仪器制造技术-热变形-第六次课资料
仪器制造技术-热变形-第六次课
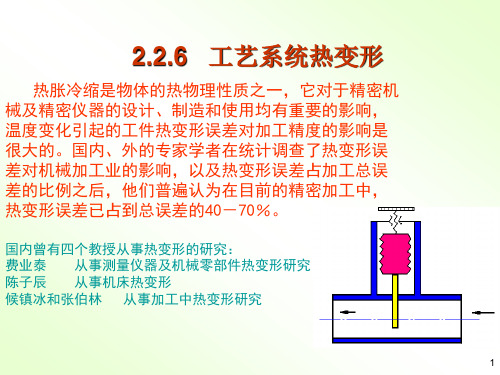
ξ(μm)
连续切削升温曲线
ξmax 0.63ξmax
间断切削升温曲线
冷却曲线 0 τc τb τ(min)
图2-9 车刀热变形曲线
胡批:在我们大自然中, 很多规律的描述都离不 开指数函数。
式中 ξ—— 热伸长量; ξmax —— 达到热平衡热伸长量; τ—— 切削时间; τc —— 时间常数(热伸长量为热平衡热伸长量约63%的时间 ,常取3~4分钟)。
热伸长方向
图4-42 双端面磨床主轴热补偿
1—主轴 2—壳体 3—过渡套筒
加速达到热平衡
高速空运转 人为加热、提前空转
控制环境温度
恒温(太花钱) 人体隔离,刻线机
L1 L2 支承距影响热变形
24
调整误差
试切法(图4-20 a)
测量误差。 试切时与正式切削时切削厚度 不同造成的误差。 机床进给机构的位移误差。
3
切削热产生及分布
Qc R1Q1 R2 Q2 QT 1 R2 Q2 Qw 1 R1 Q1
4
刀具热变形对加工精度影响
刀具热变形
◆ 特点 体积小,热容量小, 达到热平衡时间较短 温升高,变形不容忽 视(达0.03 ~0.05mm) ◆ 变形曲线(图2-9)
L L t 1.1105 400 1 4.4 103 (mm) 4.4( m)
5级丝杠累积误差全长≤5μm,可见热变形的严重性
6
◆ 板类工件单面加工时的热变形(图4-39)
8 S ΔX —— 变形挠度; L,S ——工件原有长度和厚度; α—— 工件材料线膨胀系数; Δt —— 温升。 X
各觀察點之溫升圖 12 10
金属的热变形课件.ppt

真实应力-应变曲线上,真应力几乎不随变形程度的 增加而变化。
超塑性材料的条件应力-应变曲线
超塑性材料的真实应力-应变曲线
2、流动应力(真应力)对变形速率极其敏感
特征方程: c—决定于试验条件的材料常数; m—应变速率敏感性指数。它反映材料抗局部收缩或产 生均匀拉伸变形的能力。 m 是表征超塑性的一个重要指标。 m值大,流动应力会随应变速率的增大而急速增大。 如试样某处有局部缩小,该处应变速率加大,继续变 形所需应力也随之剧增,阻止了该处断面的继续减小,促 使变形向别处发展而趋于均匀,最终获得更大的伸长率。 m=1,上式即为牛顿粘性流动公式,c为粘性系数。普 通金属,m=0.02~0.2;超塑性金属,m=0.3~1.0;m值越大, 伸长率越大。
组织稳定,则在变形过程中,晶粒长大速度 缓慢,以便在保持细晶的条件下有充分的热变形 持续时间
六、组织变化和对力学性能的影响
1、组织变化 变形后晶粒虽有些长大,但仍为等轴晶,晶粒未变形拉 长; 在试样抛光表面上不出现滑移线,没有亚结构的形成和 位错密度的增加; 有显著的晶界滑移痕迹,在许多情况下,晶界或相界处 形成空洞.
