普通三角螺纹加工尺寸的计算
螺纹计算

以外螺纹为例,普通螺纹的小径与其公称直径之间存在如下关系:d1=d﹣1.0825P,标准螺纹牙深为L=5/8H=0.5412P;数控车削中多使用机夹刀具和机夹刀片,其中机夹刀片存在刀尖圆弧半径R值,R值在车削中对螺纹牙深有影响,如图2所示,h=R,外螺纹牙顶到标准三角形底的尺寸是
K=7/8H=0.7578P,因此数控车削普通螺纹牙深计算公式为L′=K﹣h
=0.7578P﹣R,此时车出的牙底宽度不是P/4,也不是一个平面,而是以R为半径的中心角为90°的一段圆弧。
目前使用的数控机加工类教材对外螺纹牙深计算公式并不统一,多以0.6495P 作为牙深,其中参数0.6495应该来自于普通螺纹中径计算公式,d2=d﹣2×3/8H=d﹣0.6495P,综上所述,这个牙深计算方法应用于数控车削普通螺纹
是错误的,在实践中证明也完全不可行,应当及时更正。
螺纹件的加工——三角形螺纹的加工
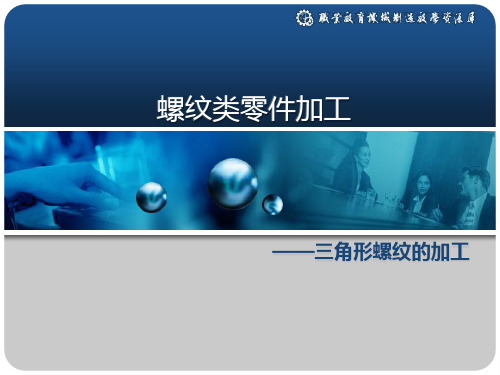
三、计划、决策
(一)零件图分析
图样内容
制
零件材料
45#钢
获取的信息
定
毛坯尺寸
φ30X100棒料
零件加工部位 φ30外圆、倒角及端面
工
零件尺寸公差 φ26外圆直径尺寸公差为-0.05;
零件总长度30的尺寸公差为-0.1。
艺 零件表面粗糙 φ26外圆Ra3.2
度
零件技术要求 零件加工表面上,不应有划痕、擦伤等损伤零件表面 的缺陷
Produced by Мiss Хiè
二、资讯
(十)车削三角形螺纹方法
1.提开合螺母法 适用于退刀时采用打开开合螺母的场合。
操作方法是:启动车床,螺纹车刀在工件外圆表面对刀后,移动车刀在 工件的起点位置,横向进给后(第一刀0.5mm左右,以后随着进给次数 的增加逐渐减少),合上开合螺母纵向进给,第一次进给结束后,在螺 母结束长度位置迅速拉开开合螺母,使刀架和丝杠脱离,然后纵向退刀 至螺母起点,重新横向进刀后,再合上开合螺母开始第二次进给,,如 此往复车削至螺纹完成。采用这种操作方法只适合车削丝杠螺距是工件 螺距整数倍的螺距的螺纹,否则会产生乱牙。
螺纹类零件加工
——三角形螺纹的加工
教学流程
1
任务布置
2
资讯
3
计划、决策
4
工作任务实施
5
自测与检查
6
评价
Produced by Мiss Хiè
一、任务布置
(一)任务布置
技术要求
1.毛坯φ30×100 2.未注倒角均为1×45° 3.零件加工表面上,不应该有划 痕、擦伤等损伤零件表面的缺 陷。 Produced by Мiss Хiè
Produced by Мiss Хiè
普通三角螺纹加工尺寸的计算
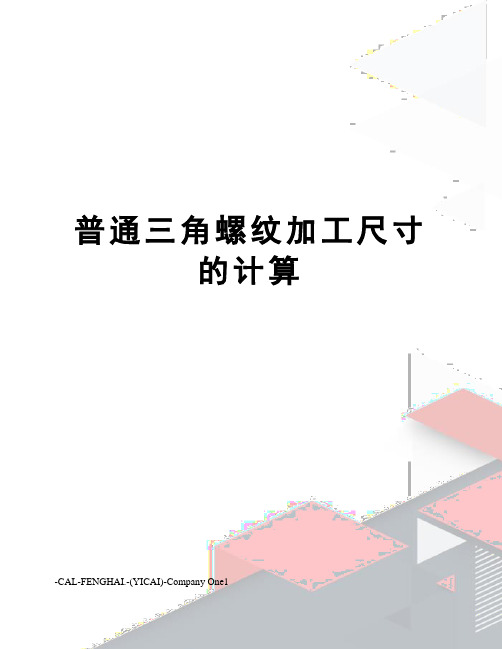
