修人员快速识别和更换损坏的零件,确
保产品的正常运行。
两者在用途与功能上的差异
1
物料清单更侧重于生产计划和物料需求的管理, 而零件明细表更侧重于产品设计和组装过程的指 导。
IATF16949-2016质量管理体系PPAP提交登记规定及全套记录表格

R
R
S
*
R
13 过程流程图
R
R
S
*
R
14 PFMEA
R
R
S
*
R
15 生产控制计划
R
S
S
*
R
16 测量系统分析结果
R
R
S
*
R
17 过程能力研究结果
R
R
S
*
R
18 包装评价
R
R
S
*
R
19 检具/辅具(需要时)(如需时)
R
S
S
*
R
20 零件提交保证书
S
S
S
S
R
22 PPAP 检查清单
S=组织必须向顾客提交,并在适当的场所保留一份记录或文件的副本。 R=组织必须在适当的场所保存,并应在顾客有要求时易于得到。 *=组织必须在适当的场所保存,并在有要求时向顾客提出。
R
S
S
*
R
5 DFMEA
R
R
S
*
R
6 试生产控制计划
7
外观批准报告(适用 时)
8
零部件物料清单和 供应商明细表
9 生产件样品 10 检具/辅具清单
一式 三份 (如需时)
R
R
S
*
R
S
S
S
*
R
R
S
S
*
R
R
S
S
*
R
R
R
S
*
R
11 工装清单
(如需时)
R
R
S
*
R
12
什么叫物料清单

物料清单(BOM)一,什么BOM表物料清单(Bill of Material, BOM)是指产品所需零部件明细表及其结构.在MRP2中,物料一词有着广泛的含义,它是所有产品,半成品,在制品,原材料,配套件,协作件,易耗品等等与生产有关的物料的统称.采用计算机辅助企业生产管理,首先要使计算机能够读出企业所制造的产品构成和所有要涉及的物料,为了便于计算机识别,必须把用图示表达的产品结构转化成某种数据格式,这种以数据格式来描述产品结构的文件就是物料清单,即是BOM.它是定义产品结构的技术文件,因此,它又称为产品结构表或产品结构树.BOM是由双亲件及子件所组成的关系树.BOM可以是自顶向下分解的形式或是以自底向上跟踪的形式提供信息.分解是从上层物料开始将其展开成下层零件,跟踪是从零件开始得到上层物料.将最终产品的需求或主生产计划中的项目分解成零件需求是MRP建立所有低层零件计划的关键一步.如果低层零件计划存在问题,通过跟踪就能确定生成这一零件需求的上层物料.为了便于计算机管理和处理的方便,BOM 必须具有某种合理的组织形式,而且为了便于在不同的场合下使用BOM,BOM还应有多种组织形式和格式.BOM是MRP2系统中最重要的基础数据其组织格式设计和合理与否直接影响到系统的处理性能,因此,根据实际的使用环境,灵活地设计合理且有效的BOM是十分重要的.BOM不仅是MRP2系统中重要的输入数据,而且是财务部门核算成本,制造部门组织生产等的重要依据,因此,BOM的影响面最大,对它的准确性要求也最高.采取有力措施,正确地使用与维护BOM是系统运行期间十分重要的工作,必须引起足够的重视.此外,BOM还是CIMS/MIS与CAD,CAPP等子系统的重要接口,是系统集成的关键之处,因此,用计算机实现BOM管理时,应充分考虑它于其他子系统的信息交换问题.BOM信息被用于MRP计算,成本计算,库存管理.BOM有各种形式,这些形式取决于它的用途,BOM的具体用途有:1.是计算机识别物料的基础依据.2.是编制计划的依据.3.是配套和领料的依据.4.根据它进行加工过程的跟踪.5.是采购和外协的依据.6.根据它进行成本的计算.7.可以作为报价参考.8.进行物料追溯.9.使设计系列化,标准化,通用化.二,BOM的使用在任何制造环境中,不同的部门和系统都为不同的目的使用BOM,每个部门和系统都从BOM中获取特定的数据.主要的BOM用户有:设计部门设计部门既是BOM的设计者,又是BOM的使用者.就使用而言,无论何时,当产品结构发生变化,或对某个零件进行重新设计,该部门都要从BOM中获取所有零件的信息及其相互间的结构信息,只有得到这些信息,才能对其进行定义,描述或修改.●工艺部门工艺部门根据BOM信息建立各零件的制造工艺和装配件的装配工艺.并确定加工制造过程中应使用的工装,模具等.●生产部门生产部门使用BOM来决定零件或最终产品的制造方法,决定领取的物料清单.