06 凝固过程的传热
合集下载
凝固过程传热2
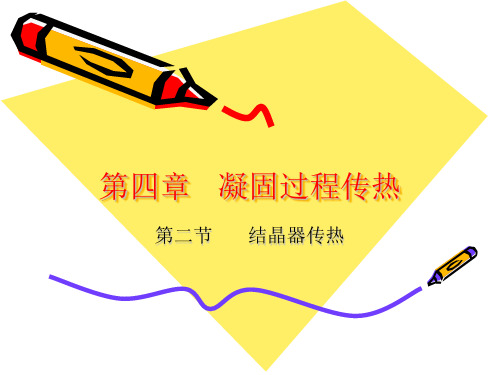
实际生产中,主要通过以下措施控制冷却水与铜壁的传热方式: (1) 结晶器水缝中水流速是保证冷却能力重要因素。 当水缝中的水的流速大于某一临界值时,就可避免水的沸 腾,保证良好的传热。 钢种不同 高温机械性能不同 临界水速不同 (2) 控制好结晶器进出水温度差,一般为5~6℃,不超过10℃。 (3) 采用高压操作,提高水缝内静压力,可以进一步控制水沸腾。
(2)紧密接触区 弯月面下部的初生坯壳由于不足以抵抗钢液静压力的作用, 与铜壁紧密接触,在该区域坯壳以传导传热的方式将热量传输 给铜壁,愈往接触区的下部,坯壳也愈厚。 (3)气隙区 产生:当坯壳凝固到一定厚度时,由于凝固收缩以及发生包晶相变, 引起坯壳收缩。牵引坯壳向内弯曲脱离铜壁,气隙开始形成。 然而,此时形成的气隙是不稳定的,在钢液静压力的作用下, 坯壳向外鼓胀,又会使气隙消失。这样,接近紧密接触区的部 分坯壳,实际上是处于气隙形成和消失的动态平衡过程中,只 有当坯壳厚度和强度到达能够够承受钢水静压力的作用时,气 隙才稳定存在。
位置:根据测定估计是17S开始产生气隙;此时约是结晶器钢 液面以下247mm处。 对气隙的认识→选择结晶器的长度。 长结晶器:连铸开发初期,对气隙认识不足,苏联 结晶器长度曾用过1500mm,认为长结晶器可增加导出热 量会使出结晶器时坯壳增厚; 短结晶器:西欧曾试用过400mm长的结晶器,认为 由于气隙形成使传效减慢,结晶器长了也无用。 结晶器太长太短都不行,一般选用700mm长较为合 适。90年代后期,为了提高拉速,增加坯壳厚度,有些 厂把结晶器长度又加长到900mm。
各个环节的具体传热: 1、结晶器中心钢水与坯壳间的传热: 传热方式:对流传热 热流密度: ql = hl (Tc − Tl ) 式中: hl—对流传热系数;tc和tl—分别为钢水温度和坯壳凝固前沿温度 (即液相线温度)。 通过对传热进行计算,结论: 1)钢水与坯壳之间的传热量远小于结晶器的散热量:因此,结晶器散 出的热量基本来自凝固潜热。不同的钢水过热度,结晶器热流差别不大。因 此,生产中不必根据浇注温度调整结晶器的供水量。 2)结晶器散出的热量基本来自凝固潜热,而钢水与坯壳之间的传热量 散热量小,因此其对整体传热影响不大,一般认为此处的热阻可以忽略不计。 3)尽管过热对整体的传热量影响不大,似乎对凝固坯壳的厚度影响不 大,但是直接决定钢水对坯壳的冲刷程度和开始凝固时间,从而影响坯壳的 实际厚度;同时,液相过热度影响着枝晶熔化和增殖等,因此是决定铸坯结 构的主要因素。(过热度在20-30℃) 4)由于结晶潜热的阻碍,液芯内钢水散热很慢,因此过热会存在很长 的时间,对凝固结晶有持久的作用。
第3章 凝固过程的传热[23页]
