jbt9172齿轮渗氮氮碳共渗工艺及质量控制
重载齿轮渗碳质量检验标准
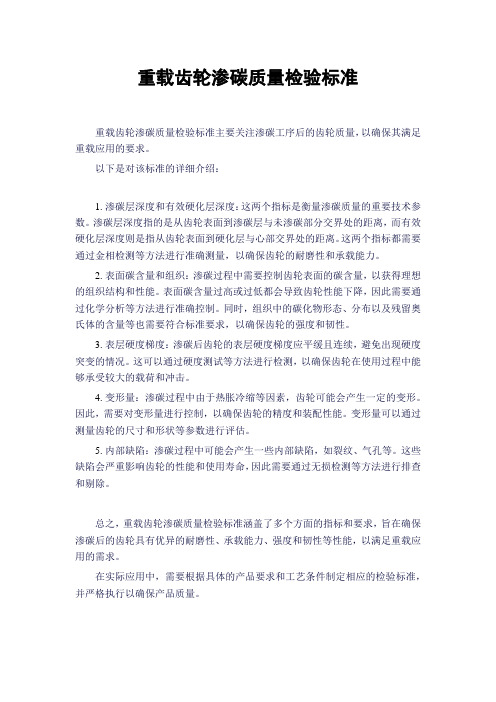
重载齿轮渗碳质量检验标准重载齿轮渗碳质量检验标准主要关注渗碳工序后的齿轮质量,以确保其满足重载应用的要求。
以下是对该标准的详细介绍:1.渗碳层深度和有效硬化层深度:这两个指标是衡量渗碳质量的重要技术参数。
渗碳层深度指的是从齿轮表面到渗碳层与未渗碳部分交界处的距离,而有效硬化层深度则是指从齿轮表面到硬化层与心部交界处的距离。
这两个指标都需要通过金相检测等方法进行准确测量,以确保齿轮的耐磨性和承载能力。
2.表面碳含量和组织:渗碳过程中需要控制齿轮表面的碳含量,以获得理想的组织结构和性能。
表面碳含量过高或过低都会导致齿轮性能下降,因此需要通过化学分析等方法进行准确控制。
同时,组织中的碳化物形态、分布以及残留奥氏体的含量等也需要符合标准要求,以确保齿轮的强度和韧性。
3.表层硬度梯度:渗碳后齿轮的表层硬度梯度应平缓且连续,避免出现硬度突变的情况。
这可以通过硬度测试等方法进行检测,以确保齿轮在使用过程中能够承受较大的载荷和冲击。
4.变形量:渗碳过程中由于热胀冷缩等因素,齿轮可能会产生一定的变形。
因此,需要对变形量进行控制,以确保齿轮的精度和装配性能。
变形量可以通过测量齿轮的尺寸和形状等参数进行评估。
5.内部缺陷:渗碳过程中可能会产生一些内部缺陷,如裂纹、气孔等。
这些缺陷会严重影响齿轮的性能和使用寿命,因此需要通过无损检测等方法进行排查和剔除。
总之,重载齿轮渗碳质量检验标准涵盖了多个方面的指标和要求,旨在确保渗碳后的齿轮具有优异的耐磨性、承载能力、强度和韧性等性能,以满足重载应用的需求。
在实际应用中,需要根据具体的产品要求和工艺条件制定相应的检验标准,并严格执行以确保产品质量。
渗氮—氮碳共渗工件的表面硬度形成机理
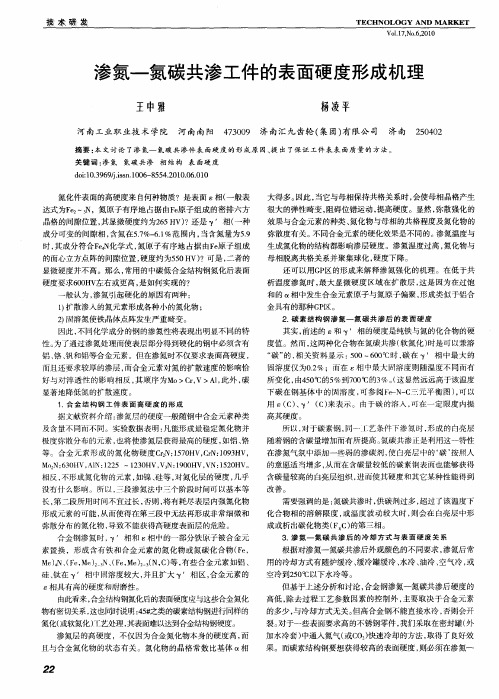
而且还要求较厚 的渗层 , 而合金元素对氮的扩散速度的影响恰
好与对淬透性的影响相反 , 其顺序 为M >C , o rV>A , 1此外 , 碳 显著地降低氮 的扩散速度。
1 合 金 结构 钢 工 件 表面 高 硬 度 的 形成 .
