IE工业工程工艺分析改善工具
(IE工业工程)IE的分析方法及工具__标准工时、工作简化

IE 的分析方法及工具(3)__ 標準工時、工作簡化IE 的分析方法及工具( 3)八、標準時間標準時間又稱“標準工時”。
一個生產工廠,廠內生產部門有無建立標準工時,或標準工時的適用性,幾乎可衡量這個工廠的管理水準,因為管理落伍的工廠,對於工作人員的績效往往缺乏一種標準的衡量工具,而往往取法于主管的好惡,而標準工時的制訂,則可打破人為的偏差,對於績效的衡量建立在一個合理、公平的制度之下:(一)、標準時間的用途1. 作業方法的比較選擇對於不同的作業方法透過方法研究、時間研究,可以選擇最好的作業方法。
2. 工廠佈置之依據有了產品,制程作了分析,每個作業制定了標準時間,即可測算每個作業(部門)的負荷,依據負荷測算所需的作業空間,可達到更為流暢的工廠佈置。
3. 可預估工廠負荷產量工廠空間有多大,制程上有了標準時間,即可測算工廠產能。
4. 生產計畫的基礎生產管制部門的生產計畫,因有了標準時間,可以更精確的做生產計畫,如在進度控制上有了問題,也可依標準時間來做人力調整。
5. 可作為人力增減之依據做何產品?計畫產量多少?工作日多少?每日計畫工作時間多少?有了上面的資訊再加上有了標準時間,即可計算所需的人力,也就可有準備的進行增補或調整。
6. 可作為新添機器設備的依據機器產能(標準時間換算)可得知生產量起伏時所需要之機器數量。
7. 流水線生產之平衡一條流水線,諸多工序,依各工序的標準時間來配置人力,使生產線平衡,流暢。
8. 可決定人工成本對製造成本及外加工之費用可依標準時間做基礎來估算。
9. 可作為效率分析的基礎在多少時間內,完成多少產品,有了標準時間,就可計算效率因有明確的計算得予提升。
10. 工作人員效率獎金計算基礎有標準時間,才可得正確合理之效率,效率的好壞在薪資的獎金上應予反應,可得激勵作用。
11. 減少管理依存度每日的工作績效透過計算,並反應在獎金上,易於激發工作人員自主自動的工作態度。
(二)、標準時間之意義生產方法可運用工種分析、工作研究等技法,並運用管理迴圈PDCA一直獲得改善,不斷的尋求最大效率,最低成本的做法,當然標準時間也就不斷的跟著做改變。
生产干部必备的IE改善手法

生产干部必备的IE改善手法1. 引言IE(Industrial Engineering)是指工业工程,它是通过优化工业生产过程,提高生产效率的一种方法。
对于生产干部来说,掌握IE改善手法是提升生产效率、降低成本的关键。
本文将介绍一些生产干部必备的IE改善手法,帮助他们更好地管理生产过程。
2. 价值流分析价值流分析是一种用于分析和改善生产过程的工具。
通过价值流分析,生产干部可以了解整个生产过程中的每个环节,找出其中的瓶颈和浪费,进而进行改进。
在进行价值流分析时,以下几个步骤是必不可少的:•绘制当前状态的价值流地图:绘制出从原材料采购到产品出货的整个生产过程地图,标注出每个环节的信息流和物流。
•识别瓶颈环节:通过分析各个环节的生产能力,找出生产过程中的瓶颈环节,即制约整个生产过程的关键环节。
•消除浪费:通过分析每个环节中的浪费,采取相应的措施来消除这些浪费,提高生产效率。
3. 连续流水线连续流水线是一种用于大批量生产的工业生产方式。
它将产品在生产过程中分成多个环节,并将每个环节的工作分配给不同的工人或机器。
通过优化流水线上各个环节的工作效率,可以提高生产效率,降低成本。
在建立连续流水线时,以下几个因素需要考虑:•流程平衡:各个环节的工作时间应该平衡,以避免某个环节成为瓶颈。
•工位布局:合理的工位布局可以减少操作员之间的移动距离,提高工作效率。
•节拍时间:合理的节拍时间可以保证连续流水线的稳定运行。
4. 作业分析作业分析是通过评估工作任务的性质和要求,确定完成任务所需的资源和时间的过程。
通过作业分析,生产干部可以更好地了解每个工作岗位的任务和要求,为员工提供相应的培训和指导,提高工作效率。
在进行作业分析时,以下几个步骤是必要的:•观察和记录:观察员工在工作岗位上的表现,并记录下每个工作任务的具体内容。
•任务分解:将每个工作任务分解成更小的子任务,确定每个子任务所需的时间和资源。
•评估和改进:评估每个工作任务的效率和质量,并根据评估结果进行改进,提高工作效率。
IE七工具

.
