品质管理8D报告单模板(品管8D报告)
8D报告模板2024

验证数量:
验证有效性
验证标记(实物、包
装):
预防再发生应采取的措施
问题关闭
负责人/日期 :
预计纠正措施完成日期
负责人/日期 :
负责人/日期
负责人/日期 :
负责人/日期
意见:
负责人/日期 :
DISCIPLINE 1
不良处理小组
DISCIPLINE 2
①客户名称:
小Байду номын сангаас领导: 成员:
②反馈时间:
③产品名称及型号:
④是否重复发生:Yes □ No □
⑤问题现象(图片)
品质问题改善跟踪报告
内部成员
问题描述(尽量详细)
DISCIPLINE 3
①初步原因分析:
初步原因分析和临时对策
范围批次号:
总数量:
负责人/日期 : 负责人/日期 :
负责人/日期
负责人/日期 :
负责人/日期
法: 环: 流出原因1永久改善措施
人: 机: 料: 法: 环: 流出原因N改善措施:
人: 机: 料: 法: 环:
DISCIPLINE 6
验证订单号:
验证方法:
验证严加抽检结论:
DISCIPLINE 7
工艺改善(文字+ 图): 治具改善(文字+ 图): 制度改善(文字+ 图): 流程改善(文字+ 图):
DISCIPLINE 4
①产生问题根本原因分析:
处理方案:
处理方案: 处理方案:
产生原因1:
产生原因2:
产生原因N:
②流出问题根本原因分析:
流出原因1:
流出原因2:
流出原因N:
品质改善8D报告书
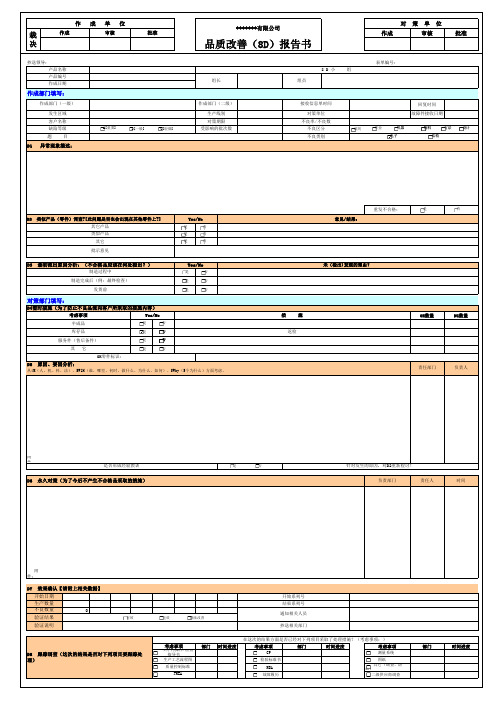
图纸 其它(调查、防
错) 二级供应商调查
部门
时间进度
作成单位
裁
作成
决
审核
批准
抄送领导: 产品名称 产品编号 作成日期
作成部门填写:
作成部门(一级)
发生区域
客户名称 缺陷等级
题
目
D1 异常现象描述:
A[重要]
B[一般]
C[轻微]
*******有限公司
品质改善(8D)报告书
组长
组员
8D小 组
对策单位
作成
审核
批准
表单编号:
作成部门(二级)
生产线别 对策期限 受影响的批次数
重发不合格:
是
否
意见/结果:
未(检出)发现的理由?
措
施
返检
OK数量
NG数量
责任部门
负责人
附 件:
是否形成经验教训
D6 永久对策(为了今后不产生不合格品采取的措施)
是
否
针对发生的原因,对D2重新检讨!
