换热器的结构
换热器类型和结构

换热器类型和结构内容1、换热器的定义换热器是将热流体的部分热量传递给冷流体的设备,即在一个大的密闭容器内装上水或其他介质,而在容器内有管道穿过。
让热水从管道内流过。
由于管道内热水和容器内冷热水的温度差,会形成热交换,也就是初中物理的热平衡,高温物体的热量总是向低温物体传递,这样就把管道里水的热量交换给了容器内的冷水,换热器又称热交换器。
2、换热器的分类与结构换热器按用途分类可以分为:冷却器、冷凝器、加热器、换热器、再沸器、蒸气发生器、废热(或余热)锅炉。
按换热方式可以分为:直接接触式换热器(又叫混合式换热器)、蓄热式换热器和间壁式换热器。
下面主要介绍一下按换热方式分类的换热器:1)直接接触式换热器直接接触式交换器是依靠冷、热流体直接接触而进行传热的,这种传热方式避免了传热间壁及其两侧的污垢热阻,只要流体间的接触情况良好,就有较大的传热速率。
故凡允许流体相互混合的场合,都可以采用混合式热交换器,例如气体的洗涤与冷却、循环水的冷却、汽—水之间的混合加热、蒸汽的冷凝等等。
它的应用遍及化工和冶金企业、动力工程、空气调节工程以及其它许多生产部门。
常用的混合式换热器有:冷却塔、气体洗涤塔、喷射式换热器和混合式冷凝器。
2)蓄热式换热器蓄热式换热器用于进行蓄热式换热的设备。
内装固体填充物,用以贮蓄热量。
一般用耐火砖等砌成火格子(有时用金属波形带等)。
换热分两个阶段进行。
第一阶段,热气体通过火格子,将热量传给火格子而贮蓄起来.第二阶段,冷气体通过火格子,接受火格子所储蓄的热量而被加热。
这两个阶段交替进行。
通常用两个蓄热器交替使用,即当热气体进入一器时,冷气体进入另一器。
常用于冶金工业,如炼钢平炉的蓄热室。
也用于化学工业,如煤气炉中的空气预热器或燃烧室,人造石油厂中的蓄热式裂化炉。
3)间壁式换热器此类换热器中,冷热俩流体间用一金属隔开,以便俩种流体不相混合而进行热量传递。
在化工生产中冷热流体经常不能直接接触,故而间壁式换热器是最常用的一种换热器。
十三种类型换热器结构原理及特点(图文并茂)

十三种类型换热器结构原理及特点(图文并茂)一、板式换热器的构造原理、特点:板式换热器由高效传热波纹板片及框架组成。
板片由螺栓夹紧在固定压紧板及活动压紧板之间,在换热器内部就构成了许多流道,板与板之间用橡胶密封。
压紧板上有本设备与外部连接的接管。
板片用优质耐腐蚀金属薄板压制而成,四角冲有供介质进出的角孔,上下有挂孔。
人字形波纹能增加对流体的扰动,使流体在低速下能达到湍流状态,获得高的传热效果。
并采用特殊结构,保证两种流体介质不会串漏。
板式换热器结构图二、螺旋板式换热器的构造原理、特点:螺旋板式换热器是一种高效换热器设备,适用汽-汽、汽-液、液-液,对液传热。
它适用于化学、石油、溶剂、医药、食品、轻工、纺织、冶金、轧钢、焦化等行业。
结构形式可分为不可拆式(Ⅰ型)螺旋板式及可拆式(Ⅱ型、Ⅲ型)螺旋板式换热器。
螺旋板式换热器结构图三、列管式换热器的构造原理、特点:列管式换热器(又名列管式冷凝器),按材质分为碳钢列管式换热器,不锈钢列管式换热器和碳钢与不锈钢混合列管式换热器三种,按形式分为固定管板式、浮头式、U型管式换热器,按结构分为单管程、双管程和多管程,传热面积1~500m2,可根据用户需要定制。
列管式换热器结构图四、管壳式换热器的构造原理、特点:管壳式换热器是进行热交换操作的通用工艺设备。
广泛应用于化工、石油、石油化工、电力、轻工、冶金、原子能、造船、航空、供热等工业部门中。
特别是在石油炼制和化学加工装置中,占有极其重要的地位。
换热器的型式。
管壳式换热器结构图五、容积式换热器的构造原理、特点:钢衬铜热交换器比不锈钢热交换器经济,并且技术上有保证。
它利用了钢的强度和铜的耐腐蚀性,即保证热交换器能承受一定工作压力,又使热交换器出水质量好。
钢壳内衬铜的厚度一般为1.0mm。
钢衬铜热交换器必须防止在罐内形成部分真空,因此产品出厂时均设有防真空阀。
此阀除非定期检修是绝对不能取消的。
部分真空的形成原因可能是排出不当,低水位时从热交换器,或者排水系统不良。
板式换热器内部结构
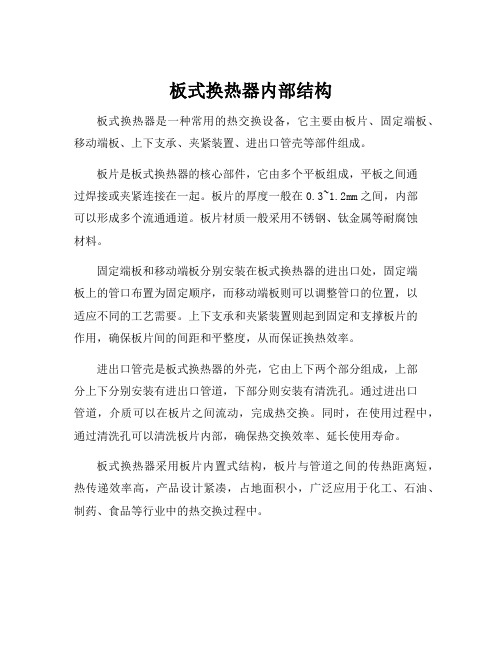
板式换热器内部结构
板式换热器是一种常用的热交换设备,它主要由板片、固定端板、移动端板、上下支承、夹紧装置、进出口管壳等部件组成。
板片是板式换热器的核心部件,它由多个平板组成,平板之间通
过焊接或夹紧连接在一起。
板片的厚度一般在0.3~1.2mm之间,内部
可以形成多个流通通道。
板片材质一般采用不锈钢、钛金属等耐腐蚀
