渗碳淬火热处理工艺
渗碳工艺流程
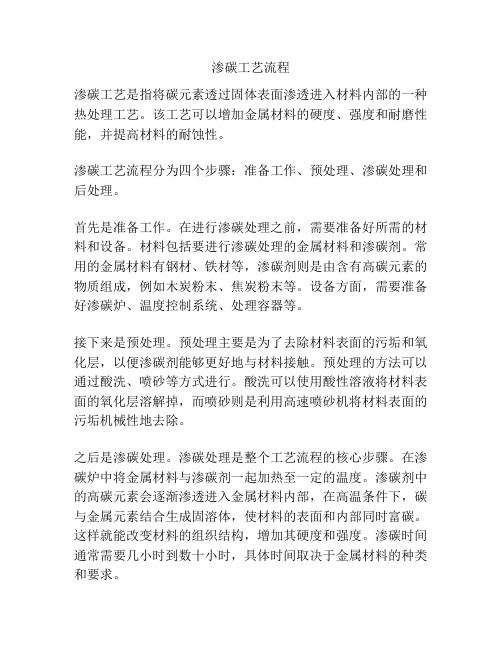
渗碳工艺流程渗碳工艺是指将碳元素透过固体表面渗透进入材料内部的一种热处理工艺。
该工艺可以增加金属材料的硬度、强度和耐磨性能,并提高材料的耐蚀性。
渗碳工艺流程分为四个步骤:准备工作、预处理、渗碳处理和后处理。
首先是准备工作。
在进行渗碳处理之前,需要准备好所需的材料和设备。
材料包括要进行渗碳处理的金属材料和渗碳剂。
常用的金属材料有钢材、铁材等,渗碳剂则是由含有高碳元素的物质组成,例如木炭粉末、焦炭粉末等。
设备方面,需要准备好渗碳炉、温度控制系统、处理容器等。
接下来是预处理。
预处理主要是为了去除材料表面的污垢和氧化层,以便渗碳剂能够更好地与材料接触。
预处理的方法可以通过酸洗、喷砂等方式进行。
酸洗可以使用酸性溶液将材料表面的氧化层溶解掉,而喷砂则是利用高速喷砂机将材料表面的污垢机械性地去除。
之后是渗碳处理。
渗碳处理是整个工艺流程的核心步骤。
在渗碳炉中将金属材料与渗碳剂一起加热至一定的温度。
渗碳剂中的高碳元素会逐渐渗透进入金属材料内部,在高温条件下,碳与金属元素结合生成固溶体,使材料的表面和内部同时富碳。
这样就能改变材料的组织结构,增加其硬度和强度。
渗碳时间通常需要几小时到数十小时,具体时间取决于金属材料的种类和要求。
最后是后处理。
后处理主要是对渗碳处理后的材料进行清洗和调质处理。
清洗是为了除去渗碳剂残留在材料表面的碳渣和污垢,通常可以通过酸洗或者喷砂等方式进行。
调质处理是为了改变材料的组织结构,使其达到所需的力学性能。
常用的调质方式有回火处理、淬火处理等。
总结起来,渗碳工艺流程包括准备工作、预处理、渗碳处理和后处理四个步骤。
通过这一工艺,可以提高金属材料的硬度、强度和耐磨性能,使得材料能够适用于各种高强度、高负荷的工程领域。
渗碳淬火的工艺流程
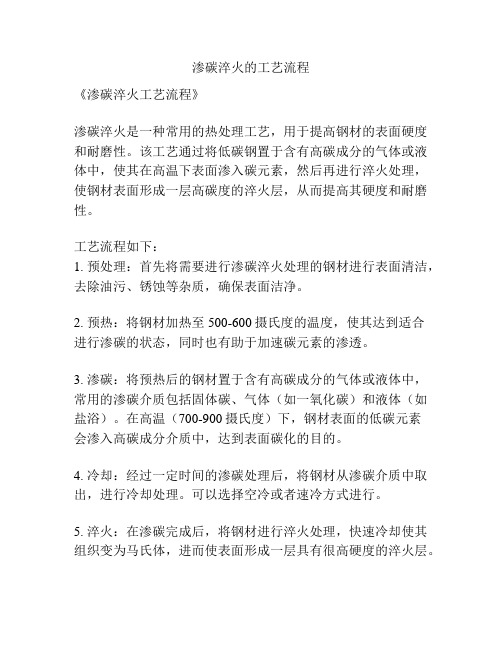
渗碳淬火的工艺流程
《渗碳淬火工艺流程》
渗碳淬火是一种常用的热处理工艺,用于提高钢材的表面硬度和耐磨性。
该工艺通过将低碳钢置于含有高碳成分的气体或液体中,使其在高温下表面渗入碳元素,然后再进行淬火处理,使钢材表面形成一层高碳度的淬火层,从而提高其硬度和耐磨性。
工艺流程如下:
1. 预处理:首先将需要进行渗碳淬火处理的钢材进行表面清洁,去除油污、锈蚀等杂质,确保表面洁净。
2. 预热:将钢材加热至500-600摄氏度的温度,使其达到适合
进行渗碳的状态,同时也有助于加速碳元素的渗透。
3. 渗碳:将预热后的钢材置于含有高碳成分的气体或液体中,常用的渗碳介质包括固体碳、气体(如一氧化碳)和液体(如盐浴)。
在高温(700-900摄氏度)下,钢材表面的低碳元素
会渗入高碳成分介质中,达到表面碳化的目的。
4. 冷却:经过一定时间的渗碳处理后,将钢材从渗碳介质中取出,进行冷却处理。
可以选择空冷或者速冷方式进行。
5. 淬火:在渗碳完成后,将钢材进行淬火处理,快速冷却使其组织变为马氏体,进而使表面形成一层具有很高硬度的淬火层。
6. 回火:淬火后的钢材虽然硬度高,但脆性也随之增加。
为了提高其韧性和耐久性,需要进行回火处理。
将淬火后的钢材加热至适当温度,再进行控制冷却,使其达到硬度和韧性的平衡状态。
通过以上工艺流程,钢材的表面硬度和耐磨性得到了显著提升,适用于需要耐磨性较高的部件和机械零件制造。
15nicr13钢渗碳热处理工艺

15nicr13钢渗碳热处理工艺15nicr13钢是一种低合金钢,主要由铁、镍、铬和碳等元素组成。
渗碳热处理是一种常用的工艺,用于改善钢的硬度和耐磨性。
本文将介绍15nicr13钢的渗碳热处理工艺及其应用。
渗碳热处理是通过将钢件浸入含有高碳含量的渗碳剂中,在高温下进行加热处理。
渗碳剂中的碳源可以是固体、液体或气体。
在渗碳剂的作用下,钢件表面的碳元素会渗入到钢件内部,使其表面形成一层富碳的高硬度层,从而提高钢件的硬度和耐磨性。
15nicr13钢的渗碳热处理工艺通常包括以下几个步骤:预处理、加热、渗碳、淬火和回火。
首先是预处理。
在进行渗碳热处理之前,钢件需要进行预处理,包括去除表面的污垢和氧化层,以及进行除磷、除硫等处理。
预处理可以提高渗碳剂的渗透性,使渗碳效果更好。
然后是加热。