IE七工具
什么是IE
IE(Industrial Engineering)是藉由設計、改善或設定 人、材料、設備的綜合性系統即工作系統,以 謀求提高生產力的技術
所謂「設計」是指工制作定更新轻的松系統,「改善」是把現 在的系統修正為更好的系更統快,而「設定」是引進設計 或已經改善的系統,並更使便其宜根基穩固,以期所期待的 機能能夠發揮。
IE七工具
作业研究与时间的关系
作
基本生产 时间
总生产所需时间
外观上的生产时间
业方法的改善
设计拙劣的浪 生产系统的 作业方法的
费
浪费
浪费
无效时间
IE活动的对象
管理拙劣所致 作业员所致无
无效时间
效时间
• • •
• • •
• • •
• • •
• • •
真正有效 生产时间
IE七工具
不安产 及全品 同质研 业量究 公设不 司计周 设差 计
IE手法光学习是没有用的,以日常实践来彻底消除浪 费才是重点!
IE七工具
IE七工具
生产方式的演变 工业工程发展简史 IE七工具
工程分析 → 1.动作研究 稼动分析 联合工程分析 生产线平衡分析 材料处理(搬运分析) 设施布置 事务工程分析
2.时间研究
目录
生产方式的演变
第三阶段:以70年代计算机在管理中 的应用为特征,它主要是柔性制造系 统、MRP、ERP的运用
美國IE協會(AIIE)
IE七工具
你适合当IE人员吗?
• 请回答下列十个问题:
问题 ①初次读一本书时,先看目录吗? ②早晨刷牙,是饭前、或饭后? ③洗手前,是否先掏出手帕? ④在打电话前,是否先将事情要点笔记起来? ⑤结帐排队于收银台时,是否准备零钱? ⑥吃饭的地方很多时,是否大致决定后才出发? ⑦在停车场,通常是后退停车? ⑧在桌上放置原子笔,笔尖朝哪一方? ⑨与人约定事情,是否用笔记起来? ⑩依先前之约,等到访问时是否再打电话?