材料。
固定端板和移动端板分别安装在板式换热器的进出口处,固定端
板上的管口布置为固定顺序,而移动端板则可以调整管口的位置,以
适应不同的工艺需要。
上下支承和夹紧装置则起到固定和支撑板片的
作用,确保板片间的间距和平整度,从而保证换热效率。
进出口管壳是板式换热器的外壳,它由上下两个部分组成,上部
分上下分别安装有进出口管道,下部分则安装有清洗孔。
通过进出口
管道,介质可以在板片之间流动,完成热交换。
同时,在使用过程中,通过清洗孔可以清洗板片内部,确保热交换效率、延长使用寿命。
板式换热器采用板片内置式结构,板片与管道之间的传热距离短,热传递效率高,产品设计紧凑,占地面积小,广泛应用于化工、石油、制药、食品等行业中的热交换过程中。
管壳式换热器内部结构
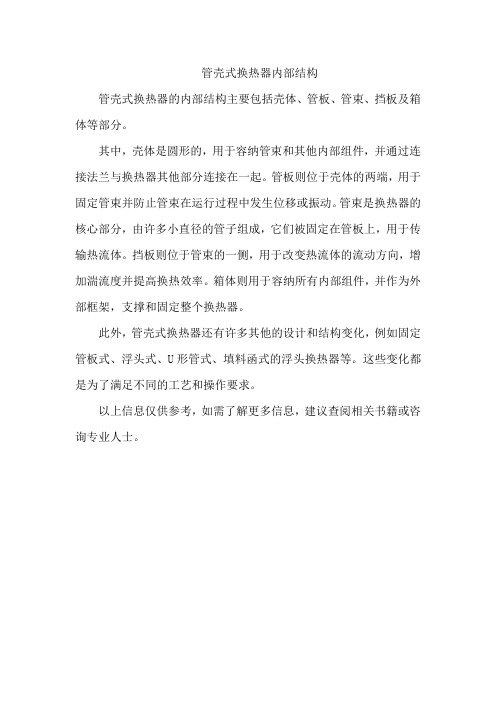
管壳式换热器内部结构
管壳式换热器的内部结构主要包括壳体、管板、管束、挡板及箱体等部分。
其中,壳体是圆形的,用于容纳管束和其他内部组件,并通过连接法兰与换热器其他部分连接在一起。
管板则位于壳体的两端,用于固定管束并防止管束在运行过程中发生位移或振动。
管束是换热器的核心部分,由许多小直径的管子组成,它们被固定在管板上,用于传输热流体。
挡板则位于管束的一侧,用于改变热流体的流动方向,增加湍流度并提高换热效率。
箱体则用于容纳所有内部组件,并作为外部框架,支撑和固定整个换热器。
此外,管壳式换热器还有许多其他的设计和结构变化,例如固定管板式、浮头式、U形管式、填料函式的浮头换热器等。
这些变化都是为了满足不同的工艺和操作要求。
以上信息仅供参考,如需了解更多信息,建议查阅相关书籍或咨询专业人士。
四种换热器的结构特点及优缺点

四种换热器的结构特点及优缺点3、四种换热器的结构特点及优缺点。
(1)固定管板式换热器组成:管箱、管板、换热管、壳体、折流板或支撑板、拉杆、定距管等。
结构特点:管板与壳体之间采用焊接连接。
两端管板均固定,可以是单管程或多管箱,管束不可拆,管板可延长兼作法兰。
优点:结构简单,制造方便,在相同管束情况下其壳体内径最小,管程分程较方便。
缺点:壳程无法进行机械清洗,壳程检查困难,壳体与管子之间无温差补偿元件时会产生较大的温差应力,即温差较大时需采用膨胀节或波纹管等补偿元件以减小温差应力。
(2)浮头式换热器组成:管箱、管板、换热管、壳体、折流板或支撑板、拉杆、定距管、钩圈、浮头盖等。
结构特点:一端管板与壳体固定,另一端管板(浮动管板)与壳体之间没有约束,可在壳体内自由浮动。
只能为多管程,布管区域小于固定管板式换热器,管板不能兼作法兰,一般有管束滑道。
优点:不会产生温差应力,浮头可拆分,管束易于抽出或插入,便于检修和清洗。
缺点:结构较复杂,操作时浮头盖的密封情况检查困难。
(3)U形管式换热器组成:管箱、管板、U形换热管、壳体、折流板或支撑板、拉杆、定距管等。
结构特点:只有一个管板和一个管箱,壳体与换热管之间不相连,管束能从壳体中抽出或插入。
只能为多管程,管板不能兼作法兰,一般有管束滑道。
总重轻于固定管板式换热器。
优点:结构简单,造价较低,不会产生温差应力,外层管清洗方便。
缺点:管内清洗因管子成U形而较困难,管束内围换热管的更换较困难,管束的固有频率较低易激起振动。
(4)填料函式换热器组成:管箱、管板、管束、壳体、折流板或支撑板、拉杆、定距管、填料函等。
结构特点:一侧管箱可以滑动,壳体与滑动管箱之间采用填料密封。
管束可抽出,管板不兼作法兰。
优点:填料函结构较浮头简单,检修清洗方便;无温差应力,(具备浮头式换热器的优点,消除了固定管板式换热器的缺点)。
缺点:密封性能较差,不适用于易挥发、易燃、易爆和有毒介质。
换热器结构图

当前位置:结构原理板式换热器结构1.固定压紧板2.连接口3.垫片4.板片5.活动压紧板6.下导杆7.上导杆8.夹紧螺栓9.支柱板式换热器结构板式换热器是由传热板片和框架组成,板上有四个角孔,供传热的两种液体通过,传热板片安装在一个侧面有固定板和活动板的框架内,用夹紧螺栓夹紧。
传热板片波纹为人字形,相邻板片具有反方向的人字形沟槽,沟槽的交叉点相互支撑形成接触点,介质流动时形成湍流,从而获得很高的传热效率。
