金属锂提取冶金学
锂电池湿法冶金

锂电池湿法冶金全文共四篇示例,供读者参考第一篇示例:锂电池湿法冶金是一种用湿法技术从矿石中提取锂金属的工艺。
随着电动汽车和移动电子设备的普及,锂电池的需求不断增长,因此锂资源的开采和提取也变得越来越重要。
目前主要的锂资源大多来自于稀有金属矿石,如锂辉石矿石。
锂电池湿法冶金的工艺流程包括矿石的破碎、浸出、富集和沉淀等步骤。
将矿石经过破碎和磨矿处理,得到细粉末状的矿石。
然后将矿石放入浸出槽中,用浸出剂(通常是盐酸或硫酸)进行浸出,将锂金属从矿石中溶解出来。
接着,通过加入沉淀剂或调节溶液的pH值,将锂金属从溶液中沉淀出来,进一步提纯得到纯度较高的锂金属。
锂电池湿法冶金的优点在于工艺简单、成本较低,可以实现大规模生产。
湿法冶金还能回收利用矿石中的其他有价值的金属元素,实现资源的综合利用。
湿法冶金也存在一些问题,如对环境的污染以及消耗大量的水资源等。
为了减少对环境的影响,提高冶金过程的效率和资源利用率,科研人员正在不断努力改进湿法冶金技术。
采用生态友好的浸出剂和沉淀剂、优化工艺条件,减少能耗和废水排放等。
还可以通过改进提取设备和自动化控制系统,提高生产效率和产品纯度。
锂电池湿法冶金是一种重要的锂提取技术,为锂资源的开发和利用提供了可行的解决方案。
随着技术的不断进步和创新,相信锂电池湿法冶金将会更加环保、高效,为锂电池产业的发展做出更大的贡献。
第二篇示例:湿法冶金的核心是溶解和析出反应。
将锂矿石在酸性或碱性条件下进行浸出,将其中的锂盐溶解到溶液中。
然后通过控制溶液的pH值、温度等条件,使得锂盐析出出来,形成纯净的锂金属。
整个过程中无需高温高压,不会产生大量的二氧化碳等废气,避免了对环境的污染。
在锂电池湿法冶金中,有几种常用的提取方法。
最常见的是碳酸锂法和氯化法。
碳酸锂法是通过将锂矿石和碳酸混合反应,再经过过滤、蒸发等步骤提取锂金属。
而氯化法是将锂矿石与氯化剂反应生成氯化锂,并通过析出等方法提取锂金属。
这两种方法各有优劣,可以根据具体的情况选择适合的方法。
金属锂提取冶金学-

_*锂生产工艺性质锂在元素周期表中属ⅠA族,其相对原子质量为6.941,天然同位素质量数为6、7,密度0.531g/cm3(20℃),熔点179~186℃,沸点1372℃,因此还原法生产工艺中易出现液状,真空条件下便于杂质元素分离,有利于产品纯度的提高;金属锂呈银白色,它与湿空气相遇,能与其中的O2、N2迅速化合,表面生成Li2O、LiOH及Li3N的覆盖层,覆盖层呈淡黄色以至黑色,所以必须在石蜡或汽油中保存。
锂的化学活性很强,能与HCl、HNO3、稀H2SO4起剧烈的反应,特别是在浓HNO3中强烈氧化,以至熔融和燃烧。
在浓H2SO4中溶解缓慢。
锂在高温下与碳作用生成LiC;与F、Cl、Br、I作用并发生燃烧,与水反应生成LiOH;在加热至熔点温度下能与S 反应生成LiS,与Si一起熔融生成Li6Si2。
此外,锂与有机化合物几卤素衍生物反应,生成相应的锂有机化合物。
碳酸锂常压下熔点730℃,分解温度1270℃,先熔融成桨状,再分解脱除CO2,阻碍分解反应的进行,但当有石灰或铝氧土参与时,可使物料变成疏松状,有利于CO2分解,如碳酸锂与石灰按2/3进行配料,在真空中进行焙烧,800℃下可完成作业。
