各种加工方法能达到的表面粗糙度分析
各种机械加工多能达到的粗糙度

抛光 单组式 0.8、0.4、0.2、0.1、0.05、0.025、0.012 7 GB6060.4-88
铸造钢铁砂型 单组式 3.2、6.3、12.5、25、50、100、800、1000 8 GB6060.1-85
▽ 8 0.4 0.63 25
0.50 20
0.40 16
表面粗糙度是指加工表面具有的较小间距和微小峰谷不平度。其两波峰或两波谷之间的距离(波距)很小(在1mm以下),用肉眼是难以区别的,因此它属于微观几何形状误差。表面粗糙度越小,则表面越光滑。表面粗糙度的大小,对机械零件的使用性能有很大的影响,主要表现在以下几个方面:
① 表面粗糙度影响零件的耐磨性。表面越粗糙,配合表面间的有效接触面积越小,压强越大,磨损就越快。
端铣 0.8、1.6、3.2、6.3
镗内孔 双组式 0.8、1.6、3.2、6.3 8 GB6060.2-85
磨内孔 0.1、0.2、0.4、0.8
手研 单组式 0.1、0.05、0.025、0.012 4
平磨 单组式 0.1、0.2、0.4、0.8 4
电火花线切割 单组式 0.63、1.25、2.5、5.0、10 5 GB6060.3-86
0.1—花△10
0.2—花△9
0.4—花△8
0.8—花△7
1.6—花△6
3.2—花△5
6.3—花△4
12.5—花△3
25—花△2
50—花△1
100—花△0(为最粗糙)
中国与美国的表面粗糙度(光洁度)对照表
表面粗糙度有Ra,Rz,Ry 之分,据GB 3505摘录:
各种加工方式对应的粗糙度等级
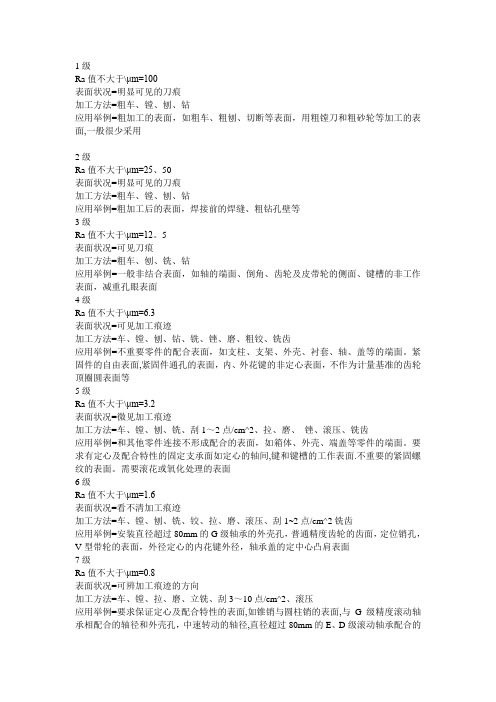
1级Ra值不大于\μm=100表面状况=明显可见的刀痕加工方法=粗车、镗、刨、钻应用举例=粗加工的表面,如粗车、粗刨、切断等表面,用粗镗刀和粗砂轮等加工的表面,一般很少采用2级Ra值不大于\μm=25、50表面状况=明显可见的刀痕加工方法=粗车、镗、刨、钻应用举例=粗加工后的表面,焊接前的焊缝、粗钻孔壁等3级Ra值不大于\μm=12。
5表面状况=可见刀痕加工方法=粗车、刨、铣、钻应用举例=一般非结合表面,如轴的端面、倒角、齿轮及皮带轮的侧面、键槽的非工作表面,减重孔眼表面4级Ra值不大于\μm=6.3表面状况=可见加工痕迹加工方法=车、镗、刨、钻、铣、锉、磨、粗铰、铣齿应用举例=不重要零件的配合表面,如支柱、支架、外壳、衬套、轴、盖等的端面。
紧固件的自由表面,紧固件通孔的表面,内、外花键的非定心表面,不作为计量基准的齿轮顶圈圆表面等5级Ra值不大于\μm=3.2表面状况=微见加工痕迹加工方法=车、镗、刨、铣、刮1~2点/cm^2、拉、磨、锉、滚压、铣齿应用举例=和其他零件连接不形成配合的表面,如箱体、外壳、端盖等零件的端面。
要求有定心及配合特性的固定支承面如定心的轴间,键和键槽的工作表面.不重要的紧固螺纹的表面。
需要滚花或氧化处理的表面6级Ra值不大于\μm=1.6表面状况=看不清加工痕迹加工方法=车、镗、刨、铣、铰、拉、磨、滚压、刮1~2点/cm^2铣齿应用举例=安装直径超过80mm的G级轴承的外壳孔,普通精度齿轮的齿面,定位销孔,V型带轮的表面,外径定心的内花键外径,轴承盖的定中心凸肩表面7级Ra值不大于\μm=0.8表面状况=可辨加工痕迹的方向加工方法=车、镗、拉、磨、立铣、刮3~10点/cm^2、滚压应用举例=要求保证定心及配合特性的表面,如锥销与圆柱销的表面,与G级精度滚动轴承相配合的轴径和外壳孔,中速转动的轴径,直径超过80mm的E、D级滚动轴承配合的轴径及外壳孔,内、外花键的定心内径,外花键键侧及定心外径,过盈配合IT7级的孔(H7),间隙配合IT8~IT9级的孔(H8,H9),磨削的齿轮表面等8级Ra