![第3章 凝固过程的传热[23页]](https://img.taocdn.com/s3/m/0059e3a9294ac850ad02de80d4d8d15abe2300f6.png)
Tw f (t)
第二类边界条件: 给出通过物体表面的比热流随
时间的变化关系
T qx, y, z, t
n
第三类边界条件: 给出物体周围介质温度以及物
体表面与周围介质的换热系数
T = n
Tw
Tf
纯金属在铸型中凝固传热模型
K-导热 C-对流 R-辐射 N-牛顿界面换热
“三传”
所谓“三传”,即金属的凝固过程是一个 同时包含动量传输、质量传输和热量传输 的三传耦合的三维传热物理过程,而在热 量传输过程中同时存在有导热、对流和辐 射传热这三种传热方式。
t x x y y z z
λ --导热系数;
T--热力学温度; q --单位体积物体单位时间内释放的热量; c--比热容;
q L f s
t
ρ--密度;
t--时间。
对具体热场用上述微分方程进行求解时,需要根 据具体问题给出导热体的初始条件与边界条件。
初始条件: 初始条件是指物体开始导热时
第3章 凝固过程的传热
主要内容
3.1 凝固过程的传热 3.2 凝固时间的计算 3.3 液态金属凝固温度场
3.1 凝固过程的传热
3.1.1 凝固过程的传热特点
金属凝固过程中,其传热特点可简要概括为: “一热、二迁、三传”。
“一热”,即在凝固过程中热量的传输是第 一位的,是最重要的,它是凝固过程能否进 行的驱动力。
(即 t = 0 时)的瞬时温度分布。
边界条件:边界条件是指导热体表面与周围
介质间的热交换情况。
“二迁”
所谓“二迁”,是指在金属凝固时存在着 两个界面,即固—液界面和金属—铸型界 面,而这两个界面随着凝固进程而发生动 态迁移,并使得界面上的传热现象变得极 为复杂。
铸造金属凝固原理课件:凝固过程的传热-

∂ T1
=Ti -T 10
∂ x x =0 πα1τ
∂ T2
= T20 -T i
∂ x x =0 πα2τ
b1 = λ1ρ1c 1
b2 = λ2ρ2c 2
T1
= b1T10 +b2T20 b1 +b2
+b1T10 +b2T20 b1 +b2
erf
( 2
x) α1τ
T2
= b1T10 +b2T20 b1 +b2
• x3 x2 x1 分別為間隙、鑄型和鑄件的“熱阻。
λ3 λ2
λ1
• 通過“系統”的比熱流q與鑄件斷面中心溫度和鑄型外表面
溫度之差成正比,而與熱阻之和成反比。顯然,比熱流q愈
大,鑄件的冷卻強度亦愈大。因而影響比熱流q的各個因素
也影響鑄件的冷卻強度。
• 魏氏準則
x1
K1
= t1中 -t1表 t1表 -t 2内
➢ 金屬的凝固Βιβλιοθήκη 度➢ 問題:為什麼在相同鑄型條件下,鋁合金鑄件斷面上的溫度場較平坦?
• 鑄型的影響 ➢ 鑄型的蓄熱係數 ➢ 鑄型的預熱溫度
∂ ∂
-
α
α
➢ 為什麼高熔點合金對金屬型的壁厚不敏感而低熔點合金則相反?
