油脂工艺课程设计(400TD棉仁压榨车间工艺流程设计-)复习过程
油脂精炼生产线课设

脱色油罐→输送泵→袋式过滤器→棒式过滤器→至脱臭工段
脱酸脱臭:
脱色油→真空析气器(-0.092MPa±)→输送泵→列管换热器(140℃±)
→列管换热器(-600Pa、190-220℃)→脱酸脱臭塔(-600Pa、240-280℃)→
↓
↑
脂肪酸罐→输送泵→板式水冷却器
列管换热器(-600Pa、150℃±)→磁力泵→列管换热器→板式换热器(与毛油
胶溶性杂质易受水分、温度及电解质的影响而改变其在油中的存在状态,生 产中常采用水化、加入电解质进行酸炼或碱炼的方法将其从油中除去。
脂溶性杂质:主要有游离脂肪酸、色素、甾醇、生育酚、烃类、蜡、酮,还 有微量金属和由于环境污染带来的有机磷、汞、多环芳烃、曲霉毒素等。
游离脂肪酸常采用碱炼、蒸馏的方法除去。色素可采用吸附脱色的方法除去。 某些油脂中的特殊成分,如棉子油中含棉酚,菜子油中含芥子甙分解产物等,也 须在精炼过程中除去。
换热器)→板式水冷却器→袋式过滤器→棒式过滤器→成品油罐区
Байду номын сангаас
1.3 油脂精炼工艺流程图
脱胶油
加热至 90℃
磷酸
混合器 1
大豆油
棕榈油等
★
碱
混合器 2
离心机 1
皂脚
热水
混合器 3
离心机 2
油相
G1
真空干燥
碱炼油
布袋收尘
白土
加料
废水
水气
加热至 100-110℃
真空脱色 ★
间接蒸汽(高压、过热) 直接蒸汽
理论碱可按毛油酸值或游离脂肪酸的百分含量进行计算。
G NaOH
GO
VA
M NaOH M KOH
10 3
油脂的生产工艺流程

油脂的生产工艺流程
《油脂的生产工艺流程》
油脂是人们日常生活中不可或缺的食用油和食品添加剂,其生产工艺流程十分复杂。
一般来说,油脂的生产工艺可以分为榨油和精炼两个主要步骤。
榨油是指从植物种子中提取油脂的过程。
首先,要将原料植物种子进行清洗和破碎的处理,然后进行压榨。
压榨的主要目的是通过一定的压力挤出油脂,同时将油渣分离出来。
压榨过程中要控制好温度和压力,以保证油脂的品质。
不同种类的油脂需要使用不同的榨油工艺,如橄榄油、花生油、大豆油等。
精炼是在榨油的基础上对油脂进行精细加工的过程。
首先要对原始油进行脱酸、脱色、脱臭等处理,以去除油品中的杂质、色素和异味。
其中,脱酸是通过碱炼、酸炼等方法将油脂中的酸成分去除;脱色是通过吸附剂吸附色素颗粒;脱臭则是通过高温蒸馏或真空蒸馏等方法去除油品中的异味。
精炼之后的油脂可以更加纯净,颜色也更加透明。
除了榨油和精炼外,还有一些特殊种类的油脂需要经过硬脂制作、氢化、酯交换等特殊加工工艺。
硬脂制作是通过对原始油进行加热冷却,使油脂中的部分成分结晶而形成硬脂;氢化是通过在催化剂作用下加氢来改变油脂的化学性质;酯交换则是利用酯化反应来改变油脂中的脂肪酸组成。
综上所述,油脂的生产工艺流程包括榨油、精炼以及特殊加工
工艺等多个步骤,每一步骤都需要严格控制条件和技术,以保证油脂的质量和食用安全。
油脂加工工艺流程

油脂加工工艺流程油脂加工工艺流程是指将原辅料经过一系列工艺步骤加工成最终的油脂产品的过程。
下面以植物油的生产工艺为例,简述一下油脂加工的工艺流程。
首先,原料的选择非常重要,植物油的原料可以是大豆、花生、葵花籽等。
这些原料要经过严格的筛选,去除杂质、坏果等,以保证产品的质量。
接下来是清洗工艺。
将原料进行清洗,除去表面的污物和农药残留。