用途由于锂的优异性能日益被人们发现和利用,目前已在国民经济各部门以及近代尖端技术——原子能、热核反应、洲际火箭、人造卫星等方面都起着非常重要的作用。
金属锂极其化合物可作为优质高能燃料,已经用于宇宙火箭、人造卫星、超声速飞机和潜水艇等燃料系统方面。
在冶金工业上,锂作为轻合金、超轻合金、耐磨合金极其它合金的组分。
锂与镁、铝、铍组成的合金,质地轻,加工性能好,强度大,已被用作飞机的结构材料。
铝电解质中加入锂盐,可降低电耗。
在玻璃工业中,将锂化合物作为加成剂,可提高玻璃的强度和韧性,降低熔点,增加电阻和延迟透明消失的作用。
玻璃中含锂较多时,能提高紫外线透射率,降低热膨胀系数,目前锂玻璃已用于制造大型电视显象管等。
金属锂提取冶金学
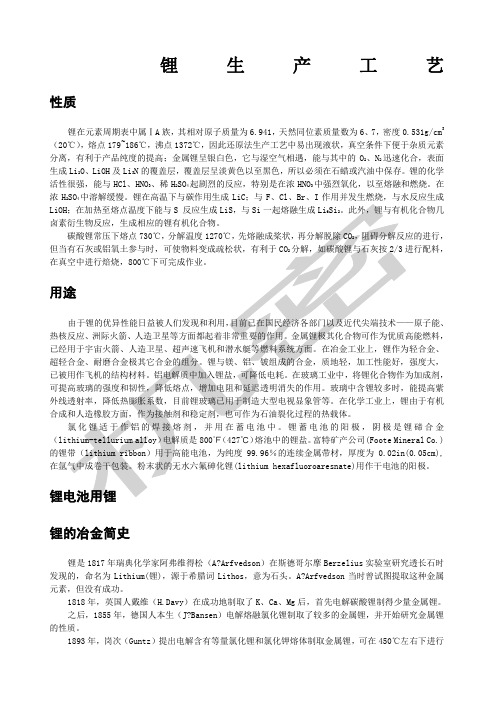
锂生产工艺性质锂在元素周期表中属ⅠA族,其相对原子质量为6.941,天然同位素质量数为6、7,密度0.531g/cm3(20℃),熔点179~186℃,沸点1372℃,因此还原法生产工艺中易出现液状,真空条件下便于杂质元素分离,有利于产品纯度的提高;金属锂呈银白色,它与湿空气相遇,能与其中的O2、N2迅速化合,表面生成Li2O、LiOH及Li3N的覆盖层,覆盖层呈淡黄色以至黑色,所以必须在石蜡或汽油中保存。
锂的化学活性很强,能与HCl、HNO3、稀H2SO4起剧烈的反应,特别是在浓HNO3中强烈氧化,以至熔融和燃烧。
在浓H2SO4中溶解缓慢。
锂在高温下与碳作用生成LiC;与F、Cl、Br、I作用并发生燃烧,与水反应生成LiOH碲合金(Co.)锂的冶金简史锂是1817年瑞典化学家阿弗维得松(A?Arfvedson)在斯德哥尔摩Berzelius实验室研究透长石时发现的,命名为Lithium(锂),源于希腊词Lithos,意为石头。
A?Arfvedson当时曾试图提取这种金属元素,但没有成功。
1818年,英国人戴维(H.Davy)在成功地制取了K、Ca、Mg后,首先电解碳酸锂制得少量金属锂。
之后,1855年,德国人本生(J?Bansen)电解熔融氯化锂制取了较多的金属锂,并开始研究金属锂的性质。
1893年,岗次(Guntz)提出电解含有等量氯化锂和氯化钾熔体制取金属锂,可在450℃左右下进行电解,使电解温度大幅度降低,使电解效率明显提高,奠定了现代电解法生产金属锂的基础。
从1817年发现元素锂到有一定金属锂的生产规模,历史76年。
自1893年研究成功融盐电解法制取金属锂,至今已有111年时间,融盐电解法提取金属锂已成为一种传统的提取工艺。
热还原法提锂的研究简史金属锂的生产(方法)1、熔盐电解法:氯化钾为支持电解质,电解温度450~500℃,氯化锂45~60%,初晶温度360~450℃之间;2COc1000℃及残压43~1.3Pa的真空条件进行还原,每次装料2.5kg,产锂175g,回收率80%,锂的纯度99%。
锂钠钾金属提取

锂钠钾金属提取
锂钠钾是化学元素周期表第1A族元素中的金属元素。
