粗糙度与加工方法
机械加工方法与零件的粗糙度及精度等级之间的对应表

机械加工方法与零件的粗糙度及精度等级之间的对应表本文章由里氏硬度计/官方网站发布。
序号=1Ra值不大于μm=100表面状况=明显可见的刀痕加工方法=粗车、镗、刨、钻应用举例=粗加工的表面,如粗车、粗刨、切断等表面,用粗镗刀和粗砂轮等加工的表面,一般很少采用-------------------------------------------------- ---------序号=2Ra值不大于μm=25、50表面状况=明显可见的刀痕加工方法=粗车、镗、刨、钻应用举例=粗加工后的表面,焊接前的焊缝、粗钻孔壁等-------------------------------------------------- ---------序号=3Ra值不大于μm=12.5表面状况=可见刀痕加工方法=粗车、刨、铣、钻应用举例=一般非结合表面,如轴的端面、倒角、齿轮及皮带轮的侧面、键槽的非工作表面,减重孔眼表面-------------------------------------------------- ---------序号=4Ra值不大于μm=6.3表面状况=可见加工痕迹加工方法=车、镗、刨、钻、铣、锉、磨、粗铰、铣齿应用举例=不重要零件的配合表面,如支柱、支架、外壳、衬套、轴、盖等的端面。
紧固件的自由表面,紧固件通孔的表面,内、外花键的非定心表面,不作为计量基准的齿轮顶圈圆表面等-------------------------------------------------- ---------序号=5Ra值不大于μm=3.2表面状况=微见加工痕迹加工方法=车、镗、刨、铣、刮1~2点/cm^2、拉、磨、锉、滚压、铣齿应用举例=和其他零件连接不形成配合的表面,如箱体、外壳、端盖等零件的端面。
要求有定心及配合特性的固定支承面如定心的轴间,键和键槽的工作表面。
不重要的紧固螺纹的表面。
需要滚花或氧化处理的表面-------------------------------------------------- ---------序号=6Ra值不大于μm=1.6表面状况=看不清加工痕迹加工方法=车、镗、刨、铣、铰、拉、磨、滚压、刮1~2点/cm^2铣齿应用举例=安装直径超过80mm的G级轴承的外壳孔,普通精度齿轮的齿面,定位销孔,V型带轮的表面,外径定心的内花键外径,轴承盖的定中心凸肩表面-------------------------------------------------- ---------序号=7Ra值不大于μm=0.8表面状况=可辨加工痕迹的方向加工方法=车、镗、拉、磨、立铣、刮3~10点/cm^2、滚压应用举例=要求保证定心及配合特性的表面,如锥销与圆柱销的表面,与G级精度转动轴承相配合的轴径和外壳孔,中速转动的轴径,直径超过80mm的E、D级转动轴承配合的轴径及外壳孔,内、外花键的定心内径,外花键键侧及定心外径,过盈配合IT7级的孔(H7),间隙配合IT8~IT9级的孔(H8,H9),磨削的齿轮表面等-------------------------------------------------- ---------序号=8Ra值不大于μm=0.4表面状况=微辨加工痕迹的方向加工方法=铰、磨、镗、拉、刮3~10点/cm^2、滚压应用举例=要求长期保持配合性质稳定的配合表面,IT7级的轴、孔配合表面,精度较高的齿轮表面,受变应力作用的重要零件,与直径小于80mm的E、D级轴承配合的轴径表面、与橡胶密封件接触的轴的表面,尺寸大于120mm的IT13~IT16级孔和轴用量规的丈量表面-------------------------------------------------- ---------序号=9Ra值不大于μm=0.2表面状况=不可辨加工痕迹的方向加工方法=布轮磨、磨、研磨、超级加工应用举例=工作时受变应力作用的重要零件的表面。
各种加工方法的经济精度和表面粗糙度

各种加工方法能够达到的尺寸的经济精度表2圆锥形孔加工的经济精度表3圆柱形深孔加工的经济精度表4花键孔加工的经济精度表6端面加工的经济精度(mm)表8同时加工平行表面的经刘精度(mm)表面长度和宽(mm)W120>120〜300加工性质注:指两平行表面距离的尺寸精度。