清洗可以采用多次水洗的方法,确保原料的纯净。
第三步是破碎和压榨。
将清洗后的原料进行破碎,然后用高压压榨机榨取油脂。
压榨是将原料中的油脂与固体部分分离的过程。
榨取的油脂水分含量较高,需要进行脱水处理。
第四步是脱水和脱酸工艺。
脱水是将压榨后的油脂中的水分去除,可以采用加热的方法使水分蒸发。
脱酸是将压榨后的油脂中的酸性物质去除,可以通过碱炼的方法或者蒸馏的方法进行。
然后是脱色工艺。
脱色是将油脂中的杂色物质去除,可以采用酸洗、碱洗、活性炭吸附等方法。
脱色后的油脂颜色明亮,透明度较高。
接下来是脱臭工艺。
脱臭是将油脂中的异味去除,可以通过高温蒸汽、真空蒸馏等方法进行。
脱臭后的油脂味道纯净,不含异味。
最后是精炼工艺。
精炼是将油脂中的杂质、色素、异味等进一步去除,以提高产品的质量。
精炼可以采用蒸馏、蒸发、结晶、洗涤等方法。
精炼后的油脂纯度高,品质优良。
通过上述一系列工艺步骤,原料经过清洗、压榨、脱水、脱酸、脱色、脱臭和精炼等工艺,最终得到质量优良的植物油产品。
油脂加工工艺流程严谨,每一个环节都要经过严格的控制,以保证产品的品质和安全性。
油脂制取工艺学(培训资料)
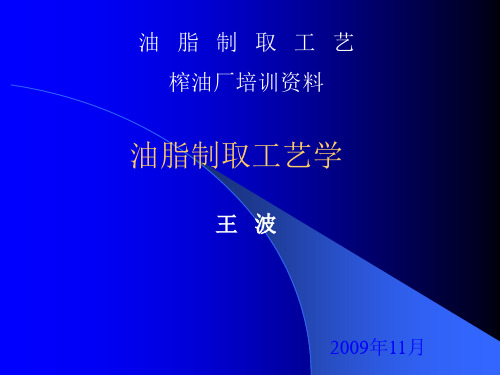
油脂工业概况
原始制油 早在人类穴居时代,古老的劳动人民就发现在 暴晒植物籽仁时可以取得油脂。
古老制油 十四世纪中叶,我国就有了楔式榨油的完整记 录;同时存在的还有人力螺旋榨。
分类 按来源分:1、动物油料 2、植物油料 3、谷物油料 4、野生油料 按工艺分: 1、低含油油料 10-30% 大豆、棉籽等 2、中含油油料 30-40% 菜籽、葵花籽等 3、高含油油料 40% 以上 花生、芝麻等
油籽的化学成分
油脂 蛋白质 碳水化合物 糖类、纤维等 水分 其它成分
棉籽含有棉酚;花生含有黄曲霉毒素; 菜籽含有硫甙葡萄糖甙等
1、减小颗粒直径,利于轧胚 2、利于物料的软化,便于水分和温度的 调节 ➢ 工艺要求 1、不出油、不成团、少出粉 2、破碎后粒度均匀,符合规定的要求
破碎的设备
BUHLER大型破碎机
齿辊式破碎机 破碎大豆、棉籽
圆盘破碎机
破碎大豆、棉籽、花 生、油棕仁等
刀板式破碎机 破碎棉籽
离心剥壳机
破碎油棕仁
➢ 工艺分类 ➢ 温脱皮
大豆的软化温度在50-70oC。脱皮率在70% ➢ 热脱皮
利用快速加热器使大豆表面温度在2-3MIN升 到 90-95oC,使种皮爆裂,皮和仁更加容易分 离。脱皮率在90%以上
品种 大豆 菜籽 棉籽 棉仁 花生仁 芝麻 油葵籽 米糠 玉米胚 芽 小麦胚 芽
脂肪
15.5 — 22.7 33 — 48 14 — 25 35 — 40 40 — 60.7
50 — 58 40 — 50 14 — 24 34 — 57 9— 10
油料加工工艺学课程设计

油料加工工艺学课程设计一、课程目标知识目标:1. 让学生掌握油料加工的基本工艺流程,包括原料处理、压榨、浸出、精炼等关键环节。
2. 使学生了解不同油料的特性及其对加工工艺的影响,如花生、大豆、油菜籽等。
3. 帮助学生理解油品质量检验的标准及方法,确保产品质量。
技能目标:1. 培养学生运用实验仪器进行油料加工实验的能力,提高实际操作技能。
2. 培养学生分析油料加工过程中出现的问题,并提出合理的解决方案。
3. 培养学生运用专业知识进行油料加工工艺的优化和改进。
情感态度价值观目标:1. 培养学生对油料加工工艺学的兴趣,激发学习热情,形成积极的学习态度。