钢件需要被加热到适当的温度,以便渗碳剂能够充分渗透到钢件内部。
加热温度通常在800℃至950℃之间,具体温度取决于钢件的材质和要求。
接下来是渗碳。
钢件被浸入含有高碳含量的渗碳剂中,并在高温下保持一段时间。
在此过程中,渗碳剂中的碳元素会通过扩散作用进入钢件表面,并在表面形成一层富碳层。
渗碳时间的长短会影响富碳层的厚度和硬度。
完成渗碳后,需要进行淬火。
淬火是将渗碳后的钢件迅速冷却,使其组织转变为马氏体。
这样可以使钢件的硬度达到最大值。
淬火方式可以选择水淬、油淬或气体淬火,具体选择取决于钢件的尺寸和要求。
最后是回火。
回火是为了消除淬火过程中产生的内应力,并调整和提高钢件的韧性。
回火温度通常在150℃至400℃之间,具体温度取决于钢件的要求。
15nicr13钢经过渗碳热处理后,可以获得较高的硬度和耐磨性。
这使得它在汽车制造、机械制造、工具制造等领域得到广泛应用。
例如,15nicr13钢可以用于制造汽车传动轴、齿轮、曲轴等零件,以及机床刀具等。
15nicr13钢的渗碳热处理工艺是一种常用的工艺,可以显著提高钢件的硬度和耐磨性。
通过预处理、加热、渗碳、淬火和回火等步骤,可以使15nicr13钢获得较高的性能,适用于各种工业领域的应用。
渗碳淬火热处理工艺
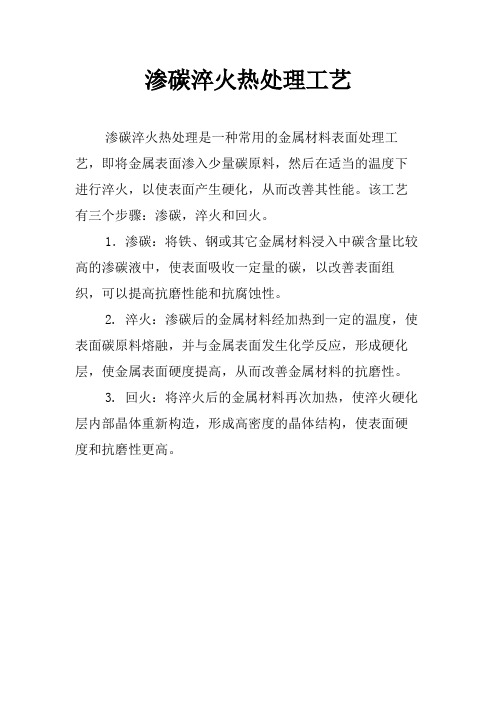
渗碳淬火热处理工艺
渗碳淬火热处理是一种常用的金属材料表面处理工艺,即将金属表面渗入少量碳原料,然后在适当的温度下进行淬火,以使表面产生硬化,从而改善其性能。
该工艺有三个步骤:渗碳,淬火和回火。
1.渗碳:将铁、钢或其它金属材料浸入中碳含量比较高的渗碳液中,使表面吸收一定量的碳,以改善表面组织,可以提高抗磨性能和抗腐蚀性。
2. 淬火:渗碳后的金属材料经加热到一定的温度,使表面碳原料熔融,并与金属表面发生化学反应,形成硬化层,使金属表面硬度提高,从而改善金属材料的抗磨性。
3. 回火:将淬火后的金属材料再次加热,使淬火硬化层内部晶体重新构造,形成高密度的晶体结构,使表面硬度和抗磨性更高。
钢的渗碳和碳氮共渗、淬火、回火工艺
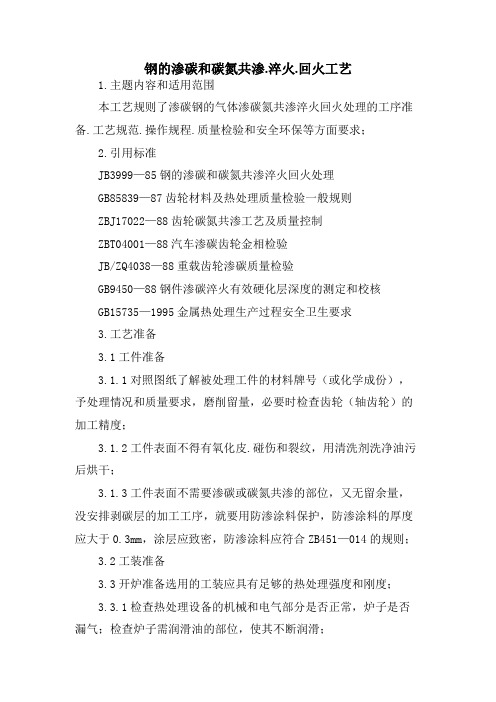
钢的渗碳和碳氮共渗.淬火.回火工艺1.主题内容和适用范围本工艺规则了渗碳钢的气体渗碳氮共渗淬火回火处理的工序准备.工艺规范.操作规程.质量检验和安全环保等方面要求;2.引用标准JB3999—85钢的渗碳和碳氮共渗淬火回火处理GB85839—87齿轮材料及热处理质量检验一般规则ZBJ17022—88齿轮碳氮共渗工艺及质量控制ZBT04001—88汽车渗碳齿轮金相检验JB/ZQ4038—88重载齿轮渗碳质量检验GB9450—88钢件渗碳淬火有效硬化层深度的测定和校核GB15735—1995金属热处理生产过程安全卫生要求3.工艺准备3.1工件准备3.1.1对照图纸了解被处理工件的材料牌号(或化学成份),予处理情况和质量要求,磨削留量,必要时检查齿轮(轴齿轮)的加工精度;3.1.2工件表面不得有氧化皮.碰伤和裂纹,用清洗剂洗净油污后烘干;3.1.3工件表面不需要渗碳或碳氮共渗的部位,又无留余量,没安排剥碳层的加工工序,就要用防渗涂料保护,防渗涂料的厚度应大于0.3mm,涂层应致密,防渗涂料应符合ZB451—014的规则;3.2工装准备3.3开炉准备选用的工装应具有足够的热处理强度和刚度;3.3.1检查热处理设备的机械和电气部分是否正常,炉子是否漏气;检查炉子需润滑油的部位,使其不断润滑;3.3.2检查测温仪表,热电隅是否正常,要定期进行校验;3.3.3定期清理气体渗碳炉炉罐中的碳黑和灰烬;3.4工件的表卡和试样3.4.1根据工件的形状和要求,选用适当的吊具和夹具;3.4.2工件间要有5~10mm的间隙;3.4.3应随炉放臵与装炉工件材质和予处理相同和符合GB8539—87“齿轮材料及热处理质量检验的一般规则”规则的样式,并放臵在有代表性的位臵,以备炉前操作抽样检查;4.渗碳和碳氮共渗淬火回火处理的工艺规范和操作规程4.1渗碳.