盘套类零件的加工
项目八 简单盘套类零件的编程及仿真加工(一)
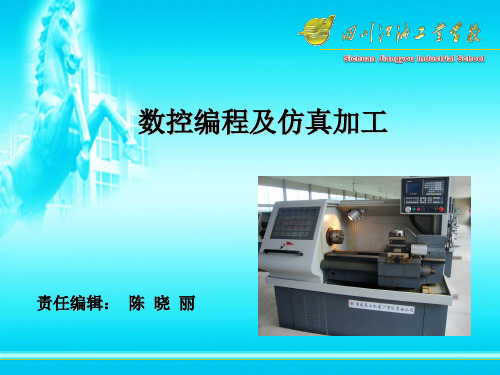
盘套类零件内孔精度要求较高,针对需多次工序才能完成的盘套类零件, 为保证其精度要求,须以内孔为定位基准,才能保证外圆轴线和内孔轴线的 同轴度要求,此时要用心轴定位。 ① 圆柱心轴 利用心轴的圆柱表面与工件定位配合,并保持较小的间隙,便于工件的装卸; 夹紧力较大,但定心精度较锥度心轴低,工件靠螺母压紧,如图8-1-5。
3、形状、位置精度
形位公差,是零件精度要求的重要内容,也是确定和影响车削工艺的 重要因素,尤其是按照其要求确定零件的定位基准和测量基准的重要指标。
项目八 简单盘套类零件的编程及仿真加工 图8-1-1 盘套类零件的技术要求
项目八 简单盘套类零件的编程及仿真加工
二、盘套类零件的装夹与定位方法
盘套类零件的内/外圆柱面、端面与基准轴线都存在相应的形位精度要求, 盘类零件的精基准可以选择外圆,但常以中心孔及一个端面为精加工基准。
图8-1-2 三爪卡盘装夹工件
项目八 简单盘套类零件的编程及仿真加工
② 薄壁套类零件的刚度差,装夹不当或夹紧力过大,易导致工件变形, 则需要采用开口套装夹,或者扇形卡爪,如图8-1-3所示。
图8-1-3 薄壁套类零件的装夹
任务八 简单盘套类零件的编程与仿真加工
2、四爪单动卡盘
四爪可以单独移动,夹紧力较大,适用于
定性和精度。当使用大直径镗孔刀杆时,稳定性便得到增强;但由于受零件 孔径所允许的空间限制,这种可能性也经常受到限制,故此,必须考虑到排 屑和刀具的径向移动。
项目八 简单盘套类零件的编程及仿真加工
四、盘套类零件刀具及其切削用量的选用
加工内孔是盘套类零件的特征之一,根据内孔的工艺要求,加工方法较 多,常用的有钻孔、扩孔、铰孔、镗孔和磨孔等。内孔加工时常用的刀具有 中心钻、麻花钻及内孔镗刀等。 1、钻孔
精选盘套类零件加工工艺
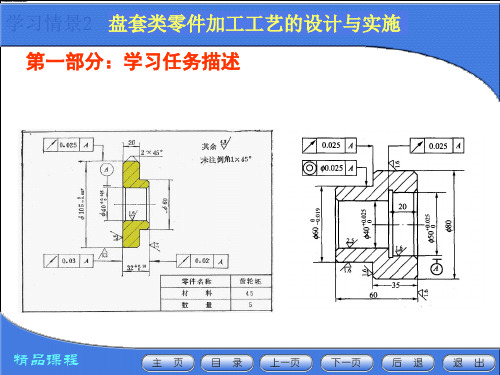
盘套类零件加工工艺的设计与实施
第三部分 学习情境
步骤一:资讯
案例教学
一单元 盘套类零件的功用、结构特点、技术要求、材料与毛坯
(二)套类零件
2、套类零件的主要技术要求 几何形状精度: 内孔的形状精度,应控制在孔径公差以内,有些精密轴套控制在孔径公差的1/2~1/3,甚至更严。对于长的套件除了圆度要求外,还应注意孔的圆柱度。 外圆表面的形状精度控制在外径公差以内。 相互位置精度: 当内孔的最终加工是在装配后进行时,套类零件本身的内外圆之间的同轴度要求较低;如最终加工是在装配前完成则要求较高,一般为0.01~0.05mm。当套类零件的外圆表面不需加工时,内外圆之间的同轴度要求很低。 套孔轴线与端面的垂直度精度,当套件端面在工作中承受载荷,或虽不承受载荷但其作为加工中的定位基准面和装配中的装配基准时,其要求较高,一般为0.01~0.05mm。 表面粗糙度: 为保证套类零件的功用和提高其耐磨性,内孔表面粗糙度Ra值为2.5—0.16µm,有的要求更高达Ra0.04µm。外径的表面粗糙度达Ra5~0.63µm。
