金属材料渗碳淬火工艺综述
渗碳淬火的工艺流程
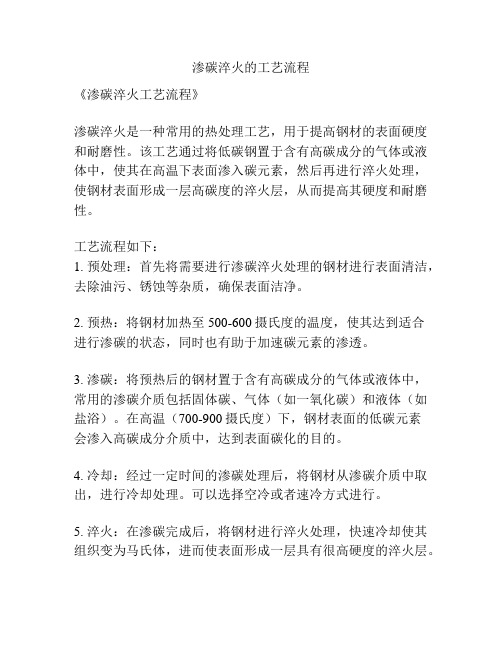
渗碳淬火的工艺流程
《渗碳淬火工艺流程》
渗碳淬火是一种常用的热处理工艺,用于提高钢材的表面硬度和耐磨性。
该工艺通过将低碳钢置于含有高碳成分的气体或液体中,使其在高温下表面渗入碳元素,然后再进行淬火处理,使钢材表面形成一层高碳度的淬火层,从而提高其硬度和耐磨性。
工艺流程如下:
1. 预处理:首先将需要进行渗碳淬火处理的钢材进行表面清洁,去除油污、锈蚀等杂质,确保表面洁净。
2. 预热:将钢材加热至500-600摄氏度的温度,使其达到适合
进行渗碳的状态,同时也有助于加速碳元素的渗透。
3. 渗碳:将预热后的钢材置于含有高碳成分的气体或液体中,常用的渗碳介质包括固体碳、气体(如一氧化碳)和液体(如盐浴)。
在高温(700-900摄氏度)下,钢材表面的低碳元素
会渗入高碳成分介质中,达到表面碳化的目的。
4. 冷却:经过一定时间的渗碳处理后,将钢材从渗碳介质中取出,进行冷却处理。
可以选择空冷或者速冷方式进行。
5. 淬火:在渗碳完成后,将钢材进行淬火处理,快速冷却使其组织变为马氏体,进而使表面形成一层具有很高硬度的淬火层。
6. 回火:淬火后的钢材虽然硬度高,但脆性也随之增加。
为了提高其韧性和耐久性,需要进行回火处理。
将淬火后的钢材加热至适当温度,再进行控制冷却,使其达到硬度和韧性的平衡状态。
通过以上工艺流程,钢材的表面硬度和耐磨性得到了显著提升,适用于需要耐磨性较高的部件和机械零件制造。
渗碳淬火钢的组织-概述说明以及解释
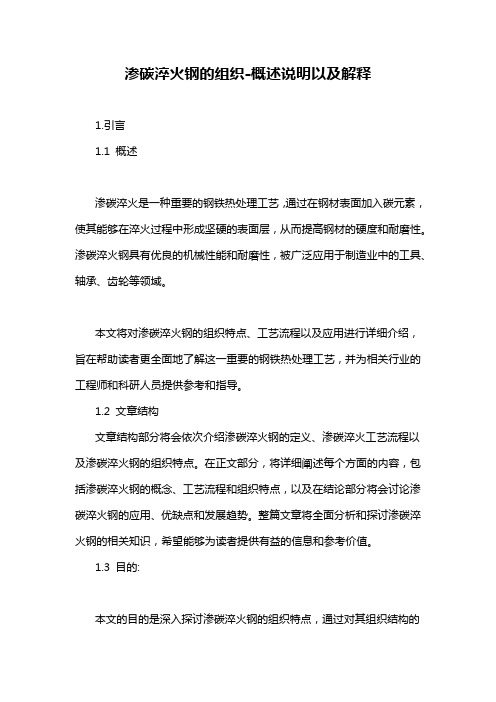
渗碳淬火钢的组织-概述说明以及解释1.引言1.1 概述渗碳淬火是一种重要的钢铁热处理工艺,通过在钢材表面加入碳元素,使其能够在淬火过程中形成坚硬的表面层,从而提高钢材的硬度和耐磨性。
渗碳淬火钢具有优良的机械性能和耐磨性,被广泛应用于制造业中的工具、轴承、齿轮等领域。
本文将对渗碳淬火钢的组织特点、工艺流程以及应用进行详细介绍,旨在帮助读者更全面地了解这一重要的钢铁热处理工艺,并为相关行业的工程师和科研人员提供参考和指导。
1.2 文章结构文章结构部分将会依次介绍渗碳淬火钢的定义、渗碳淬火工艺流程以及渗碳淬火钢的组织特点。
在正文部分,将详细阐述每个方面的内容,包括渗碳淬火钢的概念、工艺流程和组织特点,以及在结论部分将会讨论渗碳淬火钢的应用、优缺点和发展趋势。
整篇文章将全面分析和探讨渗碳淬火钢的相关知识,希望能够为读者提供有益的信息和参考价值。
1.3 目的:本文的目的是深入探讨渗碳淬火钢的组织特点,通过对其组织结构的分析和解释,帮助读者了解渗碳淬火钢的内部构造和性能特点。
同时,通过对渗碳淬火钢的组织特点进行研究,可以更好地指导工程实践中的应用,促进材料的优化设计和性能提升。
此外,还将探讨渗碳淬火钢的应用领域、优缺点以及未来发展趋势,为读者提供全面的了解和参考。
通过本文的阐述,旨在推动渗碳淬火钢在工业生产中的应用和发展,促进材料加工和工程领域的进步。