下碳在 钢基 体中 的同溶度 , 可参 阅F — — 三元平衡 图 )可 以 eN C ,
用 s( ) - ( ) 表 示 。 由 于碳 的溶 入 , 在 一 定 限 度 内提 C 、y C 来 可
据文献资料介绍 : 渗氮层 的硬度一般 随钢 中合金元素种类 及含量不同而不 同。实验数据表明 : 凡能形成最稳定氮化物并 极度弥散分布 的元素 , 也将使渗氮层获得最高 的硬度 , 如铝 、 铬 等。合金 元素形成的氮化 物硬度C2 :5 0 V,r 1 9HV r 17 H CN:0 3 , N
其实 , 前述的 s和
相的硬度是纯铁与氮的化合物的硬 相 中最大 的
度值 。然而 , 这两种化合物在氮碳共渗( 软氮化 ) 时是可以兼溶 “ ” , 碳 的 相关资料显示 : 0 5 0~60C , 0  ̄时 碳在 固溶度仅为02 .%;而在 s相中最大同溶度则 随温度不同而有
所变化 , 5  ̄ 由4 0C的5  ̄7 0 的3 。这 显然 远 远 高于 该 温度 %; 0 ℃ l J % (
技 术 研 发
T C N L G N AR E E H o 0 YA DM K T
渗氮一 氮碳共渗 工件 的表面硬度形成机理
王中雅
河南 工业职业技 术 学院 河南 南阳
杨凌平
4 30 济南汇 九齿轮 ( 团) 限公 司 济南 2 00 7 09 集 有 5 42
一
Байду номын сангаас
齿轮气体渗碳热处理工艺

Fuwa广东富华重工制造有限公司Guangdong FuWa Heavy Industries Co.,Ltd.我公司齿轮气体渗碳热处理工艺及其质量控制主要内容与使用范围本标准结合中国齿轮标准化技术委员会、机械工业部郑州机械研究所起草的《齿轮气体渗碳热处理工艺及其质量控制》,根据我公司齿轮材料及性能所编写的基本符合产品要求的一般规定。
本标准适用于钢制齿轮的气体渗碳、淬火和回火处理。
一、标准篇1、GB1818金属表面洛氏硬度试验方法2、GB1979结构钢低倍组织缺陷评级图3、GB3077合金结构钢技术条件4、GB5216保证淬透性结构钢技术条件5、GB6394金属平均晶粒度测定方法6、GB8539齿轮材料及热处理质量检验的一般规定7、GB9450钢件渗碳淬火有效硬化层深度的测定与校核8、GB9452热处理炉有效加热区测定方法9、GB10561钢中非金属夹杂物显微组织评定法10、GB/T230金属洛氏硬度试验方法11、GB/T13299钢的显微组织评定法12、GB/T225-88钢的末端淬透性试验方法13、ZB G51 108钢件在吸热式气氛中的热处理14、ZB J36 012 钢件在吸热式气氛中的热处理15、ZB T04 001汽车渗碳齿轮金相检验页14 共页1 第Fuwa广东富华重工制造有限公司Guangdong FuWa Heavy Industries Co.,Ltd.二、材料篇1、适合我公司齿轮产品的材料(见表一)(遵循我国齿轮行业车辆齿轮钢采购标准CGMA001-2004钢号淬透能力)表一2、齿轮材料的冶金质量1)化学成分合金结构钢化学成分应符合GB/T3077-88《合金结构钢技术条件》中的有关规定,保证淬透性结构钢化学成分应符合GB/5216-85《保证淬透性结构钢条件》中的有关规定。
检验标准执行GB223。
2)纯净度页14 共页2 第Fuwa广东富华重工制造有限公司Guangdong FuWa Heavy Industries Co.,Ltd.-6-6 ,含硫量<0.015%10,当有特殊要求时,10按双方,含氢量为≤5.0×钢材氧含量≤20.0×协议规定。
齿轮渗氮、氮碳共渗工艺及质量控制

齿轮渗氮、氮碳共渗工艺及质量控制
齿轮渗氮是一种提高齿轮表面硬度和耐磨性的表面处理方法,可以通过在齿轮表面注入氮气,使其在表面形成氮化层。
齿轮渗氮的主要工艺包括气体渗氮和盐浴渗氮两种方法。
1. 气体渗氮工艺:气体渗氮是将齿轮置于渗氮炉中,通过加热至高温状态,然后通过氨气或氮气等气体进行渗透处理,使氮原子渗入齿轮表面形成氮化层。
这种工艺具有操作简单、渗透深度可控、成本较低等优点。
2. 盐浴渗氮工艺:盐浴渗氮是将齿轮浸入温度较高的盐浴溶液中进行处理,使盐浴溶液中的氮原子渗透到齿轮表面形成氮化层。
这种工艺渗透速度较快,渗透深度大,但操作复杂,成本较高。
质量控制是齿轮渗氮过程中非常重要的环节,主要包括以下几个方面:
1. 温度控制:温度是齿轮渗氮过程中的重要参数,需要控制在合适的范围内,以保证渗透效果和避免过热损坏齿轮。
2. 渗氮时间控制:渗氮时间是影响氮化层深度和均匀性的重要因素,需要根据齿轮的具体要求和设计要求来确定。
3. 渗氮介质控制:选择合适的渗氮介质对于渗透效果和氮化层质量都有重要影
响,需要根据具体情况进行选择。
4. 清洗和处理后的质量检验:渗氮后需要对齿轮进行清洗和处理,以去除表面的残留物,然后进行质量检验,包括硬度测试、金相分析、氮化层厚度测量等。