盘套类零件加工工艺的设计与实施
第三部分 学习情境
步骤一:资讯
案例教学
一单元 盘套类零件的功用、结构特点、技术要求、材料与毛坯
(二)套类零件
1、套类零件的功用及结构特点 套筒类零件是一种应用范围很广的常见机械零件。在机器中主要起支承和导向作用,例如,支承回转轴的各种形式的滑动轴承、夹具体中的导向套、液压系统中的液压缸以及内燃机上的气缸套等,如图2-4所示。套筒零件由于功用不同,其结构和尺寸有较大差别,但也有共同之处:零件结构不太复杂,主要由有较高同轴要求的内外圆表面组成,零件的壁厚较小,易产生变形,轴向尺寸一般大于外圆直径,长径比大于5的深孔比较多。
第二节盘套类零件工艺设计第二节盘类零件的制造工艺(精)

第二节 盘、套类零件工艺设计一、盘、套类零件特点(一)盘类零件1、功用盘类零件在机器中主要起支承、连接作用。
2、结构特点盘类零件主要由端面、外圆、内孔等组成,一般零件直径大于零件的轴向尺寸。
3、技术要求盘类零件往往对支承用端面有较高平面度及轴向尺寸精度及两端面平行度要求;对转接作用中的内孔等有与平面的垂直度要求,外圆、内孔间的同轴度要求等。
(二)套类零件1、功用套类零件在机器中主要起支承和导向作用。
2、结构特点零件主要由有较高同轴要求的内外圆表面组成,零件的壁厚较小,易产生变形,轴向尺寸一般大于外圆直径。
3、主要技术要求孔与外圆一般具有较高的同轴度要求;端面与孔轴线(亦有外圆的情况)的垂直度要求;内孔表面本身的尺寸精度、形状精度及表面粗糙度要求;外圆表面本身的尺寸、形状精度及表面粗糙度要求等。
二、盘、套类零件制造工艺(教学)案例案例3:支承块加工。
零件图三维图1、零件工艺性分析(1)零件材料:45钢。
切削加工性良好。
刀具材料及几何参数选择同案例1。
(2)零件组成表面:两端面,外圆面,中间孔及沉孔,安装孔,侧面,十字槽,倒角等。
(3)零件结构分析:两端面起支承作用,光度要求高,轴向尺寸在安装后通过配磨保证两件等高。
轴向尺寸小,为典型的盘类零件。
(4)主要技术条件:端面粗糙度要求Ra0.4µm两端面保证平行。
2、零件工艺设计(1)毛坯选择按零件形状及要求,可选棒料。
(2)基准及安装方案分析该零件的主要基准无疑为两端面,安装孔及十字槽等表面加工均为端面作定位基准,侧表面位置,孔的中心考虑精度要求不高,且该零件为单件生产,采用划线确定;两平面的平行度则采用互为基准的方法保证。
(3)零件表面加工方法按端面Ra0.4µm的要求,其终加工方法选择精磨。
为确保零件安装平整,安装孔应与端面垂直,在加工安装孔,铣十字槽前先粗磨好平面,孔及槽等表面加工后再精磨平面。
侧面采用铣削,安装孔采用钻削,中间孔及沉孔可采用车削。
加工盘套类零件
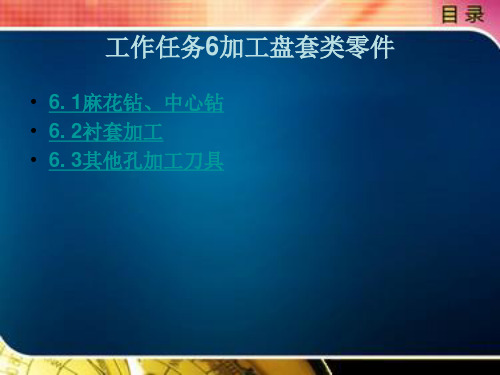
• 中心钻是用来加工轴类零件中心孔的刀具,其结构主要有三种形式: 带护锥中心钻(图6. 3 (a)、无护锥中心钻(图6. 3 ( b) )和弧形中心钻 (图6.3 (c) )
上一页 返回
6. 2 衬套加工
