ASTM E45夹杂物分析标准(中文版)
ASTM E 目录中英文
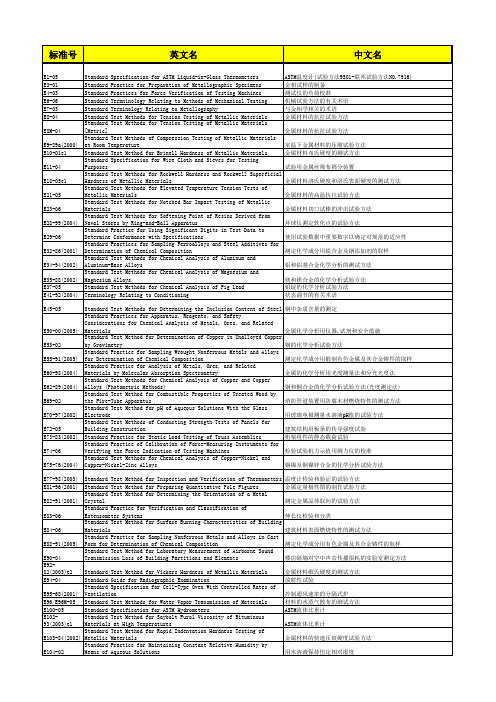
钢中非金属夹杂物含量的测定标准评级图显微检验法介绍

钢中非金属夹杂物含量的测定标准评级图显微检验法介绍GB/T 10561—2005—何群雄,孙时秋:介绍了钢中非金属夹杂物含量测定显微检验法的概况,并对国标等同采用国际标准ISO4967:1998后变化的技术内容作了简要说明。
:非金属夹杂物;标准评级图显微检验法 0钢中非金属夹杂物的评定是衡量钢内在质量的一种重要方法,通过该方法的检验能反映钢中非金属夹杂物的含量、沾污度以及类型,为满足产品设计要求或改进生产工艺提供可靠的依据,尤其是非金属夹杂物的显微检验方法,更是各国冶金学家长期研究的课题。
随着显微技术和电子金相技术的不断发展,采用自动图像仪及计算机软件来评定非金属夹杂物的方法已经越来越多的被用于进行科学研究和实际生产检验。
目前美国金属材料协会(ASTM)E4委员会已有3个显微检验方法来评定非金属夹杂物含量的方法标准,即ASTM E45-97《用评级图谱评定非金属夹杂物的人工方法》、ASTM E1122-1986《自动图像分析法检查非金属夹杂物级别的方法》和ASTM E1245-2000《采用自动图像分析法测定钢中非金属夹杂物或第二相含量的方法》。
但是,应用光学显微镜测定钢中非金属夹杂物的标准图谱评级方法,至今还是在被最广泛地采用。
随着钢铁冶金技术的不断发展和对钢铁材料质量的要求不断提高,标准图谱评级的显微方法检验标准也在不断地修改和完善之中,如现行的国际标准ISO4967-1998《用标准图谱评定钢非金属夹杂物的显微方法》和美国ASTME45-97《钢中非金属夹杂物含量测定方法》对标准图谱和评定方法都作了较大的修改和变动,较好地解决了用光学显微镜评定钢中非金属夹杂物评定的一系列问题,使标准图谱的显微评定方法日趋完善。
GB/T10561-1989《钢中非金属夹杂物显微评定方法》标准是我国钢检测领域的一项重要的基础标准,也是钢中非金属夹杂物含量的主要检测方法之一。
该标准已颁布了一项重要的基础标准,也是钢中非金属夹杂物含量的主要检测方法之一。
ASTME45-2005钢中夹杂物含量的评定方法(精)

ASTM E45-2005 钢中夹杂物含量的评定方法本标准按E45标准颁布发行。
代号后所紧跟的数字表示最初的采用年份,如果是修订本,则表示过去最近一次修的年份。
圆括号里的数字表示过去最近一次重新批准的年份。
本标准经国防部批准发布。
1 范围1.1 本标准的试验方法为测定锻钢中非金属夹杂物含量的方法。
宏观试验法包括低倍腐蚀、断口、台阶和磁粉法。
显微试验法通常包括5种检测。
依据夹杂物形状而不以化学特点,显微法将夹杂物划分为不同类型。
这里主要讨论了金相照相技术,它允许形状类似的夹杂物之间略有不同。
这些方法在主要用来评定夹杂物的同时,某些方法也可以评估诸如碳化物、氮化物、碳氮化物、硼化物和金属间化合物的组成。
除了钢以外,其它合金在有些情况下也可以应用这些方法。
根据这些方法在钢中的应用情况,将分别给予介绍。
1.2 本标准介绍了依据显微试验方法A和方法D,使用JK评级图评定夹杂物的程序。