91<lm2端铣刀铣削的加工精度在相同的条件下大体上比圆柱铣刀铣削高一级。
3细铣仅用于端铣刀铣削。
表10公制螺纹加工的经济精度表11花键加工的经济精度表12齿形加工的经济精度单头滚刀滚齿(m=1〜20mm)滚刀精度等级:AA 6〜7A8B 9C 10 圆盘形插齿刀插齿(m=1〜20mm)插齿刀精度等级:AA 6A 7B 8 磨齿:成形砂轮仿形法5〜6盘形砂轮范成法3〜6 两个盘形砂轮范成法3〜6 蜗杆砂轮范成法4〜6 用铸铁研磨轮研齿5〜6 直齿圆锥齿轮刨齿8螺旋齿圆锥齿轮刀盘铣齿8蜗轮模数滚刀滚蜗轮8 热轧齿轮(m=2〜8mm) 8〜9 热轧后冷校准齿型(m=2〜8mm)7〜8 冷轧齿轮(m W1.5mm) 7圆盘形插齿刀剃齿(m=l〜20mm)剃齿刀精度等级:ABC各种加工方法能够达到的形状的经济精度14231516牛头刨床表17平行度的经济精度表18端面跳动和垂直度的经济精度表19同轴度的经济精度表20轴心线相互平行的孔的位置经济精度最大刨削长度(mm)各种加工方法能够达到的零件表面粗糙度表22各种加工方法能够达到的零件表面粗糙度>20〜160 >20〜80>©150(mm)粗(有表皮)扩孔word格式-可编辑-感谢下载支持砂轮清理>20〜320 >3.2〜80滚压加工>0.2〜3.2钳工锉削各类型面的加工方案及经济精度表23外圆表面加工方案表24孔加工方案word格式-可编辑-感谢下载支持标准公差及形位公差附表1标准公差值1mm IT14IT18附表2平面度、直线度公差值1《金属机械加工工艺人员手册》修订本上海科学技术出版社1981年2《机械制造工艺学》顾崇衔等编著陕西科学技术出版社1982年3《航空机械设计手册》第三机械工业部612所编1979年4《机械制造工艺学课程设计简明手册》华中工学院机械制造工艺教研室编1981年5《机械工程手册》第46篇机械工业出版社1981年6《圆柱齿轮加工》上海科学技术出版社1979年切削用量切削用量的选择原则正确地选择切削用量,对提高切削效率,保证必要的刀具耐用度和经济性,保证加工质量具有重要的作用。
机械加工方法与零件的粗糙度及精度等级之间的对应表

机械加工方法与零件的粗糙度及精度等级之间的对应表序号=1Ra值不大于呵=100表面状况=明显可见的刀痕加工方法=粗车、镗、刨、钻应用举例=粗加工的表面,如粗车、粗刨、切断等表面,用粗镗刀和粗砂轮等加工的表面,一般很少采用序号=2Ra值不大于呵=25、50表面状况=明显可见的刀痕加工方法=粗车、镗、刨、钻应用举例=粗加工后的表面,焊接前的焊缝、粗钻孔壁等序号=3Ra值不大于呵=12.5表面状况=可见刀痕加工方法=粗车、刨、铣、钻应用举例=一般非结合表面,如轴的端面、倒角、齿轮及皮带轮的侧面、键槽的非工作表面,减重孔眼表面序号=4Ra值不大于呵=6.3表面状况=可见加工痕迹加工方法=车、镗、刨、钻、铣、锉、磨、粗铰、铣齿应用举例=不重要零件的配合表面,如支柱、支架、外壳、衬套、轴、盖等的端面。
紧固件的自由表面,紧固件通孔的表面,内、外花键的非定心表面,不作为计量基准的齿轮顶圈圆表面等序号=5Ra值不大于呵=3.2表面状况=微见加工痕迹加工方法二车、镗、刨、铣、舌I」1~ 2点/cm A2、拉、磨、锂、滚压、铣齿应用举例=和其他零件连接不形成配合的表面,如箱体、外壳、端盖等零件的端面。
要求有定心及配合特性的固定支承面如定心的轴间,键和键槽的工作表面。
不重要的紧固螺纹的表面。
需要滚花或氧化处理的表面序号=6Ra值不大于呵=1.6表面状况=看不清加工痕迹加工方法二车、镗、刨、铣、铰、拉、磨、滚压、舌J 1 ~ 2点/盯八2铣齿应用举例二安装直径超过80mm的G级轴承的外壳孔,普通精度齿轮的齿面,定位销孔,V型带轮的表面,外径定心的内花键外径,轴承盖的定中心凸肩表面---序号=7Ra值不大于呵=0.8表面状况=可辨加工痕迹的方向加工方法二车、镗、拉、磨、立铣、舌J 3~ 10点/cm A2、滚压应用举例=要求保证定心及配合特性的表面,如锥销与圆柱销的表面,与G 级精度滚动轴承相配合的轴径和外壳孔,中速转动的轴径,直径超过80mm 的E、D 