• 6. 2. 1钻孔加工 • 本次任务是掌握标准麻花钻的刃磨,并利用标准麻花钻进行孔加工
两条主切削刃刃口不能退火; • ⑤表面粗糙度:主后面Ra 1. 6 μm(两处)。 • 2.操作过程 • 钻孔时,应选择适当的切削用量。为使钻孔时钻头易定心,可采取车
端面→粗车外圆→钻中心孔→钻通孔→精车外圆的工艺路线。
上一页 下一页 返回
6. 2 衬套加工
• 衬套加工工艺过程(重点为钻孔)如下: • (1)装夹找正:毛坯伸出卡爪约65 mm,利用划针找正并夹紧; • (2)车端面:采用450粗车刀,手动车端面,车平即可,表面粗糙度达到
内孔车刀、油石、冷却用水、0. 02 mm/ (0~150) mm的游标卡尺等。 • 2)通孔车刀刃磨 • 衬套加工(重点为车孔)工序采用通孔车刀,采用正刃倾角车孔刀(前排
屑),其刃磨过程为:粗磨主后面、粗磨副后面、粗磨前面、精磨主后 面、精磨副后面、精磨前面、磨卷屑槽、修磨刀尖圆弧。
上一页 下一页 返回
粗磨卷屑槽、精磨副后面、精磨主后面、精磨前面、精磨卷屑槽、倒 角。 • 刃磨内沟槽车刀应注意刀刃的平直及角度、形状的正确与对称。刃磨 车槽刀时,通常左侧副后面磨出即可,刀宽的余量应放在车刀右侧磨 去。在刃磨车槽刀副切削刃时,刀头与砂轮表面的接触点应放在砂轮 边缘上,轻轻移动,仔细观察和修整副切削刃的直线度。 • 刃磨内沟槽车刀选取的几何参数如下: • ①切削刃宽度a= (4 ± 10.1) mm; • ②刀头长度L=4一5 mm ;
对机床盘套类零件的生产加工工艺探讨
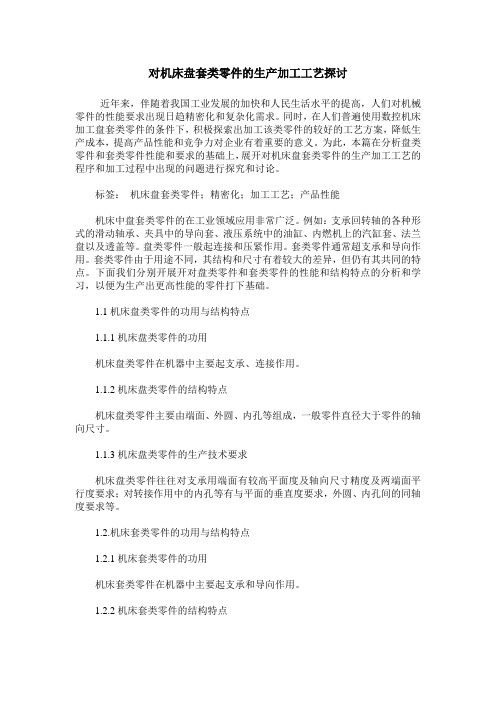
对机床盘套类零件的生产加工工艺探讨近年来,伴随着我国工业发展的加快和人民生活水平的提高,人们对机械零件的性能要求出现日趋精密化和复杂化需求。
同时,在人们普遍使用数控机床加工盘套类零件的条件下,积极探索出加工该类零件的较好的工艺方案,降低生产成本,提高产品性能和竞争力对企业有着重要的意义。
为此,本篇在分析盘类零件和套类零件性能和要求的基础上,展开对机床盘套类零件的生产加工工艺的程序和加工过程中出现的问题进行探究和讨论。
标签:机床盘套类零件;精密化;加工工艺;产品性能机床中盘套类零件的在工业领域应用非常广泛。
例如:支承回转轴的各种形式的滑动轴承、夹具中的导向套、液压系统中的油缸、内燃机上的汽缸套、法兰盘以及透盖等。
盘类零件一般起连接和压紧作用。
套类零件通常超支承和导向作用。
套类零件由于用途不同,其结构和尺寸有着较大的差异,但仍有其共同的特点。
下面我们分别开展开对盘类零件和套类零件的性能和结构特点的分析和学习,以便为生产出更高性能的零件打下基础。
1.1机床盘类零件的功用与结构特点1.1.1机床盘类零件的功用机床盘类零件在机器中主要起支承、连接作用。
1.1.2机床盘类零件的结构特点机床盘类零件主要由端面、外圆、内孔等组成,一般零件直径大于零件的轴向尺寸。
1.1.3机床盘类零件的生产技术要求机床盘类零件往往对支承用端面有较高平面度及轴向尺寸精度及两端面平行度要求;对转接作用中的内孔等有与平面的垂直度要求,外圆、内孔间的同轴度要求等。