IE的分析方法及工具

IE的分析方法及工具IE(Industiral Engineering),即工业工程,是一种研究工业生产中如何最优地运用人力、物力、财力等资源,以提高生产效益的学科。
在进行IE分析时,可以使用多种方法和工具来辅助。
以下是一些常用的IE分析方法及相关工具的简要介绍。
1.流程分析方法及工具:流程分析方法用于分析和优化工业生产过程中的流程。
常用的工具包括流程图、流程价值分析(PVA)、时间和动作研究(TAR)、价值流图(VSM)等。
流程图用于展示工业生产过程中的各个环节和关联性;PVA用于评估每个流程环节的价值并确定可能的改进点;TAR用于观察和分析工人在生产过程中的时间和动作,并提出相应的改进意见;VSM用于展示整个价值流程并识别可能的浪费环节。
2.工艺分析方法及工具:工艺分析方法用于分析和改善工业生产过程中的工艺。
常用的工具包括工艺路线图、标准操作程序(SOP)、工艺能力分析(PCA)等。
工艺路线图用于展示产品的生产流程和工艺要求;SOP用于明确每个工艺步骤的操作规范;PCA用于评估工艺的能力和稳定性,并提供改进建议。
3.人力分析方法及工具:人力分析方法用于分析和优化工业生产中的人力资源。
常用的工具包括时间研究、任务分析、工作分配、人力需求预测等。
时间研究用于测量工人在完成特定任务时所需的时间,并为人力资源的规划和管理提供依据;任务分析用于分析和描述每个工作岗位的任务要求和职责;工作分配用于合理分配人力资源以确保工作效率和质量;人力需求预测用于预测未来生产需求并相应地调整人力规模。
4.设备分析方法及工具:设备分析方法用于分析和改善工业生产中的设备使用效率和可靠性。
常用的工具包括设备维修与保养(PM)、总有效设备利用率(OEE)、故障模式和影响分析(FMEA)等。
设备维修与保养用于保障设备的正常运行和寿命延长;OEE用于评估设备的综合利用率,并提供可能的改善点;FMEA用于分析设备故障的模式和影响,并提出相应的预防和改进措施。
ie工业工程改善方案
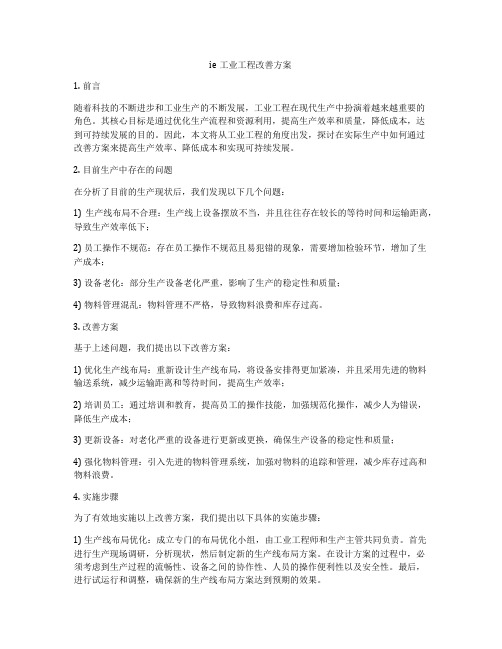
ie工业工程改善方案1. 前言随着科技的不断进步和工业生产的不断发展,工业工程在现代生产中扮演着越来越重要的角色。
其核心目标是通过优化生产流程和资源利用,提高生产效率和质量,降低成本,达到可持续发展的目的。
因此,本文将从工业工程的角度出发,探讨在实际生产中如何通过改善方案来提高生产效率、降低成本和实现可持续发展。
2. 目前生产中存在的问题在分析了目前的生产现状后,我们发现以下几个问题:1) 生产线布局不合理:生产线上设备摆放不当,并且往往存在较长的等待时间和运输距离,导致生产效率低下;2) 员工操作不规范:存在员工操作不规范且易犯错的现象,需要增加检验环节,增加了生产成本;3) 设备老化:部分生产设备老化严重,影响了生产的稳定性和质量;4) 物料管理混乱:物料管理不严格,导致物料浪费和库存过高。
3. 改善方案基于上述问题,我们提出以下改善方案:1) 优化生产线布局:重新设计生产线布局,将设备安排得更加紧凑,并且采用先进的物料输送系统,减少运输距离和等待时间,提高生产效率;2) 培训员工:通过培训和教育,提高员工的操作技能,加强规范化操作,减少人为错误,降低生产成本;3) 更新设备:对老化严重的设备进行更新或更换,确保生产设备的稳定性和质量;4) 强化物料管理:引入先进的物料管理系统,加强对物料的追踪和管理,减少库存过高和物料浪费。