●产品成本核算部门该部门利用BOM中每个自制件或外购件的当前成本来确定最终产品的成本.●物料需求计划(MRP)系统BOM是MRP的主要输入信息之一,它利用BOM决定主生产计划项目时,需要哪些自制件和外购件,需要多少,何时需要.三,BOM的构造问题:前面已经提到,BOM是系统中最重要的基础数据库,它几乎与企业中的所有职能部门都有关系,BOM构造的好坏,直接影响到系统的处理性能和使用效果.因此,根据实际环境,,灵活地构造BOM是十分关键的.就一般情况而言,构造BOM 应注意以下方面.1.在BOM中,每一个项目(零件)必须有一个唯一的编码.对于同一个项目,不管它出现在哪些产品中,都必须具有相同的编码.对于相似的项目,不管它们的差别有多么小,也必须使用不同的编码.2.为了管理上的方便,有时可以将同一零件的不同状态视为几个不同的项目,构造在产品的BOM中.3.BOM中的零件,部件的层次关系一定要反映实际装配过程,在实际装配中,有时不一定把某些零件装配成某个有名称的组件,或者由于工艺上的考虑需要将某些零件归在一起加工(例如箱子与箱盖).形成临时组件,但这些组件在产品的零件明细表和装配图上并没有反映出来,但必须在计划管理中反映出来,这就需要在BOM中设置一种物理上并不存在的项目,通常称为”虚单”或”虚拟件”,其目的是简化MRP的编程过程和减少零件之间的影响.4.根据生产实际情况,有时为了强化某些工装,模具的准备工作,还可以将这些工具构造在BOM中.这样就可以将一些重要的生产准备工作纳入计划中.有时为了控制某个重要的零件在加工过程中的某些重要环节,比如,进行质量检测等,还可将同一个零件的不同加工状态视为不同的零件,构造在BOM中.5.为了满足不同部门获取零件的不同信息,可以灵活地设计BOM中每个项目的属性.例如,计划方面的,成本方面,库存方面,订单方面.四,BOM的维护BOM是任何管理系统中基础中的基础,如果没有BOM,就无法制造出同样的产品,为此要想提高生产管理系统的效率,BOM的正确与否是十分重要的.(1)不正确BOM造成影响●一些项目为BOM所遗漏,造成零件短缺.●BOM中列入了一些不必要的项目,导致零件过多储备.●由于缺件的数量过多,导致制造的低效率.●订单不能按期交货●质量低下●计划缺乏可信性●不正确的产品成本●废弃的库存(2)BOM中发生错误的环节●工程部门产生BOM时●为BOM准备数据时●BOM数据录入时(3)正确维护BOM的方法●指定专人负责维护BOM●经常监测BOM,检查项目数量及其生效日期●对工程改变进行分类●危机性改变—立即完成.如,产品不能实现其功能,或不利于安全时.●紧急性改变—迅速完成.如,工程部门设置一个合理日期来完成改变●常规改变—从经济实用角度要求变化时再完成.●通知要进行的工程改变●实施工程改变。
物料清单明细表重复

物料清单明细表重复(原创版)目录1.物料清单明细表的概念与作用2.物料清单明细表重复的原因3.解决物料清单明细表重复的方法4.避免物料清单明细表重复的建议正文一、物料清单明细表的概念与作用物料清单明细表是生产管理中的一种重要文档,用于记录一个产品在生产过程中所需要的全部原材料、零部件、半成品等物品的名称、数量、规格等信息。
它对于确保生产计划的顺利执行,以及控制生产成本具有重要的作用。
二、物料清单明细表重复的原因在实际的生产管理过程中,物料清单明细表有时会出现重复的情况,这主要是由以下几个原因导致的:1.信息录入错误:在制作物料清单明细表时,可能会出现信息录入错误,导致相同的物品信息被重复录入。
2.物料编码问题:如果物料编码系统存在问题,可能会导致相同的物料被赋予不同的编码,从而使得这些物料在物料清单明细表中被重复列出。
3.物料清单的复制粘贴:在制作物料清单明细表时,为了节省时间,可能会采用复制粘贴的方式,这样如果复制的物料清单存在重复的物料,粘贴后就会导致物料清单明细表重复。
三、解决物料清单明细表重复的方法要解决物料清单明细表重复的问题,可以采取以下几种方法:1.仔细核对物料信息:在制作物料清单明细表后,要仔细核对每一项物料信息,确保没有重复的物料。
2.优化物料编码系统:如果物料编码系统存在问题,应该及时进行优化,确保每一个物料都有唯一的编码。
3.提高信息录入的准确性:在录入物料信息时,要确保信息的准确性,避免因为信息录入错误而导致物料清单明细表重复。
