超重力技术是利用超重力原理创建起来的一种新型的强化传递过程和多
超重力技术的研究及应用

超重力技术的研究及应用郭浩;牛杰【摘要】超重力技术是一种过程强化技术,通过离心力实现传质过程的强化.超重力技术广泛应用于吸收、蒸馏、汽提、萃取等分离过程,在化工、环保等领域也有广阔的应用前景.论述了超重力技术的基本原理及特点,重点介绍了超重力技术在化工尾气处理、精馏、纳米材料、催化剂制备及消除粉尘等方面的应用,并对超重力技术的研究方向和应用前景做了展望.【期刊名称】《化工装备技术》【年(卷),期】2016(037)005【总页数】4页(P61-64)【关键词】超重力;过程强化;吸收;蒸馏;传质过程【作者】郭浩;牛杰【作者单位】中国石化长城能源化工(宁夏)有限公司;中国石化长城能源化工(宁夏)有限公司【正文语种】中文【中图分类】TQ051.8超重力HIGEE(high gravity)技术是一种过程强化的新技术,主要是通过强大的离心力——超重力,使气-液流速及填料的比表面积大大提高,液体在高湍动、高分散、强混合及界面更新急速的条件下与气体以极大的相对速度在弯曲流道中逆向接触,从而强化传质过程。
超重力技术广泛应用于吸收、蒸馏、汽提、萃取等分离过程[1]。
与传统技术相比,超重力技术在实际应用中主要有以下特点[1-5]:(1)传递效率显著提高,传递系数可提高1~3个数量级,极大地减小了设备的体积,降低了设备投资。
(2)物料在设备内的停留时间极短(0.1~1.0 s),适用于某些特殊的反应及处理过程。
(3)易于操作及开停车,维护检修方便。
(4)填料不易堵塞。
(5)气相压降小,动力能耗小,适用于大气量、高气速的场合。
超重力设备结构如图1所示,主要由外壳、转轴、转子、填料及液体分布器等组成。
该设备核心部分是转子,其主要作用是装载和固定填料,在动力驱动下带动填料旋转,以实现良好的气液接触。
在压力作用下,气相由进气口进入外腔,在转轴外缘处进入填料,最后从排气口排出;液体由喷水管进入,经喷头洒在转轴内缘,在离心力的作用下进入转轴外缘。
超重力反应强化技术及工业应用

超重力反应强化技术及工业应用超重力反应强化技术及其工业应用超重力反应强化技术是一种通过增加反应体系中的离心力,从而提高反应速率和效率的技术。
它在工业领域有着广泛的应用,可以用于合成新材料、催化剂的制备、化学反应的优化等方面。
本文将介绍超重力反应强化技术的原理和工业应用,并探讨其在工业生产中的优势和前景。
一、超重力反应强化技术的原理超重力反应强化技术是利用离心力对反应体系进行强化,从而促进反应的进行。
离心力的增加可以通过旋转容器或采用离心机实现。
当反应体系受到离心力的作用时,分子之间的相互作用力和传质速率都会增强,从而加快反应速率。
此外,超重力还可以改变反应体系的物理和化学性质,例如改变溶剂的性质、增加物质的溶解度等,从而进一步优化反应条件。
二、超重力反应强化技术的工业应用1. 新材料合成超重力反应强化技术可以用于合成具有特殊性质的材料,例如高分子材料、纳米材料等。
在超重力条件下,反应分子之间的相互作用力增强,能够促进聚合反应的进行,从而得到高分子材料。
此外,超重力还可以改变材料的晶体结构和形貌,使其具有更好的性能和应用价值。
2. 催化剂的制备超重力反应强化技术可以用于催化剂的制备过程中。
催化剂的性能往往与其结构和形貌密切相关,而超重力可以改变反应体系的物理和化学性质,从而影响催化剂的形成过程。