级滚动轴承配合的轴径及外壳孔,内、外花键的定心内径,外花键键侧及定心外径,过盈配合IT7级的孔(H7),间隙配合IT8〜IT9级的孔(H8,H9),磨削的齿轮表面等序号=8Ra值不大于呵=0.4表面状况=微辨加工痕迹的方向加工方法二铰、磨、镗、拉、舌J 3~ 10点/盯八2、滚压应用举例二要求长期保持配合性质稳定的配合表面,IT7级的轴、孔配合表面,精度较高的齿轮表面,受变应力作用的重要零件,与直径小于80mm 的E、D级轴承配合的轴径表面、与橡胶密封件接触的轴的表面,尺寸大于120mm 的IT13〜IT16级孔和轴用量规的测量表面序号=9Ra值不大于呵=0.2表面状况=不可辨加工痕迹的方向加工方法=布轮磨、磨、研磨、超级加工应用举例=工作时受变应力作用的重要零件的表面。
粗糙度25的加工方式

粗糙度25的加工方式
粗糙度25意味着在制造过程中留下的表面粗糙度是25微米。
以下是一些可能的加工方式:
1.铣削-使用高速旋转的铣刀在工件表面切削,可以在较短的时间内获得精度较高的表面。
2.砂纸磨削-使用砂纸或砂轮磨削工件表面,可以逐渐减少表面的粗糙度,直到达到所需水平。
3.抛光-使用抛光剂和旋转的抛光头,可以在工件表面生成光滑的表面。
4.化学刻蚀-使用化学溶液在表面蚀刻工件,可以在表面留下一定深度的凹陷和起伏,以减少表面的粗糙度。
5.激光表面处理-使用激光照射表面,可以使表面物质蒸发或熔化,从而达到磨削或抛光的效果。
粗糙度与加工方法对应表

表面粗糙度选用-----------------------------------------------------------序号=1Ra值不大于\μm=100表面状况=明显可见的刀痕加工方法=粗车、镗、刨、钻应用举例=粗加工的表面,如粗车、粗刨、切断等表面,用粗镗刀和粗砂轮等加工的表面,一般很少采用-----------------------------------------------------------序号=2Ra值不大于\μm=25、50表面状况=明显可见的刀痕加工方法=粗车、镗、刨、钻应用举例=粗加工后的表面,焊接前的焊缝、粗钻孔壁等-----------------------------------------------------------序号=3Ra值不大于\μm=12.5表面状况=可见刀痕加工方法=粗车、刨、铣、钻应用举例=一般非结合表面,如轴的端面、倒角、齿轮及皮带轮的侧面、键槽的非工作表面,减重孔眼表面-----------------------------------------------------------序号=4Ra值不大于\μm=6.3表面状况=可见加工痕迹加工方法=车、镗、刨、钻、铣、锉、磨、粗铰、铣齿应用举例=不重要零件的配合表面,如支柱、支架、外壳、衬套、轴、盖等的端面。
紧固件的自由表面,紧固件通孔的表面,内、外花键的非定心表面,不作为计量基准的齿轮顶圈圆表面等-----------------------------------------------------------序号=5Ra值不大于\μm=3.2表面状况=微见加工痕迹加工方法=车、镗、刨、铣、刮1~2点/cm^2、拉、磨、锉、滚压、铣齿应用举例=和其他零件连接不形成配合的表面,如箱体、外壳、端盖等零件的端面。
要求有定心及配合特性的固定支承面如定心的轴间,键和键槽的工作表面。
机械加工方法与零件的粗糙度及精度等级之间的对应表
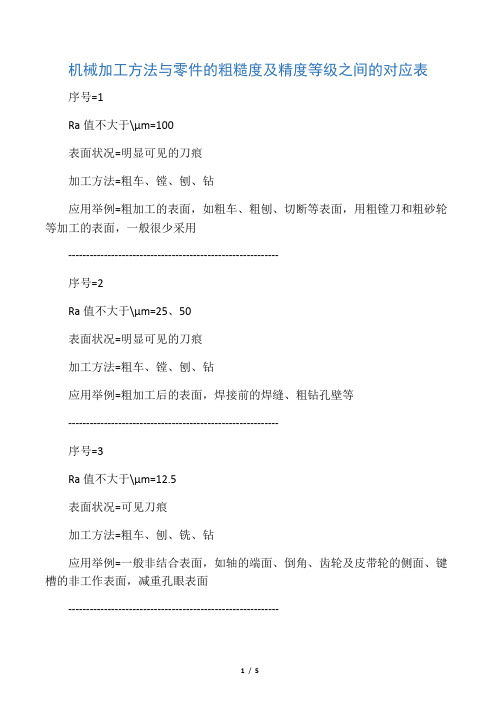
机械加工方法与零件的粗糙度及精度等级之间的对应表序号=1Ra值不大于\μm=100表面状况=明显可见的刀痕加工方法=粗车、镗、刨、钻应用举例=粗加工的表面,如粗车、粗刨、切断等表面,用粗镗刀和粗砂轮等加工的表面,一般很少采用-----------------------------------------------------------序号=2Ra值不大于\μm=25、50表面状况=明显可见的刀痕加工方法=粗车、镗、刨、钻应用举例=粗加工后的表面,焊接前的焊缝、粗钻孔壁等-----------------------------------------------------------序号=3Ra值不大于\μm=12.5表面状况=可见刀痕加工方法=粗车、刨、铣、钻应用举例=一般非结合表面,如轴的端面、倒角、齿轮及皮带轮的侧面、键槽的非工作表面,减重孔眼表面-----------------------------------------------------------Ra值不大于\μm=6.3表面状况=可见加工痕迹加工方法=车、镗、刨、钻、铣、锉、磨、粗铰、铣齿应用举例=不重要零件的配合表面,如支柱、支架、外壳、衬套、轴、盖等的端面。