1.2.机床套类零件的功用与结构特点1.2.1机床套类零件的功用机床套类零件在机器中主要起支承和导向作用。
1.2.2机床套类零件的结构特点机床零件主要由有较高同轴要求的内外圆表面组成,零件的壁厚较小,易产生变形,轴向尺寸一般大于外圆直径。
1.2.3、机床套类零件的主要技术要求孔与外圆一般具有较高的同轴度要求;端面与孔轴线(亦有外圆的情况)的垂直度要求;内孔表面本身的尺寸精度、形状精度及表面粗糙度要求;外圆表面本身的尺寸、形状精度及表面粗糙度要求等。
任务1法兰盘的数控编程与仿真

《数控编程与仿真》教案首页学时学时掌握盘类零件的结构特点和加工工艺的特点,正确分析盘类零件的加工工艺。
的编程格式及应用,掌握盘类通过掌握知识、掌握技能,培养学生学会学习、学会工作的学习方法的能力掌握数控编程方法与相关指令,培养学生善于劳动组织与实施的社会能力环节内容意图 任务描述(15")1.提问:(1)什么是盘类零件?(2)盘类零件能否用轴类零件的指令进行加工?学生通过观看数控加工零件的视频,回答以上问题。
2.引入加工零件名称:连接法兰盘轮廓 加工零件类型描述:盘类零件任务内容描述:熟悉机床操作流程,编制连接法兰盘的程序并进行仿真加工。
关注学生课前知识储备状态 通过多媒体手段引入教学任务分析 本任务会用到G94指令、G72指令 等盘类零件加工指令。
通过本任务的学习,使学生熟记指令的功能与作用,运用该指令编制程序。
学生明白重难点理论知识讲解 (35") 1.盘类零件的结构特点盘类零件一般是指径向尺寸比轴向尺寸(即厚度)大,且最大与最小内外圆直径相差较大,以端面面积大为主要特征的零件。
机器上各种衬套、齿轮带轮、轴承套等属于盘类零件如下图所示,因支撑与配合的需要,盘类零件一般有内孔。
2.G94端面单一固定车削循环外圆车削:格式G00X ZG94X(U) Z(W) FX:切削终点坐标值Z: 切削终点坐标值F:切削速度R :切削起点和切削终点Z 轴坐标值之差;功能:实现端面或者锥度端面切削,(模态指令)。
走刀路线分析1)X 向快速进至与终点坐标同一X 坐标的位置上;2)Z 向以进给速度车削至终点位置; 3)X 向以进给速度退至与起点同一X 坐标的位置;4)Z 向快速退回起点3.锥端面车削循环 G94 X(U)_Z(W)_ R_ F_;格式G00X ZG94X(U) Z(W) R__FX:切削终点坐标值Z: 切削终点坐标值F:切削速度R :切削起点(B 点)和切削终点(C点)Z 坐标值之差。
盘套类零件的车削

盘套类零件的车削1. 盘类零件的加工盘类零件的轴向L(纵向)尺寸一般远小于径向D尺寸,且最大外圆直径D与最小内圆直径d 相差较大,并以端面面积大为主要特征,如图6-1所示。
这类零件有:圆盘、台阶盘以及带有其他形状的齿形盘、花盘、轮盘和圆盘形零件等。
在这类零件中,较多部分是作为动力部件,配合轴杆类零件传递运动和转矩。
盘类零件的主要表面为内圆面、外圆面及端面等,其加工方法与其毛坯材料、加工余量有关.分别简介如下。
一、工艺分析1.选材与选毛坯盘类零件一般需承受交变载荷,工作时处于复杂应力状态。