普通三角螺纹加工尺寸的计算-CAL-FENGHAI.-(YICAI)-Company One1普通三角形螺纹加工尺寸的计算驻马店高级技工学校—王俊荣摘要:螺纹加工中比较重要的是尺寸的计算,只有正确的计算才能加工出合格的螺纹。
因为三角形螺纹的牙型比较小,加工时由于车刀的挤压使牙型外胀,还有螺纹刀刀尖不是削平的梯形,而是圆弧形的,所以有必要把理论尺寸和实际加工尺寸之间的关系讲明白,让螺纹的加工变得更准确。
关键词:三角形螺纹牙型高度总的背吃刀量多线螺纹加工我们在加工螺纹时螺纹尺寸的计算十分重要,特别是螺纹理论尺寸与实际加工尺寸的不同给学生的学习带来很多困难,三角形螺纹加工尺寸的计算是加工三角形螺纹的重要部分,只有掌握正确的计算方法,才能加工出合格的产品。
一、普通三角形螺纹的基本牙型普通三角形螺纹的基本牙型如图1所示,各基本尺寸的名称如下:图1 普通三角螺纹基本牙型D—内螺纹大径(公称直径);d—外螺纹大径(公称直径);D2 —内螺纹中径;d2—外螺纹中径;D1—内螺纹小径;d1—外螺纹小径;P—螺距;H—原始三角形高度。
三角形螺纹的基本尺寸有:1、牙型角α螺纹轴向剖面内螺纹两侧面的夹角。
普通三角形螺纹α=60o,2、螺距P 它是沿轴线方向上相邻两牙间对应点的距离。
3、导程P h在同一条螺旋线上的相邻两牙在中径线上对应两点之间的轴向距离。
4、牙型高度:外螺纹牙顶和内螺纹牙底均在H/8处削平,外螺纹牙底和内螺纹牙顶均在H/4处削平。
h1=H-H/8-H/4=5/8H=5、大径:d=D(公称直径)6、中径:d 2=D2= d -2×3/8H=d7、小径:d 1=D1= d -2×5/8H= d二、加工普通三角形外螺纹前螺杆直径和加工时吃刀深度的计算。
1、M20的外螺纹,公称直径是大径20,高速车削三角形螺纹时,受车刀挤压后会使螺纹大径尺寸胀大,因此车螺纹外圆的直径,应比螺纹大径小,当螺纹螺距为~时,外径一般可以小~。
三角螺纹的编程与加工解析

二、螺纹加工切削用量选择
1、主轴转速n
2、进给速度F
单头螺纹:F=P 多头螺纹:F=L
P:零件的螺距,单位mm K:保险系数,一般取80
石家庄市工业职业技术学校数字资源
二、螺纹加工切削用量选择
3、切削深度(背吃刀量)
(1)切削方式
(2)切削深度
直进法
斜进法
t1=t2=t3=t4
t1>t2 >t3 >t4
编程步骤
2.2确定加工工艺 换尖刀加工 M22×1.5螺纹
G92 X20.2 Z-18 F1.5;
oz
A x
石家庄市工业职业技术学校数字资源
编程步骤
2.2确定加工工艺 换尖刀加工 M22×1.5螺纹
G92 X20.05 Z-18 F1.5;
oz
A x
石家庄市工业职业技术学校数字资源
M27×2 的螺纹该 如何加工 呢?