紧固件的自由表面,紧固件通孔的表面,内、外花键的非定心表面,不作为计量基准的齿轮顶圈圆表面等-----------------------------------------------------------序号=5Ra值不大于\μm=3.2表面状况=微见加工痕迹加工方法=车、镗、刨、铣、刮1~2点/cm^2、拉、磨、锉、滚压、铣齿应用举例=和其他零件连接不形成配合的表面,如箱体、外壳、端盖等零件的端面。
要求有定心及配合特性的固定支承面如定心的轴间,键和键槽的工作表面。
不重要的紧固螺纹的表面。
需要滚花或氧化处理的表面-----------------------------------------------------------序号=6Ra值不大于\μm=1.6表面状况=看不清加工痕迹加工方法=车、镗、刨、铣、铰、拉、磨、滚压、刮1~2点/cm^2铣齿应用举例=安装直径超过80mm的G级轴承的外壳孔,普通精度齿轮的齿面,定位销孔,V型带轮的表面,外径定心的内花键外径,轴承盖的定中心凸肩表面-----------------------------------------------------------Ra值不大于\μm=0.8表面状况=可辨加工痕迹的方向加工方法=车、镗、拉、磨、立铣、刮3~10点/cm^2、滚压应用举例=要求保证定心及配合特性的表面,如锥销与圆柱销的表面,与G 级精度滚动轴承相配合的轴径和外壳孔,中速转动的轴径,直径超过80mm的E、D级滚动轴承配合的轴径及外壳孔,内、外花键的定心内径,外花键键侧及定心外径,过盈配合IT7级的孔(H7),间隙配合IT8~IT9级的孔(H8,H9),磨削的齿轮表面等-----------------------------------------------------------序号=8Ra值不大于\μm=0.4表面状况=微辨加工痕迹的方向加工方法=铰、磨、镗、拉、刮3~10点/cm^2、滚压应用举例=要求长期保持配合性质稳定的配合表面,IT7级的轴、孔配合表面,精度较高的齿轮表面,受变应力作用的重要零件,与直径小于80mm的E、D级轴承配合的轴径表面、与橡胶密封件接触的轴的表面,尺寸大于120mm 的IT13~IT16级孔和轴用量规的测量表面-----------------------------------------------------------序号=9Ra值不大于\μm=0.2表面状况=不可辨加工痕迹的方向加工方法=布轮磨、磨、研磨、超级加工应用举例=工作时受变应力作用的重要零件的表面。
不同加工方法获得的表面粗糙度
各种加工方法能达到的表面粗糙度由于机械加工表面质量对机器零件的使用性能如耐磨性、接触刚度、疲劳强度、配合性质、抗腐蚀性能以及精度的稳定性能有很大的影响,因此对机器零件的重要表面应提出一定的表面质量要求。
加工表面质量包括两个反复面的内容:(1)已加工表面的几何形状特征,主要指已加工表面的粗糙度、波度和纹理方向。
(2)已加工表面层的物理品质,主要包括表面层的加工硬化程度及冷硬层深度,表面层残余应力的性质、大小及分布状况,加工表面层的金相组织变化。
已加工表面粗糙度1. 表面粗糙度的形成原因及降低措施(1)切削加工表面粗糙度形成原因1)几何因素,几何因素所产生的表面粗糙度主要决定于残留面积高度(见图3-1中的H)。
图3-1 车削时的残留面积高度2)物理因素,切削加工后表面的实际粗糙度最大值往往高于残留面积高度,这主要是因为在切削加工过程中还存在各种物理因素的影响。
这些物理因素主要是积屑瘤、鳞刺、金属材料的塑性变形,以及工艺系统的振动等。