• 澆注條件的影響 ➢ 砂型鑄造中增加過熱程度相當於提高了鑄型的溫度,使鑄
件的溫度梯度減小。
α
∫
α
-β β
α
α
-∞
-
α
∂T ∂τ
=α∂ ∂
2T x2
➢ 鑄型溫度場 — 邊界條件 ➢ 鑄型溫度場運算式
α
∞
-
α
∂T ∂τ
凝固过程的传热
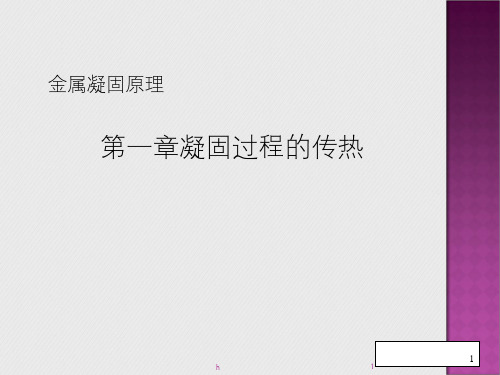
为解析具有这种界面温度降的传热问题,这里引进虚拟凝固 层厚度和虚拟铸型厚度的概念。即将图1-6 a分解为图1-6b和图16c使后两者的组合等效于前者。这种方法将界面热阻转化成了铸 件和铸型上虚拟加厚的凝固层和铸型厚度,即图中S0和- Eo上的 热阻,同时令这两个热阻上的温度降恰好等于界面上的温度降。 这样,就把一个具有界面热阻的复杂的传热问题,转变成了在界 面上理想接触因而具有共同的界面温度Ti的纯导热问题。
由式(1—14)可知,金属和铸型的热物性结合起来决定凝固速度:在金属
方面,熔点高而熔化热和密度小的金属有利于较快凝固;在铸型方面:
大的铸型有利于较快凝固。
反映铸型的吸热能力,称力
铸型的蓄热系数。
由式(1-14)还可以看出,金属凝固层厚度与凝固时间的平方根成正比
,这说明金属的凝固速度开始时快,尔后随铸型的温度升高而逐渐变慢。
h
18
18
§1-1 凝固过程的传热特点
h
19
19
§1-1 凝固过程的传热特点
凝固过程的传热有如下一些特点: 简单地说:一热、二迁、三传。 首先它是一个有热源的传热过程。金属凝固时释放的潜热,可以看成是一
个热源释放的热,但是金属的凝固潜热,不是在金属全域上同时释放,而只是 在不断推进中的凝固前沿上释放。即热源位置在不断地移动;另外,释放的潜 热量也随着凝固进程而非线性地变化。
h
28
28
§1-1 凝固过程的传热特点
非解析法有图解法、电模拟法和数值模拟法等,自从电子计算机问世以来, 数值模拟法得到了迅速的发展。
主导方程(1-1)是均质、各向同性体的传导微分方程,它表示热传导过程的 能量守恒原理。
h
29
29
§1-1 凝固过程的传热特点
由式(1—14)可知,金属和铸型的热物性结合起来决定凝固速度:在金属
方面,熔点高而熔化热和密度小的金属有利于较快凝固;在铸型方面:
大的铸型有利于较快凝固。
反映铸型的吸热能力,称力
铸型的蓄热系数。
由式(1-14)还可以看出,金属凝固层厚度与凝固时间的平方根成正比
,这说明金属的凝固速度开始时快,尔后随铸型的温度升高而逐渐变慢。
h
18
18
§1-1 凝固过程的传热特点
h
19
19
§1-1 凝固过程的传热特点
凝固过程的传热有如下一些特点: 简单地说:一热、二迁、三传。 首先它是一个有热源的传热过程。金属凝固时释放的潜热,可以看成是一
个热源释放的热,但是金属的凝固潜热,不是在金属全域上同时释放,而只是 在不断推进中的凝固前沿上释放。即热源位置在不断地移动;另外,释放的潜 热量也随着凝固进程而非线性地变化。
h
28
28
§1-1 凝固过程的传热特点
非解析法有图解法、电模拟法和数值模拟法等,自从电子计算机问世以来, 数值模拟法得到了迅速的发展。
主导方程(1-1)是均质、各向同性体的传导微分方程,它表示热传导过程的 能量守恒原理。
h
29
29
§1-1 凝固过程的传热特点
第3章 凝固过程的传热(1)

液相向固相转变时还包含有弯曲固-液界面的形成(产生毛细作用)和热量的微观
熔体内形成了固体,产生一个面积为A的固-液界面,就要克服一个与之相对
运输,在合金凝固时还存在溶质的微观运输。 应的额外能量-界面能。因此,A/v值高的异质系统要比A/v值低的异质系统能量更 高,更不稳定。可以用平衡温度(熔点)来表达两相之间的相对稳定性。由毛细作 用引起的熔点温度变化(曲率过冷度)为, 其中,K是曲率, K