板式换热器特点◎传热效率高:传热板片波纹结构设计合理,有利于强化传热,可以使介质在较低流速下形成激烈的湍流状态,结垢可能性降低,传热效率高“”,比传统换热器换热效率高 3-5 倍;◎结构紧凑:板式换热器由于传热系数高,所以结构极为紧凑,占地面积小,在换热量相等的条件下,其所占空间仅为管壳式换热器的 30%-40% ,节约大量空间;◎阻力损失小:传热板片处波纹方向科学,采用流线型设计,避免流动死区,流道当量直径大,减少了压力损失;◎热损失小:因结构紧凑体积小,换热器外表面积小,所以热损失小,通常设备无需保温;◎维修、清洗方便:在维修、清洗设备时,可快速拆下夹紧螺栓,移动板片清洗,更换胶垫,一般当天可拆洗安装完毕;◎随机应变:由于板式换热器容易拆卸,可根据需求通过增减换热板片来改变换热器面积,或者变更流程达到最合适的换热效果;◎运行安全可靠:本公司的板式换热器密封性能好,在板片夹紧状态下变形小,回弹性好,组装及维修重新组装后垫片密封可靠,并且在密封装置上设计了两道密封,更加安全可靠;◎投资低:在相同热量的前提下,板式换热器比传统换热器相比,其换热器面积、占地面积、流体阻力、冷却水用量等项目数减少,使得设备投资、基建投资、动力消耗等费用大大降低;◎应用广泛:可广泛用于化学工业、钢铁工业、机械制造业、食品工业、电力工业、纺织工业、造纸工业、集中供暖、油脂工业、船舶、医药、空调、水处理等众多领域。
板式换热器结构图BR系列板式换热器BRG系列汽水板式换热器换热机组★换热机组的组成北京思创伟业换热设备有限公司制造的换热机组是一套组装在底座上的热交换组合装置,换热机组包括以下组件:◎板式换热器◎循环泵◎电控柜◎补水定压装置◎仪器、仪表◎温控设备◎机组底座◎机组管道连接所必需的阀门、管线和管道附件★换热机组主要优点◎低噪音;◎按用户的需要量身定做,经济合理;◎先进的优化设计, 技术方案最佳;◎选择,多种控制方式供您选择,丰俭由己;◎多种系列、型号板式换热器,总有一款适合您;◎高品质配套设备,性能优良;◎全部厂内组装测试,良好运行有保障;◎机构紧凑,占地面积小;◎设备在生产过程中的运行、维修费用低;◎成熟的经验和完善的售后服务。
板式换热器典型结构

板式换热器典型结构板式换热器是一种常见的换热设备,广泛应用于化工、冶金、电力、制药等工业领域。
它的典型结构包括:板叠堆、板组、端板、挡板、密封条和连接件等部分。
1. 板叠堆板叠堆是板式换热器的核心部分,由多个平行的金属板组成。
这些金属板通常是波纹状的,以增加换热面积和强化对流传热效果。
板叠堆的材质通常选择不锈钢、钛合金、镍合金等耐腐蚀材料,以适应不同工况的需求。
2. 板组板组是由板叠堆叠加在一起形成的整体结构。
板组的数量和排列方式决定了换热器的换热效率和流体的流动路径。
一般来说,板组越多,换热面积越大,换热效果越好。
板组的排列方式主要有单通道、多通道和多效等形式,用于满足不同的换热要求。
3. 端板端板是将板组固定在一起的部分,通常由厚重的金属材料制成。
端板具有良好的密封性能,能够确保流体在板组内部的流动方向和流量分布均匀。
端板上还设置有进出口管道和连接口,用于与外部系统进行流体的连接和调节。
4. 挡板挡板位于板组的两端,用于分隔流体的进出口。
挡板上开设了流体通道和孔洞,使得流体可以在板组内部按照预定的路径流动,从而实现换热的目的。
挡板的设计和布置对于换热器的性能和效率有着重要的影响。
5. 密封条密封条位于板叠堆和端板之间,用于保持板组内部的密封性。
密封条通常采用橡胶或聚四氟乙烯等材料制成,具有良好的耐腐蚀性和密封性能。
通过适当的压力和温度控制,可以确保换热器的工作安全和稳定。
6. 连接件连接件用于将板组、端板、挡板和密封条等部分紧密地连接在一起。
连接件通常采用螺栓、螺母和密封垫等元件组成,能够承受换热器内部流体的压力和温度载荷。
连接件的质量和紧固程度对于换热器的性能和安全运行至关重要。
板式换热器的典型结构包括板叠堆、板组、端板、挡板、密封条和连接件等部分。
这些部分相互协作,通过流体的流动和热量的传递,实现了高效的换热过程。
板式换热器具有结构紧凑、换热效率高、适应性强等优点,是现代工业中不可或缺的重要设备之一。
换热器类型和结构

换热器类型和结构换热器是一种将热能从一个介质传递到另一个介质的设备,常用于工业和家庭中,用于加热和冷却过程。
换热器的类型和结构多种多样,下面将介绍几种常见的换热器类型和结构。
1. 管壳式换热器(Shell and tube heat exchanger)管壳式换热器由一个外壳和多个管束组成,热介质通过管束中流动,冷介质在外壳中流动。
管束通常由多个并列的管道组成,管道两端连接在固定的管板上。
热介质从一个管道进入,冷介质从另一个管道进入,通过壁面传递热能。
管壳式换热器具有结构简单,换热效率高,适用于高温、高压、高流量的工况。
2. 板式换热器(Plate heat exchanger)板式换热器由多个平行排列的金属板组成,每两个板之间形成一个热交换通道。