四、避免物料清单明细表重复的建议为了避免物料清单明细表重复,可以采取以下几种方法:1.建立严格的物料编码制度:通过建立严格的物料编码制度,可以避免因为物料编码问题导致的物料清单明细表重复。
2.使用专业的物料清单管理软件:通过使用专业的物料清单管理软件,可以提高物料清单明细表制作的效率和准确性,避免重复。
模具图上零件明细表及物料定单的标准化
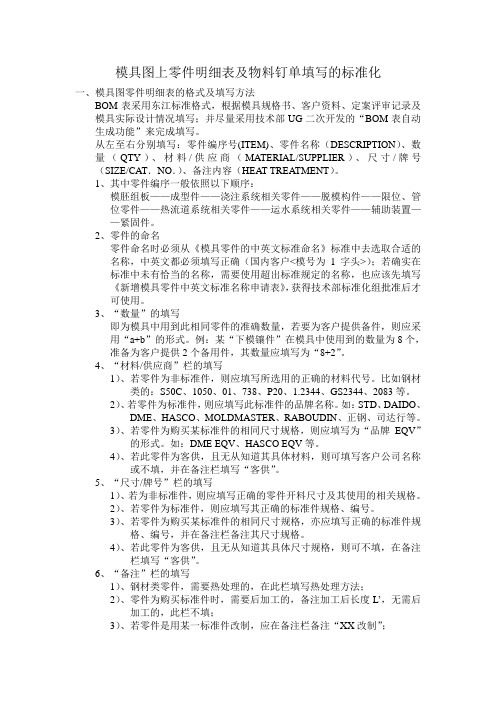
模具图上零件明细表及物料钉单填写的标准化一、模具图零件明细表的格式及填写方法BOM表采用东江标准格式,根据模具规格书、客户资料、定案评审记录及模具实际设计情况填写;并尽量采用技术部UG二次开发的“BOM表自动生成功能”来完成填写。
从左至右分别填写:零件编序号(ITEM)、零件名称(DESCRIPTION)、数量(QTY)、材料/供应商(MATERIAL/SUPPLIER)、尺寸/牌号(SIZE/CAT.NO.)、备注内容(HEAT TREATMENT)。
1、其中零件编序一般依照以下顺序:模胚组板——成型件——浇注系统相关零件——脱模构件——限位、管位零件——热流道系统相关零件——运水系统相关零件——辅助装置——紧固件。
2、零件的命名零件命名时必须从《模具零件的中英文标准命名》标准中去选取合适的名称,中英文都必须填写正确(国内客户<模号为1字头>);若确实在标准中未有恰当的名称,需要使用超出标准规定的名称,也应该先填写《新增模具零件中英文标准名称申请表》,获得技术部标准化组批准后才可使用。
3、“数量”的填写即为模具中用到此相同零件的准确数量,若要为客户提供备件,则应采用“a+b”的形式。
例:某“下模镶件”在模具中使用到的数量为8个,准备为客户提供2个备用件,其数量应填写为“8+2”。
4、“材料/供应商”栏的填写1)、若零件为非标准件,则应填写所选用的正确的材料代号。
比如钢材类的:S50C、1050、01、738、P20、1.2344、GS2344、2083等。
2)、若零件为标准件,则应填写此标准件的品牌名称。
如:STD、DAIDO、DME、HASCO、MOLDMASTER、RABOUDIN、正钢、司达行等。
3)、若零件为购买某标准件的相同尺寸规格,则应填写为“品牌EQV”的形式。
如:DME EQV、HASCO EQV等。
4)、若此零件为客供,且无从知道其具体材料,则可填写客户公司名称或不填,并在备注栏填写“客供”。
BOM知多少

导读:本文将对BOM管理的难点、BOM的含义与几种细分类型的BOM概念,以及不同类型的BOM之间如何转换做科普。
物料清单(Bill of Materials,简称BOM)是描述企业产品组成的技术文件。
对制造企业而言,BOM是制造信息化的“骨架”,覆盖了产品设计、生产计划制定、物料采购、质量管理和设计改进等流程,为生产活动提供了最直接依据。
而如何实现对BOM准确、高效的管理是制造企业一直以来关注的问题。
本文将对BOM管理的难点、BOM的含义与几种细分类型的BOM概念,以及不同类型的BOM之间如何转换做科普。
01BOM管理的乱象导致生产混乱激烈的市场竞争环境促使市场的细分和产品的多样化越来越明显,对新产品的上市周期也提出了更高要求。
企业根据制造BOM(或工程BOM)备料却经常因产品设计变动而制造BOM(或工程BOM)未及时调整,从而造成BOM管理失误,严重影响生产过程。
此外,企业可能需要对工艺进行调整,例如需要更换或增减加工步骤,需要对BOM进行修改,如果修改不及时或者不准确,会影响生产进度和产品质量。
如今,制造企业已因BOM管理中的乱象而产生了较多生产乱象:(1)生产数据缺乏准确性:进行BOM管理时,若更新不及时或清单错误,会导致生产过程缺乏准确的数据,包括零件清单、物料清单、工艺等。
来自BOM的数据不准确或者错误便会导致生产计划和采购计划出现偏差;(2)物料出现短缺:若设计要求或实际生产条件出现变动,BOM未随之改变或及时调整,可能会出现物料短缺问题,没有及时处理会导致生产计划无法按时完成;(3)替代物料选择错误:在采购过程中,可能存在某些物料已经停产或者难以采购的情况,此时便需要进行物料替换。
如果选择了不正确的替换物料,会影响产品的质量和性能;(4)各部门之间协同性低下:在一些产品中,BOM可能存在多个层级,需要对BOM进行分层管理,将涉及到层级之间的关系和数据的传递,需要进行有效的沟通和协调。