值不大于\μm=0.4表面状况=微辨加工痕迹的方向加工方法=铰、磨、镗、拉、刮3~10点/cm^2、滚压应用举例=要求长期保持配合性质稳定的配合表面,IT7级的轴、孔配合表面,精度较高的齿轮表面,受变应力作用的重要零件,与直径小于80mm的E、D级轴承配合的轴径表面、与橡胶密封件接触的轴的表面,尺寸大于120mm的IT13~IT16级孔和轴用量规的测量表面9级Ra值不大于\μm=0.2表面状况=不可辨加工痕迹的方向加工方法=布轮磨、磨、研磨、超级加工应用举例=工作时受变应力作用的重要零件的表面.保证零件的疲劳强度、防腐性和耐久性,并在工作时不破坏配合性质的表面,如轴径表面、要求气密的表面和支承表面,圆锥定心表面等.IT5、IT6级配合表面、高精度齿轮的表面,与G级滚动轴承配合的轴径表面,尺寸大于315mm的IT7~IT9级级孔和轴用量规级尺寸大于120~315mm的IT10~IT12级孔和轴用量规的测量表面等10级Ra值不大于\μm=0。
各种加工方法的经济精度和表面粗糙度

各种加工方法能够达到的尺寸的经济精度表1 孔加工的经济精度表2 圆锥形孔加工的经济精度表3 圆柱形深孔加工的经济精度表4 花键孔加工的经济精度表5 外圆柱表面加工的经济精度表6 端面加工的经济精度(mm)表7 用成形铣刀加工的经济精度(mm)注:指加工表面至基准的尺寸精度。
表8 同时加工平行表面的经刘精度(mm)注:指两平行表面距离的尺寸精度。
表9 平面加工的经济精度注:1 表内资料适用于尺寸<1m,结构刚性好的零件加工,用光洁的加工表面作为定位和测量基准。
2 端铣刀铣削的加工精度在相同的条件下大体上比圆柱铣刀铣削高一级。
3 细铣仅用于端铣刀铣削。
表10 公制螺纹加工的经济精度表11 花键加工的经济精度表12 齿形加工的经济精度各种加工方法能够达到的形状的经济精度表13 平面度和直线度的经济精度表14 圆柱形表面形状精度的经济精度注:形状精度等级的公差值见附表2、3。
表15 曲面加工的经济精度表16 在各种机床上加工时形状的平均经济精度各种加工方法所能够达到的相互位置的经济精度表17 平行度的经济精度表18 端面跳动和垂直度的经济精度表19 同轴度的经济精度表20 轴心线相互平行的孔的位置经济精度注:对于钻、卧镗及组合机床的镗孔偏差同样适用于铰孔。
表21 轴心线相互垂直的孔的位置经济精度注:在镗空间的垂直孔时,中心距误差可按上式相应的找正方法选用。
各种加工方法能够达到的零件表面粗糙度表22 各种加工方法能够达到的零件表面粗糙度各类型面的加工方案及经济精度表23 外圆表面加工方案表24 孔加工方案表25 平面加工方案——机械篇标准公差及形位公差附表1 标准公差值注:基本尺寸小于1mm时,无IT14至IT18。
13 22-4-25 10:32附表2 平面度、直线度公差值附表3 圆度、圆柱度公差值附表4 平行度、垂直度、倾斜度公差值附表5 同轴度、对称度、圆跳动、全跳动公差值参考文献1 《金属机械加工工艺人员手册》修订本上海科学技术出版社1981年2 《机械制造工艺学》顾崇衔等编著陕西科学技术出版社1982年3 《航空机械设计手册》第三机械工业部612所编1979年4 《机械制造工艺学课程设计简明手册》华中工学院机械制造工艺教研室编1981年5 《机械工程手册》第46篇机械工业出版社1981年6 《圆柱齿轮加工》上海科学技术出版社1979年切削用量切削用量的选择原则正确地选择切削用量,对提高切削效率,保证必要的刀具耐用度和经济性,保证加工质量,具有重要的作用。
各种机械加工多能达到的粗糙度

பைடு நூலகம்
各种机械加工多能达到的粗糙度
2010-06-08 110611 分类: 机械加工 字号 订阅
1、一般车床的加工精度可达IT8~IT7,表面粗糙度为Ra25~Ra1.6.
