20CrMnTi齿轮渗碳和碳氮共渗工艺对比[1]
20CrMnTi钢渗氮、低温渗碳淬火复合热处理

20CrMnTi钢渗氮、低温渗碳淬火复合热处理
王滨生;孙晓滨
【期刊名称】《金属热处理》
【年(卷),期】1998()3
【摘要】20CrMnTi钢渗氮、低温渗碳淬火复合热处理哈尔滨量具刃具厂(哈尔宾150040)王滨生孙晓滨NitridingandLowTemperatureCarburizingofSteel20CrMnTiWangBinsheng,SunXiaobin20...
【总页数】2页(P4-5)
【关键词】钢;渗氮;低温渗碳淬火;复合热处理
【作者】王滨生;孙晓滨
【作者单位】哈尔滨量具刃具厂
【正文语种】中文
【中图分类】TG161
【相关文献】
1.碳氮共渗与磁化电解渗硫复合处理后20CrMnTi钢的摩擦磨损性能 [J], 黄友庭;陈文哲
2.不锈钢低温渗氮/渗碳S相渗层技术的研究进展 [J], 孙金全;崔洪芝;赫庆坤;刘赞;陶鹏;阎璐
3.GCr15钢的渗氮淬火复合热处理 [J], 王滨生;常晓智
4.9SiCr钢渗氮淬火复合热处理 [J], 王滨生;冯明旺
5.20CrMnTi钢渗碳和碳氮共渗后耐磨性能的研究 [J], 李全贵
因版权原因,仅展示原文概要,查看原文内容请购买。
渗碳及碳氮共渗齿轮热处理质量检验综述

渗碳及碳氮共渗齿轮热处理质量检验综述作者:赵美惠来源:《科技创新导报》2011年第17期摘要;齿轮的热处理质量直接关系到齿轮的使用寿命,而齿轮的热处理工艺通常有二种:渗碳及碳氮共渗,通用对层深、硬度及金相组织的检测,可以很好的控制齿轮的热处理质量。
关键词:金相法硬度法硬度碳化物中图分类号:TP2 文献标识码:A 文章编号:1674-098X(2011)06(b)-0091-01齿轮是汽车结构中的重要基础部件,齿轮质量的优劣,直接影响着汽车产品的性能和使用寿命。
影响汽车齿轮使用寿命的因素很多,除设计、选材、冷加工及使用条件外、齿轮的热处理质量起着重要的作用。
渗碳及碳氮共渗齿轮热处理质量的好坏是通过有效硬化层深度、硬度及金相组织来鉴别的,因此必须对齿轮热处理后的质量进行准确的检验及严格的控制。
1 检验与控制1.1 渗碳及碳氮共渗层深(1)金相法测层深在1987年以前,国内对渗碳及碳氮共渗件层深的检验多采用“金相法”,各生产厂家根据本厂的生产特点及产品的使用情况,制定各自不同的检验标准和技术要求。
用金相法检测层深,必须是在平衡的组织状态下进行,即零件必须进行等温退火处理,再进行检验。
渗层深度包括过共析层、共析层及全部过渡区域,即由表面起到心部组织为止的总深度。
共析层深度系指由表面起至出现显著的铁素体为止的深度。
表面层含碳量应大于0.8%。
渗碳层中过共析和共析层深度应为渗碳层总深度的50%~75%。
用金相法检测层深最大的问题是:它是一种间接的测量方法,不能直接反映零件的使用性能。
如果渗碳层深度合格而淬火组织不合格,用金相法测层深是无法检测到的。
