冲天炉熔炼工艺操作规程
冲天炉熔炼安全操作规程
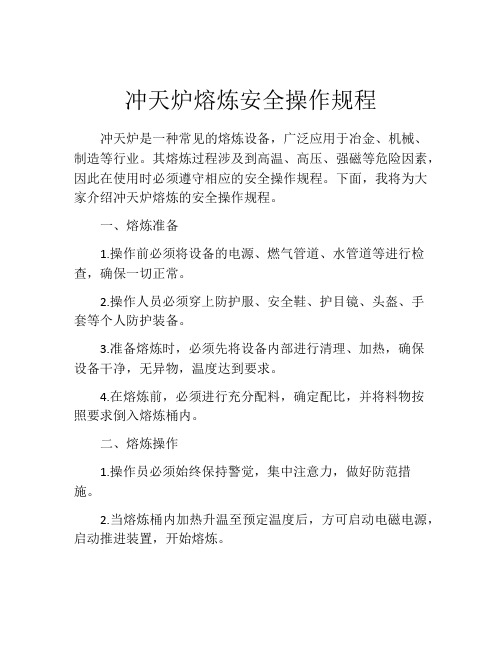
冲天炉熔炼安全操作规程冲天炉是一种常见的熔炼设备,广泛应用于冶金、机械、制造等行业。
其熔炼过程涉及到高温、高压、强磁等危险因素,因此在使用时必须遵守相应的安全操作规程。
下面,我将为大家介绍冲天炉熔炼的安全操作规程。
一、熔炼准备1.操作前必须将设备的电源、燃气管道、水管道等进行检查,确保一切正常。
2.操作人员必须穿上防护服、安全鞋、护目镜、头盔、手套等个人防护装备。
3.准备熔炼时,必须先将设备内部进行清理、加热,确保设备干净,无异物,温度达到要求。
4.在熔炼前,必须进行充分配料,确定配比,并将料物按照要求倒入熔炼桶内。
二、熔炼操作1.操作员必须始终保持警觉,集中注意力,做好防范措施。
2.当熔炼桶内加热升温至预定温度后,方可启动电磁电源,启动推进装置,开始熔炼。
3.操作员必须时刻关注设备运行情况,确保其正常运转、熔炼效果良好。
4.操作过程中必须保持适当的熔炼压力和速度,以充分熔化物料,并控制物质燃烧速度,防止设备损坏。
5.若发现设备出现异常,必须立即停机,排除故障。
如遇重大事故,应立即通知有关部门,做好报告和应急处理。
三、操作结束1.熔炼完成后,必须关闭电源、燃气管道及推进装置,将设备恢复到初始状态。
2.设备内残留的物料必须清理干净,避免对设备造成损坏。
3.设备必须经过检查,确认安全后方可下线。
以上就是冲天炉熔炼安全操作规程的基本内容。
在熔炼过程中,操作员必须时刻保持警觉,秉持安全第一的原则,保护好自己和周围的人员安全。
同时,也需要加强设备的保养和维护,做好熔炼前的准备工作,确保设备正常运转,从而最大程度地避免事故发生。
冲天炉熔炼工艺规程
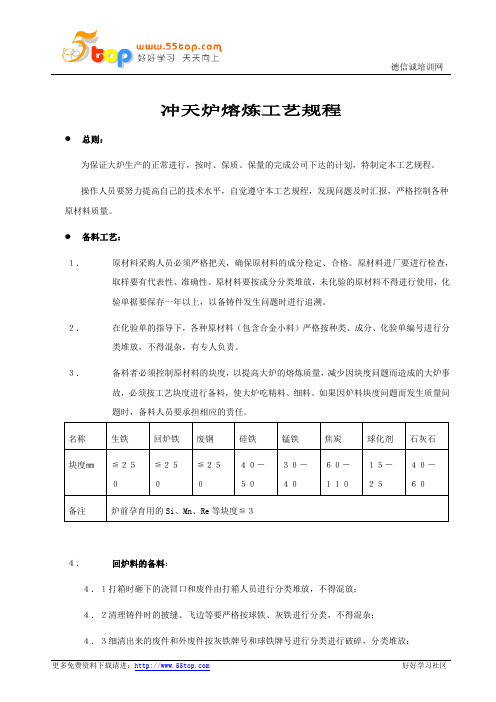
冲天炉熔炼工艺规程●总则:为保证大炉生产的正常进行,按时、保质、保量的完成公司下达的计划,特制定本工艺规程。
操作人员要努力提高自己的技术水平,自觉遵守本工艺规程,发现问题及时汇报,严格控制各种原材料质量。
●备料工艺:1.原材料采购人员必须严格把关,确保原材料的成分稳定、合格。
原材料进厂要进行检查,取样要有代表性、准确性。
原材料要按成分分类堆放,未化验的原材料不得进行使用,化验单据要保存一年以上,以备铸件发生问题时进行追溯。
2.在化验单的指导下,各种原材料(包含合金小料)严格按种类、成分、化验单编号进行分类堆放,不得混杂,有专人负责。
3.备料者必须控制原材料的块度,以提高大炉的熔炼质量,减少因块度问题而造成的大炉事故,必须按工艺块度进行备料,使大炉吃精料、细料。
如果因炉料块度问题而发生质量问题时,备料人员要承担相应的责任。
4.回炉料的备料:4.1打箱时砸下的浇冒口和废件由打箱人员进行分类堆放,不得混放;4.2清理铸件时的披缝、飞边等要严格按球铁、灰铁进行分类,不得混杂;4.3细清出来的废件和外废件按灰铁牌号和球铁牌号进行分类进行破碎,分类堆放;4.4外购的回炉铁,应进行化验后根据成分进行分类堆放,成分特殊时,应进行评审师是否能使用?如果成分特殊要进行特殊放置;4.5破碎铁要按照块度进行破碎,破碎人员要负责料场的管理,分类明确,质量合格。
4.6大炉返回的铁水饼及条铁,由大炉人员进行分类堆放或按照牌号加入料桶内;5.废钢、生铁的备料:5.1生铁必须破碎成单块,按照种类、牌号、化验单分类堆放;5.2废钢备料人员不得备用块度超标的废钢,废钢中不得有危险的容器、及不明物。
