氮碳共渗与碳氮共渗的区别
渗碳与渗氮的区别

钢的渗碳和渗氮钢的渗碳---就是将低碳钢在富碳的介质中加热到高温(一般为900--950C),使活性碳原子渗入钢的表面,以获得高碳的渗层组织。
随后经淬火和低温回火,使表面具有高的硬度、耐磨性及疲劳抗力,而心部仍保持足够的强度和韧性。
渗碳钢的化学成分特点(1)渗碳钢的含碳量一般都在0.15--0.25%范围内,对于重载的渗碳体,可以提高到0.25--0.30%,以使心部在淬火及低温回火后仍具有足够的塑性和韧性。
但含碳量不能太低,否则就不能保证一定的强度。
(2)合金元素在渗碳钢中的作用是提高淬透性,细化晶粒,强化固溶体,影响渗层中的含碳量、渗层厚度及组织。
在渗碳钢中通常加入的合金元素有锰、铬、镍、钼、钨、钒、硼等。
常用渗碳钢可以分碳素渗碳钢和合金渗碳钢两大类。
(1)碳素渗碳钢中,用得最多的是15和20钢,它们经渗碳和热处理后表面硬度可达56--62HRC。
但由于淬透性较低,只适用于心部强度要求不高、受力小、承受磨损的小型零件,如轴套、链条等。
(2)低合金渗碳钢如20Cr、20Cr2MnVB、20Mn2TiB等,其渗透性和心部强度均较碳素渗碳钢高,可用于制造一般机械中的较为重要的渗碳件,如汽车、拖拉机中的齿轮、活塞销等。
(3)中合金渗碳钢如20Cr2Ni4、18Cr2N4W、15Si3MoWV等,由于具有很高的淬透性和较高的强度及韧性,主要用以制造截面较大、承载较重、受力复杂的零件,如航空发动机的齿轮、轴等。
固体渗碳;液体渗碳;气体渗碳---渗碳温度为900--950C,表面层w(碳)为0.8--1.2%,层深为0.5--2.0mm。
渗碳后的热处理---渗碳工件实际上应看作是由一种表面与中心含量相差悬殊码复合材料。
渗碳只能改变工件表面的含碳量,而其表面以及心部的最终强化则必须经过适当的热处理才能实现。
渗碳后的工件均需进行淬火和低温回火。
淬火的目的是使在表面形成高碳马氏体或高碳马氏体和细粒状碳化物组织。
钢的碳氮共渗5-4讲解

5.4 钢的碳氮共渗1:定义:在钢的表面同时渗入碳和氮的化学热处理工艺称为碳氮共渗。
2:氰化:碳氮共渗可以在气体介质中进行,也可在液体介质中进行.因为液体介质的主要成分是氰盐,故液体碳氮共渗又称为氰化。
3:目的:对低碳结构钢、中碳结构钢以及不锈钢等,为了提高其表面硬度、耐磨性及疲劳强度,进行820—850℃碳氮共渗。
中碳调质钢在570—600℃温度进行碳渗共渗,可提高其耐磨性及疲劳强度,而高速钢在550—560℃碳氮共渗的目的是进一步提高其表面硬度、耐磨性及热稳定性.4:软氮化:根据共渗温度不同,可以把碳氮共渗分为高温(900—950℃)、中温(700—880℃)及低温三种。
其中低温碳氮共渗,最初在中碳钢中应用,主要是提高其耐磨性及疲劳强度,而硬度提高不多(在碳素钢中),故又谓之软氮化。