(2)硬度法测层深随着汽车产业的发展,检测标准与国际国准的接轨日趋重要,1988年我国等效采用了ISO2639《钢件渗碳淬火硬化层深度的测定和校核》而制定了国家标准GB/T9450《钢件渗碳淬火有效硬化层深度的测定和校核》,即开始使用“硬度法”对渗碳淬火件进行“有效硬化层深度”的检测。
20CrMnTi热处理工艺
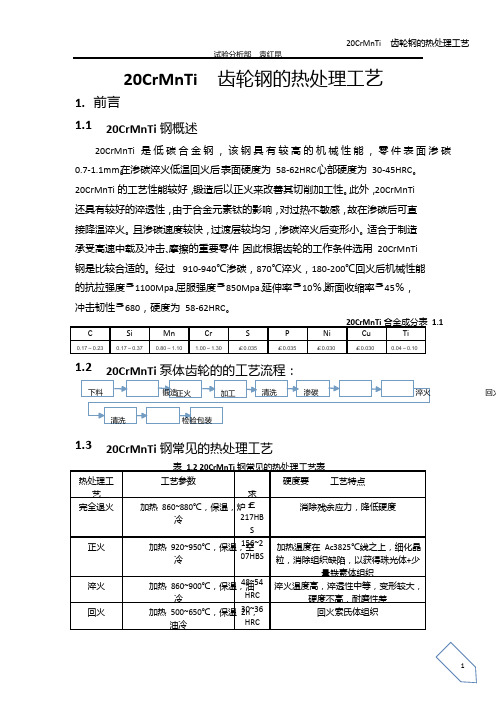
20CrMnTi 齿轮钢的热处理工艺1. 前言1.1 20CrMnTi 钢概述20CrMnTi 是低碳合金钢,该钢具有较高的机械性能,零件表面渗碳 0.7-1.1mm 。
在渗碳淬火低温回火后,表面硬度为58-62HRC ,心部硬度为30-45HRC 。
20CrMnTi 的工艺性能较好,锻造后以正火来改善其切削加工性。
此外,20CrMnTi 还具有较好的淬透性,由于合金元素钛的影响,对过热不敏感,故在渗碳后可直 接降温淬火。
且渗碳速度较快,过渡层较均匀,渗碳淬火后变形小。
适合于制造 承受高速中载及冲击、摩擦的重要零件,因此根据齿轮的工作条件选用20CrMnTi 钢是比较合适的。
经过910-940℃渗碳,870℃淬火,180-200℃回火后机械性能 的抗拉强度³1100Mpa 、屈服强度³850Mpa 、延伸率³10%、断面收缩率³45%, 冲击韧性³680,硬度为58-62HRC 。
20CrMnTi 合金成分表1.1 C Si Mn Cr S P Ni Cu Ti0.17~0.230.17~0.370.80~1.101.00~1.30£0.035£0.035£0.030£0.0300.04~0.101.2 20CrMnTi 泵体齿轮的的工艺流程:1.3 20CrMnTi 钢常见的热处理工艺表1.2 20CrMnTi 钢常见的热处理工艺表热处理工艺 工艺参数硬度要求工艺特点完全退火加热860~880℃,保温,炉 冷£217HB S消除残余应力,降低硬度正火加热920~950℃,保温,空 冷156~2 07HBS 加热温度在Ac3825℃线之上,细化晶 粒,消除组织缺陷,以获得珠光体+少 量铁素体组织淬火 加热860~900℃,保温,油 冷 48~54 HRC 淬火温度高,淬透性中等,变形较大, 硬度不高,耐磨性差回火加热500~650℃,保温2h , 油冷30~36HRC 回火索氏体组织下料 锻造 正火清洗淬火回火加工渗碳包装清洗检验气体渗碳加热900~920℃,以0.15~0.2mm/h计保温时间加热温度不超过920℃,以避免晶粒长大渗碳后淬火与回火淬火:加热820~850℃,保温后油冷60~63HRC心部保持良好韧性的同时,表层获得高的强度、硬度、耐磨性与耐蚀性回火:加热180~200℃,保温2h,空冷表:56~62HRC心:35~40HRC气体碳氮共渗共渗温度840~860℃,出炉油冷60~65HRC心部保持良好韧性的同时,表层获得高的强度、硬度、耐磨性与耐蚀性回火温度160~180℃,出炉空冷表:58~62HRC心:35~40HRC固体渗硼渗硼温度900℃,保温4h,油冷(渗硼剂:85%SiC+10%B4C+5%KBF4) 。
渗氮 渗碳 碳氮共渗

渗氮渗碳碳氮共渗碳氮共渗是一种常见的表面处理技术,通过渗碳和渗氮来改善材料的硬度和耐磨性。