2.正文2.1 渗碳淬火钢的定义渗碳淬火是一种金属材料的表面处理技术,通过在金属表面强化碳元素的浓度,然后进行淬火处理,使得材料在表面形成高碳含量的硬化层,从而提高材料的硬度和耐磨性。
渗碳淬火钢是通过将金属材料在含碳气氛中加热至一定温度,使得碳原子渗透到金属表面,形成碳化层,然后经过淬火处理,使碳元素固溶在铁基体中,形成马氏体组织,最终实现对材料性能的提升。
渗碳淬火钢的应用范围广泛,包括汽车零部件、机械零件、工程机械等领域。
通过渗碳淬火处理,可以提高材料的表面硬度和耐磨性,延长材料的使用寿命,同时也能够提高材料的抗拉强度和抗疲劳性能,使其在高强度、高磨损环境下表现出色。
渗碳淬火热处理工艺
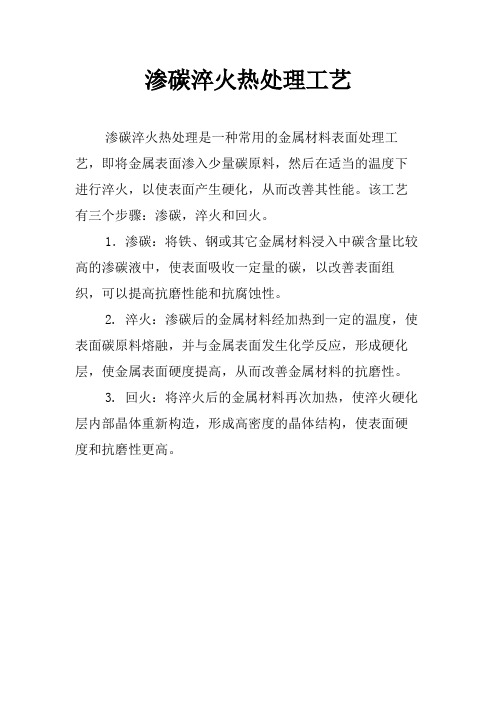
渗碳淬火热处理工艺
渗碳淬火热处理是一种常用的金属材料表面处理工艺,即将金属表面渗入少量碳原料,然后在适当的温度下进行淬火,以使表面产生硬化,从而改善其性能。
该工艺有三个步骤:渗碳,淬火和回火。
1.渗碳:将铁、钢或其它金属材料浸入中碳含量比较高的渗碳液中,使表面吸收一定量的碳,以改善表面组织,可以提高抗磨性能和抗腐蚀性。
2. 淬火:渗碳后的金属材料经加热到一定的温度,使表面碳原料熔融,并与金属表面发生化学反应,形成硬化层,使金属表面硬度提高,从而改善金属材料的抗磨性。
3. 回火:将淬火后的金属材料再次加热,使淬火硬化层内部晶体重新构造,形成高密度的晶体结构,使表面硬度和抗磨性更高。
山东金属表面渗碳工艺

山东金属表面渗碳工艺
山东金属表面渗碳工艺
1、渗碳处理是对金属表面处理的一种,方法是将工件置入具有活性渗碳介质中加热到单相奥氏体区进行渗碳处理。
渗碳处理可以使渗过碳的工件表面获得很高的硬度,同时保持心部保持原来的硬度和良好的韧性。
2、渗碳处理属于化学热处理,而化学热处理的状态由渗入元素在气氛和金属内部的化学位浓度来判定。
渗入的碳元素化学位浓度在工件表面处也就是边界处不连续,在金属内部有一定的浓度梯度,这个过程属于混合控制。
3、渗碳处理初期,工件表面碳浓度低于碳势浓度,而在工件内部碳浓度呈梯度变化,两者的变化情况不同。
工件在渗碳处理保温阶段通过表面Fe-C反应及内部扩散进行渗碳,我们可以通过控制这两种反应来达到控制渗碳的目的。
4、碳势和温度是影响渗碳处理的关键性因素,提高渗碳温度有利于加快渗碳速度,提高碳浓度有利于提高工件表面硬度,但要注意碳化物的形成,影响产品组织性能。
渗碳淬火热处理工艺【详解】

渗碳淬火热处理工艺详解内容来源网络,由深圳机械展收集整理!1、钢的淬火钢的淬火与回火是热处理工艺中最重要,也是用途最广泛的工序。
淬火可以显著提高钢的强度和硬度。
为了消除淬火钢的残余应力,得到不同强度,硬度和韧性配合的性能,需要配以不同温度的回火。
所以淬火和回火又是不可分割的、紧密衔接在一起的两种热处理工艺。
淬火、回火作为各种机器零件及工、模具的最终热处理是赋予钢件最终性能的关键工序,也是钢件热处理强化的重要手段之一。
1.1 淬火的定义和目的把钢加热到奥氏体化温度,保温一定时间,然后以大于临界冷却速度进行冷却,这种热处理操作称为淬火。
钢件淬火后获得马氏体或下贝氏体组织。
图4为渗碳齿轮20CrNi2Mo材料淬火、回火工艺。
