不锈钢熔模铸造缺陷分析及质量控制
铸造缺陷质量分析报告

铸造缺陷质量分析报告标题:铸造缺陷质量分析报告摘要:本次报告对一批铸造件的缺陷进行了详细分析,并提供了解决方案,以提高铸件的质量和可靠性。
通过对缺陷的分类、原因分析和改进措施的制定,本报告的目标是降低缺陷率、提高产品质量,并为企业的生产过程提供指导。
一、引言铸造工艺是一种常见且重要的金属加工方式,但由于多种因素的影响,铸造件常常出现各种缺陷。
本报告对以下几种常见铸造缺陷进行了分析:气孔、砂眼、夹渣和缩孔。
二、缺陷分类和特征1. 气孔:气孔是铸造件内部的圆形或椭圆形气体空洞,在表面上通常呈孔状。
这种缺陷的特征是大小不一、分布不均匀,并且可能与材料中的气体分离有关。
2. 砂眼:砂眼是在铸造件表面形成的小凹陷或孔穴,并且通常有砂粒残留。
这种缺陷的主要原因是在型腔填充过程中砂芯未能完全固化或砂芯破裂。
3. 夹渣:夹渣是铸造件内部存在金属残留或其他非金属杂质的缺陷。
它通常表现为呈条状、点状或块状分布的较暗色物质。
4. 缩孔:缩孔是在铸造件中形成的不完全填充的孔洞,通常位于较厚的截面部分。
这种缺陷的主要原因是在凝固过程中金属收缩引起的。
三、缺陷原因分析1. 气孔:气孔的形成主要与以下因素有关:金属液中溶解的气体、型腔设计不合理、浇注过程中液态金属的气体浸润和释放等。
解决方案包括采取适当的除气处理、改进型腔设计、控制浇注工艺等。
2. 砂眼:砂眼通常与砂芯制备和浇注过程中的温度、浇注速度等相关。
解决方案包括优化砂芯制备工艺、调整浇注参数以及改善浇注系统设计等。
3. 夹渣:夹渣的原因主要与金属液的净化和过滤不足、浇注过程中金属液与非金属杂质的接触等有关。
解决方案包括加强净化处理、使用过滤器、改进浇注工艺等。
4. 缩孔:缩孔的形成与金属凝固收缩不平衡、铸造温度过低、浇注过程中金属液的顺流速度等相关。
解决方案包括优化浇注工艺、控制冷却速度等。
四、改进措施根据对缺陷原因的分析,提出了以下改进措施:1. 加强除气处理:通过采用真空或压力浇注等技术,有效去除金属液中的气体;2. 优化砂芯工艺:提高砂芯的强度和温度稳定性,避免砂芯破裂;3. 加强金属液净化:采用有效的净化剂和过滤器,去除金属液中的杂质;4. 调整浇注参数:合理控制浇注温度和速度,确保金属液充满型腔;5. 优化冷却过程:控制冷却速度,减少金属凝固收缩引起的缺陷。
不锈钢熔模铸造缺陷分析及质量控制
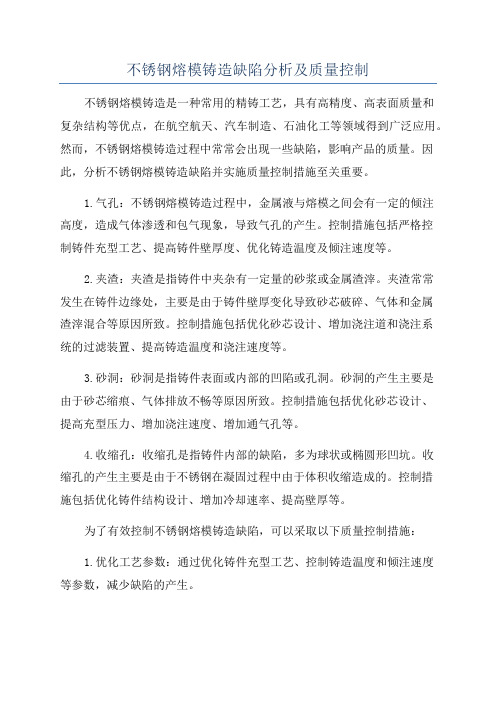
不锈钢熔模铸造缺陷分析及质量控制不锈钢熔模铸造是一种常用的精铸工艺,具有高精度、高表面质量和复杂结构等优点,在航空航天、汽车制造、石油化工等领域得到广泛应用。
然而,不锈钢熔模铸造过程中常常会出现一些缺陷,影响产品的质量。
因此,分析不锈钢熔模铸造缺陷并实施质量控制措施至关重要。
1.气孔:不锈钢熔模铸造过程中,金属液与熔模之间会有一定的倾注高度,造成气体渗透和包气现象,导致气孔的产生。
控制措施包括严格控制铸件充型工艺、提高铸件壁厚度、优化铸造温度及倾注速度等。
2.夹渣:夹渣是指铸件中夹杂有一定量的砂浆或金属渣滓。
夹渣常常发生在铸件边缘处,主要是由于铸件壁厚变化导致砂芯破碎、气体和金属渣滓混合等原因所致。
控制措施包括优化砂芯设计、增加浇注道和浇注系统的过滤装置、提高铸造温度和浇注速度等。
3.砂洞:砂洞是指铸件表面或内部的凹陷或孔洞。
砂洞的产生主要是由于砂芯缩痕、气体排放不畅等原因所致。
控制措施包括优化砂芯设计、提高充型压力、增加浇注速度、增加通气孔等。
4.收缩孔:收缩孔是指铸件内部的缺陷,多为球状或椭圆形凹坑。