4. 实施步骤为了有效地实施以上改善方案,我们提出以下具体的实施步骤:1) 生产线布局优化:成立专门的布局优化小组,由工业工程师和生产主管共同负责。
首先进行生产现场调研,分析现状,然后制定新的生产线布局方案。
在设计方案的过程中,必须考虑到生产过程的流畅性、设备之间的协作性、人员的操作便利性以及安全性。
最后,进行试运行和调整,确保新的生产线布局方案达到预期的效果。
2) 培训员工:建立规范化的操作流程和培训计划,对员工进行技能培训和操作规范培训。
培训计划由专门的人力资源部门制定,培训内容包括设备操作流程、安全操作规范、以及可能出现的故障应对方法。
工业工程(IE)作业分析
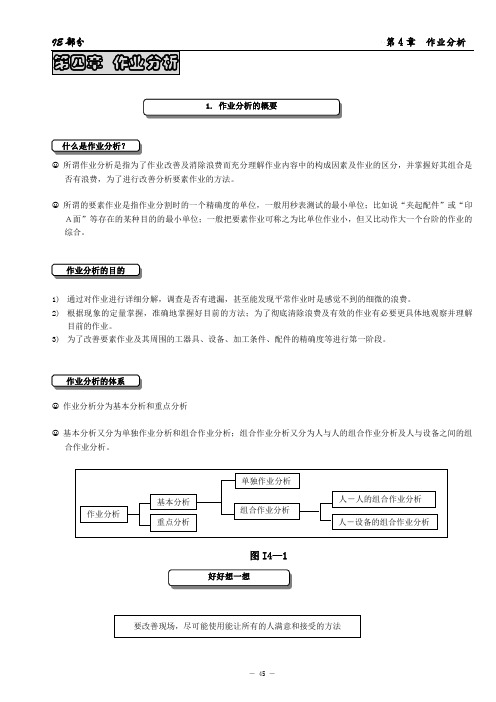
☺ 所谓作业分析是指为了作业改善及消除浪费而充分理解作业内容中的构成因素及作业的区分,并掌握好其组合是否有浪费,为了进行改善分析要素作业的方法。
☺所谓的要素作业是指作业分割时的一个精确度的单位,一般用秒表测试的最小单位;比如说“夹起配件”或“印A面”等存在的某种目的的最小单位;一般把要素作业可称之为比单位作业小,但又比动作大一个台阶的作业的综合。
1)通过对作业进行详细分解,调查是否有遗漏,甚至能发现平常作业时是感觉不到的细微的浪费。
2) 根据现象的定量掌握,准确地掌握好目前的方法;为了彻底清除浪费及有效的作业有必要更具体地观察并理解目前的作业。
3) 为了改善要素作业及其周围的工器具、设备、加工条件、配件的精确度等进行第一阶段。
☺ 作业分析分为基本分析和重点分析☺ 基本分析又分为单独作业分析和组合作业分析;组合作业分析又分为人与人的组合作业分析及人与设备之间的组合作业分析。
图I4—1图I4—2(1)将作业按要素作业分割的单位越小越好,但一定要保证能检测到的大小。
(3/100分~5/100分为界限)(2)分为主要目的要素和辅助目的要素①主要目的要素:磨,切削,装配,分割等②辅助目的要素:夹配件,放材料等(3)作业分为作业者要素及设备要素;比如以机加工为中心的作业时又分为人的作业时间和设备作业时间。
(4)尽可能把要素作业分为不同的目的;比如加工、移动、检查、等待等。
(5)分为规则要素及不规则要素①规则要素:每一个作业或一个周期所发生的要素。
例:把配件安装在设备上,把配件从设备上拆除。
②不规则要素:作业中需要,但跟规则或基本要素作业的周期相比无规则间距所发生的因素。
例:用测试仪测数据,刷掉刀架上的铁屑等。
☺首先对测试对象进行充分的预备调查。
(1) 调查对象作业是否正常地按规定进行。
(2) 调查材料是否与正规的一致。
(3)调查是否使用规定的设备设备或工具。
(4) 调查现场配置是否处于规定的状态。
(5) 其它条件是否在规定的状态下进行。
IE标准工时介绍

IE标准工时介绍什么是IE标准工时?IE标准工时是一种常用于生产管理的指标,用来衡量一个工艺、工序或整个生产线完成一定数量产品所需要的标准时间。
IE,即工业工程师(Industrial Engineer)的缩写,是专门负责工序分析和工作方式改善的职位。
在生产环境中,IE标准工时可以被应用于多个方面,例如生产计划制定、过程优化、工时成本计算等。
它提供了衡量生产效率和工时成本的重要依据,对于企业提高生产效率和控制成本具有重要意义。