铝在400℃挤压所形成的动态回复亚晶
a)光学显微组织(偏振光 430×);b)透射电子显微组织
影响亚晶尺寸的因素:
形变温度:形变温度高,亚晶尺寸大;
形变速率:形变速率小,亚晶尺寸大。
应变与回复同时进行,避免了冷加工效果的积 累,位错密度较冷变形时低。
动态回复产生的亚组织,不能靠综合冷加工和 静态回复两个过程迭加得到。
εc—开始发生动态再结晶的 临界变形量。
真应力
全国仪器仪表制造职业技能理论知识练习题(附参考答案)
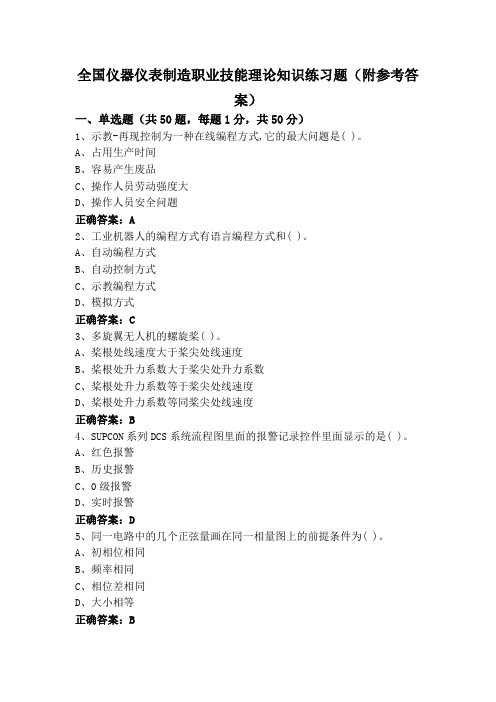
全国仪器仪表制造职业技能理论知识练习题(附参考答案)一、单选题(共50题,每题1分,共50分)1、示教-再现控制为一种在线编程方式,它的最大问题是( )。
A、占用生产时间B、容易产生废品C、操作人员劳动强度大D、操作人员安全问题正确答案:A2、工业机器人的编程方式有语言编程方式和( )。
A、自动编程方式B、自动控制方式C、示教编程方式D、模拟方式正确答案:C3、多旋翼无人机的螺旋桨( )。
A、桨根处线速度大于桨尖处线速度B、桨根处升力系数大于桨尖处升力系数C、桨根处升力系数等于桨尖处线速度D、桨根处升力系数等同桨尖处线速度正确答案:B4、SUPCON系列DCS系统流程图里面的报警记录控件里面显示的是( )。
A、红色报警B、历史报警C、0级报警D、实时报警正确答案:D5、同一电路中的几个正弦量画在同一相量图上的前提条件为( )。
A、初相位相同B、频率相同C、相位差相同D、大小相等正确答案:B6、遥控无人机进入下滑后( )。
A、当下滑线正常时,如速度小,表明目测高,应适当收小油门B、当下滑线正常时,如速度大,表明目测低,应适当增加油门C、当下滑线正常时,如速度大,表明目测高,应适当收小油门D、当下滑线正常时,如速度小,表明目测高,应适当增大油门正确答案:C7、在多级直流放大器中,对零点飘移影响最大的是( )。
A、后级B、中间级C、前级D、前后级一样正确答案:C8、两相继电器接线的过电流保护装置( )。
A、只能作相间短路保护,不能作单相短路保护B、既可以作相间短路保护,又可以作单相短路保护C、只能作单相短路保护,不能作相间短路保护D、既不可作相间短路保护,又不可作单相短路保护正确答案:A9、陀螺仪是利用( )原理制作的。
A、惯性B、光电效应C、超导D、电磁波正确答案:A10、变频器的功能预置必须在“编程模式”下进行,功能预置的第一步是找出需要的( )。
A、功能码B、复位键C、软件D、程序正确答案:A11、多旋翼无人机飞行时出现航向偏移,可能是( )出现故障。
6-1材料科学与工程专业《金属热处理原理及工艺》课件-第六章--贝氏体转变

6.1、贝氏体相变的基本特征 6.2、贝氏体的组织形态和亚结构 6.3、贝氏体相变机制 6.4、贝氏体转变动力学 6.5、贝氏体转变影响因素 6.6、贝氏体力学性能
温度 (℃)
800 700 600 500
400 300 200 100
0
共析碳钢C曲线分析
稳定的奥氏体区
过 冷 奥 氏
碳化物 分布在F条之间; 形态取决于含碳量 与A有位向关系,从A中析出;
上
F
贝பைடு நூலகம்
氏
羽毛状
体
Fe3C
上贝氏体的形成.swf
由成束的、大致平行的F板条加碳化物组成。
组织形态: 由成束的、大致平行的F板条加碳化物组成。