2. 增强学生的环保意识,使其关注油料加工过程中的能源消耗和废弃物处理问题。
3. 培养学生的团队合作精神,提高沟通协作能力,为今后从事相关工作奠定基础。
本课程针对高年级学生,结合课程性质、学生特点和教学要求,明确以上课程目标。
通过本课程的学习,学生将能够掌握油料加工的基本知识,具备实际操作能力,并形成正确的价值观,为我国油料加工业的发展贡献自己的力量。
后续教学设计和评估将围绕这些具体的学习成果展开。
二、教学内容1. 油料加工基本原理:包括油料的成分、油脂的提取方法、加工过程中各阶段的变化等,对应教材第一章内容。
2. 油料预处理工艺:介绍原料的选择、清理、破碎、蒸炒等预处理过程,对应教材第二章第一节。
3. 油脂压榨工艺:讲解压榨法的分类、原理及设备,重点掌握液压压榨和螺旋压榨,对应教材第二章第二节。
4. 油脂浸出工艺:学习溶剂浸出的基本原理、设备以及浸出过程中的影响因素,对应教材第二章第三节。
5. 油脂精炼工艺:探讨油脂精炼的目的、方法及工艺流程,包括脱胶、脱酸、脱色、脱臭等,对应教材第三章。
6. 油品质量检验:介绍油品质量检验的标准、方法和仪器,包括物理、化学及感官指标,对应教材第四章。
7. 油料加工工艺优化与环保:分析现有加工工艺的优缺点,探讨节能减排措施,对应教材第五章。
油脂制取工艺流程(一)

油脂制取工艺流程(一)
一、前置处理
(一)清洗
首先将原料进行清洗,去除表面杂质和污垢,保持原料的洁净度。
(二)干燥
清洗过的原料需要进行干燥处理。
在干燥的过程中,需要使用高温和大气流使原料表
面水分和内部水分得到充分挥发,确保原料干燥后不会发生变质或腐烂。
二、制取过程
(一)压榨
将干燥后的原料放入压榨机中,采用压榨工艺来制取出油脂。
该工艺是利用物理压榨
的方式,经过过滤和其他处理技术,制成纯净的油脂。
(二)萃取
萃取是一种化学制取油脂的方法,利用化学萃取剂进入原料中,帮助分离油脂成分。
萃取过程需要根据原料的不同特点来选择萃取剂,以确保提取的油脂成分纯净无杂质。
(三)分离
在萃取后,需要将萃取到的油脂与其他材料分离出来。
这一步可以通过离心、溶剂萃
取等方式来实现。
(四)精制
精制是为了使得油脂成分更加纯净。
在这个过程中,需要将油脂进行去酸、去色、去
异物等处理,并在适当的条件下调整其酸值、色度等特性的参数。
三、包装
在制取完成后,需要对油脂进行包装,并进行质量检查。
油脂的包装可以采用塑料桶、铁桶、罐装等形式来进行,以便于运输和储存。
四、储存
油脂是一种易氧化、易变质的物品,需要储存在阴凉、干燥、通风良好的环境中。
在
储存油脂的过程中,需要定期检查,确保油脂的质量和储存环境的卫生状况。
总之,油脂制取工艺流程需要严格按照生产标准来操作,以制取出纯净、健康的油脂产品。
在生产过程中,需要关注原材料的质量、生产的卫生状况以及检测油脂的质量,确保符合相关的生产标准。
油料压榨工艺

河南鸣人装备油脂工程有限公司
油料压榨制油设备生产线
一、工艺流程
油料→清选除杂→磁选→破碎→调质→压榨→毛油→过滤
↓↓
压榨饼去精炼二、工序说明
去杂工序:精选优质大豆为原料,首先应对原料进行清选、去石、磁选,组合式平面回转筛低速大摆幅运作,运行平稳产量高,容易除杂,故障率低,除杂效果非常理想,配套刹克龙风运除杂枫网系统,有效保证车间干净卫生。
破碎工序:经筛选后的大豆进入破碎机进行破碎,破碎是破坏大豆细胞组织,增加大豆榨油时挤榨的表面积,缩短油路。