本文将对渗氮、渗碳和碳氮共渗的原理、应用和工艺进行详细介绍。
一、渗氮渗氮是将氮原子渗入材料表面形成氮化物层的过程。
氮原子通过高温处理和氮气氛的作用,渗透到材料表面并与材料中的元素反应,形成硬质氮化物层。
这一薄层氮化物层不仅能提高材料的硬度和抗磨损性能,还能改善材料的耐腐蚀性。
渗氮的主要应用领域包括机械制造、汽车工业、航空航天等。
在机械制造中,渗氮可以增加零件的硬度和耐磨性,延长使用寿命;在汽车工业中,渗氮可以提高引擎零件的耐磨性和抗腐蚀性能;在航空航天领域,渗氮可以增强航空发动机部件的耐高温和耐磨性能。
渗氮的工艺流程一般包括清洗件表面、装配件和炉内预处理、渗氮和回火处理等步骤。
渗氮一般采用封闭式和开放式两种方式进行,根据具体应用需求可以选择合适的渗氮工艺。
二、渗碳渗碳是将碳原子渗入材料表面形成碳化物层的过程。
碳原子通过高温处理和含有碳气体的氛围,渗透到材料表面并在表面与材料中的元素反应,形成硬质碳化物层。
渗碳技术不仅能提升材料的硬度和耐磨性,还可以改善材料的断裂韧性和抗腐蚀性。
渗碳广泛应用于机械零件、钢铁制品等领域。
渗碳后的材料表面硬度高、耐磨性好,适用于制作耐磨零件,如轴承、齿轮等;同时碳化层的外表面与空气隔绝,降低了材料的腐蚀速率,提高了零件的使用寿命。
渗碳的工艺流程包括预处理、渗碳、淬火和回火等。
渗碳一般采用气体渗碳和液体渗碳两种方式进行,具体工艺参数可以根据材料的要求进行选择。
三、碳氮共渗碳氮共渗是将碳原子和氮原子同时渗入材料表面形成碳氮共渗层的过程。
碳氮共渗通过碳氮共渗剂和高温处理,使碳原子和氮原子分别与材料中的元素发生反应,形成硬质碳氮化物层。
碳氮共渗能够同时获得渗碳和渗氮的特性,提高材料的硬度、耐磨性和抗腐蚀性。
碳氮共渗广泛应用于汽车工业、航空航天等领域。
在汽车工业中,碳氮共渗可以提高零部件的硬度和耐磨性,同时还可以提高零部件的抗磨损能力和抗腐蚀性;在航空航天领域,碳氮共渗可以增强发动机部件的抗高温性能和抗腐蚀能力。
常用渗碳(碳氮共渗)钢
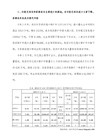
零件表面要求耐磨,心部又要求有良好的强韧性,常采用20Cr、20CrMnTi钢等淬透性较好的低合金渗碳(碳氮共渗)钢。如长期在摩擦条件下工作,承受一定交变负荷和冲击负荷的活塞销、销轴等常采用20Cr钢渗碳(碳氮共渗)淬火;对交变负荷重、冲击较大的齿轮(截面≤30~35 mm),则采用20CrMnTi钢渗碳(碳氮共渗)淬火。20CrMnTi钢渗碳(碳氮共渗)淬火晶粒细小,淬透性好,且热处理变形小,可保证心部得到以低碳马氏体为主体的组织,心部强度高(HRC38~43),同时又有较高的塑韧性(αk≥100 J/cm2);对负荷更重的大截面(工件壁厚≥35~40 mm)的渗碳(碳氮共渗)齿轮,可同重型拖拉机、汽车一样,采用30CrMnTi钢,保证心部较高强度,且心部与渗碳(碳氮共渗)层过渡区的强度也较高。
渗碳(碳氮共渗)钢选材也以淬透性为主,心部要求较高强韧性,一般选用低碳合金钢,否则选用低碳钢,渗碳(碳氮共渗)是充分发挥材料的潜力,所以要尽量选用符合零件性能要求的材料,以提高经济效益。