热介质和冷介质分别流经交错摆放的板状导热表面,通过板壁传递热量。
板式换热器具有体积小、效率高、维修方便等优点,广泛应用于化工、船舶、食品加工等行业。
3. 螺旋板换热器(Spiral plate heat exchanger)螺旋板换热器由两个平行的螺旋板组成,形成多个独立的对流通道。
热介质和冷介质分别流经螺旋板的内外侧,通过螺旋通道的壁面传递热量。
螺旋板换热器具有紧凑结构、传热效率高、能耗低等特点,适用于高粘度介质和高含固体颗粒介质。
4. 换气式换热器(Air-to-air heat exchanger)换气式换热器用于空气调节系统中,用于回收室内排出空气中的热量和湿度。
换热器通过两个独立的通风系统,使室内和室外空气交换热量。
热空气通过热交换器释放热量给冷空气,从而提高能源利用效率。
5. 水冷却器(Water-cooled heat exchanger)水冷却器是一种热交换装置,用于冷却工业设备或发动机。
水通过冷却器中的管道流动,吸收设备或发动机产生的热量,然后通过冷却器外壳的散热片将热量散发到空气中。
水冷却器可以降低设备或发动机的温度,提高其工作效率和寿命。
- 1、下载文档前请自行甄别文档内容的完整性,平台不提供额外的编辑、内容补充、找答案等附加服务。
- 2、"仅部分预览"的文档,不可在线预览部分如存在完整性等问题,可反馈申请退款(可完整预览的文档不适用该条件!)。
- 3、如文档侵犯您的权益,请联系客服反馈,我们会尽快为您处理(人工客服工作时间:9:00-18:30)。
换热器的结构管壳式换热器就是具有换热管和壳体的一种换热设备,换热管与管板连接,再用壳体固定。
按其结构型式,主要分为:固定管板式换热器、浮头式换热器、U形管式换热器、填料函式换热器、方形壳体翅片管换热器等。
详细结构如下:固定管板式换热器:固定管板式换热器结构如上图所示,换热器的两端管板采用焊接方法与壳体连接固定。
换热管可为光管或低翅管。
其结构简单,制造成本低,能得到较小的壳体内径,管程可分成多样,壳程也可用纵向隔板分成多程,规格范围广,故在工程中广泛应用。
其缺点是壳侧不便清洗,只能采用化学方法清洗,检修困难,对于较脏或对材料有腐蚀性的介质不能走壳程。
壳体与换热管温差应力较大,当温差应力很大时,可以设置单波或多波膨胀节减小温差应力浮头式换热器浮头式换热器结构如下图,其一端管板与壳体固定,而另一端的管板可以在壳体内自由浮动。
壳体和管束对热膨胀是自由的,故当两种介质的温差较大时,管束与壳体之间不会产生温差应力。
浮头端设计成可拆结构,使管束可以容易地插入或抽出,这样为检修和清洗提供了方便。
这种形式的换热器特别适用于壳体与换热管温差应力较大,而且要求壳程与管程都要进行清洗的工况。
浮头式换热器的缺点是结构复杂,价格较贵,而且浮头端小盖在操作时无法知道泄漏情况,所以装配时一定要注意密封性能U形管式换热器上图为双壳程U形管式换热器。
U形管式换热器是将换热管弯成U形,管子两端固定在同一块管板上。
由于换热管可以自由伸缩,所以壳体与换热管无温差应力。
因U形管式换热器仅有一块管板,所以结构较简单,管束可从壳体内抽出,壳侧便于清洗,但管内清洗稍困难,所以管内介质必须清洁且不易结垢。
U形管式换热器一般用于高温高压情况下,尤其是壳体与换热管金属壁温差较大时。
壳程可设置纵向隔板,将壳程分为两程(如图中所示)。
填料函式换热器上图为填料函式双管程双壳程换热器,填料函式换热器的换热管束可以自由滑动,壳侧介质靠填料密封。
对于一些壳体与管束温差较大,腐蚀严重而需经常更换管束的换热器,可采用填料函式换热器。
它具有浮头换热器的优点,又克服了固定管板式换热器的缺点,结构简单,制造方便,易于检修清洗。
填料函式换热器的缺点:使用直径小;不适于高温、高压条件下;壳程介质不适于易挥发、易燃、易爆、有毒等介质方形壳体翅片管换热器:方形壳体翅片管换热器的壳体为方箱形(如上图所示),其换热管为带翅片的翅片管。
换热管可为单排或多排换热管。
翅片材料可采用碳钢、不锈钢、铝或铜材等。
翅片的翅高、翅距和翅片厚度可根据实际工况而定。
这种形式的换热器因为采用了翅片管,可大大强化传热面积,所以特别适用于给热系数较低的流体。
壳程流通面积可设计较大,流动阻力较小,所以对于压力较低和对压力降要求较小的流体特别适用。
在实际生产中,常常用这种换热器来加热或冷却低压空气。
其缺点:因为壳体为方箱形,虽然管程可承受高压介质,但壳程只能承受较低压力的介质。
这种换热器的金属消耗量大,制造成本较高。
在实际生产装置中,为提高壳程的耐压能力,往往将壳体做成圆形,而管束采用方形布管。