(2) 螺纹牙型高度 h=0.65P
(3) 螺纹大径 D=M
石家庄市工业职业技术学校数字资源
一、螺纹加工尺寸分析
3、螺纹加工轴向尺寸
轴向尺寸=L1+L+L2
L1:切入段长度(2~5mm), 一般大于2P。
L:螺纹加工有效长度。
L2:切出段长度(1~3mm), 若有退刀槽,则为退刀槽的一半。
石家庄市工业职业技术学校数字资源
石家庄市工业职业技术学校数字资源
编程步骤
4、确定加工工艺
换尖刀加工 M27×2螺纹
M08 M03 S400; G00 X28;
Z-16; G92 X26.1 Z-35 F2;
X25.5; X24.9; X24.5; X24.4; X24.4; M09; M30;
螺纹计算公式

一、挤牙丝攻内孔径计算公式:公式:牙外径-1/2×牙距例1:公式:M3×0.5=3-(1/2×0.5)=2.75mmM6×1.0=6-(1/2×1.0)=5.5mm例2:公式:M3×0.5=3-(0.5÷2)=2.75mmM6×1.0=6-(1.0÷2)=5.5mm二、一般英制丝攻之换算公式:1英寸=25.4mm(代码)例1:(1/4-30)1/4×25.4=6.35(牙径)25.4÷30=0.846(牙距)则1/4-30换算成公制牙应为:M6.35×0.846例2:(3/16-32)3/16×25.4=4.76(牙径)25.4÷32=0.79(牙距)则3/16-32换算成公制牙应为:M4.76×0.79三、一般英制牙换算成公制牙的公式:分子÷分母×25.4=牙外径(同上)例1:(3/8-24)3÷8×25.4=9.525(牙外径)25.4÷24=1.058(公制牙距)则3/8-24换算成公制牙应为:M9.525×1.058四、美制牙换算公制牙公式:例:6-326-32 (0.06+0.013)/代码×6=0.1380.138×25.4=3.505(牙外径)25.4÷32=0.635(牙距)那么6-32换算成公制牙应为:M3.505×0.635二、1、孔内径计算公式:牙外径-1/2×牙距则应为:M3.505-1/2×0.635=3.19那么6-32他内孔径应为3.192、挤压丝攻内孔算法:下孔径简易计算公式1:牙外径-(牙距×0.4250.475)/代码=下孔径例1:M6×1.0M6-(1.0×0.425)=5.575(最大下孔径)M6-(1.0×0.475)=5.525(最小)例2:切削丝攻下孔内径简易计算公式:M6-(1.0×0.85)=5.15(最大)M6-(1.0×0.95)=5.05(最小)M6-(牙距×0.860.96)/代码=下孔径例3:M6×1.0=6-1.0=5.0+0.05=5.05五、压牙外径计算简易公式:1.直径-0.01×0.645×牙距(需通规通止规止)例1:M3×0.5=3-0.01×0.645×0.5=2.58(外径)例2:M6×1.0=6-0.1×0.645×1.0=5.25(外径)六、公制牙滚造径计算公式:(饱牙计算)例1:M3×0.5=3-0.6495×0.5=2.68(车削前外径)例2:M6×1.0=6-0.6495×1.0=5.35(车削前外径)七、压花外径深度(外径)外径÷25.4×花齿距=压花前外径例:4.1÷25.4×0.8(花距)=0.13 压花深度应为0.13八、多边形材料之对角换算公式:1.四角形:对边径×1.414=对角径2.五角形:对边径×1.2361=对角径3.六角形:对边直径×1.1547=对角直径公式2: 1.四角:对边径÷0.71=对角径2.六角:对边径÷0.866=对角径九、刀具厚度(切刀):材料外径÷10+0.7参考值十、锥度的计算公式:公式1:(大头直径-小头直径)÷(2×锥度的总长)=度数等于查三角函数值公式2:简易(大头直径-小头直径)÷28.7÷总长=度数滚牙径计算公式一、60°牙型的外螺纹中径计算及公差(国标GB 197/196)a. 中径基本尺寸计算:螺纹中径的基本尺寸=螺纹大径-螺距×系数值公式表示:d/D-P×0.6495例:外螺纹M8螺纹中径的计算8-1.25×0.6495=8-0.8119≈7.188b.