采用对辊破碎机,以保证破碎后的大豆颗粒均匀又有较高的机械强度,一般对大豆破碎控制在4-6瓣/粒,有利于物料的充分均匀蒸炒调质,提高压榨出油率。
调质工序:蒸炒热源为导热油或蒸汽,用于将破碎后的大豆颗粒经过湿润、加热、蒸炒成为熟料,以利于压榨制油和改善油品质量。
采用立式调质锅进行炒籽,既节省能源又可保证炒籽的温度和炒籽的均匀性,蒸炒目的是使物料中的蛋白质充分变性,使物料达到适合压榨机压榨的可塑性和弹性,从而提高榨油的出油率以及得到理性的压榨饼和优质油脂。
压榨工序:物料蒸炒调质至机榨适应温度经过分料绞龙输送至压榨机进行压榨,压榨机采用多台新型节能6YL-130型螺旋榨油机进行并联压榨生产,机榨饼一次成型,机榨饼残油7%左右,所得压榨毛油香味纯正,品质高。
压榨毛油经过叶片振动过滤机过滤后进精炼车间进行精炼生产。
三、车间工艺技术指标
筛选后含杂<0.1%
破碎颗粒:4-6瓣
入榨水分:6-8%
入榨温度:100-110度。
榨油厂流程

榨油厂流程(1)压榨工艺流程原料→清理→破碎→调质→压榨→过滤→毛油(2)工艺流程说明1)筛选去石工序清理对于油料前处理工艺非常重要。
因为油料中大块硬杂和铁屑可能会楔入设备中导致物料堵塞,这样会腐蚀设备、缩短使用寿命、降低工作效率。
因此需要用清理筛筛去大的杂质,用磁选器清除金属杂质,去石机去除物料中的并肩泥等硬杂。
配上吸风风网系统,可以有效的控制原料的尘杂,保证原料的清洁度。
2)破碎工序原料经过破碎机破碎后表面积增大,利于蒸炒时温度和水分的传递,蒸炒效果提高。
3)调质工序调质的作用是调节油料籽的水分和温度,使其有一定的可塑性。
使得依附于油料表面的油脂分子间吸引力减弱,油脂分子与生胚凝胶部分的结合性降低,实现料胚在压榨时更容易分离油脂;4)榨油工序螺旋榨油机的主要部分是榨膛,榨膛是同榨笼和在榨笼内旋转的螺旋轴组成的。
它的工作过程是利用螺旋轴螺旋导程的缩小,使榨膛空间体积不断缩小而产生压榨作用;榨出的油脂从榨笼缝隙中挤压流出,同时将残渣压成屑状饼片,从榨轴末端不断排出。
用提升输送设备将压榨饼送入饼库暂存;进入压榨机的油料胚片经过榨机处理后,得到的毛油进入油渣分离工序。
5)油渣分离工序从榨油机出来的毛油,经过油渣分离、过滤机过滤后,油中含杂≤0.5%。
叶片过滤机具有结构紧凑、运转平稳、振动排渣(避免人工清渣,操作方便)、劳动强度低、全封闭式操作、物料损耗低等特点。
其工作原理是:待滤液经泵进入过滤机内并充满,在压力的作用下,滤液中的固体杂质被不锈钢滤网截留,并在滤网上形成滤饼,滤液透过滤网经滤咀进入出液管流出罐体,从而得到澄清的滤液。
随着过滤时间的增加,被截留在滤网上的固体杂质越来越多,使滤饼厚度不断增加,过滤阻力增大,罐内的压力升高,当压力升到一定值时需要排渣,停止向罐内输入滤液,然后通入蒸汽吹干滤饼。
关闭蒸汽,打开蝶阀,使滤叶振动,将滤网上的滤饼振落经罐体下方排渣口排出。
- 1、下载文档前请自行甄别文档内容的完整性,平台不提供额外的编辑、内容补充、找答案等附加服务。
- 2、"仅部分预览"的文档,不可在线预览部分如存在完整性等问题,可反馈申请退款(可完整预览的文档不适用该条件!)。
- 3、如文档侵犯您的权益,请联系客服反馈,我们会尽快为您处理(人工客服工作时间:9:00-18:30)。