废钢的成分要求稳定、单一,废钢的厚度要大于3㎜,不得有严重的锈蚀、氧化;高Mn、Cr废钢要单独堆放,单独配料,杜绝混料,以免造成铸件的报废。
修炉、修包工艺:1.修后炉:1.1修炉前必须做好一切准备工作,检查上料口及周围、上料设施的情况,并将其清扫干净,确保设备及人员的安全;1.2修后炉时首先清除炉膛内部的挂渣,特别时风口及其周围的部分,熔化带以上不许修补的部位,如有挂渣、凸起应清除干净。
冲天炉熔炼操作工艺
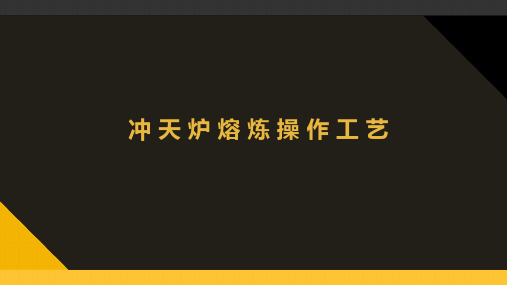
(7)熔化及控制
熔化初期应经常疏通风口,以保证风口畅通,观察并记录风量、风压的变化。从正式送风开始8~10min,在第一排风口可看到铁液滴快速下落,说明底焦高度合适。若大于10min,说明底焦高度偏高,应适当降低层焦量;若小于8min,说明底焦高度偏低,应适当增加层焦量,直至从风口看到底焦燃烧正常。冲天炉是连续熔化,应保证连续加料,始终保持炉料满炉 以满足炉料的充分预热,这对保证铁液温度稳定是很重要的。根据配料单,及时调整配料比例,每次调整前,应加一批隔离焦,处理好交界铁液。
冲天炉正常操作过程
(8)停风打炉
THANKS
冲天炉ห้องสมุดไป่ตู้炼操作工艺
A
燃料与原材料的选用
B
操作参数的选定
C
操作过程各个环节的控制
冲天炉熔炼操作工艺
冲天炉正常操作过程
(1)修炉
铲除炉壁表面残渣挂铁
刷上泥浆水
覆上修炉材料,敲打结实
修炉材料组成
40%~50%耐火泥
适量的水分
60%~50%石英砂
冲天炉正常操作过程
(1)修炉
修前炉则用老煤粉与耐火泥的混合料
结构紧实
尺寸正确
表面光滑
冲天炉正常操作过程
(2)烘炉
炉子修毕后,可在炉底和前炉装入木柴,引火烘炉;前炉必须烘透,以保证首包铁液温度。
(3)点火
烘炉后,开风前2.5~3h加入木柴,引火点着,并敞开风口盖作自然通风
冲天炉正常操作过程
(4)加底焦
待木柴燃旺后,由加料口往炉内加入三分之一的底焦,待其烧着后,再加入约一半左右的底焦,然后鼓小风几分钟,并测定底焦高度,再加底焦至规定的高度。这里的所谓底焦量,是指装入金属炉料以前加入炉内的全部焦炭量,而底焦高度则是从第一排风口中心线起,至底焦顶面为止的那一部分高度,炉缸内的底焦是不包括在底焦高度内的。
冲天炉熔炼安全操作规程模版

冲天炉熔炼安全操作规程模版一、概述本安全操作规程旨在规范冲天炉熔炼过程中的安全操作措施,保障人员和设备的安全。
所有从事冲天炉熔炼操作的人员必须遵守此规程。
二、安全准备1. 在进行冲天炉熔炼前,必须进行安全检查,确保设备正常运行,消防器材齐全并处于可用状态。
2. 所有从事熔炼作业的人员必须穿戴合适的个人防护装备,包括防火服、耐热手套、防护眼镜、耐酸碱靴等。
3. 了解熔炼物料的安全性质和危险特性,做好相应的防护措施。
三、操作要点1. 根据熔炼工艺要求,准备好所需的物料,并按照标准比例进行配料,确保配料的准确性和稳定性。
2. 在装料前,需检查熔炼炉的密闭性,确保无漏风现象。
3. 严禁将易燃物品或其他危险物品放置在炉周范围内,以避免引发火灾或爆炸。
4. 老化炉皮和冶炼渣应及时清理,以确保炉腔的正常使用。
5. 在熔炼过程中,应确保炉腔内的温度、压力和熔体的流动情况处于正常范围内。
如发现异常情况,应及时停机排查。