这三种金属都具有极强的化学活性,因此它们在自然界中往往以化合物的形式存在。
然而,由于锂、钠、钾在工业和生活中的广泛应用,对它们的提取和加工成为了一个重要的课题。
锂的提取主要有两种方法:碳酸锂法和氯化锂法。
碳酸锂法是将锂矿石经过破碎、浮选等物理化学处理后得到含锂的碳酸锂。
然后,利用高温还原或碱性碳酸锂与二氧化碳反应产生碳酸氢锂等方法进行进一步的提取和纯化。
而氯化锂法则是利用铁锂矿或锂硅矿经过氯化反应,反应生成氯化锂和其他副产品,然后通过溶液萃取、逆萃取、晶体分离等过程得到纯化的氯化锂。
钠的主要提取方法是氯化法和电解法。
氯化法是通过与钾矿石一起加热,生成氯化物混合物,然后通过溶液萃取和化学纯化得到纯钠氯化物。
最后,通过加热还原,得到纯钠金属。
而电解法则利用电解池中的氯化钠溶液,通过电流的作用,使钠离子在电解池阳极处还原成钠金属,成为一种直接获得纯净钠的方法。
钾的提取主要采用电解法。
钾电解的重要原料是氯化钾和氢氧化钾,这两者是通过钾矿石的浸出、结晶、脱水等工艺得到的。
在电解
池中,通过直流电流的作用,使氯化钾和氢氧化钾中的钾离子在电解
池的阳极处还原成金属钾,而阴极则放出氢气。
以上是锂、钠、钾金属的主要提取方法。
在实际应用中,还需要
进行脱氧、纯化和加工等工艺步骤,以得到满足不同领域需求的金属
产品。
同时,锂、钠、钾的连续开发和利用也需要更多的科研人员参与,以提高金属提取和加工的效率和环保性,推动这些金属在新能源、冶金、化工等领域的应用。
金属锂提取冶金学:
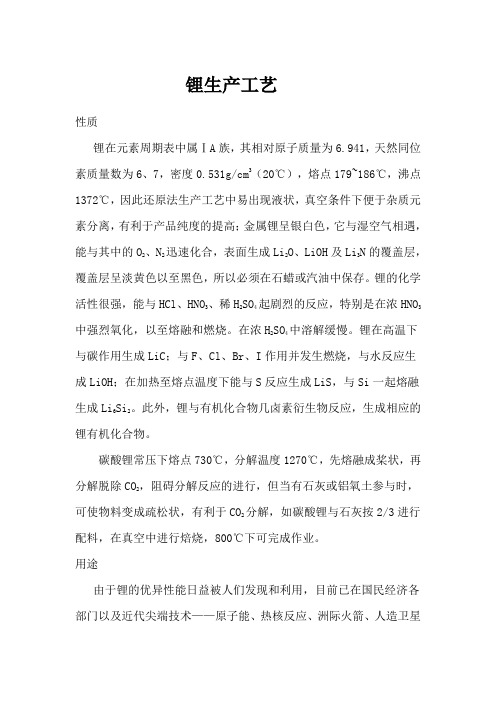
锂生产工艺性质锂在元素周期表中属ⅠA族,其相对原子质量为6.941,天然同位素质量数为6、7,密度0.531g/cm3(20℃),熔点179~186℃,沸点1372℃,因此还原法生产工艺中易出现液状,真空条件下便于杂质元素分离,有利于产品纯度的提高;金属锂呈银白色,它与湿空气相遇,能与其中的O2、N2迅速化合,表面生成Li2O、LiOH及Li3N的覆盖层,覆盖层呈淡黄色以至黑色,所以必须在石蜡或汽油中保存。
锂的化学活性很强,能与HCl、HNO3、稀H2SO4起剧烈的反应,特别是在浓HNO3中强烈氧化,以至熔融和燃烧。
在浓H2SO4中溶解缓慢。
锂在高温下与碳作用生成LiC;与F、Cl、Br、I作用并发生燃烧,与水反应生成LiOH;在加热至熔点温度下能与S反应生成LiS,与Si一起熔融生成Li6Si2。
此外,锂与有机化合物几卤素衍生物反应,生成相应的锂有机化合物。
碳酸锂常压下熔点730℃,分解温度1270℃,先熔融成桨状,再分解脱除CO2,阻碍分解反应的进行,但当有石灰或铝氧土参与时,可使物料变成疏松状,有利于CO2分解,如碳酸锂与石灰按2/3进行配料,在真空中进行焙烧,800℃下可完成作业。
用途由于锂的优异性能日益被人们发现和利用,目前已在国民经济各部门以及近代尖端技术——原子能、热核反应、洲际火箭、人造卫星等方面都起着非常重要的作用。
金属锂极其化合物可作为优质高能燃料,已经用于宇宙火箭、人造卫星、超声速飞机和潜水艇等燃料系统方面。
在冶金工业上,锂作为轻合金、超轻合金、耐磨合金极其它合金的组分。