收缩孔的产生主要是由于不锈钢在凝固过程中由于体积收缩造成的。
控制措施包括优化铸件结构设计、增加冷却速率、提高壁厚等。
为了有效控制不锈钢熔模铸造缺陷,可以采取以下质量控制措施:1.优化工艺参数:通过优化铸件充型工艺、控制铸造温度和倾注速度等参数,减少缺陷的产生。
2.加强设备管理:定期检查和维护熔模设备,确保各项设备的正常运行。
3.严格原材料控制:对原材料进行检验,确保其质量合格。
4.检测和分析技术:采用非破坏性检测技术,如X射线检测、超声波检测等,对铸件进行缺陷检测和分析,及时发现和解决问题。
5.过程控制和持续改进:建立严格的质量控制流程,持续跟踪和改进生产过程中的关键环节,提高产品质量和生产效率。
综上所述,通过分析不锈钢熔模铸造缺陷并实施相应的质量控制措施,可以有效降低缺陷的发生率,提高产品的质量和可靠性。
熔模铸件缺陷分析及对策

熔模铸件缺陷分析及对策 熔模铸造(又称失蜡铸造),它是一种 近净形成形的先进工艺。熔模铸造的工艺特 点归纳起来为三点: ① 使用可熔(溶)性一次模和一次型 (芯),不用开型起模,无分型面。
② 采用涂料浆制型壳,涂层对蜡模(易熔 模)复印性好。 ③ 采用热壳浇注,金属液充型性好。
因此,熔模铸造可以制造尺寸精度高 (CT4-6),表面粗糙度低(Ra0.8-3.2μ)的 复杂铸件。
① 硅溶胶和硅酸乙酯水解液粘结剂本身粘度小,故配
制的面层涂料粉液比较高,如配锆英粉涂料时粉液比
可达4以上,配刚玉粉涂料时粉液比也可在3.2以上,配
石英粉涂料时可达2.2左右。 ② 水玻璃粘结剂因自身粘度高,故水玻璃涂料粉液 比很低,配石英粉涂料时,粉液比常为:1.0—1.1。但 也可以通过降低水玻璃密度:1.26—1.28g/cm3,模数
3、金属液精确复型的影响因素
⑴ 合适的型壳温度:
薄壁件及小件要求型壳经焙烧后,尽可能的保证有足够 高的型壳温度迅速浇注。因为提高型壳温度对改善金属液流 动能力、复型能力有良好的效果。过高的合金熔炼温度常因 增加金属液的吸气量,减少结晶形核基底等因素,而对材质 产生不利影响。 厚大件要求型壳温度较低为好,冷却速度快,减少形成 缩孔、缩松的缺陷倾向。 硅溶液、硅酸乙酯型壳的焙烧温度为 1050-1100℃ ,水 玻璃型壳焙烧温度为850℃,出炉后迅速浇注。
罩密封,使铸件在还原气氛中冷却。
⑵ 清理对熔模铸件表面粗糙度的影响
清理对熔模铸件表面粗糙度的影响也很大,应
注意以下几个方面: ① 喷砂清理的方法比喷丸清理铸件表面粗糙度 好2级以上。
② 采用高压水力清砂是保证铸件表面粗糙度较
好的方法。
③ 整组铸件组振壳后,先喷丸再切割,个别清不到的
不锈钢熔模铸造缺陷分析及质量控制

熔模铸造的工艺流程通常为 :压型创造→蜡模压制→蜡模组装→浸涂料→撒砂→硬化及干燥→脱蜡→焙烧→浇注→ 落砂及清理。
由于其工艺环节较多,过程较复杂,于是最终铸件的品质受诸多因素的影响很大,不易进行控制。
结合不锈钢熔模铸造生产过程中浮现的若干缺陷类型,探讨、分析不锈钢熔模铸造过程中品质控制的关键环节.1在生产中,有时发现成批铸件表面浮现麻坑(见图 1-1)。
呈规则的半球形小坑,凹坑直径为 013~018mm,深 013~015mm,麻坑在铸件局部呈密集状分布。
该缺陷虽不影响铸件使用性能,但无法修整,严重影响了铸件的表面品质,导致铸件成批报废。
对该缺陷进行能谱分析(见图 1—2 ) ,结果表明该缺陷位置存在着微量的 Mg、Ca 等元素。
图(1-1)铸件表面麻坑缺陷图(1—2)麻坑缺陷位置的能谱分析该表面麻坑缺陷产生的主要原因是面层型壳材料不合格。
在铸造生产中多采用锆砂作为型壳面层耐火材料,其导热性好,蓄热能力大,耐火度高,热震稳定性好。