2、钻床用于钻孔加工精度可达IT13~IT11,表面粗糙度Ra80~Ra20;用于扩孔精度达IT10,表面粗糙度Ra10~Ra5.;用于铰孔精度可达IT7,表面粗糙度Ra5~ra1.25。
表面粗糙度参数及其数值(Surface Roughness Parameters and their Values)常用的3个分别是:
轮廓算数平均偏差(Ra)--arithmetical mean deviation of the profile;
微观不平度十点高度(Rz)--the point height of irregularities;
抛喷丸 0.2、0.4、0.8、1.6、3.2、6.3、12.5、25、50、100 10 GB6060.5-88
喷砂 0.8、1.6、3.2、6.3、12.5、25 6
抛喷丸+喷砂 综合以上二项 16 GB6060.5-88
端铣 0.8、1.6、3.2、6.3
镗内孔 双组式 0.8、1.6、3.2、6.3 8 GB6060.2-85
磨内孔 0.1、0.2、0.4、0.8
手研 单组式 0.1、0.05、0.025、0.012 4
平磨 单组式 0.1、0.2、0.4、0.8 4
电火花线切割 单组式 0.63、1.25、2.5、5.0、10 5 GB6060.3-86
▽ 8 0.4 0.63 25
0.50 20
0.40 16
表面粗糙度基础知识

表面粗糙度基础知识表面粗糙度是机械加工中评定零件表面质量的一个重要指标,它在一定程度上反映了零件的加工质量。
它对零件的配合性质、耐磨性、抗腐蚀性、密封性、接触刚度及抗疲劳能力都有影响。
Roughness, an important index of surface quality of component, reflects the machining quality of component and affects the fitting property, wearability, anti-corrosion, tightness, rigidity and anti-fatigue capability of component.零件的表面过于粗糙,会造成接触刚度降低、耐磨性差、疲劳强度和耐蚀性下降,配合性质改变:相对运动件的表面粗糙度过细,不易储存润滑油,加重磨损,同时过细的表面还将大大提高制造成本。
为了反映零件使用性能要求,对零件表面可以采用一个或几个表面粗糙度评定参数。
如下图所示:图1:21-13 轴1 表面粗糙度的定义和评定参数Definition and parameter of roughness表面粗糙度是指加工表面上具有的较小的间距和峰谷所组成的微观几何特性。
一般由所采用的加工方法和其他因素形成。
Caused by machining and other factors.表面粗糙度的评定参数:轮廓算数平均偏差Ra,微观不平度十点高度Rz,轮廓最大高度Ry。
表1:术语及定义Table 1: terms and definitionTerm Definition DiagramRemarks轮廓算数平均偏差Ra 在取样长度内轮廓绝对值的算术平均值Ra=微观不平度十点高度Rz 在取样长度内5个最大的轮廓峰值与5个最小的轮廓谷深的平均值之和Rz=+轮廓最大高度Ry 在取样长度轮廓峰顶线和轮廓谷底线之间的距离2 表面粗糙度的基本符号及含义2.1基本符号basic sign表示表面可用任何方法获得,当不加注粗糙度数值或有关说明(如表面处理、局部热处理)时,仅适用简化代号标注。
各种加工工艺能够达到的零件表面粗糙度

本文中详细整理了不同的加工工艺所能达到的表面粗糙度,使用者可根据表格自行查询:
加 工 方 法
表面粗糙度
Ra/μm
Rz/μm