锂与镁、铝、铍组成的合金,质地轻,加工性能好,强度大,已被用作飞机的结构材料。
铝电解质中加入锂盐,可降低电耗。
在玻璃工业中,将锂化合物作为加成剂,可提高玻璃的强度和韧性,降低熔点,增加电阻和延迟透明消失的作用。
玻璃中含锂较多时,能提高紫外线透射率,降低热膨胀系数,目前锂玻璃已用于制造大型电视显象管等。
在化学工业上,锂由于有机合成和人造橡胶方面,作为接触剂和稳定剂,也可作为石油裂化过程的热载体。
高中化学 金属锂的冶炼

高中化学金属锂的冶炼
金属锂的冶炼主要有以下几个步骤:
1. 矿石选矿:首先从锂矿石中提取含锂的矿物。
常见的锂矿石主要有云母矿石、钨锂辉石矿石、蓝闪锂辉石矿石等。
2. 矿石破碎和磨矿:将锂矿石破碎成适当的颗粒大小,然后通过磨矿的方式使其细化。
3. 矿石浸出:将细磨后的锂矿石与化学试剂(如硫酸、氟化钙等)进行反应浸出,使得锂溶解在浸出液中。
4. 锂沉淀:将浸出液与碳酸锂等化学试剂反应,使得锂以碳酸锂的形式沉淀出来。
5. 锂碳酸盐的烧结:将锂碳酸盐进行烧结,使得其中的杂质和水分等被蒸发掉,得到纯净的锂碳酸盐。
6. 电解精炼:将锂碳酸盐加热到一定温度后,经过电解精炼,将其中的杂质进一步去除,得到纯度更高的锂金属。
以上步骤是一种常见的金属锂冶炼流程,实际的冶炼过程可能会有所差异,具体步骤会根据不同的矿石种类和提取方法有所不同。
锂电池湿法冶金

锂电池湿法冶金
锂电池湿法冶金是一种从废旧锂电池中回收有价值金属(如锂、钴、镍等)的方法。
以下是一般的湿法冶金流程:
1. 电池拆解:将废旧锂电池进行拆解,分离出正极、负极、电解液等组件。
2. 材料预处理:对正极和负极材料进行预处理,例如破碎、筛分等,以增加材料的表面积,提高后续浸出效率。
3. 浸出:将预处理后的正极和负极材料浸泡在化学溶剂中,使金属离子溶解到溶液中。
常用的浸出剂包括酸、碱或其他络合剂。
4. 分离:通过过滤、沉淀、萃取等方法,将浸出液中的金属离子与其他杂质分离。
5. 金属回收:采用化学沉淀、电解、溶剂萃取等技术,从分离后的溶液中回收金属。
这可以得到高纯度的金属产品,如锂盐、钴盐、镍盐等。
6. 废水处理:对湿法冶金过程中产生的废水进行处理,以满足环保要求。
湿法冶金在锂电池回收领域具有一些优势,如回收率高、产品纯度高、对环境相对友好等。
然而,它也面临一些挑战,如成本较高、工艺复杂、废液处理等问题。
为了提高湿法冶金的效率和可持续性,研究人员正在不断探索和改进相关技术。
需要注意的是,锂电池湿法冶金是一个复杂的过程,具体的工艺流程可能会因电池类型、材料组成和回收目标而有所不同。
此外,湿法冶金过程中需要严格控制操作条件和安全措施,以确保操作人员的安全和环境保护。
金属锂制备工艺研究进展

2019年第5期新疆有色金属0引言金属锂性质非常活泼,其在原子能、核工业、冶金行业、电子等领域都具有非常重要的应用[1-3]。
锂原子量具有最小的电化学当量值,其标准电极电位为-3.03V ,用锂作负极活性物质的电池叫锂电池,锂电池具有重量轻、体积小、储电能力大、充电速度快、适用范围广等特点,是一种较为理想的新能源电池材料。
