阀门生产制造工艺流程
阀门制造工艺
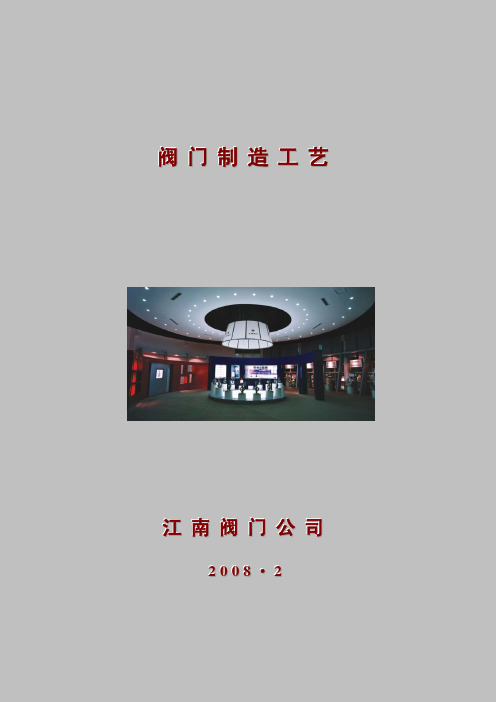
(3)夹砂(渣):夹砂(渣)俗称砂眼,是在铸件的内部出现不连贯的圆形 的或不规则的孔洞,孔内夹杂着型砂或钢渣,尺寸大小没有规律,聚集在一 处或多处,往往在上型的部分较多。
产生夹砂(渣)的原因:夹渣是由于钢水在冶炼或浇注过程中,离散的钢
原砂+固化剂(对甲苯磺酸水溶液)-(120~180S)-树脂+硅烷-(60~90S)-出砂
-4-
中国·江南阀门有限公司 上海江南造船阀门有限公司
(二) 铸件的铸造工艺设计: 正确而有效的控制铸件凝固是获得优质铸钢件的头等重要条件,采取正
确的工艺措施(浇注系统、冒口和冷铁、工艺补正量等),形成合理的工艺方案。阀门 铸钢件由于其壁厚不均匀,一般采取顺序冷却、顺序凝固的原则,以消除 铸件内部的缩孔和缩松等缺陷。
-1-
中国·江南阀门有限公司 上海江南造船阀门Байду номын сангаас限公司
切屑粘性大和加工硬化倾向强等缺点,很难达到要求的尺寸精度和光洁度, 给机加工的刀具、工艺和设备带来很大困难。另外,阀门密封面在加工精度、 配合角度和光洁度以及配对密封付的要求也很高,给机械加工带来很大难度。 (4)从阀门零件的工艺安排上讲,阀门的主要零件个数不多,结构相对简单, 大部分尺寸的加工精度不高,外部比较粗糙,这就给人一种属于简单机械的 印象。其实阀门的心脏密封部位可是极其精密,其密封面要求很高,平整度、 光洁度、硬度,以及两个密封面形成的密封付的吻合度都有达到零对零,才 能满足气体密封试验的零泄漏。这种以粗糙的基准来保证精密的零对零要求, 就是阀门加工的最大工艺难点。 (5)从阀门的试验和检验上讲,阀门是压力管道重要的启闭、调节元件,而 压力管道的使用工况是千变万化的,高温高压、低温深冷、易燃易爆、剧毒 强腐蚀。可是阀门制造的试验和检验条件不可能达到工况的同等要求,国际、 国内的各种阀门试验标准规定都是在接近常温的条件下,用空气或水当成介 质进行试验的。这就存在一个最根本的问题就是正常出厂试验合格的阀门产 品,在苛刻的实际工况条件下就会产生由于材料、铸件、密封等问题而难以 满足使用要求,还会发生重大的质量事故。难怪有些干了一辈子的老阀门专 家,越老越拘谨、越干越担心。
阀门生产工艺流程

阀门生产工艺流程
3.2.2.1阀体
阀门阀体(铸造,密封面堆焊)
铸件采购(按标准)——入厂检验(按标准)——堆焊槽
——超声波探伤(按图样)——堆焊及焊后热处理——精加工——研磨密封面——密封面硬度检验、着色探伤。
3.2.2.2阀门内件制造工序
A 、需堆焊密封面的内件如阀瓣、阀座等
原材料采购(按标准)——入厂检验(按标准)——制作毛坯(圆钢或锻件,按图纸工艺要求)——粗加工超声波探伤面(图样要求时)——粗加工堆焊槽——堆焊及焊后热处理——精加工各部——研磨密封面——密封面硬度检验、着色探伤。