通过超重力反应强化技术,可以调控催化剂的晶体结构和形貌,提高其催化活性和选择性,从而实现高效催化反应。
3. 化学反应的优化超重力反应强化技术可以用于化学反应的优化。
在超重力条件下,反应体系的传质速率增加,反应物与催化剂之间的接触面积增大,从而加快反应速率。
此外,超重力还可以改变反应体系的物理和化学性质,例如改变溶剂的性质、增加物质的溶解度等,从而优化反应条件,提高反应的选择性和产率。
三、超重力反应强化技术的优势和前景超重力反应强化技术具有以下优势:1. 提高反应速率和效率:通过增加离心力,可以加快反应速率和提高反应效率,从而节省时间和成本。
5-超重力技术及工业化应用
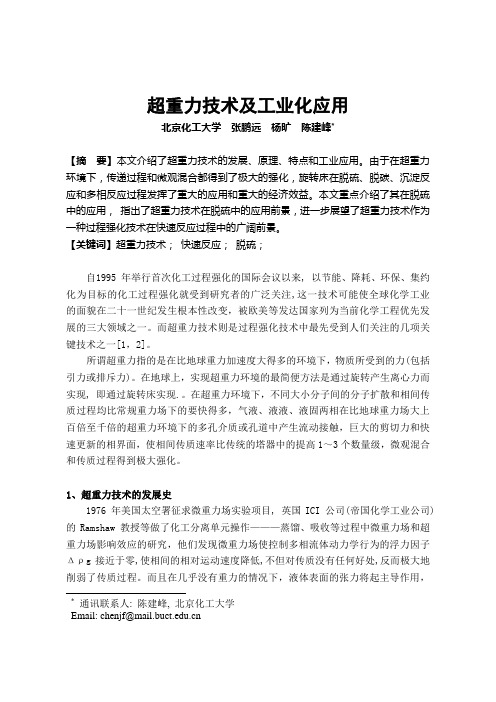
超重力技术及工业化应用北京化工大学张鹏远杨旷陈建峰*【摘要】本文介绍了超重力技术的发展、原理、特点和工业应用。
由于在超重力环境下,传递过程和微观混合都得到了极大的强化,旋转床在脱硫、脱碳、沉淀反应和多相反应过程发挥了重大的应用和重大的经济效益。
本文重点介绍了其在脱硫中的应用,指出了超重力技术在脱硫中的应用前景,进一步展望了超重力技术作为一种过程强化技术在快速反应过程中的广阔前景。
【关键词】超重力技术;快速反应;脱硫;自1995 年举行首次化工过程强化的国际会议以来, 以节能、降耗、环保、集约化为目标的化工过程强化就受到研究者的广泛关注,这一技术可能使全球化学工业的面貌在二十一世纪发生根本性改变,被欧美等发达国家列为当前化学工程优先发展的三大领域之一。
而超重力技术则是过程强化技术中最先受到人们关注的几项关键技术之一[1,2]。
所谓超重力指的是在比地球重力加速度大得多的环境下,物质所受到的力(包括引力或排斥力)。
在地球上,实现超重力环境的最简便方法是通过旋转产生离心力而实现, 即通过旋转床实现.。
在超重力环境下,不同大小分子间的分子扩散和相间传质过程均比常规重力场下的要快得多,气液、液液、液固两相在比地球重力场大上百倍至千倍的超重力环境下的多孔介质或孔道中产生流动接触,巨大的剪切力和快速更新的相界面,使相间传质速率比传统的塔器中的提高1~3个数量级,微观混合和传质过程得到极大强化。
1、超重力技术的发展史1976 年美国太空署征求微重力场实验项目, 英国ICI 公司(帝国化学工业公司) 的Ramshaw 教授等做了化工分离单元操作———蒸馏、吸收等过程中微重力场和超重力场影响效应的研究,他们发现微重力场使控制多相流体动力学行为的浮力因子Δρg接近于零,使相间的相对运动速度降低,不但对传质没有任何好处,反而极大地削弱了传质过程。
而且在几乎没有重力的情况下,液体表面的张力将起主导作用,*通讯联系人: 陈建峰, 北京化工大学Email: chenjf@液体凝聚在一起,组分基本上得不到分离。
超重力床——精选推荐
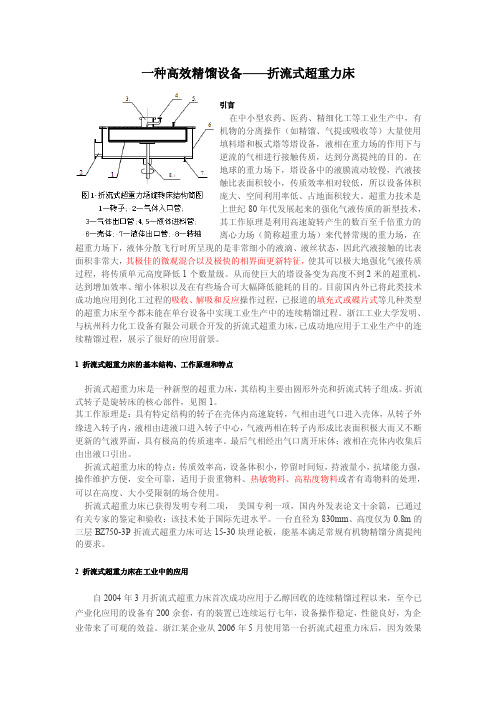
一种高效精馏设备——折流式超重力床引言在中小型农药、医药、精细化工等工业生产中,有机物的分离操作(如精馏、气提或吸收等)大量使用填料塔和板式塔等塔设备,液相在重力场的作用下与逆流的气相进行接触传质,达到分离提纯的目的。
在地球的重力场下,塔设备中的液膜流动较慢,汽液接触比表面积较小,传质效率相对较低,所以设备体积庞大、空间利用率低、占地面积较大。