一、碳和氮同时在钢中扩散的特点同时在钢中渗入碳和氮,如前所述,至少已是三元状态图的问题,故应以Fe-N-C三元状态图为依据。
但目前还很不完善,还不能完全根据三元状态图来进行讨论。
在这里重要讲述一些C、N二元共渗的一些特点。
1.共渗温度不同,共渗层中碳氮含量不同。
氮含量随着共渗温度的提高而降低,而碳含量则起先增加,至一定温度后反而降低。
渗剂增碳能力不同,达到最大碳含量的温度也不同。
2.碳、氮共渗时碳氮元素相互对钢中溶解度及扩散深度有影响。
由于N使y相区扩大,且Ac3点下降,因而能使钢在更低的温度增碳。
氮渗入浓度过高,在表面形成碳氮化合物相,因而氮又障碍着碳的扩散。
碳降低氮在、相中的扩散系数,所以碳减缓氮的扩散。
3.碳氮共渗过程中碳对氮的吸附有影响.碳氮共渗过程可分成两个阶段:第一阶段共渗时间较短(1—3小时),碳和氮在钢中的渗入情况相同;若延长共渗时间,出现第二阶段,此时碳继续渗入而氮不仅不从介质中吸收,反而使渗层表面部分氮原子进入到气体介质中去,表面脱氮,分析证明,这时共渗介质成分有变化,可见是由于氮和碳在钢中相互作用的结果。
表面化学热处理技术

化学热处理渗碳:为了获得高硬度、高耐磨的表面及强韧的心部,渗碳后必须进行淬火加低温回火处理。
按渗碳介质可分为:气体渗碳、液体渗碳、固体渗碳。
渗氮:①渗氮层具有高硬度、高耐磨性;②渗氮层比热容打,在钢件表面形成压应力层可显著提高耐疲劳性能,渗氮层的耐疲劳性优于渗碳层;③渗氮层表面有化学稳定性高的ε相,能显著提高耐腐蚀性。
渗氮能形成性能优越的渗氮层,但由于工艺时间太长,使得生产率太低,成本高,应尽量少采用。
渗氮一般用在强烈磨损、耐疲劳性要求非常高的零件,有的场合是除要求机械性能外还要求耐腐蚀的零件。
碳氮共渗(俗称“氰化”):按工艺温度分:低温碳氮共渗(520-580℃),工艺温度低,共渗过程是以氮原子为主、碳原子为辅的渗入过程,俗称“软氮化”;中温碳氮共渗(780-880℃);高温碳氮共渗(880-930℃)。
优点:①与渗碳相比处理温度低,渗后可直接淬火,工艺简单,晶粒不易长大,变形裂倾向小,能源消耗少,共渗层的疲劳性和抗回火稳定性好;②与渗氮相比,生产周期大大缩短,对材料适用广。
氮碳共渗:氮碳共渗起源于西德,是在液体渗氮基础上发展起来的。
早期氮碳共渗是在含氰化物的盐浴中进行的。
由于处理温度低,一般在500-600℃,过程以渗氮为主,渗碳为辅,所以又称为“软氮化”。
氮碳共渗工艺的优点如下:①氮碳共渗有优良的性能:渗层硬度高,碳钢氮碳共渗处理后渗层硬度可达HV570-680;渗氮钢、高速钢、模具钢共渗后硬度可达HV850-1200;脆性低,有优良的耐磨性、耐疲劳性、抗咬合性和耐腐蚀性。
②工艺温度低,且不淬火,工件变形小。
③处理时间短,经济性好。
④设备简单,工艺易掌握。
存在问题是:渗层浅,承受重载荷零件不宜采用。
渗硼:渗硼是一种有效地表面硬化工艺。