常用的6h外螺纹中径公差(以螺距为基准)上限值为”0”下限值为P0.8-0.095 P1.00-0.112 P1.25-0.118 P1.5-0.132 P1.75-0.150 P2.0-0.16P2.5-0.17上限计算公式即基本尺寸,下限值计算公式d2-hes-Td2即中径基本尺寸-偏差-公差M8的6h级中径公差值:上限值7.188 下限值:7.188-0.118=7.07C常用的6g级外螺纹中径基本偏差: (以螺距为基准)P 0.80-0.024 P 1.00-0.026 P1.25-0.028 P1.5-0.032P1.75-0.034 P2-0.038 P2.5-0.042上限值计算公式d2-ges即基本尺寸-偏差下限值计算公式d2-ges-Td2即基本尺寸-偏差-公差例M8的6g级中径公差值:上限值7.188-0.028=7.16 下限值:7.188-0.028-0.118=7.042注:①以上的螺纹公差是以粗牙为准,对细牙的螺纹公差相应有些变化,但均只是公差变大,所以按此控制不会越出规范界限,故在上述中未一一标出.②螺纹的光杆坯径尺寸在生产实际中根据设计要求的精度和螺纹加工设备的挤压力的不同而相应比设计螺纹中径尺寸加大0.04—0.08之间,为螺纹光杆坯径值,例我们公司的M8外螺纹6g级的螺纹光杆坯径实在7.08—7.13即在此范围.③考虑到生产过程的需要外螺纹在实际生产的未进行热处理和表面处理的中径控制下限应尽量保持在6h级为准二、60°内螺纹中径计算及公差(GB 197 /196)a. 6H级螺纹中径公差(以螺距为基准)上限值:P0.8+0.125 P1.00+0.150 P1.25+0.16 P1.5+0.180P1.25+0.00 P2.0+0.212 P2.5+0.224下限值为”0”,上限值计算公式2+TD2即基本尺寸+公差例M8-6H内螺纹中径为:7.188+0.160=7.348 上限值:7.188为下限值b. 内螺纹的中径基本尺寸计算公式与外螺纹相同即D2=D-P×0.6495即内螺纹中径螺纹大径-螺距×系数值c. 6G级螺纹中径基本偏差E1(以螺距为基准)P0.8+0.024 P1.00+0.026 P1.25+0.028 P1.5+0.032P1.75+0.034 P1.00+0.026 P2.5+0.042 例:M8 6G级内螺纹中径上限值:7.188+0.026+0.16=7.374下限值:7.188+0.026=7.214上限值公式2+GE1+TD2即中径基本尺寸+偏差+公差下限值公式2+GE1即中径尺寸+偏差三、外螺纹大径的计算及公差(GB 197/196)a. 外螺纹的6h大径上限值即螺纹直径值例M8为φ8.00上限值公差为”0”b. 外螺纹的6h级大径下限值公差(以螺距为基准)P0.8-0.15 P1.00-0.18 P1.25-0.212 P1.5-0.236 P1.75-0.265P2.0-0.28 P2.5-0.335大径下限计算公式:d-Td 即螺纹大径基本尺寸-公差例:M8外螺纹6h大径尺寸:上限为φ8,下限为φ8-0.212=φ7.788c. 外螺纹6g级大径的计算与公差6g级外螺纹的基准偏差(以螺距为基准)P0.8-0.024 P1.00-0.026 P1.25-0.028 P1.5-0.032 P1.25-0.024 P1.75 –0.034P2.0-0.038 P2.5-0.042上限计算公式d-ges 即螺纹大径基本尺寸-基准偏差下限计算公式d-ges-Td 即螺纹大径基本尺寸-基准偏差-公差例: M8 外螺纹6g级大径上限值φ8-0.028=φ7.972下限值φ8-0.028-0.212=φ7.76注:①螺纹的大径是由螺纹光杆坯径及搓丝板/滚丝轮的牙型磨损程度来决定的,而且其数值在同样毛坯及螺纹加工工具的基础上与螺纹中径成反比出现即中径小则大径大,反之中径大则大径小.②对需进行热处理和表面处理等加工的零件,考虑到加工过程的关系实际生产时应将螺纹大径控制在6h级的下限值加0.04mm以上,如M8的外螺纹在搓(滚)丝的大径应保证在φ7.83以上和7.95以下为宜.四、内螺纹小径的计算与公差a. 内螺纹小径的基本尺寸计算(D1)螺纹小径基本尺寸=内螺纹基本尺寸-螺距×系数例:内螺纹M8的小径基本尺寸8-1.25×1.0825=6.646875≈6.647b. 内螺纹6H级的小径公差(以螺距为基准)及小径值计算P0.8 +0. 2 P1.0 +0. 