B、阀杆
原材料采购(按标准)——入厂检验(按标准)——制作毛坯(圆钢或锻件,按图纸工艺要求)——粗加工堆焊槽——堆焊及焊后热处理——精加工各部——磨削外圆——阀杆表面处理(氮化、淬火、化学镀层)——最终处理(抛光、磨削等)——研磨密封面——密封面硬度检验、着色探伤。
C、不需堆焊密封面的内件等
原材料采购(按标准)——入厂检验(按标准)——制作毛坯(圆钢或锻件,按图纸工艺要求)——粗加工超声波探伤面(图样要求时)——精加工各部。
3.2.2.3紧固件
紧固件制造标准DL439-1991。
原材料采购(按标准)——入厂检验(按标准)——制作毛坯(圆钢或锻件,按图纸工艺要求)并取样进行必要的检验——粗加工——精加工——光谱检验。
3.2.2.4总装
领取零件——清理、清洗——粗装配(按图样)——水压试验(按图纸、工艺)——合格后、拆开、擦净——最终装配——与电装或执行器调试(对电动阀门)——油漆包装——发运。
阀门制造工艺流程(3篇)

第1篇一、引言阀门作为管道系统中不可或缺的组成部分,其质量直接影响到管道系统的正常运行。
阀门制造工艺流程是保证阀门质量的关键,本文将从原材料采购、工艺设计、加工制造、装配检验、包装运输等环节详细阐述阀门制造工艺流程。
二、原材料采购1. 材料选择:根据阀门用途、工作介质、工作温度和压力等因素,选择合适的金属材料。
如碳钢、不锈钢、合金钢等。
2. 材料采购:按照设计要求,从正规供应商处采购所需原材料,确保材料质量符合国家标准。
三、工艺设计1. 设计方案:根据阀门用途、工作介质、工作温度和压力等因素,确定阀门结构形式、连接方式、密封形式等。
2. 工艺方案:根据设计方案,制定合理的加工工艺,包括热处理、机加工、装配、检验等环节。
四、加工制造1. 零件加工:按照工艺方案,对原材料进行切割、锻造、热处理、机加工等工序,加工出合格零件。
2. 零件检验:对加工出的零件进行尺寸、形状、表面质量等检验,确保零件符合设计要求。
3. 零件装配:将检验合格的零件进行装配,包括阀体、阀盖、阀杆、密封件等。
4. 装配检验:对装配后的阀门进行外观、尺寸、密封性能等检验,确保阀门符合设计要求。
五、装配检验1. 装配:将加工合格的零件按照设计要求进行装配,包括阀体、阀盖、阀杆、密封件等。
2. 检验:对装配后的阀门进行外观、尺寸、密封性能等检验,确保阀门符合设计要求。
3. 性能试验:对阀门进行压力、流量、密封等性能试验,验证阀门在实际使用中的性能。
六、包装运输1. 包装:将检验合格的阀门进行清洁、擦干,然后按照要求进行包装,确保阀门在运输过程中不受损坏。
2. 运输:将包装好的阀门运输至客户指定地点,确保运输安全、快捷。
七、售后服务1. 技术咨询:为客户提供有关阀门选型、安装、维护等方面的技术咨询。
2. 故障排除:在客户使用过程中,如遇到阀门故障,及时为客户提供故障排除服务。
3. 维修保养:为客户提供阀门维修、保养等服务,确保阀门长期稳定运行。