1.3 按照钢的类型和性能要求,可以采用宏观法或显微法,也可以将二者结合起来,以得到最佳结果。
1.4 这些试验方法仅仅为推荐方法,对任何级别的钢而言,这些方法都不能作为合格与否的判据。
1.5 该标准以国际单位制规定的单位为标准单位,圆括号里的内容为转化的近似值。
1.6 本标准未注明与安全相关的事项,如果有的话,也只涉及本标准的使用。
标准使用者应建立适当的安全和健康操作规程,并且在使用标准前应确定其适用性。
2 参考文献2.1 ASTM标准:D 96 用离心法分离原油中水和沉淀物的试验方法。
E 3 制备金相试样指南E 7 金相显微检测术语E 381 钢棒,钢坯,钢锭和锻件的宏观试验法E 709 磁粉检测指南E 768 自动测定钢中夹杂物的试样的制备和评定操作规程E 1245 用自动图像分析法确定金属中夹杂物或第二相含量的操作规程E1444 磁粉探伤法的操作规程E 1951 光电子显微镜和扫描电镜操作指南2.2 SAE标准:AMS 2300,高级飞行性能钢的清洁度:磁粉检测程序AMS 2301,飞行性能钢的清洁度:磁粉检测程序AMS 2303,飞行性能钢的清洁度:耐腐蚀马氏体钢磁粉检测程序AMS 2304,特种飞行性能钢的清洁度:磁粉检测程序2.32.4 ISO标准:ISO 3763,锻钢——非金属夹杂物的宏观评定法ISO 4967,钢——使用标准图谱的非金属夹杂物显微评定方法2.5 ASTM附加标准:钢中夹杂物评级图Ⅰ-r和评级图Ⅱ低碳钢的4张显微照片3 术语3.1 定义:3.1.1 本标准中用到的定义,见ASTM E7 。
钢中非金属夹杂物检验标准ASTME45-2018a与IS04967-2013异同点解析

ISO
计算值
1
1Hale Waihona Puke 11313
9
9
9
27
27
4
4
4
321
16
16
16
745
36
36
36
1027
1356
1733
2157
Copyright©博看网. All Rights Reserved.
DS 类直径μm
ISO
规定值
25
49
64
81
100
25
25
49
64
81
100
19
38
53
76
19
38
53
76
107
151
法(氧化物和硅酸盐法)、D 法(低夹杂物含量检验法)
和 E 法(SAM 评级法),显微检验法用于检测非金属夹
杂物的尺寸、分布、数量和类型,通过与标准评级图谱
比较,评出夹杂物类型和级别。ASTME45-2018a 中包
含两套标准评级图谱,图谱 I-A 和图谱 II。其中图谱
I-A 是以 JK 评级图为基础进行细化而形成的,包含
准在此基础上增加了 DS 类(大颗粒球状氧化物),将
物),每类夹杂物又根据宽度分为粗系和细系;ISO 标
采用苏联标准体系。
超过 D 类粗系夹杂物直径(ϕ 13μm)的单颗粒夹杂物
但是两个标准仍存在一定的差异,鉴于此,本文深入
定义为 DS 类单独评级。此外,ASTME45-2018a 规定
研 析 了 两 个 标 准 的 最 新 版 本(ISO4967-2013 和
Copyright©博看网. All Rights Reserved.