通过合理的工艺选择和质量控制,可以确保齿轮渗氮的效果和质量,提高齿轮的使用寿命和性能。
齿轮标准大全资料.doc

齿轮标准大全(精度部分)1 、 GB/T 2821-92齿轮几何要素代号(已作废)(注:已有GB/T 2821-2003 在标准参考资料<十二> 中)2 、 GB1356-88 渐开线圆柱齿轮基本齿廓(已作废)(注:已有GB/T 1356-2001 在标准汇编中)3 、 GB1357-87 渐开线圆柱齿轮模数(已作废)(注:已有“GB/T 1357-2008 通用机械和重型机械用圆柱齿轮模数”在标准汇编第九部分中)4 、 GB1356-88 渐开线圆柱齿轮基本齿廓、GB1357-87 渐开线圆柱齿轮模数编制说明5 、 GB10095-88 渐开线圆柱齿轮精度(已作废)6 、 GB10095-88 渐开线圆柱齿轮精度编制说明(注:已有GB/T 10095.1.2-2001 在标准参考资料<九>中)7 、 GB10096-88 齿条精度8 、 GB10096-88 齿条精度编制说明9 、 GB6443-86 渐开线圆柱齿轮图样上应注明的尺寸数据10 、 GB6443-86 渐开线圆柱齿轮图样上应注明的尺寸数据编制说明11 、 GB/T13924-94 渐开线圆柱齿轮精度检验规范12 、 GB/T13924-94 渐开线圆柱齿轮精度检验规范编制说明(注:已有GB/T 13924-2008渐开线圆柱齿轮精度检验细则在标准参考资料<九>中)13 、 JB/T53441-94 渐开线圆柱齿轮产品质量分等通则(注:标准出版社出版标准汇编中没有)14 、 JB/T53441-94 渐开线圆柱齿轮产品质量分等通则编制说明(蜗轮蜗杆部分)1 、GB10085-88圆柱蜗杆传动基本参数2 、GB10085-88圆柱蜗杆传动基本参数编制说明3 、GB10086-88圆柱蜗杆传动、蜗轮术语及代号4 、GB10087-88圆柱蜗杆基本齿廓5 、GB10087-88圆柱蜗杆基准齿形编制说明6 、GB10088-88圆柱蜗杆模数和直径7 、GB10088-88圆柱蜗杆模数和直径编制说明8 、GB10089-88圆柱蜗杆、蜗轮精度9 、GB10089-88圆柱蜗杆、蜗轮精度编制说明10 、 GB/T12760-91圆柱蜗杆、蜗轮图样上应注明的尺寸数据(圆弧齿轮部分)1 、 GB 1840-89圆弧圆柱齿轮模数2 、 GB 1840-89圆弧圆柱齿轮模数修订说明3 、 GB12759=91双圆弧圆柱齿轮基本齿廓4 、 GB12759=91双圆弧圆柱齿轮基本齿廓编制说明5 、 GB/T13799-92双圆弧圆柱齿轮承载能力计算方法6 、、 GB/T13799-92双圆弧圆柱齿轮承载能力计算方法编制说明7 、 GB/T14348.1-93双圆弧齿轮滚刀型式和尺寸(注:标准出版社出版标准汇编中没有)8 、 GB/T14348.2-93双圆弧齿轮滚刀技术条件(注:标准出版社出版标准汇编中没有)9 、 GB/T14348.1-93双圆弧齿轮滚刀型式和尺寸、GB/T14348.2-93双圆弧齿轮滚刀技术条件编制说明10 、 GB/T 15752-1995圆弧圆柱齿轮基本术语11 、 GB/T 15752-1995圆弧圆柱齿轮基本术语编制说明12 、 GB/T 15753-1995圆弧圆柱齿轮精度13 、 GB/T 15753-1995圆弧圆柱齿轮精度编制说明(锥齿轮部分)1 、 GB10062-88锥齿轮承载能力计算方法(已作废)(注:已有GB/T 10062.1.2.3-2003在标准参考资料<十一 > 中)2 、 GB10062-88锥齿轮承载能力计算方法编制说明3 、 GB11365-89锥齿轮和准双曲面齿轮精度4 、 GB11365-89锥齿轮和准双曲面齿轮精度编制说明5 、 GB11367-89锥齿轮胶合承载能力计算方法(注:标准出版社出版标准汇编中没有)6 、 GB11367-89锥齿轮胶合承载能力计算方法编制说明7 、 GB12368-90锥齿轮模数8 、 GB12368-90锥齿轮模数编制说明9 、 GB12369-90直齿及斜齿锥齿轮基本齿廓10 、 GB12369-90直齿及斜齿锥齿轮基本齿廓编制说明11 、 GB12370-90锥齿轮和准双曲面齿轮术语12 、 GB12371-90锥齿轮图样上应注明的尺寸数据13 、 GB12371-90锥齿轮图样上应注明的尺寸数据编制说明(齿轮装置部分)1 、 GB6404-86齿轮装置噪声声功率级测定方法(已作废)(注:已有 GB/T 6404.1-2005/ISO8579-1:2002 (代替 GB/T 6404-1986 )齿轮装置的验收规范第1 部分:空气传播噪声的试验规范在最新标准中)2 、 GB6404-86 齿轮装置噪声声功率级测定方法编制说明3 、 GB8542-87 透平齿轮传动装置技术条件4 