纯 ZrSiO4 的耐火度在 2000℃以上,但随着杂质含量增加,耐火度相应下降。
当锆砂中含有氧化物杂质时,其分解温度会下降,如含有 Ca、Mg 氧化物时,分解温度会降至 1300℃摆布, 当含有 K、Na 氧化物时,其分解温度会降至 900℃摆布[1,2].锆砂是 ZrO2 SiO2 二元系中惟一的化合物,但其分解时析出的无定形 SiO2 具有很高的活性,能与金属中的Cr、Ni、Ti、Mn、Al 等合金元素在高温下发生化学反应,导致铸件表面产生麻坑缺陷,恶化铸件的表面品质。
不锈钢铸件加工或者抛光后,在加工表面位置时,会浮现分散的规则球状的黑点缺陷(见图 1—3) ,其缺陷位置的能谱分析(见图 1—4)。
可见该黑点缺陷存在 O、Si、Mn 等元素.图 (1-3)铸件黑点缺陷图(1—4)黑点缺陷位置的能谱分析该黑点缺陷产生的原因可能是由于钢液中存在有非金属夹杂物(主要是金属元素的氧化物、硫化物和硅酸盐)而导致的。
304不锈钢精密铸造件加工外观缺陷的分析与改善

304不锈钢精密铸造件加工外观缺陷的分析与改善摘要:本文主要介绍了304不锈钢精密铸造件(以下简称精铸件)加工过程中暗花缺陷的原因分析及改善过程,因不锈钢精铸件的加工在行业内较为普通,且加工工艺较为特殊,因此希望本文有一定的推广及借鉴作用。
关键词:不锈钢;精密铸造;加工;外观缺陷本文所讲的精密铸造是熔模精密铸造,它是精密铸造的工艺方法之一。
是采用失蜡法制壳,利用废钢加合金的方式浇注成铸件,再通过机械加工等工序制作成符合客户要求的精密零件,是一种历史悠久的传统制造业,是工业门类中的基础行业之一。
304不锈钢为奥氏体不锈钢,熔炼浇注及机械加工是此类零件的关键质量控制点,品质问题轻则耽误订单交期,重则损失客户丢失市场。
因此,相关品质问题的改善就显得尤为重要。
1、缺陷概述本公司生产的一种材质为304的不锈钢精铸件,车加工后零件表面出现了大面积的白色暗花(见图1)不良率28%左右,形状、大小、位置不定,经擦拭、水洗、超声波清洗等表面处理后,缺陷仍无法消除掉。
精刀返车后暗花变淡但却未完全消失,初步判断该缺陷产生的原因是数控车加工工艺设置不当。
随后将车加工工序拆分为粗车和精车,同时提高转速,减少车削量。
经试加工后发现暗花缺陷无明显好转,结果表明车加工工艺的调整对零件表面暗花的改善收效甚微,不是暗花产生的根本原因。
零件表面暗花左图的局部放大图图12、缺陷分析为了进一步分析缺陷的产生原因,从宏观角度,安排专人对本批次零件的生产过程进行倒查,核查过程中未发现异常情况。
继而从微观角度,用电子显微镜对零件的暗花缺陷展开进一步的分析,发现暗花区域相对于正常区域来说,零件的走刀路径模糊杂乱,局部棱线崩缺且有类似粘刀的异物附着(见图2)。
通过缺陷区域的放大分析得知,暗花缺陷更像是铸件本身的组织缺陷。
参考上述检测结果,为了进一步对零件的内部组织进行分析,以查明暗花缺陷的根本原因,我们对零件暗花缺陷部位进行线割截取,交品质部制样后分别在200倍、500倍和1000倍的显微镜下进行金相检验,通过图3的金相图片可以看出,碳化物在奥氏体晶界上无规则的大量聚集,粗大且成网状分布。
模具铸造五大缺陷及解决对策

缺陷一:铸造缩孔主要原因有合金凝固收缩产生铸造缩孔和合金溶解时吸收了大量的空气中的氧气、氮气等,合金凝固时放出气体造成铸造缩孔。
解决的办法:1)放置储金球。
2)加粗铸道的直径或减短铸道的长度。
3 )增加金属的用量。
4)采用下列方法,防止组织面向铸道方向出现凹陷。
a.在铸道的根部放置冷却道。
b.为防止已熔化的金属垂直撞击型腔,铸道应成弧形。
C.斜向放置铸道。