淬火的目的一般有:1.1.1 提高工具、渗碳工件和其他高强度耐磨机器零件等的强度、硬度和耐磨性。
例如高速工具钢通过淬火回火后,硬度可达63HRC,且具有良好的红硬性。
渗碳工件通过淬火回火后,硬度可达58~63HRC。
1.1.2 结构钢通过淬火和高温回火(又称调质)之后获得良好综合力学性能。
例如汽车半轴经淬火和高温回火(280~320HB)及外圆中频淬火后,不仅提高了花键耐磨性,而且使汽车半轴承受扭转、弯曲和冲击载荷能力(尤其是疲劳强度和韧性)大为提高。
淬火时,最常用的冷却介质是水、盐水、碱水和油等。
通常碳素钢用水冷却,水价廉易得,合金钢用油来冷却,但对要求高硬度的轧辊采用盐水或碱水冷却,辊面经淬火后硬度高而均匀,但对操作要求非常严格,否则容易产生开裂。
1.2 钢的淬透性2.2.1 淬透性的基本概念所谓钢材的淬透性是指钢在淬火时获得淬硬层深度大小的能力(即钢材淬透能力),其大小用钢在一定条件下(顶端淬火法)淬火获得的有效淬硬层深度来表示,淬透性是每种钢材所固有的属性,淬硬层愈深,就表明钢的淬透性愈好,例如45、40Cr 、42CrMo钢三种试样,按相同条件淬火后(油冷却),经检测45钢能被淬透的最大直径(称临界直径)φ10mm;40Cr钢能被淬透的最大直径φ22mm; 42CrMo钢能被淬透的最大直径φ40mm。
金属材料渗碳淬火工艺综述
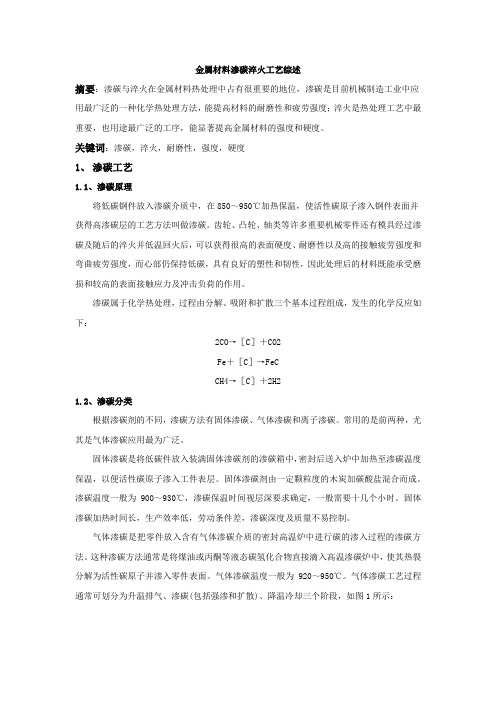
金属材料渗碳淬火工艺综述摘要:渗碳与淬火在金属材料热处理中占有很重要的地位,渗碳是目前机械制造工业中应用最广泛的一种化学热处理方法,能提高材料的耐磨性和疲劳强度;淬火是热处理工艺中最重要,也用途最广泛的工序,能显著提高金属材料的强度和硬度。
关键词:渗碳,淬火,耐磨性,强度,硬度1、渗碳工艺1.1、渗碳原理将低碳钢件放入渗碳介质中,在850~950℃加热保温,使活性碳原子渗入钢件表面并获得高渗碳层的工艺方法叫做渗碳。
齿轮、凸轮、轴类等许多重要机械零件还有模具经过渗碳及随后的淬火并低温回火后,可以获得很高的表面硬度、耐磨性以及高的接触疲劳强度和弯曲疲劳强度,而心部仍保持低碳,具有良好的塑性和韧性,因此处理后的材料既能承受磨损和较高的表面接触应力及冲击负荷的作用。
渗碳属于化学热处理,过程由分解、吸附和扩散三个基本过程组成,发生的化学反应如下:2CO→[C]+CO2Fe+[C]→FeCCH4→[C]+2H21.2、渗碳分类根据渗碳剂的不同,渗碳方法有固体渗碳、气体渗碳和离子渗碳。
常用的是前两种,尤其是气体渗碳应用最为广泛。
固体渗碳是将低碳件放入装满固体渗碳剂的渗碳箱中,密封后送入炉中加热至渗碳温度保温,以便活性碳原子渗入工件表层。
固体渗碳剂由一定颗粒度的木炭加碳酸盐混合而成。
渗碳温度一般为900~930℃,渗碳保温时间视层深要求确定,一般需要十几个小时。
固体渗碳加热时间长,生产效率低,劳动条件差,渗碳深度及质量不易控制。
气体渗碳是把零件放入含有气体渗碳介质的密封高温炉中进行碳的渗入过程的渗碳方法。
这种渗碳方法通常是将煤油或丙酮等液态碳氢化合物直接滴入高温渗碳炉中,使其热裂分解为活性碳原子并渗入零件表面。
气体渗碳温度一般为920~950℃。