、 GB8542-87 透平齿轮传动装置技术条件编制说明5 、 GB8543-87 验收试验中齿轮装置机械振动的测定(已作废)(注:已有GB/T 6404.2-2005/ISO 8579-2:2002 (代替 GB/T 8543-1987 )齿轮装置的验收规范第2 部分:验收试验中齿轮装置机械振动的测定在最新标准中)6 、 GB8543-87 验收试验中齿轮装置机械振动的测定编制说明7 、 GB/T14231-93 齿轮装置效率测定方法8 、 GB/T14231-93 齿轮装置效率测定方法编制说明9 、 JB/T5076-91 齿轮装置噪声评价10 、 JB/T5076-91 齿轮装置噪声评价编制说明11 、 JB/T5077-91 通用齿轮装置型式试验方法12 、 JB/T5077-91 通用齿轮装置型式试验方法编制说明13 、 JB/T6078-92 齿轮装置质量检验总则14 、 JB/T6078-92 齿轮装置质量检验总则编制说明15 、 JB/T7929-95 齿轮传动装置清洁度16 、 JB/T7929-95 齿轮传动装置清洁度编制说明17 、 JB/T8831-1999 工业齿轮润滑油选用方法(已作废)(注:已有JB/T8831-2001在标准出版社出版标准汇编中)18 、 JB/T8831-1999工业齿轮润滑油选用方法编制说明(齿轮热处理部分)1 、 GB/T3480.5-2008直齿轮和斜齿轮承载能力计算第五部分;材料的强度和质量2 、 GB/T3480.5-2008直齿轮和斜齿轮承载能力计算第五部分;材料的强度和质量编制说明3 、 GB/T17879-1999齿轮磨削后表面回火的浸蚀检验(注:标准出版社出版标准汇编中没有)4 、 GB/T17879-1999齿轮磨削后表面回火的浸蚀检验编制说明5 、 JB/T5078-91高速齿轮材料选择及热处理质量控制的一般规定6 、 JB/T7516-94齿轮气体渗碳热处理工艺及其质量控制7 、 JB/T9171-1999齿轮火焰及感应淬火工艺及其质量控制8 、 JB/T9171-1999齿轮火焰及感应淬火工艺及其质量控制标准介绍9 、 JB/T9172-1999齿轮渗氮、氮碳共渗工艺及其质量控制10 、 JB/T9172-1999齿轮渗氮、氮碳共渗工艺及其质量控制标准介绍11 、 JB/T9173-1999齿轮碳氮共渗工艺及其质量控制12 、 JB/T9173-1999齿轮碳氮共渗工艺及其质量控制标准介绍(齿轮减速器部分)1 、 JB/T8853-2001圆柱齿轮减速器2 、 JB/T7935-1999圆弧圆柱蜗杆减速器3 、 JB/T7936-1999直廓环面蜗杆减速器4 、 JB/T9050.1-1999圆柱齿轮减速器通用技术条件5 、 JB/T9050.2-1999圆柱齿轮减速器接触斑点测定方法6 、 JB/T9050.3-1999圆柱齿轮减速器加载试验方法7 、 JB/T9051-1999平面包络环面蜗杆减速器(新齿轮精度部分)1 、 GB/T10095.1-2008圆柱齿轮精度制第1部分:轮齿同侧齿面偏差的定义和允许值2 、 GB/T10095.2-2008圆柱齿轮精度制第2部分:径向综合偏差与径向跳动的定义和允许值3 、 GB/Z18620.1-2008圆柱齿轮检验实施规范第1部分:轮齿同侧齿面的检验4 、 GB/Z18620.2-2008圆柱齿轮检验实施规范第2部分:径向综合偏差、径向跳动、齿厚和侧隙的检验3 、 GB/Z18620.3-2008圆柱齿轮检验实施规范第3部分:齿轮坯、轴中心距和轴线平行度4 、 GB/Z18620.4-2008圆柱齿轮检验实施规范第4部分:表面结构和轮齿接触斑点的检验5 、 GB/T 13924-2008渐开线圆柱齿轮精度检验细则6 、 GB/T 1357-2008通用机械和重型机械用圆柱齿轮模数(齿轮刀具国标部分)1 、 GB/T 6081-2001直齿插齿刀基本型式和尺寸2 、 GB/T 6082-2001直齿插齿刀通用技术条件3 、 GB/T 6083-2001齿轮滚刀基本型式和尺寸4 、 GB/T 6084-2001齿轮滚刀通用技术条件5 、 GB/T 14333-93盘形剃齿刀6 、 GB/T 14348.1-93双圆弧齿轮滚刀型式和尺寸7 、 GB/T 14348.2-93双圆弧齿轮滚刀技术条件8 、 GB 9205-88镶片齿轮滚刀(齿轮刀具行标部分)1 、 JB/T 2494.1-94小模数齿轮滚刀基本型式和尺寸2 、 JB/T 2494.2-94小模数齿轮滚刀技术条件3 、 JB/T 3095.1-94小模数直齿插齿刀基本型式和尺寸4 、 JB/T 3095.2-94小模数直齿插齿刀技术条件5 、 JB/T 3227-1999高精度齿轮滚刀通用技术条件6 、 JB/T 4103-94剃前齿轮滚刀基本型式和尺寸7 、 JB/T 