渗碳及碳氮共渗齿轮热处理质量检验综述
齿轮渗氮、氮碳共渗工艺及质量控制

齿轮渗氮、氮碳共渗工艺及质量控制
齿轮渗氮是一种提高齿轮表面硬度和耐磨性的表面处理方法,可以通过在齿轮表面注入氮气,使其在表面形成氮化层。
齿轮渗氮的主要工艺包括气体渗氮和盐浴渗氮两种方法。
1. 气体渗氮工艺:气体渗氮是将齿轮置于渗氮炉中,通过加热至高温状态,然后通过氨气或氮气等气体进行渗透处理,使氮原子渗入齿轮表面形成氮化层。
这种工艺具有操作简单、渗透深度可控、成本较低等优点。
2. 盐浴渗氮工艺:盐浴渗氮是将齿轮浸入温度较高的盐浴溶液中进行处理,使盐浴溶液中的氮原子渗透到齿轮表面形成氮化层。
这种工艺渗透速度较快,渗透深度大,但操作复杂,成本较高。
质量控制是齿轮渗氮过程中非常重要的环节,主要包括以下几个方面:
1. 温度控制:温度是齿轮渗氮过程中的重要参数,需要控制在合适的范围内,以保证渗透效果和避免过热损坏齿轮。
2. 渗氮时间控制:渗氮时间是影响氮化层深度和均匀性的重要因素,需要根据齿轮的具体要求和设计要求来确定。
3. 渗氮介质控制:选择合适的渗氮介质对于渗透效果和氮化层质量都有重要影
响,需要根据具体情况进行选择。
4. 清洗和处理后的质量检验:渗氮后需要对齿轮进行清洗和处理,以去除表面的残留物,然后进行质量检验,包括硬度测试、金相分析、氮化层厚度测量等。
通过合理的工艺选择和质量控制,可以确保齿轮渗氮的效果和质量,提高齿轮的使用寿命和性能。
渗碳及碳氮共渗齿轮热处理质量检验综述

渗碳及碳氮共渗齿轮热处理质量检验综述作者:赵美惠来源:《科技创新导报》2011年第17期摘要;齿轮的热处理质量直接关系到齿轮的使用寿命,而齿轮的热处理工艺通常有二种:渗碳及碳氮共渗,通用对层深、硬度及金相组织的检测,可以很好的控制齿轮的热处理质量。
关键词:金相法硬度法硬度碳化物中图分类号:TP2 文献标识码:A 文章编号:1674-098X(2011)06(b)-0091-01齿轮是汽车结构中的重要基础部件,齿轮质量的优劣,直接影响着汽车产品的性能和使用寿命。
影响汽车齿轮使用寿命的因素很多,除设计、选材、冷加工及使用条件外、齿轮的热处理质量起着重要的作用。
渗碳及碳氮共渗齿轮热处理质量的好坏是通过有效硬化层深度、硬度及金相组织来鉴别的,因此必须对齿轮热处理后的质量进行准确的检验及严格的控制。
1 检验与控制1.1 渗碳及碳氮共渗层深(1)金相法测层深在1987年以前,国内对渗碳及碳氮共渗件层深的检验多采用“金相法”,各生产厂家根据本厂的生产特点及产品的使用情况,制定各自不同的检验标准和技术要求。
用金相法检测层深,必须是在平衡的组织状态下进行,即零件必须进行等温退火处理,再进行检验。
渗层深度包括过共析层、共析层及全部过渡区域,即由表面起到心部组织为止的总深度。
共析层深度系指由表面起至出现显著的铁素体为止的深度。
表面层含碳量应大于0.8%。
渗碳层中过共析和共析层深度应为渗碳层总深度的50%~75%。
用金相法检测层深最大的问题是:它是一种间接的测量方法,不能直接反映零件的使用性能。
如果渗碳层深度合格而淬火组织不合格,用金相法测层深是无法检测到的。
(2)硬度法测层深随着汽车产业的发展,检测标准与国际国准的接轨日趋重要,1988年我国等效采用了ISO2639《钢件渗碳淬火硬化层深度的测定和校核》而制定了国家标准GB/T9450《钢件渗碳淬火有效硬化层深度的测定和校核》,即开始使用“硬度法”对渗碳淬火件进行“有效硬化层深度”的检测。