EN 45545-1中文

EN 45545-1欧洲标准1998年7月ICS描述符英语版本铁路应用—铁路车辆防火—第1部分:综述本欧洲标准草案提交给欧洲标准化委员会(CENCEME;EC)成员审核,本标准草案由技术委员会制定。
如果本草案要成为欧洲标准,欧洲标准化委员会/欧洲电工标准化委员会应承诺履行其委员会的国际章程,在该章程规定的条件下,本欧洲标准不经任何修改即可赋予某一国家标准的法律地位。
本欧洲标准草案由欧洲标准化委员会/欧洲电工标准化委员会确定以三种官方语言(英语、法语、德语)出版,其他任何一种语言的版本,可由欧洲标准化委员会/欧洲电工标准化委员会的成员负责翻译,并通知联合国秘书处。
所翻译语言的版本与正式版本一样具有相同的法律地位。
欧洲标准化委员会的成员有澳大利亚、比利时、捷克共和国、丹麦、芬兰、法国、德国、希腊、冰岛、爱尔兰、意大利、卢森堡、荷兰、挪威、葡萄牙、西班牙、瑞典、瑞士和英国。
注:此文件不是欧洲标准,是为审查和征求意见而分发。
此文件受到更改不另行通知,此文件不应看作为欧洲标准。
CEN欧洲标准化委员会中心秘书处:B-1050布鲁塞尔,路德大街36号© 1998 CEN/CENELEC 各国成员有权在世界范围内以任何形式和任何方法使用 Ref.No.EN 45545-1: 1998E目 录前言 3 ···············································································································································································································································································································································································································································································································································································································································································································································································································································································································································································································································································································································································································································································································································································································································································································································································································