结构可参见下面附图左图为我厂设计制造的空气段间冷却器的剖视图。
该换热器的管束采用方形排列的翅片管,管束长度为3.7m。
为提高壳体的承压能力,壳体采用圆筒形,直径900mm。
换热管为紫铜整体轧制翅片管,翅片外径36mm,翅片根径为20mm,换热管内径16mm,翅片间距2.5mm,翅片厚度为0.5mm,换热总面积为440m2。
空气条件:流量:30000Nm3/h温度:100-40ºC工作压力:0.1MPa压降:150mm水柱总热负荷:597000kcal/h管壳式换热器主要由换热管束、壳体、管箱、分程隔板、支座等组成。
换热管束包括换热管、管板、折流板、支持板、拉杆、定距管等。
换热管可为普通光管,也可为带翅片的翅片管,翅片管有单金属整体轧制翅片管、双金属轧制翅片管、绕片式翅片管、叠片式翅片管等,材料有碳钢、低合金钢、不锈钢、铜材、铝材、钛材等。
壳体一般为圆筒形,也可为方形。
管箱有椭圆封头管箱、球形封头管箱和平盖管箱等。
分程隔板可将管程及壳程介质分成多程,以满足工艺需要。
管壳式换热器在结构设计时,必须考虑许多因素,例如传热条件、材料、介质压力、温度、管壳程壁温温差、介质结垢情况、流体性质以及检修和清洗条件等等,从而确定一种适合的结构形式。
对于同一种形式的换热器,由于各种不同工况,往往采用的结构并不相同。
在工程设计中,应按其特定的条件进行分析设计,以满足工艺需要。
换热面积的计算在管壳式换热器的设计中,确定了一种换热器的结构形式后,首先必须确定的一个重要因素是有效换热面积,换热面积的多少决定了换热器的大小。
如果换热面积太小,使工艺过程不能实现,使换热器介质出口温度不能得到有效控制。
如果换热面积太大,不仅造成材料的浪费,增加投资,而且增大了换热器的体积,使其占据过多的空间。
计算换热面积的一个重要参数是总传热系数,它包括冷热介质的给热系数、介质的污垢系数和金属壁的传热系数。
其中计算较为复杂的是介质的给热系数。
介质的给热系数不仅与介质的物性有关,而且与介质的流动状态有关。
介质的流动状态是由换热器的结构决定的,如果换热器的结构作很小改动,将引起介质流动状态作较大的变化。
在一个换热器中,同一种介质的温度是不断变化的,所以在换热器中的不同位置,同一种介质的热力学数据因温度的不同而不同。
在实际计算中,往往将一种介质分成许多个温度区域,在不同的温度区域,对介质的热力学数据作相应的计算。
在换热器的设计过程中,换热面积确实定是最为关键的一步,它不仅需要计算方法正确严密,而且各种参数必须十分精确。
换热器的分析计算过程是一个动态的计算过程,往往须不断地调整换热器的结构参数。
而管壳式换热器的结构参数很多,其中一项的改变将会使计算结果产生很大变化,所以需要不断的反复,不仅要使换热面积满足需要,而且还应兼顾到其它许多因素,例如介质阻力情况等等。
流体阻力的计算在管壳式换热器的分析设计中,流体的阻力计算是极为重要的,流体的阻力对于工艺过程是较为关键的参数,它不仅影响到整个系统的压力平衡,而且对于节能降耗也起到重要的作用。
在实际生产中,常常由于流体阻力不适而使工艺过程难以实现。
在管壳式换热器中,流体的阻力包括壳程流体的阻力及管程流体的阻力。
壳程流体阻力包括介质进口管、出口管、换热管间、折流板缺口等处阻力。
介质进出口管阻力可以通过改变进出口管的大小来进行调节。
换热管间的介质阻力可以通过改变换热管间的介质流通面积来进行调节,例如改变换热管的布管形式,改变壳体直径,改变折流板间距等。
折流板缺口处的介质阻力可以通过改变折流板缺口高度来进行调节。
管程流体的阻力包括介质进出口管、换热管内、管箱等处阻力。
介质进出口管阻力可以通过改变进出口管的大小来进行调节。
换热管内的介质阻力可以通过改变换热管的数量,换热管的长度,换热管的直径以及管程数等来进行调节。
管箱处的介质阻力可以通过改变管箱处的介质流通面积来进行调节。
换热器中流体的阻力计算,应分别计算出换热器内部各处的流体阻力。
只有掌握了介质阻力的分布情况,才能够通过有效调整换热器各处的结构尺寸来改变介质的阻力,从而满足工艺要求。
管束震动分析对于管壳式换热器,一个容易被无视的问题是换热管的振动。
而换热管束的振动往往是换热管破坏的主要原因,使换热器过早报废。
引起换热管振动的因素很多,也较复杂。
当介质流量接近使换热管产生共振的临界流量时,将引起换热管束产生较大的振动。
另外换热器内部介质的局部湍流、涡流也会引起换热管振动。
换热管振动的位置较广,可以是某两个折流板间的所有换热管同时产生振动,或只有几排换热管产生振动。
也可能是在介质进口或出口端的某些换热管产生振动。