6. 操作人员在熔炼过程中应保持警觉,严禁戏水、嬉戏或与他人不当言行,确保操作专注和安全。
7. 熔炼过程中,操作人员应保持良好的通讯,及时与其他相关人员进行沟通,确保信息的畅通。
8. 在换班或作业结束时,需要对熔炼炉进行全面检查,确保设备和场地的安全。
四、紧急处理1. 发生火灾时,操作人员应立即拉响警钟,并按照紧急处理程序启动事故应急预案。
2. 发生气体泄漏或毒气中毒事故时,立即撤离现场,并通知专业人员进行处理。
3. 发生人身伤害事故时,立即寻求医疗救助,并向相关主管报告事故情况。
五、消防安全1. 冲天炉熔炼现场应配备足够数量的消防器材,并定期进行检查和维护。
2. 熔炼过程中,操作人员应保持消防通道畅通,严禁堆放易燃物品。
3. 熔炼过程中如发现明火或火星飞溅,应立即采取措施进行扑灭和防止火势扩大。
六、废弃物处理1. 废弃物应按照相关规定进行分类、封装和储存,并交由专门处理机构进行处理。
2. 废弃物处理记录应详细填写,并定期归档保存。
冲天炉铸造过程中安全操作规程(3篇)

冲天炉铸造过程中安全操作规程冲天炉是一种用于炼铁、炼钢等冶金熔炼过程的重要设备,但由于其操作过程涉及高温、高压、易燃等安全风险,因此需要制定一系列的安全操作规程,以确保人员安全和生产顺利进行。
以下是冲天炉铸造过程中的安全操作规程,共计____字:一、冲天炉基本安全操作规程1. 操作人员必须经过相应的技术培训,并持有相关的操作证书,方可从事冲天炉操作工作。
2. 在进入冲天炉作业区域前,必须戴上符合标准的防护帽、耐高温手套、防护眼镜、防护口罩等个人防护装备。
3. 在操作过程中,严禁饮酒、嚼槟榔等妨碍工作安全的行为。
4. 进入冲天炉作业区域前,必须检查有关设备和安全装置是否正常运行。
5. 炉前设有警示牌和安全标志的位置,不得随意移动或遮挡。
6. 严禁在冲天炉作业区域内吸烟或使用明火。
7. 操作人员在离开冲天炉作业区域前,必须停止设备运行,并将电源关闭。
8. 发现安全事故隐患或紧急情况时,应立即进行报警,并采取必要的安全措施。
9. 在冲天炉作业结束后,必须进行设备检查、清理和维护,确保设备安全。
二、冲天炉高温操作安全操作规程1. 操作人员必须戴上符合标准的高温防护服、耐高温手套、耐高温防护鞋等个人防护装备。
2. 在操作过程中,禁止随意触摸或接触高温部件,以免导致烫伤。
3. 炉体内温度高,操作人员不得长时间停留在炉旁,以免受热过度。
4. 在操作过程中,操作人员应保持清醒和注意力集中,以防意外发生。
5. 在高温操作过程中,必须经常检查冲天炉设备和管道的温度状况,如发现异常应及时采取措施。
6. 炉体内产生的高温气体和废气必须通过合适的通风设备进行排放。
7. 禁止将易燃物品置于冲天炉附近,以防高温引发火灾。
8. 结束高温操作后,必须等待冲天炉完全冷却后再进行设备检查和维护。
三、冲天炉高压操作安全操作规程1. 操作人员在进入冲天炉作业区域前,必须检查高压设备和管道的工作状态是否正常。
2. 炉体内的高压气体和流体必须遵循相关操作规程和安全标准进行控制和释放。
冲天炉熔炼工序工艺规程
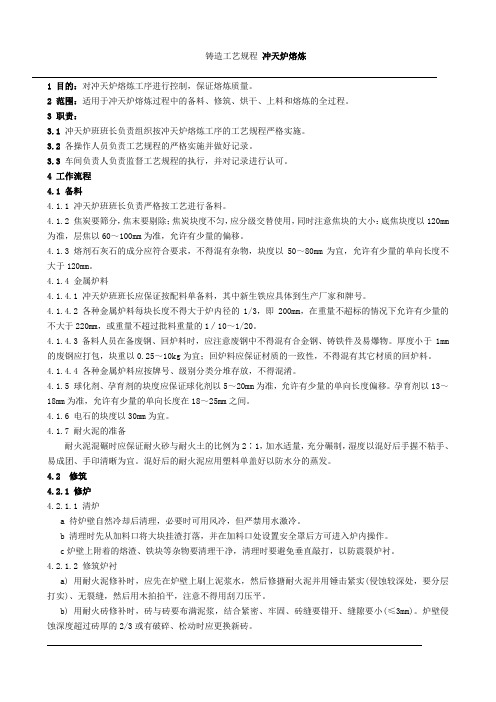
铸造工艺规程冲天炉熔炼1 目的:对冲天炉熔炼工序进行控制,保证熔炼质量。
2 范围:适用于冲天炉熔炼过程中的备料、修筑、烘干、上料和熔炼的全过程。