································································································································································································································································································································································································································································································································································································································································································································································································································································································································································································································································································································································································································································································································································································································································································································································································································································································································································································································································································································································································引言 4 1. 范围 4 2. 规范性引用文件 4 3. 定义 53.1 铁路车辆 5 3.2 滞留时间 5 3.3 工作人员 5 3.4 工作种类 5 3.5 火灾危险 5 3.6 重新装备 54. 术语 55. 目的 66. 设计种类 67. 操作种类78. 车辆分类79. 火险等级7 10. 防火措施7 11. 一致性评定811.1 设计验证和生效8 11.2 质量保证8前言此欧洲标准已由CEN/TC 256“铁路应用”与CENELEC/TC 9X“铁路电气和电子应用”的“防火安全”联合工作组制定的。
ASTMA中文
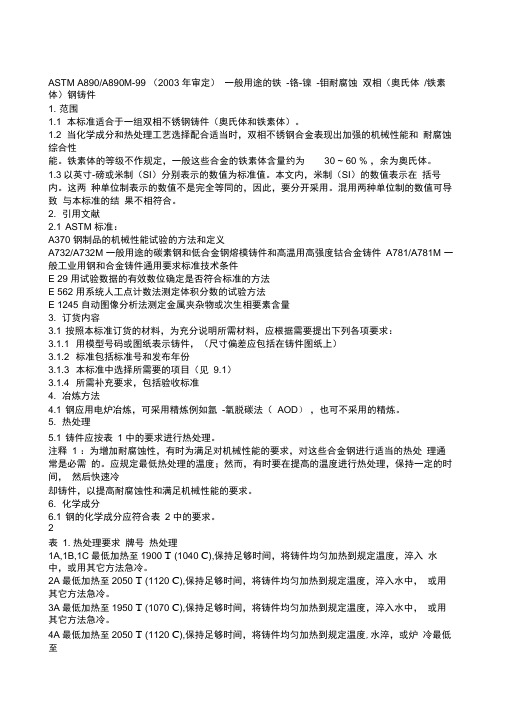
ASTM A890/A890M-99 (2003 年审定)一般用途的铁-铬-镍-钼耐腐蚀双相(奥氏体/铁素体)钢铸件1. 范围1.1 本标准适合于一组双相不锈钢铸件(奥氏体和铁素体)。
1.2 当化学成分和热处理工艺选择配合适当时,双相不锈钢合金表现出加强的机械性能和耐腐蚀综合性能。
铁素体的等级不作规定,一般这些合金的铁素体含量约为30 ~ 60 % ,余为奥氏体。
1.3以英寸-磅或米制(SI)分别表示的数值为标准值。
本文内,米制(SI)的数值表示在括号内。
这两种单位制表示的数值不是完全等同的,因此,要分开采用。
混用两种单位制的数值可导致与本标准的结果不相符合。
2. 引用文献2.1 ASTM 标准:A370 钢制品的机械性能试验的方法和定义A732/A732M 一般用途的碳素钢和低合金钢熔模铸件和高温用高强度钴合金铸件A781/A781M 一般工业用钢和合金铸件通用要求标准技术条件E 29 用试验数据的有效数位确定是否符合标准的方法E 562 用系统人工点计数法测定体积分数的试验方法E 1245 自动图像分析法测定金属夹杂物或次生相要素含量3. 订货内容3.1 按照本标准订货的材料,为充分说明所需材料,应根据需要提出下列各项要求:3.1.1 用模型号码或图纸表示铸件,(尺寸偏差应包括在铸件图纸上)3.1.2 标准包括标准号和发布年份3.1.3 本标准中选择所需要的项目(见9.1)3.1.4 所需补充要求,包括验收标准4. 冶炼方法4.1 钢应用电炉冶炼,可采用精炼例如氩-氧脱碳法(AOD),也可不采用的精炼。
5. 热处理5.1 铸件应按表1 中的要求进行热处理。
注释 1 :为增加耐腐蚀性,有时为满足对机械性能的要求,对这些合金钢进行适当的热处理通常是必需的。
应规定最低热处理的温度;然而,有时要在提高的温度进行热处理,保持一定的时间,然后快速冷却铸件,以提高耐腐蚀性和满足机械性能的要求。
6. 化学成分6.1 钢的化学成分应符合表2 中的要求。
齿轮钢中英文标准版本
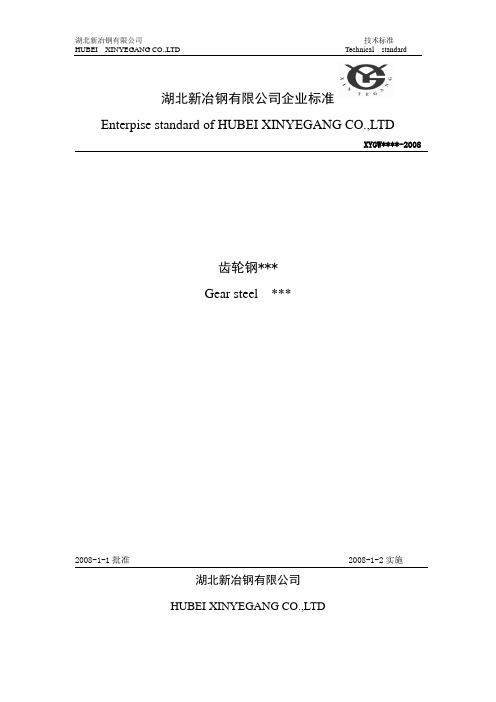
湖北新冶钢有限公司企业标准Enterpise standard of HUBEI XINYEGANG CO.,LTDXYGW****-2008齿轮钢***Gear steel ***2008-1-1批准 2008-1-2实施湖北新冶钢有限公司HUBEI XINYEGANG CO.,LTDXYGW****-2008前言Foreword本标准由湖北新冶钢有限公司提出The standard is proposed and issued by HUBEI XINYEGANG CO.,LTD.本标准由湖北新冶钢有限公司技术部归口The standard is archived by Technology Department of HUBEI XINYEGANG CO.,LTD. 本标准主要起草人:(签字)李博鹏Drawn up by :(signature)Li BoPeng本标准主要审核人:(签字)Audited by:(signature)本标准批准人:(签字)Approved by :(signature)齿轮钢***技术条件Specification of Gear Steel ***1适用范围Scope本技术条件适用于供出口用齿轮钢***热轧或者热锻棒材.This specification is applied for the hot rolled or hot-forged bar of gear steel *** expecilly used for our export product delivery.本标准规定了热轧和锻制的合金结构钢尺寸、外形、重量及允许偏差、技术要求、试验方法、检验规则、包装、标志和质量证明书等。
This standard specifies the dimensions, shapes, weight and allowed deviations,technical requirement, inspection methods, inspection rules, packing, marking and quality certificates of hot rolled or forged structural alloy steels.本标准适用于直径或厚度不大于250mm的合金结构钢棒材。
ASTM标准中非金属夹杂物测定结果的测量不确定度分析