铁素体(羽毛状) 束内相邻F位向差很小,束与束之间位向差较大; 亚结构是位错; C%<0.03%,接近平衡浓度; F有浮凸; F惯习面{111},与A位向关系接近K—S。
上
F
贝
氏
羽毛状
体
Fe3C
组织形态: 由成束的、大致平行的F板条加碳化物组成。
1、转变有BS和Bf 温度 2、转变产物(α+碳化物) 3、转变动力学(形核+长大,可等温转变) 4、转变不完全性 5、转变的扩散性(C扩散,Fe、Me不扩散) 6、有浮凸效应,新、旧相有一定晶体学取向关系
6.2、贝氏体的组织形态和亚结构
一.上贝氏体(B上) B转变区的较高温度区域形成的B称为上贝。 (约350~550℃)
+
产
A
A向产物 转变终止线
产 物 区
体 区 A向产
物
Ms 物转变开始线
区
M+AR Mf
A1 A1~550℃;高温转变区; 扩散型转变;P 转变区。
仪器制造技术的复习要点

仪器制造技术课程复习要点第一章工艺过程基本概念与组成重点章节。
本章主要考点为名词概念。
可能出现计算大题自由度的分析。
重点掌握概念:工序,安装,工位,工步,进给,动作,加工工艺规程,机械加工余量,工序尺寸,时间定额,生产纲领,基准(设计基准,工艺基准,定位基准,测量基准,粗基准,精基准),粗基准和精基准的选择原则,基准重合,基准统一,互为基准,六点定位原理以及自由度的分析(特别要求掌握自由度的分析,有可能出现计算题,课后16题),过定位,欠定位,完全定位,不完全定位,最好能够掌握定位误差的计算(课后17题)。
第二章加工精度分析与制造质量监控技术重点章节。
本章的重点是随机误差的分析。
可能会出现关于废品率,可修复废品率,不可修复废品率的计算题。
重点复习内容:将课本上的相关的例题理解掌握,最后自己做一遍。
还有课后的习题6,7,9,10。
以及刘伟试卷上的相关的计算题。
重点掌握概念:加工精度。
方法误差(又叫原理误差)的概念。
机床误差包括哪三个,分别是什么。
主轴误差包括哪三个。
误差敏感方向。
刚度以及关于刚度的计算(课后有一习题)。
系统刚度和各部件刚度之间的关系(47面)。
渐精加工的概念。
工艺系统的受热变形包括哪些,主要来源是哪个。
切屑热怎么产生的。
残余内应力。
什么是时效,自然失效和人工时效的应用。
加工误差的分类。
加工误差相关的计算(一定要掌握其中的正态分步分析法)。
工序能力。
什么是表面质量,它包括什么。
影响表面质量的工艺因素有哪些,怎么才能减小表面粗糙度值(进给量,主偏角,副偏角,前角等概念)。
加工表面的冷作硬化以及加工表面金相组织变化。
加工过程中的振动包含哪两种,它们的特点。
第三章常用的仪器仪表材料的特性和选材方法本章主要考点为基本概念和简答。
重点掌握的概念:工程材料分为哪几种,分别是什么。
加工硬化,残余内应力,钢的热处理:退火,正火,淬火,回火,调质处理,合金钢中元素含量的判断(课本87和88面),形变铝合金,高分子材料(包含哪些内容,塑料,橡胶等等),复合材料(复合材料的优点),纳米材料了解的知识点:钢中含碳量的范围,碳钢的牌号,铸铁的分类。
热塑性变形.完整版PPT资料

热变形中已经形成但未长大的再结晶晶核以 晶粒越细小均匀,金属的强度和塑、韧性指标均越高。
通过锻造或轧制,可使这些碳化物被打碎、并均匀分布,从而改善了它们对金属基体的削弱作用。
热塑性变形及的机理长大途中遗留下的再结晶晶粒,在变形停止后 (2)晶界滑移 热塑性变温形时度,由于足晶界够强度高降低,时使得,晶界会滑动易继于进续行;长大,此过程称为亚动态 1.
