渗碳工艺的几种常见方法)
金属零件增碳的方法

金属零件增碳的方法
金属零件增碳是一种常用的工艺,它可以增加金属零件的硬度和耐磨性,使其
更适合于特定的使用环境和工作条件。
以下是几种常见的金属零件增碳的方法:
1. 渗碳法:渗碳法是将含有高碳含量的气体(如一氧化碳)与金属零件置于高
温环境中进行反应,使碳元素在金属表面渗透并扩散到深层。
这种方法可以在金属零件的表面形成一层含碳深度达到相应要求的薄硬层,提高其硬度和耐磨性。
2. 离子渗碳法:离子渗碳法是一种使用离子束照射金属零件表面的方法。
通过
将含有碳离子的气体加速到高速,并将其束流引向金属零件表面,碳离子会在金属表面形成一层较深的渗碳层。
这种方法可以在金属零件的表面形成均匀的薄硬层,具有较高的耐磨性和强度。
3. 化学渗碳法:化学渗碳法是通过在含碳化合物的溶液中浸泡金属零件,使其
在高温环境下与溶液中的碳元素发生反应,从而在金属表面形成渗碳层。
这种方法适用于复杂形状的金属零件,能够实现较深层次的渗碳,提高零件的耐磨性和强度。
4. 气体渗碳法:气体渗碳法是将金属零件置于含有碳气体的高温环境中进行反应。
通过在一定时间内暴露在碳气体中,金属零件的表面会发生化学反应,形成渗碳层。
这种方法简单易行,适用于大批量生产。
以上是几种常见的金属零件增碳的方法。
选择适当的增碳方法取决于金属零件
的要求、形状和生产需求。
增碳后的金属零件具有更高的硬度和耐磨性,在使用过程中更加可靠和耐用。
渗碳钢的热处理知识点总结

一、渗碳钢的热处理工序用于制造渗碳零件的钢称为渗碳钢。
渗碳钢的主要热处理工序一般是在渗碳之后再进行淬火和低温回火。
处理后零件的心部为具有足够强度和韧性的低碳马氏体组织,表层为硬而耐磨的回火马氏体和一定量的细小碳化物组织。
有些结构零件,是在承受较强烈的冲击作用和受磨损的条件下进行工作的,例如汽车、拖拉机上的变速箱齿轮,内燃机上的凸轮、活塞销等。
根据工作条件,要求这些零件具有高的表面硬度和耐磨性,而心部则要求有较高的强度和适当的韧性,即要求工件“表硬里韧”的性能。
为了兼顾上述双重性能,可以采用低碳钢通过渗碳淬火及低温回火来达到,此时零件心部是低碳钢淬火组织,保证了高韧性和足够的强度,而表层(在一定的深度)则具有高碳量(0.85%~1.05%),经淬火后有很高的硬度(HRC>60),并可获得良好的耐磨性。
二、渗碳钢的成分特点渗碳钢的含碳量一般都很低(在 0.15%~0.25%之间),属于低碳钢,这样的碳含量保证了渗碳零件的心部具有良好的韧性和塑性。
为了提高钢的心部的强度,可在钢中加入一定数量的合金元素,如Cr、Ni、Mn、Mo、W、Ti、B等。
其中 Cr、Mn、Ni 等合金元素所起的主要作用是增加钢的淬透性,使其在淬火和低温回火后表层和心部组织得到强化。
另外,少量的Mo、W、Ti等碳化物形成元素,可形成稳定的合金碳化物,起到细化晶粒、抑制钢件在渗碳时发生过热的作用。
微量的B(0.001%~0.004%)能强烈地增加合金渗碳钢的淬透性。
渗碳钢的分类根据淬透性或强度等级的不同,合金渗碳钢分为三类。
低淬透性合金渗碳钢即低强度渗碳钢(抗拉强度≤800MPa),如15Cr、20Cr、15Mn2、20Mn2等。
这类钢淬透性低,经渗碳、淬火与低温回火后心部强度较低且强度与韧性配合较差。
主要用于制造受力较小,强度要求不高的耐磨零件,如柴油机的凸轮轴、活塞销、滑块、小齿轮等。
这类钢渗碳时心部晶粒易于长大,特别是锰钢。