超重力技术是上世纪80年代发展起来的强化气液传质的新型技术,其工作原理是利用高速旋转产生的数百至千倍重力的离心力场(简称超重力场)来代替常规的重力场,在超重力场下,液体分散飞行时所呈现的是非常细小的液滴、液丝状态,因此汽液接触的比表面积非常大,其极佳的微观混合以及极快的相界面更新特征,使其可以极大地强化气液传质过程,将传质单元高度降低1个数量级。
从而使巨大的塔设备变为高度不到2米的超重机,达到增加效率、缩小体积以及在有些场合可大幅降低能耗的目的。
目前国内外已将此类技术成功地应用到化工过程的吸收、解吸和反应操作过程,已报道的填充式或碟片式等几种类型的超重力床至今都未能在单台设备中实现工业生产中的连续精馏过程。
浙江工业大学发明、与杭州科力化工设备有限公司联合开发的折流式超重力床,已成功地应用于工业生产中的连续精馏过程,展示了很好的应用前景。
1 折流式超重力床的基本结构、工作原理和特点折流式超重力床是一种新型的超重力床,其结构主要由圆形外壳和折流式转子组成。
折流式转子是旋转床的核心部件,见图1。
其工作原理是:具有特定结构的转子在壳体内高速旋转,气相由进气口进入壳体,从转子外缘进入转子内,液相由进液口进入转子中心,气液两相在转子内形成比表面积极大而又不断更新的气液界面,具有极高的传质速率。
最后气相经出气口离开床体;液相在壳体内收集后由出液口引出。
折流式超重力床的特点:传质效率高,设备体积小,停留时间短,持液量小,抗堵能力强,操作维护方便,安全可靠,适用于贵重物料、热敏物料、高粘度物料或者有毒物料的处理,可以在高度、大小受限制的场合使用。
什么是化工本质安全?本质安全详解
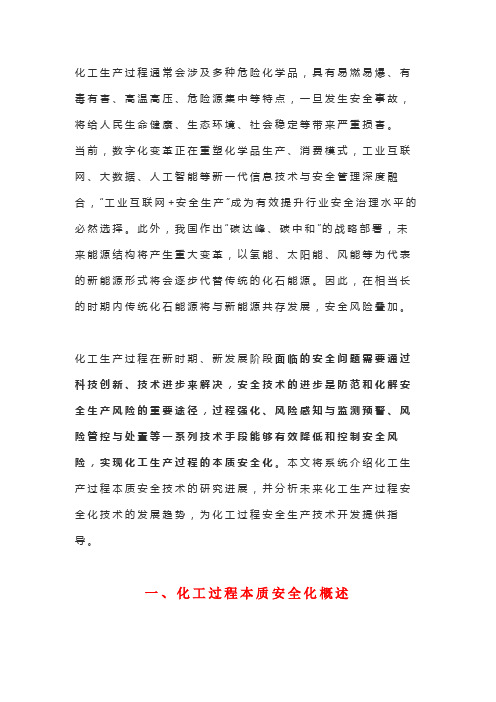
化工生产过程通常会涉及多种危险化学品,具有易燃易爆、有毒有害、高温高压、危险源集中等特点,一旦发生安全事故,将给人民生命健康、生态环境、社会稳定等带来严重损害。
当前,数字化变革正在重塑化学品生产、消费模式,工业互联网、大数据、人工智能等新一代信息技术与安全管理深度融合,“工业互联网+安全生产”成为有效提升行业安全治理水平的必然选择。
此外,我国作出“碳达峰、碳中和”的战略部署,未来能源结构将产生重大变革,以氢能、太阳能、风能等为代表的新能源形式将会逐步代替传统的化石能源。
因此,在相当长的时期内传统化石能源将与新能源共存发展,安全风险叠加。
化工生产过程在新时期、新发展阶段面临的安全问题需要通过科技创新、技术进步来解决,安全技术的进步是防范和化解安全生产风险的重要途径,过程强化、风险感知与监测预警、风险管控与处置等一系列技术手段能够有效降低和控制安全风险,实现化工生产过程的本质安全化。
本文将系统介绍化工生产过程本质安全技术的研究进展,并分析未来化工生产过程安全化技术的发展趋势,为化工过程安全生产技术开发提供指导。
一、化工过程本质安全化概述本质安全(i n h e r en t sa f e t y)概念最早由英国的T re vo r K l e tz 于1976年提出,其理念是从工艺源头上永久地消除风险,而不是单独靠控制系统、报警系统、联锁系统的使用来减小事故发生概率和减轻事故后果的严重性。
本质安全是绝对安全的理想状态,生产运行上很难达到,实际中需要通过本质安全化(i n h e r e n t l y s af e r)的一系列技术措施降低过程风险,使化工过程本质上更安全。