IE标准工时的计算方法IE标准工时的计算方法通常分为直接计时和间接计时两种方式。
具体计算方法如下:直接计时直接计时是通过对工艺工序的实际操作进行计时,以确定完成一定数量产品所需的平均时间。
这种计算方法需要IE工程师实地观察并记录工人完成一次工序所需的时间,并取得多次实测数据的平均值。
直接计时方法适用于工序比较简单、固定以及操作规程稳定的生产环境。
间接计时间接计时是通过对整个生产过程中的各个环节进行观察和分析,结合历史数据和标准工时数据库,计算得出每个环节所需的标准工时。
间接计时方法适用于复杂的生产流程、多个工序交替进行的情况。
IE工程师通过分析工艺流程图、工序操作说明和人员配备情况,综合考虑诸多因素,包括机器间距离、工种经验、设备效率等,计算出各个环节的标准工时。
这些标准工时最终汇总起来,形成整个生产过程所需的标准工时。
IE标准工时的应用IE标准工时在生产管理中具有广泛的应用价值,主要体现在以下几个方面:生产计划制定通过标准工时的衡量,可以确定生产计划的合理性和可行性。
生产计划制定时,需要考虑生产能力、资源配备、工时成本等因素,IE标准工时提供了一个客观的指标,帮助管理者进行决策。
过程优化通过对每个环节的标准工时进行分析,可以找出生产过程中的瓶颈和低效环节,进而优化生产流程,提高生产效率。
IE工程师可以通过分析数据和观察现场,提出改进建议,例如优化工艺流程、提高设备效率、优化人员分配等。
IE7大手法

IE七大手法百科名片IE(工业工程)七大手法是企业内部IE人员或其他人员用来进行流程或其他活动改善的基本手法(工具)。
目录简介版本内容使用目的简介版本内容使用目的展开编辑本段简介“IE”是应用科学及社会学的知识,以合理化、舒适化的途径来改善我们工作的品质及效率,以达到提高生产力,增进公司之利润,进而使公司能长期的生存发展,个人的前途也有寄托之所在。
因此,简单地说“IE”就是代表“合理化及改善”的意义,为了顾及记忆的方便,我们就以中文“改善”来代表“IE”的含义。
编辑本段版本IE七大手法的归纳有很多版本,主要有以下几种:一、基础IE里的内容:IE手法包括:方法研究(程序分析、动作分析),作业测定,布置研究,Line Balance等,但不够七个。
在现场IE里,IE七大手法包括:程序分析、动作分析,搬运分析,动作经济原则,作业测定,布置研究,Line Balance。
二、台湾公司的教材里1、工程分析。
2、搬运工程分析。
3、运动分析(工作抽查)4、生产线平衡。
5、动作分析。
6、动作经济原则。
7、工厂布置改善。
三、其它的各种说法:1、IE七大手法为:作业分析、程序分析(运用ECRS技巧)、动作分析(动作经济原则)、时间分析、稼动分析、布置搬动分析、生产线平衡2、IE七大手法:流程分析法、动作分析法、动作经济原则、时间研究、工作抽查法、人机配置法、工作简化法3、IE七大手法:动作改善法(动改法)、防止错误法(防错法)、5*5W1H 法(五五法)、双手操作法(双手法)、人机配合法(人机法)、流程程序法(流程法)、工作抽样法(抽样法)4、IE七大手法:程序分析、时间分析、动作分析、流水线分析、稼动分析、物料分析、环境分析。
其中最常用的IE七大手法为:防错法、动改法、流程法、五五法、人机法、双手法和抽样法。
编辑本段内容防错法又称防愚法、愚巧法(Poka-yaka),其意义即是防止愚笨的人做错事。