气体渗碳工艺过程通常可划分为升温排气、渗碳(包括强渗和扩散)、降温冷却三个阶段,如图1所示:图1 井式炉滴注式气体渗碳工艺过程1.3、渗碳优化为了充分发挥渗碳层的作用,使零件表面获得高硬度和耐磨性,心部保持足够的强度和韧性,金属材料在渗碳后必须进行热处理,进行预冷、淬火、低温回火处理。
渗碳淬火轴加工工艺
渗碳淬火轴加工工艺渗碳淬火轴是一种常用的机械零件,广泛应用于机械设备领域。
为了满足不同场合的需求,常常需要对渗碳淬火轴进行特定的加工工艺,以保证其性能和质量。
下面将介绍一种常见的渗碳淬火轴加工工艺,帮助读者更好地了解渗碳淬火轴的生产方法。
1. 材料准备渗碳淬火轴的材料选择是相当重要的,典型的材料为45钢、40Cr、20CrMnTi等。
在选择材料时,需要考虑材料的耐磨性、强度和韧性等因素,以适应不同的使用环境和条件。
同时,必须严格执行国家标准或企业标准的要求,确保材料质量可靠。
2. 热处理在渗碳淬火轴的生产中,热处理工艺是必不可少的一环。
通常情况下,采用化学热处理技术(例如渗碳、氮化等)对材料进行表面增加硬度和耐磨性的处理。
处理结束后,对轴的硬度、强度、韧性等性能进行严格的测试,以确保轴能够满足设备的各种要求。
3. 粗加工粗加工阶段是渗碳淬火轴制作的关键步骤。
首先,需要选好切削刀具和夹具,并精准地定位和夹紧轴。
然后,按照预定的加工方案,进行车削、铣削、钻孔、镗孔等粗加工操作,以获得平整、精度高的轴表面。
此外,在加工过程中,需要不断检查轴的质量,保证各项性能指标合格。
细加工阶段是精密加工的过程,通常包括磨削、抛光、拉伸等操作。
磨削是将轴表面的高度差和表面质量进一步提高的关键工艺,可采用圆柱磨、内圆磨、平面磨等不同的磨削方法。
抛光可以让轴表面更加光滑,同时提升轴的耐腐蚀性和防氧化能力。
拉伸则是调整轴的截面尺寸和形状,以满足不同设备对轴的要求。
在细加工阶段,需要密切关注轴的表面质量和几何形状,不断进行测试和监测。
5. 淬火回火淬火回火是渗碳淬火轴制作中最关键的工艺环节之一。
在淬火过程中,轴表面会发生相变,获得很高的硬度和耐磨性。
回火则是为了调整轴的硬度和韧性,以防止过硬导致轴出现断裂等现象。
淬火回火工艺需要严格控制温度、时间、气氛等因素,确保淬火和回火质量稳定可靠,同时也防止轴表面出现过硬或过软的现象。
渗碳淬火材料电镀前处理工艺流程
渗碳淬火材料电镀前处理工艺流程下载温馨提示:该文档是我店铺精心编制而成,希望大家下载以后,能够帮助大家解决实际的问题。
文档下载后可定制随意修改,请根据实际需要进行相应的调整和使用,谢谢!并且,本店铺为大家提供各种各样类型的实用资料,如教育随笔、日记赏析、句子摘抄、古诗大全、经典美文、话题作文、工作总结、词语解析、文案摘录、其他资料等等,如想了解不同资料格式和写法,敬请关注!Download tips: This document is carefully compiled by theeditor.I hope that after you download them,they can help yousolve practical problems. The document can be customized