化工过程全生命周期的本质安全如图1所示,最小化、替代、缓和、简化这4个本质安全化策略适用于研发、设计、建设、操作、变更和维护等化工过程的整个生命周期。
工艺过程的本质安全化与被动型、主动型和程序型安全防护措施一起构成了化工过程的保护层,其中本质安全化工艺技术在所有保护层中处于最核心的部分,对安全风险控制起到决定性作用。
超重力分离技术解读

超重力气-固接触技术的突出特点主要表现在以下3个方面: a. 在超重力流化床中,由于重力场强度和流化速度均可调 节,因此可将流化速度控制在鼓泡速度之下操作,从而获得 良好的流化质量。
b. 在超重力条件下,由于颗粒有效重力增加,因而流化时气 固之间的相互作用(相对速度)大大增强,从而使其传质传热 速率远高于传统流化床。
动、强混合以及界面急速更新的情况下与气体以极大的相 对速度在弯曲孔道中逆向接触,极大地强化了传质过程。超 重力技术被认为是强化传递和多相反应过程的一项突破性 技术,被誉为“化学工业的晶体管”和“跨世纪的技术”
气相经气体进口管由切向引入转子外腔,在气体压 力的作用下由转子外缘处进入填料。液体由液体进 口管引入转子内腔,经喷头淋洒在转子内缘上。进 入转子的液体受到转子内填料的作用,周向速度增 加,所产生的离心力将其推向转子外缘。在此过程 中,液体被填料分散、破碎形成极大的、不断更新 的表面积,曲折的流道加剧了液体表面的更新。这 样,在转子内部形成了极好的传质与反应条件。液 体被转子抛到外壳汇集后经液体出口管离开超重机。 气体自转子中心离开转子,由气体出口管引出,完成 传质与反应过程。
离心力场(超重力场) 被用于相间分离,无论在日常生活还是 在工业应用上,都已有相当长的历史。但为一项特定的手段 用于传质过程的强化,引起工业界的重视是70 年代末出现的 “Higee”, 这是英国帝国化学公司的ColinRamshaw 教授领 导的新科学小组提出的专利技术。它的诞生最初是由设想
用精馏分离去应征美国太空署关于微重力条件下太空实验 项目引起的。70 年代末至80 年代初,英国帝国化学工业公司 ( ICI) 连续提出被称之为“Higee”的多项专利。利旋转填 料床中产生的强大离心力———超重力,使气、液的流速及 填料的比表面积大大提高而不液泛。液体在高分散、高湍
超重力技术应用在化工工业中的研究

超重力技术应用在化工工业中的研究
随着科技的不断进步和发展,超重力技术也逐渐被应用于化工工业中。
超重力
技术是利用高速旋转加速度产生的高重力场对物质进行处理的一种新型技术,具有诸如快速反应速度、高效和节能等优点,在化学合成、分离、提纯和生产中得到了广泛的应用。
超重力技术的应用在化工工业中重新定义了分子、离子、元素和原子之间的相
互作用,从而有望实现更加高效的化学反应。
在超重力场中,反应物分子与亲、疏水性介质之间的相互作用会被大大增强,可以加快化学反应的速度,提高反应物之间的亲和性。
此外,由于物质在超重力场中的分子自由路径因飞行时间缩短而减小,因此反应性质也会因此得到改善。
这些特性使得超重力技术成为化工生产中一个不可或缺的工具。
超重力技术成功应用在化工生产中,不仅可以提高化学品的纯度和成品率,还
有助于生产更高性能的材料。
例如在高分子生产方面,超重力技术可以改善聚合反应条件,促进高分子的产生,从而提高聚合产物的质量和产率,同时还能使聚合物的分子量分布变窄,加快聚合反应速率,提高聚合物的分子量。