低碳钢渗碳(碳氮共渗)淬火与中碳钢调质(正火)高频表面淬火,虽二者都是提高零件表面硬度、耐磨性及疲劳强度,但使用时应有区分。一般讲,低碳钢淬火主要用于σb=700~1000 MPa的较大负荷及冲击较大、中低速的齿轮,花键轴类等零件;而中碳钢高频表面淬火则用于相对负荷较轻(400~700 MPa),冲击较小的齿轮、轴类等零件。因中碳马氏体的高频淬火层的耐磨性及调质心部的强韧性均较低碳钢渗碳(碳氮共渗)淬火的渗碳(碳氮共渗)层及低碳马氏体心部的为低。此外,受高频淬火工艺的影响,较大模数(m=5~6)重载齿轮及锥形伞齿轮,齿面高频淬火层沿齿廓分布而无法完成;尤以大锥齿轮两弧齿面硬度差值大,使用中常发生断齿等过早期损坏现象,影响正常运行。对此,应考虑采用20CrMnTi钢渗碳(碳氮共渗)淬火取代40Cr钢调质与高频淬火,虽然制造成本高了些,但一顶几用,还是利大于弊。
20CrMnTi材料性能和热处理工艺

20CrMnTi材料性能和热处理工艺一、20CrMnTi材料分析20CrMnTi是低碳合金钢,该钢具有较高的机械性能,零件表面渗碳0.7-1.1mm。
在渗碳淬火低温回火后,表面硬度为58-62HRC,心部硬度为30-45HRC。
20CrMnTi的工艺性能较好,锻造后以正火来改善其切削加工性。
此外,20CrMnTi还具有较好的淬透性,由于合金元素钛的影响,对过热不敏感,故在渗碳后可直接降温淬火。
且渗碳速度较快,过渡层较均匀,渗碳淬火后变形小。
适合于制造承受高速中载及冲击、摩擦的重要零件,因此根据齿轮的工作条件选用20CrMnTi钢是比较合适的。
经过910-940℃渗碳,870℃淬火,180-200℃回火后机械性能的抗拉强度≥1100Mpa、屈服强度≥850Mpa、延伸率≥10%、断面收缩率≥45%,冲击韧性≥680,硬度为58-62HRC。
20CrMnTi 合金成分表如下:二、20CrMnTi钢的特性⑴、20CrMnTi钢中加入Cr、Mn元素,主要是提高钢的淬透性。
⑵、20CrMnTi钢中加入Ti元素主要是为了细化晶粒。
⑶、20CrMnTi钢淬火加热时,Cr、Mn、Si元素完全固溶于奥氏体中,提高钢的淬透性。
Ti元素以碳化TiC形式钉扎于奥氏体晶界,阻止奥氏体晶粒的长大。
⑷、20CrMnTi钢淬火后,Cr、Mn、Si元素固溶强化基体组织,并改善基体组织的回火稳定性。
⑸、20CrMnTi钢低温回火时,部分Cr、Mn元素从基体组织中扩散到析出的渗碳体Fe3C中,形成合金渗碳体(Cr、Mn、Fe)3C,改善其硬度。
合金渗碳体(Cr、Mn、Fe)3C与碳化物TiC同基体组织一起共同作用,使钢产生较高的强度、硬度与耐磨性,同时保持良好的韧性。
⑹、20CrMnTi钢渗碳或碳氮共渗后碳层均匀,加工和热处理工艺性能优良,不易出现过热,渗碳后可直接淬火,淬火变形小。
⑺、20CrMnTi钢正火后切削加工性能优良,相对加工性能为75%,表面粗糙度低。
20CrMnTi钢真空碳氮复合渗工艺与渗层特性研究