合金凝固组织特征不仅取决于冷却条件,而且取决于合金成分(见图1.8 所示的 Al-Cu系中Al和金属间化合物θ (Al2Cu)相之间的部分相图)。 理解不同的凝固组织如何受合金成分和凝固条件的影响非常重要。不 管凝固组织看来多么复杂,但都可以把问题简化为两种基本的凝固组织形 态,即树枝晶和共晶(包晶也以树枝状生长)。 一般情况下还会有两者的混合体。可以归 纳为: (a)纯物质:平面状或树枝状生长; (b)固溶体树枝晶 (不管有无枝晶间析出相); (c)树枝晶和枝晶间共晶; (d)共晶。 理解了这两种生长方式就可以解释几 乎所有合金的凝固组织。 铸造合金的设计前提就是获得所需的性 能和良好的铸造性(易充型、低缩孔和低热裂倾向)。
一些涉及凝固过程的重要生产环节有:铸造(连续铸造、模锭铸造、砂型铸
造、精密铸造、金属型铸造),焊接,锡焊/铜焊,快速成型过程,定向凝固等。 此外,纯物质的结晶也非常重要。例如,半导体及硅晶体制备是现代固体物
理和技术的重要部分。集成电路是所有新型电子器件(无线电、手表、计算机 等)的基础单元,制造集成电路需要大尺寸、低缺陷的单晶,而这种单晶的制 备则需要对掺杂元素的量和均匀性进行严格控制。到目前为止,这种单晶还只 能从熔体中生长。半导体物理方面的需求极大促进了凝固理论和技术的进步。 虽然铜制品的铸造可以追溯到公元前4000年。公元前1600年,中国也出现
凝固过程的传热

PDF 文件使用 "pdfFactory Pro" 试用版本创建
3、凝固过程中传热的特点
(2)金属凝固时存在着两个界面,即固液相间界面和金属铸 型间界面,在这些界面上,通常发生极为复杂的传热现象。
图1-5 金属-铸型界面模型
a) 微观的界面传热模型 b)简化的宏观界面传热模型
PDF 文件使用 "pdfFactory Pro" 试用版本创建
2、凝固过程中传热的方式 (2) 辐射:
T , 4 T 4 c c q = K − 100 100
其中: Tc--环境温度, T,c--铸件温度。 (3) 对流:
PDF 文件使用 "pdfFactory Pro" 试用版本创建
三、传热条件与凝固方式
液态金属 浇 入 铸型 后 ,随着温 度 的降 低 , 发生 凝固。 除 纯 金属和 共 晶 合金以外,凝固 都 在一定的温度 范围内 进 行。 在凝固过程中, 断 面 一 般呈 现 三 个 区 域 :固相 区 、凝 固 区 ( 液固 两 相 区 )、液相 区 。三 个区 域 在铸件断 面 的 位 置 和 宽窄随时 间 发生 变 化 。 这 种凝固过程中的动 态变 化情 况可用凝固动态曲线进行分析。 金属的凝固方式 ( 逐层 凝固、 糊状 凝固、中 间 凝固 ) 取决于凝固区的宽度,可以直接从凝固动态曲线上判断。
PDF 文件使用 "pdfFactory Pro" 试用版本创建
1、温度场的概念
物体内各点的温度分布情况,称为温度场。 根据温度T随时间τ的变化,温度场可分为: 不稳定温度场:T=f (x,y,z,τ) 稳定温度场: T=f (x,y,z) 根据温度 T 随坐标 x,y,z 的变化,温度场可分为: 一维温度场:T=f (x,τ) 二维温度场:T=f (x,y,τ) 三维温度场:T=f (x,y,z,τ) 最简单的温度场:一维稳定温度场 T=f (x)
凝固过程中的传热

第四章 凝固过程中的传热、传质与液 体流动
一、凝固过程中的传热 二、凝固过程中的传质 三、凝固过程中的液体流动
1
一、凝固过程中的传热
在凝固过程中,伴随着潜热的释放、液相与固相降温放出物理热,定向凝 固时,还需外加热源使凝固过程以特定的方式进行,各种热流被及时导 出,凝固才能维持。 宏观上讲,凝固方式和进程主要是由热流控制的。
10
4. 温度场与凝固过程的分析 铸件凝固时间的确定:
对温度场研究的目的是进行凝固过程分析。 以无限大平板铸件为例,由铸件放热与铸型吸热相等 Q1=Q2,可得
铸件凝固层厚度:? ? K ? , K为常数
Chvorinov 根据大量实验结果的分析,创造性地引入铸件模数的概念,
得出了著名的平方根定律: M ? K ? c
7
(1)解析法
直接从传热微分方程出发,在给定的
定解条件下,求出温度场的解析解
,实际条件下很少、只有引入许多假设
的条件下。
大平板铸件:
图中:S、L、M分别表示固相、液相和铸型的参数, Tk为凝固界面温度
根据界面上的热平衡:
?