236 P1.25 +0.265 P1.5 +0.3 P1.75 +0.335P2.0 +0.375 P2.5 +0.48内螺纹6H级的下限偏差公式D1+HE1即内螺纹小径基本尺寸+偏差注:6H级的下偏值为“0”内螺纹6H级的上限值计算公式=D1+HE1+TD1即内螺纹小径基本尺寸+偏差+公差例:6H 级M8内螺纹小径的上限值6.647+0=6.6476H级M8内螺纹小径的下限值6.647+0+0.265=6.912c. 内螺纹6G级的小径基本偏差(以螺距为基准)及小径值计算P0.8 +0.024 P1.0 +0.026 P1.25 +0.028 P1.5 +0.032 P1.75 +0.034P2.0 +0.038 P2.5 +0.042内螺纹6G级的小径下限值公式=D1+GE1即内螺纹基本尺寸+偏差例: 6G级M8内螺纹小径的下限值6.647+0.028=6.6756G级M8内螺纹小径的上限值公式D1+GE1+TD1即内螺纹基本尺寸+偏差+公差例: 6G级M8内螺纹小径的上限值是6.647+0.028+0.265=6.94注:①内螺纹的牙高直接关系到内螺纹的承载力矩的大小,故在毛坯生产中应尽量在其6H级上限值以内②在内螺纹的加工过程中,内螺纹小径越小会给加工具——丝锥的使用效益有所影响.从使用的角度讲是小径越小越好,但综合考虑时一般采用小径的在中限至上限值之间,如果是铸铁或铝件时应采用小径的下限值至中限值之间③内螺纹6G级的小径在毛坯生产中可按6H级执行,其精度等级主要考虑螺纹中径的镀层,故只在螺纹加工时考虑丝锥的中径尺寸而不必考虑光孔的小径。
普通螺纹牙深计算

普通螺纹牙深计算
1.前言
普通螺纹牙是一种常见的螺纹结构,应用广泛于机械制造、建筑工程等领域。
有时我们需要计算螺纹牙的深度,以便进行加工或者校验。
在这篇文章中,我们将介绍如何计算普通螺纹牙的深度。
2.什么是普通螺纹牙深度?
普通螺纹牙深度是指在内圈壁和外圈壁之间形成的螺纹沟槽的深度。
螺纹牙深度和螺纹牙高度是螺纹设计中两个基本参数,它们相互关联,同时也对螺纹的性能产生着很大的影响。
3.螺纹牙深度的计算公式
螺纹牙深度的计算公式如下:
H=P×0.866
其中,H表示螺纹牙深度,单位为毫米;P表示螺距的倒数,单位为牙/毫米;0.866为三角形的高度系数。
4.实例分析
我们现在来看一个普通螺纹牙深度的实例:
要求:计算一个M12×1.5的螺纹牙的深度。
解决方法:根据公式,先求出螺距的倒数,即:
P=1/1.5=0.6667(牙/毫米)
再代入公式:
H=P×0.866=0.6667×0.866≈0.5772(毫米)
所以,对于这个M12×1.5的螺纹牙,其深度约为0.5772毫米。
5.注意事项
1.在计算螺纹牙深度时,需要先知道螺距的值。
2.对于带有斜底的螺纹结构,深度计算方法有所不同,需要根据实际情况进行相应调整。
3.螺纹牙深度和螺纹牙高度是螺纹设计中两个基本参数,必须相互匹配,才能保证螺纹的良好性能和密封性。
6.结论
计算普通螺纹牙深度是螺纹设计和制造中一个基本的过程,通过本文的介绍,我们了解到了计算螺纹牙深度的公式和方法,同时也提醒大家在实际操作过程中要注意细节事项,以保证螺纹牙的质量和可靠性。
普通60度三角螺纹深度怎么计算
普通60度三角螺纹深度怎么计算我是车工,级别很低的那种现在想学车螺纹不知道怎么车,不知道多大的直径该车多宽的螺距和深度。
该怎么计算呢?望懂的师傅指点指点再此感激您了。
希望就是您能说的尽量能让我懂,我理解能力有限,不要说的太复杂了,我举个例子:M45的普通60度三角螺纹它的螺距和深度怎么计算?我现在就是要学车这种螺纹。
M50或M60或更多的其他螺纹计算也是一样吗都有规律吗?望个位师傅指教指教谢谢了!如果直接标注M45、M50、M60的话说明是普通粗牙螺纹。
像这类螺纹如果要加工的话,需要通过查表来确定螺纹的螺距,知道螺距后可以通过公示计算螺纹的小径,中径,大径。
如果就加工来讲,以M45的螺纹为例,公称直径为45mm,查表后得知M45螺距为4.5mm。
现在就可以计算了,d=45小径=d-1.0825p=45-1.0825*4.5 结果你自己算吧。
所谓小径可以说是你车削的终点。
下面是螺距表格,和计算方法表格:普通粗牙螺纹不标螺距,这些螺距是标准化规定。