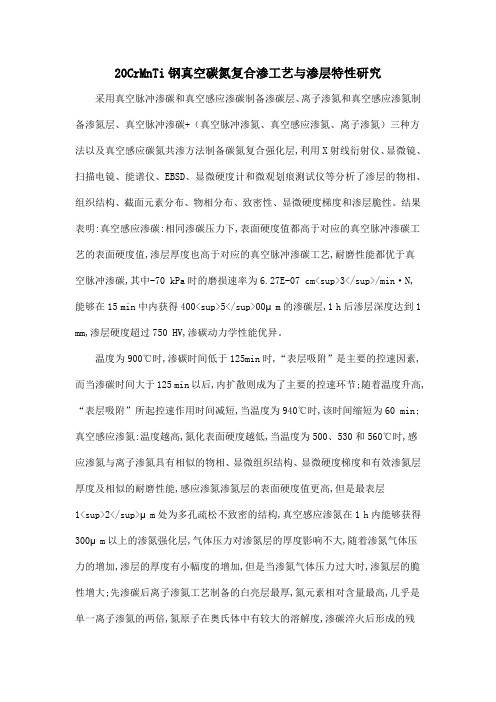
20CrMnTi钢真空碳氮复合渗工艺与渗层特性研究采用真空脉冲渗碳和真空感应渗碳制备渗碳层、离子渗氮和真空感应渗氮制备渗氮层、真空脉冲渗碳+(真空脉冲渗氮、真空感应渗氮、离子渗氮)三种方法以及真空感应碳氮共渗方法制备碳氮复合强化层,利用X射线衍射仪、显微镜、扫描电镜、能谱仪、EBSD、显微硬度计和微观划痕测试仪等分析了渗层的物相、组织结构、截面元素分布、物相分布、致密性、显微硬度梯度和渗层脆性。
结果表明:真空感应渗碳:相同渗碳压力下,表面硬度值都高于对应的真空脉冲渗碳工艺的表面硬度值,渗层厚度也高于对应的真空脉冲渗碳工艺,耐磨性能都优于真空脉冲渗碳,其中-70 kPa时的磨损速率为6.27E-07 cm<sup>3</sup>/min·N,能够在15 min中内获得400<sup>5</sup>00μm的渗碳层,1 h后渗层深度达到1 mm,渗层硬度超过750 HV,渗碳动力学性能优异。
温度为900℃时,渗碳时间低于125min时,“表层吸附”是主要的控速因素,而当渗碳时间大于125 min以后,内扩散则成为了主要的控速环节;随着温度升高,“表层吸附”所起控速作用时间减短,当温度为940℃时,该时间缩短为60 min;真空感应渗氮:温度越高,氮化表面硬度越低,当温度为500、530和560℃时,感应渗氮与离子渗氮具有相似的物相、显微组织结构、显微硬度梯度和有效渗氮层厚度及相似的耐磨性能,感应渗氮渗氮层的表面硬度值更高,但是最表层1<sup>2</sup>μm处为多孔疏松不致密的结构,真空感应渗氮在1 h内能够获得300μm以上的渗氮强化层,气体压力对渗氮层的厚度影响不大,随着渗氮气体压力的增加,渗层的厚度有小幅度的增加,但是当渗氮气体压力过大时,渗氮层的脆性增大;先渗碳后离子渗氮工艺制备的白亮层最厚,氮元素相对含量最高,几乎是单一离子渗氮的两倍,氮原子在奥氏体中有较大的溶解度,渗碳淬火后形成的残留奥氏体有助于活性氮原子的吸附,马氏体形成时的晶格畸变产生许多空隙,有利于氮原子的扩散,使其具有更厚的渗层,白亮层主要由碳化物Fe<sub>4</sub>N强化,弥补了单一渗碳后表面硬度较低的不足;不同气体压力的真空感应碳氮共渗都有效地提高了20CrMnTi钢的表面摩擦性能,其中当压力为-25 kPa时,耐磨性能最好,磨损速率最低,磨损速率为5.32E-07cm<sup>3</sup>/min·N。
最全的渗碳和渗氮区别整理表格
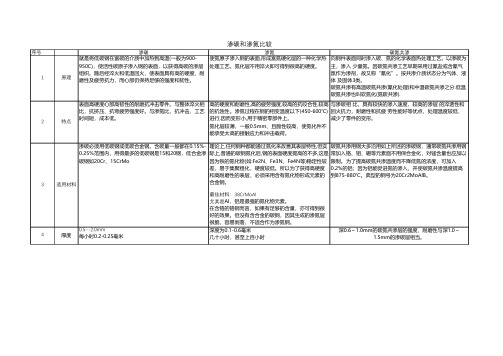
序号渗碳和渗氮比较12特点表面高硬度心部高韧性的耐磨抗冲击零件。
与整体淬火相比,抗挤压、抗弯疲劳强度好。
与渗氮比,抗冲击,工艺时间短,成本低。
高的硬度和耐磨性,高的疲劳强度,较高的抗咬合性,较高的抗蚀性。
渗氮过程在钢的相变温度以下(450-600℃)进行,因而变形小,用于精密零部件上。
氮化层较薄,一般0.5mm、且脆性较高,使氮化件不能承受太高的接触应力和冲击载荷。
渗碳渗氮就是将低碳钢在富碳的介质中加热到高温(一般为900-950C),使活性碳原子渗入钢的表面,以获得高碳的渗层组织。