其材料应具有良好的综合力学性能,因此常用45钢或40Cr钢先做锻件,并进行调质处理,较少直接用圆钢做毛坯,但对于承受载荷较小圆盘类零件或主要用来传递运动的齿轮,也可以直接用铸件或采用圆钢、有色金属件和非金属件毛坯。
2.确定工序间的加工余量盘类零件的毛坯加工余量在选毛坯时就已确定,但每一个工序的加工,须为下一工序留下加工余量。
3.定位基准与装夹方法盘类零件内孔、端面的尺寸精度、形位精度、表面粗糙度,是盘类零件加工的主要技术要求和要解决的主要问题。
盘类零件加工时通常以内孔、端面定位或外圆、端面定位、使用专用心轴(一种带孔工件的夹具)或卡盘装夹工件。
二、工艺过程特点一般来说,车削加工通常以内孔、端面定位、插人心轴装夹工件,这符合基准重合、基准统一原则。
车内孔时,车削步骤的选择原则除了与车外圆有共同点之外,还有下列几点:1)为保证内外圆同轴,最好采用"一刀落"的方法,即粗车端面、粗车外圆、钻孔、粗镗孔、精镗孔、精车端面、精车外圆、倒角、切断、调头车另一端面和倒角。
如果零件尺寸较大,棒料不能插入主轴锥孔中,可以将棒料比要求尺寸放长lomm左右切断。
在镗孔时不要镗穿,以增加刚性,车到需要尺寸以后再切断。
2)对于精度要求较高的内孔,可按下列步骤进行车削,即钻孔、粗铰孔、精铰孔、精车端面、磨孔。
但必须注意,在粗铰孔时应留铰孑L或磨孔余量。
盘类零件的制造工艺和套类零件的制造工艺
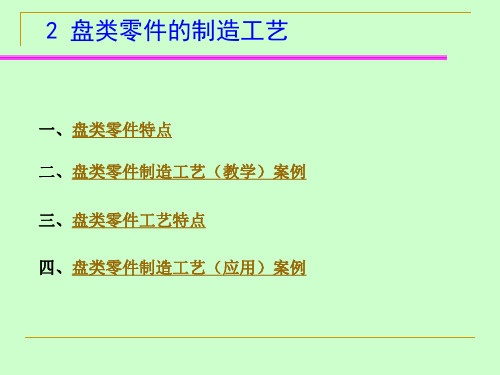
Байду номын сангаас 零件加工工艺过程卡
二、盘类零件制造工艺(教学)案例
5、零件加工仿真
支承块加工仿真
二、盘类零件制造工艺(教学)案例
6、本零件加工小结 (1)零件安装 (2)表面加工 (3)主要表面保证
三、盘类零件工艺特点
1、毛坯选择 2、基准选择 3、安装方案 (1)采用三爪卡盘安装 (2)用专用夹具安装 (3)用虎钳安装 4、表面加工方法 5、典型工艺路线 下料(或备坯)→ 去应力处理 → 粗车 → 半精 车 → 平磨端面(亦可按零件情况不作安排)→ 非回转面 加工 → 去毛刺 → 中检 → 最终热处理 → 精加工主要 表面(磨或精车)→ 终检
零件加工工艺过程卡
二、套类零件制造工艺案例
3、零件加工过程
轴套加工过程
三、套类零件制造工艺特点
1、毛坯选择 2、套类零件的基准与安装 3、主要表面的加工 4、典型工艺路线 备坯→ 去应力处理 → 基准面加工 → 孔加工粗加 工 → 外圆等粗加工 → 组织处理 → 孔半精加工 → 外圆 等半精加工 → 其它非回转面加工 → 去毛刺 → 中检→ 零件最终热处理 → 精加工孔 → 精加工外圆的等 → 清洗 →终检
2 盘类零件的制造工艺
一、盘类零件特点
二、盘类零件制造工艺(教学)案例 三、盘类零件工艺特点 四、盘类零件制造工艺(应用)案例
一、盘类零件特点
1、盘类零件一般功用
2、结构特点 3、技术要求
二、盘类零件制造工艺(教学)案例
案例3:支承块加工
零 件 三 维 图
二、盘类零件制造工艺(教学)案例
零件图
四、盘类零件制造工艺(应用)案例
3、零件加工过程
连接盘加工仿真