将工件置于能产生活性硼的介质中,经过加热、保温,使硼原子渗入工件表面形成硼化物层的过程称为渗硼。
金属零件渗硼后,表面形成的硼化物(FeB、Fe2B、TiB2、ZrB2、VB2、CrB2)及碳化硼等化合物的硬度极高,热稳定性。
金属热处理中渗氮工艺常识

金属热处理中渗氮工艺常识金属热处理中的各种渗氮工艺使氮原子渗入钢铁工件表层内的化学热处理工艺;传统的气体渗氮是把工件放入密封容器中﹐通以流动的氨气并加热﹐保温较长时间后﹐氨气热分解產生活性氮原子﹐不断吸附到工件表面﹐并扩散渗入工件表层内﹐从而改变表层的化学成分和组织﹐获得优良的表面性能。
如果在渗氮过程中同时渗入碳以促进氮的扩散﹐则称为氮碳共渗。
钢铁渗氮的研究始於20世纪初﹐20年代以后获得工业应用。
最初的气体渗氮﹐仅限於含铬﹑铝的钢﹐后来才扩大到其他钢种。
从70年{BANNED}始﹐渗氮从理论到工艺都得到迅速发展并日趋完善﹐适用的材料和工件也日益扩大﹐成为重要的化学热处理工艺之一。
渗入钢中的氮一方面由表及裡与铁形成不同含氮量的氮化铁﹐一方面与钢中的合金元素结合形成各种合金氮化物﹐特别是氮化铝﹑氮化铬。
这些氮化物具有很高的硬度﹑热稳定性和很高的弥散度﹐因而可使渗氮后的钢件得到高的表面硬度﹑耐磨性﹑疲劳强度﹑抗咬合性﹑抗大气和过热蒸汽腐蚀能力﹑抗回火软化能力﹐并降低缺口敏感性。
与渗碳工艺相比﹐渗氮温度比较低﹐因而畸变小﹐但由於心部硬度较低﹐渗层也较浅﹐一般只能满足承受轻﹑中等载荷的耐磨﹑耐疲劳要求﹐或有一定耐热﹑耐腐蚀要求的机器零件﹐以及各种切削刀具﹑冷作和热作模具等。
渗氮有多种方法﹐常用的是气体渗氮和离子渗氮。
气体渗氮:一般以提高金属的耐磨性为主要目的﹐因此需要获得高的表面硬度。
它适用於38CrMnAc等渗氮钢。
渗氮后工件表面硬度可达HV850~1200。
渗氮温度低﹐工件畸变小﹐可用於精度要求高﹑又有耐磨要求的零件﹐如鏜床鏜杆和主轴﹑磨床主轴﹑气缸套筒等。
但由於渗氮层较薄﹐不适於承受重载的耐磨零件。
气体参氮可採用一般渗氮法(即等温渗氮)或多段(二段﹑三段)渗氮法。
前者是在整个渗氮过程中渗氮温度和氨气分解率保持不变。
温度一般在480~520℃之间﹐氨气分解率为15~30%﹐保温时间近80小时。
这种工艺适用於渗层浅﹑畸变要求严﹑硬度要求高的零件﹐但处理时间过长。
最全的渗碳和渗氮区别整理表格
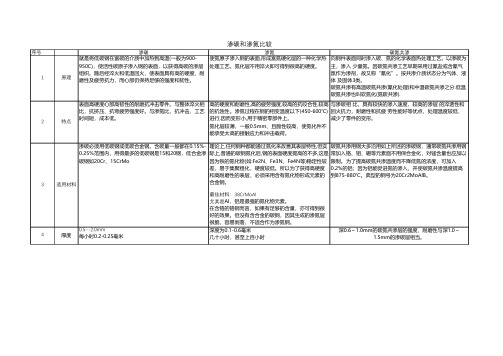
序号渗碳和渗氮比较12特点表面高硬度心部高韧性的耐磨抗冲击零件。
与整体淬火相比,抗挤压、抗弯疲劳强度好。
与渗氮比,抗冲击,工艺时间短,成本低。
高的硬度和耐磨性,高的疲劳强度,较高的抗咬合性,较高的抗蚀性。
渗氮过程在钢的相变温度以下(450-600℃)进行,因而变形小,用于精密零部件上。
氮化层较薄,一般0.5mm、且脆性较高,使氮化件不能承受太高的接触应力和冲击载荷。