自动气割、带锯或圆盘锯割断
>10~80
>40~320
切 断
车
>10~80
>40~320
铣
>10~40
>40~160
砂 轮
>1.25~5
>6.3~20
黄铜、青铜
>0.32~1.25
>1.6~6.3
细 铰
钢
>0.16~1.25
>0.8~6.3
轻合金
>0.32~1.25
>1.6~6.3
黄铜、青铜
>0.08~0.32
>0.4~1.6
端铣刀
铣削
粗
>2.5~20
>10~80
精
>0.32~5
>1.6~20
细
>0.16~1.25
>0.8~6.3
高速铣削
粗
>0.63~2.5
>0.4~1.6
砂布抛光
>0.08~2.5
>0.4~10
电抛光
>0.01~2.5
>0.05~10
螺纹加工
切 削
板牙、丝锥、
自开式板牙头
>0.63~5
>20~3.2
车刀或梳
刀车、铣
>0.63~10
>3. 2~40
磨
>0.16~1.25
>0.8~6.3
研 磨
>0.04~1.25
>0.2~6.3
滚 轧
搓丝模
>0.8~6.3
圆柱铣
刀铣削
粗
>2.5~20
粗加工、半精加工、精加工 国标 表面粗糙度
粗加工、半精加工、精加工国标表面粗糙度【主题】粗加工、半精加工、精加工国标表面粗糙度【导言】在工程制造领域,粗加工、半精加工、精加工是我们经常会遇到的工艺术语,而国标表面粗糙度则是评定加工质量的重要标准。
本文将对这些主题进行全面解读,帮助您更深入地理解工程制造中的精度和粗糙度要求。
一、粗加工、半精加工、精加工的定义和区别1. 粗加工:指在工件上去除余量,但不要求高精度和光洁度的加工工艺。
通常是为了消除初始形状和大小偏差,使工件成为半成品状态,为后续的半精加工或精加工提供基础。
2. 半精加工:介于粗加工和精加工之间的加工过程,既要求加工精度,又要求较高的表面质量。
通常需要在粗加工的基础上进行二次加工,以获得更高的尺寸精度和表面质量。
3. 精加工:指在半成品上进行的高精度、高光洁度的加工工艺。
其目的是满足产品的特定精度要求,使产品达到设计要求的形状和表面状态。
二、国标表面粗糙度参数及其意义1. Ra值:表面粗糙度平均值,通常用于评定表面的整体光洁度,Ra值越小,表面越光滑。
2. Rz值:通常称为最大高度,是指由表面轮廓上最高点到最低点之间的距离,反映了表面的不规则程度。
3. Rt值:最大毛坯高度,是指在测定长度内,最大的毛坯表面高度差,用于评定最大局部高度差。
这些国标表面粗糙度参数是工件表面质量的重要指标,对机械零件的密封性、耐磨性、传动精度等都有着重要的影响。
三、文章总结和回顾本文首先对粗加工、半精加工、精加工进行了定义和区别,帮助读者了解工件加工的不同阶段和要求;接着介绍了国标表面粗糙度参数及其意义,让读者对表面质量的评定有了更清晰的认识。
笔者在个人观点中指出,粗加工、半精加工、精加工在工程制造中具有重要意义,对工件的质量、精度和表面质量都有着不可替代的作用,而国标表面粗糙度则是这些工艺的重要评定标准。
希望读者在实际工程应用中能够充分重视这些关键要素,从而保证制造出更加精密和优质的产品。
通过本文的阅读,相信您对粗加工、半精加工、精加工和国标表面粗糙度已经有了更深入的理解。
各种加工方法表面光洁度
1、一般车床的加工精度可达IT8~IT7,表面粗糙度为Ra25~Ra1.6.2、钻床用于钻孔加工精度可达IT13~IT11,表面粗糙度Ra80~Ra20;用于扩孔精度达IT10,表面粗糙度Ra10~Ra5.;用于铰孔精度可达IT7,表面粗糙度Ra5~ra1.25。