4104-94剃前齿轮滚刀技术条件8 、 JB/T 7654.1-94整体硬质合金小模数齿轮滚刀基本型式和尺寸9 、 JB/T 7654.2-94整体硬质合金小模数齿轮滚刀技术条件10 、 JB/T 7967-1999渐开线内花键插齿刀基本型式和尺寸11 、 JB/T 7968.1-1999磨前齿轮滚刀基本型式和尺寸12 、 JB/T 7968.2-1999磨前齿轮滚刀技术条件13 、 JB/T 7970.1-1999盘形齿轮铣刀基本型式和尺寸14 、 JB/T 7970.2-1999盘形齿轮铣刀技术条件15 、 JB/T 8345-96弧齿锥齿轮铣刀 1 ︰ 24 圆锥孔尺寸及公差16 、 JB/T 9990.1-1999直齿锥齿轮精刨刀基本型式和尺寸17 、 JB/T 9990.2-1999直齿锥齿轮精刨刀技术条件(锥齿轮部分)1 、 GB/T10062.1-2003/ISO10300-1:2001锥齿轮承载能力计算方法第1部分:概述和通用影响系数2 、 GB/T10062.2-2003/ISO10300-1:2001锥齿轮承载能力计算方法第2部分:齿面接触疲劳(点蚀)强度计算3 、 GB/T10062.3-2003/ISO10300-1:2001锥齿轮承载能力计算方法第3部分:齿根弯曲强度计算4 、 GB/Z6413.1-2003/ISO/TR 13989-1:2000圆柱齿轮、锥齿轮和准双曲面齿轮胶合承载能力计算方法第 1 部分:闪温法5 、 GB/Z6413.2-2003/ISO/TR 13989-1:2000圆柱齿轮、锥齿轮和准双曲面齿轮胶合承载能力计算方法第 2 部分:积分温度法1 、 GB/Z 19414-2003/ISO/TR 13593:1999工业用闭式齿轮齿轮传动装置2 、 GB/T 19406-2003/ISO 9085:2002渐开线直齿和斜齿圆柱齿轮承载能力计算方法工业齿轮应用3 、 GB/T2821-2003/ISO 701:1998齿轮几何要素代号(齿轮量仪部分)1 、 GB/T 1217-2004公法线千分尺2 、 GB 5106-85圆柱直齿渐开线花键量规3 、GB 6060.2-85表面粗糙度比较样块磨、车、镗、铣、插及刨加工表面4 、 GB 6060.5-88表面粗糙度比较样块抛(喷)丸、喷砂加工表面5 、 GB/T 6316-1996齿厚游标卡尺6 、 GB/T 6320-1997杠杆齿轮比较仪7 、 GB/T 6467-2001齿轮渐开线样板8 、 GB/T 6468-2001齿轮螺旋线样板9 、 GB 10919-89矩形花键量规10 、 JB/T 10008-1999测量蜗杆11 、 JB/T 10012-1999万能测齿仪12 、 JB/T 10013-1999万能渐开线检查仪13 、 JB/T 10019-1999齿轮齿距测量仪14 、 JB/T 10020-1999万能齿轮测量机15 、 JB/T 10021-1999齿轮螺旋线测量仪16 、 JB/T 10022-1999便携式齿轮齿距测量仪17 、 JB/T 10023-1999便携式齿轮基节测量仪18 、 JB/T 10024-1999立式滚刀测量仪19 、 JB/T 10025-1999齿轮双面啮合综合测量仪20 、 JB/T 10026-1999齿轮单面啮合整体误差测量仪。
齿轮碳氮共渗工艺过程

齿轮碳氮共渗工艺过程1. 简介齿轮碳氮共渗是一种用于提高齿轮表面硬度和耐磨性的热处理工艺。
在该工艺过程中,齿轮将被加热至一定温度(通常在800°C-950°C之间),并浸泡在富氮气体环境中。
碳和氮将渗入齿轮的表面,形成一层硬度更高的表面层。
2. 工艺流程齿轮碳氮共渗的工艺流程主要包括以下几个步骤:2.1 清洗预处理在进行齿轮碳氮共渗之前,首先需要对齿轮进行清洗预处理。
这可以通过浸泡在溶液中或使用超声波清洗机来完成。
清洗的目的是去除齿轮表面的污垢和氧化物,以保证共渗剂能够更好地渗透到齿轮表面。
2.2 加热处理清洗完毕后,将齿轮放入加热炉中进行加热处理。
加热温度和时间的选择取决于材料的种类和要求的硬度。
通常,加热温度在800°C-950°C之间,并保持一定时间(通常在1-4小时)。
2.3 碳氮共渗处理在完成加热处理后,将炉子中的气氛置换为含氮气气氛。
这可以通过向炉内注入氮气或使用其他氮气源来实现。
在共渗处理期间,氮气将与加热齿轮的表面反应,并在其表面形成一层氮化物。
同时,共渗剂中的碳和氮将渗入到齿轮的表面层中,提高其硬度和耐磨性。
2.4 冷却处理碳氮共渗处理完成后,将齿轮从炉中取出并进行冷却处理。
这可以通过自然冷却或使用其他冷却介质(如水或油)来实现。
冷却的目的是快速冷却齿轮,从而使其表面固化,并保持渗层的稳定性。
2.5 清洗后处理完成冷却处理后,将齿轮再次进行清洗。
这可以通过浸泡在溶液中或使用超声波清洗机来完成。