碳氮共渗处理4.1.1装炉4.1.1.1工件装炉前应把炉温升到渗碳或共渗温度,连续生产时可干上一炉出炉后立即装炉;4.1.1.2工件应装在炉子的有效加热区内,加热区的炉温不得超过±15℃;4.1.1.3每炉装载量不大于设备的装载量;4.1.2气体渗碳工艺规范和操作规程4.1.2.1气体渗碳工艺规范参照图1,低碳合金渗碳钢的渗碳温度取上限;4.1.2.2排气期排气期的渗剂滴入量,参照表1,炉子到温后的排气时间的长短取决于排气程度,应取气进行分析,当CO2和O2的含量低于0.5%时,即可关闭试样孔,转入强渗期;无气体分析仪时,可观察废气火苗的颜色和状态,当火苗呈杏黄色,上升无力时,排气基本结束;一般地排气时间为1~1.5小时;4.1.2.3强渗期,关闭试样孔,点燃排出的废气;检查炉盖及通风机轴处是否漏气;调整煤油.异丙醇的滴入量,滴量多少取决于设备大小,装炉工件表面积的大小及炉子密封的情况,表1的滴量供选择时参考;强渗期炉气成份应控制在表2规则的范围内;有条件应采用红外线CO2碳位自控仪或露点仪控制炉气或用奥氏体分析仪对炉气进行分析,作为调正滴量的依据;强渗期的炉压控制在100~300pa;废气燃烧的火苗高度控制在200~250㎜的长度;根据工件有效硬化层要求和渗速经验,约达到1/2~2/3渗层深度时,抽验第一根试样,根据第一个试样的渗层确定第二个试样的时间,当有效硬化层深度达到或接近工件的有效硬化深度时,即可进入扩散期;4.1.2.4扩散期:扩散期的煤油.异丙醇滴量约为强渗期的0.5倍,为了保证炉压,并同时加滴甲醇,扩散期的时间与工件要求的有效硬化层深度有关,有效硬化层深度愈深,扩散时间要求愈长一些,与工件的碳势(试样的碳势)有关,碳势高要求扩散时间长一些,还与试样渗层深度有关,为了保证工件表面0.85~1.0%的碳浓度和合理的过滤层,扩散时间约为1~3小时;4.1.2.5降温期:抽验的第三个试样,如果网状碳化物≥5级为作正火处理,920℃出炉空冷,对20CrMnMo17Cr2Ni20CrNi2Mo当工件室冷到300-400℃时要放到回火炉中炉冷,防止在表面和次层在空冷时产生马氏体,形成表面裂纹;对于17CrNi2Mo.20Cr2NiMo等Cr.Ni渗碳钢即使碳化物不超级也要出炉空冷,空冷的炉温度为860~880℃;对于碳化物不超级的20CrMnTi.20CrMnMo~840℃,保渗碳齿轮,随炉冷到830温0.5~1H后直接淬火;4.1.3气体碳氮共渗工艺规范和操作规程;4.1.3.1气体碳氮共渗操作规程;4.1.3.2采用煤油加氨氧的气体碳氮共渗工艺曲线4.1.3.3共渗过程其炉气成分应符合下表规则4.2.1工件渗碳后直接淬火;对本质细晶粒钢工件渗碳后可采用直接淬火的方法,以获得所需要的表层和心部硬度以及有效硬化层深度,如20CrMo.20CrMnMo,以及含硼和稀土的合金钢渗碳件;直接淬火一般在炉中降温到830~850℃,均温0.5~1H出炉后淬火工件渗碳后直接淬火另一个条件是渗层金相组织网状碳化物≤4级;工件要求渗层深,炉中碳势又高的情况,容易造成碳化物超级,而对于模数≤5的20CrMnTi.20CrMnMo齿轮,渗碳深度1.2~1.3㎜(含磨量)碳化物不易超级,可以直接淬火,模数大于5的齿轮视渗层的金相组织中网状碳化物的级别而定,如果网状碳化物小于4级可以直接淬火;5级以上则要高温正火,消除网状碳化物或降低网状碳化物级别;4.2.2工件渗碳后空冷后再淬火,按方法有以下几种原因:a.工件渗碳后需要进行机械加工,如制碳层;b.容易发生过热的碳钢和非细晶粒合金钢件,以及某些不宜直接淬火的工件(如需要在压床上淬的齿轮);c.渗层组织如出现网状碳化物超级对于a.b两种情况,炉冷到850~860℃空冷,但对20CrMnMo渗件要求在400℃以下缓冷,否则易再次表层出现马氏体组织形成裂纹,对于C种情况,要求在900~930℃出炉直接空冷;4.2.312CrNi3.12Cr2Ni4.17CrNi2Mo.20CrNi4.20Cr2Ni4.20Cr2Ni4MoA.20Cr2Ni4WA等高强合金渗碳件,渗碳炉冷到920℃出炉空冷(用于制作大模数齿轮),400以下缓冷,并增加一次至二次650~680℃,5~6H的高温回火;这种高温回火称为催化或促变处理,它不仅能改善机械加工性能,更主要它是获得良好淬火组织的条件和保证;必须严格执行;4.2.4碳氮共渗的工件一般都从共渗温度或低于共渗温度出炉直接淬火;4.2.5经过渗碳淬火或碳氮共渗淬的工件,通常采用180℃±10℃的低温回火;4.2.5.1碳氮共渗齿轮回火的温度为180℃±10℃,回火时间3H;4.2.5.2模数1~3的齿轴渗碳淬火后温度200~210℃,时间3H,模数1~3的齿轮渗碳淬火后的回温度220℃±10℃,时间3H4.2.5.3模数3~5的齿轴.