渗碳的名词解释
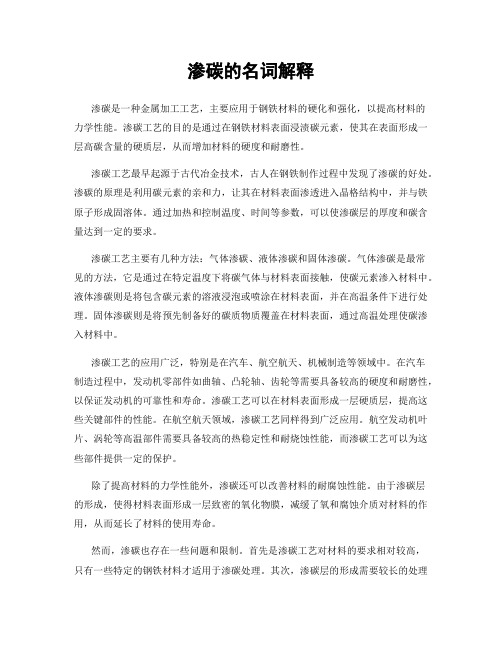
渗碳的名词解释渗碳是一种金属加工工艺,主要应用于钢铁材料的硬化和强化,以提高材料的力学性能。
渗碳工艺的目的是通过在钢铁材料表面浸渍碳元素,使其在表面形成一层高碳含量的硬质层,从而增加材料的硬度和耐磨性。
渗碳工艺最早起源于古代冶金技术,古人在钢铁制作过程中发现了渗碳的好处。
渗碳的原理是利用碳元素的亲和力,让其在材料表面渗透进入晶格结构中,并与铁原子形成固溶体。
通过加热和控制温度、时间等参数,可以使渗碳层的厚度和碳含量达到一定的要求。
渗碳工艺主要有几种方法:气体渗碳、液体渗碳和固体渗碳。
气体渗碳是最常见的方法,它是通过在特定温度下将碳气体与材料表面接触,使碳元素渗入材料中。
液体渗碳则是将包含碳元素的溶液浸泡或喷涂在材料表面,并在高温条件下进行处理。
固体渗碳则是将预先制备好的碳质物质覆盖在材料表面,通过高温处理使碳渗入材料中。
渗碳工艺的应用广泛,特别是在汽车、航空航天、机械制造等领域中。
在汽车制造过程中,发动机零部件如曲轴、凸轮轴、齿轮等需要具备较高的硬度和耐磨性,以保证发动机的可靠性和寿命。
渗碳工艺可以在材料表面形成一层硬质层,提高这些关键部件的性能。
在航空航天领域,渗碳工艺同样得到广泛应用。
航空发动机叶片、涡轮等高温部件需要具备较高的热稳定性和耐烧蚀性能,而渗碳工艺可以为这些部件提供一定的保护。
除了提高材料的力学性能外,渗碳还可以改善材料的耐腐蚀性能。
由于渗碳层的形成,使得材料表面形成一层致密的氧化物膜,减缓了氧和腐蚀介质对材料的作用,从而延长了材料的使用寿命。
然而,渗碳也存在一些问题和限制。
首先是渗碳工艺对材料的要求相对较高,只有一些特定的钢铁材料才适用于渗碳处理。
其次,渗碳层的形成需要较长的处理时间,特别是对于较厚的渗碳层,处理时间更长。
此外,渗碳过程中材料内部会产生应力,可能会导致变形和破裂,因此处理过程需要严格控制。
总之,渗碳是一种重要的金属加工工艺,可以通过在材料表面形成一层高碳含量的硬质层,提高材料的硬度、耐磨性和耐腐蚀性能。
连续炉渗碳工艺

连续炉渗碳工艺一、工艺概述连续炉渗碳工艺是一种将碳元素渗入钢材表面以提高其硬度和耐磨性的加工工艺。
该工艺通过在连续炉中对钢材进行预处理和加热,然后将其浸入含有碳化物的盐浴中进行渗碳处理,最后通过淬火和回火等步骤来完成整个加工过程。
二、设备与材料1. 连续式生产线:用于将钢材送入炉内进行预处理和加热。
2. 渗碳炉:用于将钢材浸入含有碳化物的盐浴中进行渗碳处理。
3. 盐浴:用于在渗碳炉中形成含有碳化物的介质。
4. 淬火槽:用于快速冷却已经渗碳的钢材。
5. 回火炉:用于将淬火后的钢材加热到适当的温度,以减少其脆性并增加其韧性。
6. 碱洗槽:用于去除表面残留的盐浴。
三、工艺步骤1. 钢材进入预处理区域:首先,钢材会被送入连续式生产线的预处理区域。
在这里,钢材会被清洗和去除表面氧化物等杂质。
2. 钢材进入加热炉:经过预处理后,钢材会被送入加热炉中进行加热。
在这里,钢材会被加热到所需温度(通常为850℃至950℃)。
3. 钢材进入渗碳炉:一旦钢材达到所需温度,它就会被送入渗碳炉中。
在这里,钢材将被浸入含有碳化物的盐浴中进行渗碳处理。
该过程通常需要10至30分钟。
4. 钢材进入淬火槽:一旦渗碳完成,钢材将被迅速冷却以形成马氏体组织。
这个过程通常通过将钢材浸入水或油中来实现。