andmodified after downloading,please adjust and use it according toactual needs, thank you!In addition, our shop provides you with various types ofpractical materials,such as educational essays, diaryappreciation,sentence excerpts,ancient poems,classic articles,topic composition,work summary,word parsing,copy excerpts,other materials and so on,want to know different data formats andwriting methods,please pay attention!渗碳淬火材料的电镀前处理工艺流程详解渗碳淬火是一种常见的金属表面处理技术,主要用于提高金属材料的硬度和耐磨性。
渗碳后的热处理工艺如何进行
工件渗碳后,提供了表层高碳、心部低碳这样一种含碳量的工件。
为了得到合乎理想的性能,需要进行适当的热处理。
在渗碳后常见的热处理主要有直接淬火、一次加热淬火、两次加热淬火这三种方法。
下面我们就来针对这三个方面具体介绍一下。
一、直接淬火直接淬火是在工件渗碳后,预冷到一定温度,然后立即进行淬火冷却。
这种方法一般适用于气体渗碳、真空渗碳或者液体渗碳。
固体渗碳时,由于工件装于箱内,出炉、开箱都比较困难,较难采用该种方法。
直接淬火的优点主要是减少加热、冷却次数,简化操作,减少变形及氧化脱碳。
其缺点是由于渗碳时在较高的渗碳温度停留较长的时间,容易发生奥氏体晶粒长大。
直接淬火虽然经过预冷也不能改变奥氏体晶粒度,因而可能在淬火后机械性能降低。
只有本质细晶粒钢,在渗碳时不发生奥氏体晶粒的显著长大,才能采用直接淬火。
二、一次加热淬火一次加热淬火是渗碳后缓冷,在此加热淬火。
这种热处理对心部强度要求不高,而表面又要求有较高的硬度和耐磨性时,可选用稍高于Ac1的淬火加热温度。
如此处理,渗层先共析碳化物未溶解,奥氏体晶粒细化,硬度较高,耐磨性较好,而心部尚存在有大量先共析铁素体,强度和硬度较低。
三、两次淬火在渗碳缓冷后进行两次加热淬火。
第一次淬火加热温度在Ac3以上,目的是细化心部组织,并消除表面网状碳化物。
第二次淬火加热温度选择在高于渗碳层成分的Ac1点温度。
二次加热淬火的目的是细化渗碳层中马氏体晶粒,获得隐晶马氏体、残余奥氏体及均匀分布的细粒状碳化物的渗层组织。
由于两次淬火发需要多次加热,不仅生产周期长、成本高,而且会增加热处理时的氧化、脱碳及变形等缺陷。
以前两次淬火法多应用于本质粗晶粒钢,但是现在的渗碳钢基本上都是用铝脱氧的本质细晶粒钢,因而目前两次淬火法在生产上很少应用,仅对性能要求较高的零件才偶尔采用。
渗碳淬火浅谈
渗碳淬火浅谈--华北地区第十六届热处理技术交流会论文集2007-10-11 摘自:北京市总工会技术英才网 作者:陈进磊郑树林摘要:大型重载齿轮在冶金、矿山、建材、起重、运输等重型机械传动中占有重要的地位,硬齿面大型重载齿轮可以减少传动所需功率、增大承载能力、降低成本、提高使用寿命。