第41卷第2期2020年4月化工装备技术ASTM标准中非金属夹杂物测定结果的测量不确定度分析吴志刚**万章张强连晓明(合肥通用机械研究院有限公司国家压力容器与管道安全工程技术研究中心合肥通用研究院特种设备检验站有限公司)摘要根据ASTM E45-18a ”Sfa/jc/artf 7>sf jV/efAods/b r ZJeferm/nyng'fAe//3c/usy〇/3CoufenfofSfee/ ",采用XJG-05光学显微镜及QuantLab-M G定量金相分析软件对ASTM A335 Gr.Pl1钢管试样中的非金属夹杂物进行测定。
依据JJF 1059.1—2012《测量不确定度评定与表示》标准分析了非金属夹杂物测定结果的测量不确定度来源,并对每个不确定度分量进行了评定。
根据不确定度传播规律得到合成不确定度,并最终计算出扩展不确定度。
分析结果表明:ASTM A335 G r.P l l钢管试样中夹杂物种类为C类粗系硅酸盐夹杂物,夹杂物评级为C1.5e,扩展不确定度{/=0.018,置信因子(=2。
关键词非金属夹杂物评级不确定度评定扩展不确定度中图分类号 TG 115.2 D O I:10.16759/ki.issn.1007-7251.2020.04.002Analysis of Measurement Uncertainty of Non-Metallic InclusionsBased on ASTM StandardsWU Zhigang WAN Zhang ZH ANG Q iang LIAN X iaom ingAbstract: According to ASTM E45-18a"Standard Test Methods for Determining the Inclusion Content of Steel", XJG-05 optical microscope and QuantLab-MG quantitative metallographic analysis software were usedto determine non-metallic inclusions in ASTM A335 Gr.Pll steel pipe samples. According to JJF 1059.1—2012"Evaluation and Expression of Uncertainty in Measurement''standard, the sources of measurement uncertainty ofnon-metallic inclusion measurement results were analyzed, and each uncertainty component was evaluated. Thesynthetic uncertainty was obtained according to the law of uncertainty propagation, and the extended uncertaintywas finally calculated. The results showed that the type of inclusions in the ASTM A335 Gr.Pl 1steel pipe samplewas a class C coarse silicate inclusion, the inclusion rating was C1.5e, the expanded uncertainty U = 0.018, and theconfidence factor k = 2.Key words: Non-metallic inclusion rating; Uncertainty assessment; Expanded uncertainty〇引言组织结构和力学性能,因此准确测定钢中非金属夹杂物的含量级别十分重要。
- 1、下载文档前请自行甄别文档内容的完整性,平台不提供额外的编辑、内容补充、找答案等附加服务。
- 2、"仅部分预览"的文档,不可在线预览部分如存在完整性等问题,可反馈申请退款(可完整预览的文档不适用该条件!)。
- 3、如文档侵犯您的权益,请联系客服反馈,我们会尽快为您处理(人工客服工作时间:9:00-18:30)。
ASTM E45-1997 钢中夹杂物含量的评定方法(中译)1 范围1.1 本标准的试验方法为测定锻钢中非金属夹杂物含量的方法。
宏观试验法包括微蚀、断口、台阶和磁粉法。
显微试验法通常包括5种检测。
根据夹杂物形状而不是化学特点,显微法将夹杂物划分为不同类型。
这里主要讨论了金相照相技术,它允许形状类似的夹杂物之间略有不同。
这些方法在主要用来评定夹杂物的同时,某些方法也可以评估诸如碳化物、氮化物、碳氮化物、硼化物和金属间化合物的组成。
除了钢以外,其它合金在有些情况下也可以应用这些方法。
根据这些方法在钢中的应用情况,将分别给予介绍。
1.2 本标准适用于人工评定夹杂物含量。