缺陷二:铸件表面粗糙不光洁缺陷型腔表面粗糙和熔化的金属与型腔表面产生了化学反应,主要体现出下列情况。
1)包埋料粒子粗,搅拌后不细腻。
2)包埋料固化后直接放入茂福炉中焙烧,水分过多。
3)焙烧的升温速度过快,型腔中的不同位置产生膨胀差,使型腔内面剥落。
4)焙烧的最高温度过高或焙烧时间过长,使型腔内面过于干燥等。
5 )金属的熔化温度或铸圈的焙烧的温度过高,使金属与型腔产生反应,铸件表面烧粘了包埋料。
6)铸型的焙烧不充分,已熔化的金属铸入时,引起包埋料的分解,发生较多的气体,在铸件表面产生麻点。
7)熔化的金属铸入后,造成型腔中局部的温度过高,铸件表面产生局部的粗糙。
解决的办法:a.不要过度熔化金属。
b.铸型的焙烧温度不要过高。
C.铸型的焙烧温度不要过低(磷酸盐包埋料的焙烧温度为800度-900 度)。
d.避免发生组织面向铸道方向出现凹陷的现象。
e.在蜡型上涂布防止烧粘的液体。
缺陷三:铸件发生龟裂缺陷有两大原因,一是通常因该处的金属凝固过快,产生铸造缺陷(接缝);二是因高温产生的龟裂。
1)对于金属凝固过快,产生的铸造接曜,可以通过控制铸入时间和凝固时间来解决。
铸入时间的相关因素:蜡型的形状。
铸到的粗细数量。
铸造压力(铸造机)。
包埋料的透气性。
凝固时间的相关因素:蜡型的形状。
铸圈的最高焙烧温度。
包埋料的类型。
金属的类型。
铸造的温度。
2)因高温产生的龟裂,与金属及包埋料的机械性能有关。
下列情况易产生龟裂:铸入温度高易产生龟裂;强度高的包埋料易产生龟裂;延伸性小的银烙合金及钻烙合金易产生龟裂。
304不锈钢熔模铸造中缩孔、缩松的几种防止措施
熔模铸造中缩松的几种特有解决方案
缩松是铸造最常见的缺陷之一,是铸件在冷却过程中热节或远浇口部位得不到有效的补缩而产生的细小分散的孔洞。
熔模铸造因为热壳浇注的特点,在浇注系统设计时大大地限制了冒口、冷铁对于缩松的处理,但是却有一系列独特的解决方案。
1、型壳底部淬水
部位:铸件浇注位置底部。
铸件浇注位置底部远离浇冒口,补缩通道过长,如果铸件较高或底部有热节,就容易产生缩松。
原理:通过淬水使型壳底部温度迅速降低,对铸件起到底部激冷的作用。
操作:热壳浇注后,型壳立刻淬水,视铸件薄厚在水中停顿1-3秒,深度为易缩松的位置。
案例1圆环产品,材质304不锈钢,浇注温度1640℃
此产品组树后高度方向尺寸较大,见图1和图2,浇注后于圆环浇注位置的下半圆A处容易出现缩松,如图1,经分析认为补缩通道过长导致下半圆凝固时钢水得不到有效补缩,从而产生缩松。
工艺改进为型壳底部淬水,深度如图2所示,效果良好,基本解决下半圆的缩松问题。
图1 圆环剖面图图2 圆环组树淬水示意图
2、喷水激冷
3、局部补砂泥
4、中空型壳
5、加保温棉
6、工艺散热冷铁
7、冷铁、热贴。
熔模铸造常见缺陷及防止方法
型 壳 变 形
型壳变形大多在脱蜡、焙烧或浇注时产生
1涂料的粘度过大,涂层过厚,涂料堆积
2硬化剂浓度低温度低硬化时间太短,硬化不足
3脱蜡水温度低,脱蜡时间过长
4焙烧时型壳受挤压或温度过高
1控制涂料粉液比和粘度
2避免涂料局部堆积
3控制硬化剂浓度,温度和硬化时间
1表面层涂料粘度不要太高,增加涂料流动性2避免蜡模表面及局部涂料堆积,应使涂料分 布均匀
3表面层浸涂料撒砂后,先经一定时间的自然 干燥后,再进行化学硬化
4表面层的化学硬化要充分
型 壳 分 层 和 鼓 胀
1涂料撒砂后,表面有浮砂
2表面层撒砂的粒度过细,砂中粉尘过多或砂 粒受潮含水分过多
3型壳表面层化学硬化后风干时间过短,残留 硬化剂过多
2模料收缩率大或太脆
3压型设计不正确,或起模操作不当
4压型温度过低,使熔模冷却太快