负责部门
责任人
时间
附 件:
D7 效果确认【请附上相关数据】
开始日期
生产数量
不良数量
0
验证结果
有效
验证说明
制造完成后(例:最终检查) 发货前
Yes/No
是
否
是
否
是
否
对策部门填写:
D4暂时措施(为了防止不良品流向客户所采取的措施内容)
考虑事项
Yes/No
半成品
是
否
库存品
是
否
服务件(售后备件)
是否其它是否OK零件标识: D5 原因、要因分析: 从4M(人、机、料、法)、5W1H(谁、哪里、何时、做什么、为什么、如何)、5Why(5个为什么)方面考虑。
8D报告模板 8DReport
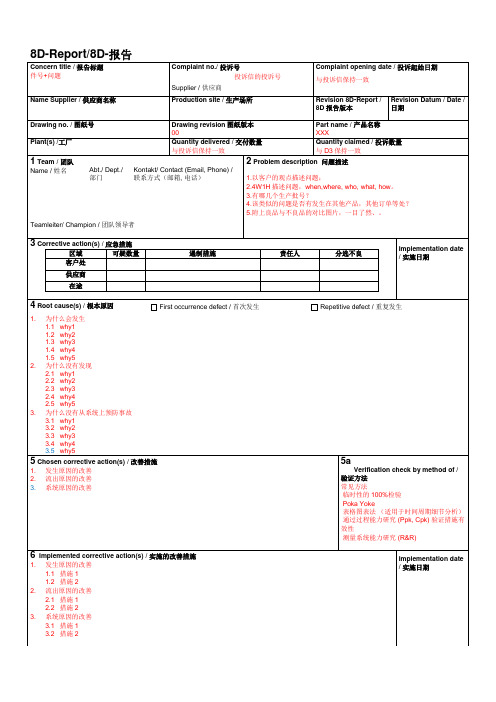
.所有的证据请编号与8D内容对应
例如:
D2.不良照片
D3.挑选指导书/断点标识照片/断点批次信息
D4.原因分析
4.1发生原因的相关作证
4.2流出原因的相关作证
4.3系统原因的相关作证
D6.改善措施
6.1.1措施1的佐证
6.1.2措施2的佐证
6.2.2....
D7预防措施
7.1相关变更文件的截图并圈出变更点
Implementation date/实施日期
Update of Design FMEA no./设计FMEA更新更新的文件需要截图并用红色方框圈出放在附件作为佐证
Update of Process FMEA no./过程FMEA更新
Update of Control plan no./控制计划更新
临时性的100%检验
Poka Yoke
表格图表法(适用于时间周期细节分析)
通过过程能力研究(Ppk, Cpk)验证措施有效性
测量系统能力研究(R&R)
6Implemented corrective action(s)/实施的改善措施
1.发生原因的改善
1.1措施1
1.2措施2
2.流出原因的改善
2.1措施1
Revision 8D-Report/8D报告版本
Revision Datum / Date/日期
Drawing no./图纸号
Drawing revision图纸版本
00
Part name/产品名称
XXX
Plant(s)/工厂
Quantity delivered /交付数量
与投诉信保持一致
Quantity claimed/投诉数量
8D报告范本
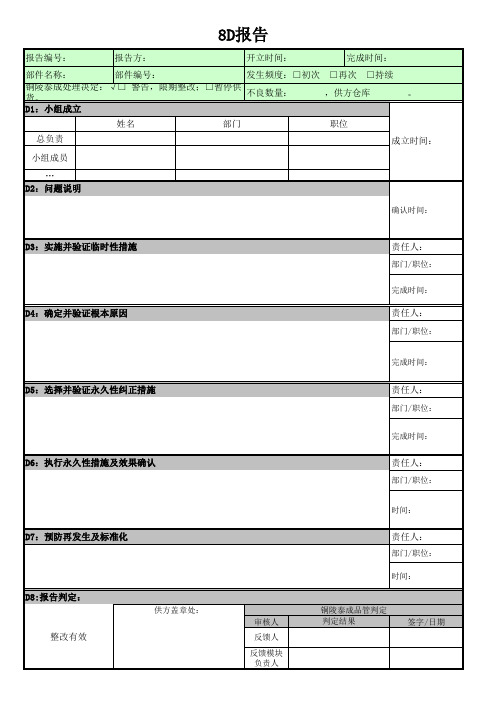