5. 钢材进入回火炉:淬火后的钢材很脆性,在回火炉中将其加热到适当的温度(通常为150℃至250℃)以减少其脆性并增加其韧性。
6. 钢材进入碱洗槽:最后,钢材将被送入碱洗槽中去除表面残留的盐浴。
这个过程通常涉及使用强碱性溶液进行清洗。
四、工艺优点1. 连续炉渗碳工艺可以在较短的时间内对大量钢材进行处理,提高生产效率。
2. 该工艺可以在一次加工中完成多个步骤,减少了加工时间和成本。
3. 渗碳后的钢材具有高硬度和耐磨性,适用于制造高强度机械零件等领域。
五、工艺缺点1. 连续炉渗碳需要大量的设备和能源投入,成本较高。
2. 该工艺可能导致钢材表面出现不均匀的渗碳层,影响其质量。
零件渗碳工艺
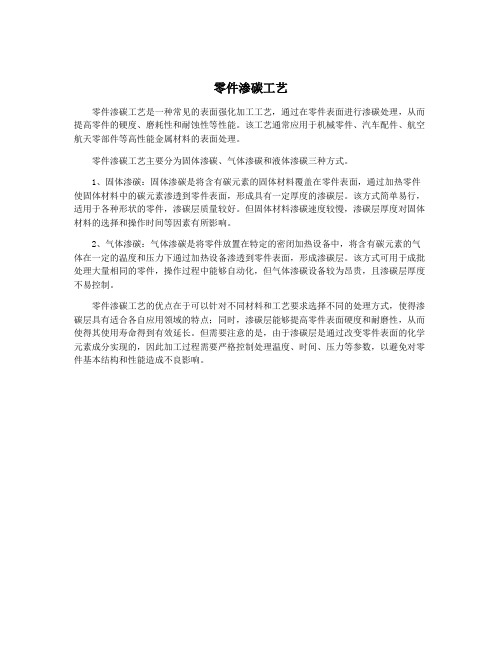
零件渗碳工艺
零件渗碳工艺是一种常见的表面强化加工工艺,通过在零件表面进行渗碳处理,从而提高零件的硬度、磨耗性和耐蚀性等性能。
该工艺通常应用于机械零件、汽车配件、航空航天零部件等高性能金属材料的表面处理。
零件渗碳工艺主要分为固体渗碳、气体渗碳和液体渗碳三种方式。
1、固体渗碳:固体渗碳是将含有碳元素的固体材料覆盖在零件表面,通过加热零件使固体材料中的碳元素渗透到零件表面,形成具有一定厚度的渗碳层。
该方式简单易行,适用于各种形状的零件,渗碳层质量较好。
但固体材料渗碳速度较慢,渗碳层厚度对固体材料的选择和操作时间等因素有所影响。
2、气体渗碳:气体渗碳是将零件放置在特定的密闭加热设备中,将含有碳元素的气体在一定的温度和压力下通过加热设备渗透到零件表面,形成渗碳层。
该方式可用于成批处理大量相同的零件,操作过程中能够自动化,但气体渗碳设备较为昂贵,且渗碳层厚度不易控制。
零件渗碳工艺的优点在于可以针对不同材料和工艺要求选择不同的处理方式,使得渗碳层具有适合各自应用领域的特点;同时,渗碳层能够提高零件表面硬度和耐磨性,从而使得其使用寿命得到有效延长。
但需要注意的是,由于渗碳层是通过改变零件表面的化学元素成分实现的,因此加工过程需要严格控制处理温度、时间、压力等参数,以避免对零件基本结构和性能造成不良影响。
表面渗碳处理工艺

表面渗碳处理工艺渗碳与渗氮一般是指钢的表面化学热处理渗碳必须用低碳钢或低碳合金钢。
可分为固体、液体、气体渗碳三种。
应用较广泛的气体渗碳,加热温度900-950℃。
渗碳深度主要取决于保温时间,一般按每小时0.2-0.25mm估算。
表面含碳量可达百分之0.85-1.05。
渗碳后必须热处理,常用淬火后低温回火。
得到表面高硬度心部高韧性的耐磨抗冲击零件。
渗氮应用最广泛的气体渗氮,加热温度500-600℃。
氮原子与钢的表面中的铝、铬、钼形成氮化物,一般深度为0.1-0.6mm,氮化层不用淬火即可得到很高的硬度,这种性能可维持到600-650℃。
工件变形小,可防止水、蒸气、碱性溶液的腐蚀。
但生产周期长,成本高,氮化层薄而脆,不宜承受集中的重载荷。
主要用来处理重要和复杂的精密零件。
涂层、镀膜是物理的方法。
“渗”是化学变化,本质不同。
钢的渗碳---就是将低碳钢在富碳的介质中加热到高温(一般为900--950℃),使活性碳原子渗入钢的表面,以获得高碳的渗层组织。
随后经淬火和低温回火,使表面具有高的硬度、耐磨性及疲劳抗力,而心部仍保持足够的强度和韧性。
渗碳钢的化学成分特点1)渗碳钢的含碳量一般都在0.15--0.25%范围内,对于重载的渗碳体,可以提高到0.25--0.30%,以使心部在淬火及低温回火后仍具有足够的塑性和韧性。