3、铣床加工精度一般为IT9~IT8,表面粗糙度为Ra6.3~Ra1.6.4、刨床加工精度为IT9~IT8,表面粗糙度为Ra25~Ra1.6.5、磨床加工精度一般为IT6~IT5,表面粗糙度为Ra0.8~Ra0.1.0.012—花△13(为最精确)0.025—花△120.05—花△110.1—花△100.2—花△90.4—花△80.8—花△71.6—花△63.2—花△56.3—花△412.5—花△325—花△250—花△1100—花△0(为最粗糙)中国与美国的表面粗糙度(光洁度)对照表表面粗糙度有Ra,Rz,Ry 之分,据GB 3505摘录:表面粗糙度参数及其数值(Surface Roughness Parameters and their Values)常用的3个分别是:轮廓算数平均偏差(Ra)--arithmetical mean deviation of the profile;微观不平度十点高度(Rz)--the point height of irregularities;轮廓最大高度(Ry)--maximum height of the profile。
Ra--在取样长度L内轮廓偏距绝对值的算术平均值。
Rz--在取样长度内5个最大的轮廓峰高的平均值与5个最大的轮廓谷深的平均值之和。
Ry--在取样长度L内轮廓峰顶线和轮廓谷底线之间的距离。
如果图面没标注粗糙度选用Ra /Rz /Ry 的情况下默认为Ra。
中美表面粗糙度(光洁度)对照表中国旧标准 ( 光洁度 ) 中国新标准 (粗糙度)Ra 美国标准 (微米)Ra 美国标准(微英寸)Ra▽ 4 6.3 8.00 3206.30 250▽ 5 3.2 5.00 2004.00 1603.20 125▽ 6 1.6 2.50 1002.00 801.60 63▽ 7 0.8 1.25 501.00 400.80 32▽ 8 0.4 0.63 250.50 200.40 16表面粗糙度是指加工表面具有的较小间距和微小峰谷不平度。
各种加工方法能达到的表面粗糙度
75
抛光(精)
0.8~0.1
76
抛光(精密)
0.1~0.025
ID
加工方法
表面粗糙度Ra(μm)
77
抛光(砂带抛光)
0.2~0.1
78
抛光(砂布抛光)
1.6~0.1
79
抛光(电抛光)
1.6~0.012
80
螺纹加工/切削/板牙、丝锥
3.2~0.8
81
螺纹加工/切削/车刀或梳刀车、铣
6.3~0.8
ID
加工方法
表面粗糙度Ra(μm)
1
自动气割、带锯或圆盘锯割断
50~12.5
2
切断(车)
50~12.5
3
切断(铣)
25~12.5
4
切断(砂轮)
3.2~1.6
5
车削外圆(粗车)
12.5~3.2
6
车削外圆(半精车金属)
6.3~3.2
7
车削外圆(半精车非金属)
3.2~1.6
8
车削外圆(精车金属)
3.2~0.8
推削(精)
0.8~0.2
59
推削(精密)
0.4~0.025
60
外圆磨内圆磨(半精、一次加工)
6.3~0.8
61
外圆磨内圆磨(精)
0.8~0.2
62
外圆磨内圆磨(精密)
0.2~0.1
63
外圆磨内圆磨(精密、超精密磨削)
0.050~0.025
64
外圆磨内圆磨(镜面磨削外圆磨)
< 0.050
65
平面磨(精)
82
螺纹加工/切削/磨
0.8~0.2
各种加工方法能达到的表面粗糙度
各种加工方法能达到的表面粗糙度由于机械加工表面质量对机器零件的使用性能如耐磨性、接触刚度、疲劳强度、配合性质、抗腐蚀性能以及精度的稳定性能有很大的影响,因此对机器零件的重要表面应提出一定的表面质量要求。
加工表面质量包括两个反复面的内容:(1)已加工表面的几何形状特征,主要指已加工表面的粗糙度、波度和纹理方向。
(2)已加工表面层的物理品质,主要包括表面层的加工硬化程度及冷硬层深度,表面层残余应力的性质、大小及分布状况,加工表面层的金相组织变化。
已加工表面粗糙度1. 表面粗糙度的形成原因及降低措施(1)切削加工表面粗糙度形成原因1)几何因素,几何因素所产生的表面粗糙度主要决定于残留面积高度(见图3-1中的H)。