根据直径螺距表中d*t(d-螺纹公称直径;t-螺距).1*0.25 1.6*0.35 2*0.4 2.5*0.45 3*0.5 4*0.7 5*0.8 6*1 8*1.25 10*1.5 12*1.75 14*2 16*2 18*2.5 20*2.5 22*2.5 24*3 27*3 30*3.5 33*3.5 36*4 39*4 42*4.5 45*4.5 48*5 52*5 56*5.5 60*5.5 64*6计算方法:螺距P 原始三角形高度H=0.866P 牙高(工作高度) H=0.5413P 内螺纹大径D--内螺纹公称直径外螺纹大径d--外螺纹公称直径内螺纹中径D=D-0.6495P 外螺纹中径d=d-0.6495P内螺纹小径D=D-1.0825P 外螺纹小径d=d-1.0825P查表和计算方法都明白之后,值得注意的是加工时的方法,和经验的运用,多学多看,多问师傅总没有坏处。
三角螺纹的尺寸计算
第一二课时车削螺纹的基本知识一螺旋线的形成直角三角形围绕圆柱旋转一周,斜边在圆柱表面上所形成的曲线,就是螺旋线二、螺纹的分类按用途和牙形分螺纹联接用传动用锯齿形螺纹矩形螺纹梯形螺纹三角形螺纹管螺纹圆形螺纹按螺旋方向分:右旋和左旋按螺旋线数分:单线和多线按母体分:圆柱螺纹和圆锥螺纹三、螺纹术语1.螺纹在圆柱表面上,沿着螺旋线所形成的,具有相同剖面的连续凸起和沟槽2.螺纹牙型、牙型角和牙型高度螺纹牙型是通过轴线剖面上,螺纹的轮廓形状。
牙型角是螺纹牙型上,相邻两牙侧间的夹角牙型高度是螺纹牙型上,牙顶到牙底之间,垂直与轴线的距离。
3.螺纹直径公称直径代表螺纹尺寸的直径,指螺纹大径的基本尺寸。
外螺纹大径(d)亦称外螺纹顶径。
外螺纹小径(d1)亦称外螺纹底径。
内螺纹大径(D)亦称外螺纹底径。
内螺纹小径(D1)亦称外螺纹孔径。
中径(D2,d2)是一个假象圆柱的直径,母线通过牙型上沟槽和凸起宽度相等的地方。
4.螺距(P)相邻两牙在中径线上对应两点间的轴向距离。
5.螺纹升角(ψ)在中径圆柱上,螺旋线的切线与垂直于螺纹轴线的平面之间的夹角。
计算公式:tanψ=P/πd2四螺纹代号1,三角螺纹:普通粗牙螺纹由“M”表示M后的数字表示公称直径普通粗牙螺纹由“M”和公称直径×螺距表示2,矩形螺纹:是由矩形公称直径×螺距来表示3,梯形螺纹:是由螺纹代号Tr、公称直径×螺距表示。
4,锯齿形螺纹:是由螺纹的特征代号S和公称直径×螺距表示第三四五课时车削三角螺纹一、三角螺纹的尺寸计算一、普通螺纹的尺寸计算牙型角为60度用(Mxx)表示(1)螺纹大径D=d(2)中径d2=D2=d-0.6495P(3)牙型高度h1=0.5413P(4)螺纹小径d1=D1=d-1.0825P二、英制螺纹在我国应用很少,牙型角为55度螺距与公制换算公式:P=1in/n=25.4/n(mm)P为螺距n为牙数三、管螺纹分为非螺纹密封管螺纹(圆柱)和螺纹密封管螺纹(圆锥),均为55度,用(Gx/x)表示四,三角形螺纹车刀1对螺纹车刀的要求1、车刀的尖角一定要等于螺纹的牙形角。
三角螺纹尺寸国标
三角螺纹尺寸国标主要分为以下几个部分:
1. 螺纹直径:三角螺纹的直径分为M系列、R系列、G系列等。
其中,M系列最常用,例如M2、M3、M4等。
2. 螺纹长度:螺纹长度分为短螺纹(如M20以下)和长螺纹(如M20以上)。
螺纹长度的表示方法为:螺纹直径×螺纹长度,如M20×50。
3. 螺纹间距:三角螺纹的螺距(即相邻两个螺纹的距离)通常在0.5~2.5mm之间。
4. 牙型:三角螺纹的牙型分为三角形和梯形两种,通常采用三角形牙型。
5. 精度等级:三角螺纹的精度等级分为C级、A级、B级等,其中C级为普通精度,A 级和B级为高精度。
6. 材质和硬度:国标三角螺纹通常采用Q235钢材,硬度为4.8级。
此外,还有不锈钢、铜等材质的三角螺纹。
7. 用途:三角螺纹广泛应用于机械、建筑、汽车等行业,用于紧固连接两个带有通孔的零件。
普通螺纹尺寸计算
二、普通螺纹要素及名称
(五)螺纹中径(d2、D2)
宽度相等
中径
二、普通螺纹要素及名称
(五)螺纹中径(d2、D2) 牙底
牙顶
小径D1、d1 中径D2、d2 大径 D、d
牙顶
内螺纹
牙底
外螺纹
三、普通螺纹的尺寸计算
d2 h d1 h
d D h D1 h D2
外螺纹
名称 牙型角
螺纹大径 螺纹中径
螺纹小径 牙型高度
谢谢!