清洗的目的是去除共渗剂残留和其他可能存在的污垢,以保证齿轮表面的干净度和质量。
3. 后续处理齿轮碳氮共渗完成后,还可以进行一些后续处理,以进一步提高其性能和质量。
例如,可以进行回火处理来减轻共渗处理过程中的应力,并提高齿轮的韧性。
此外,还可以进行抛光和润滑处理,以提高齿轮的表面质量和耐磨性。
4. 应用领域齿轮碳氮共渗工艺广泛应用于各种设备和机械领域。
金相法测量渗碳(碳氮共渗)齿轮的有效硬化层深度
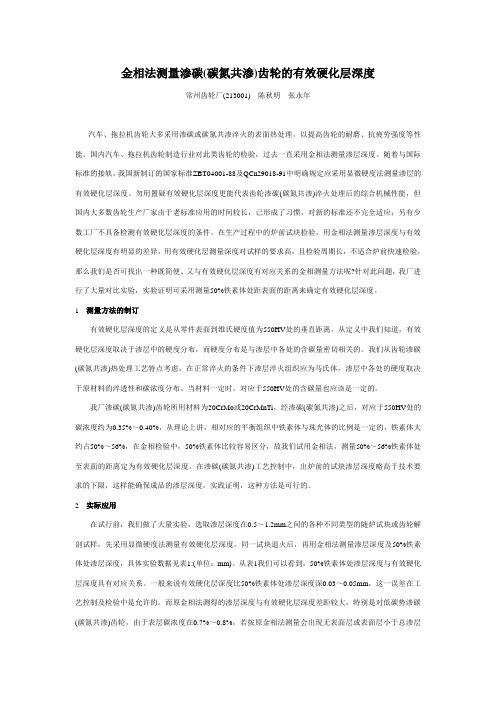
金相法测量渗碳(碳氮共渗)齿轮的有效硬化层深度常州齿轮厂(213001)陈秋明张永年汽车、拖拉机齿轮大多采用渗碳或碳氮共渗淬火的表面热处理,以提高齿轮的耐磨、抗疲劳强度等性能。
国内汽车、拖拉机齿轮制造行业对此类齿轮的检验,过去一直采用金相法测量渗层深度。
随着与国际标准的接轨,我国新制订的国家标准ZBT04001-88及QCn29018-91中明确规定应采用显微硬度法测量渗层的有效硬化层深度。
勿用置疑有效硬化层深度更能代表齿轮渗碳(碳氮共渗)淬火处理后的综合机械性能,但国内大多数齿轮生产厂家由于老标准应用的时间较长,已形成了习惯,对新的标准还不完全适应;另有少数工厂不具备检测有效硬化层深度的条件。
在生产过程中的炉前试块检验,用金相法测量渗层深度与有效硬化层深度有明显的差异,用有效硬化层测量深度对试样的要求高,且检验周期长,不适合炉前快速检验,那么我们是否可找出一种既简便、又与有效硬化层深度有对应关系的金相测量方法呢?针对此问题,我厂进行了大量对比实验,实验证明可采用测量50%铁素体处距表面的距离来确定有效硬化层深度。
1测量方法的制订有效硬化层深度的定义是从零件表面到维氏硬度值为550HV处的垂直距离。
从定义中我们知道,有效硬化层深度取决于渗层中的硬度分布,而硬度分布是与渗层中各处的含碳量密切相关的。
我们从齿轮渗碳(碳氮共渗)热处理工艺特点考虑,在正常淬火的条件下渗层淬火组织应为马氏体,渗层中各处的硬度取决于原材料的淬透性和碳浓度分布。
当材料一定时,对应于550HV处的含碳量也应该是一定的。
我厂渗碳(碳氮共渗)齿轮所用材料为20CrMo或20CrMnTi,经渗碳(碳氮共渗)之后,对应于550HV处的碳浓度约为0.35%~0.40%,从理论上讲,相对应的平衡组织中铁素体与珠光体的比例是一定的,铁素体大约占50%~56%,在金相检验中,50%铁素体比较容易区分,故我们试用金相法,测量50%~56%铁素体处至表面的距离定为有效硬化层深度。
碳氮共渗热处理工艺
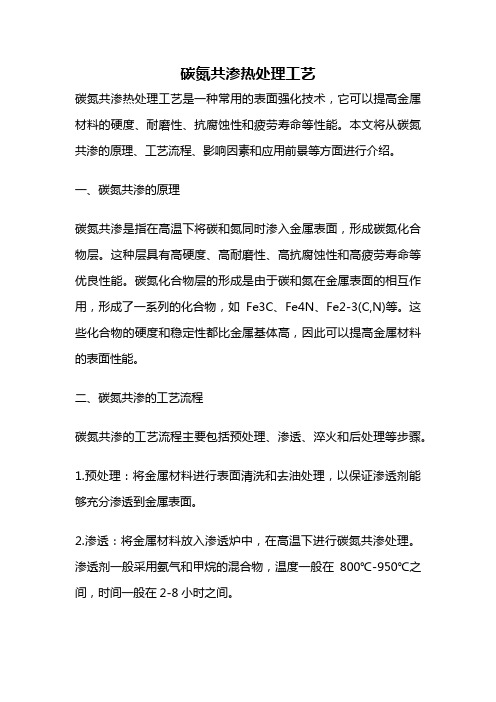
碳氮共渗热处理工艺碳氮共渗热处理工艺是一种常用的表面强化技术,它可以提高金属材料的硬度、耐磨性、抗腐蚀性和疲劳寿命等性能。
本文将从碳氮共渗的原理、工艺流程、影响因素和应用前景等方面进行介绍。
一、碳氮共渗的原理碳氮共渗是指在高温下将碳和氮同时渗入金属表面,形成碳氮化合物层。
这种层具有高硬度、高耐磨性、高抗腐蚀性和高疲劳寿命等优良性能。
碳氮化合物层的形成是由于碳和氮在金属表面的相互作用,形成了一系列的化合物,如Fe3C、Fe4N、Fe2-3(C,N)等。
这些化合物的硬度和稳定性都比金属基体高,因此可以提高金属材料的表面性能。
二、碳氮共渗的工艺流程碳氮共渗的工艺流程主要包括预处理、渗透、淬火和后处理等步骤。
1.预处理:将金属材料进行表面清洗和去油处理,以保证渗透剂能够充分渗透到金属表面。
2.渗透:将金属材料放入渗透炉中,在高温下进行碳氮共渗处理。
渗透剂一般采用氨气和甲烷的混合物,温度一般在800℃-950℃之间,时间一般在2-8小时之间。
3.淬火:将渗透后的金属材料迅速冷却,以保证碳氮化合物层的稳定性和硬度。
4.后处理:对淬火后的金属材料进行退火处理,以消除残余应力和提高材料的韧性。
三、碳氮共渗的影响因素碳氮共渗的效果受到多种因素的影响,如温度、时间、渗透剂成分、金属材料成分和表面状态等。
1.温度:温度是影响碳氮共渗效果的重要因素。
温度过低会导致渗透剂无法充分渗透到金属表面,温度过高会导致碳氮化合物层的过度生长和烧结。
2.时间:时间是影响碳氮共渗效果的另一个重要因素。
时间过短会导致碳氮化合物层的厚度不足,时间过长会导致碳氮化合物层的过度生长和烧结。
3.渗透剂成分:渗透剂成分对碳氮共渗效果也有很大的影响。
不同的渗透剂成分会导致不同的化合物生成,从而影响碳氮化合物层的性能。
4.金属材料成分和表面状态:金属材料的成分和表面状态也会影响碳氮共渗效果。
不同的金属材料对渗透剂的反应不同,表面状态的不同也会影响渗透剂的渗透性能。
- 1、下载文档前请自行甄别文档内容的完整性,平台不提供额外的编辑、内容补充、找答案等附加服务。
- 2、"仅部分预览"的文档,不可在线预览部分如存在完整性等问题,可反馈申请退款(可完整预览的文档不适用该条件!)。