阀门生产工艺流程
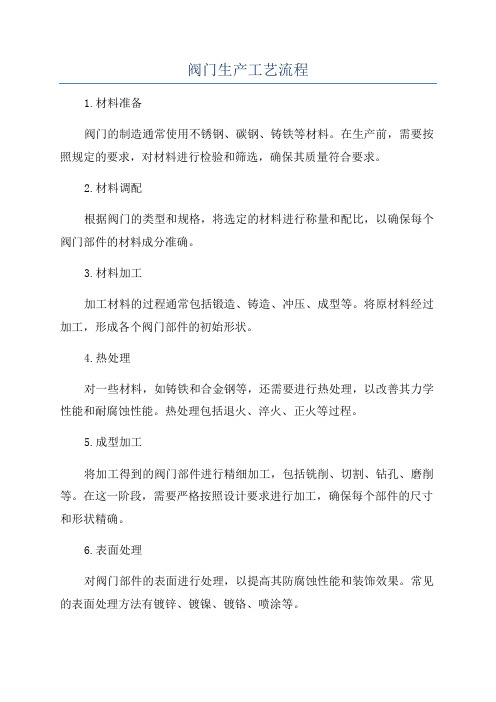
阀门生产工艺流程1.材料准备阀门的制造通常使用不锈钢、碳钢、铸铁等材料。
在生产前,需要按照规定的要求,对材料进行检验和筛选,确保其质量符合要求。
2.材料调配根据阀门的类型和规格,将选定的材料进行称量和配比,以确保每个阀门部件的材料成分准确。
3.材料加工加工材料的过程通常包括锻造、铸造、冲压、成型等。
将原材料经过加工,形成各个阀门部件的初始形状。
4.热处理对一些材料,如铸铁和合金钢等,还需要进行热处理,以改善其力学性能和耐腐蚀性能。
热处理包括退火、淬火、正火等过程。
5.成型加工将加工得到的阀门部件进行精细加工,包括铣削、切割、钻孔、磨削等。
在这一阶段,需要严格按照设计要求进行加工,确保每个部件的尺寸和形状精确。
6.表面处理对阀门部件的表面进行处理,以提高其防腐蚀性能和装饰效果。
常见的表面处理方法有镀锌、镀镍、镀铬、喷涂等。
7.装配将经过加工和处理的各个阀门部件进行装配。
这包括安装阀瓣、阀座、活塞、轴等,并根据需要进行密封件的安装。
8.检验对装配完成的阀门进行检验,包括尺寸、密封性能、压力等方面的检测。
确保阀门的质量符合标准和要求。
9.调试与包装对检验合格的阀门进行调试,确保其操作正常。
之后,将阀门进行清洁和包装,以便运输和存储。
10.发货和维护阀门在出厂前进行最后的质量检查,如确认标志、清晰的标识和正确的说明书等。
然后将阀门发往目的地。
阀门在使用过程中需要进行定期的维护保养,以确保其正常使用和延长使用寿命。
以上是一个简要的阀门生产工艺流程,实际阀门生产流程可能因具体的阀门类型、规格和生产技术的不同而有所差异。
阀门制造工艺流程
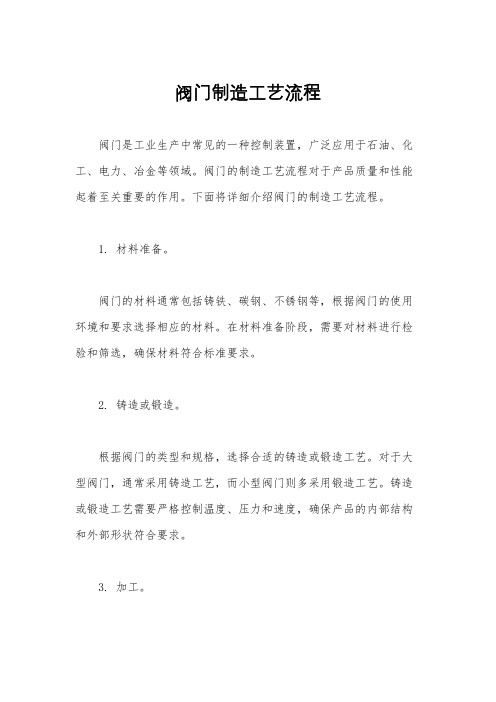
阀门制造工艺流程阀门是工业生产中常见的一种控制装置,广泛应用于石油、化工、电力、冶金等领域。
阀门的制造工艺流程对于产品质量和性能起着至关重要的作用。
下面将详细介绍阀门的制造工艺流程。
1. 材料准备。
阀门的材料通常包括铸铁、碳钢、不锈钢等,根据阀门的使用环境和要求选择相应的材料。
在材料准备阶段,需要对材料进行检验和筛选,确保材料符合标准要求。
2. 铸造或锻造。
根据阀门的类型和规格,选择合适的铸造或锻造工艺。
对于大型阀门,通常采用铸造工艺,而小型阀门则多采用锻造工艺。
铸造或锻造工艺需要严格控制温度、压力和速度,确保产品的内部结构和外部形状符合要求。
3. 加工。
经过铸造或锻造的阀门需要进行加工,包括车削、铣削、钻孔等工艺。
加工工艺需要精确控制尺寸和表面粗糙度,以确保阀门的密封性能和使用寿命。
4. 组装。
在阀门的组装过程中,需要将阀体、阀盖、阀芯等零部件进行组装,并进行密封性能测试。
组装工艺需要严格按照工艺要求进行,确保阀门的各项性能符合标准。
5. 检测。