武汉轻工大学《油脂加工工艺学》课程工艺设计说明书设计题目: 400T/D棉仁压榨车间工艺流程设计姓名 ______XXX______学号 ____1101079XX_院 (系)_ 食品科学与工程_专业 _ 油脂及植物蛋白质指导教师 ______XXX_________2014年 1月 5日课程设计任务书一、设计题目400D/T棉仁压榨车间工艺流程设计二、设计目的培养学生综合运用所学基础理论和专业知识的能力、分析和解决油脂工厂工艺设计中一般工程技术问题的能力;提高学生的绘图能力和计算机应用能力;增强和拓展学生的专业技能;通过课程工艺设计,深化学生对设计思想、设计方法、设计规范的理解,培养学生良好的学习方法,为毕业设计打下良好的基础。
三、设计任务400T/D棉仁压榨车间工艺流程设计。
四、时间安排2014年12月4日至6日查阅、收集资料;2014年12月7日至10日工艺设计计算并撰写设计计算说明书草稿;2014年12月21日至24日绘制工艺流程草图;2014年12月25日至27日完成设计计算说明书、工艺流程图并打印;2014年1月5日上交整套设计资料(包括电子版)。
五、设计内容1. 收集查阅设计资料;2. 物料衡算及热量衡算;3. 设备选型;4. 绘制工艺流程图;5. 撰写设计计算说明书。
六、设计工作要求1. 按时有序地完成各项设计内容;2. 独立完成设计任务,不弄虚作假,不抄袭别人的成果;3. 严格遵守纪律,在指定的地点进行课程设计;4. 严格遵守CAD设计室的有关规章制度;5. 按规范撰写设计计算说明书。
七、设计成绩评定由指导教师根据学生完成任务的情况、课程设计说明书及工艺图纸的质量及工作态度等进行综合评定。
成绩按优秀、良好、中等、及格和不及格五个等级进行评定。
优秀者人数一般不得超过总人数的20%。
成绩不及格者不能得到相应的学分,需重新进行课程设计后经考核及格方可获得学分。
八、参考文献1. 油脂制取与加工工艺学2. 化工工艺设计概论3. 化工工艺设计手册4. 化工原理5. 化工制图6. 食品工厂设计原理7. 油脂工厂设计手册8. 通风除尘及气力输送目录CONTENT一、总论 4二、工艺流程设计方案的确定 42.1 生产工艺方案 5三、工艺流程说明 53.1 棉仁高水分蒸胚 5 3.2 预榨 63.3 油渣分离7四、工艺计算74.1 物料衡算74.2 能量衡算10五、设备选型115.1 蒸炒锅选型11 5.2 螺旋榨油机选型11 5.3 斗式提升机选型11 5.4 刮板输送机选型125.5 油渣分离设备选型12六、设计体会13七、参考文献13八、附录一、总论棉籽即棉花的种子,外部为坚硬的褐色籽壳,形状大小也因品种而异,籽壳内有胚,是棉籽的主要部分,也称籽仁(棉仁)。
籽仁含油量可达35-45%,含蛋白质39%左右,含棉酚0.2%-2%。
目前棉籽也是重要的榨油原料,棉籽油含有大量的不饱和脂肪酸,其商业上的重要性在于它的油和其他产品。
精炼棉籽油一般呈橙黄色或棕色,脂肪酸中含有棕榈酸21.6-24.8%,硬脂酸1.9-2.4%,花生酸0-0.1%,油酸18.0-30.7%,亚油酸44.9-55.0%,精炼后的棉清油清除了棉酚等有毒物质,可供人食用。
棉清油中含有大量人体必需的脂肪酸,最宜与动物脂肪混合食用,因为棉清油中亚油酸的含量特别多,能有效抑制血液中胆固醇上升,维护人体的健康。
人体对棉清油的吸化吸收率为98%。
目前,我国的制油工业主要是采用的两种生产工艺,一是压榨法制油工艺,二是浸出法制油工艺。
借助机械外力的作用,将油脂从油料中挤压出来的取油方法称为压榨法取油。
按压榨时榨料所受压力的大小以及压榨取油的深度,压榨法取油可分为一次压榨和预榨。