- 3、如文档侵犯您的权益,请联系客服反馈,我们会尽快为您处理(人工客服工作时间:9:00-18:30)。
7. 1 随炉试样检验 7. 1. 1 表面硬度
表面硬度检验按 GB/T 5030、GB/T 4340、GB/T 1818 测量;对渗氮后要磨削的齿轮,应将试样 表面磨去加工余量后测量,硬度应符合技术条件规定,推荐测试负荷见表 2。
4
有效硬化层深度 mm
维氏硬度(HV)测试负荷 N
540~570
—
480~500
500~530
调整 退氮 30~40 >95 480~500
500~530
6. 4. 2 处理时间 按齿轮材料、渗层深度要求选择的工艺类别等综合确定。一般按每小时 0.01 mm 的平均渗速估算
时间。 6. 4. 3 冷却方式
a)气体渗氮、离子渗氮、离子氮碳共渗后在炉内冷至 200℃ 以下后空冷; b)气体氮碳共渗后也可采用油冷; c)液体氮碳共渗后一般采用水冷; d)为减少变形,对高精度不磨齿的齿轮可采用分段冷却。 6. 4. 4 清洗 液体氮碳共渗后要及时清洗、中和附在齿轮上的残盐、残渣。
成品齿轮轮齿工作高度中间部位的齿面硬度。 3. 2 渗层深度
齿轮或试样经渗氮、氮碳共渗后,从硬化层表面垂直测至规定的硬度或显微组织处的距离。 3. 3 界限硬度值
为确定渗氮、氮碳共渗后齿轮的有效硬化层深度而规定的最低硬度值。
国家机械工业局 1999-06-24 批准
2000-01-01 实施
1
JB/T 9172-1999
JB/T 9172-1999 表2
≤0.15
>0.15~0.3
9.806
49.03
>0.3 98.06,也可用(HR15N)
7. 1. 2 渗层深度 渗层深度检验以硬度法为主,金相法为辅,检验结果应符合产品技术要求。
7. 1. 2. 1 硬度法 测定有效硬化层深度,选用 4.9 N 负荷,从试样表面垂直测至界限硬度处的距离。 测试负荷只能在 1.96~19.6 N 范围内选取。 渗层深度在 0.3 mm 以下时,按 GB/T 9451 进行测定。
GB/T 1818—1994 金属表面洛氏硬度试验方法
GB/T 1348—1988 球墨铸铁件
GB/T 3077—1988 合金结构钢 技术条件
GB/T 3480—1997 渐开线圆柱齿轮承载维氏硬度试验方法
GB/T 5030—1985 金属小负荷维氏硬度试验方法
中华人民共和国机械行业标准
齿轮渗氮、氮碳共渗 工艺及质量控制
Gear nitriding and nitrocarburizing process and its quality control
JB/T 9172-1999
代替 ZB J17 001—88
1 范围
本标准规定了齿轮渗氮(气体、离子)及氮碳共渗(气体、离子、液体)的有关术语、材料选择、 处理设备、工艺及质量控制。
齿轮渗氮、氮碳共渗后用肉眼检查表面,不得有氧化皮、碰伤、剥落、电弧烧伤、残盐存留等缺陷。 7. 2. 2 齿面硬度
a)抽检批量生产的齿轮,当随炉试样合格时,每批抽检 1 件,约在相隔 120°的三个轮齿上,在 齿高中部各测 1~3 点,也可用维氏硬度计或表面洛氏硬度计(HR15N)测量端面或齿顶硬度;
前言
本标准是对 ZB J17 001—88《齿轮渗氮、氮碳共渗工艺及质量控制》的修订。 本标准自实施之日起代替 ZB J17 001—88。 本标准的附录 A 是提示的附录。 本标准由全国齿轮标准化技术委员会提出并归口。 本标准负责起草单位:郑州机械研究所。 本标准主要起草人:李耀珍、陈秀玉、杨星原。
按 GB/T 11354 有关规定检验压痕周边碎裂程度,每件测 3 点,至少有两点处于相同级别,1~3 级为合格。对留有磨量的齿轮,可磨去加工余量后测量,测量结果应符合技术条件。对要求高的齿轮, 经双方协商可对试样采用声发射法检验。 7. 1. 5 渗层疏松
渗层表面化合物层疏松按 GB/T 11354 评定,1~3 级为合格。 7. 1. 6 渗层中氮化物形态
5
JB/T 9172-1999 b)当随炉试样检查不合格时,应取同炉的齿轮 3 件,每件测 3 个轮齿,每个轮齿测 1~3 点; c)对无法用硬度计检查的齿轮,一般以随炉试样的测量值为准; d)硬度不符合技术条件要求时,应根据具体情况进行返修处理或判废。 7. 2. 3 渗层深度与轮齿中心硬度 a)批量生产的齿轮,在随炉试样检验合格情况下应定期抽检。若随炉试样不合格,则该批至少抽 检 1 件齿轮。检验方法同 7.1.2、7.1.3; b)单件重要的齿轮,一般以随炉试样测量为准。经协商可将一个轮齿的末端沿一个角度磨制抛光 并腐蚀,用带有刻度的放大镜测量渗层深度。用肖氏硬度计检测轮齿中心的硬度,测量结果应达到产 品图样和技术文件的规定值; c)渗氮、氮碳共渗层深度的均匀度为技术条件要求中值的±15%。 7. 2. 4 抽检 抽检齿轮的渗氮、氮碳共渗层脆性、渗层疏松、氮化物形态。检查同 7.1.4、7.1.5、7.1.6。 7. 2. 5 变形 对精度要求高的齿轮,抽查 1~3 件,用相应量具检查齿轮几何精度,其结果应符合技术条件要求。 7. 2. 6 局部防渗 用肉眼观察局部防渗部位,一般应基本保持原金属色,若发现有渗氮色,可用硬度计或高硬度锉 刀进行检查,以不影响切削加工为准。