但含碳量不能太低,否则就不能保证一定的强度。
2)合金元素在渗碳钢中的作用是提高淬透性,细化晶粒,强化固溶体,影响渗层中的含碳量、渗层厚度及组织。
在渗碳钢中通常加入的合金元素有锰、铬、镍、钼、钨、钒、硼等。
常用渗碳钢可以分碳素渗碳钢和合金渗碳钢两大类1)碳素渗碳钢中,用得最多的是15和20钢,它们经渗碳和热处理后表面硬度可达56--62HRC。
但由于淬透性较低,只适用于心部强度要求不高、受力小、承受磨损的小型零件,如轴套、链条等。
2)低合金渗碳钢如20Cr、20Cr2MnVB、20Mn2TiB等,其渗透性和心部强度均较碳素渗碳钢高,可用于制造一般机械中的较为重要的渗碳件,如汽车、拖拉机中的齿轮、活塞销等。
渗碳的方法原理应用

渗碳的方法原理应用1. 渗碳的定义渗碳是一种金属表面处理工艺,通过在金属表面形成富碳层,提高金属材料的硬度和耐磨性。
渗碳是通过将含碳化合物加热至高温,使其在金属表面扩散,形成富碳层的过程。
2. 渗碳的原理渗碳的原理基于扩散理论,即在高温下,含碳化合物中的碳原子会从高浓度区域向低浓度区域扩散,最终在金属表面形成富碳层。
渗碳的速率取决于温度、时间和温度梯度。
3. 渗碳的方法渗碳的方法主要包括以下几种:•固体渗碳:将含碳化合物(如氰化钠、氰化钾等)与金属样品一同加入高温容器中,通过高温加热使碳原子扩散到金属表面。
•液体渗碳:通过将含有碳源的液体(如液态碳氢化合物)浸泡金属样品,使碳原子通过溶液扩散到金属表面。
•气体渗碳:通过在高温环境下,将含碳气体(如甲烷、一氧化碳等)与金属样品接触,使碳原子在金属表面扩散。
•离子渗碳:通过将含碳化合物(如氰化物)溶解在溶剂中,再通过电场作用将碳离子引入金属样品,实现渗碳。
4. 渗碳的应用渗碳广泛应用于许多领域,主要包括以下几个方面:•机械工程:在机械工程中,渗碳可以提高金属的硬度和耐磨性,用于制造轴承、齿轮等零部件,增加其使用寿命。
•汽车工业:在汽车工业中,渗碳可以用于制造曲轴、减震器等零部件,提高其耐磨性和强度。
•航空航天:在航空航天领域,渗碳可用于制造发动机零部件、航空轴承等高性能材料,提高其抗腐蚀性能和疲劳寿命。
•工具制造:在工具制造中,渗碳可以用于制造刀具、钻头等工具,提高其切削性能和寿命。
•能源领域:在能源领域,渗碳可用于制造石油钻具、钻井机零部件等设备,提高其耐磨性和使用寿命。
5. 渗碳的优点和注意事项渗碳具有以下优点:•提高材料硬度和耐磨性;•延长材料使用寿命;•显著改善材料表面性能。
渗碳需要注意以下事项:•清洁金属表面,避免表面有锈蚀、油污等影响渗碳效果;•控制渗碳工艺参数,如温度、时间,以保证渗碳层的质量;•选择合适的渗碳方法,根据不同材料和应用场景进行选择;•进行适当的后处理,如淬火、回火等,以提高渗碳层的性能。
渗碳的工艺流程

渗碳的工艺流程渗碳工艺是一种将碳元素引入金属表面以增加材料硬度和耐磨性的方法。
以下是一种常见的渗碳工艺流程。
首先是前处理。
在渗碳之前,需要对金属零件进行一系列的前处理工作。
这包括清洗、除油、除锈等步骤,以确保表面干净并且没有杂质。
接下来是表面准备。
在金属表面准备阶段,需要对材料进行一系列的处理工序,以便渗碳剂能够充分渗入金属的表面。
这些工序包括机械刨削、打磨或者玻璃珠喷砂等方法,以去除表面的氧化物和其他不良物质,并获得一定的粗糙度。
然后是渗碳剂的选择。