阀门制造完成后,需要进行各项性能和质量的检测。
包括密封性能测试、耐压测试、耐磨测试等。
检测工艺需要严格按照标准要求进行,确保产品的质量和性能符合要求。
6. 包装。
经过检测合格的阀门需要进行包装,以防止在运输和使用过程中受到损坏。
包装工艺需要选择合适的包装材料和方式,确保产品的完好性。
7. 出厂。
最后,经过包装的阀门可以出厂销售或存放。
在出厂过程中,需要对产品进行标识和记录,以便跟踪产品的使用和维护情况。
以上就是阀门制造工艺流程的详细介绍,每个环节都需要严格控制和管理,以确保产品的质量和性能符合要求。
希望本文对阀门制造工艺有所帮助,谢谢阅读!。
阀门制造工艺流程

阀门制造工艺流程
阀门制造工艺流程是指将原材料经过一系列的加工、装配、检验等工序,最终制造成符合要求的阀门的过程。
下面将详细介绍阀门制造的主要工艺流程。
首先,阀门制造的第一步是选材。
根据阀门的使用条件和要求,选用适当的材料,如铸铁、碳钢、不锈钢等。
接下来,进行铸造工艺。
对于铸铁材料,使用砂型铸造工艺,通过砂型制作、铸造、冷却等步骤,得到阀门的铸件。
对于其他材料,可以采用离心铸造、压力铸造等工艺。
铸造完成后,进入下一步的加工工艺。
首先是铸件的清理和修整,包括去除铸件上的氧化皮和砂浆,并修正不合格尺寸。
然后进行粗加工,如铣削、钻孔等,以消除铸件内外表面的缺陷和余量。
紧接着是精加工工艺。
通过数控机床等设备,对阀体、阀盖等进行精度修整,以保证阀门的密封性和精度要求。
同时,也要对阀杆、阀芯等零部件进行加工。
加工完成后,进行组装工艺。
将阀座、阀杆、阀盖、阀板等零部件按照设计要求进行组装,并进行严格的拧紧、固定,以确保阀门的正常运行。
组装完毕后,进行测试和调试工艺。
使用水压试验或气密性试验等方法,检验阀门的密封性能、开关灵活性以及工作压力的
承受能力。
根据测试结果,进行必要的调整和修正,以确保阀门达到标准要求。
最后,进行表面处理和涂装工艺。
对阀门进行清洁、除锈处理,然后进行表面喷涂,以提高阀门的耐腐蚀、抗氧化能力,延长使用寿命。
综上所述,阀门制造工艺流程包括选材、铸造、加工、组装、测试调试、表面处理等多个环节。
每个环节都需要严格按照质量标准和技术要求进行操作,以确保阀门最终的质量和性能。
阀门工艺流程

阀门工艺流程
阀门是工业生产中常用的一种控制元件,其工艺流程对产品质
量和性能有着重要影响。
阀门工艺流程主要包括原材料采购、加工
制造、装配调试和质量检验等环节。
首先,原材料采购是阀门工艺流程的第一步。
在采购原材料时,需要对材料的质量、规格、数量进行严格把控,确保原材料符合生
产要求。
同时,还需要对供应商进行严格的审核和评估,选择具有
稳定供货能力和良好信誉的供应商合作。
其次,加工制造是阀门工艺流程的核心环节。
在加工制造过程中,需要根据产品的设计要求,进行材料切割、成型、焊接、加工
等工艺操作,确保产品的尺寸精度和表面质量达到要求。