3 职责:3.1冲天炉班班长负责组织按冲天炉熔炼工序的工艺规程严格实施。
3.2各操作人员负责工艺规程的严格实施并做好记录。
3.3车间负责人负责监督工艺规程的执行,并对记录进行认可。
4 工作流程4.1 备料4.1.1 冲天炉班班长负责严格按工艺进行备料。
4.1.2 焦炭要筛分,焦末要剔除;焦炭块度不匀,应分级交替使用,同时注意焦块的大小:底焦块度以120mm 为准,层焦以60~100mm为准,允许有少量的偏移。
4.1.3 熔剂石灰石的成分应符合要求,不得混有杂物,块度以50~80mm为宜,允许有少量的单向长度不大于120mm。
4.1.4 金属炉料4.1.4.1 冲天炉班班长应保证按配料单备料,其中新生铁应具体到生产厂家和牌号。
4.1.4.2 各种金属炉料每块长度不得大于炉内径的1/3,即200mm,在重量不超标的情况下允许有少量的不大于220mm,或重量不超过批料重量的1∕10~1/20。
4.1.4.3备料人员在备废钢、回炉料时,应注意废钢中不得混有合金钢、铸铁件及易爆物。
厚度小于1mm 的废钢应打包,块重以0.25~10kg为宜;回炉料应保证材质的一致性,不得混有其它材质的回炉料。
4.1.4.4 各种金属炉料应按牌号、级别分类分堆存放,不得混淆。
4.1.5 球化剂、孕育剂的块度应保证球化剂以5~20mm为准,允许有少量的单向长度偏移。
孕育剂以13~18mm为准,允许有少量的单向长度在18~25mm之间。
4.1.6 电石的块度以30mm为宜。
4.1.7 耐火泥的准备耐火泥混碾时应保证耐火砂与耐火土的比例为2∶1,加水适量,充分碾制,湿度以混好后手握不粘手、易成团、手印清晰为宜。
混好后的耐火泥应用塑料单盖好以防水分的蒸发。
4.2 修筑4.2.1 修炉4.2.1.1 清炉a 待炉壁自然冷却后清理,必要时可用风冷,但严禁用水激冷。
冲天炉操作规程
冲天炉操作规程
《冲天炉操作规程》
冲天炉是一种用于冶炼金属的设备,其操作规程对保证安全生产和生产效率起着至关重要的作用。
下面是冲天炉操作规程的相关内容。
一、操作前准备
1. 检查冲天炉设备及周围环境,保证设备完好无损。
2. 检查工艺用水、燃料和炉料,确保充足。
3. 检查安全设施和消防器材,确保完好有效。
二、启动冲天炉
1. 严格按照操作手册的要求操作,按照程序启动冲天炉。
2. 观察炉内燃料着火情况,确保点火顺利。
三、冶炼过程
1. 在冶炼过程中,要严格按照工艺要求投放炉料和燃料,确保冶炼质量。
2. 定时对炉内温度和压力进行监控,及时调整操作参数,确保冶炼过程平稳进行。
四、冶炼结束
1. 冶炼结束时,要及时停止投放炉料和燃料,将熔炼好的金属材料取出。
2. 关闭冲天炉前,要彻底清理炉内渣和灰,保证设备的清洁。
五、安全操作
1. 操作人员要严格遵守操作规程,不得擅自更改操作流程。
2. 在操作过程中,要严格遵守安全操作规定,确保人身安全。
3. 发现设备异常或安全隐患时,要及时上报,并停止冶炼操作。
《冲天炉操作规程》的制定和执行,能够在一定程度上提高冶炼生产效率,保护设备和人员的安全。
希望所有操作人员严格遵守规程,确保冲天炉设备的正常运行和生产的顺利进行。
冲天炉熔炼操作规程
冲天炉熔炼操作规程一、修炉1、修炉前要在加料口设防护铁板,避免掉物伤人。
修炉要使用36V安全电灯。
2、清除炉壁上粘附的铁块、熔渣。
3、按炉膛尺寸要求砌砖,砖与砖之间配合紧密牢固;泥口缝隙要小于2mm,砖缝用炉料塞实,保证风眼角度和尺寸要求。