防错法主要探讨如何避免做错事情,使工作第一次就做好的精神能够具体实现。
- 1、下载文档前请自行甄别文档内容的完整性,平台不提供额外的编辑、内容补充、找答案等附加服务。
- 2、"仅部分预览"的文档,不可在线预览部分如存在完整性等问题,可反馈申请退款(可完整预览的文档不适用该条件!)。
- 3、如文档侵犯您的权益,请联系客服反馈,我们会尽快为您处理(人工客服工作时间:9:00-18:30)。
4、工业工程意识
(1)增值与非增值
(2)成本和效率意识
(3)问题和改善意识
分析:现场七大浪费分析
第二章工艺程序分析
1、程序分析的概念、特点和目的
2、程序分析的四大基本要素及表示符号
3、流程分析的步骤:流程图,数据收集,流程分析,改善方案,标准化
4、工艺程序分析案例:改善四原则ECRS;
5、作业流程程序分析案例:减少工序数量,缩短总作业时间
6、布置和经路分析
7、生产线平衡技巧与改善
案例:合成型工艺程序图分析
案例:直列型工艺程序图分析
案例:分解型工艺程序图分析
案例:复合型工艺程序图分析
案例:流程法案例解析
案例:外购件接收、检验入库线路图案例:生产线平衡步骤案例分析
第三章人—机工艺动作分析
1、人—机操作分析的含义
2、人—机操作分析的主要过程
3、人—机操作分析图
4、人—机操作分析应用实例分析;
5、一人一机动作分析
6、一人多机动作分析
案例:机加工人—机操作案例分析
案例:车外圆一人多机操作案例分析案例:沖压作业的人机作业图的绘制第四章联合工艺动作分析
1、联合操作分析的过程
2、联合操作分析图
3、联合作业分析的基本原则
案例:叉车搬运联合作业图的绘制
案例:汽车装配工序联合作业视频案例第五章双手工艺动作分析
1、双手操作分析的作用
2、双手作业分析图
3、双手操作分析图实例分析
案例:切割作业双手操作改善案例
第六章动作分析经济原则
1、动作分析的目的与改善顺序
2、动作分析的要领
3、目视动作观察法
4、影像动作观察法
5、动素与动素分析
6、动素分析的应用实例
7、动作经济的四条基本原则
8、动作经济原则:12种动作浪费
案例:电阻元件插入电路板的动素分析表案例:手的动作等级视频案例分析
实例:通过改变作业顺序减少涂漆作业实例:改变机器的操作位置缩短动作距离实例:利用惯性力分离工件的切屑
实例:利用高度调整机构固定作业高度
第七章工艺动作时间研究方法之——秒表法
1、时间研究目的与方法:秒表,记录表,流程分解原则
2、秒表时间研究的工具
3、秒表时间研究步骤
4、作业分解——划分操作单元
5、秒表测时的方法:连续测时法、归零测时法、累计测时法
6、标准时间的构成与计算
案例:秒表测时基本格式实例
第八章工艺动作时间研究方法之——工作抽样
1、工作抽样是对工作时间及工作状态进行瞬时观测
2、工作抽样的方法和步骤
3、确定观测路径
4、设计工作抽样观测表
5、确定观测期间及一天的观测次数
6、观测数据的整理与分析
案例:机械设备开动率观测数据
第九章工艺动作时间研究之——模特排时法(MOD)
1、模特法的基本原理
2、模特法的特点
3、模特法的动作分类
4、模特法的动作分析
5、模特法动作改进
6、模特法应用案例
案例:成对MOD动作分析
案例:反射MOD动作分析
案例:同时MOD动作分析
案例:MOD动作分析实例
第八章工艺标准化作业
1、标准作业再发防止
2、防错的机制
3、防错十大原理
案例:防错案例分析。