数控机床设计第七章课后习题答案
第七章数控车床自动编程
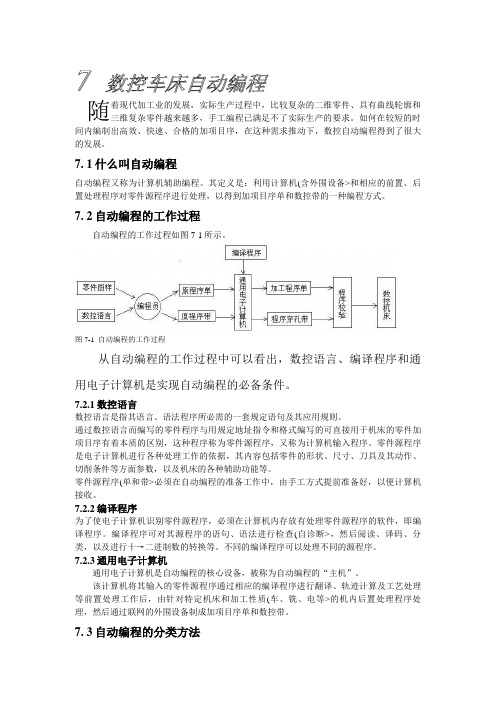
着现代加工业的发展,实际生产过程中,比较复杂的二维零件、具有曲线轮廓和三维复杂零件越来越多,手工编程已满足不了实际生产的要求。
如何在较短的时间内编制出高效、快速、合格的加项目序,在这种需求推动下,数控自动编程得到了很大的发展。
7. 1什么叫自动编程自动编程又称为计算机辅助编程。
其定义是:利用计算机(含外围设备>和相应的前置、后置处理程序对零件源程序进行处理,以得到加项目序单和数控带的一种编程方式。
7. 2自动编程的工作过程自动编程的工作过程如图7-1所示。
图7-1 自动编程的工作过程从自动编程的工作过程中可以看出,数控语言、编译程序和通用电子计算机是实现自动编程的必备条件。
7.2.1数控语言数控语言是指其语言、语法程序所必需的一套规定语句及其应用规则。
通过数控语言而编写的零件程序与用规定地址指令和格式编写的可直接用于机床的零件加项目序有着本质的区别,这种程序称为零件源程序,又称为计算机输入程序。
零件源程序是电子计算机进行各种处理工作的依据,其内容包括零件的形状、尺寸、刀具及其动作、切削条件等方面参数,以及机床的各种辅助功能等。
零件源程序(单和带>必须在自动编程的准备工作中,由手工方式提前准备好,以便计算机接收。
7.2.2编译程序为了使电子计算机识别零件源程序,必须在计算机内存放有处理零件源程序的软件,即编译程序。
编译程序可对其源程序的语句、语法进行检查(自诊断>,然后阅读、译码、分类,以及进行十→二进制数的转换等。
不同的编译程序可以处理不同的源程序。
7.2.3通用电子计算机通用电子计算机是自动编程的核心设备,被称为自动编程的“主机”。
该计算机将其输入的零件源程序通过相应的编译程序进行翻译、轨迹计算及工艺处理等前置处理工作后,由针对特定机床和加工性质(车、铣、电等>的机内后置处理程序处理,然后通过联网的外围设备制成加项目序单和数控带。
7. 3自动编程的分类方法随自动编程一般可按所用设备(编程系统>、插补类型和编程语言等进行分类,目前多按所用设备(除数控机床已具备其直接编程功能外>分类。
《机械制造装备设计》2版 习题思考题解答 第7章 普通机床数控化改造

第7章 普通机床数控化改造7.1 完成C616普通车床的数控改造。
利用微机对纵、横调向进给系统进行开环控制,纵向脉冲当量为0.01mm/脉冲,横向脉冲当量为0.005mm/脉冲,驱动元件采用步进电机,传动系统采用滚珠丝杠副,刀架采用自转位刀架。
答:一 纵向进给系统的设计计算1. 切削力计算切削力c F 为 vP F c c 1000= 查机床说明书,KW P c 4=。
取 m in /100m v =,主传动系统总效率65.0=总ηNN F F N N F F N F c p c f c 93615606.06.078015605.05.0156010065.04601000=⨯===⨯===⨯⨯⨯=2. 