总之,换热管的振动可能发生在换热管束的任何一处或多处。
换热器的管束振动分析,就是要确定换热管的振动位置以及振动性质,了解引起换热管产生振动的原因,从而消除换热管的振动。
消除换热管振动的方法有很多,可以通过改变换热器的结构尺寸来改变换热管束的固有频率或流体的流动状态,从而消除换热管的振动。
或者在换热管束的振动部位增加局部支撑板,来约束换热管的振动。
换热器网络分析在一个工程系统中,往往不是对单一的某台换热器进行分析,常常是对由多个换热器组成的网络进行联合计算,其间还有一些其它设备〔例如:阀门、混合、别离等设备〕。
下列图为一个简单的换热器网络。
对一个换热器网络应进行综合的考虑并进行系统的分析。
在一个工程系统中,往往不是对单一的某台换热器进行分析,常常是对由多个换热器组成的网络进行联合计算,其间还有一些其它设备〔例如:阀门、混合、别离等设备〕。
下列图为一个简单的换热器网络。
对一个换热器网络应进行综合的考虑并进行系统的分析。
换热器强度计算确定了换热器的结构及尺寸以后,必须对换热器的所有受压元件进行强度计算。
因为管壳式换热器一般用于压力介质的工况,所以换热器的壳体大多为压力容器,必须按照压力容器的标准进行计算和设计,对于钢制的换热器,我国一般按照GB150<<钢制压力容器>>标准进行设计,或者美国ASME 标准进行设计。
对于其它一些受压元件,例如管板、折流板等,可以按照我国的GB151<<管壳式换热器>>或者美国TEMA标准进行设计。
对于其它材料的换热器,例如钛材、铜材等应按照相应的标准进行设计。
下面提供一氮气冷却器的受压元件强度计算,以供参考。
该换热器为U形管式换热器,壳体直径500mm,管程设计压力3.8MPa,壳程设计压力0.6MPa。
详细强度计算如下:1.壳程筒体强度计算:氮气冷却器(U形管式换热器)筒体计算计算条件筒体简图计算压力P c0.60MPa设计温度 t100.00︒ C内径D i500.00mm材料16MnR(热轧) ( 板材)试验温度许用应力[σ]170.00MPa设计温度许用应力[σ]t170.00MPa试验温度下屈服点σs345.00MPa钢板负偏差C10.00mm腐蚀裕量C2 1.00mm焊接接头系数φ0.85厚度及重量计算计算厚度δ == 1.04mm有效厚度δe =δn- C1- C2= 7.00mm名义厚度δn= 8.00mm 重量481.06Kg压力试验时应力校核压力试验类型液压试验试验压力值PT = 1.25P = 0.7500MPa压力试验允许通过的应力水平[σ]T[σ]T≤0.90 σs = 310.50MPa 试验压力下圆筒的应力σT = = 31.95MPa校核条件σT≤[σ]T校核结果合格压力及应力计算最大允许工作压力[P w]= = 3.99014MPa设计温度下计算应力σt = = 21.73MPa[σ]tφ144.50MPa 校核条件[σ]tφ≥σt结论合格2.前端管箱筒体强度计算氮气冷却器前端管箱筒体计算计算条件筒体简图计算压力P c 3.80MPa设计温度 t100.00︒ C内径D i500.00mm材料0Cr18Ni9 ( 板材)试验温度许用应力[σ]137.00MPa设计温度许用应力[σ]t137.00MPa试验温度下屈服点σs205.00MPa钢板负偏差C10.80mm腐蚀裕量C20.00mm焊接接头系数φ0.85厚度及重量计算计算厚度δ == 8.29mm有效厚度δe =δn- C1- C2= 11.20mm名义厚度δn= 12.00mm 重量75.76Kg压力试验时应力校核压力试验类型液压试验试验压力值PT = 1.25P = 4.7500MPa压力试验允许通过的应力水平[σ]T[σ]T≤0.90 σs = 184.50MPa 试验压力下圆筒的应力σT = = 127.53MPa校核条件σT≤[σ]T校核结果合格压力及应力计算最大允许工作压力[P w]= = 5.10266MPa设计温度下计算应力σt = = 86.72MPa[σ]tφ116.45MPa 校核条件[σ]tφ≥σt结论合格3.前端管箱封头强度计算氮气冷却器前端管箱封头计算计算条件椭圆封头简图计算压力P c 3.80MPa设计温度 t100.00︒ C内径D i500.00mm曲面高度h i125.00mm材料0Cr18Ni9 (板材)试验温度许用应力[σ]137.00MPa设计温度许用应力[σ]t137.00MPa钢板负偏差C10.80mm腐蚀裕量C20.00mm焊接接头系数φ 1.00厚度及重量计算形状系数K = = 1.0000计算厚度δ = = 6.98mm有效厚度δe =δn- C1- C2= 11.20mm最小厚度δmin= 0.75mm名义厚度δn= 12.00mm 结论满足最小厚度要求重量32.23Kg压力计算最大允许工作压力[P w]= = 6.06962MPa 4.