S
? ? ?
?TS ?x
? ? ?x??
?
?
L
? ? ?
? TL ?x
? ? ?x??
边界条件相似 k s
按傅里叶导热微分方程可得相似条件:
k? k?
? ,? ,
即: l , 2
?
? ?,, ,,
l ,,2
?
??? ?
??
l2
k
2 l
Fo= ? ?
l2
?1
----定义为傅里叶数是
两个过程相似的必要条件是 Fo相等。
一、凝固过程中的传热 二、凝固过程中的传质 三、凝固过程中的液体流动
1
一、凝固过程中的传热
在凝固过程中,伴随着潜热的释放、液相与固相降温放出物理热,定向凝 固时,还需外加热源使凝固过程以特定的方式进行,各种热流被及时导 出,凝固才能维持。 宏观上讲,凝固方式和进程主要是由热流控制的。
10
4. 温度场与凝固过程的分析 铸件凝固时间的确定:
对温度场研究的目的是进行凝固过程分析。 以无限大平板铸件为例,由铸件放热与铸型吸热相等 Q1=Q2,可得
铸件凝固层厚度:? ? K ? , K为常数
Chvorinov 根据大量实验结果的分析,创造性地引入铸件模数的概念,
得出了著名的平方根定律: M ? K ? c
7
(1)解析法
直接从传热微分方程出发,在给定的
定解条件下,求出温度场的解析解
,实际条件下很少、只有引入许多假设
的条件下。
大平板铸件:
图中:S、L、M分别表示固相、液相和铸型的参数, Tk为凝固界面温度
根据界面上的热平衡:
?
S
? ? ?
?TS ?x
? ? ?x??
?
?
L
? ? ?
? TL ?x
? ? ?x??
边界条件相似 k s
按傅里叶导热微分方程可得相似条件:
k? k?
? ,? ,
即: l , 2
?
? ?,, ,,
l ,,2
?
??? ?
??
l2
k
2 l
Fo= ? ?
l2
?1
----定义为傅里叶数是
两个过程相似的必要条件是 Fo相等。
金属凝固理论 第4章 液态金属凝固过程中的传热、传质及液体流动

3) 金属的凝固温度
金属的凝固温度越高,在凝固过程中铸件表面和铸型内表 面的温度越高,铸型内外表面的温差就越大,致使铸件断 面温度场出现较大的梯度。如有色金属与钢铁相比,其温 度场较平坦。
2020/10/15
11/56
(2)铸型性质的影响 1)铸型的蓄热系数
铸型的蓄热系数越大,对铸件的冷却能力就越大, 铸件内的温度梯度就越大。铸型的导热系数越大, 能把铸型内表面吸收的热迅速传至外表面,使铸 型内表面保持强的吸热能力,铸件内的温度梯度 也就大。
向中心推进时,把铸型加热到更高温度,所以铸 件内温度场较平坦。
2)铸件的形状 铸件的棱角和弯曲表面,与平面的散热条件不同。
向外凸出的部分,散出的热量被较大体积的铸型 所吸收,铸件的冷速较大,如果铸件内凹的表面, 则相反。
2020/10/15
13/56
三、铸件的凝固方式及影响因素
TL
TS
L
S+L S
第四章 液态金属凝固过程 中的传热、传质及液体流动
2020/10/15
1/56
第一节 凝固过程中的传热
在材料成形过程中,液态金属的过热热量和 凝固潜热主要是通过传导而释放的。
2020/10/15
2/56
一、凝固过程中的热传导及傅里叶方程
温度场基本概念: 稳定温度场: 不随时间而变的温度场(即温度只是坐标的函 数),其表达式为:
2020/10/15
T n
Tw Tf
4/56
凝固过程中,热量传递有三种形式:传导、辐射、 对流。
以热传导为主。 热传导过程取决于温度的分布——温度场:温度
随空间和时间的变化。 T = f(x,y,z,t) Fourier热传导方程:
金属的凝固温度越高,在凝固过程中铸件表面和铸型内表 面的温度越高,铸型内外表面的温差就越大,致使铸件断 面温度场出现较大的梯度。如有色金属与钢铁相比,其温 度场较平坦。
2020/10/15
11/56
(2)铸型性质的影响 1)铸型的蓄热系数
铸型的蓄热系数越大,对铸件的冷却能力就越大, 铸件内的温度梯度就越大。铸型的导热系数越大, 能把铸型内表面吸收的热迅速传至外表面,使铸 型内表面保持强的吸热能力,铸件内的温度梯度 也就大。
向中心推进时,把铸型加热到更高温度,所以铸 件内温度场较平坦。
2)铸件的形状 铸件的棱角和弯曲表面,与平面的散热条件不同。
向外凸出的部分,散出的热量被较大体积的铸型 所吸收,铸件的冷速较大,如果铸件内凹的表面, 则相反。
2020/10/15
13/56
三、铸件的凝固方式及影响因素
TL
TS
L
S+L S
第四章 液态金属凝固过程 中的传热、传质及液体流动
2020/10/15
1/56
第一节 凝固过程中的传热
在材料成形过程中,液态金属的过热热量和 凝固潜热主要是通过传导而释放的。
2020/10/15
2/56
一、凝固过程中的热传导及傅里叶方程
温度场基本概念: 稳定温度场: 不随时间而变的温度场(即温度只是坐标的函 数),其表达式为:
2020/10/15
T n
Tw Tf
4/56
凝固过程中,热量传递有三种形式:传导、辐射、 对流。
以热传导为主。 热传导过程取决于温度的分布——温度场:温度
随空间和时间的变化。 T = f(x,y,z,t) Fourier热传导方程:
- 1、下载文档前请自行甄别文档内容的完整性,平台不提供额外的编辑、内容补充、找答案等附加服务。
- 2、"仅部分预览"的文档,不可在线预览部分如存在完整性等问题,可反馈申请退款(可完整预览的文档不适用该条件!)。
- 3、如文档侵犯您的权益,请联系客服反馈,我们会尽快为您处理(人工客服工作时间:9:00-18:30)。
T f Ti
06.3
金属型铸造的凝固传热
2、铸型一侧
x ' T T0 边界条件为: x' 0
T Ti
T A Berf x' 2 t '
铸型温度场为:
x E0 TM Ti (Ti T0 ) erf ( N ) S0 S
N S /M
06.3
M V / A C t f
这一定义与捷克和斯洛伐克著名工程师 Chvorinov 早 在上世纪30年代通过实验得出的结果一致。
06.2
非金属型铸造的凝固传热
2、温度因素
所作凝固阶段中凝固金属的温度保持不变的假设与 实际凝固过程不符。 尽管如此,推导出的公式仍然是适用的。因为: ① 理论计算时少算了传 热面积,计算时忽 略了棱角效应,相 铸件表面 当于少算了图中 A处 附近的热 的传热面积,故计 流线 算的凝固时间要比 实际的长;
06.2
非金属型铸造的凝固传热
② 实际过程中,温度实际分 布如图中左半区所示,但 计算时少算了图中斜线部 分代表的物理热,计算的 时间比实际凝固的时间短。 这两种因素相互抵消的结 果,使实测结果符合计算 值。
凝固结束时刻铸件 断面上的温度分布
06.3
由于金属型有很高的导热性能, 热流的限制环节通常不在铸型, 而在于 S-M 的界面处,界面热阻 导致了温度降 TiS-TiM ,特别是有 气隙存在时,温度降更大。 为了解存在有界面温度降的传 热问题,引进虚拟凝固层厚度和 虚拟铸型厚度的概念,即将一个 温度分布不连续问题处理成连续 问题,进而求出解析解。特点是 将界面热阻转化成了虚拟凝固层 与铸型的热阻,且两个热阻的温 度降之和恰好等于界面上的温度 降。
金属型铸造的凝固传热
三、界面温度Ti