滚珠丝杠设计计算综合导轨车床丝杠的轴向力为()[]N N G F kF F c f t 6.1274800156016.078015.1)(=+⨯+⨯=++=μ取:15.1=k ,16.0=μG :工作台作用在导轨上的重量约800N1) 强度计算滚珠丝杠转速ht DP vf n π1000= 其中:m in /100m v = mm f 3.0= mm D 80= mm P h 6= 则min /206803.01001000r n t =⨯⨯⨯⨯=π 查表得h T 15000=,代入式(7.2),得出h h T n L t 1810150002*********=⨯⨯== 查表得:运转系数 2.1=d f , 硬度系数1=H f ,代入式(7.3),得出N N C 4.4008186.127412.13=⨯⨯⨯=选取滚珠丝杠型号为CB32x6—35E2。
2) 效率计算丝杠螺旋升角 523'= λ ,摩擦角01'=ϕ,则传动效率为:()()953.001523tan 523tan tan tan ='+''=+= ϕλλη 横向进给系统的设计与纵向进给系统设计类似,计算略。
数控机床结构与维护 习题及答案 (韩鸿鸾第2版 ) 第5--7章

第五章自动换刀装置装调与维修一、填空题1.经济型数控车床方刀架换刀时的动作顺序是:刀架抬起、刀架转位、刀架定位和夹紧。
2.车削中心动力刀具主要由三局部组成:动力源、变速装置和刀具附件(钻孔附件和铳削附件等)。
3.车削中心加工工件端面或柱面上与工件不同心的外表时,主轴带开工件作分度运动或直接参与插补运动,切削加工主运动由动力刀具来实现。
4.无机械手换刀的方式是利用刀库与机床主轴的相对运动实现刀具交换。
5.刀库一般使用电动机或液压系统来提供转动动力,用刀具运动机构来保证换刀的可靠性,用定位机构来保证更换的每一把刀具或刀套都能可靠地准停。
6.刀库的功能是储存加工工序所需的各种刀具,并按程序指令,把将要用的刀具准确地送到换刀位置,并接受从主轴送来的已用刀具。
二、选择题(请将正确答案的代号填在空格中)1.代表自动换刀的英文是(B)。
A.APCB.ATCC.PLC2.双齿盘转塔刀架由(C )将转位信号送可编程控制器进行刀位计数。
A.直光栅B.编码器C.圆光栅3.刀库的最大转角为(C ),根据所换刀具的位置决定正转或反转,由控制系统自动判别,以使找刀路径最短。
A.90°B.1200C. 180°4.回转刀架换刀装置常用数控(A )。
A.车床B.铳床C.钻床5,数控机床自动选择刀具中任意选择的方法是采用(C )来选刀换刀。
A.刀具编码B.刀座编码C.计算机跟踪记忆6.加工中心的自动换刀装置由驱动机构、(A )组成。
A,刀库和机械手B.刀库和控制系统C.机械手和控制系统D.控制系统7.圆盘式刀库的安装位置一般在机床的(A )上。
A.立柱B.导轨C.工作台8 .加工中心换刀可与机床加工重合起来,即利用切削时间进行(B )o三、判断题(正确的划“ J”,错误的划“X”)1. (X)数控车床采用刀库形式的自动换刀装置。
2. (义)排刀式刀架一般用于大规格数控车床。
3. (X)无机械手换刀主要用于大型加工中心。
数控技术 第七章 数控机床的进给伺服系统

三 步进电动机的基本控制方法
(2) 双电压功率放大电路 优点:功耗低,改善了脉冲 优点:功耗低, 前沿。 前沿。 缺点:高低压衔接处电流波 缺点: 形呈凹形, 形呈凹形,使步进电机 输出转矩降低, 输出转矩降低,适用于 大功率和高频工作的步 进电机。 进电机。