以锂为主要合金元素的新型铝合金,突出的优点是密度小、弹性模量高,在铝及其合金中,每加入1%的锂,比重可下降3%,弹性模量提高6%,世界各国研制出各种牌号的铝锂合金,并广泛应用于导弹、航空材料、飞机以及航空飞行器等[4-5]。
目前金属锂的制备方法[6-7]主要有金属热还原法、熔盐电解法和真空蒸馏法,其中金属热还原法是由氧化锂转化为金属锂的方法,熔盐电解法是由锂盐转化为金属锂的方法,真空蒸馏法是将粗金属锂变为高纯金属锂的方法。
金属热还原法制备金属锂流程短、效率高,缺点是不可连续生产,设备要求高,控制难度较大。
熔盐电解法制备金属锂工艺简单、电流效率高,但不足之处是电解产生大量有毒有害的氯气,环保要求高。
真空蒸馏法[8-9]是目前普遍采用的一种金属锂提纯方法,国内外学者对真空蒸馏金属锂做了较多的研究,该工艺可以有效降低金属锂中杂质的含量。
1金属热还原法制备锂金属金属热还原法主要包括硅铁热还原法以及铝热还原法。
金属热还原法制备金属锂具有流程短、原料来源不需额外加工、生产周期短等优点[10]。
1.1硅铁热还原法硅热还原法制备金属锂反应方程式:Si(s)+2Li 2O(s)→SiO 2(s)+4Li(g)(1)铁热还原法制备金属锂反应方程式:2Fe(s)+3Li 2O(s)→Fe 2O 3(s)+6Li(g)(2)硅铁热还原法的还原剂包括硅还原剂、铁还原剂以及硅铁还原剂,被还原的物质为氧化锂,由于碳酸锂在高温下可分解为氧化锂,因此很多人也采用碳酸锂进行直接还原。
狄跃忠等[11]研究了碳酸锂在不同温度条件下分解的热力学分析,并以此为基础,研究了碳酸锂分解为氧化锂的实验条件,在900℃,真空度4Pa ,保温2h 的条件下,最终由碳酸锂得到氧化锂,分解率达到99.86%。
- 1、下载文档前请自行甄别文档内容的完整性,平台不提供额外的编辑、内容补充、找答案等附加服务。
- 2、"仅部分预览"的文档,不可在线预览部分如存在完整性等问题,可反馈申请退款(可完整预览的文档不适用该条件!)。
- 3、如文档侵犯您的权益,请联系客服反馈,我们会尽快为您处理(人工客服工作时间:9:00-18:30)。
金属锂提取冶金学 The document was prepared on January 2, 2021锂生产工艺性质锂在元素周期表中属ⅠA族,其相对原子质量为,天然同位素质量数为6、7,密度cm3(20℃),熔点179~186℃,沸点1372℃,因此还原法生产工艺中易出现液状,真空条件下便于杂质元素分离,有利于产品纯度的提高;金属锂呈银白色,它与湿空气相遇,能与其中的O2、N2迅速化合,表面生成Li2O、LiOH及Li3N的覆盖层,覆盖层呈淡黄色以至黑色,所以必须在石蜡或汽油中保存。
锂的化学活性很强,能与HCl、HNO3、稀H2SO4起剧烈的反应,特别是在浓HNO3中强烈氧化,以至熔融和燃烧。
在浓H2SO4中溶解缓慢。
锂在高温下与碳作用生成LiC;与F、Cl、Br、I作用并发生燃烧,与水反应生成LiOH;在加热至熔点温度下能与S反应生成LiS,与Si一起熔融生成Li6Si2。
此外,锂与有机化合物几卤素衍生物反应,生成相应的锂有机化合物。