其他ASTM标准介绍了用JK评级图的自动法(ASTM E1122 )和图像分析法(ASTM E1245 )。
1.3 按照钢的类型和性能要求,可以采用宏观法或显微法,也可以将二者结合起来,以得到最佳结果。
1.4 这些试验方法仅仅为推荐方法,对任何级别的钢而言,这些方法都不能作为合格与否的判据。
1.5 本标准未注明与安全相关的事项,如果有的话,也只涉及本标准的使用。
标准使用者应建立适当的安全和健康操作规程,并且在使用标准前应确定其适用性。
2 参考文献2.1 ASTM标准:A 295 高碳耐磨轴承钢技术条件A 485 强淬透性耐磨轴承钢技术条件A 534 耐磨轴承用渗碳钢技术条件A 535 特种性能的滚珠和滚柱轴承钢技术条件A 756 耐磨轴承用不锈钢技术条件A 866 耐磨轴承用中碳钢技术条件D 96 用离心法分离原油中水和沉淀物的试验方法E 3 制备金相试样指南E 7 金相显微镜术语E 381 钢棒,钢坯,钢锭和锻件的宏观试验法E 709 磁粉检测指南E 768 自动测定钢中夹杂物的试样的制备和评定操作规程E 1122 用自动图像分析法获得JK夹杂物等级的操作规程E 1245 用自动图像分析法确定金属中夹杂物或第二相含量的操作规程2.2 SAE标准:J421,磁粉法测定钢的清洁度等级J422,钢中夹杂物评定的推荐操作规程2.3 航空材料技术条件2300,高级飞行性能钢的清洁度:磁粉检测程序2301,飞行性能钢的清洁度:磁粉检测程序2303,飞行性能钢的清洁度:耐腐蚀马氏体钢磁粉检测程序2304,特种飞行性能钢的清洁度:磁粉检测程序2.4 ISO标准:ISO 3763,锻钢——非金属夹杂物的宏观评定法ISO 4967,钢——使用标准图谱的非金属夹杂物显微评定方法2.5 ASTM附加标准:钢中夹杂物评级图Ⅰ-r和评级图Ⅱ低碳钢的4张显微照片3 术语3.1 定义:3.1.1 本标准中用到的定义,见ASTM E7 。
3.1.2 ASTM E7 中定义了夹杂物数量;由于这些试验方法中有些涉及到长度的测量,或将长度或(和)数量数值化,因而用“夹杂物等级”一词更好。
3.2 本标准的专业术语定义:3.2.1 纵横比——显微镜下的长、宽比。
3.2.2 断续条状夹杂物—— 3 个或 3 个以上的 B 型或C 型夹杂物排成一列,并且平行于热加工轴,列与列之间相距不超过15 µm,一列内任意两个相邻的夹杂物间距不小于 40 µm 。
3.2.3 夹杂物类型——对硫、铝、硅类的夹杂物的定义,见ASTM E7。
球状氧化物,有的试验方法中称为游离的、相对不易变形的夹杂物,纵横比不大于 5 :1 。
在其他的方法中,氧化物被划分为可变形的和不可变形的两类。
3.2.4 JK 夹杂物等级——一种基于瑞士Jernkontoret 程序的、测定非金属夹杂物的方法。
方法A和D 主要是JK评定法,方法E也使用了JK评级图。
3.2.5 条状夹杂物——一个在变形区被大大拉长的夹杂物,或者3个或3个以上的B型或C型夹杂物排成一列,且平行于热加工轴,列与列之间相距不超过15µm,一列内任意两个相邻的夹杂物间距不小于 40µm 。
3.2.6 最差视场评定——通过给试样表面某处各类夹杂物最严重的视场赋值来评定试样中各类夹杂物的方法。
4 意义和使用4.1 这些试验方法包括4个宏观、5个微观试验方法,它们是用来描述钢中夹杂物含量和试验结果的程序。
4.2 夹杂物是以尺寸、形状、密集程度和分布状态,而不是以化学成分为特征的。
尽管化学成分尚未确定,显微试验法已把夹杂物归入几种化学成分相似的某一类物质(如把硫化物、氧化物和硅酸盐——最终归为氧化物一类)。
第12.2.6 条描述了更容易分辨夹杂物的金相照相技术。
用该技术检测到的是分布于试样表面的夹杂物。
4.3 宏观试验法相对显微试验法来说,能测定更大面积的表面,而且由于其检测是肉眼可见或低倍的,因而它们更适合于检测大夹杂物,而不适于检测长度小于0.40mm 的夹杂物。
但它不能分辨夹杂物的类型。
4.4 显微试验法用来表述某些夹杂物的特征,这些夹杂物因脱氧或在固体钢中溶解度有限(成为析出夹杂物)而形成。
这类夹杂物在几何外形上,如尺寸、形状、密集度和分布,具有明显的特点,而在化学成分上无特殊性。
显微试验法并非用来评估外来夹杂物(如熔渣或难熔物),也不是评估碳化物、碳氮化物、氮化物、硼化物或金属间化合物的,尽管有时也用于后者。
4.5 由于许多给定钢中的夹杂物数量随位置而异,钢坯必须进行统计抽样,才能测确定其夹杂物含量。
抽样数必须与钢坯尺寸和特性相符合。
由于自动图像分析法能够进行更准确的微观评定,因而对夹杂物很少的材料,适用于自动图像分析法(见ASTM E1122)。
4.6 宏观和显微试验法的结果可以作为材料外运凭证,但不能作为接收或拒收材料的依据。
这些试验数据的评判标准可见ASTM产品标准或用户与厂方的协议。
4.7 这些试验方法计划用于锻造金属件。
由于没有规定最低变形量,故这些试验方法不适用于铸件和少量加工件。