4、炉底用型砂逐层夯实,硬度要均匀。
底与炉壁形成圆角,做好向过桥倾斜角度,出铁口呈喇叭口形。
5、铁水槽要修的光滑平整,刷上一层涂料烤干。
二、点火与烘炉1、点火到熔化时间约1.5小时,点火后风眼全部打开,并用小风机吹风助燃木柴,而后上后上1/2的底焦。
底焦应严格的手工挑选块度在100-180mm。
2、待第一批焦炭烧红后,加第二批焦炭剩余的1/2的底焦。
将后炉门封死,为了提高烘炉质量,使炉壁完全干燥,而后开鼓风机送少量的风助燃焦炭,约10分钟左右,焦炭烧红后,关闭风机,清除前炉里的炉灰,盖好炉盖上料。
三、上料1、上料人员应提前将称提前调好,掌握自己所上的品种规格重量。
2、上第一批料的石灰石用量是正常用量的2.5倍。
炉料长度不要大于炉经的1/3,炉料中不得混有轴承钢、密封金属罐。
3、上满炉料后,预热炉料30分钟开始溶化,开风半分钟后关闭风眼。
4、密切关注前炉观查孔,禁止上大料。
使炉内保持充满状态,使炉料能够充分预热。
5、大炉操作人员在大炉溶化时,随时观察风眼变化,使风眼保持明亮畅通。
6、更换新材料牌号时,应加隔焦,是正常层焦的2倍。
四、打炉1、停炉前先打开风眼观察孔,而后停风。
2、炉底不得有积水,应提前铺好一层干砂防止铁水飞溅。
3、炉料落炉后,材料分清走。
五、风机操作的有关注意事项1、每次开车前必须检查润滑是否适量,新风机运行100小时后,更换润滑剂,以后每半年检查一次,检修、跟换润滑剂,平时不需要填加润滑剂。
2、开车前盘车三转。
冲天炉熔炼安全操作规程
冲天炉熔炼安全操作规程13、吊炉前盖时必须挂牢,人离开后再起吊。
上各种金属炉料时严禁混夹易燃易爆物品投炉,不能有封闭的压力容器和管子等炉料上炉避免出现危险。
.17.14、冲天炉炉内发生“棚料”严重时,应立即停风打开风眼出净炉渣和铁水,用铁棒撞击(拔捅)料层。
排除“棚料”后,应补加焦炭复风继续熔炼。
15、如出现炉壳、前炉、铁水包发红时,视其情况如面积不大可用湿麻袋贴敷或吹风冷却。
如发红面积大(发亮)则应停炉处理。
16、停风打炉时,必须放净铁水和炉渣,清理熔炼周围场地应没有明水,在炉底下面垫上一层干砂,并在炉底门打开时必须迅速撤离到安全位置上,打炉垮下的炉料必须专人现场注水湿透,防止复燃烧损焦炭及发生火灾。
注水时操作者应离炉料保持一定距离,以免水蒸气伤人。
17、熔炼工作完毕后,保持炉子周围场地整洁通道畅通,无安全隐患后方可离开现场。
18、在开炉前、开炉中、打炉时、打炉后,应注意蓄水池、炉前坑、排渣沟及在周边操作安全,防止跌倒滑落伤害。
19、行车吊包吊铁水时要专人指挥,钩好起吊时吊包下面和旁边近距离严禁站人。
20、注意吊包(浇包)行车与浇注操作人员的协调配合,行车吊铁水包运行时要匀速缓慢平稳,防止铁水发生共振和浇注时铁水飞溅伤人。
21、注意浇注摇包用电安全,防止按钮开关、电缆线、因破损发生漏电事故。
22、操作浇注摇铁水按钮开关人员应预先在砂箱适当位置站稳。
同时稳定摇包减速机转盘人员也应在活动站台上站稳扶好铁水包。
行车工、浇注工要集中注意力,相互配合,平稳浇注,确保浇注安全。
23、铁水浇注前或浇注中应有专人监视指挥,非操作人员不得站在浇注现场.18.观看滞留。
24、当浇注途中砂箱跑铁水时应有专人有条不紊地予以处置堵漏,防止漏铁水接触到电器或电源上,以防触电或烧伤事故发生。
25、冲天炉在熔炼过程中各岗位各工种操作人员严禁违章违规操作。