三 步进电动机的基本控制方法
(3) 斩波恒流功放电路 优点: 优点:1)R3较小(小 R3较小( 较小 于兆欧) 于兆欧)使整个 系统功耗下降, 系统功耗下降, 效率提高。 效率提高。 2)主回路不串 电阻, 电阻,电流上升 快,即反应快。 即反应快。 3)由于取样绕 组的反馈作用, 组的反馈作用, 绕组电流可以恒定在确定的数值上, 绕组电流可以恒定在确定的数值上,从而保证在很大频率范 围内,步进电机能输出恒定的转矩。 围内,步进电机能输出恒定的转矩。
二 数控机床对伺服系统的基本要求
1 高精度 一般要求定位精度为0.01~0.001mm; ; 一般要求定位精度为 高档设备的定位精度要求达到0.1um以上。 以上。 高档设备的定位精度要求达到 以上 2 快速响应 3 调速范围宽 调速范围指的是 max/nmin 。 调速范围宽:调速范围指的是 调速范围指的是:n 进给伺服系统:一般要求 进给伺服系统 一般要求0~30m/min,有的已达到 一般要求 ,有的已达到240m/min 主轴伺服系统:要求 主轴伺服系统 要求1:100~1:1000恒转矩调速 要求 恒转矩调速 1:10以上的恒功率调速 以上的恒功率调速
一 直流伺服电动机调速原理
7-30 直流电动机的机械特性
二 直流电动机的PWM调速原理 直流电动机的 调速原理
7-24 脉宽调制示意图 脉宽调制示意图
Ud =
τ
T
U = δ T U δ T 称为导通率
第七章机床主要技术参数

10
E1
③为了便于采用双速或三速电动机,公比为2的某次方根
E2
2
机械工程学院 School of Mechanical Engineering
第七章 机床主要技术参数的确定
标准公比
①公比是2的某次方根,其数列每隔若干项增加或缩小2 倍,如 3 2 数列为10、12.5、16、20、25、32、40等, 每隔两级增大2倍。
机械工程学院 School of Mechanical Engineering
第七章 机床主要技术参数的确定 (2)运动参数 ①主运动参数 Ⅰ 主运动最高转速nmax和最低转速nmin Ⅱ 转速级数Z Ⅲ 公比φ Ⅳ 变速范围Rn= nmax/ nmin ②进给运动参数:情况同① (3)动力参数:指主运动、进给运动和其他辅助运动的 动力消耗。
ηS 可以用于主传动功率P主和进给传动功率Ps行粗略估算 车床:Ps=(0.03~0.04) P主(KW)
钻床:Ps=(0.04~0.05) P主(KW)
铣床:Ps=(0.04~0.05) P主(KW)
机械工程学院 School of Mechanical Engineering
第七章 机床主要技术参数的确定 7.3.3 快速运动功率的确定
按照等比数列排列的主轴转速,往往可以通过串联若干滑 移齿轮来实现。所以主轴转速n n=n电•iⅠ•iⅡ•••= n电•i总
因此,主轴转速按照等比数列排列时,充分利用了每一对滑移齿 轮的传动比,用同样数量的齿轮,可得到较多的变速级数。
机械工程学院 School of Mechanical Engineering
第七章 机床主要技术参数的确定 4.公比的选用