5压注时模料温度偏高
1控制熔模在压型中的冷却时间
2改用收缩率小、韧性好的模料
3改进压型设计,增大圆角或起模斜度,起模 时用力要均匀
4提高压型的工作温度
5降低压注时模料的温度
鼓 包
1模料中搅入了气体
2起模太早,被压缩的气包膨胀
3熔模没有及时冷却,或冷却不充分
4制模室温度过高
1配置模料时应避免裹入过多的气体
2适当延长保压时间
3从压型取出的熔模应及时冷却并控制冷却时 间
4严格控制制模室工作温度
变
形
1起模过早,
2压型设计不良
3熔模存放状态不良,引起变形
4熔模存放温度过高
5熔模存放时间过长
6熔模收缩率偏大
1延长保压时间,或采用校正模
薄壁熔模不锈钢铸件的易发缺陷和措施
薄壁熔模不锈钢铸件的易发缺陷和措施李彦荣朱书新(石家庄艾力格不锈钢制品有限公司,河北石家庄050011)工程技术口青要】分析薄壁件缩孔和缩松的成因,并通过对几种熔模不锈钢铸件的实践工艺改进实倒分析,提出了预防和解决薄壁件缩孔和缩松的措施。
供键翊熔模薄壁不锈钢铸件;缩孔和缩松在熔模不锈钢铸件的各种缺陷中,缩孔(松)占了很大的比例,而在薄壁铸件中缩孔f松)的比例则更大,严重影响了铸件得内部质量,所以对于薄壁铸件来说,缩孔(松)是比较难解决的棘手问题。
1缩孔缩松形成原因合金在液态收缩和凝固时,铸件某部位(通常是最后凝固的热节处)不能及时得到液体金属的补缩,就在该处产生缩孔。
合金液在型壳内凝固时,当合金凝固范围较大就会形成较宽的凝固区域,在凝固区域内是按“体积凝固”方式进行凝固,即在该区域内同时形成晶核并长大,到凝固后期,固相比例大,枝晶生长连成骨架,把未凝固金属液分割成孤立的或近乎孤立的小熔池,这些金属液凝固时就难以得到补缩,从而形成了许多细小分散的小孔,成为缩松。
,2薄壁熔模不锈钢铸件的工艺改进实例我们公司近几年也做了一些薄壁铸件,开始量产时因缩孔(松)的废品率很高,通过rL次试验及工艺改进,已能正常生产。
主要采取的措施有:合理布置浇口,浇冒口保温措施,提高浇注温度,沾水和埋砂等,下面就我们的实际经验结合实例加以说明。
1)见图1,l比{寿件材质为SS304,形状简单,壁厚均匀,但只有2.5m m。
最初浇口设置在A处,湃主舌发现在侧壁与圆弧交界处总出现或多或少的缩孔(松),并且无法焊补。
分析认为,侧壁交界处为该铸件的热节,此处经钢水冲刷,目散热不良,所以对于薄壁件来说浇口A对此处的补缩距离就显得太远了。
因此,在B和C处增加两个巾10的小浇口,重新布置浇口后,该铸件缩孑L(松)缺陷大大降低了。
2)见图2,此铸件为一个泵壳,材质SS304,四个支腿是由壁厚为5.1—9.9m m的三个面绍成的,壳体和弯脖部分壁厚在5.1m m左右。
如何消除不锈钢熔模铸件的毛刺缺陷
如何消除不锈钢熔模铸件的毛刺缺陷【摘要】对因硅溶胶型壳裂纹而引起的铸件毛刺缺陷进行了分析,找出了影响此类缺陷的主要原因,制定了防范措施,并在实际生产中取得一定效果。
【关键词】硅溶胶型壳;不锈钢精密铸造;毛刺;型壳裂纹我公司主要生产硅溶胶型壳的不锈钢精密铸件,有阀门管件和机械零件等。
铸件的毛刺是生产中时常批量产生的缺陷,必须在后处理工序经过打磨和抛丸等工序才能消除,即造成人物力的浪费,又影响了铸件表面的质量及尺寸精度,给生产和经营带来不利影响。
1.原因分析毛刺缺陷一般发生在铸件的外表面或较大平面上,连续或断续不规则凸起,形成毛刺飞边。
大件比小件发生几率要高。
形成毛刺的原因是由于型壳在浇注前就产生了裂纹,钢水注入后,渗入型壳的裂纹之中,凝固后就形成了毛刺缺陷。
而型壳的裂纹形成的原因有以下三点:1.1在型壳干燥时产生的,由于面层干燥过快,或涂料干燥收缩过大引起的。