气体渗碳淬火是实现齿面硬化的主要方法,在化学热处理快速发展的同时,总是有新的或是老的问题重复的出现,这里我就据自己的一点理解谈谈渗碳淬火的工艺。
关键词:表面脱碳,网状碳化物,渗碳层深,一次淬火,二次淬火大多数的渗碳钢都采用低含碳量高合金材料,在齿面渗碳淬火后,心部还能保证一定良好的机械性能,我们厂大多采用的渗碳钢种为20CrMnMo,20CrNi2Mo,17Cr2Ni2Mo,一直以来我们沿用渗碳工艺采用为渗碳+一次淬火+回火。
需要达到的要求为:1.表面高倍组织主要包括回火马氏体和游离碳化物。
允许存在可见的低于20%的残余奥氏体。
2.不允许有互相连接的完全包围晶粒的网状碳化物。
3.在500X不应有可见的完全脱碳现象。
4.表面碳含量从试棒上确定,表面含碳量的理想值应为0.7~0.9%。
5.不允许有在500X下可见的微小裂纹。
6.晶间氧化不宜超过试棒表面下的0.025mm7.心部高倍组织达到使齿轮能够被适当的奥氏体化,从而对其进行硬化。
在放大500X不允许有可见的块状铁素体,高倍组织应主要包括回火马氏体。
在工艺的执行过程中,许多厂家都会遇到这样的情况;1.渗碳结束后,试块表层有网状碳化物,这是造成后期淬火裂纹及磨削裂纹的主要原因。
2.渗碳结束后,工件表面硬度达不到理想硬度值,这种情况比较复杂,在排除设备及工艺原因的基础上,多数认为是由于工件齿面表面脱碳造成的,也有因为加热温度不当,保温时间不当或是冷却速度不够等原因造成的(如图四)。
3.残余奥氏体偏多。
它的形成原因是由于第一,加热温度高,第二加热时间长,第三,冷却设备的限制,造成过冷度的增加。
- 1、下载文档前请自行甄别文档内容的完整性,平台不提供额外的编辑、内容补充、找答案等附加服务。
- 2、"仅部分预览"的文档,不可在线预览部分如存在完整性等问题,可反馈申请退款(可完整预览的文档不适用该条件!)。
- 3、如文档侵犯您的权益,请联系客服反馈,我们会尽快为您处理(人工客服工作时间:9:00-18:30)。
金属材料渗碳淬火工艺综述
摘要:渗碳与淬火在金属材料热处理中占有很重要的地位,渗碳是目前机械制造工业中应用最广泛的一种化学热处理方法,能提高材料的耐磨性和疲劳强度;淬火是热处理工艺中最重要,也用途最广泛的工序,能显著提高金属材料的强度和硬度。
关键词:渗碳,淬火,耐磨性,强度,硬度
1、渗碳工艺
1.1、渗碳原理
将低碳钢件放入渗碳介质中,在850~950℃加热保温,使活性碳原子渗入钢件表面并获得高渗碳层的工艺方法叫做渗碳。
齿轮、凸轮、轴类等许多重要机械零件还有模具经过渗碳及随后的淬火并低温回火后,可以获得很高的表面硬度、耐磨性以及高的接触疲劳强度和弯曲疲劳强度,而心部仍保持低碳,具有良好的塑性和韧性,因此处理后的材料既能承受磨损和较高的表面接触应力及冲击负荷的作用。
渗碳属于化学热处理,过程由分解、吸附和扩散三个基本过程组成,发生的化学反应如下:
2CO→[C]+CO2
Fe+[C]→FeC
CH4→[C]+2H2
1.2、渗碳分类
根据渗碳剂的不同,渗碳方法有固体渗碳、气体渗碳和离子渗碳。