此外,超重力技术还可以用于分离和提纯化合物。
在超重力场中,由于分子间
相互作用力增强,有利于分子间相互转移,从而加快分离效率。
超重力技术因此被用于纯化生物大分子、萃取药物和分离油品等场合,使得处理速度提高,同时节约了时间和成本。
总之,超重力技术在化工工业中的应用是一个前景广阔的领域,可以为化学反应、材料制备、分离和提纯提供一种新的工具。
虽然目前仍存在使用上的限制,但这种技术的前景依旧非常令人期待。
超重力精馏技术

填料式内部结构图
填料中逆流接触进行传质传热。
3
超重力精馏设备
气液通量可得到极大 提高 , 气体、液体通量可 相应增大到很大而不产生
持液量比较小 , 液体在转
子内的停留时间很短 , 适合处
理一些热敏性、昂贵或者有毒 的物料。
液泛。
填料式 特点
1
在相同的操作条件下 , 与常用的板式塔、填料 塔相比 , 传质单元高度可 降低1~2个数量级,体积传 质系数可提高 1~3 个数量 级 , 设备的体积可缩小 10 倍以上。
存在, 基本的气液传质单元是液膜与液滴 , 这也
是超重力精馏过程与传统精馏过程的本质区别。
与传统 精馏的 区别
3
超重力精馏设备
填料式
它是由转子、液体分布器和外壳组成的。机器
的核心部分是转子, 其主要作用是固定和带动填料 旋转, 实现良好的流体接触和微观混合。精馏过程 中 , 流体在超重力精馏设备中的流动形式为 : 蒸汽 从超重力精馏设备气体入口进入设备的外腔 , 在压 力的作用下自填料的外侧穿过旋转的填料进入设备 的内腔 , 然后从位于设备顶部的气体出口流出 ; 液 体由位于中央的一个静止分布器射出后 , 进入旋转 填料的内侧, 受离心力与摩擦力的双重作用向外甩 出填料 , 经外壳收集后 , 从液体出口排出 ; 气液在
质速率相比较传统塔器设备提高 1~3 个数量级,极大得强化了微观混合和传质过程。
2
超重力精馏原理
2
超重力精馏原理
从本质上讲 , 超重力精馏过程与传统精馏过
程不同的是 : 在传统精馏过程中最基本的气液传
质单元是气泡 ; 而在超重力精馏过程中 , 填料内 只有液膜、液滴与流满填料空间的气相 , 无气泡
- 1、下载文档前请自行甄别文档内容的完整性,平台不提供额外的编辑、内容补充、找答案等附加服务。
- 2、"仅部分预览"的文档,不可在线预览部分如存在完整性等问题,可反馈申请退款(可完整预览的文档不适用该条件!)。
- 3、如文档侵犯您的权益,请联系客服反馈,我们会尽快为您处理(人工客服工作时间:9:00-18:30)。
超重机(旋转填料床)
它是把填料固定在特定的模具里, 用轴承与上部的电机相连结,利用 电机带动, 以达到相对较高的旋转 速度, 从而产生一个较高的离心加 速度
设备结构及原理
❖ 逆流型旋转填料床 ❖ 错流型旋转填料床
逆流型旋转填料床
错流型旋转填料床
超重力技术特点
❖ (1) 极大地强化了传递过程(传质单元高度 仅1~3 cm)
超重力技术
❖ 超重力技术是利用超重力原理创建
起来的一种新型的强化传递过程和多相 反应过程的技术。
超重力指的是比地球重力加速 度大得多的环境下,物质所受的力 (包括引力和斥力)。
如何实现超重力
通过旋转产生离心力而实现
(即是通过离心力场的作用而达到模拟超重力环境的目的)
超重力技术的基本原理