因操作人员违章违规操作对设备的损坏及人员伤害事故均由当事人负责。
冲天炉熔炼设备操作规程
冲天炉熔炼设备操作规程1目的规范冲天炉熔炼的生产过程,确保提供温度和成分都符合要求的铁水,防止和消除熔炼过程中可能出现的各种故障。
2适用范围适用于公司冲天炉铸造铁水的熔炼。
3工艺规定3.1 备料3.1.1焦碳、生铁、铁合金、石灰石等材料的成分,性能及其它质量指标必须经技检部检验合格后使用。
3.1.2金属料的最大尺寸不得超过加料口附近炉径的三分之一。
3.1.3废钢、回炉铁锈蚀严重的必须处理方可投炉。
3.1.4 各类炉料分类堆放,不得混杂,未经处理的弹壳,废枪支等危险物不得混入,防止橡胶、塑料等有害杂物的投炉。
3.1.5 各类炉料保持干燥、洁净,防止附着泥砂。
3.1.6 铁合金的粒度为20—80mm,如受潮应烘干后使用。
3.1.7 孕育剂干净无水分,粒度为5—10mm。
3.2铸造工艺配方为确保刹车盘的铸造材质,满足GB/T9439—1988、JB/T7945—1955中关于HT250之规定,针对客户要求,结合本公司生产实际特制定冲天炉配方(冲天炉分配方B、配方B):冲天炉熔炼配方B:采用固定的张店14#原料铁冲天炉熔炼配方B:3.3修炉与烘炉:3.3.1 修炉须在大炉冷却后进行,必要时可鼓风吹冷,但不得用水浇冷。
3.3.2 冲天炉修炉时,先铲除炉壁表面的残渣挂铁,小于半块或破碎松动的耐火砖换成新砖,清理时避免水平或过重敲击,耐火砖的接触面要涂满耐火泥,贴合紧密,砖缝要小于2mm,上下砖缝必须错开,然后刷上泥浆水,覆上修炉材料,并用锤敲打结实,修炉材料由40—50%耐火泥和60—50%石英砂及适量的水泥混制而成,炉膛尺寸,风口大小,形状、斜度、位置应符合工艺要求。
3.3.3 修前炉使用老煤粉与耐火泥的混合料,炉壁必须结构紧实,尺寸正确,表面光滑。
3.3.4 炉壁与炉底交界处应修出半径为40—60mm的园角,并向出铁口方向倾斜5°—6°。
3.3.5 过桥保持平直并与观察孔在同一直线上。
- 1、下载文档前请自行甄别文档内容的完整性,平台不提供额外的编辑、内容补充、找答案等附加服务。
- 2、"仅部分预览"的文档,不可在线预览部分如存在完整性等问题,可反馈申请退款(可完整预览的文档不适用该条件!)。
- 3、如文档侵犯您的权益,请联系客服反馈,我们会尽快为您处理(人工客服工作时间:9:00-18:30)。
冲天炉熔炼工艺规程
1、范围
本规程规定了冲天炉熔炼的炉料准备、装炉、炉前控制、质量控制、熔炼球铁、修炉和修包。
本规程适用于冲天炉熔炼灰铸铁和球墨铸铁。
2、炉料准备
2.1、焦碳
2.1.1焦碳块度:底焦100mm~150mm、层焦大于60mm。
焦碳应分类存放。
2.1.2焦碳的硫分含量小于或等于1.0%,灰分含量小于或等于1
3.5%,水分含量小于或等于5%。
2.1.3焦碳应存放于棚内,不应受风、雨、雪等侵蚀,不应混有其它物质。
2.2金属材料
2.2.1金属炉料的长度不大于熔炉加料口处最小直径的三分之一,重量在25公斤以下。
2.2.2废钢表面应干燥、清洁、无严重锈蚀、无泥砂杂物,不应有密闭容器。
重量在0.10公斤~5公斤、厚度小于1mm的应打包。
2.2.3生铁屑应压块使用,块度约φ155mm×60mm,重约7公斤。
2.2.4加入炉内的硅铁块度应小于70mm,最小不小于20mm,铁合金应避免潮湿。
2.2.5严禁危险物及其它有害物质混入炉料。