常用的是前两种,尤其是气体渗碳应用最为广泛。
固体渗碳是将低碳件放入装满固体渗碳剂的渗碳箱中,密封后送入炉中加热至渗碳温度保温,以便活性碳原子渗入工件表层。
固体渗碳剂由一定颗粒度的木炭加碳酸盐混合而成。
渗碳温度一般为900~930℃,渗碳保温时间视层深要求确定,一般需要十几个小时。
固体渗碳加热时间长,生产效率低,劳动条件差,渗碳深度及质量不易控制。
气体渗碳是把零件放入含有气体渗碳介质的密封高温炉中进行碳的渗入过程的渗碳方法。
这种渗碳方法通常是将煤油或丙酮等液态碳氢化合物直接滴入高温渗碳炉中,使其热裂分解为活性碳原子并渗入零件表面。
气体渗碳温度一般为920~950℃。
气体渗碳工艺过程通常可划分为升温排气、渗碳(包括强渗和扩散)、降温冷却三个阶段,如图1所示:
图1 井式炉滴注式气体渗碳工艺过程
1.3、渗碳优化
为了充分发挥渗碳层的作用,使零件表面获得高硬度和耐磨性,心部保持足够的强度和韧性,金属材料在渗碳后必须进行热处理,进行预冷、淬火、低温回火处理。
渗碳件经淬火并低温回火后,表层组织为高碳细针状回火马氏体组织加细粒状渗碳体及少量残余奥氏体,硬度为58~62HRC。
2、淬火工艺
2.1、淬火简介
将钢加热至临界点Ac3或Ac1以上一定温度,保温后以大于临界冷却速度的速度的冷却得到马氏体(或下贝氏体)的热处理工艺叫做淬火。
淬火的目的就是为了使它的组织全部或大部转变为马氏体,获得高硬度,然后在适当温度下回火,使工件具有预期的性能。
淬火可以提高金属工件的硬度及耐磨性,因而广泛用于各种工、模、量具及要求表面耐磨的零件(如齿轮、轧辊、渗碳零件等)。
通过淬火与不同温度的回火配合,可以大幅度提高金属的强度、韧性及疲劳强度,并可获得这些性能之间的配合(综合机械性能)以满足不同的使用要求
钢铁工件在淬火后具有以下特点:①得到了马氏体、贝氏体、残余奥氏体等不平衡(即不稳定)组织。
②存在较大内应力。
③力学性能不能满足要求。
因此,钢铁工件淬火后一般都要经过回火。
2.2、淬火温度的选择
淬火加热温度的选择应以得到均匀细小的奥氏体晶粒为原则,以便淬火后获得细小的马
氏体组织。
淬火温度主要根据钢的临界点确定,亚共析钢通常加热至Ac3以上30~50℃;共析钢、过共析钢加热至Ac1以上30~50℃。
对于低合金钢,淬火温度亦应根据临界点Ac1或Ac3确定,考虑合金元素的作用,为了加速奥氏体化,淬火温度可以偏高些,一般为Ac1或Ac3以上50~100℃。
高合金工具钢含有较多强碳化合物形成元素,奥氏体晶粒粗化温度高,则可以采取更高的淬火加热温度。
45钢、A3钢,这两种都属于亚共析钢,45钢的Ac3值是790℃,A3钢的Ac3值是810℃,Cr12的Ac3值是900℃。
45钢的淬火温度应该在810℃到840℃之间;A3钢的淬火温度在840℃到890℃之间;Cr12的淬火温度在930℃到980℃之间。
2.3、淬火介质
钢从奥氏体状态冷至Ms点以下所用的冷却介质叫淬火介质。
介质冷却能力越大,钢的冷却速度越快,越容易超过钢的临界淬火速度,则工件越容易淬硬,淬硬层的深度越深。
常用的淬火介质有水、盐水或碱水溶液及各种矿物油等。
以上介质各有优缺点。