碳酸锂常压下熔点730℃,分解温度1270℃,先熔融成桨状,再分解脱除CO2,阻碍分解反应的进行,但当有石灰或铝氧土参与时,可使物料变成疏松状,有利于CO2分解,如碳酸锂与石灰按2/3进行配料,在真空中进行焙烧,800℃下可完成作业。
用途由于锂的优异性能日益被人们发现和利用,目前已在国民经济各部门以及近代尖端技术——原子能、热核反应、洲际火箭、人造卫星等方面都起着非常重要的作用。
金属锂极其化合物可作为优质高能燃料,已经用于宇宙火箭、人造卫星、超声速飞机和潜水艇等燃料系统方面。
在冶金工业上,锂作为轻合金、超轻合金、耐磨合金极其它合金的组分。
锂与镁、铝、铍组成的合金,质地轻,加工性能好,强度大,已被用作飞机的结构材料。
铝电解质中加入锂盐,可降低电耗。
在玻璃工业中,将锂化合物作为加成剂,可提高玻璃的强度和韧性,降低熔点,增加电阻和延迟透明消失的作用。
玻璃中含锂较多时,能提高紫外线透射率,降低热膨胀系数,目前锂玻璃已用于制造大型电视显象管等。
在化学工业上,锂由于有机合成和人造橡胶方面,作为接触剂和稳定剂,也可作为石油裂化过程的热载体。
氯化锂适于作铝的焊接熔剂,并用在蓄电池中。
锂蓄电池的阳极,阴极是锂碲合金(lithium-telluriumalloy)电解质是800℉(427℃)熔池中的锂盐。
富特矿产公司(FooteMineralCo.)的锂带(lithiumribbon)用于高能电池,为纯度%的连续金属带材,厚度为,在氩气中成卷干包装。
粉末状的无水六氟砷化锂(lithiumhexafluoroaresnate)用作干电池的阳极。
锂电池用锂锂的冶金简史锂是1817年瑞典化学家阿弗维得松(AArfvedson)在斯德哥尔摩Berzelius 实验室研究透长石时发现的,命名为Lithium(锂),源于希腊词Lithos,意为石头。
AArfvedson当时曾试图提取这种金属元素,但没有成功。
1818年,英国人戴维()在成功地制取了K、Ca、Mg后,首先电解碳酸锂制得少量金属锂。
之后,1855年,德国人本生(J Bansen)电解熔融氯化锂制取了较多的金属锂,并开始研究金属锂的性质。
1893年,岗次(Guntz)提出电解含有等量氯化锂和氯化钾熔体制取金属锂,可在450℃左右下进行电解,使电解温度大幅度降低,使电解效率明显提高,奠定了现代电解法生产金属锂的基础。
从1817年发现元素锂到有一定金属锂的生产规模,历史76年。
自1893年研究成功融盐电解法制取金属锂,至今已有111年时间,融盐电解法提取金属锂已成为一种传统的提取工艺。
热还原法提锂的研究简史金属锂的生产(方法)1、熔盐电解法:氯化钾为支持电解质,电解温度450~500℃,氯化锂45~60%,初晶温度360~450℃之间;电解法生产金属锂的某些技术参数2、热还原法:a)、碳热还原法Li2O+C=2Li+CO,1937年美国矿物局提出,反应温度1680℃,,但反应产物易被CO污染,发生二次反应,难于实施;b)、氢还原法Li2O+H2=2Li+H2O,试验发现易产生中间化合物,可能是LiH;c)、硅还原法方法1:2Li2O+2CaO+Si=4Li+SiO22CaO,采用79#硅铁,硅过量10%,采用CO使其在真空中分解,然后与60份CaO混合,在1300℃×10-6大气的40份Li2真空下,锂的回收率可达%;方法2:碳酸锂:石灰=2:3(质量比)配料,焙烧,加过量10~15%的75#硅铁,制球,1000℃及残压43~的真空条件进行还原,每次装料,产锂175g,回收率80%,锂的纯度99%。