图3-1 车削时的残留面积高度2)物理因素,切削加工后表面的实际粗糙度最大值往往高于残留面积高度,这主要是因为在切削加工过程中还存在各种物理因素的影响。
这些物理因素主要是积屑瘤、鳞刺、金属材料的塑性变形,以及工艺系统的振动等。
(2)降低切削加工表面粗糙度的措施1)刀具方面,增大刀尖圆弧半径rε,减小主偏角kr及副偏角k′r;使用长度比进给量稍大一些的修光刃(k′r=0°);提高刀具刃磨质量,减小刀具前、后到面的粗糙值(抛光至Ra1.25μm以下);采用较大的前角y0加工塑性大的材料;限制副刀刃上的磨损量;选用细粒的硬质合金切削谈素工具钢,用金刚石或矿物陶瓷刀具加工有色金属,高速钢刀具采用TiN涂层等。
2)工件方面,切削低碳钢、低合金钢时,对工件进行调质处理;加工中碳钢及中碳合金钢时,若采用较高切削速度,工件应为珠光体组织,若采用较低切削速度,工件应为片状珠光体加细晶粒的铁素体组织;易切削钢中应含有硫、铅等元素;灰铸铁中石墨的颗粒尺寸应小。
3)切削条件反复面,以较高的切削速度切削塑性材料,减小进给量(见图3-2);采用高效切削液;提高机床运动精度,增强工艺系统刚度等。
图3-2 切削速度及进给量对表面粗糙度的影响工件:35钢,刀具:YT15,切削深度a p=0.5mm(3)磨削表面粗糙形成原因及降低措施磨削表面粗糙度形成原因既有几何因素(残留面积),也有塑性变形、软化、微熔等物理因素,以及工艺系统振动的印象,因此降低磨削表面粗糙度的主要措施是:1)砂轮特性方面,采用细粒度砂轮(砂轮粒度号一般不超过80号,常用的是46~60号);根据工件材料、磨料等选择适宜的砂轮轮硬度(通常选用中软砂轮);刚玉或氧化铝类砂轮适于磨削各种钢制零件,碳化硅类砂轮适于磨削硬质合金、铸铁、黄铜、铝等,人造金刚石砂轮适于加工光学玻璃、陶瓷,立方氮化硼砂轮可用于磨削高硬度、高强度钢;组织紧密的砂轮适用于精磨、成形磨削,中等组织的砂轮适用于一般磨削,疏松组织的砂轮适用于粗磨、平面磨、内圆磨、以及热敏感性较强的材料、软金属和薄壁工件的磨削;增大砂轮宽度,采用直径较大砂轮等。
- 1、下载文档前请自行甄别文档内容的完整性,平台不提供额外的编辑、内容补充、找答案等附加服务。
- 2、"仅部分预览"的文档,不可在线预览部分如存在完整性等问题,可反馈申请退款(可完整预览的文档不适用该条件!)。
- 3、如文档侵犯您的权益,请联系客服反馈,我们会尽快为您处理(人工客服工作时间:9:00-18:30)。
各种加工方法能达到的表面粗糙度
ID 加工方法表面粗糙度Ra(μm)
1
自动气割、带锯或圆盘锯割断
50~12.5
2
切断(车)
50~12.5
3
切断(铣)
25~12.5
4
切断(砂轮)
3.2~1.6
5
车削外圆(粗车)
12.5~3.2
6
车削外圆(半精车金属)
6.3~3.2
7
车削外圆(半精车非金属)
3.2~1.6
8
车削外圆(精车金属)
3.2~0.8
9
车削外圆(精车非金属)
1.6~0.4
10
车削外圆(精密车或金刚石车金属)
0.8~0.2
11
车削外圆(精密车或金刚石车非金属)0.4~0.1
12
车削端面(粗车)
12.5~6.3
13
车削端面(半精车金属)
6.3~3.2
14
车削端面(半精车非金属)
6.3~1.6
15
车削端面(精车金属)
6.3~1.6
16
车削端面(精车非金属
6.3~1.6
17
车削端面(精密车金属)0.8~0.4
18
车削端面(精密车非金属)0.8~0.2
19
切槽(一次行程)
12.5
20
切槽(二次行程)
6.3~3.2
21
高速车削
0.8~0.2
22
钻(≤φ15mm)6.3~3.2
23
钻(>φ15mm)25~6.3
24