在重力加速度g →0时,两相接触过程的动力因 素即浮力因子Δρg →0 ,两相间不会因密度差 而产生相间流动,此时分子间力(如表面张力) 将会起主要作用。液体团聚至表面积最小的状 态而不得伸展,相间传递失去两相充分接触的 前提条件,使相间传递作用越来越弱,分离无法 进行。反之, g 越大,Δρg 越大,流体相对速度也 越大,巨大的切应力不仅克服了表面张力,而且 可使液体在切应力的作用下被拉伸成膜成丝成 滴,从而使得相间接触面积增大,导致相间传递 过程极大加强。超重力技术正是通过高速旋转, 利用离心力来增大g ,从而增大Δρg 达到强化 相间传递过程的效果
超重力技术
超重力技术可以加快氧的传递,试验表明 拟塑性流体在超重机中的氧传递速率较 鼓泡搅拌釜中快6~ 20 倍。
在国外的应用
❖ a. 精馏、 ❖ b. 吸收(天燃气干燥、脱碳、脱硫) 、 ❖ c. 解吸(从受污染的地下水中吹出芳烃) ❖ d. 化学热泵(吸收解吸) 、 ❖ e. 旋转电化学反应器及燃料电池(快速去除气泡, 降
合成纳米材料时,微观混合与宏观混合 是同时进行的,当微观混合占主导地位 时,反应中的两相体系能充分混合,生 成的产物粒度较小。超重力技术则极大 地强化了微观混合过程,使产物粒度大 大减低。
超重力反应结晶法可以制备出立方形、链锁
状、纺锤形、片状等不同形态的纳米CaCO3 。 在不添加任何晶体生长抑制剂的情况下,可以 制备出平均粒度为15~ 40 nm、分布很窄的 纳米CaCO3 颗粒;在添加特定晶习控制条件 下,可以制备出轴比大于10 、单个颗粒平均粒 度小于10 nm、分布均匀的链锁状CaCO3 。
这项技术中尚有未充分揭示的现象和值得深入 研究的理论, 还需要大家进一步去探索。
造成污染的黑液变为肥水是造纸厂减少污染 的重要方法之一) 。
粉尘是重要的污染源之一,传统使用工业 除尘器在除效率和处理量方面,随着工业 除尘标准的提高,已不能满足环境保护的 要求。
传统技术
传统的生物氧化反应一般在发酵罐中进 行。由于物料的粘度不断增加,生化反应 的速率受氧的传递控制,表观速率很低。 为了达到一定的生产能力,发酵罐的体积 较大。
低超电压) ❖ f . 旋转盘换热器、蒸发器、 ❖ g. 旋转聚合反应器 ❖ h. 选择性吸收分离天然气中的H2S 与CO2 ❖ i. 聚合物脱除挥发物(聚苯乙烯脱单体)
结束语
由于超重力技术的广泛适用性以及具有传统设 备所不具有的更小、更精、更安全的特点、更 能适应环境和对环境友好的特殊品质, 它有可 能成为化学工程与科学发展的新阶段。
❖ (2) 极大地缩小了设备尺寸与重量(不仅降 低了投资,也对环境有了一定改善)
❖ (3) 物料在设备内的停留时间极短(10~ 100 ms)
❖ (4) 易于操作, 由启动到进入定态运转时 间极短(1 min 内)
❖ (5) 快速而均匀的微观混合
在国内应用
(1) 制备纳米材料 (2) 油田注水脱氧 (3) 吸收气体强化
传统技术
❖ 一种是采用真空解吸法利用2个真空塔。 ❖ 另一种是只用1 个真空塔,同时在真空塔
出口水中加入化学药剂。
超重力技术
❖ 以氨或碳铵溶液作吸收剂,用超重力技术脱除 硫酸厂尾气中SO2 是另1 项国家科委“八五”
攻关项目。吸收后得到的亚硫酸铵产品可用 作化肥(适用于缺硫的土壤) 、药厂的原料和 造纸代替烧碱制草浆的原料(亚铵代替烧碱使