(2)降低切削加工表面粗糙度的措施1)刀具方面,增大刀尖圆弧半径rε,减小主偏角kr及副偏角k′r;使用长度比进给量稍大一些的修光刃(k′r=0°);提高刀具刃磨质量,减小刀具前、后到面的粗糙值(抛光至Ra1.25μm以下);采用较大的前角y0加工塑性大的材料;限制副刀刃上的磨损量;选用细粒的硬质合金切削谈素工具钢,用金刚石或矿物陶瓷刀具加工有色金属,高速钢刀具采用TiN涂层等。
2)工件方面,切削低碳钢、低合金钢时,对工件进行调质处理;加工中碳钢及中碳合金钢时,若采用较高切削速度,工件应为珠光体组织,若采用较低切削速度,工件应为片状珠光体加细晶粒的铁素体组织;易切削钢中应含有硫、铅等元素;灰铸铁中石墨的颗粒尺寸应小。
3)切削条件反复面,以较高的切削速度切削塑性材料,减小进给量(见图3-2);采用高效切削液;提高机床运动精度,增强工艺系统刚度等。
图3-2 切削速度及进给量对表面粗糙度的影响工件:35钢,刀具:YT15,切削深度a p=0.5mm(3)磨削表面粗糙形成原因及降低措施磨削表面粗糙度形成原因既有几何因素(残留面积),也有塑性变形、软化、微熔等物理因素,以及工艺系统振动的印象,因此降低磨削表面粗糙度的主要措施是:1)砂轮特性方面,采用细粒度砂轮(砂轮粒度号一般不超过80号,常用的是46~60号);根据工件材料、磨料等选择适宜的砂轮轮硬度(通常选用中软砂轮);刚玉或氧化铝类砂轮适于磨削各种钢制零件,碳化硅类砂轮适于磨削硬质合金、铸铁、黄铜、铝等,人造金刚石砂轮适于加工光学玻璃、陶瓷,立方氮化硼砂轮可用于磨削高硬度、高强度钢;组织紧密的砂轮适用于精磨、成形磨削,中等组织的砂轮适用于一般磨削,疏松组织的砂轮适用于粗磨、平面磨、内圆磨、以及热敏感性较强的材料、软金属和薄壁工件的磨削;增大砂轮宽度,采用直径较大砂轮等。
光洁度与粗糙度与加工方法的关系
光洁度与粗糙度与加工方法的关系光洁度与粗糙度与使用设备、刀具及加工参数都有着直接的关系,下面将相关标准及对比介绍如下:
一、光洁度与粗糙度Ra、Rz数值对照换算表
二、表面粗糙度国际标准
三、中美表面粗糙度对照表
四、表面粗糙度代号和画法
GB/T131-93规定,表面粗糙度代号是由规定的符号和有关参数组成,表面粗糙度符号的画法和意义如下表所示:
常用表面粗糙度Ra的数值与加工方法
五、常用加工方法与粗糙度对照表
六、表面粗糙度的选择
表面粗糙度的选择,既要考虑零件表面的功能要求,又要考虑经济性,还要考虑现有的加工设备。
一般应遵从以下原则:
(1) 同一零件上工作表面比非工作表面的参数值要小;
(2) 摩擦表面要比非摩擦表面的参数小。
有相对运动的工作表面,运动速度越高,其参数值越小;
(3) 配合精度越高,参数值越小。
间隙配合比过盈配合的参数值小;
(4) 配合性质相同时,零件尺寸越小,参数值越小;
(5) 要求密封、耐腐蚀或具有装饰性的表面,参数值要小。
各种加工方法对应表面粗糙度值
用普通材料和一般生产过程所能得到的典型粗糙度数值
粗糙度等级Ra
表面状况 加工方法举例
应用举例
50(▽1)
明显可见的刀痕 25(▽2) 可见的刀痕 12.5(▽3) 粗面
微见的刀痕 粗加工 锯断、粗车、粗铣、粗刨、钻孔及用粗锉刀、粗砂轮加工
不接触表面或不重要的接触面。
如螺栓孔、机座底面等 6.3(▽4)
可见加工痕迹 3.2(▽5) 微见加工痕迹 1.6(▽6) 半光面
看不见加工痕迹 半精加工 精车、精铣、粗铰、粗拉、精刨、扩孔、粗镗、粗磨、精锉、粗刮。
不产生相对运动的接触面或相对运动速度不高的接触面。
如键和键槽的工作面机盖与机体的结合面
0.8(▽7)
可辩加工痕迹方向 0.4(▽8) 微辩加工痕迹方向 0.2(▽9) 光面
不可辩加工痕迹方向 精加工
金刚石车刀的精车、精镗、精磨、精刮、粗研、精铰、精拉削、挤压、粗珩
相对运动速度较高的接触面,要求很好密合的接触面。
如齿
轮的工作面轴承的重要表面。
0.1(▽10) 暗光泽面 0.05(▽11) 亮光泽面 0.025(▽12) 镜状光泽面 0.0125(▽13) 雾状光泽面 0.006(▽14)
最光面
镜面
光加工 抛光、细磨、精研、精珩、超精加工。
极重要的摩擦表面。
如发动机气缸内表面、精密量具的工作表面。
各种加工方式对应的粗糙度等级