M27×1.5-6H
M — 普通三角形螺纹(代号) 27 — 螺纹公称直径,即大径 1.5 — 螺纹的螺距,细牙。粗牙不标注 6H — 内螺纹中径和小径的公差带代号
四、普通螺纹加工尺寸计算
M27×1.5-6g
大径d=27,根据公差带的代号
,查表可得:d=ø
中径d2=27-0.6495×1.5=26.02 根据公差带的代号,查表可得:
普通三角形螺纹尺寸计算
零件的数控加工
主讲人:王东
一、螺纹的应用
二、普通螺纹要素及名称
(一)牙型及牙型角 牙型
普通螺纹的牙型是三角形形状,牙型角α为60度。
二、普通螺纹要素及名称
(二)线数(n)
n=1
n=2
单线螺纹
双线螺纹
二、普通螺纹要素及名称
(三)螺距(P)和导程(L)
L
L
P
P
单线螺纹
双线螺纹
导程(L)= 线数(n) × 螺距(P),单线螺纹L = P ,双线螺纹L=2P
二、普通螺纹要素及名称
(四)螺纹大径(d、D)和螺纹小径(d1、D1) 牙底
牙顶
h 小径(d1) h 大径(d) 大径(D)
- 1、下载文档前请自行甄别文档内容的完整性,平台不提供额外的编辑、内容补充、找答案等附加服务。
- 2、"仅部分预览"的文档,不可在线预览部分如存在完整性等问题,可反馈申请退款(可完整预览的文档不适用该条件!)。
- 3、如文档侵犯您的权益,请联系客服反馈,我们会尽快为您处理(人工客服工作时间:9:00-18:30)。
普通三角形螺纹加工尺寸的计算
驻马店高级技工学校—王俊荣
摘要:螺纹加工中比较重要的是尺寸的计算,只有正确的计算才能加工出合格的螺纹。
因为三角形螺纹的牙型比较小,加工时由于车刀的挤压使牙型外胀,还有螺纹刀刀尖不是削平的梯形,而是圆弧形的,所以有必要把理论尺寸和实际加工尺寸之间的关系讲明白,让螺纹的加工变得更准确。
关键词:三角形螺纹牙型高度总的背吃刀量多线螺纹加工我们在加工螺纹时螺纹尺寸的计算十分重要,特别是螺纹理论尺寸与实际加工尺寸的不同给学生的学习带来很多困难,三角形螺纹加工尺寸的计算是加工三角形螺纹的重要部分,只有掌握正确的计算方法,才能加工出合格的产品。
一、普通三角形螺纹的基本牙型
普通三角形螺纹的基本牙型如图1所示,各基本尺寸的名称如下:
图1 普通三角螺纹基本牙型
D—内螺纹大径(公称直径);
d—外螺纹大径(公称直径);
D2 —内螺纹中径;
d2—外螺纹中径;
D1—内螺纹小径;
d1—外螺纹小径;
P—螺距;
H—原始三角形高度。
三角形螺纹的基本尺寸有:
1、牙型角α螺纹轴向剖面内螺纹两侧面的夹角。
普通三角形螺纹α=60o,
2、螺距P 它是沿轴线方向上相邻两牙间对应点的距离。
3、导程P h在同一条螺旋线上的相邻两牙在中径线上对应两点之间的轴向距离。
4、牙型高度:外螺纹牙顶和内螺纹牙底均在H/8处削平,外螺纹牙底和内螺纹牙顶均在H/4处削平。
h1=H-H/8-H/4=5/8H=0.5413P
5、大径:d=D(公称直径)
6、中径:d
2=D
2
= d -2×3/8H=d -0.6495P
7、小径:d
1=D
1
= d -2×5/8H= d -1.0825P
二、加工普通三角形外螺纹前螺杆直径和加工时吃刀深度的计算。
1、M20的外螺纹,公称直径是大径20,高速车削三角形螺纹时,受车刀挤压后会使螺纹大径尺寸胀大,因此车螺纹外圆的直径,应比螺纹大径小,当螺纹螺距为1.5~3.5时,外径一般可以小0.2~0.4。
2、按照普通三角形螺纹理论公式,我们加工圆柱螺纹时因牙型高度为0.5413P,我们加工时进刀深度也应该是0.5413P,但是实际加工中却采用0.6495P的进刀深度。
这个问题在初学加工螺纹时给同学们带来很多困惑,那么我们加工中到底该采用哪个进刀深度?