后端壳程封头强度计算氮气冷却器后端壳程封头计算计算条件椭圆封头简图计算压力P c0.60MPa设计温度 t100.00︒ C内径D i500.00mm曲面高度h i125.00mm材料16MnR(热轧) (板材)试验温度许用应力[σ]170.00MPa设计温度许用应力[σ]t170.00MPa钢板负偏差C10.00mm腐蚀裕量C2 2.00mm焊接接头系数φ 1.00厚度及重量计算形状系数K = = 1.0000计算厚度δ = = 0.88mm有效厚度δe =δn- C1- C2= 6.00mm最小厚度δmin= 0.75mm名义厚度δn= 8.00mm 结论满足最小厚度要求重量19.61Kg压力计算最大允许工作压力[P w]= = 4.05567MPa 结论合格5.管板强度计算氮气冷却器管板计算设计条件0.60MPa 壳程设计压力3.80MPa 管程设计压力100.00︒ C 壳程设计温度100.00︒ C 管程设计温度8.00mm 壳程筒体壁厚12.00mm 管程筒体壁厚壳程筒体腐蚀裕量C1.00mm 管程筒体腐蚀裕量 C0.00mm500.00mm 换热器公称直径换热管使用场合一般场合a型管板与法兰或圆筒连接方式 ( a b c d型 )换热管与管板连接方式 ( 胀接或焊接 ) 焊接材料(名称及类型) 0Cr18Ni970.00mm名义厚度管0.40强度削弱系数0.40刚度削弱系数材料泊松比0.30210.00mm2隔板槽面积3.50mm换热管与管板胀接长度或焊脚高度l191000.00MPa 设计温度下管板材料弹性模量137.00MPa 设计温度下管板材料许用应力68.50MPa许用拉脱力壳程侧结构槽深h10.00mm板管程侧隔板槽深h2 4.00mm 壳程腐蚀裕量0.00mm管程腐蚀裕量0.00mm材料名称0Cr18Ni9换管子外径d19.00mm热管子壁厚2.00mm管 U型管根数n138根换热管中心距 S25.00mm 设计温度下换热管材料许用应力137.00MPa垫片材料软垫片压紧面形式1a或1b垫垫片外径D o565.00mm 片垫片内径D i515.00mm a型垫片厚度δg mm 垫片接触面宽度Ωmm垫片压紧力作用中心园直径D G547.11mm ( c型 )管板材料弹性模量0.00MPa( d型 )管板材料弹性模量0.00MPa ( b d 型 )管箱圆筒材料弹性模量0.00MPa ( b c型 )壳程圆筒材料弹性模量0.00MPa( c d型 )管板延长部分形成的凸缘宽度0.00mm( c型〕壳体法兰或凸缘厚度0.00mm( d型 )管箱法兰或凸缘厚度0.00mm参数计算管板布管区面积三角形排列正方形排列一根换热管管壁金属横截面积= 106.81mm2管板开孔前抗弯刚度b c d 型0.00N·mm 管板布管区当量直径436.43mma 型其他系数0.80系数按和查图得 : = 0.000000系数按和查图得 : = 0.000000a d 型= 0b c型0.00a ,c 型= 0b ,d 型0.00a 型= 0其他0.00旋转刚度无量刚系数0.00系数0.2696按和0.07130.0000管板厚度或管板应力计算a管板计算厚度取、大值61.345 mm型管板名义厚度66.000 mm管板中心处径向应力= 0MPa = 0MPa bcd布管区周边处径向应力= 0MPa 型= 0MPa边缘处径向应力= 0MPa = 0MPa 管板应力校核单位:MPa|σr|r=0=b工况|σr |r=Rt=c|σr|r=R=d|σr|r=0=型工况|σr|r=Rt=|σr|r=R=换热管轴向应力计算及校核: MPa (单位)计算工况计算公式计算结果校核只有壳程设计压力,管程设计压力=0 : |-1.59|≤合格只有管程设计压力,壳程设计压力=0 : =|6.29|≤合格壳程设计压力,管程设计压力同时作用: |4.69|≤合格换热管与管板连接拉脱力校核拉脱力q3.21 ≤[q]MPa校核合格重量64.89Kg6.