渗碳渗氮就是将低碳钢在富碳的介质中加热到高温(一般为900-950C),使活性碳原子渗入钢的表面,以获得高碳的渗层组织。
随后经淬火和低温回火,使表面具有高的硬度、耐磨性及疲劳抗力,而心部仍保持足够的强度和韧性。
使氮原子渗入钢的表面,形成富氮硬化层的一种化学热处理工艺。
氮化层不用淬火即可得到很高的硬度。
原理碳氮共渗向钢件表面同时渗入碳、氮的化学表面热处理工艺。
以渗碳为主,渗入 少量氮。
因碳氮共渗工艺早期采用过氰盐或含氰气氛作为渗剂,故又称“氰化”。
按共渗介质状态分为气体、液体 及固体3类。
碳氮共渗有高温碳氮共渗(氰化处理)和中温碳氮共渗之分.低温碳氮共渗也叫软氮化(氮碳共渗).与渗碳相 比,具有较快的渗入速度,较高的渗层 的淬透性和回火抗力,耐磨性和抗疲 劳性能好等优点,处理温度较低,减少了零件的变形。
3适用材料渗碳必须用低碳钢或低碳合金钢。
含碳量一般都在0.15%-0.25%范围内,用得最多的低碳钢是15和20钢,低合金渗碳钢如20Cr、15CrMo理论上,任何钢种都能通过氮化来改善其表层特性,但实际上,普通的碳钢氮化后,钢的表面硬度提高的不多,这是因为铁的氮化物(如:Fe2N、Fe3N、Fe4N等)稳定性较差,易于集聚粗化,硬度较低。
所以为了获得高硬度和高耐磨性的表层,必须采用含有氮化物形成元素的合金钢。
最佳材料:38CrMoAl尤其是AI,铝是最强的氮化物元素。
在含铬的铬钢而言,如果有足够的含量,亦可得到很好的效果。
但没有含合金的碳钢,因其生成的渗氮层很脆,容易剥落,不适合作为渗氮钢。
渗碳与渗氮的区别
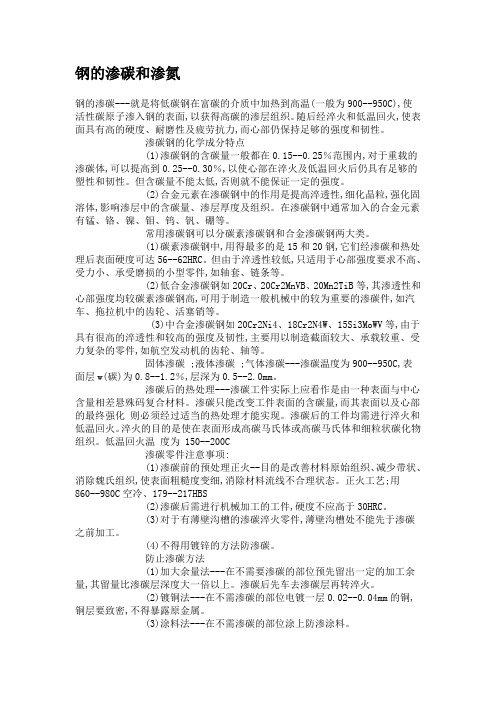
钢的渗碳和渗氮钢的渗碳---就是将低碳钢在富碳的介质中加热到高温(一般为900--950C),使活性碳原子渗入钢的表面,以获得高碳的渗层组织。
随后经淬火和低温回火,使表面具有高的硬度、耐磨性及疲劳抗力,而心部仍保持足够的强度和韧性。
渗碳钢的化学成分特点(1)渗碳钢的含碳量一般都在0.15--0.25%范围内,对于重载的渗碳体,可以提高到0.25--0.30%,以使心部在淬火及低温回火后仍具有足够的塑性和韧性。
但含碳量不能太低,否则就不能保证一定的强度。
(2)合金元素在渗碳钢中的作用是提高淬透性,细化晶粒,强化固溶体,影响渗层中的含碳量、渗层厚度及组织。
在渗碳钢中通常加入的合金元素有锰、铬、镍、钼、钨、钒、硼等。
常用渗碳钢可以分碳素渗碳钢和合金渗碳钢两大类。
(1)碳素渗碳钢中,用得最多的是15和20钢,它们经渗碳和热处理后表面硬度可达56--62HRC。
但由于淬透性较低,只适用于心部强度要求不高、受力小、承受磨损的小型零件,如轴套、链条等。
(2)低合金渗碳钢如20Cr、20Cr2MnVB、20Mn2TiB等,其渗透性和心部强度均较碳素渗碳钢高,可用于制造一般机械中的较为重要的渗碳件,如汽车、拖拉机中的齿轮、活塞销等。