一次压榨又称全压榨,要求压榨过程将榨料中尽可能多的油脂榨出,压榨后饼中残油3%~5%。
而预榨仅要求压榨过程将榨料中约70%的油脂榨出,榨饼中残油15%~18%,预榨饼再进行溶剂浸出取油。
压榨法取油与其他取油方法相比具有工艺简单、配套设备少、对油料品种适应性强、生产灵活、油品质量好、色泽浅、风味纯正等优点,但压榨后的饼残油量高,压榨过程的动力消耗大,榨条等零部件易磨损。
压榨取油之前通常要对料胚进行蒸炒,将生胚蒸炒成熟胚。
压榨毛油中含有一定量的饼屑,在油脂精炼之前必须进行除渣。
故典型的压榨工序包括蒸炒、压榨、毛油除渣。
二、工艺流程方案生产工艺流程设计和车间布置设计是两个重要设计项目。
他们决定着车间的功能和生产合理与否。
一般工艺流程设计开始于前,车间布置设计在工艺流程设计的基础上进行。
生产工艺流程设计的目的是通过用图解的形式表示出在声场过程中由原料制得成品时物料发生的变化及其流向,以及表示生产中采用的化工单元过程和机械设备。
根据工艺流程还可以进一步设计出管道流程和计量——控制流程。
因此,工艺流程设计是工艺设计的核心,而工艺流程设计的质量也是直接决定车间的生产命运。
流程的选择一般要注意:1、 尽可能充分地利用原料以期得到最大的产品得率;2、 所制取的产品质量优良;3、 生产的机械化、适当的自动化,以便掌握生产过程的工作 变得简单而容易;4、生产方法对操作人员的安全要考虑;2.1生产工艺方案→三、 工艺流程说明3.1蒸炒阶段油料生坯经过湿润、蒸炒、炒坯等处理转变为熟坯的过程称为蒸炒。
蒸炒是压榨取油生产中一道十分重要的工序,润湿蒸炒是指在蒸炒开始时利用添加水分或者是喷入直接蒸汽的方法使生坯达到最优的蒸炒开始水分,再将湿润过的料坯进行蒸炒,使蒸炒后熟坯中的水分、温度及结构性能最适宜压榨取油的要求。
一般蒸炒的最高温度不宜超过130℃,在蒸炒温度及料坯水分相对稳定的条件下,料坯蒸炒的时间愈长,蛋白质的变性程度愈深,生产中通常先采用层式蒸炒锅进行润湿蒸炒,再用炸机调整炒锅进行炒坯干燥。
a ) 润湿除了要求均匀润湿和充分搅拌外,还需要有一定的时间让水分在料坯间和料坯内部扩散均匀,其中棉籽采用高水分蒸胚的润湿水分为18%—22%,在润湿时为了使料坯有充分的时间与水分接触,保证料坯的润湿均匀,蒸炒锅润湿层的装料要满,装料量一般控制在80%—90%。
要关闭排气孔,保持蒸炒锅密闭,以防水分散失。
当采用高水分蒸坯时,必须有足够的蒸炒条件与之配合,以保证满足低水分入榨的要求,为此,可以在料坯进入蒸锅之前进行润湿,以延长蒸炒时间。
b)蒸坯蒸坯时要求料坯要蒸透蒸匀。
为此,蒸坯层的装料要满,装料量控制在80%-90%之间,以延长蒸坯时间。
要关闭排气孔,保持蒸炒锅密闭,以增大蒸锅空间的温度,充分发挥料坯的自蒸作用,并防止油脂氧化和棉酚的变性。
经过蒸坯,料配温度应提高至95℃-100℃。
湿润与蒸炒时间约需50-60min。
c)炒坯锅中的存料量要少,一般装料量控制在40%左右。
经过炒坯,出料温度应达到105℃-110℃,水分含量在5%-8%之间。
炒坯时间约20分钟,料坯一次压榨的入榨水分通常为1.0%-2.5%,入榨温度为125℃-130℃,而料坯入榨的预榨水分为4%-5%,入榨温度为110℃-115℃,因此,蒸炒全过程通常需要90-120min。
其中,料坯在层式蒸炒锅中约需1.5h,在榨机蒸炒锅中约需0.5h。