水的冷却能力大,但冷却特性不好;由冷却特性好,但冷却能力又低。
45钢、A3钢Cr12的Ms点都是220℃。
2.4、淬火方法
选择适当的淬火方法同选择淬火介质一样,可保证在获得所要求的淬火组织和性能条件下尽量减小淬火应力,减少工件变形和开裂趋向。
常用的淬火方法有单液淬火、双液淬火、分级淬火和等温淬火。
3.1、模具热处理方式
模具材料主要为45#钢、A3钢,也有不少用的是Cr12合金。
采用的热处理方式是碳氮共渗→淬火(淬火介质是盐水或淬火油)→低温回火。
钢的碳氮共渗:碳氮共渗是向钢的表层同时渗入碳和氮的过程。
习惯上碳氮共渗又称为氰化,目前以中温气体碳氮共渗和低温气体碳氮共渗(即气体软氮化)应用较为广泛。
中温气体碳氮共渗的主要目的是提高钢的硬度,耐磨性和疲劳强度。
低温气体碳氮共渗以渗氮为主,其主要目的是提高钢的耐磨性和抗咬合性。
3.2、热处理常见的问题
在热处理常见的问题是模具出现变形、开裂的情况。
模具热处理后变形和开裂的主要原因:(1)、材质问题:S、P、Si等元素含量超过国家标准,或气孔、氧化物夹杂过多,都是导致热处理后模具开裂的主要原因。
(2)、热处理操作工艺的问题:淬火时,工件温度、零件形状、是否及时回火,都会导致零件开裂。
(3)、模具设计不合理。
(4)、工人操作不当。
3.3、主要材料45#的热处理工艺
1)对热处理设备及相应设施进行检查。
检查循环水系统是否畅通无阻,箱体密封圈是否
完整,确认达到要求后,按下列程序进行操作。
2)从动力配电柜给井式渗碳炉送电。
3)合上渗碳炉控制柜空气开关。
4)设定渗碳炉温度(870℃)。
5)打开循环水系统。
6)当炉温升至300℃时启动风机。
7)当温度升至780℃,滴入酒精进行排气,70~90滴/分钟。
8)炉温升至870±10℃时,炉内废气排尽,方可工件装炉。
9)装炉后酒精滴入量120~160滴/分钟,快速排气,废气排尽后改为70~90滴/分钟.
10)炉温升至870℃时,匀温0.5小时,关闭酒精。
11)进入强渗阶段:煤油100~150滴/分钟,三乙醇氨40~70滴/分钟,压力120~210
mm水柱,强渗9小时,降温至850°C进入扩散阶段。
12)扩散阶段:煤油40~80滴/分钟,三乙醇氨50~80滴/分钟,压力60~120mm水柱。
扩散时间为3小时。
13)扩散阶段结束后,停止加热,出炉淬火。
14)工件全部出炉后,盖上炉盖,炉温自然降温至100℃时,关闭循环水.
15)附碳氮共渗工艺图,如图2所示。
图2 45#钢碳氮共渗工艺图
执行此工艺之后,模具的硬度达到了60HRC 以上,耐磨性和抗断裂性能都有很大提高,明显提高了模具的寿命。
3、 结论
渗碳淬火在模具制造、机械制造等许多行业起到了非常重要的作用。
长期的生产实践中采用的碳氮共渗→淬火(淬火介质是盐水或淬火油)→低温回火的热处理工艺取到了显著的效果,提高了模具的寿命,使模具的耐磨性、疲劳强度、抗压强度都有了很大的提高。
参考文献
1) 崔忠圻主编,金属学与热处理.机械工业出版社 2007年
2) 《简明热处理手册》编写组,简明热处理手册.北京出版社 1985年
3) 热处理学会编写,热处理手册. 机械工业出版社 2001年
温
度。