(3)中合金渗碳钢如20Cr2Ni4、18Cr2N4W、15Si3MoWV等,由于具有很高的淬透性和较高的强度及韧性,主要用以制造截面较大、承载较重、受力复杂的零件,如航空发动机的齿轮、轴等。
固体渗碳 ;液体渗碳 ;气体渗碳---渗碳温度为900--950C,表面层w(碳)为0.8--1.2%,层深为0.5--2.0mm。
渗碳后的热处理---渗碳工件实际上应看作是由一种表面与中心含量相差悬殊码复合材料。
渗碳只能改变工件表面的含碳量,而其表面以及心部的最终强化则必须经过适当的热处理才能实现。
渗碳后的工件均需进行淬火和低温回火。
淬火的目的是使在表面形成高碳马氏体或高碳马氏体和细粒状碳化物组织。
各种渗层比较解读

Fe2B
或FeB+Fe2B
渗后
热处理
淬火+低温回火
无
无
淬火+回火
渗层
硬度
56~64HRC
950~1200HV
500~1000HV
58~67HRC
1300~2300HV
常用
渗剂
固:木炭,碳酸盐,粘结剂
优点
比渗氮工艺的渗层厚,可承受重载荷;工艺时间短;渗前不需要调质处理
常用固体渗剂
50%铬铁+
45%Al2O3+5%NH4Cl
常用硼砂盐浴
5%~10%钒粉+
95%~90%无水硼砂+少量中性盐
固体粉末或颗粒
40%~50%钛粉+
55%~45%Al2O3+3%NaF+2%NH4Cl
硼砂盐浴
4%~8%铌粉+
96%~92%硼砂
渗温
/℃
950~1050
900~1000
900~1000
渗氮层的机械性能比渗碳层的好;渗氮温度低,渗后不进行淬火处理,工件变形小;渗氮温度低
与渗氮相比,氮碳共渗的速度快,渗层韧性更高
与渗碳相比处理温度低,变形小,共渗层的机械性能更好
工艺时间短,渗层机械性能好
缺点
硬度和耐磨性不如渗氮层高;渗碳温度高,工件变形大;渗后往往需要淬火处理
渗氮层较薄、且脆性大,不能承受太大的接触应力和高的冲击载荷;渗氮时间长,生产率低,成本较高
8%~15%V2O5+
60%~70%Na2B4O7+1%~3%NaF+Al
常用固体粉末
碳氮共渗
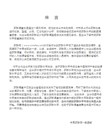
共渗温度的选择应综合考虑渗层质量、共渗速度与变形量等因素。国内大多数工厂的碳氮共渗温度在820~860℃范围内。温度超过900℃,渗层中含氮量太低,类似单纯渗碳,而且容易过热,工件变形较大。温度过低,不仅速度慢,而且表层含氮量过高,容易形成脆性的高氮化合物,渗层变脆。另外还将影响心部组织的强度和韧性。
3.共渗介质的配比与供应量 氨在共渗介质中所占的比例,影响渗层的碳氮浓度与组织状态。在一定范围内加大氨量,能使表层含碳量增加。氮的渗入能降低钢的临界点,增加了碳在奥氏体中的溶解度,加快碳原子的扩散速度,有利于碳的吸收与扩散。但是,表面含氮量的增加是有一定限度的,这个限值与共渗温度有关。过量的氨分解出大量的氮和氢,还会阻碍工件吸收碳。