齿轮渗碳淬火后进行二次回火;第一次回火温度230℃,时间4H;第二次齿轴的回火温度230℃,回火时间3H;4.2.5.4模数≥6的齿轮.齿轴,渗碳后直接淬火的工件,需要进行三次回火;第一次回火温度230℃,回火时间3H;第二次回火,齿轴的回火温度230℃,时间3H,齿轮的回火温度240℃,时间3H;第三次回火,齿轴的回火温度220℃,时间3H,齿轮的回火温度240℃,时间3H;4.2.5.5模数≥6的齿轮齿轴渗碳后空冷,后加热淬火;进行二次回火;第一次回火温度230℃,时间4H;第二次回火,齿轴的回火温度220℃,时间4H,齿轮的回火温度240℃,时间4H;4.2.5.6前一次回火后,工件空冷到室温或≤50℃,才能进行下一次回火;4.2.5.7工件回火必须放在回火炉的有效加热区内(渗碳淬火的齿轮部分需量出回火炉底部300㎜);4.3渗碳和碳氮共渗淬火回火件的最后处理;4.3.1清理:进行喷砂,以清除赤面的油污和氧化模;4.3.2校直和矫正:用偏摆仪检查齿轴的变形,当超过允许变形时,应对其校直和矫正;随后进行去应力回火;条件允许(淬火工件量少时)应在淬火后马上进行校直,然后再回火;5.质量检验5.1外观:不得有裂纹和碰伤5.2表面硬度5.2.1硬度检验方法,按GB23083《金属洛氏硬试验法》或其他硬度试验法进行;5.2.2表面硬度的偏差范围,表面硬度不得超过下表规则:5.3.1有效硬化层检验方法,按GB《钢的渗碳硬化层有效硬化层深度的测定和校验》中的规则执行;5.3.2有效硬化层深度偏差不得超过下表规则;根据零件的要求,按有关标准进行检定;5.5变形:零件的变形应符合技术要求;6.安全与环保6.1操作者要穿戴好必须的劳动保护用品;6.2执行所用设备的安全操作规程;6.3气体渗碳或碳氮共渗出炉淬火时,同时淬火的工件量大时,应先检查油温,当油温>100℃时,应先降油温后淬火,以防止油槽着火;着火时需用灭火器,石棉被灭火,严禁用水灭火;6.4要防止渗碳炉滴注器渗漏,以免引起炉盖着火,烧毁电机或造成渗剂失火;6.5其它方面按GB15735—1995,金属热处理生产过程安全卫生要求;。
渗碳工艺

渗碳工艺渗碳是将零件放在渗碳剂(渗碳介质)中,加热到中相奥氏体温度,经保温使碳原子渗人零件表面层的过程。
其目的是使零件表面层含碳量增加。
渗碳层的含碳量最好在C= 0.85%一1.05%范围内,其深度一般为0.5一Zmm。
经淬火和低温四大处理后,使表面层具有高的硬度和耐磨性,而心部仍保持原来高的塑性和韧性。
为达到上述目的,渗碳零件必须是低碳钢和低合金钢。
根据所用渗碳剂不同,渗碳方法分为固体渗碳、气体渗碳和液体渗碳三种。
其中气体渗碳法生产率高,渗碳质且易控制,且易实现机器化和自动化。
它是目前应用最广的一种方$。
气体渗碳法是将工件放人密封的加热炉(如井式气体渗碳炉)中,通人渗碳剂,加热到900—950℃,使零件在高温的渗碳气氛中进行渗碳的一种方法。
常用的气体渗碳剂有煤油、丙酮、天然气等化合物,而最常用的是煤油和丙酮。
零件渗碳后必须进行热处理,才能有效地发挥渗碳层的作用。
常用的热处理有下面三种。
(1)直接淬火法:零件渗碳后,出炉经预冷,再淬火和低温回火的热处理工艺。
这种方法,只用于要求具有高的表面硬度,而其它性能不作要求的零件。
(2)一次淬火法:零件渗碳后出炉空冷.再重新加热到淬火温度,进行淬火和低温回火的热处理工艺。
这种方法,用于对表面和心部的组织和机械性能,均有要求的零件。
(3)二次淬火法;它的方法是:第一次淬火(或正火)是把零件渗碳后重新加热到A以上(850~900℃)进行油冷,其目的是使心部组织细化和消除表面层的网状渗联体。
然后再将零件加热到共析钢和过共析钢正常的淬火温度(A ;以上)进行第二次淬火,其目的是为了使表面层硬化。
最后,再进行低温回火,以降低淬火内应力。
此法工艺较复杂,主要用于表面层硬度、耐磨性和疲劳强度,以及心部的韧性和塑性等要求较高的重载零件。
渗碳工工件的工艺流程
渗碳工工件的工艺流程渗碳是一种热处理方法,用于提高钢件表面的硬度和耐磨性。
渗碳工艺流程包括准备工作、预处理、渗碳、淬火和回火等步骤。