焙烧作业:CaOLi2CO3 CO2+Li2O还原反应的主体反应为:2Li2O+Si=4Li+SiO2当75#硅铁过量10~15%、锂回收率80%时,全工艺过程:投入:40g碳酸锂+60g石灰+硅铁产出:锂++渣可计算出有关的技术经济指标:产品率%,渣率%,碳酸锂消耗:t-Li;石灰消耗:吨;硅铁消耗:吨;副产渣:吨;硅铁利用率%。
硅热法生产金属锂技术经济与成本表d)、铝热还原法由于铝比硅具有更高的活性,可大规模生产,价格也不太高,所以采用铝作还原剂,更为适宜。
3Li2O+2Al=Al2O3+6Li但试验发现,在采用铝还原剂时会生成铝酸盐,因此,必须向混合物中添加CaO这样的强碱,才能使反应顺利进行。
因此,总反应是:3Li2O+CaO+2Al=CaOAl2O3+6Li当采用Li2OCaO和铝压团,在900℃下,真空度小于×10-6大气压时,经过十五个小时的反应,锂的回收率可达%。
也有人采用锂辉石矿为原料,添加CaO,用铝直接还原,在真空条件下,于1150℃时,锂的提取率为%,对此,曾成功地进行过半工业试验,每次装10kg左右的料,锂的提取率达到95%,由此申请了两个铝热还原法的专利。
铝热法生产金属锂工艺参数某工艺:碳酸锂与铝氧土按分子比1:1进行配料,焙烧后制得铝酸锂烧成料,铝粉作还原剂,在13~68Pa真空及1150℃~1200℃下进行还原作业,锂的回收率为90%。
焙烧作业表示为:Li2CO3+Al2O3=CO2+Li2OAl2O3还原作业可表示为:Li2OAl2O3+2/3Al=2Li+4/3Al2O3当锂回收率90%时,可以计算出有关的技术经济指标:产品率:%;渣率%;渣组成:Li2O%;%;%。
这是一种优质的铝氧土,可以作为碳酸锂的焙烧助剂。
在用渣作为焙烧助剂时,计算结果表明可以取得用铝氧土作助剂相同的技术效果外,还可以提高铝的利用率及锂的回收率(由90%提到%),减少了碳酸锂用量,每吨金属锂的原材料成本可以降低20%以上。
铝热法生产金属锂技术经济与成本表金属锂的生产(电解)当前金属锂唯一的工业生产方法是氯化锂——氯化钾融盐电解法。
电解质中氯化锂为55%,氯化钾为45%,电解在460℃左右进行。
电流效率约80%。
金属锂纯度%。
生产1公斤金属锂需要电解6公斤氯化锂,电解时,氯化锂中的钠全部富集到金属锂中,因此,氯化锂中的钠量对金属锂的产品纯度影响很大。
用高纯氯化锂电解,则可直接制得用于锂电池的高纯金属锂。
纯度在%以内的金属锂,主要从改进现有融盐电解工艺可直接制取。
制取纯度高于%的金属锂,则需要采取提纯措施。
国外提纯金属锂的方法有:真空蒸馏法、过滤法、区熔法、吸收法、氢还原法以及精馏法等。
目前工业上用的锂电解槽有:德国式、法国式、和美国式三种类型。