金相法测量渗碳(碳氮共渗)齿轮的有效硬化层深度
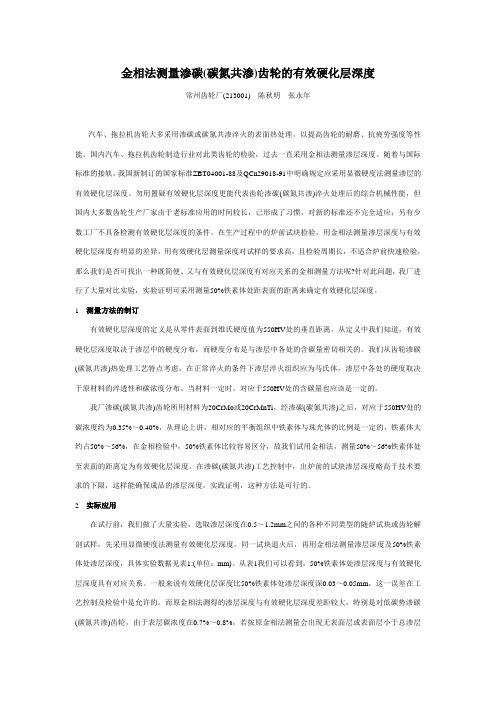
金相法测量渗碳(碳氮共渗)齿轮的有效硬化层深度常州齿轮厂(213001)陈秋明张永年汽车、拖拉机齿轮大多采用渗碳或碳氮共渗淬火的表面热处理,以提高齿轮的耐磨、抗疲劳强度等性能。
国内汽车、拖拉机齿轮制造行业对此类齿轮的检验,过去一直采用金相法测量渗层深度。
随着与国际标准的接轨,我国新制订的国家标准ZBT04001-88及QCn29018-91中明确规定应采用显微硬度法测量渗层的有效硬化层深度。
勿用置疑有效硬化层深度更能代表齿轮渗碳(碳氮共渗)淬火处理后的综合机械性能,但国内大多数齿轮生产厂家由于老标准应用的时间较长,已形成了习惯,对新的标准还不完全适应;另有少数工厂不具备检测有效硬化层深度的条件。
在生产过程中的炉前试块检验,用金相法测量渗层深度与有效硬化层深度有明显的差异,用有效硬化层测量深度对试样的要求高,且检验周期长,不适合炉前快速检验,那么我们是否可找出一种既简便、又与有效硬化层深度有对应关系的金相测量方法呢?针对此问题,我厂进行了大量对比实验,实验证明可采用测量50%铁素体处距表面的距离来确定有效硬化层深度。
1测量方法的制订有效硬化层深度的定义是从零件表面到维氏硬度值为550HV处的垂直距离。
从定义中我们知道,有效硬化层深度取决于渗层中的硬度分布,而硬度分布是与渗层中各处的含碳量密切相关的。
我们从齿轮渗碳(碳氮共渗)热处理工艺特点考虑,在正常淬火的条件下渗层淬火组织应为马氏体,渗层中各处的硬度取决于原材料的淬透性和碳浓度分布。
当材料一定时,对应于550HV处的含碳量也应该是一定的。
我厂渗碳(碳氮共渗)齿轮所用材料为20CrMo或20CrMnTi,经渗碳(碳氮共渗)之后,对应于550HV处的碳浓度约为0.35%~0.40%,从理论上讲,相对应的平衡组织中铁素体与珠光体的比例是一定的,铁素体大约占50%~56%,在金相检验中,50%铁素体比较容易区分,故我们试用金相法,测量50%~56%铁素体处至表面的距离定为有效硬化层深度。
渗氮 渗碳 碳氮共渗

渗氮渗碳碳氮共渗碳氮共渗是一种常见的表面处理技术,通过渗碳和渗氮来改善材料的硬度和耐磨性。
本文将对渗氮、渗碳和碳氮共渗的原理、应用和工艺进行详细介绍。
一、渗氮渗氮是将氮原子渗入材料表面形成氮化物层的过程。
氮原子通过高温处理和氮气氛的作用,渗透到材料表面并与材料中的元素反应,形成硬质氮化物层。
这一薄层氮化物层不仅能提高材料的硬度和抗磨损性能,还能改善材料的耐腐蚀性。
渗氮的主要应用领域包括机械制造、汽车工业、航空航天等。
在机械制造中,渗氮可以增加零件的硬度和耐磨性,延长使用寿命;在汽车工业中,渗氮可以提高引擎零件的耐磨性和抗腐蚀性能;在航空航天领域,渗氮可以增强航空发动机部件的耐高温和耐磨性能。
渗氮的工艺流程一般包括清洗件表面、装配件和炉内预处理、渗氮和回火处理等步骤。
渗氮一般采用封闭式和开放式两种方式进行,根据具体应用需求可以选择合适的渗氮工艺。
二、渗碳渗碳是将碳原子渗入材料表面形成碳化物层的过程。
碳原子通过高温处理和含有碳气体的氛围,渗透到材料表面并在表面与材料中的元素反应,形成硬质碳化物层。
渗碳技术不仅能提升材料的硬度和耐磨性,还可以改善材料的断裂韧性和抗腐蚀性。