准备工作:首先,需要根据工件的类型和要求选择适当的渗碳材料。
渗碳材料可以是固体、液体或气体,如固体渗碳材料可以是碳化钠,液体渗碳材料可以是硝酸盐溶液,气体渗碳材料可以是一氧化碳气氛。
同时,还需要准备好渗碳设备和工具,如渗碳炉、渗碳箱、渗碳盖等。
预处理:在开始渗碳前,需要对工件进行预处理。
这包括清洗和去除表面油脂、锈蚀和其他杂质。
常见的方法有酸洗、砂轮打磨和喷砂。
处理完成后,将工件放入预热炉中进行加热至适当温度。
渗碳:渗碳是将碳元素通过固体、液体或气体渗入钢件表面的过程。
渗碳温度通常在800-950摄氏度之间,时间从几小时到几十小时不等。
渗碳过程中,需要控制渗碳介质的成分和温度,以确保渗碳层的均匀和预设的渗碳深度。
过程中还需要控制渗碳介质的流量和气氛,以确保渗碳层的质量。
淬火:渗碳后的工件表面具有高碳含量,但内部仍然是低碳含量。
为了均匀分布碳元素,提高整体硬度,需要对工件进行淬火处理。
淬火是将工件迅速冷却至室温或低于室温的过程。
淬火方法有水淬、油淬和气体淬三种。
选择合适的淬火介质取决于材料的类型和硬度要求。
回火:淬火后的工件表面硬度很高,但脆性也会增加。
为了提高工件的韧性和降低脆性,需要对工件进行回火处理。
回火是在高温下(通常在150-600摄氏度之间),将工件加热一段时间,然后冷却至室温的过程。
回火过程中,需要控制回火温度和时间,以达到要求的硬度和韧性。
以上就是渗碳工艺流程的介绍。
其中,渗碳、淬火和回火是主要的步骤,通过控制温度、时间和介质成分等参数,可以使工件表面形成均匀的硬化层,并提高整体硬度和耐磨性。
渗碳工艺在机械制造、汽车零部件和航空航天等领域有广泛的应用。
热处理零件渗碳工艺
热处理零件渗碳工艺
热处理零件渗碳工艺,也称为渗碳热处理,是一种提高金属零件表面硬度和耐磨性的方法。
下面是一般的渗碳工艺流程:1. 准备工件:
- 选择适合的材料,通常为低碳钢或中碳钢。
- 切割、清洗和去除表面氧化物等处理,确保工件表面光洁干净。
2. 预处理:
- 对工件进行预加热处理,以去除内部应力和水分,一般在500~800摄氏度进行均匀加热。
- 对工件进行表面清洁和脱脂,以保证渗碳过程的有效进行。
3. 渗碳处理:
- 将准备好的工件放置在含有渗碳介质的密闭容器中,渗碳介质通常为固体、液体或气体,常用的渗碳介质有气体:一氧化碳(CO)、液体:氰化钠(NaCN)溶液、固体:繁缕石(酸性)等。
- 控制温度和时间,通常温度在800~950摄氏度之间,并保持一定的时间,以使碳元素渗透到工件的表面层中。
- 渗碳时间和温度根据工件材料和要求的硬度深度来确定,通常为几小时至数十小时。
4. 冷却和清洁:
- 在渗碳结束后,将工件从渗碳介质中取出,并进行冷却,可
以采用水冷或者油冷等方式。
- 清洁工件表面的渗碳残留物,以及附着在外表面的污垢。
5. 后处理:
- 经过渗碳处理后的工件,可以进行热处理工艺中的其他步骤,如淬火、回火等,以进一步调整工件的组织结构和性能。
需要注意的是,渗碳工艺中温度、时间和渗碳介质的选择需要根据具体的工件要求和材料特性进行确定。
此外,操作过程中需注意安全,防止渗碳介质产生有害气体对人身和环境造成危害。
因此,渗碳工艺通常在专门的热处理设备或炉中进行,且需严格遵守相关的操作规范和安全标准。
渗碳前预备热处理
渗碳前预备热处理
渗碳前的预备热处理是热处理工艺的一个重要环节,主要包括以下几个步骤:
1. 预热处理:这一步的主要目的是消除零件中的水分和残余气体,使零件具备适合后续热处理的条件。
同时,预热还可以使零件加热均匀,减少因温度差异引起的热应力和变形。
2. 加热处理:将零件加热到渗碳温度,通常在900℃左右。
加热过程中需
要注意控制温度,避免温度过高或过低,影响渗碳效果。
3. 保温处理:在加热温度下保持一定时间,使零件充分吸收热量,达到热平衡。
保温时间需要根据零件的材质、尺寸和要求来确定。
4. 冷却处理:渗碳后的冷却过程也十分重要,因为它决定了最终的相变组织。
根据不同的需求,可以选择不同的冷却方式,如空冷、油冷或水冷等。
通过合理的预备热处理,可以提高渗碳零件的机械性能和耐磨性,满足各种工程应用的需求。
渗碳淬火热处理工艺
渗碳淬火工艺1、钢的淬火钢的淬火与回火是热处理工艺中最重要,也是用途最广泛的工序。
淬火可以显著提高钢的强度和硬度。