Ra 值不大于 呵=100表面状况 =明显可见的刀痕加工方法 =粗车、镗、刨、钻应用举例 =粗加工的表面,如粗车、粗刨、切断等表面,用粗镗刀和粗砂轮 等加工的表面,一般很少采用2级Ra 值不大于呵=25、50表面状况 =明显可见的刀痕加工方法 =粗车、镗、刨、钻应用举例 =粗加工后的表面,焊接前的焊缝、粗钻孔壁等3级Ra 值不大于 呵=12.5表面状况 =可见刀痕加工方法 =粗车、刨、铣、钻应用举例 =一般非结合表面, 槽的非工作表面,减重孔眼表面4级Ra 值不大于 呵=6.3表面状况 =可见加工痕迹应用举例 =不重要零件的配合表面,如支柱、支架、外壳、衬套、轴、盖等 的端面。
紧固件的自由表面,紧固件通孔的表面,内、外花键的非定心表面, 不作为计1级如轴的端面、倒角、齿轮及皮带轮的侧面、键加工方法 =车、镗、刨、钻、铣、锉、磨、粗铰、铣齿量基准的齿轮顶圈圆表面等5级Ra值不大于呵=3.2表面状况=微见加工痕迹加工方法二车、镗1」、铣、舌I」1~ 2点/cm八2、拉、磨、锂、滚压、铣齿应用举例=和其他零件连接不形成配合的表面,如箱体、外壳、端盖等零件的端面。
要求有定心及配合特性的固定支承面如定心的轴间,键和键槽的工作表面。
不重要的紧固螺纹的表面。
需要滚花或氧化处理的表面6级Ra值不大于呵=1.6表面状况=看不清加工痕迹加工方法二车、镗、刨、铣、铰、拉、磨、滚压、舌I」1~ 2点/cm八2铣齿应用举例=安装直径超过80mm 的G 级轴承的外壳孔,普通精度齿轮的齿面,定位销孔,V 型带轮的表面,外径定心的内花键外径,轴承盖的定中心凸肩表面7级Ra值不大于呵=0.8表面状况=可辨加工痕迹的方向加工方法二车、镗、拉、磨、立铣、舌I」3~ 10点/cm八2、滚压应用举例=要求保证定心及配合特性的表面,如锥销与圆柱销的表面,与G 级精度滚动轴承相配合的轴径和外壳孔,中速转动的轴径,直径超过80mm 的E、D 级滚动轴承配合的轴径及外壳孔,内、外花键的定心内径,外花键键侧及定心外径,过盈配合IT7级的孔(H7),间隙配合IT8〜IT9级的孔(H8, H9),磨削的齿轮表面等8级Ra值不大于呵=0.4表面状况=微辨加工痕迹的方向加工方法二铰、磨、镗、拉、舌I」3〜10点/cm八2、滚压应用举例二要求长期保持配合性质稳定的配合表面,IT7级的轴、孔配合表面,精度较高的齿轮表面,受变应力作用的重要零件,与直径小于80mm 的E、D级轴承配合的轴径表面、与橡胶密封件接触的轴的表面,尺寸大于120mm 的IT13~ IT16级孔和轴用量规的测量表面9级Ra值不大于呵=0.2表面状况=不可辨加工痕迹的方向加工方法=布轮磨、磨、研磨、超级加工应用举例=工作时受变应力作用的重要零件的表面。
- 1、下载文档前请自行甄别文档内容的完整性,平台不提供额外的编辑、内容补充、找答案等附加服务。
- 2、"仅部分预览"的文档,不可在线预览部分如存在完整性等问题,可反馈申请退款(可完整预览的文档不适用该条件!)。
- 3、如文档侵犯您的权益,请联系客服反馈,我们会尽快为您处理(人工客服工作时间:9:00-18:30)。
粗糙度与加工方法表面粗糙度选用与加工方法表面粗糙度选用序号=1Ra值不大于\μm=100表面状况=明显可见的刀痕加工方法=粗车、镗、刨、钻应用举例=粗加工的表面,如粗车、粗刨、切断等表面,用粗镗刀和粗砂轮等加工的表面,一般很少采用序号=2Ra值不大于\μm=25、50表面状况=明显可见的刀痕加工方法=粗车、镗、刨、钻应用举例=粗加工后的表面,焊接前的焊缝、粗钻孔壁等序号=3Ra值不大于\μm=12.5表面状况=可见刀痕加工方法=粗车、刨、铣、钻应用举例=一般非结合表面,如轴的端面、倒角、齿轮及皮带轮的侧面、键槽的非工作表面,减重孔眼表面序号=4Ra值不大于\μm=6.3表面状况=可见加工痕迹加工方法=车、镗、刨、钻、铣、锉、磨、粗铰、铣齿应用举例=不重要零件的配合表面,如支柱、支架、外壳、衬套、轴、盖等的端面。
紧固件的自由表面,紧固件通孔的表面,内、外花键的非定心表面,不作为计量基准的齿轮顶圈圆表面等序号=5Ra值不大于\μm=3.2表面状况=微见加工痕迹加工方法=车、镗、刨、铣、刮1~2点/cm^2、拉、磨、锉、滚压、铣齿应用举例=和其他零件连接不形成配合的表面,如箱体、外壳、端盖等零件的端面。