渗碳广泛应用于机械零件、钢铁制品等领域。
渗碳后的材料表面硬度高、耐磨性好,适用于制作耐磨零件,如轴承、齿轮等;同时碳化层的外表面与空气隔绝,降低了材料的腐蚀速率,提高了零件的使用寿命。
渗碳的工艺流程包括预处理、渗碳、淬火和回火等。
渗碳一般采用气体渗碳和液体渗碳两种方式进行,具体工艺参数可以根据材料的要求进行选择。
三、碳氮共渗碳氮共渗是将碳原子和氮原子同时渗入材料表面形成碳氮共渗层的过程。
碳氮共渗通过碳氮共渗剂和高温处理,使碳原子和氮原子分别与材料中的元素发生反应,形成硬质碳氮化物层。
碳氮共渗能够同时获得渗碳和渗氮的特性,提高材料的硬度、耐磨性和抗腐蚀性。
碳氮共渗广泛应用于汽车工业、航空航天等领域。
在汽车工业中,碳氮共渗可以提高零部件的硬度和耐磨性,同时还可以提高零部件的抗磨损能力和抗腐蚀性;在航空航天领域,碳氮共渗可以增强发动机部件的抗高温性能和抗腐蚀能力。
烧结铁基材料渗碳或碳氮共渗层深度的测定及其验证 -回复

烧结铁基材料渗碳或碳氮共渗层深度的测定及其验证-回复烧结铁基材料的渗碳或碳氮共渗层深度的测定及其验证是研究领域中的一个重要问题。
渗碳或碳氮共渗处理是一种将碳和氮等元素渗入铁基材料表面以增强其表面性能的工艺。
本文将一步一步回答这个问题。
第一步:测定渗碳或碳氮共渗层深度的方法有很多方法可以用来测定渗碳或碳氮共渗层的深度。
以下是一些常见的方法:1. 金相显微镜(Metallographic microscopy):这是一种通过显微镜观察样品切面的方法。
首先,样品需经过磨削、抛光等处理,然后在显微镜下观察样品切面,通过比较渗层与基体的差异来确定渗层深度。
2. X射线衍射(X-ray diffraction):X射线衍射可以通过测量衍射谱来确定渗碳层的厚度。
这种方法基于不同晶面的衍射强度与晶面间距之间的关系,利用衍射线的宽度,可以计算出渗碳层的深度。
3. 扫描电子显微镜(Scanning Electron Microscope,SEM):SEM可以通过观察样品表面的形貌来分析渗碳或碳氮共渗层。
由于SEM具有高分辨率的特点,可以清晰地观察到渗碳层与基体之间的界面,从而推测出渗碳层的深度。
4. 电子探针微区分析(Electron Probe Micro Analyzer,EPMA):EPMA 是一种通过扫描电子显微镜结合能谱仪来进行元素分析的方法。
通过在样品上进行能量分散分析,可以确定不同元素的分布情况,进而确定渗碳层的深度。
这些方法各有优缺点,并在实际应用中常常结合使用,以提高测量结果的准确性和可靠性。
第二步:验证渗碳或碳氮共渗层深度的方法验证渗碳或碳氮共渗层深度的方法主要采用金属lography、X射线衍射和物理性能测试等方法。
1. 金属lography方法:可以通过显微镜对渗碳或碳氮共渗样品的切面进行观察,利用金相显微镜观察渗碳或碳氮共渗层的形态、连续性和厚度,并与预定渗层深度进行比较,以验证渗碳或碳氮共渗层的深度。
烧结铁基材料渗碳或碳氮共渗层深度的测定及其验证

烧结铁基材料渗碳或碳氮共渗层深度的测定及其验证一、引言烧结铁基材料是一种重要的工程材料,其性能与渗碳或碳氮共渗层的深度密切相关。
准确测定和验证渗碳或碳氮共渗层的深度对于材料性能的改进和优化非常重要。
二、渗层深度测定方法1.金相显微镜法使用金相显微镜对材料进行观察,通过观察渗碳或碳氮共渗层的深度来测定渗层的深度。