设主轴最高转速与最低转速之比值,称为转速范围Rn,则: Rn=nmax /nmin = nZ/n1 =n1φ z-1/n1 =φ z-1 即 z=1+lgRn/lgφ (Z为转速级数) 选用标准公比φ的一般原则: ①用于大批大量生产的自动化与半自动化机床,因为要求较高的 生产率,相对转速损失要小,因此φ要小些,一般取1.12或1.26。 ②大型机床加工大尺寸工件,机动时间长,选择合理的切削速度 对提高生产率作用较大,φ应小些,取1.12或1.26。 ③中型通用机床,万能性较大,因而要求转速级数z要多一些, 但结构又不能过于复杂, φ常取1.26或1.41。 ④小型机床切削加工时间常比辅助时间少,结构要求简单一些, 变速级速也不多,公比φ常取1.58或1.78。
数控技术第七章 高速切削加工实例

图7-8 粗加工刀具路径
第一节 螺旋薄壁零件加工实例
6)单击“接受”按钮。
图7-9 粗加工仿真
第一节 螺旋薄壁零件加工实例
3.精加工 1)在窗口左侧PowerMILL资源管理器中,右击“刀具”→“产生 刀具”→“端铣刀”,设置铣刀直径为4mm,长度为20mm。 2)在主工具栏中单击刀具路径策略按钮,打开“新的”对话框, 选择“精加工”选项卡,如图7-10所示,然后选择“等高精加 工”,在“等高精加工”对话框中作如图7-11所示的设置。
图7-10 “精加工”选项卡
第一节 螺旋薄壁零件加工实例
图7-11 “等高精加工”对话框
3)在主工具栏中单击进给和转速按钮,
第一节 螺旋薄壁零件加工实例
打开“进给和转速”对话框,设置如图7-12所示参数后,单击 “接受”按钮,退出该对话框。
图7-12 精加工“进给和转速”对话框
第一节 螺旋薄壁零件加工实例
第一节 螺旋薄壁零件加工实例
2)在主工具栏中单击毛坯按钮,打开“毛坯”对话框,在“限界” 选项中输入其长、宽、高3个方向的极限坐标,如图7-2所示。
图7-2 “毛坯”对话框
第一节 螺旋薄壁零件加工实例
2.粗加工
图7-3 “端铣刀”对话框
第一节 螺旋薄壁零件加工实例
1)在刀具工具栏中单击按钮,显示出所有刀具图标,单击按钮, 打开“端铣刀”㊀对话框,选择“刀尖”选项卡,设置参数如图73所示,单击“关闭”退出。 2)在主工具栏中单击刀具路径策略按钮,打开“新的”对话框, 选择“三维区域清除”选项卡,选择“偏置区域清除”,如图7-4 所示,“偏置区域清除”对话框中的设置如图7-5所示。 3)在主工具栏中单击“进给和转速”按钮,打开“进给和转速” 对话框,设置参数如图7-6所示,单击“接受”按钮,退出该对话 框。 4)在主工具栏中单击按钮,打开“快进高度”对话框,按图7-7所 示设置参数后,单击“接受”按钮,退出对话框。
数控装备设计 各章习题答案

讨论题: 1、步进电机的主要特征是什么?基本工作状态是怎样的? 2、测量装置的作用是什么? 3、增量测量和绝对测量有何区别? 4、简述直流电动机的调速原理和调速方式? 5、简述旋转变压器工作原理,它有几种型式?
第4章
习题:
1、某些指令一旦写入程序中,在后续程序段中会一直有效,直到出现同组指令,才会被取
O
BC
Y
D
α
GK
A
X
讨论题 1
F
y A(5,3)
x
o
讨论题 3
4、什么是 B 刀具半径补偿?C 刀具半径补偿? 5、何谓数值积分法,它进行直线插补和圆弧插补时有何不同?