随后经淬火和低温回火,使表面具有高的硬度、耐磨性及疲劳抗力,而心部仍保持足够的强度和韧性。
使氮原子渗入钢的表面,形成富氮硬化层的一种化学热处理工艺。
氮化层不用淬火即可得到很高的硬度。
原理碳氮共渗向钢件表面同时渗入碳、氮的化学表面热处理工艺。
以渗碳为主,渗入 少量氮。
因碳氮共渗工艺早期采用过氰盐或含氰气氛作为渗剂,故又称“氰化”。
按共渗介质状态分为气体、液体 及固体3类。
碳氮共渗有高温碳氮共渗(氰化处理)和中温碳氮共渗之分.低温碳氮共渗也叫软氮化(氮碳共渗).与渗碳相 比,具有较快的渗入速度,较高的渗层 的淬透性和回火抗力,耐磨性和抗疲 劳性能好等优点,处理温度较低,减少了零件的变形。
3适用材料渗碳必须用低碳钢或低碳合金钢。
含碳量一般都在0.15%-0.25%范围内,用得最多的低碳钢是15和20钢,低合金渗碳钢如20Cr、15CrMo理论上,任何钢种都能通过氮化来改善其表层特性,但实际上,普通的碳钢氮化后,钢的表面硬度提高的不多,这是因为铁的氮化物(如:Fe2N、Fe3N、Fe4N等)稳定性较差,易于集聚粗化,硬度较低。
所以为了获得高硬度和高耐磨性的表层,必须采用含有氮化物形成元素的合金钢。
最佳材料:38CrMoAl尤其是AI,铝是最强的氮化物元素。
在含铬的铬钢而言,如果有足够的含量,亦可得到很好的效果。
但没有含合金的碳钢,因其生成的渗氮层很脆,容易剥落,不适合作为渗氮钢。
- 1、下载文档前请自行甄别文档内容的完整性,平台不提供额外的编辑、内容补充、找答案等附加服务。
- 2、"仅部分预览"的文档,不可在线预览部分如存在完整性等问题,可反馈申请退款(可完整预览的文档不适用该条件!)。
- 3、如文档侵犯您的权益,请联系客服反馈,我们会尽快为您处理(人工客服工作时间:9:00-18:30)。
试验设备 RJJ-90-9T 井式渗碳炉 。试验材料 , 为工厂同一批实际生产的齿轮零件 。工艺流程 :下料 —锻造 —正火 —渗碳 (碳氮共渗) —淬火 —回火 —清 洗 。钢坯齿轮经正火后 ,带状组织 3 级 ,晶粒度 9 级 。 试验工艺分别见图 1 和图 2 。
图 1 20CrMnTi渗碳工艺
61~63 40~43 018~1 8 级 合格 合格 合格 不合格
60~63 39~42 018~1 8 级 合格 合格 合格 合格
渗碳 59~62 38~40 018~1 6 级 合格 合格 合格 合格
60~62 40~42 018~1 6 级 合格 合格 合格 合格
60~62 37~40 018~1 6 级 合格 合格不合格 合格
Ξ 收稿日期 :2000-07-17 作者简介 :余华俐 (1966- ) 湖南常德人 现主要从事机械工程材料 、模具的教学工作 1
· 06·
60~62 38~40 018~1 6 级 合格 合格 合格 合格
59~62 40~42 018~1 6 级 合格不合格合格 不合格
3 结束语
目前 ,工厂已采用此工艺进行正式生产 ,齿轮变 形问题得到了解决 。而且由此带来明显节能效果 ,每 年可节电 5 万 kW·h, 也减少了原渗碳因温度高 ,电 炉耐热材料寿命短 ,维修频繁的问题 ,降低了成本 ,提 高了效益 。