2.扫描电镜-能谱分析法利用扫描电镜对材料进行高分辨率的观察,并通过能谱分析来确定渗碳或碳氮共渗层的深度。
3.硬度测试法通过对材料硬度进行测试,分析硬度的变化来确定渗碳或碳氮共渗层的深度。
4.腐蚀试验法将材料进行腐蚀试验,通过观察渗碳或碳氮共渗层在腐蚀后的深度变化来确定渗层的深度。
5.金相显微镜和扫描电镜相结合法通过金相显微镜和扫描电镜相结合的方法来测定渗碳或碳氮共渗层的深度,结合两种方法的优势来提高测定的精度。
6.综合测定法结合以上多种方法进行综合测定,以获得更加准确和可靠的渗层深度数据。
三、渗层深度的验证方法1.金相组织观察观察渗层处的组织结构是否符合渗碳或碳氮共渗的特征,以验证渗层的深度。
2.硬度测试验证通过硬度测试来验证渗层处硬度的变化是否与渗碳或碳氮共渗的预期变化一致,从而验证渗层的深度。
3.电子探针分析利用电子探针对渗层处的元素进行分析,以验证渗层的深度和渗层元素的分布情况。
四、结论通过以上测定和验证方法,能够准确测定和验证烧结铁基材料的渗碳或碳氮共渗层的深度,为材料性能的优化和改进提供了可靠的数据支持。
希望以上研究成果能够为相关工程领域的研究和应用提供参考。
五、应用领域烧结铁基材料的渗碳或碳氮共渗层深度的测定和验证在许多工程领域具有重要的应用价值。
在汽车制造领域,烧结铁基材料被广泛应用于引擎零部件和制动系统。
准确测定和验证渗层深度可以确保这些零部件具有良好的耐磨性和耐腐蚀性,提高汽车的性能和安全性。
在航空航天领域,烧结铁基材料常用于制造飞机发动机和涡轮机零部件。
通过测定和验证渗层深度,可以提高这些零部件的耐高温和高压能力,确保航空器的安全飞行。
20CrMnTi齿轮渗碳和碳氮共渗工艺对比[1]
![20CrMnTi齿轮渗碳和碳氮共渗工艺对比[1]](https://img.taocdn.com/s3/m/9ad47bc95fbfc77da269b14c.png)
60~62 38~40 018~1 6 级 合格 合格 合格 合格
59~62 40~42 018~1 6 级 合格不合格合格 不合格
3 结束语
目前 ,工厂已采用此工艺进行正式生产 ,齿轮变 形问题得到了解决 。而且由此带来明显节能效果 ,每 年可节电 5 万 kW·h, 也减少了原渗碳因温度高 ,电 炉耐热材料寿命短 ,维修频繁的问题 ,降低了成本 ,提 高了效益 。
61~63 40~43 018~1 8 级 合格 合格 合格 不合格
60~63 39~42 018~1 8 级 合格 合格 合格 合格
渗碳 59~62 38~40 018~1 6 级 合格 合格 合格 合格
60~62 40~42 018~1 6 级 合格 合格 合格 合格
60~62 37~40 018~1 6 级 合格 合格不合格 合格
摘 要 :通过 20CrMnTi齿轮渗碳和碳氮共渗工艺对比试验 ,寻求减少齿轮变形 ,提高生产效率的方法 。 关键词 :齿轮 ,渗碳 ,碳氮共渗 中图分类号 :TG15618 + 2 文献标识码 :A 文章编号 :1007-4414 (2000) 04-0060-01
农用车齿轮要求高硬度 ,高耐磨性 ,高冲击韧度 和疲劳强度 ,一直采用 20CrMnTi材料 ,其常规热处理 为渗碳工艺 ,但热处理过程中 ,变形控制是技术难题 , 废品率极高 。我们采用碳氮共渗工艺与原工艺进行 对比试验 ,以寻找减少变形 ,提高生产效率的途径 。