管程设备法兰强度计算氮气冷却器管箱法兰强度计算设计条件简图设计压力 p 3.800 MPa计算压力 pc 3.800 MPa设计温度 t 100.0 ° C轴向外载荷 F 0.0 N外力矩 M 0.0 N.mm壳材料名称0Cr18Ni9体许用应力137.0 MPa法材料名称#许用 [s ]f 137.0 MPa兰应力 [s ]tf 137.0 MPa材料名称40Cr螺许用 [s ]b 212.0 MPa应力 [s ]tb 189.0 MPa栓公称直径 d B 24.0 mm螺栓根径 d 1 20.8 mm数量 n 24 个Di 500.0 Do 660.0垫结构尺寸Db 615.0 D外565.0 D内 515.0 δ0 16.0 mm Le 22.5 LA 31.5 h 35.0 δ1 26.0 材料类型软垫片N 25.0 m 2.00 y 11.0 压紧面形状1a,1b b 8.94 DG 547.1 片b0≤6.4mm b= b0 b0≤6.4mm DG= ( D外+D内 )/2b0 > 6.4mm b=2.53b0 > 6.4mm DG= D外 - 2b螺栓受力计算预紧状态下需要的最小螺栓载荷WaWa= πbDG y = 169119.0N操作状态下需要的最小螺栓载荷Wp Wp = Fp + F = 1127044.1N所需螺栓总截面积 Am Am = max (Ap ,Aa ) = 5963.2 mm2 实际使用螺栓总截面积 AbAb = = 8117.5mm2力矩计算操FD = 0.785pcN LD= L A+ 0.5δ1= 44.5 mm MD= FD LD= 33185876.0N.mm= 745750.0作FG = Fp= 233573.5 N LG= 0.5 ( Db - DG )= 33.9mm MG= FG LG= 7928625.5N.mmMp FT = F-FD= 147150.2 N LT=0.5(LA + d 1 +LG )= 45.7mm MT= FT LT= 6728066.0N.mm外压: Mp = FD (LD - LG )+FT(LT-LG ); 内压: Mp = MD+MG+MT Mp = 47842568.0N.mm预紧Ma W = 1492550.6 N LG = 33.9 mm Ma=W LG =50664460.0N.mm计算力矩 Mo= Mp 与中大者 Mo=50664460.0N.mm螺栓间距校核实际间距= 80.5mm最小间距56.0 (查GB150-98表9-3)mm最大间距158.4mm形状常数确定89.44 h/ho = 0.4 K = Do/DI = 1.3201.6由K查表9-5得T=1.789 Z =3.694 Y =7.145 U=7.851整体法兰查图9-3和图9-4 FI=0.85944 VI=0.314150.00961松式法兰查图9-5和图9-6 FL=0.00000 VL=0.000000.00000查图9-7 由得f = 1.06578 整体法兰 =572246.8松式法兰 = 0.00.2ψ=δf e+1=1.44 g = y /T ==0.81 1.59= 0.98剪应力校核计算值许用值结论预紧状态0.00MPa操作状态0.00MPa输入法兰厚度δf = 46.0 mm时, 法兰应力校核应力性质计算值许用值结论轴向应力158.57MPa=205.5 或=342.5( 按整体法兰设计的任意式法兰,取 )校核合格径向应力77.96MPa= 137.0校核合格切向应力54.14MPa= 137.0校核合格综合应力=118.27MPa= 137.0校核合格法兰校核结果校核合格7.接管开孔补强计算氮气冷却器开孔补强计算接管: a,φ219×16计算方法 : GB150-1998 等面积补强法, 单孔设计条件简图计算压力p c 3.8MPa设计温度100℃壳体型式圆形筒体壳体材料名称及类型0Cr18Ni9 板材壳体开孔处焊接接头系数φ0.85壳体内直径D i500mm 壳体开孔处名义厚度δn12mm壳体厚度负偏差 C10.8mm壳体腐蚀裕量C20mm壳体材料许用应力[σ]t137MPa接管实际外伸长度100mm接管实际内伸长度0mm 接管材料0Cr18Ni9接管焊接接头系数1名称及类型管材接管腐蚀裕量0mm 补强圈材料名称补强圈外径mm补强圈厚度mm接管厚度负偏差C1t2mm 补强圈厚度负偏差C1rmm 接管材料许用应力[σ]t137MPa 补强圈许用应力[σ]t MPa开孔补强计算壳体计算厚度δ8.293mm 接管计算厚度δt 2.63mm 补强圈强度削弱系数f rr0接管材料强度削弱系数f r1开孔直径d191mm 补强区有效宽度B382mm 接管有效外伸长度h155.28mm 接管有效内伸长度h20mm 开孔削弱所需的补强面积A1584mm2壳体多余金属面积A1555.2 mm2接管多余金属面积A21257mm2补强区内的焊缝面积A364mm2A1+A2+A3=1876 mm2 ,大于A,不需另加补强。