2.3孕育剂和球化剂
2.3.1硅铁含硅量及球化剂的硅、镁含量应符合标准。
2.3.2硅铁和球化剂应存放在干燥处,防止受潮。
2.3.3硅铁粒度为3mm~8mm,粉状硅铁和粉化球化剂不能使用。
2.4熔剂
2.4.1各种熔剂块度20mm~60mm,最大块度不大于80mm。
2.4.2石灰石中氧化钙不低于85%,不应混有泥土、砂石等有害杂质。
2.5耐火砖及点火木材应符合标准规定。
2.5.1耐火砖不应有疏松、裂纹、不合格的不能使用。
2.5.2耐火砖应放在棚内。
2.5.3潮湿木材和刨花不能使用,长度应小于500mm,高和宽应小于200mm。
3、装炉
3.1炉底、炉壁烘干后,铺上刨花,再装入木材,然后打开风口,点火。
加入底焦总量的40%~60%,,
等全部烧着后再加入余下底焦,随后短时鼓风,吹净灰分,趟透过桥,并从风口处观察和测量底焦高度、进行调整。
3.2装料时注意炉料均匀分布,在熔化过程中使炉料料柱与装料口平齐。
3.3严格按配料规定加料。
加料应过秤,称量允差为5%,并做好装料记录。
3.4装料顺序:焦碳、熔剂、回炉铁及铁屑、生铁、铁合金、废钢。
3.5焦碳加入量根据焦耗及铁水温度进行调整。
3.6严格遵守各种牌号铸铁的炉料配比,未经班组长、技术员同意,不能随意变更炉料。
3.7发生搭棚现象时,装炉工要立即报告班组长,不应无故停风。
3.8停止装料应经班组长许可。
3.9装料完毕,应加压铁,压铁层数不能超过两层。
3.10无论开始送风或停止送风都应先把风口盖打开,方能开动或停止风机。
4、炉前控制
4.1点火前应打开风口,开炉前应准备好炉前用的各种工具及各种炉前处理合金。
4.2应保持风量计的完好正常,开风后15分钟内应随时注意风量、风压及加氧量等数值与波动。
送氧应在开风5分钟以后,铁料开始熔化时进行,送氧后风量相应减少到规定值。
4.3风眼必须经常保持明亮,遇有严重结渣,应马上清除,清理风口时不能停风,不能同时捅两个风口,注意铁水熔化速度及温度,以便随时调整风量,加氧风口应随时注意氧枪喷嘴与焦碳距离变化,发现异常及时调节。
4.4出铁槽应经常保持清洁,不应有冷铁在内。
4.5风带内进风口附近的铁渣应在开风前清理干净。
4.6处理交界铁水时,前批料应在后批料下来前出清。
交界铁水降级使用,浇注不重要铸件。
4.7熔化后期应减小风量,未经班组长同意不能任意停风。
中途停氧之后应补足底焦并调整风量到正常值,同时将氧枪喷嘴与焦碳距离调到最大。
5、质量控制
5.1开炉点火前对各种使用的原材料按工艺规定进行检查。
5.2开炉后记录各项工艺控制参数,并及时通知炉前控制工。
5.3对铁水温度进行检查,前期出炉温度不低于1400℃,中期出炉温度不低于1440℃,后期不低于1420℃,铁水浇注温度为1300℃~1450℃,薄壁件小件取上限,厚大件取下限。
5.4浇注三角试片及机械性能试棒的砂型均应与铸型相类似,且应具有代表性。
5.5铁水浇入三角试块铸型后,待到暗红色时,取出侵入水中,然后击断,检验试块断口的白口深度
(或宽度),如不符合规定应马上采取处理措施。
5.6在熔化高牌号铸铁时,开风后第一批铁水作废或浇注要求不高的铸件。
铸铁的化学成分及机械性能应符合表1的规定。
表1 铸铁的化学成分及机械性能
6、碱性冲天熔炼球墨铸铁(以下简称球铁)
6.1熔化
6.1.1球铁用原材料应在第5~7批料开始加,石灰石加入量应不少于批焦量的二分之一.