注:当齿轮设计的接触疲劳极限与弯曲疲劳极限位于 GB/T 3480 疲劳极限区域图的不同位置时,参见附录 A(提 示的附录)选择材料。
5 设备要求
5. 1 气体渗氮、氮碳共渗设备 a)齿轮在有效加热区内加热时,其设备应能保证处理温度控制在预定温度±10℃ 之内; b)渗氮、氮碳共渗炉氨的分解率应能根据工艺要求作适当的调整; c)渗氮、氮碳共渗炉应能根据工艺要求良好密封;气体应均匀接触齿轮表面,最好有流通装置; d)测试仪表的精度为 0.5 级(JJG 74); e)氮碳共渗设备应具有充分燃烧、排出废气的装置,环境中 CN– 含量应控制在 0.3 mg/m3 以下; f)渗氮罐应定期进行退氮处理。
3
工艺类型 一段法 二段法 三段法
JB/T 9172-1999
齿轮的装炉量、位置及方向要恰当,使炉内介质流畅和每个轮齿加热均匀,以减少变形。 6. 4 齿轮渗氮、氮碳共渗工艺 6. 4. 1 温度及参数
根据齿轮材料、形状、模数及技术要求选取表 1 中的温度及参数。 表1
均温
气体渗氮
温度 ℃
氨分解率 %
5. 2 离子渗氮、氮碳共渗设备 a)设备应设置电压、电流、温度、真空度和气体流量的测量指示仪表,温度应能自动控制和记录;
2
JB/T 9172-1999
b)极限真空度应不低于 6.7 Pa(5×10–2Torr),压升率不大于 1.3×10–1Pa/min(1×10–3Torr/min); c)设备应具有可靠的灭弧装置。 5. 3 液体氮碳共渗设备 a)应有良好的吸风防护罩等安全防护装置; b)应有中和消除有毒废液处理装置,排放须符合环境保护条例。
6 工艺控制
6. 1 渗剂 6. 1. 1 常用种类
a)渗氮:氨、热分解氨、氮氢混合气、氨加氧; b)氮碳共渗:氨加甲醇、氨加二氧化碳、氨加吸热性气氛、微毒盐类等。 6. 1. 2 要求 渗剂不得对齿轮产生有害影响,应符合标准渗剂技术条件。 6. 2 齿轮渗氮、氮碳共渗预处理要求 6. 2. 1 基体处理 6. 2. 1. 1 合金结构钢采用调质。调质回火温度一般比渗氮温度高 20℃ 以上,调质加工表面不允许有 脱碳,调质硬度应符合技术条件。 6. 2. 1. 2 碳素钢氮碳共渗齿轮在冲击性能要求不高时可采用正火处理,正火后硬度应符合技术条件要求。 6. 2. 2 去应力退火 对变形要求小的齿轮,在渗氮前应进行一次或数次去应力退火,其最高温度应低于调质回火温度, 高于渗氮、氮碳共渗温度。 6. 2. 3 表面清理 齿轮渗氮、氮碳共渗前必须除去锐边、清洗干净,不得有油污、氧化皮等其它有害的杂物。 6. 2. 4 局部防渗 对不需渗氮、氮碳共渗部位,用镀层、防渗涂料或机械屏蔽法防渗。 6. 2. 5 待处理齿轮表面粗糙度 Ra 应小于 3.2 μm。 6. 2. 6 夹具 6. 2. 6. 1 气体渗氮及氮碳共渗夹具应设计合理、吊挂牢固。经一定时间使用后要进行退氮处理。 6. 2. 6. 2 离子渗氮及氮碳共渗夹具与齿轮之间的间隙应适当,以免打弧。 6. 3 齿轮渗氮、氮碳共渗工艺规程 6. 3. 1 随炉试样 a)随炉试样的材料成分、预先热处理、金相组织、力学性能应与齿轮相一致。高可靠度齿轮最好 在齿轮上取样; b)试样尺寸(圆棒直径或方形试样厚度)应近似于分度圆齿厚; c)随炉试样被检表面粗糙度 Ra 应小于 0.8 μm,表面不得有脱碳层、氧化皮、锈斑和油污; d)试样应放置在能代表该炉齿轮渗层质量的位置上。 6. 3. 2 装炉
本标准适用于合金结构钢和球墨铸铁制齿轮的渗氮、氮碳共渗以及 45 碳素结构钢氮碳共渗。 2 引用标准
下列标准所包含的条文,通过在本标准中引用而构成为本标准的条文。本标准出版时,所示版本
均为有效。所有标准都会被修订,使用本标准的各方应探讨使用下列标准最新版本的可能性。
GB/T 699—1988 优质碳素结构钢 技术条件
GB/T 9451—1988 钢件薄表面总硬化层深度或有效硬化层深度测定
GB/T 11354—1989 钢铁零件渗氮层深度测定和金相组织检验
GB/T 13299—1991 钢的显微组织评定法
YB/T 5148—1993 金属平均晶粒度测定方法
JJG 74—1992
自动平衡式显示仪表检定规程
3 术语
本标准采用下列术语。 3. 1 齿面硬度
7. 1. 2. 2 金相法 用金相显微镜按 GB/T 11354 规定,从试样表面垂直测至与基体组织有明显分界处的距离。当基
体组织界线不明显、无法正确判断时,应以硬度法为准。 7. 1. 3 心部硬度