为了消除淬火钢的残余应力,得到不同强度,硬度和韧性配合的性能,需要配以不同温度的回火。
所以淬火和回火又是不可分割的、紧密衔接在一起的两种热处理工艺。
淬火、回火作为各种机器零件及工、模具的最终热处理是赋予钢件最终性能的关键工序,也是钢件热处理强化的重要手段之一。
1.1 淬火的定义和目的把钢加热到奥氏体化温度,保温一定时间,然后以大于临界冷却速度进行冷却,这种热处理操作称为淬火。
钢件淬火后获得马氏体或下贝氏体组织。
图4为渗碳齿轮20CrNi2Mo材料淬火、回火工艺。
度200℃8 空冷时间h图4 渗碳齿轮20CrNi2Mo材料淬火、回火工艺淬火的目的一般有:1.1.1 提高工具、渗碳工件和其他高强度耐磨机器零件等的强度、硬度和耐磨性。
例如高速工具钢通过淬火回火后,硬度可达63HRC,且具有良好的红硬性。
渗碳工件通过淬火回火后,硬度可达58~63HRC。
1.1.2 结构钢通过淬火和高温回火(又称调质)之后获得良好综合力学性能。
例如汽车半轴经淬火和高温回火(280~320HB)及外圆中频淬火后,不仅提高了花键耐磨性,而且使汽车半轴承受扭转、弯曲和冲击载荷能力(尤其是疲劳强度和韧性)大为提高。
淬火时,最常用的冷却介质是水、盐水、碱水和油等。
通常碳素钢用水冷却,水价廉易得,合金钢用油来冷却,但对要求高硬度的轧辊采用盐水或碱水冷却,辊面经淬火后硬度高而均匀,但对操作要求非常严格,否则容易产生开裂。
1.2 钢的淬透性2.2.1 淬透性的基本概念所谓钢材的淬透性是指钢在淬火时获得淬硬层深度大小的能力(即钢材淬透能力),其大小用钢在一定条件下(顶端淬火法)淬火获得的有效淬硬层深度来表示,淬透性是每种钢材所固有的属性,淬硬层愈深,就表明钢的淬透性愈好,例如45、40Cr 、42CrMo钢三种试样,按相同条件淬火后(油冷却),经检测45钢能被淬透的最大直径(称临界直径)φ10mm;40Cr钢能被淬透的最大直径φ22mm;42CrMo钢能被淬透的最大直径φ40mm。
- 1、下载文档前请自行甄别文档内容的完整性,平台不提供额外的编辑、内容补充、找答案等附加服务。
- 2、"仅部分预览"的文档,不可在线预览部分如存在完整性等问题,可反馈申请退款(可完整预览的文档不适用该条件!)。
- 3、如文档侵犯您的权益,请联系客服反馈,我们会尽快为您处理(人工客服工作时间:9:00-18:30)。
渗碳淬火工艺1、钢的淬火钢的淬火与回火是热处理工艺中最重要,也是用途最广泛的工序。
淬火可以显著提高钢的强度和硬度。
为了消除淬火钢的残余应力,得到不同强度,硬度和韧性配合的性能,需要配以不同温度的回火。
所以淬火和回火又是不可分割的、紧密衔接在一起的两种热处理工艺。
淬火、回火作为各种机器零件及工、模具的最终热处理是赋予钢件最终性能的关键工序,也是钢件热处理强化的重要手段之一。
1.1 淬火的定义和目的把钢加热到奥氏体化温度,保温一定时间,然后以大于临界冷却速度进行冷却,这种热处理操作称为淬火。
钢件淬火后获得马氏体或下贝氏体组织。
图4为渗碳齿轮20CrNi度图4 渗碳齿轮20CrNi2Mo材料淬火、回火工艺淬火的目的一般有:1.1.1 提高工具、渗碳工件和其他高强度耐磨机器零件等的强度、硬度和耐磨性。
例如高速工具钢通过淬火回火后,硬度可达63HRC,且具有良好的红硬性。
渗碳工件通过淬火回火后,硬度可达58~63HRC。
1.1.2 结构钢通过淬火和高温回火(又称调质)之后获得良好综合力学性能。
例如汽车半轴经淬火和高温回火(280~320HB)及外圆中频淬火后,不仅提高了花键耐磨性,而且使汽车半轴承受扭转、弯曲和冲击载荷能力(尤其是疲劳强度和韧性)大为提高。
淬火时,最常用的冷却介质是水、盐水、碱水和油等。
通常碳素钢用水冷却,水价廉易得,合金钢用油来冷却,但对要求高硬度的轧辊采用盐水或碱水冷却,辊面经淬火后硬度高而均匀,但对操作要求非常严格,否则容易产生开裂。
1.2 钢的淬透性2.2.1 淬透性的基本概念所谓钢材的淬透性是指钢在淬火时获得淬硬层深度大小的能力(即钢材淬透能力),其大小用钢在一定条件下(顶端淬火法)淬火获得的有效淬硬层深度来表示,淬透性是每种钢材所固有的属性,淬硬层愈深,就表明钢的淬透性愈好,例如45、40Cr 、42CrMo钢三种试样,按相同条件淬火后(油冷却),经检测45钢能被淬透的最大直径(称临界直径)φ10mm;40Cr钢能被淬透的最大直径φ22mm; 42CrMo钢能被淬透的最大直径φ40mm。