1.2脱蜡时蜡模膨胀大于型壳膨胀,而型壳湿强度又较差使型壳开裂。
1.3型壳焙烧工艺不当,产生型壳裂纹。
2.改进措施2.1型壳的干燥2.1.1型壳干燥车间温度、湿度对型壳裂纹的影响制壳工况三要素有温度、湿度和风速。
我公司以3″球阀阀体为例作实验,产品材质为0Cr18Ni9,在风速一定的情况下,对型壳干燥车间的温度和湿度每隔4小时测量一次。
当温度变化超过5℃或湿度变化超过10%时,生产铸件较大部分出现表面毛刺缺陷。
在相同温度和湿度条件下,调整风速。
在对被层调整风速时,铸件表面毛刺影响极小;在对面层调整风速时,吹中强风干燥的型壳,浇注后铸件表面有严重毛刺缺陷,吹微风干燥或无风干燥时,铸件表面无毛刺缺陷。
经过以上统计分析,确定型壳干燥工艺为:(1)面层干燥间温度控制在20-24℃范围内,湿度在60%-70%范围内,无风或微风干燥。
(2)过渡层和背层干燥间温度在22-26℃范围内,湿度在50%-55%。
干燥时要求吹中强风,但不要正对模壳,要尽量使干燥间空气流动。
- 1、下载文档前请自行甄别文档内容的完整性,平台不提供额外的编辑、内容补充、找答案等附加服务。
- 2、"仅部分预览"的文档,不可在线预览部分如存在完整性等问题,可反馈申请退款(可完整预览的文档不适用该条件!)。
- 3、如文档侵犯您的权益,请联系客服反馈,我们会尽快为您处理(人工客服工作时间:9:00-18:30)。
1. 3 凹陷
在生产中有时也发现部分铸件表面有不规则的凹 陷 (见图 5) ,其缺陷位置的能谱分析见图 6。可见缺陷 部位存在着 Zr 及微量 Ca 、M g 的偏聚。
466
©
图 6 凹陷缺陷位置的能谱分析 该缺陷产 生的 主要原 因可 能是锆 砂中 混有 微量 Ca 、Mg 等杂质 ,导致锆砂的高温稳定性能下降 ,从而型 壳在脱蜡或焙烧阶段发生向内的鼓胀变形 ,进而产生铸 件凹陷缺陷 。 1. 4 缩陷 在部分铸件热节部位表面有时会呈现出不规则的 凹陷 (缩陷) ,见图 7 ,其缺陷位置的局部放大见图 8 ,可 以看出缩陷缺陷位置附近表面出现较明显的砂粒印迹 。
(1) 充分焙烧型壳 。 (2) 脱氧 、除渣处理应充分 ,同时保证对熔体表面氧 化物等夹渣应及时处理干净 。必要时在浇注完毕的型 壳周围人为地造成还原性气氛 ,如向刚浇注完毕的型壳 撒木屑 。同时也要避免加入过量的脱氧剂 ,以防反而增 加钢水中非金属夹杂物的含量 。如不锈钢的脱氧剂多 用锰铁和 硅铁 ,其 在钢 水中 反应生 成 Mn O 和 Si O2 , SiO2 熔点较高 ,在钢水中悬浮很难排除干净 ,易与金属 反应生成硅酸盐系列的非金属夹杂 ,是表面黑点缺陷的 主要来源之一 。 (3) 控制适宜的浇注温度 。为了保证钢 液充满型 腔 ,获得良好的铸件表面质量 ,必须采用足够高的浇注 温度 。但是浇注温度过高 ,容易加剧表面合金元素的氧 化从而产生表面麻点等其他缺陷。因此 ,在保证获得轮 廓清晰的铸件条件下 ,应采用较低的浇注温度 。
(2) 合金原料及辅料的供给需保持相对稳定的渠 道 ;严格控制炉料 ,入炉前需要对炉料进行必要的清理 ,
468
©
不能有锈污 ,严格按照操作规程进行 ,避免将外来夹杂 引入合金熔体内部。 2. 2 涂挂 、脱蜡控制方面
(1) 严格涂料浆质量控制和管理 定期监测涂料浆 中粘结剂提取液的胶凝时间 ,坚决废弃已经老化变质的 涂料 ,特别是面层涂料 。
图 3 铸 件黑 点缺陷