对于虚拟的M-S间界面处,根据能量守恒和热流连续 条件,从凝固层传出的热流密度等于传入铸型的,即
TS TM S ( ) x ' 0 M ( ) x ' 0 x' x' T f Ti S M N(Ti T0) erf ( )
M T f T0 Ti T0 M erf ( )
06.3
金属型铸造的凝固传热
一、凝固时间
对于金属固相-液相一侧,当凝固的厚度为S’ 时,即
x' S '
T Tf
T f A Berf
S' 2 S t'
因为A、B和Tf皆为常数,所以可定义新常数——凝固 系数:
S ' / 2 S t'
t' 所以凝固S’厚度所需时间为:
无过热纯金属在砂 型中凝固时的近似温度分布
06.2
非金属型铸造的凝固传热
根据上述假设,子系统中无热源,热传导方程可简化为: T 2T m 2 t x
其通解为: T A Berf
x
2 mt
2
y
A、B——积分系数 erf(y)——误差函数
erf ( y )
e
0
2
可见,金属和铸型的热物性共同决定凝固速度,且凝固 度与凝固时间的平方根成反比。当金属的熔点高而熔化潜 和密度小时,凝固速度快;铸型的吸热能力 (m cm m ) 愈 有利于较快凝固。
06.2
非金属型铸造的凝固传热
四、实际铸件的情况
1、尺寸因素
对于一个体积为 V、表面积为 A的实际铸件,其完 全凝固的时间与其当量厚度 M 相关,通常定义当量厚 度:
纯金属在铸型中凝固时的传热模型 K-导热 C-对流 R-辐射 N-牛顿界面换热
06 凝固过程的传热
06.1
凝固过程传热基础
06.2
06.3
非金属型铸造的凝固传热
金属型铸造的凝固传热
06.1
凝固过程传热基础
一、凝固过程传热的特点
①有热源(凝固潜热释放)的传热且热源位置(固-液界面 处)在不断地移动,释放的凝固潜热量也随着凝固进程 而非线性地变化着。 ②系统同时存在两个界面,且界面处发生极为复杂的传热 现象。在液-固界面,即使对于宏观一维传热的单相凝固, 由于生长界面凹凸不平或固相以枝晶生长,即可能存在 三维传热现象,并存在对流传热;在铸型-金属固相界面, 存在界面热阻,甚至由于固相收缩存在气隙,形成微观 对流和辐射传热。 ③材料的热物理性质随降温发生非线性变化。
由于金属材料性能优,应用面广,且从金属材料的 制备、区域提纯、自生复合材料及单晶的制备到超高速冷 却制备金属玻璃,无不涉及凝固,凝固过程对金属材料的 组织、结构、性能及缺陷的形成与分布起着重要作用,因 此对其研究较为深入,理论也相对成熟,且金属凝固理论 可部分用于陶瓷和高分子材料体系。本篇主要以金属为对 象,介绍其凝固过程和相关理论。
M (T f T0 ) M erf ( )
根据L-S界面的热平衡关系,凝固潜热全部传入凝固层
Ti T0
exp( )[M erf ( )] C S
2
T f T0 L
对于具体的铸型和铸件,用叠代法很容易求出φ值。
06.3
金属型铸造的凝固传热
06.1
凝固过程传热基础
二、凝固温度场与凝固速度的计算
计算三子系统中各点温度随时间的变化 (温度场)和凝固速度非常重要,因为它们直 接影响金属的结晶组织,铸件的缩孔、缩松、 应力状态和使用性能。
计算方法主要有解析法和非解析法,非解 析法又包括图解法、电模拟法和数值模拟法。
06.1
凝固过程传热基础
。
界面层
金属-铸型界面模型
06.1
凝固过程传热基础
在整个凝固过程中,假设不计液相的热阻,凝固速 率主要受三种热阻的控制: ① 凝固金属层热阻:
Rs S / s
S——凝固金属层的厚度
② 铸型热阻: Rm I m / m ③ 界面热阻: Ri 1/ hi
Im——铸型的厚度