同时,还
需要对加工设备进行定期维护和保养,确保设备的正常运转和生产
效率。
接着,装配调试是阀门工艺流程的重要环节。
在装配调试过程中,需要将加工制造好的零部件进行组装,进行密封性能测试、通
气性能测试、耐压性能测试等,确保产品的性能稳定和可靠。
同时,还需要对装配工艺进行不断改进和优化,提高装配效率和产品质量。
最后,质量检验是阀门工艺流程的最后一道关。
在质量检验过程中,需要对产品的外观质量、尺寸精度、性能指标等进行全面检测,确保产品符合相关标准和要求。
同时,还需要建立完善的质量档案和追溯体系,对产品的质量进行跟踪和管理。
总之,阀门工艺流程是一个复杂的系统工程,需要各个环节的紧密配合和协同合作。
只有严格执行工艺流程,不断优化和改进,才能生产出质量可靠的阀门产品,满足市场和客户的需求。
阀门生产的主要步骤
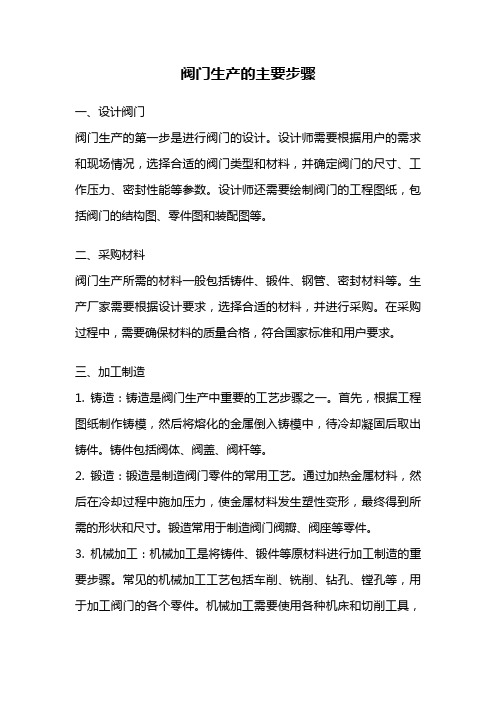
阀门生产的主要步骤一、设计阀门阀门生产的第一步是进行阀门的设计。
设计师需要根据用户的需求和现场情况,选择合适的阀门类型和材料,并确定阀门的尺寸、工作压力、密封性能等参数。
设计师还需要绘制阀门的工程图纸,包括阀门的结构图、零件图和装配图等。
二、采购材料阀门生产所需的材料一般包括铸件、锻件、钢管、密封材料等。
生产厂家需要根据设计要求,选择合适的材料,并进行采购。
在采购过程中,需要确保材料的质量合格,符合国家标准和用户要求。
三、加工制造1. 铸造:铸造是阀门生产中重要的工艺步骤之一。
首先,根据工程图纸制作铸模,然后将熔化的金属倒入铸模中,待冷却凝固后取出铸件。
铸件包括阀体、阀盖、阀杆等。
2. 锻造:锻造是制造阀门零件的常用工艺。
通过加热金属材料,然后在冷却过程中施加压力,使金属材料发生塑性变形,最终得到所需的形状和尺寸。
锻造常用于制造阀门阀瓣、阀座等零件。
3. 机械加工:机械加工是将铸件、锻件等原材料进行加工制造的重要步骤。
常见的机械加工工艺包括车削、铣削、钻孔、镗孔等,用于加工阀门的各个零件。
机械加工需要使用各种机床和切削工具,如车床、铣床、钻床等。
4. 焊接:焊接是将阀门的各个零件进行连接的方法之一。
通过加热和施加压力,使金属材料熔化并连接在一起。
常见的焊接方法包括电弧焊、气焊、TIG焊等。
四、装配调试在阀门生产的装配调试阶段,将已经加工好的各个零件进行组装。
首先,将阀体、阀盖、阀杆等零件进行装配,然后根据设计要求安装密封件、传动装置等。
装配完成后,需要进行阀门的调试,包括检查阀门的开闭灵活性、密封性能等。
五、表面处理和涂装阀门的表面处理和涂装是为了提高阀门的耐腐蚀性和美观度。
常见的表面处理方法包括喷砂、镀锌、电镀等,常见的涂装方法包括喷涂、浸涂等。
表面处理和涂装需要根据阀门的材料和使用环境进行选择。
六、质量检验阀门生产完成后,需要进行质量检验。
质量检验包括外观检查、尺寸检查、材料分析、压力测试等。