醇 ,甲醇于 400~500 ℃裂解 ,反应如下 :CH3OH →CO +2H2, 气氛中 CO 含量为 33%,H2 为 6617% 。碳浓 度约为 014%, 没有富化作用 ,只起保护作用 。而根 据铁2碳相图 ,在 727 ℃时发生珠光体向奥氏体转变 , 在 750 ℃时奥氏体 中 的 碳 含 量 达 0178%, 在 时 ,通入适量煤油和氨气 ,一方面可以快速提高炉内 碳势 ,缩短炉气回复时间 ;另一方面对齿轮表面进行 碳氮共渗 ,缩短随后的共渗时间 。当温度升到 860 ℃ 即调整煤油和氨气至正常工艺参数 。这样 ,共渗时间 比常规共渗工艺缩短 1h, 故生产效率与原渗碳工艺 相比基本相同 。但由于共渗温度低 ,齿轮变形大大减 小 ,且晶粒得到细化 ,其力学性能提高了 。齿轮共渗 后经热处理表面获得含氮马氏体和少量氮化物 ,比渗 碳热处理后的表层具有更高硬度 ,高耐磨性 。
碳氮共渗和渗碳

碳氮共渗和渗碳
碳氮共渗和渗碳是热处理中常见的两种工艺。
这两种工艺都是为
了在金属材料表面形成一层淬火硬化层,提高材料的硬度和耐磨性。
下面将介绍这两种工艺的基本原理和应用。
碳氮共渗是指同时在金属材料表面扩散一定浓度的碳和氮原子。
在热处理过程中,一定温度下将金属件浸入含有碳和氮的混合气体中,使得碳和氮原子渗入金属表面,与金属原子共同形成一层淬火硬化层。
这种工艺适用于低碳合金钢、工具钢等材料的淬火处理,可以提高材
料的硬度和耐磨性,延长材料的使用寿命。
渗碳是指在金属材料表面扩散一定浓度的碳原子。
在热处理过程中,将金属件浸入含有碳的气体中,使得碳原子渗入金属表面形成一
层淬火硬化层。
渗碳工艺适用于低碳合金钢、铬钼钢等材料的淬火处理。
与碳氮共渗相比,渗碳工艺更加经济实惠,但硬化层的厚度相对
较薄,且耐热性能较差。
在实际应用中,选择碳氮共渗或渗碳工艺需要考虑许多因素,例
如金属种类、加工要求、环境污染等。
因此,发展新型热处理工艺和
选择可持续发展的材料成为了热处理技术研究的重要方向。
总的来说,碳氮共渗和渗碳是热处理工艺中常用的两种硬化工艺,适用范围较广。
在实际应用中,需要根据具体情况选择合适的工艺,
并注重环境保护,推动热处理技术的可持续发展。
- 1、下载文档前请自行甄别文档内容的完整性,平台不提供额外的编辑、内容补充、找答案等附加服务。
- 2、"仅部分预览"的文档,不可在线预览部分如存在完整性等问题,可反馈申请退款(可完整预览的文档不适用该条件!)。
- 3、如文档侵犯您的权益,请联系客服反馈,我们会尽快为您处理(人工客服工作时间:9:00-18:30)。
表面硬度为齿宽中部节圆附近的表面 的硬度。
汽车齿轮表面硬度要求一般为HRC58 -63,我 公 司 的 产 品 要 求 在 HV700 以 上 。表 面硬度是齿轮热处理的一个至关重要的因 素,表面硬度低,耐磨性能差,降低抗接触 应 力 的 能 力, 使 齿 面 容 易 形 成 疲 劳 剥 落 。表 面硬度不合格是常见的热处理缺陷之一, 渗碳及碳氮共渗齿轮硬度不足多由渗碳时 间不足,淬火时脱碳,淬火温度过低,淬火 冷却速度不足,表面残余奥氏体量过多,回 火过度,工件表面不清洁等因素造成的。 1 . 3 碳化物数量及分布
参考文献 [1] 方 向 威 ,等 编 著 . 金 相 检 验 . 机 械 电 子 工
业部理化人员资格培训教材. [2] 李 炯 辉 , 林 德 成 编 著. 金 属 材 料 金 相 图
谱.机械工业出版社.