共渗层的深度应该与工件服役条件和钢材成分相适应。心部的含碳量较高或工件的承载能力较低时,如纺织机钢令圈、40Cr钢制汽车齿轮,渗层应薄些,常在0.50mm以上。一些原来渗碳的零件改为碳氮共渗,深度要求可适当减薄。
共渗层中的浓度梯度宜尽量平缓,以保证层深与心部良好结合,防止渗层剥落。
4NaCNO→Na2CO3+CO+2【N】+2NaCN
2CO→CO2+【C】
由以上反应可以看出,盐浴的活性直接决定于NaCNO含量。新配置的盐浴熔化后,不能立即使用,必须停留一段时间,使一部分NaCN氧化为NaCNO。
加热时,NaCN与空气和盐浴中的氧作用,产生氰酸钠:
2NaCN+O2→2NaCNO
氰酸钠并不稳定,继续被氧化和自身分解,产生活性碳、氮原子。
- 1、下载文档前请自行甄别文档内容的完整性,平台不提供额外的编辑、内容补充、找答案等附加服务。
- 2、"仅部分预览"的文档,不可在线预览部分如存在完整性等问题,可反馈申请退款(可完整预览的文档不适用该条件!)。
- 3、如文档侵犯您的权益,请联系客服反馈,我们会尽快为您处理(人工客服工作时间:9:00-18:30)。
氮碳共渗:又称软氮化或低温碳氮共渗,即在铁-氮共析转变温度以下,使工件表面在主要渗入氮的同时也渗入碳。
碳渗入后形成的微细碳化物能促进氮的扩散,加快高氮化合物的形成。
这些高氮化合物反过来又能提高碳的溶解度。
碳氮原子相互促进便加快了渗入速度。
此外,碳在氮化物中还能降低脆性。
氮碳共渗后得到的化合物层韧性好,硬度高,耐磨,耐蚀,抗咬合。
常用的氮碳共渗方法有液体法和气体法。
处理温度530~570℃,保温时间1~3小时。
早期的液体盐浴用氰盐,以后又出现多种盐浴配方。
常用的有两种:中性盐通氨气和以尿素加碳酸盐为主的盐,但这些反应产物仍有毒。
气体介质主要有:吸热式或放热式气体(见可控气氛)加氨气;尿素热分解气;滴注含碳、氮的有机溶剂,如甲酰胺、三乙醇胺等。
氮碳共渗不仅能提高工件的疲劳寿命、耐磨性、抗腐蚀和抗咬合能力,而且使用设备简单,投资少,易操作,时间短和工件畸变小,有时还能给工件以美观的外表。
碳氮共渗:以渗碳为主同时渗入氮的化学热处理工艺。
它在一定程度上克服了渗氮层硬度虽高但渗层较浅,而渗碳层虽硬化深度大,但表面硬度较低的缺点。
应用较广泛的只有气体法和盐浴法。
气体碳氮共渗介质是渗碳剂和渗氮剂的混合气,例如滴煤油(或乙醇、丙酮)、通氨;吸热或放热型气体中酌加高碳势富化气并通氨;三乙醇胺或溶入尿素的醇连续滴注。
[C]、[N]原子的产生机制除与渗碳、渗氮相同外,还有共渗剂之间的合成和分解:
CO+NH3⇔HCN+H2O
CH4+NH3⇔HCN+3H2
2HCN⇔2[C]+2[N]+H2
碳氮共渗并淬火、回火后的组织为含氮马氏体、碳氮化合物和残余奥氏体。
深0.6~1.0mm 的碳氮共渗层的强度、耐磨性与深1.0~1.5mm的渗碳层相当。
为减少变形,中等载荷齿轮等可用低于870℃的碳氮共渗代替930℃进行的渗碳。