第3章 习题: 1、数控机床对伺服系统有哪些基本要求? 2、判断题:
1)给步进电机输入一个脉冲信号,其转子转过的角度称为步距角。( ) 2)伺服系统可分为三种类型,其中的全闭环系统因设计和调整较简单,故被广泛应用。 () 3、三相步进电动机常用的工作方式:______________________、______________________ 和_____________________________。 4、结合下图说明步进电动机工作原理。
较大。 (5)惯量匹配。移动部件加减速时都有较大惯量,要求系统的快速响应性能要好,因而
电动机的惯量与移动部件的惯量要匹配。 (6)较强的过载能力。要求电动机加减速时有很快的响应速度,使电动机可能在过载条
件下工作,这就要求电动机有较强的抗过载能力。 2、1)正确 2)错误 3、单三拍(工作方式) 双三拍(工作方式) 六拍(工作方式) 4、如图所示步进电机有 A、B、C 三相,每相有两个磁极,转子有四个磁极。当 A 相绕组 通以直流电时,定子 A 相磁极产生磁场,并对转子产生磁拉力,使转子的 1、3 极与定子的 A 相磁极对齐。后再将 B 相绕组通以直流电时,B 相磁极产生磁通,这时转子 2、4 极与定 子 B 相磁极对齐。如果按 A→B→C→A 的通电顺序,转子则沿逆时针方向一步步转动起来, 每步转过 30°,这个角度叫做步距角。
数控铣床加工实训智慧树知到答案章节测试2023年陕西工业职业技术学院

第一章测试1.世界上第一台数控机床是()年研制出来的。
A:1958B:1947C:1952D:1930答案:C2.开环控制系统是指不带()的控制系统。
A:测量B:数控C:反馈D:伺服答案:A3.对数控铣床坐标轴最基本的要求是()轴控制。
A:2B:3C:4D:5答案:A4.数控机床开机后,必须先进行返回参考点操作。
()A:错B:对答案:B5.滚珠丝杠副消除轴向间隙的目的主要是减小摩擦力矩。
()A:对B:错答案:B第二章测试1.采用半径编程方法填写圆弧插补程序段时,当其圆弧所对应的圆心角()180度时,该半径R取负值。
A:大于B:小于C:小于或等于D:大于或等于答案:A2.()符号的意义为“复位”。
A:DELB:RESETC:COPYD:AuTo答案:B3.G00和G01的运行轨迹都一样,只是速度不一样。
()A:对B:错答案:B4.只需根据零件图样进行编程,而不必考虑是刀具运动还是工件运动。
()A:对B:错答案:B5.下列G代码中()指令为非模态G代码。
A:G00B:G02C:G28D:G01答案:C第三章测试1.绝对编程和增量编程不能在同一程序中混合使用。
()A:错B:对答案:A2.刀具补偿包括长度补偿和()补偿。
A:直径B:半径C:三项均对D:轴向答案:B3.下列哪一个指令不能设立工件坐标系()。
A:G54B:G91C:G92D:G55答案:B4.在铣床上加工表面有硬皮的毛坯零件时,应采用顺铣方式。
()A:错B:对答案:A5.立铣刀的刀位点是刀具中心线与刀具底面的交点。
()A:错B:对答案:B第四章测试1.刀位点是刀具上代表刀具在工件坐标系的一个点,对刀时,应使刀位点与对刀点重合。
()A:错B:对答案:B2.刀具半径补偿指令在返回零点状态是()。
A:初始状态B:暂时抹消C:抹消D:模态保持答案:D3.设定的加工XY平面由()指令执行。
A:G17B:G19C:G20D:G18答案:A4.在数控铣床上进行对刀练习,初学者可以用冷却喷管模拟对刀操作训练。