图 2 20CrMnTi碳氮共渗工艺
2 试验结果及分析
在两炉经不同工艺处理的齿轮中 ,随机各拿出 5 个来进行硬度 ,变形量等技术参数检测结果见表 1 。
可见 ,齿轮经碳氮共渗后 ,性能及技术参数均优 于原渗碳工艺 。在碳氮共渗过程中 ,齿轮入炉温度 860 ℃,入炉后降为 550 ℃左右 ,升温 750 ℃约需 45~ 50min,750 ℃升至 860 ℃约需 40min。在升温中只通甲
醇 ,甲醇于 400~500 ℃裂解 ,反应如下 :CH3OH →CO +2H2, 气氛中 CO 含量为 33%,H2 为 6617% 。碳浓 度约为 014%, 没有富化作用 ,只起保护作用 。而根 据铁2碳相图 ,在 727 ℃时发生珠光体向奥氏体转变 , 在 750 ℃时奥氏体 中 的 碳 含 量 达 0178%, 在 750 ~ 860 ℃的过程中 ,齿轮表面已有较强的吸碳能力 。此 时 ,通入适量煤油和氨气 ,一方面可以快速提高炉内 碳势 ,缩短炉气回复时间 ;另一方面对齿轮表面进行 碳氮共渗 ,缩短随后的共渗时间 。当温度升到 860 ℃ 即调整煤油和氨气至正常工艺参数 。这样 ,共渗时间 比常规共渗工艺缩短 1h, 故生产效率与原渗碳工艺 相比基本相同 。但由于共渗温度低 ,齿轮变形大大减 小 ,且晶粒得到细化 ,其力学性能提高了 。齿轮共渗 后经热处理表面获得含氮马氏体和少量氮化物 ,比渗 碳热处理后的表层具有更高硬度 ,高耐磨性 。
表 1 20CrMnTi齿轮渗碳和碳氮共渗性能对比
工法线
表面硬 心部硬 渗层深晶粒
齿圈径
孔径 花键
长度变
度 HRC 度 HRC 度 mm 度
向跳动 动工差
61~63 40~43 018~1 8 级 合格 合格 合格 合格
碳氮 62~64 42~45 018~1 8 级 合格 合格 合格 合格
共渗 61~63 41~44 018~1 8 级 合格 合格 合格 合格
摘 要 :通过 20CrMnTi齿轮渗碳和碳氮共渗工艺对比试验 ,寻求减少齿轮变形 ,提高生产效率的方法 。 关键词 :齿轮 ,渗碳 ,碳氮共渗 中图分类号 :TG15618 + 2 文献标识码 :A 文章编号 :1007-4414 (2000) 04-0060-01
农用车齿轮要求高硬度 ,高耐磨性 ,高冲击韧度 和疲劳强度 ,一直采用 20CrMnTi材料 ,其常规热处理 为渗碳工艺 ,但热处理过程中 ,变形控制是技术难题 , 废品率极高 。我们采用碳氮共渗工艺与原工艺进行 对比试验 ,以寻找减少变形 ,提高生产效率的途径 。
Vol13 No4 2000212
机械研究与应用
第
MECHANICALRESEARCH&APPLICATION
13 卷 第 4 2000 年 12
期 月
工艺改进
20CrMnTi 齿轮渗碳和碳氮共渗工艺对比Ξ
余华俐1 ,杨宾崇2
(1 兰州工业高等专科学校 机械工程系 ,甘肃 兰州 730050;2 兰拖集团有限责任公司 ,甘肃 兰州 730050)