不同的金属材料和工件要求,需要使用不同类型的渗碳剂。
渗碳剂通常由含有碳的化合物组成,如氯化碳、氰化钠、氯乙烯等。
渗碳剂的选择是根据金属材料和产品要求的硬度、耐磨性和其他特性来确定的。
接下来是温度控制。
温度是渗碳过程中的一个重要因素。
通常,金属材料会被放置在一个热处理炉中,然后将渗碳剂加热到适当的温度。
这些温度可以在500℃至1000℃之间,具体取决于所用的渗碳剂和金属材料。
然后是渗碳时间。
渗碳时间是指金属材料在渗碳剂中浸泡的时间。
这个时间通常在几小时到几十个小时之间,取决于材料的厚度和所需的渗碳深度。
之后是冷却处理。
完成渗碳后,金属零件需要通过逐渐降温的方式进行冷却。
这是为了避免由于快速冷却引起的热应力,从而导致零件变形或开裂。
最后是后处理。
在渗碳完成后,金属零件可能需要进行一些后处理工序,例如洗涤、清洁和抛光等,以使零件表面更加光滑。
总结起来,渗碳工艺流程包括前处理、表面准备、渗碳剂选择、温度控制、渗碳时间、冷却处理和后处理。
每个步骤都是关键的,不仅影响渗碳效果,而且还会对金属零件的性能产生重要的影响。
通过精心设计和优化每个步骤,可以实现理想的渗碳结果,提高金属零件的硬度和耐磨性。
- 1、下载文档前请自行甄别文档内容的完整性,平台不提供额外的编辑、内容补充、找答案等附加服务。
- 2、"仅部分预览"的文档,不可在线预览部分如存在完整性等问题,可反馈申请退款(可完整预览的文档不适用该条件!)。
- 3、如文档侵犯您的权益,请联系客服反馈,我们会尽快为您处理(人工客服工作时间:9:00-18:30)。
渗碳工艺的几种常见方法
1、一次加热淬火低温回火,渗碳温度820~850ºC或780~810ºC
特点:对心部强度要求高者,采用820~850ºC淬火,心部组织为低碳马氏体;表面要求硬度高者,采用780~810ºC加热淬火可以细化晶粒
适用范围:适用于固体渗碳后的碳钢和低合金钢工件。
气体、液体渗碳后的粗晶粒钢,某些渗碳后不宜直接淬火的工件及渗碳后需机械加工的零件
2、渗碳、高温回火,一次加热淬火、低温回火,渗碳温度840~860ºC
特点:高温回火使马氏体和残留奥氏体分解,渗层中碳和合金元素以碳化物形式析出,便于工削加工及淬火后渗层残留奥氏体减少
适用范围:主要用于CR-NI合金钢渗碳工件
3、二次淬火低温回火
特点:第一次淬火(或正火),可以消除渗层网状碳化物及细化心部组织。
第二次淬火主要改善渗层组织,但对心部性能要求较高时应在心部AC3以上淬火
适用范围:主要用于对力学性能要求很高的重要渗碳工件,特别是对粗晶粒钢。
但在渗碳后需进行两次高温加热,使工件变形及氧化脱碳增加,热处理过程较复杂
4、二次淬火冷处理低温回火
特点:高于AC1或AC3(心部)的温度淬火,高合金钢表层残留奥氏体较多,经冷处理(-70~80ºC)促使奥氏体转变,从而提高表面硬度和耐磨性
适用范围:主要用于渗碳后不需要机械加工的高合金钢工件
5、直接淬火低温回火
特点:不能细化钢的晶粒。
工件淬火畸变较大,合金钢渗碳件表面残留奥氏体量较多,表面硬度较低
适用范围:操作简单,成本低廉。
井式炉用来处理对变形和承受冲击载荷不大的零件,适用于气体渗碳和液体渗碳工艺
6、预冷直接淬火低温回火,淬火温度800~850ºC
特点:可以减少工件淬火畸变,渗碳层中残留奥氏体量也可稍有降低,表面硬度略有提高,但奥氏体晶粒没有变化
适用范围:操作简单,工件氧化、脱碳及淬火变形均较小。
广泛用于细晶粒钢制造的各种工件。