美国式锂电解槽,槽体由钢板焊成,外壁和底部用气体火焰加热,由顶部插入5根直径毫米,长米的石墨阳极,垂直安放。
阴极固定在槽底,由低碳钢制作。
正常作业条件是:槽温450~475℃,直流电压6~伏。
电解槽总容量约为3立方米,每公斤金属锂耗电46度(不包括加热熔盐用能耗)。
电解:当今金属锂的工业化生产工艺主要是电解氯化锂和氯化钾熔融混合物,有时也在此电解中加入一些LiBr,或者利用Li2CO3、LiOH在低共熔混合物中直接转化成金属锂。
超纯锂也可从含85~90%的LiBr和10~15%LiCl的熔盐混合物中制得。
金属锂的精炼:金属锂性质活泼,电解得金属锂后要经过1~2次真空精炼以除去钠、钾和镁等杂质,尔后加工成棒材、带材、或颗粒产品销售。
精炼后的金属锂含Li ≥%,其余小于(%):、、、、、、、。
金属锂的生产工艺(还原)熔盐电解法制取金属锂的主要缺点是锂必不可免地被钠和钾所污损,而且阳极析出的氯气也需处理和利用。
真空热还原法则可避免这些缺点。
它可以从Li2O、Li2OAl2O3甚至直接从锂辉石得到金属锂。
从而省却了制取对设备有腐蚀作用的无水氯化锂的过程。
当以Li2O为原料时,Li2O是由Li2CO3分解而得到的。
Li2CO3上CO2的平衡压力在810、890和1270℃时分别为2、及101kPa。
为了使熔点为735℃的Li2CO3在热分解时不致熔化而使CO2难于析出,是将Li2CO3和CaO按质量比为1:制团,再将团块在真空下热分解的。
产物则是Li2O和CaO的混合物。
它对于下一步的真空热还原过程也是有利的。
还原剂用硅粉,2Li2O+Si==4Li+SiO2在标准状态下的吉布斯自由能变化为正值,并且是吸热反应;ΔG0278=+298Kj,ΔH0278=+320Kj。
因而这一反应只能在高温、真空下进行,而将析出的锂蒸气不断抽出。
但此时有一部分Li2O会和SiO2D生成原硅酸锂。
反应式+Si4CaO+2Li2OSiO2+Si==4Li(汽)+2(2CaSiO2)的ΔG01000k=-351Kj。
将磨细后的Li2O、CaO和理论量110%的硅粉压团,然后在真空炉内于1000~1300℃下还原。
析出的锂收集于冷凝器内。
在1000℃下锂的回收率为75%,而在1300℃为93%。
在所得锂中的主要杂质为%、%。
以铝粉为原料时可以用Li2OAl2O3为原料。
烧结由Li2CO3和Al2O3组成的炉料便可得到铝酸锂。
还原反应3(Li2OAl2O3)+2Al==6Li(汽)+4Al2O3在1100℃下,锂的平衡蒸汽压为。
在1150~1200℃和的剩余压力下进行真空热还原可以得到纯度很高的锂。
锂的回收率可达95~98%。
为此要配入过量的铝粉。
采用这一方法无须往炉料中加入CaO。
这样也保证了产品的纯度。
还原过程得到的氧化铝渣又可用以制备下一批铝酸锂。
锂冶金存在的问题及展望1、熔盐电解法存在的问题及解决方向降低锂电解的电耗率锂电解的电耗可由下式表示:W=KV/r=3862V/rV为平均槽电压,r为电流效率。
以4#资料显示的数据为例,则吨电耗为38620(Kwh/t-Li)为降低电流效率可从降低槽电压和提高电流效率入手。
●考虑改进槽结构。
●增加单槽的电流效率。