原始三角形高度=P/2cot(a/2),削平高度:外螺纹牙顶和内螺纹牙底均在H/8处削平,外螺纹牙底和内螺纹牙顶均在H/4处削平。
以外三角形螺纹为例:要在牙顶削去H/8,牙底削去H/4,如何削去呢?只有靠刀具的加工来达到。
底部要达到规定的削平处,螺纹车刀前端是刀尖圆弧,圆弧应小于P/8,而标准规定的牙底形状是削平的梯形,和规定的标准不完全一样,加工时刀具一定要往下切,刀具要切到H/4的中央,因此吃刀量为H/8+5H/8=3H/4=3/4×0.866P=0.6495。
也就不难理解。
例1:加工一个M20×2的螺纹,加工螺纹前的螺杆直径是多少?螺纹的总吃刀量是多少?
解:加工螺纹前螺杆的直径20-0.2=19.8mm
总的背吃刀量=0.6495p=0.6495×2=1.299mm
分五次切削,每次背吃刀量a
p1
=0.5 mm
a
p2
=0.35 mm
a
p3
=0.25 mm
a
p4
=0.199 mm
三、加工普通三角形内螺纹前螺杆直径和加工时吃刀深度的计算
1、车削三角形内螺纹时,因车刀切削时的挤压作用,内孔直径会缩小,(车削塑性材料较明显),车削内螺纹前内孔应比内螺纹小径略大些,又由于内螺纹加工后的实际顶径允许大于D的基本尺寸,所以实际生产中,普通螺纹在车内螺纹前的孔径尺寸,可以用下列近似公式计算:
车削塑性金属的内螺纹时,D=d-p
车削脆性性金属的内螺纹时,D=d-1.05p
2、加工普通三角形内螺纹时由于车刀的挤压作用,车削塑性金属的内螺纹时,吃刀深度为P/2。
车削脆性性金属的内螺纹时,吃刀深度为1.05P/2。
例2:内螺纹的加工,加工一材料为45钢的M20×2的内螺纹,加工前轴的尺寸为多少?总的背吃刀量为多少?
=D-P=20-2=18 mm
解:加工前孔径尺寸D
孔
总的背吃刀量为(20-18)/2=1 mm
a p1=0.4 mm
a p2=0.3 mm
a p3=0.2 mm
a p4=0.1 mm
四、多线螺纹加工是的计算。
多线螺纹的加工深度与单线螺纹加工相同,车削多线螺纹可用小滑板退刀的方法解决,第二线螺纹的起点与第一线螺纹的起点相差一个螺距,第三线螺纹的起点与第二线螺纹的起点相差一个螺距的距离,依次类推,即可车削多线螺纹,同时多螺线纹的终点要一致。
例3:加工一个M24×4(P2)双线外螺纹,材料为45钢,试述背吃刀量和加工双线螺纹的方法。
解:此时一定要注意计算牙深时用的是螺距P=4/2=2 mm,千万不要用导程4 mm. 加工前轴颈:d=24-0.2=23.8 mm
总的背吃刀量=0.6495p=0.6495×2=1.299 mm
分五次切削,每次背吃刀量a p1=0.5 mm
a p2=0.35 mm
a p3=0.25 mm
a p4=0.199 mm
加工双线螺纹的方法:先把小滑板导轨找正到与车床主轴轴线平行。
按导程4 mm 车好一条螺旋槽后,把小滑板向前或向后移动2 mm,再车第二条螺旋槽即可。
五、车螺纹的方法和步骤。
图2 螺纹切削方法与步骤。