- 1、下载文档前请自行甄别文档内容的完整性,平台不提供额外的编辑、内容补充、找答案等附加服务。
- 2、"仅部分预览"的文档,不可在线预览部分如存在完整性等问题,可反馈申请退款(可完整预览的文档不适用该条件!)。
- 3、如文档侵犯您的权益,请联系客服反馈,我们会尽快为您处理(人工客服工作时间:9:00-18:30)。
第七章课后习题答案
1.简述数控车床的分类。
⑴按数控系统功能分类:①经济型数控车床;②全功能型数控车床;
③车削中心;④FMC车床。
⑵按主轴的配置形式分类:①卧式数控车床;②立式数控车床。
⑶按数控系统控制的轴数分类:①两轴控制的数控车床;②四轴控制
的数控车床。
⑷按加工零件的基本类型:卡盘式数控车床、顶尖式数控车床。
⑸按数控系统的不同控制方式分类:直线控制数控车床、轮廓控制数
控车床等。
⑹按性能分类:多主轴车床、双主轴车床、纵切式车床、刀塔式车床、
排刀式车床等。
2.数控车床的组成如何。
①车床主机。
主机是数控车床的机械部件,主要包括床身、主轴箱、
刀架、尾座、进给传动机构等。
②数控系统。
数控系统是数控车床的控制核心,其主体是一台计算机(包括CPU、存储器、CRT等)。
③伺服驱动系统。
伺服驱动系统是数控车床切削工作的动力部分,主要实现主运动和进给运动,由伺服驱动电路和伺服驱动装置两大部分组成。
④辅助装置。
辅助装置是数控车床中为加工服务的配套部分,如液压、气动装置,冷却、照明、润滑、防护和排屑装置等。
⑤机外编程器。
机外编程器是在普通的计算机上安装一套编程软件,使用这套编程软件以及相应的后置处理软件,就可以生成加工程序。
通过车床控制系统上的通信接口或其他存储介质(如软盘、光盘等),把生成的加工程序输入到车床的控制系统中完成零件的加工。
3.简述数控车床的特点有哪些。
⑴结构特点:①传动链短;②机床刚度大,转速较高,可实现无级变速。
③轻拖
动,润滑好,排屑方便,机床寿命较长;④加工冷却充分,防护较
严密;⑤自动换刀;⑥模块化设计等。
⑵加工特点:①高精度;②高效率;③高柔性和高可靠性;④工艺能力强。
4.数控车床主要应用与何种零件加工。
①精度要求高的回转体零件;②轮廓形状复杂的回转体零件;③表面
粗糙度好的回转体零件;④特殊螺纹的回转体零件;⑤超精密、超低
表面粗糙度的回转体零件。
5.简述数控铣床的分类。
⑴按主轴布置形式分类:①立式数控铣床;②卧式数控铣床;③立卧
两用数控铣床。
⑵按数控系统控制的坐标轴数量分类:①2.5坐标联动数控铣床;②3坐标联动数控铣床;③4坐标联动数控铣床;④5坐标联动数控铣床。
6.数控铣床的组成如何。
①主轴部件。
是切削加工的功率输出部件。
它由主轴箱、主轴电动机、主轴和主轴轴承等零件组成。
主轴的启、停和变转速等动作均由数控系统控制,并且通过装在主轴上的刀具参与切削运动。
②进给伺服系统。
由进给电动机和进给执行机构组成,按照程序设定的进给速度实现刀具和工件之间的相对运动,包括直线进给运动和旋转运动。
③控制系统。
控制系统部分是由CNC装置、可编程控制器、伺服驱动装置以及操作面板等组成。
它是执行顺序控制动作和完成加工过程的控制中心。
④辅助装置。
辅助装置包括润滑、冷却、排屑、防护、液压、气动和检测系统等部分。
这些装置虽然不直接参与切削运动,但对数控铣床的加工效率、加工精度和可靠性起着保障作用,是数控铣床中不可缺少的部分。
⑤机床基础件。
机床基础件通常是指底座、立柱、横梁等,它是整个机床的基础和框架。
它们主要承受机床的静载荷以及在加工时产生的切削负载,必须有足够的刚度。
7.数控铣削的主要加工对象有哪些?其特点是什么。