要求有定心及配合特性的固定支承面如定心的轴间,键和键槽的工作表面。
不重要的紧固螺纹的表面。
需要滚花或氧化处理的表面序号=6Ra值不大于\μm=1.6表面状况=看不清加工痕迹加工方法=车、镗、刨、铣、铰、拉、磨、滚压、刮1~2点/cm^2铣齿应用举例=安装直径超过80mm的G级轴承的外壳孔,普通精度齿轮的齿面,定位销孔,V型带轮的表面,外径定心的内花键外径,轴承盖的定中心凸肩表面序号=7Ra值不大于\μm=0.8表面状况=可辨加工痕迹的方向加工方法=车、镗、拉、磨、立铣、刮3~10点/cm^2、滚压应用举例=要求保证定心及配合特性的表面,如锥销与圆柱销的表面,与G级精度滚动轴承相配合的轴径和外壳孔,中速转动的轴径,直径超过80mm的E、D 级滚动轴承配合的轴径及外壳孔,内、外花键的定心内径,外花键键侧及定心外径,过盈配合IT7级的孔(H7),间隙配合IT8~IT9级的孔(H8,H9),磨削的齿轮表面等序号=8Ra值不大于\μm=0.4表面状况=微辨加工痕迹的方向加工方法=铰、磨、镗、拉、刮3~10点/cm^2、滚压应用举例=要求长期保持配合性质稳定的配合表面,IT7级的轴、孔配合表面,精度较高的齿轮表面,受变应力作用的重要零件,与直径小于80mm的E、D级轴承配合的轴径表面、与橡胶密封件接触的轴的表面,尺寸大于120mm的IT13~IT16级孔和序号=9Ra值不大于\μm=0.2表面状况=不可辨加工痕迹的方向加工方法=布轮磨、磨、研磨、超级加工应用举例=工作时受变应力作用的重要零件的表面。
保证零件的疲劳强度、防腐性和耐久性,并在工作时不破坏配合性质的表面,如轴径表面、要求气密的表面和支承表面,圆锥定心表面等。
IT5、IT6级配合表面、高精度齿轮的表面,与G 级滚动轴承配合的轴径表面,尺寸大于315mm的IT7~IT9级级孔和轴用量规级尺寸大于120~315mm的IT10~IT12级孔和轴用量规的测量表面等序号=10Ra值不大于\μm=0.1表面状况=暗光泽面加工方法=超级加工应用举例=工作时承受较大变应力作用的重要零件的表面。
保证精确定心的锥体表面。
液压传动用的孔表面。
汽缸套的内表面,活塞销的外表面,仪器导轨面,阀的工作面。
尺寸小于120mm的IT10~IT12级孔和轴用量规测量面等.序号=11Ra值不大于\μm=0.05表面状况=亮光泽面加工方法=超级加工应用举例=保证高度气密性的接合表面,如活塞、柱塞和汽缸内表面,摩擦离合器的摩擦表面。
对同轴度有精确要求的孔和轴。
滚动导轨中的钢球或滚子和高速摩擦的工作表面序号=12Ra值不大于\μm=0.025表面状况=镜面光泽面加工方法=超级加工应用举例=高压柱塞泵中柱塞和柱塞套的配合表面,中等精度仪器零件配合表面,尺寸大于120mm的IT6级孔用量规、小于120mm的IT7~IT9级轴用和孔用量规测量表面序号=13Ra值不大于\μm=0.012表面状况=雾状镜面加工方法=超级加工应用举例=仪器的测量表面和配合表面,尺寸超过100mm的块规工作面序号=14Ra值不大于\μm=0.0063表面状况=雾状表面加工方法=超级加工应用举例=块规的工作表面,高精度测量仪器的测量面,高精度仪器摩擦机构的支承表面八、材料的力学性能小结一、固体材料的性能1.比强度和比模量比强度就是单位密度下的强度,其特点是,在强度相同的情况下,材料密度愈小,比强度愈高。
比模量是单位密度下的模量,原理同比强度。
2.应力的概念,应力与压强的区别所谓应力是受外力作用时,材料内部产生的大小相等但方向相反的反作用力抵抗外力,定义单位面积上的这种反作用力为应力;而压强是单位面积上所受的压力大小。
不难发现,应力是受外力作用时产生的内力,而压强则是外力。
3.应变A 线应变在直角坐标中试件的长度在变形前后的改变量与原长之比,定义为线应变,用ε表示。
线应变以伸长为正,缩短为负。
B 切应变单元体的两条相互垂直的棱边,在变形后的直角改变量,定义为角应变或切应变,用γ表示。
一点在x-y方向、y-z方向z-x方向的切应变,分加别为γxy、γyz、γzx。
切应变以直角减少为正,反之为负。
应变不是仅对弹性变形而言,ε(%) ―试样标距部分伸长量,(mm);L0 ―试样标距部分长度(mm)。