科技创新导报 S c i e n c e a n d T e c h n o l o g y I n n o v a t i o n H e r a l d
下测至515HV处的垂直距离。 (3)深度的控制 齿轮表面的硬化层深度是使其获得优
良 性 能 的 重 要 参 数 。不 同 用 途 , 不 同 模 数 的 齿 轮 , 其 深 度 亦 不 相 同 。对 同 一 种 齿 轮 而 言,如果层深过厚,会导致齿轮的弯曲疲劳 性能下降,脆性增大,而如果层深过薄,也 会降低弯曲疲劳强度,还会造成齿面早期 疲劳剥落, 甚 至 硬 化 层 被 压 碎 。为 了 使 齿 轮 获得良好的抗弯曲疲劳性能,渗碳层深度 不宜太厚;但在要保证齿面的抗接触疲劳 性 能 时, 则 渗 碳 层 应 以 深 一 些 为 好 。如何合 理地选择渗碳层深度,一般是根据齿轮材 料, 使 用 情 况 和 工 艺 条 件 做 全 面 考 虑 。通 常 是依据齿轮模数的大小进行确定。
目前普遍认为,从兼顾疲劳强度和耐 磨性能出发,将渗碳层表面的碳浓度控制 在0.8%~1.05%范围之内,是比较合理的。
生产中往往由于渗碳浓度过高,造成渗 层中碳化物级别超出要求范围,所以应严 格控制热处理工艺,保证生产出合格产品。 1 . 4 非马氏体组织
国家标准中规定:表面非马氏体组织 最深不得超过0.02mm。
值得提出的是,齿轮表面是否需要有 明显的碳化物存在,目前的意见尚不一致, 一种看法是:由于齿轮在使用时主要是由 于接触应力作用而损坏,而碳化物的存在 容易成为疲劳的起始点,所以主张齿面应
无 明 显 碳 化 物 。另 一 种 看 法 是 : 为 了 保 证 齿 面具有足够的碳浓度和良好的耐磨性,使 齿面上均匀分布着细小颗粒状的碳化物是 必要的。
1 检验与控制 1 . 1 渗碳及碳氮共渗层深
(1)金相法测层深 在1987年以前,国内对渗碳及碳氮共 渗 件 层 深 的 检 验 多 采 用“ 金 相 法 ”, 各 生 产 厂家根据本厂的生产特点及产品的使用情 况,制定各自不同的检验标准和技术要求。 用金相法检测层深,必须是在平衡的 组织状态下进行,即零件必须进行等温退 火 处 理, 再 进 行 检 验 。渗 层 深 度 包 括 过 共 析 层、共 析 层 及 全 部 过 渡 区 域, 即由表面起到 心 部 组 织 为 止 的 总 深 度 。共 析 层 深 度 系 指 由表面起至出现显著的铁素体为止的深 度 。表 面 层 含 碳 量 应 大 于 0 . 8 % 。渗 碳 层 中 过 共析和共析层深度应为渗碳层总深度的 50%~75%。 用金相法检测层深最大的问题是:它 是一种间接的测量方法,不能直接反映零 件 的 使 用 性 能 。如 果 渗 碳 层 深 度 合 格 而 淬 火组织不合格,用金相法测层深是无法检 测到的。 (2)硬度法测层深 随着汽车产业的发展,检测标准与国 际国准的接轨日趋重要,1988年我国等效 采 用 了 I S O 2 6 3 9《 钢 件 渗 碳 淬 火 硬 化 层 深 度 的 测 定 和 校 核 》而 制 定 了 国 家 标 准 G B / T 9 4 5 0《 钢 件 渗 碳 淬 火 有 效 硬 化 层 深 度 的 测 定 和 校 核 》, 即开始使用“ 硬 度 法 ”对渗碳淬 火 件 进 行“ 有 效 硬 化 层 深 度 ”的 检 测 。标 准 规定:从零件表面到维氏硬度值为550HV1 处的垂直距离为零件的淬硬层深度,也叫 有效硬化层深度。 用硬度法检测层深,它的检测结果直接 反映了零件的使用性能,因而更直观有效。 在QC/T262及QCn29018汽车行业标准 中,对汽车渗碳及碳氮共渗齿轮的有效硬 化层深度的检测部位及方法进行了明确规 定:从轮齿表面起,在9.81N(1Kgf)载荷下 测至550HV,也可以在49.031N(5Kgf)载荷