主要加工对象:①平面类零件,其特点是各个加工单元面是平面或可以展开为平面;②变斜角类零件,其特点是加工面不能展开为平面,但在加工中,加工面与铣刀圆周接触的瞬间为一条线;③曲面类零件,其特点是加工面不能展开为平面,加工面始终与铣刀点接触。
8.简述加工中心的分类。
⑴按布局方式分类:①立式加工中心;②卧式加工中心;③龙门式加工中心;④复合加工中心;⑤并联机床(虚拟轴机床)。
⑵按换刀形式分类:①带刀库、机械手的加工中心;②无机械手的加工中心;③转塔刀库式加工中心。
⑶按机床功用分类:①镗铣加工中心机床;②钻削加工中心机床;③车削加工中心机床。
⑷按运动坐标轴数和同时控制坐标轴数:三轴二联动、三轴三联动、四轴三联动、五轴四联动、六轴五联动及其多轴五联动等。
⑸按工作台数量和功能分类:单工作台加工中心、双工作台加工中心、多工作台加工中心。
⑹按加工精度分类:普通加工中心和高精度加工中心。
9.加工中心的组成如何。
组成:①基础部件;②组成部件;③伺服系统;④数控系统;⑤自动换刀系统;
⑥辅助装置。
10.简述加工中心的特点有哪些。
①机床的刚度高、抗振性好。
为了满足加工中心高自动化、高速度、高精度、高可靠性的要求,加工中心的静刚度、动刚度和机械结构系统的阻尼比都高于普通机床(机床在静态力作用下所表现的刚度称为机床的静刚度;机床在动态力作用下所表现的刚度称为机床的动刚度)。
②机床的传动系统结构简单,传递精度高,速度快。
加工中心传动装置主要有三种,即滚珠丝杠副;静压蜗杆-蜗母条;预加载荷双齿轮-齿条。
它们由伺服电机直接驱动,省去齿轮传动机构,传递精度高,速度快。
一般速度可达15m/min,最高可达100m/min;
③主轴系统结构简单,无齿轮箱变速系统(特殊的也只保留1~2级齿轮传动)。
主轴功率大,调速范围宽,并可无级调速。
目前加工中心95%以上的主轴传动都采用交流主轴伺服系统,速度可从10~20000r/min无级变速。
驱动主轴的伺服电机功率一般都很大,是普通机床的1~2倍,由于采用交流伺服主轴系统,主轴电动机功率虽大,但输出功率与实际消耗的功率保持同步,不存在大马拉小车那种浪费电力的情况,因此其工作效率最高,从节能角度看,加工中心又是节能型的设备;
④加工中心的导轨都采用了耐磨损材料和新结构,能长期的保持导轨的精度,在高速重切削下,保证运动部件不振动,低速进给时不爬行及运动中的高灵敏度。
导轨采用钢导轨、淬火硬度≥HRC ,与导轨配合面用聚四氟乙烯贴层。
这样处理的优点:a.摩擦系数小;b.耐磨性好;c.减振消声;d.工艺性好。
所以加工中心的精度寿命比一般的机床高;
⑤设置有刀库和换刀机构。
这是加工中心与数控铣床和数控镗床的主要区别,使加工中心的功能和自动化加工的能力更强了。
加工中心的刀库容量少的有几把,多的达几百把。
这些刀具通过换刀机构自动调用和更换,也可通过控制系统对刀具寿命进行管理;
⑥控制系统功能较全。
它不但可对刀具的自动加工进行控制,还可对刀库进行控制和管理,实现刀具自动交换。
有的加工中心具有多个工作台,工作台可自动交换,不但能对一个工件进行自动加工,而且可对一批工件进行自动加工。
这种多工作台加工中心有的称为柔性加工单元。
随着加工中心控制系统的发展,其智能化的程度越来越高,如FANUCl6系统可实现人机对话、在线自动编程,通过彩色显示器与手动操作键盘的配合,还可实现程序的输入、编辑、修改、删除,具有前台操作、后台编辑的前后台功能。
加工过程中可实现在线检测,检测出的偏差可自动修正,保证首件加工一次成功,从而可以防止废品的产生。