ε=ㄓL/L0 。
应变和应力一样也是归一化的结果,即单位长度的变形量。
不管是在弹性还是在塑性阶段都是一个衡量指标。
4.弹性模量(刚度)弹性模量是指材料在外力作用下描述抵抗弹性变形能力的物理量,在拉伸试验中用E表示。
E表示了在比例极限内材料应力应变曲线的斜率。
E=ζ/ε。
5.ζp、ζe、ζs、ζbζp--比例极限,在ζp以下,材料的应力与应变呈线性关系,即ζp是材料呈比例关系的最大应力;ζe--弹性极限,ζe是材料呈弹性关系的最大应力;ζs--屈服极限,在屈服阶段应力不变而应变不断增加,这种现象叫屈服。
对应的应力ζs叫屈服极限。
低碳钢的屈服段有上下屈服点,做试验到达屈服点时,应变并不是一个恒定值,有一个应力惯性效应(上屈服点)和应变继续增加的小应力(下屈服点)阶段,形成了应力在上下屈服点间来回振荡的局面,你看到的图形是试验时应力应变仪纪录的结果。
ζb--强度极限,材料应力达到ζb后,即使外力不增加,变形继续增加,材料发生颈缩,很快断裂。
所以ζb是材料强度计算的重要指标。
在应力、应变图上,在应变坐标中,0-ζe为弹性阶段,ζe-ζs为屈服阶段,ζs-ζb为强化阶段,ζb-k为局部变形阶段。
6.屈强比概念屈强比越小,构件万一超载时,产生塑性变形的时间越长,则离断裂的时间长,易发现和马上采取措施(如停机、换构件等),即时间裕度大,可靠性高。
屈强比大,则屈服强度高,材料强度利用率高。
7.塑性指标产生塑性变形而不断裂的性能称为塑性。
塑性的大小用伸长率δ和断面收缩率ψ表示。
伸长率δ的值随试样原始长度增加而减小。
所以,同一材料的短试样(Lo=5do)比长试样(Lo=10do)伸长率大20%左右。
用短试样和长试样测得的伸长率分别用δ5和δ10表示。
8.条件屈服强度大多数金属材料在拉伸时没有明显的屈服现象,按GB228-87要求,取规定非比例伸长与原标距长度比为0.2%时的应力,记为ζp0.2,作为屈服强度指标,称为条件屈服强度,可用ζ0.2表示。
9.硬度布氏硬度、洛氏硬度、维氏硬度的使用如下:布氏硬度因压痕面积较大,能反映出较大范围内被测金属的平均硬度,故试验结果较精确。
但因压痕较大,所以不宜测试成品或薄片金属的硬度。
洛氏硬度试验法的优点是操作迅速简便,由于压痕较小,故可在工件表面或较薄的金属上试验。
同时,采用不同标尺,可测出从极软到极硬材料的硬度。
其缺点是因压痕较小,对组织较粗大且不均匀的材料,测得的硬度不精确。
洛氏硬度虽可测极软到极硬的材料,但不同标尺的硬度值之间没有简单的换算关系,使用上很不方便。
维氏硬度与洛氏硬度试验相同,但其试验时所加载荷小,压入深度浅,故适用于测试零件表面淬硬层及化学热处理的表面层(如渗氮层、渗碳层等),同时维氏硬度是一个连续一致的标尺,试验时载荷可任意选择而不影响其硬度值的大小。
但其测定较麻烦,工作效率较低。
10.冲击韧度①ak没有确切的力学意义,它表明在高应变速率时,材料的脆性发展趋势。
②一次冲击试验能灵敏地揭示材料的冶金及加工缺陷和产生的脆性。
③不同温度下的系列冲击试验,可揭示材料的低温脆化倾向(冷脆转变)。
④材料碳含量愈高脆性愈大。
⑤冲击试验得到广泛应用,但Ak、a k不能直接用于计算。
11.断裂韧度在材料所承受的应力低于许用应力的情况下,突然发生的无明显塑性变形的脆性断裂,称为低应力脆断,即断裂韧度。
低应力脆断总是由材料中宏观裂纹的失稳扩展引起的,其大小可用应力强度因子KⅠ来描述。
12.疲劳破坏许多机械零件如弹簧、轴、齿轮等,在工作时承受交变载荷,既使交变应力低于屈服强度,但经一定循环次数后便发生断裂。
疲劳破坏的主要特点:①应力水平低,往往远低于ζs ;②断裂前无明显形变。
对称弯曲循环疲劳极限用ζ-1表示。
①疲劳曲线(ζ~N)有明显的水平线段,则水平线段对应的应力为ζ-1 ;②疲劳曲线没有明显的水平线段,则在规定的疲劳寿命内不发生疲劳破坏所对应的最大应力。
工件表面留存残余压应力时,工件产生表面拉应力时要先抵消表面压应力,所以表面拉应力幅度减小,表面疲劳强度由表面交变载荷幅和频率决定,故工件表面留存残余压应力时,材料表面疲劳极限提高。
13.高温蠕变金属在高温长时间应力作用下,即使所加应力小于该温度下的屈服强度,也会逐渐产生明显的塑性变形直至断裂。