如果在齿面上出现较深的非马氏体组 织,势必造成表面硬度下降,加剧麻点磨损 和疲劳剥落的产生,这是不允许的。
2 小结 齿轮的热处理质量直接关系到齿轮的
使用寿命,即:齿轮的表面及心部的金相组 织缺陷直接影响着齿轮使用性能。
在现生产中,通常是以零件的金相检 验来保证产品的热处理质量,稳定产品的 热 处 理 工 艺, 生 产 合 格 产 品 。同 时 也 可 以 通 过理化分析的方法,根据零件的损坏形态, 原材料的结构缺陷,判定零件损坏的性质, 分析失效原因。
织的检测,可以很好的控制齿轮的热处理质量。
关键词: 金相法 硬度法 硬度 碳化物
中图分类号:TP2
文献标识码:A
文章编号:1674-098X(2011)06(b)-0091-01
齿轮是汽车结构中的重要基础部件, 齿轮质量的优劣,直接影响着汽车产品的 性 能 和 使 用 寿 命 。影 响 汽 车 齿 轮 使 用 寿 命 的 因 素 很 多 , 除 设 计 、选 材 、冷 加 工 及 使 用 条 件 外 、齿 轮 的 热 处 理 质 量 起 着 重 要 的 作 用 。渗 碳 及 碳 氮 共 渗 齿 轮 热 处 理 质 量 的 好 坏 是 通 过 有 效 硬 化 层 深 度 、硬 度 及 金 相 组 织来鉴别的,因此必须对齿轮热处理后的 质量进行准确的检验及严格的控制。
根 据 渗 层 中 碳 化 物 的 大 小 、形 状 、数 量 及分布情况分为8级,评定时按QC/T262及 QCn29018中的碳化物级别图进行,常啮合 齿轮1-5级合格,换档齿轮1-4级合格,检 测部位以齿顶角及工作面为准。
渗 层 中 碳 化 物 的 数 量 、形 状 以 及 分 布 , 直接影响着齿轮的使用寿命,块状呈断续 网状或者网状分布的碳化物,它们破坏了 金属基体的连续性,起着造成应力集中的 缺口作用, 并 可 能 成 为 裂 纹 源 。在 齿 轮 使 用 过程中,导致牙齿折断,齿端崩损,加速齿 面疲劳麻点的形成11 NO.17
Science and Technology Innovation Herald
渗碳及碳氮共渗齿轮热处理质量检验综述
赵美惠 ( 山东上汽汽车变速器有限公司 山东省烟台市 2 6 5 5 0 0 )
摘 要; 齿轮的热处理质量直接关系到齿轮的使用寿命, 而齿轮的热处理工艺通常有二种: 渗碳及碳氮共渗, 通用对层深、硬度及金相组
所谓非马氏体组织,通常是指在渗碳 或碳氮共渗层中最表面出现的黑色组织或 黑色网络组织,这种组织只有极薄的一层, 约为0.008~0.04mm,这种黑色组织一般为 屈氏体组织。
零件在渗碳气氛中,由于氧原子在其 表面上富集,并沿着晶界向里扩散,致使钢 中 的 铬 、锰 、硅 等 元 素 发 生 内 氧 化 , 同 时 又 因为渗入的碳与其它合金元素相互作用, 生成合金碳化物,故而造成了在氧化物或 碳化物附近区域奥氏体中合金元素的贫化 现象,在淬火过程中,零件的表面区形成了 沿晶界分布的屈氏体组织,轻者呈网状,重 者则连成片。
91