图 4 黑点缺陷位置的能谱分析 该黑点缺陷产生的原因可能是由于钢液中存在有 非金属夹杂物 (主要是金属元素的氧化物 、硫化物和硅 酸盐) 而导致的 。非金属夹杂物的来源既有外来的 ,例 如金属炉料带入的泥沙杂质 ,从炉衬耐火材料上剥落下 来的碎粒以及在浇注过程中型壳被钢液冲刷下来的碎 砂等 ;也有熔体内部产生的 ,如钢液中的元素被氧化生 成的氧化物 。上述非金 属夹杂中 的硅酸 盐类 , 如 Fe2 Si O3 、M n Si O3 、FeO ·Al2 O3 ·SiO2 等 使钢液中的硅被 氧化成 SiO2 , SiO2 与钢液中的 M nO 、FeO 以及 Al2 O3 等化合物反应而生成多组元复合化合物 ,这类夹杂物的 熔点比合金熔体温度低而呈液态存在 。又由于它们有 较大的表面张力 ,并且与钢液之间不相互润湿 ,因此在 钢液中聚成球形 ,钢液凝固后形成球形夹杂物 ,在铸件 表面形成的是规则的球状黑点缺陷 。
在生产中有时也发现部分铸件表面有突出的金属
467
特种铸造及有色合金 2008 年年会专刊)
图 14 毛刺缺陷位置的能谱分析 颗粒(见图 16) 。该缺陷有时无法修整 ,影响了铸件的 表面质量。
图 15 铸件夹砂缺陷
图 16 铸件多肉缺 陷
该缺陷产生的主要原因可能是面层涂料存在问题 或者涂挂操作不当而导致的 。面层涂料如果含气量大 或者面层涂料对蜡模的浸润性差或者涂挂前两层时没 有及时清除气泡 ,在焙烧或合金浇注阶段导致型壳产生 鼓泡 ,最终会被金属液填充 ,从而产生多肉缺陷 。
465
©
特种铸造及有色合金 2008 年年会专刊)
坑缺陷 ,恶化铸件的表面质量。 1. 2 黑点缺陷
不锈钢铸件加工或抛光后 ,在加工表面位置 ,有时 会出现分散的规则球状的黑点缺陷 ,见图 3。其缺陷位 置的能谱分析 见图 4 。可见该黑点缺陷存在着 O 、Si 、 Mn 等元素的偏聚 。
图 5 铸件凹陷缺陷
图 10 疤痕缺陷位置的能谱分析 该缺陷产生的主要原因可能是型壳中残留过多的 皂化物且型壳焙烧不良或者型壳存放时间过长 (或湿度 大) ,导致型壳中残留的碳质等物质较多 ,当钢液进入此 类型壳中 ,将导致合金熔体表面与型壳发生反应 ,从而 产生表面蜂窝状凹陷的疤痕缺陷 。 1. 6 岛状凸起 (蛤蟆皮) 在生产中有时也发现部分铸件表面有大小不等的 块状凸起 (如图 11) 。其缺陷位置的能谱分析如图 12 所示。可见缺陷部位存在着 Cr 和 C 元素的偏聚 ,以及 微量 Ca 、Mg 元素。 该缺陷产生的主要 原因是型壳 局部硬化 、风干不 透 ,水份 、盐类富集 ;或者浇注过程中型壳面层的低熔点 夹杂物与金属液发生烧蚀 ,使 Cr 合金元素被氧化而导 致的。
1 典型铸造缺陷及其成因分析
图 1 铸件表面麻坑缺陷
1. 1 表面麻坑缺陷
在生产实践中 ,有时发现 成批铸件表面出 现麻坑 (如图 1) , 呈 规则 的 半 球形 小坑 , 凹坑 直径 为 013 ~ 01 8m m ,深为 01 3~01 5m m ,麻坑在铸件局部呈密集状 分布。该缺陷虽不影响铸件使用性能 ,但无法修整 ,严 重影响了铸件的表面质量 ,导致铸件成批报废 。对该缺 陷进行能谱分析 (如图 2) ,结果表明该缺陷位置存在着 微量的 Mg、Ca 等元素。
(2) 保证型壳导热性良好 确保蜡模表层在蜡模整 体膨胀前熔化 ;同时保证型壳面层透气性良好 ,减轻蜡 模整体受热膨胀对型壳产生的张力 ,防止型壳开裂 。
(3) 提高型壳干燥率 型壳越干燥 ,型壳强度越高 , 承受脱蜡时蜡模膨胀的能力越强 ,型壳越不容易开裂 。 同时适宜的型壳干燥率也确保型壳中残留水分少 ,在脱 蜡时不会受蒸气高温作用而出现异常沸腾现象 ,从而避 免型壳局部破损开裂 。 2. 3 焙烧 、熔炼及浇注控制方面
2 铸件的质量控制