6.1.2球铁配料用生铁含磷量≤0.06%,含硫量≤0.03%。
6.1.3球铁出铁温度应控制在1400℃~1460℃。
当低于此范围时,不能浇注小件和薄壁件;当高于1460℃时应注意合金的覆盖与捣实。
6.2球化处理
6.2.1球化处理采用包内冲入法。
6.2.2用稀土镁硅铁合金作球化剂时,使用前应将碎块、粉末筛除,球花剂加入量为该包铁水的1.6~2.2%。
6.2.3球化反应时间:从第一次堵出铁口开始计,应控制在1~2分钟,严防球化不良。
待反应基本停止,立即补满铁水,吊出进行扒渣;当浇包高度超过1.6m时,也可一次将铁水装满浇包进行处理。
6.3扒渣
6.3.1用专用扒渣工具将铁水表面渣子扒净,立即覆盖草灰1~2锹。
稍加搅拌后进行二次扒渣,应将渣扒净以防止“回硫”。
6.3.2扒渣时应使包向后倾斜,从包后面扒出渣子,不能从包嘴处扒渣,以免损坏包嘴。
6.4孕育处理
6.4.1一次孕育:使用75#硅铁,粒度5mm~20mm。
加入量为铁水重量的0.6%~0.8%。
使用时覆盖在球化剂上面。
6.4.2二次孕育;使用75#硅铁,每块重约0.5Kg~3.5Kg,厚度≤70mm。
加入量为铁水总重的0.4%~0.6%。
加入时轻放在铁水表面,并用铁棍轻点助熔,不应搅拌铁水面,待其开始发红熔化即覆盖草灰或珍珠岩准备浇注。
6.5炉前球化检验
采用火苗法、三角试块法和快速金相法进行检验。
6.6浇注
6.6.1浇注前撇渣时,不应将浮硅块或浮硅层破坏。
6.6.2接到炉前检验合格通知后应在15分钟内(以出铁口开始计)应全部浇完,超过15分钟浇不完的铁水报废。
6.6.3浇注中应注意观察铁流火苗情况和流淌出的铁片、铁豆是否有缩陷,发现异常应立即停止浇注、并迅速报告技术员或班组长,采取处理措施。
6.6.4每炉次用中期铁水浇注三根试块,试块冷却至700℃以下才能开箱。
7、修炉及修包
7.1清理
7.1.1清理时先从加料口把大块挂渣打落,并在加料口处放好安全罩,修炉人员戴好安全帽后再进行炉内清理和修炉。
7.1.2清理炉壁时,不能用锤子垂直敲打炉壁。
砖面不应残留炉渣、铁片等。
7.2修补炉壁
7.2.1砌砖时,耐火粘土等材料应布满全部接触面,砖与砖之间缝隙不应超过3mm、上下层砖缝应错开。
7.2.2炉壁的耐火砖有侵蚀及松动裂纹现象时,应用耐火材料补平,保证质量及原有尺寸。
7.2.3修炉时按规定尺寸修理,修完后检查并记录各主要部位尺寸。
主要部位尺寸应符合以下规定:熔化带为Φ1050mm~Φ1140mm,风口区为Φ900mm~950mm,炉缸去为Φ780mm~820mm。
7.3修风口
7.3.1修风口时应保证工艺规定的风口大小及位置、形状不应任意改变。
其中1排风口为Φ20mm×8mm×5°,2排风口为Φ30mm×8mm×10°。
7.3.2在炉内风口上都应凸起20mm~30mm。
7.4修出铁口和出渣口。
7.4.1出铁口处炉壁为70mm,直径为30mm,出渣口处厚度为60mm,直径为50mm,内外做成喇叭状。
7.4.2前炉和大炉之间过桥尺寸为45mm×150mm。
7.5修出铁槽及前炉。
7.5.1前炉的修理与风口以下的炉壁相同。
7.5.2出铁槽的修理与修炉壁相同,其斜度与炉底一样。
表面应刷一层涂料,保证其光洁平直。
7.5.3焦碳粉应过60号筛才能使用。
7.6修理炉底
7.6.1修炉底首先用修炉材料将炉底空隙覆好,避免炉底材料漏掉。
7.6.2修炉底前应先将炉底门气眼清理干净。
7.6.3将炉底门关好后,铺上炉底材料,并使其有合适的强度与水分。
7.6.4炉底以出铁口为准,厚度为200mm~250mm,斜度为1:12(即5°~6°)。
7.6.5炉底与炉壁连接处要有圆角,半径为50~80mm。
7.7烘炉
7.7.1点火前首先把风口打开,点火应在开风前2小时~3小时,点火时间不能过短或过长。
装木柴应先从工作门装入部分木柴,并用较小的木柴铺满炉底,以免将炉底砸坏,最后从加料口将木柴加足。
7.7.2大炉、前炉的炉底及出铁槽修好后填入木柴用慢火烘干。
7.7.3开始装料前应先装入部分焦碳,鼓风烘燃必须超过20分钟。