渐与主变形方向一致,形成流线。 一般来说,晶内滑移是最主要且最常见的 a)空位和原子的移动方向 b)晶内扩散 c)晶界扩散
热塑性变2形.机热理塑性变形的机理
变形机理主要有:晶内滑移、晶内孪生、晶界 滑移和扩散蠕变。
一般来说,晶内滑移是最主要且最常见的 (1)晶内滑移
热变形的主要机理是晶内滑移。高温时原子 间距加大,热振动和扩散速度增加,位错滑移、攀 移、交滑移及节点脱锚比低温容ቤተ መጻሕፍቲ ባይዱ;滑移系增多, 滑移灵便性提高,各晶粒之间变形更加协调;晶界 对位错运动阻碍作用减弱。
和晶界扩散。晶内扩散引起晶粒在拉应力
扩散蠕变示意 a)空位和原子的移动方向 b)晶内扩
散 c)晶界扩散
方向上的伸长变形(见图b),或在受压方
向上的缩短变形;而晶界扩散引起晶粒的
“转动”,如图c所示。扩散性蠕变既直
接为塑性变形作贡献,也对晶界滑移起调
节作用。
3.热塑性变形对金属组织和性能的影响
1)对组织的影响
1.热塑性变形时软化过程
(3)静态回复 在较低的温度下、或在较早阶段发生转变的
过程称为静态回复。它是变形后的金属自发地向 自由能降低的方向转变的过程。 (4)静态再结晶
仪器制造工艺学课后部分答案

仪器制造的关键技术有哪些?一、信息获取技术:1.传感器技术2.精密测试技术3.智能仪表技术4.现场溯源技术二、信息处理控制技术:1.现场总线技术2.智能控制技术3.系统集成技术三、精密制造技术:1.仪器现代设计技术2.仪器特种工艺技术3.现代管理技术选材的一般原则1.使用性能原则零件的使用性能是保证完成规定功能的必要条件2.工艺性能原则材料的工艺性能表示材料加工的难易程度3.经济性原则在首先满足零件性能要求的前提下,选材应使产品的成本尽可能低廉2-7试述灰铸铁、球墨铸铁、可锻铸铁的主要用途?1.灰铸铁主要用于制造汽车、齿轮箱体、仪器中的汽缸、仪器座底等承受压力及振动的基件。
球墨铸铁使用在一些受力复杂、综合性能要求较高、但无较大冲击力的场合下使用的机械零件,可成功的取代某些钢件。
3.可锻铸铁常用于制造那些壁薄、形状复杂,承受振动或冲击载荷的机件,如汽车和拖拉机的后桥外壳、活塞环、可锻铸铁管接头3-1什么是工艺过程控制要求和基本内容答:六大要素:人、机器、原材料、操作方法、测量、环境。
这六种要素在质量管理领域称为5IME3-2电子产品的制造过程可以分为几个阶段?试述每个阶段的主要内容答:产品设计性试制阶段:.产品设计工艺性审查2.制订产品设计性试制工艺方案3.编制必要的工艺文件4.进行工艺质量文件5.参加样机试生产和设计定型会。
产品生产性试制阶段:1.制订产品生产性试制的工艺方案2.编制全套工艺文件3.设计,制造新产品的全套工装,设计工序质量控制点,进行工艺分析4.进行工艺标准化审查5.组织指导产品试生产产品批量生产阶段:制订批量生产的工艺方案2.进行工艺质量评审。
3、组织,指导批量生产3-3什么是加工工艺过程工艺规程工艺规程在生产过程中起何作用?答:在机械产品生产过程中,直接改变生产对象形状、尺寸、性能及位置的过程称为工艺工艺过程。
按照一定的条件选择产品最合理的工艺过程,将实现这个工艺过程的程序、内容、方法工具、设备、材料以及每一个环节应该遵守的技术规程,用文字和图表的形状表示出来这就是工艺规程。
HRT6(变模)

由上面定义知Vm是膨胀膜初始压力体积(v0)与膨胀膜膨胀中间压 力体积(vm)之和,代入上式得:
· · · · · · · · · · · · · · · · · · · · · · · · · · · · · · · · · · · · · · · · · · · · · · · · · · · · · · · · · · · · · · · · · · · · · · · · · · · · · · · · · · · · · · · · · · · · · · · · · · · · · · (6) Pb · E0 2(1 ) (v0 vm ) V 上式也是GB50021-2001《岩土工程勘察规范》旁压试验采用的计算 公式。 由于膨胀膜内在的抗力和加压系统体积损失,计算岩体变形模量时 ,必须对其进行校正。则式5变为:
· · · · · · · · · · · · · · · · · · · · · · · · · · · · · · · · · · · · · · · · · · · · · · · · · · · · · · · · · · · · · (8)
公式8是PROBEX-1变模仪在岩石围岩孔进行变形试验计算变形模量 公式,而在极软岩或土中所做的变形试验应使用抱括膨胀膜内在的 抗力(Δ pi)的公式7计算其变形模量。上述各物理量的意义见下图。
实例7-1:向家坝水电站坝地基灌浆处理钻孔变模测试 向家坝水电站坝基岩体为白垩系下统灌口组下段(K1g1)砂岩,为 确定地基灌浆参数进行了灌浆试验。采用了灌前后钻孔变模测试来 评价地基经灌浆处理后,岩体变模提高情况。共计完成了 5 孔60 余 点变模测试工作。灌前变形模量较低,平均值为 1.73GPa ,低于 1.0GPa 测试点占 60.5% 。灌后变形模量大幅度提高,变形模量大于 1.0GPa测点占86.5%,平均值为4.58GPa。灌浆大大地改善砂岩地基 变形特性。
- 1、下载文档前请自行甄别文档内容的完整性,平台不提供额外的编辑、内容补充、找答案等附加服务。
- 2、"仅部分预览"的文档,不可在线预览部分如存在完整性等问题,可反馈申请退款(可完整预览的文档不适用该条件!)。
- 3、如文档侵犯您的权益,请联系客服反馈,我们会尽快为您处理(人工客服工作时间:9:00-18:30)。
温度场解析方法总结
12
轴承使用中的热变形问题
影响游隙的三个 主要因素
1. 温度变化 2. 装配应力 3. 旋转速度
urA urO A
urF urA T
u rO
urF
A
T
13
轴承按照DB DF布置时的热变形影响
极端条件下的热变形问题
14
机床热变形特点
❖ 体积大,热容量大,温升不高(15-25度),达到热平 衡时间长(4-6小时)
φ
图4-39 平面加工热变形
7
传统计算公式的问题
L L t 20 0 C
1.没有考虑零件形状对热变形的影响; 2.是用平均温度计算的,没有考虑温度 场的影响; 3.没有考虑零部件的装配环境;
8
车 削 中 轴 的 热 变 形
9
轴之非均匀非稳定温度场热变形
温度场特解:
T(r, z,t)
连续切削升温曲线 间断切削升温曲线
冷却曲线
0 τc
τb τ(min)
图2-9 车刀热变形曲线
max 1 e c
胡批:在我们大自然中, 很多规律的描述都离不 开指数函数。
式中 ξ—— 热伸长量;
ξmax —— 达到热平衡热伸长量; τ—— 切削时间;
τc —— 时间常数(热伸长量为热平衡热伸长量约63%的时间
1
r
z
rR
T
rR
KR
1
Hale Waihona Puke n1m112 n
2 m
h R
J
0
n
R
Fnm
I
1
(
m
R
R)
m I0 m R
Gnm 1 2 2 2 I0 m R m I1 m RR h sin m z m cos m z
10
非均匀温度场热变形求解过程 —温度场、热应力和热变形的关系
国内曾有四个教授从事热变形的研究: 费业泰 从事测量仪器及机械零部件热变形研究 陈子辰 从事机床热变形 候镇冰和张伯林 从事加工中热变形研究
1
热变形之影响
2
热源
工艺系统热源
工艺系统热源
内部热源 外部热源
热源的种类
切削热 摩擦热
环境热源 辐射热
❖ 切削热--导致工件或刀具热变形,绝对温升明显 ❖摩擦热——运动副摩擦,主要影响机床,绝对温升不明显 ❖环境热--温差,有温差就会有变形,还会产生热应力
aQ k
t 0
z
Gdzdt
z
4aQ
b2
Cnm • n J 0
n1 m1
nr
•
h sin m z m cosm z
轴之径向热变形
r1
R
T(r,
0
z, t )dr
4 aQ 2Rk
n1
Cnmn h sin
m1
mz
m
cosm z
R 0
J0 nrdr
r2 u rR R rR
R 2G
15
机床热变形对加工精度影响
其他机床热变形(图4-37)
❖ 立铣(图a) ❖ 外圆磨(图b) ❖ 导轨磨(图c)
b)外圆磨床受热变形形态
a)铣床受热变形形态
c)导轨磨床受热变形形态
图4-37 立式铣床、外圆磨床、导轨磨床受热变形
16
如何研究机床热变形? 陈子辰教授怎么干的?