实际工件的有效淬硬深度与钢的淬透性、工件尺寸及淬火介质的冷却能力等许多因素有关,例如,同一钢种在相同介质中淬火,小件比大件的淬硬层深;同一钢种相同尺寸时,水淬比油淬的淬硬层深。
同一种钢,其成分和冶炼质量必然在一定范围内波动,因而有关手册上所提供的某钢号的淬透性曲线往往不是一条线,而是一个范围,称淬透性带。
图5为40Cr钢的淬透性带。
图5 40Cr钢的淬透性带1.2.2、淬透性的表示方法钢的淬透性值可用J(HRC/ d )表示,其中J表示末端淬透性,d表示至水冷端的距离,HRC为该处测得的硬度值。
例如淬透性值J (42/5)表示距水冷端5mm处试样硬度值为42HRC;淬透性值J (30~35/10)表示距水冷端10mm处试样硬度值为30~35HRC。
对淬透性值有具体要求的钢应根据GB/T5216-2004《保证淬透性结构钢》标准的规定订货,其钢号最后用H表示,例如42CrMoH。
2、钢的回火2.1 回火的定义和目的钢淬火后必须经过回火,回火是指将淬火钢加热到Ac1(钢件加热时的临界点)以下的某一温度,经过保温,然后以一定的冷却方法冷至室温的热处理工艺,见图4。
回火的目的:2.1.1 降低脆性,减少或消除内应力,防止工件变形或开裂。
2.1.2 获得工艺所要求的力学性能。
淬火工件的硬度高且脆性大,通过适当回火可调整硬度,获得所需要的塑性、韧性。
2.1.3稳定工件尺寸。
淬火马氏体和残余奥氏体都是非平衡组织,它们会自发地向稳定的平衡组织转变,从而引起工件尺寸和形状的改变,通过回火可使淬火马氏体和残余奥氏体转变为较稳定组织,以保证工件在使用过程中不发生尺寸和形状的变化。
2.1.4 对于某些高淬透性的合金钢,空冷便可淬成马氏体,如采用退火软化,则周期很长。
此时可采用高温回火,降低硬度,以利切削加工。
淬火钢不经回火一般不能直接使用,为了避免工件在放置过程中发生变形和开裂,淬火后应及时回火。
2.2、回火的种类淬火钢回火后组织性能决定于回火温度,根据回火温度范围,可将回火分为三类:2.2.1 低温回火低温回火的温度为150~250℃,回火后组织为回火马氏体,低温回火主要降低钢的淬火内应力和脆性,同时保持钢在淬火后的高硬度(一般为58~64HRC)和耐磨性,常用于处理各种工具、模具、轴承、渗碳件及经表面淬火工件。
2.2.2中温回火中温回火的温度为350~500℃,回火后不仅保持较高硬度(一般为35~45HRC)和强度,而且具有高的弹性极限和足够的韧性。
中温回火主要用于各种弹簧的处理,还用于某些塑料模、热锻模以及要求较高强度的轴、轴套等。
2.2.3 高温回火高温回火的温度为500~650℃。
高温回火后的组织为回火索氏体,这种组织具有良好的综合力学性能。
二、化学热处理工件放在一定的化学介质中加热到一定温度,使其表面与介质相互作用,吸收其中某些化学元素的原子(或离子),并自表面向内部扩散的过程称为化学热处理。
化学热处理包括渗碳、渗氮、碳氮共渗等。
化学热处理的结果是改变了金属表面的化学成分和性能。
例如低碳钢经过表面渗碳淬火后,该钢种的工件表面就具有了普通高碳钢淬火后的高硬度、高耐磨的性能特征,而心部仍保留低碳钢淬火后良好的塑性、韧性的特征。
显然这是单一的低碳钢或高碳钢所不能达到的。
1、钢的渗碳1.1钢的渗碳基本原理和气体渗碳工艺1.1.1钢的渗碳基本原理在渗碳温度下(920℃)渗碳过程包括三个基本过程:一是由介质(甲醇、煤油、异丙醇)分解出活性原子。
如分解产生的一氧化碳和甲烷分解出活性碳原子:2CO ——CO2+[C]CH4——2H2+[C]二是活性碳原子被工件表面吸收。
三是被吸收碳原子向工件内部扩散。
渗碳过程由分解、吸收、扩散三过程组成,三个过程又是同时发生的,全部过程存在着复杂物理化学反应。
1.1.2气体渗碳工艺气体渗碳法是将工件放入密封的渗碳炉内,图8为气体渗碳法示意图,使工件在920℃高温的渗碳气氛中进行渗碳。
通入的有机物液体(甲醇、煤油、异丙醇)在高温下分解,产生活性碳原子,并被加热到奥氏体状态的工件表面吸收,而后向钢内部扩散。
渗碳时最主要的工艺参数是加热温度和保温时间。
加热温度愈高,渗碳速度就愈快, 且扩散层的厚度也愈深。