d)均匀蒸炒为了减少蒸炒过程的不一致性,生产上必须采取措施以保证料坯的均匀蒸炒:保证进入蒸炒锅的生坯质量(水分、坯厚及粉末度的)合格和稳定;均匀进料;对料坯的湿润应均匀一致,防止结团;蒸坯时充分利用料层的自蒸作用,防止硬皮的产生;蒸炒锅各层存料高度要合理,料门控制机构灵活可靠;加热应充分均匀,保证加热蒸汽质量及流量的稳定,夹套中空气和冷凝水的排除要及时;保证各层蒸锅的合理排气,保证足够的蒸炒时间;回榨油渣的掺入应均匀等。
3.2压榨压榨取油的过程,就是借助机械外力的作用,将油脂将渣料中挤压出来的过程,压榨取油效果取决于许多因素,主要包括渣料结构和压榨条件两大方面。
此外,榨油设备结构及其选型在某种程度上也将影响出油效果。
(a)榨料结构的影响,在要求残油率较低的情况下,榨料的合理低水分和高温是必需的,但榨料温度过高而超过某一限度(如130℃)不允许的;(b)压榨条件的影响,除榨料自身结构条件以外,压榨条件如压力、时间、温度、料层厚度、排油阻力等是提高出油效果的决定因素;(c)榨油设备的影响,榨油设备的类型和结构在一定程度上影响到工艺条件的确定,要求压榨设备在结构设计上应该尽可能满足多方面的要求。
此外,压榨取油的必要条件:(a)榨料通道中油脂的液压越大越好;(b)榨料中流油毛细管的直径越大越好,数量越多越好(即多孔性越大越好);(c)流油毛细管的长度越短越好;(d)压榨时间在一定限度内要尽量长些;(e)受压油脂的黏度越低越好。
3.3油渣分离毛油中悬浮杂质的存在,对毛油的输送、暂存及油脂精炼都产生不良影响,对毛油中悬浮杂质的分离,通常采用沉降和过滤的方法。
在实际生产中,一般将压榨毛油中悬浮杂质的分离工艺分为油-渣分离(粗分离)和悬浮物分离(细分离)两个步骤。
因此,在压榨毛油粗分离后,还必须进一步对毛油中悬浮物进行细分离,要求经过细分离后毛油中悬浮杂质含量控制在0.1%以下。
一般要求压榨过程的排渣量需控制在10%以下,而实际上有时可高达15%以上。
若仅利用澄油箱进行重力沉降,可以使分离后的毛油含杂量由10%-15%降至1%左右,而采用重力沉降和过滤机结合的方法,可使分离后毛油含杂量降至0.1%-0.3%。
采用通常的分离工艺和设备,分离出的饼渣含油率一般为20%-50%。
对于含渣量高的压榨毛油,最好采用沉降和过滤两步分离的方法,第一步在澄油箱内将大而重的固体饼渣分离,第二步用板框压滤机和叶片式过滤机分离细小的饼屑。
四、工艺计算4.1 物料衡算(以下为压榨工艺所需数据)含油率:棉仁40%含杂率:清理前5%;清理后0.50%水 分: 11%~12%含壳率: 剥壳分离后仁中含壳率6%~10% 剥壳分离后壳中含仁率≤0.50%4.1.1组份物料衡算⑴仁、杂(仁中含壳率取8%)无杂净仁=400×(1-8%)= 368 t/d净杂=400×8%=32 t/d(2) 油分、水分(仁壳中含水量统一取11%)仁中含油=368×35%=128.80 t/d仁中含水=368×11%=40.48 t/d4.1.2 按工序进行物料衡算脱水E 2 脱水E 3仁−−−→1生胚N 高水分蒸胚2N −−−−→半熟胚调整炒胚3N −−−→熟胚压榨−−→预榨饼N 4润湿吃水E 1 毛油E 4(1)高水分蒸胚棉仁润湿后水分含量在18%-22%,取20% 1111+=20%+E N E N ⨯润湿吃水生胚仁中含水率润湿吃水生胚 即: 1111×11%20%E N E N +=+ 代入数据得: E 1=45.00 t/d炒胚脱水,出料水分5%—8%,出料温度105—110℃,取水分为6%。