从上述不锈钢熔模铸造铸件的缺陷种类及可能形 成原因来看 ,形成铸件缺陷的影响因素很多 ,各环节的 工艺控制好坏都将影响到最终的铸件质量 。结合上述 生产实践中所遇到的铸造缺陷 ,主要从以下 3 个方面对 铸件质量进行严格控制 ,铸件质量有了明显提高 ,取得 了较好的经济效益。
2. 1 原材料控制方面 (1) 面层材料由于直接与合金熔体接触 ,对铸件的
图 7 铸件缩陷缺陷 该缺陷产生的主要原因可能是铸件局部散热条件 差 ,或者浇注温度与型壳温度过高且浇注速度过快 ,导 致在铸件热节部位产生缩陷缺陷。 1. 5 疤痕 在生产中在部分铸件的局部表面也出现有蜂窝状 凹陷 ,即疤 痕 ( 见图 9) 。其缺陷位置 的能谱分 析见图 10。可见缺陷部位存在着 C、O 及微量 Ca 、M g 的偏聚 。
不锈钢熔模铸造缺陷分析及质量控制 汤 彬等
图 8 缩陷缺陷位置的局放大
图 11 铸件岛状凸起缺陷
图 9 铸 件疤 痕缺陷
图 12 岛状凸起缺陷位 置的 能谱分析 1. 7 毛刺
部分铸件表面有时会有分散的毛刺缺陷 (如图 13) ,其缺陷位置的能谱分析见图 14。可见缺陷部位存 在着 C 及微量 Ca 、Mg 的偏聚 。
图 2 麻坑缺陷位置的能谱分析 分解温度会降至 9 00 ℃左右[ 1 ] 。锆砂是 ZrO2 ·Si O2 二 元系中唯一的化合物 ,但其分解时析出的无定形 SiO2 具有很高的活性 ,能与金属中的 Cr 、Ni 、Ti 、M n、Al 等 合金元素在高温下发生化学反应 ,致使铸件表面产生麻
收稿日期 : 2008203220 第一作者简介 :汤彬 ,男 ,1974 年出生 ,博士 ,副教授 ,清华大学基础工业训练中心 ,北京 (10084) ,电话 : 010 - 62773802 , E - mail : bt ang @t singhua . edu. cn
Key wor ds : Invest ment Ca sti ng , Casti ng Def ect s , Qualit y Cont rol
熔模铸造的工艺流程通常为 :压型制造 →蜡模压制 →蜡模组装 →浸涂料 →撒砂 →硬化及干燥 →脱蜡 →焙 烧 →浇注 →落砂及清理 。由于其工艺环节较多 ,过程较 复杂 ,因而最终铸件的质量受诸多因素的影响很大 ,不 易进行控制 。结合我厂不锈钢熔模铸造生产过程中出 现的若干缺陷类型 ,探讨 、分析不锈钢熔模铸造过程中 质量控制的关键环节 。
Def ect Ana lysis an d Qual ity Con tr ol on Sta in less St eel In vest men t Cast in g
Ta ng Bin1 , Gao J in gxiu2 , Li Shu a ng sho u1 , Li Yuef ei2 , Zen g Da b e n1 (1. Tsinghua Uni versi t y , Beji ng , Chi na ; 2. Anye Preci sion Casti ng Co. Lt d. , Qi nhuangdao , Chi na)
©
图 13 铸件毛刺缺陷 该缺陷产生的主要原因可能是型壳上存在有分散 性的孔洞 (蚁孔) 。产生蚁孔的主要有 :面层涂料中的粉 液比太低 ;面层砂的粒度大 ,而面层涂料的粘度低 ; 涂料 对蜡模的浸润性差或者涂挂面层时操作不当导致的[ 2 ] 。 1. 8 氧化物夹砂
在部分铸件表面局部会粘附金属氧化物 ,清除后呈 斑疤 (见图 15) 。其缺陷主要是由于熔体质量不高 ,浇 注期间存在氧 化物夹杂 ,最终形成铸件 氧化物夹砂缺 陷。 1. 9 铸件多肉