图8 气体渗碳法示意图温 920℃度℃ 渗碳 830-850℃排气 强渗 扩散 淬火时间(h )图 9 气体渗碳典型工艺 图9为气体渗碳典型工艺,从工艺中明显可见渗碳剂分解(含排气)、强渗(吸收)、扩散和炉冷到850℃直接油冷淬火的全过程。
1.2 渗碳件质量要求对渗碳件质量要求在国标GB/T8539-2000中已有明确规定,这里对几个主要方面再说明一下。
1.2.1 表面硬度和心部硬度齿表面硬度是指成品齿轮工作齿高中间部位齿面硬度,对锥齿轮指齿顶部表面硬度。
轮齿的心部硬度是指齿宽中部齿根30o 切线的法向上,深度为5倍硬化层深,但不少于1倍模数。
这是一个推荐测量部位,为了便于可操作性,可按技术条件或供需双方协议的图10 齿心部硬度示意图检查方法进行检查。
一般检测齿宽中部法截面上,在轮齿的中心线与齿根圆相交处的硬度,见图10示意图。
表面硬度和心部硬度是工件耐磨性能的重要指标,也是材料抗接触疲劳和弯曲疲劳的一个特性。
经渗碳淬火后表面硬度应达到58~64HRC(大截面齿轮和齿轮轴一般56~62HRC),心部硬度根据不同质量要求按规定控制,一般在25~42HRC,MQ级齿轮要求25HRC 以上,ME级齿轮要求35HRC以上。
硬度一般采用里氏硬度计或洛氏硬度计作为检测工具。
1.2.2 渗碳层表面碳浓度和碳浓度梯度渗碳零件表面碳浓度要求控制在0.75~0.95%为宜,过低会使耐磨性下降,过高时脆性增大,强度不能满足要求。
碳浓度梯度反映了碳浓度沿渗层下降的指标,它间接地反映了渗层的硬度梯度。
碳浓度下降得越平稳越好,以保证渗层与基体牢固结合,避免在使用过程中产生剥落现象。
图11为相同渗碳层总深度(3 mm)三种碳浓度梯度状况。
图11 相同渗碳层总深度(3 mm)三种碳浓度梯度a)好 b)不好 c)不好1.2.3 有效硬化层深度(渗碳层深度)有效硬化层深度取决于零件的工作条件和心部强度,是确定零件承载能力的重要参数。
目前对有效硬化层深度我厂技术设计部推荐采用GC/SY01-10《渗碳淬火齿轮有效硬化层深度技术规范》的标准。
有效硬化层深度是指零件渗碳淬火后,从零件表面到维氏硬度值为550HV1处的垂直距离。
测定硬度所采用的试验力为9.807N(1 kgf)。
1.3、零件渗碳后的热处理工件渗碳的目的在于使表面获得高的硬度和耐磨性,因此渗碳后的工件,必须通过热处理使表面获得马氏体组织,渗碳后的热处理方法有三种:1.3.1直接淬火法直接淬火法是将工件自渗碳温度炉冷到淬火温度后立即淬火,然后在160~190℃进行低温回火。
这种方法不需要重新加热淬火,因而减小了热处理变形,节省了时间和降低成本,但由于渗碳温度高,渗碳加热时间长,因而奥氏体晶粒粗大,淬火后残余奥氏体量较多,使工件性能下降,所以直接淬火法只适用于本质细晶粒钢或性能要求较低的工件。
这是一般工厂经常采用工艺。
1.3.2 一次淬火法一次淬火法是将工件自渗碳后以适当方式冷至室温,然后再重新加热淬火并低温回火。
对于要求心部有较高强度和较好韧性的零件,可以细化晶粒。
这是大型齿轮、齿轮轴等经常采用方法。
1.3.3 两次淬火法两次淬火法是将工件自渗碳后冷至室温后再进行两次淬火。
第一次淬火目的是细化心部晶粒,淬火温度较高,第二次淬火目的是细化表层晶粒,淬火温度较低,这种方法适宜用使用性能要求很高的工件,缺点是工艺复杂,生产周期长,工件容易变形,工厂应用较少。
对于零件有不允许渗碳硬化部位应在设计图样上标明,该部位可采用防渗涂料进行保护。
近几年来,我厂为适应宝钢进口设备齿轮箱的国产化要求,对热处理进行了相应技术改造,添置具有国内外先进水平的计算机过程控制的大型渗碳炉,由工业计算机、进口智能控温仪、进口智能碳控仪、氧探头等组成,炉温控制精度≤±3℃,炉温采用炉内主控,炉外辅控;碳浓度控制精度≤±0.05%;渗碳层深度偏差≤10%;渗碳硬化层深度范围1~6mm 。
从而对炉内碳浓度、炉温、渗碳硬化层深度等实现精确控制,保证了产品渗碳质量。
为减少盘形齿轮变形,从俄罗斯进口了淬火压床。
目前我厂有φ3000×2000mm、φ2000×2500mm、φ1700×2000mm、φ1200×2000mm、φ900×1200mm井式气体渗碳炉五台。
2、我国对齿轮用钢的冶金质量检验标准和要求齿轮钢材的冶金质量不仅影响到产品的机械性能,特别是疲劳性能,而且还影响到齿轮生产过程中的冷热加工性能及热处理工艺性能。