• 创立温度敏感点概念,利用振动分析中的 模态分析理论建立热变形模型。
,常取3~4分钟)。
5
工件热变形
◆ 圆柱类工件热变形 ➢ 长度:
L L t
(4-17)
➢ 直径:
D D t
(4-18)
式中
ΔL, ΔD —— 长度和直径热变形量; L,D —— 工件原有长度和直径; α—— 工件材料线膨胀系数; Δt —— 温升。
➢ 例:长400mm丝杠,加工过程温升1℃,热伸长量为:
❖ 结构复杂,温度场和变形不均匀,对加工精度影响显著
。某外圆磨床,4-6小时内,砂轮和主轴间距减小27微米
车床热变形(图4-36)
200
ΔY
80
位移 /μm 温升 / ℃
150
前轴承温升 60
100
40
50
ΔX
20
0
12
34
运转时间 / h
a) 车床受热变形形态
b) 温升与变形曲线
图2-10 车床受热变形
φ/ 4
Δt —— 温升。
结果:加工时上表面升温,工件向
上拱起,磨削时将中凸部分磨平,
冷却后工件下凹。
例 : 高 600mm , 长 2000mm 的 床 身
,若上表面温升为3℃,则变形量
为: X L2 t 1.1 20002 3
8S
8 600
0.022 (mm)
此值已大于精密导轨平直度要求
• 试验中采用缩小模型法 • 传感器测温度分布、测变形量 • 提出补偿机床热变形误差的方法。
17
温度敏感点
18
空转试验
• 模擬3600 rpm轉速,主軸空轉、Z方向的滾 珠導螺桿、及Z方向的滑軌來回空跑之空切 削熱機下的溫度分佈與熱誤差。
• 切削條件:
– X軸進給 2mm/pass – Y軸進給 10 um – Z軸來回速度約50cm /sec – 主軸轉速 3600rpm
2.2.6 工艺系统热变形
热胀冷缩是物体的热物理性质之一,它对于精密机 械及精密仪器的设计、制造和使用均有重要的影响, 温度变化引起的工件热变形误差对加工精度的影响是 很大的。国内、外的专家学者在统计调查了热变形误 差对机械加工业的影响,以及热变形误差占加工总误 差的比例之后,他们普遍认为在目前的精密加工中, 热变形误差已占到总误差的40-70%。
L L t
1.1105 400 1 4.4 103(mm)
4.4(m)
5级丝杠累积误差全长≤5μm,可见热变形的严重性
6
◆ 板类工件单面加工时的热变形(图4-39)
X L2 t
8S
(5-19)
式中 ΔX —— 变形挠度;
S
L,S ——工件原有长度和厚度;
L
α—— 工件材料线膨胀系数;
19
空转温升
溫升(℃)
各觀察點之溫升圖
12
10
8
X軸滑軌
Y軸滑軌
6
Z軸滑軌
砂輪
4
主軸軸承
2
0
0
50 100 150 200 250 300 350
時間 (min)
20
空转主轴热位移
displacement (um)
主軸位移量
14
12
10
8
X
Y 6
Z
4
2
0
0
100
200
300
400
500
time (min)
3
切削热产生及分布
Qc
R1Q1
R2
Q2
QT 1 R2 Q2
Qw 1 R1 Q1
4
刀具热变形对加工精度影响
刀具热变形
◆ 特点
➢ 体积小,热容量小, 达到热平衡时间较短
➢ 温升高,变形不容忽 视(达0.03 ~0.05mm)
◆ 变形曲线(图2-9)
ξ(μm)
ξmax
0.63ξmax
21
减小热变形对加工精度影响的措施
减少热源发热和隔离热源
❖ 减少热量产生:1)控制切削用量切削热、降切削速度 改变刀具几何参数;2)降低摩擦副的摩擦系数,流体轴 承;3)充分冷却“淋浴” ❖ 隔离热源:将液压系统从机床中分离,或用隔热罩