基于MRP的汽车零部件产品包装物料需求计划模型研究

基于MRP的汽车零部件产品包装物料需求计划模型研究一、简述随着汽车工业的快速发展,汽车零部件产品的生产和包装已经成为了汽车产业链中的重要环节。
为了提高生产效率,降低成本企业需要对汽车零部件产品包装物料的需求进行合理规划。
传统的需求计划方法在面对复杂多变的市场环境时,往往难以满足企业的需求。
因此本文旨在研究一种基于物料需求计划(MRP)的汽车零部件产品包装物料需求计划模型,以提高企业在市场环境下的生产计划水平。
MRP(Material Requirements Planning)是一种先进的生产计划方法,它将企业的原材料、半成品和成品的需求与现有资源相匹配,从而为企业提供一个合理的生产计划。
通过对MRP模型的研究和应用,企业可以更好地控制生产过程中的物料需求,降低库存成本,提高生产效率。
本文首先分析了汽车零部件产品包装物料需求计划的基本原理和方法,然后结合实际案例,对基于MRP的汽车零部件产品包装物料需求计划模型进行了深入研究。
在研究过程中,本文采用了多种数学建模方法,如线性规划、整数规划等,以求解最优的物料需求计划方案。
通过对所得到的模型进行实证分析,验证了模型的有效性和可行性。
本文通过研究基于MRP的汽车零部件产品包装物料需求计划模型,为企业提供了一种有效的生产计划方法,有助于企业更好地应对市场变化,提高生产效率和降低成本。
1.1 研究背景和意义随着全球经济的快速发展,汽车产业作为国民经济的重要支柱产业,其市场需求和竞争也日益激烈。
在这个过程中,汽车零部件产品的质量、成本和交付周期成为企业竞争力的关键因素。
为了满足市场需求并降低生产成本,企业需要对汽车零部件产品的包装物料需求进行有效的计划和管理。
MRP(Material Requirements Planning,物料需求计划)作为一种先进的生产计划方法,通过对生产过程的需求进行详细的分析和计算,为企业提供了一种科学合理的物料需求计划模型。
然而在汽车零部件产品的包装物料需求计划方面,目前尚缺乏系统的研究和应用。
IATF16949-2016质量管理体系PPAP提交登记规定及全套记录表格

IATF16949-2016质量管理体系PPAP提交登记规定及全套记录表格R=组织必须在适当的场所保存,并应在顾客有要求时易于得到。
*=组织必须在适当的场所保存,并在有要求时向顾客提出。
编号:035-060-168-006T蒙凌工程机械有限公司技术部编号:编号:035-060-168-006T编号:035-060-168-006T1、本表由一级供应商认真填写,并加盖二级供应商和供应商公章后将原件提交给Motiontec品管部;2、本表是最终批准的重要输入之一,如有变动应及时通知Motiontec品管部。
3、当二级供应商变化时,应及时通过Motiontec品管部,以确定是否进行生产件批准。
1编号:035-060-168-006T编号:Motiontec/R.706.13编号:035-060-168-006TMotiontec采购部:1.必要时,供应商应附详细的自审报告;2.在完成各过程的内部批准并确认满足批量生产、供货要求时才可提交本表; 3.SQE 尽量携带本表去供应商现场确认; 4.在不适用的选项的 ”。
Motiontec采购部:生产件批准状况通知PRODUCTION PART APPROVAL STATUS NOTICENO:致:先生/女士(职务)供应商名称:地址:供适用范围(产品型号)APPLICATION(VEHICLES)零件号PART NUMBER零件名称PART NAME更改等级/更改日期CHENGE LEVEL/DATED更改号CHENGE NUMBER原用零件号ORIGINAL PART NUMBERPPAP 编号MOTIONTEC PPAP NUMBER生产件批准状况如下:Production part approval status is as follow批准状态有效截止日期/数量CLASS THROUGH DATE/QUANTITY备注:Motiontec品管工程师Motiontec SQE采购工程师MANAGER编号:035-060-168-006TMotiontec2、版面不够,可附页;3、任何产品变更、物流/运输方式变化导致包装改变时,应向Motiontec品管部门确认是否进行重新认可。