宏观法5 宏观试验法5.1 概述5.1.1 微蚀试验——该试验用来显示夹杂物含量和分布,这些夹杂物通常分布于横截面或与轧制、锻造方向垂直的截面。
一些实例也进行了纵截面上的检测。
在需要检测区域切取并加工一截面,用合适的腐蚀剂腐蚀。
通常使用的腐蚀剂为盐酸和水在71~82 ℃的混合溶液,正如本试验名称所示,腐蚀后,用肉眼或低放大倍数即可看出被腐蚀表面的夹杂物。
有关本试验的详细内容可见ASTM E381。
对有疑义的结果应通过显微法或其他方法确认。
5.1.1.1 用5.1.1的方法,硫化物表现为浸蚀麻点。
5.1.1.2 这种方法只能检测大块氧化物。
5.1.2 断口试验——该方法用于确定厚度约为9~13 mm的硬化工件断口上的夹杂物。
本试验基本用于钢的分析,因为钢才有可能达到约60HRC的硬度,而且其断口的晶粒尺寸可达7级或更细。
试样外部不能有过量的导致断裂的凹槽或划痕。
断口最好在通过工件轴心的纵向上。
用肉眼或放大约10倍即可检测夹杂物的长度和分布。
回火色或发兰能够有助于对断续状氧化物的判断。
ISO 3763为断面夹杂物的评定提供了一种图示法。
实例表明,用这种方法可以测出长度仅为0.40 mm的夹杂物。
5.1.3 台阶法——该试验方法用来评定轧钢或锻钢加工面上的夹杂物。
按规定的在表面下的直径加工试样。
在良好光照度下,肉眼或低放大倍率即可观察到夹杂物。
有时也把试样加工成更小的直径,以便检测原直径试样后做进一步检验。
该试验一般用于检测3 mm及其以上长度的夹杂物。
5.1.4 磁粉法——磁粉法是台阶法的一种变异。
它是针对铁磁材料,通过加工、磁化试样来判定夹杂物的。
断续的仅有0.40 mm长的夹杂物形成缺磁区,吸引磁粉,进而显现夹杂物。
详细内容见第6章。
5.2 优点:5.2.1 这些方法使试样表面大泛围的检测变得很容易。
多数情况下,人们更关心的是钢中更大的夹杂物,它们呈不均匀分布,且间距较大,这为大面积检测创造了更好的机会。
5.2.2 制备宏观检验用试样较快,仅需要机加工和磨削即可。
不需要高抛光的表面,宏观法对评定大块夹杂物具有足够的灵敏度。
5.3 缺点:5.3.1 不能区分不同夹杂物的形态。
5.3.2 不适宜检测小球状夹杂物或很小的被拉长的链状夹杂物。
5.3.3 磁粉法会导致对显微结构的错误判断,如残奥沟痕、树枝状晶或某合金中的碳化物。
如果磁化电流很大,这种误判很容易出现。
6 磁粉法——详细程序6.1 试样:6.1.1 试样应按6.2制备,由圆形或方形截面的钢锭、钢坯或钢棒上切取试样的步骤推荐如下:6.1.1.1 横截面面积在230 cm2以上——如图1或图2所示,切取1/4截面,用锻造或(和)机加工的方法制成直径为60~150 mm的圆柱形试样。
还可以用另一种方法,即锻或轧制成150 mm的方形或圆形截面,按6.1.1.2加工出1/4截面。
6.1.1.2横截面面积在100~230 cm2(包括100 cm2和230cm2)——如图1或图2所示,切取1/4截面,用锻造或(和)机加工的方法制成最大直径的圆柱试样。
6.1.1.3 横截面面积在100 cm2以下——把试样加工成圆柱体。
另一种方法是制成3个直径的台阶试样,每一个直径对应的圆柱体长度为75 mm。
D为第一个台阶的直径,其值低于标准允许的圆柱试样尺寸;第二个台阶的直径为3/4D;第三个台阶的直径为1/2D。
6.1.2 试样应符合以下要求,除非6.1.1.1~6.1.1.3另有规定。
6.1.2.1 检测表面长度一般为125 mm,通常还需要25 mm的延伸量。
6.1.2.2 从坯料上切取试样的最小值如下:圆形或方形截面坯料尺寸,mm 试样最小尺寸,mm≤12.7 0.7612.7~19(包含19) 1.1319~25.4(包含25.4) 1.5225.4~38(包含38) 1.8938~51(包含51) 2.2851~64(包含64) 3.1764~89(包含89) 3.9689~115(包含115) 4.75115~152(包含152) 6.356.1.2.3 切取的1/4截面应大于图1和图2所示尺寸,以保证试样表面包含坯料的中心。
坯料中心在试样表面上的位置应贴以标记。
6.2 试样制备:6.2.1 试样粗加工后,在稍高于临界温度的温度下水淬或油淬,并根据化学成分进行200~650 ℃的回火,使硬度达到约300HB。
注意避免淬裂。
热处理会形成一个更为均匀的组织,其硬度足以使该组织保留一部分磁性,有助于试验后磁粉聚集。
6.2.2 热处理后,磨削试样(包括端部),或者进行清理,以保证磁粉的良好吸附。
磨削应在与试样长度垂直的方向上进行,并避免形成磨削裂纹。
纵向划痕可能足够深,使磁粉聚集,以致夹杂物模糊不清。
6.2.3 磁化前,应用快干溶剂彻底清洗试样,去除油脂和手指印。
6.3 步骤:6.3.1 沿试样纵向反复通电1/5~1/2 s,电流强度应为在试样直径上160~470 A/cm。