扩孔、粗(有表皮)12.5~6.3
25
扩孔、精
6.3~1.6
26
锪倒角(孔的)
3.2~1.6
27
带导向的锪平面
6.3~3.2
28
镗孔(粗镗)
12.5~6.3
29
镗孔(半精镗金属)
6.3~3.2
30
镗孔(半精镗非金属)
6.3~1.6
31
镗孔(精密镗或金刚石镗金属)0.8~0.2
32
镗孔(精密镗或金刚石镗非金属)
0.4~0.2
33
高速镗
0.8~0.2
34
铰孔(半精铰一次铰)钢
6.3~3.2
35
铰孔(半精铰一次铰)黄铜
6.3~1.6
36
铰孔(半精铰二次铰)铸铁
3.2~0.8
37
铰孔(半精铰二次铰)钢、轻合金1.6~0.8
38
铰孔(半精铰二次铰)黄铜、青铜0.8~0.4
39
铰孔(精密铰)钢
0.8~0.2
40
铰孔(精密铰)轻合金
0.8~0.4
41
铰孔(精密铰)黄铜、青铜
0.2~0.1
42
圆柱铣刀铣削(粗)
12.5~3.2
43
圆柱铣刀铣削(精)
3.2~0.8
44
圆柱铣刀铣削(精密)0.8~0.4
45
端铣刀铣削(粗)12.5~3.2
46
端铣刀铣削(精)
3.2~0.4
47
端铣刀铣削(精密)0.8~0.2
48
高速铣削(粗)
1.6~0.8
49
高速铣削(精)0.4~0.2
50
刨削(粗)
12.5~6.3
51
刨削(精)
3.2~1.6
52
刨削(精密)
0.8~0.2
53
刨削(槽的表面)6.3~3.2
54
插削(粗)
25~12.5
55
插削(精)6.3~1.6
56
拉削(精)1.6~0.4
57
拉削(精密)0.2~0.1
58
推削(精)0.8~0.2
59
推削(精密)0.4~0.025
60
外圆磨内圆磨(半精、一次加工)
6.3~0.8
61
外圆磨内圆磨(精)
0.8~0.2
62
外圆磨内圆磨(精密)
0.2~0.1
63
外圆
磨内圆磨(精密、超精密磨削)0.050~0.025
64
外圆磨内圆磨(镜面磨削外圆磨)< 0.050
65
平面磨(精)
0.8~0.4
66
平面磨(精密)
0.2~0.05
67
珩磨(粗、一次加工)
0.8~0.2
68
珩磨(精、精密)
0.2~0.025
69
研磨(粗)
0.4~0.2
70
研磨(精)
0.2~0.025
71
研磨(精密)
< 0.050
72
超精加工(精)
0.8~0.1
73
超精加工(精密)
0.1~0.05
74
超精加工(镜面加工、两次加工)< 0.025
75
抛光(精)
0.8~0.1
76
抛光(精密)
0.1~0.025
77
抛光(砂带抛光)
0.2~0.1
78
抛光(砂布抛光)
1.6~0.1
79
抛光(电抛光)
1.6~0.012
80
螺纹加工/切削/板牙、丝锥、自开式板牙头3.2~0.8
81
螺纹加工/切削/车刀或梳刀车、铣6.3~0.8
82
螺纹加工/切削/磨
0.8~0.2
83
螺纹加工/切削/研磨
0.8~0.050
84
螺纹加工/滚轧/搓丝模
1.6~0.8
85
螺纹加工/滚轧/滚丝模
1.6~0.2
86
齿轮及花键加工/切削/粗滚3.2~1.6
87
齿轮及花键加工/切削/精滚1.6~0.8
88
齿轮及花键加工/切削/精插1.6~0.8
89
齿轮及花键加工/切削/精刨3.2~0.8
90
齿轮及花键加工/切削/拉3.2~1.6
91
齿轮及花键加工/切削/剃0.8~0.2
92
齿轮及花键加工/切削/磨0.8~0.1
93
齿轮及花键加工/切削/研0.4~0.2
94
齿轮及花键加工/滚轧/热轧0.8~0.4
95
齿轮及花键加工/滚轧/冷轧0.2~0.1
96
刮(粗)
3.2~0.8
97
刮(精)0.4~0.05
98
滚压加工0.4~0.05
99
钳工锉削12.5~0.8
100
砂轮清洗50~6.3。