一般,对于金属型,Ri>>Rm或Rs ,故凝固速率受界面热 阻的控制;对于砂型,Rm>>Rs和Ri,凝固速率主要取决于 铸型热阻。
S '2 4 S 2
06.3
当 x' S 0 时,t ' t 0
金属型铸造的凝固传热
t0
S0
2
4 S 2
(S S 0 ) 2 凝固的总时间 t '=t 0 t 4 S 2 S 2 2SS0 凝固实际厚度S的时间为: t t 't 0 4 S 2
第二篇 凝固理论及应用
随着温度的降低,物质会由液相转变为固相, 即出现凝固现象。凝固的固相可能是晶体也可能 是非晶体,主要取决于物质的种类、液体的粘度 和冷却速度。 固 - 液相变是相变研究的重要内容,涉及的 范围非常广泛。根据相变的分类,固 - 液相变从 热力学分属一级相变,从结构型相变分属重构型 相变,从动力学分属非匀相型相变。
金属型铸造的凝固传热
铸件铸型系统的温度分布 a)铸件-铸型系统的温度分布; b)铸型温度在虚拟系统中的分布; c)铸件温度在虚拟系统中的分布
06.3 金属型铸造的凝固传热 为了简化求解过程,作如下假定: ① 一维传热,半无限大金属型; ② 界面换热系数hi为常数; ③ 金属在固定的凝固点Tf下凝固(相当于纯金属); ④ 忽略液体的过热和对流; ⑤ 铸件与铸型的物理参数不随温度而变。 建立如下坐标系: a)在铸件一侧 x' x S 0 b)在铸型一侧
M ( S S C S ) /( M M C M )
——决定于金属和铸型的热学性质和密度
06.3
金属型铸造的凝固传热
四、凝固系数φ
TS S ' L S ( ) ( )0 t ' x' (T f Ti ) 2 erf ( ) exp( ) CS L
λ——导热系数
相变 潜热 或反 应热
系统 内能 增加
该方程的实质反映了能量守恒,即微单元体中通过热传导增加 的热量加上本身发生的热量等于内能的增加。
06.1
凝固过程传热基础
通常,导热系数λ只是温度的函数,所以对于系统中 任意点(微单元体):
2T 2T 2T T C ( 2 2 2 )q t x y z 1 T 2 T 2 T 2T q 2 2 2 t x y z
早期为了改善金属的凝固质量,对凝固过程的研究 多偏重于工艺过程等外部因素,近20年来,借助冶金物理 化学、金属学和高等数学等的理论和方法,主要对凝固过 程的传热、传质和固 - 液界面动力学三方面进行了研究, 特别注重凝固的微观过程,即以原子的尺度去观察固 - 液 界面在凝固过程中所发生的现象,使凝固理论得到了较大 的发展。
凝 固 理 论 及 应 用
第六章 凝固过程的传热
第七章 凝固过程中液态金属的流动
第八章 凝固过程中的质量传输
第九章 凝固热力学
第十章 凝固动力学
第十一章 几种合金的凝固
06
凝固过程的传热
发生凝固的前提是金属 液的温度要降低且凝固时有潜 热释放,因此很自然地会提出 由此造成的热量如何流动的问 题。由于大部分金属材料都是 液态成型的问题,而液态成型 又是在模具(铸型)中进行的, 因此考虑铸型 + (金属液 L+金 属固相 S )为系统,也可以取 L+S 为系统,铸型为环境,重 点研究三个子系统中热量传递 和温度场问题。
d ,是奇函数。
根据边界条件得:T Tm (Tm T0 )erf
x
2 mt ——凝固过程中砂型断面上温度的分布方程
06.2
非金属型铸造的凝固传热
三、凝固层厚度与凝固时间的关系
M-S界面处的热流可计算为: m C m m T q x 0 m ( ) x 0 (T0 Tm ) x t 由于传入铸型中的热来自金属凝固释放的潜热, 凝固潜热可计算为: S q x0 L S ( )