责任人:
部门/职位: 完成时间:
D4:确定并验证根本原因
责任人:
部门/职位:
完成时间:
D5:选择并验证永久性纠正措施
责任人:
部门/职位: 完成时间:
D6:执行永久性措施及效果确认
责任人:
部门/职位:
时间:
D7:预防再发生及标准化
责任人:
部门/职位: 时间:
D8:报告判定:
供方盖章处: 审核人 铜陵泰成品管判定 判定结果 签字/日期
整改有效
反馈人 反馈模块 负责人
8D报告
报告编号: 部件名称: 报告方: 部件编号: 开立时间: 完成时间: 发生频度:□初次 □再次 □持续 ,供方仓库告,限期整改;□暂停供货。 不良数量: D1:小组成立 姓名 总负责 小组成员 … D2:问题说明 部门
确认时间:
D3:实施并验证临时性措施
品质管理8D报告单模板(品管8D报告)
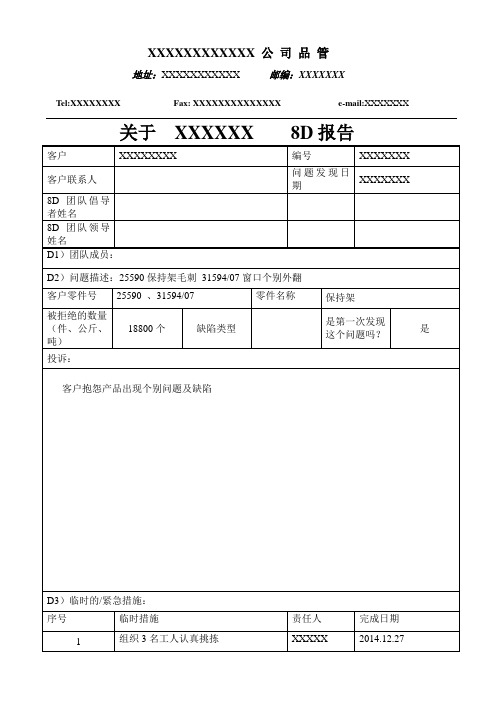
2014.12.27
2
4人去客户工厂挑拣
XXXX
2014.1.12
描述采取的其它的行动方案:(非质量问题的行动方案)
D4)根本原因
【D4-1】原因分析(从人、机、料、法、环、测等各方面查找潜在原因并确定根本原因。可附上鱼骨刺图等分析过程)
1.压坡工序模具上的框子定位不准,间隙有0.2mm
2.操作工没有把产品放正。
3.包装终检抽检没有检验出不合格产品。
1.故障件分析:
型号
25590
毛刺
31594/10
窗口外翻
2.确认根本原因:
公司已组成分析小组,小组认为:
4.A:压坡工序模具上的框子定位不准,操作工没有把产品放正。
5.B:包装终检抽检没有检验出不合格产品。
【D5】永久措施:
序
根本原因
永久措施
责任人
完成日期
完成情况
Tel:XXXXXXXXFax:XXXXXXXXXXXXXXe-mail:XXXXXXX
XXXXXXXXXXXX公司品管
地址:XXXXXXXXXXX邮编:XXXXXXX
关于XXXXXX8D报告
客户
XXXXXXXX
编号
XXXXXXX
客户联系人
问题发现日期
XXXXXXX
8D团队倡导者姓名
8D团队领导姓名
系统性的预防建议
相关文件或内容
责任人
完成日期
完成情况
FMEA
控制计划
系统文件
标识和可追溯性程序ZC-Q-BZ01
操作指导书
附图片
图纸/规格
【D8】团队总结:通过本次问题,进行深刻整改,杜绝此类问题再次发生。
品质8D报告模板

批量/Lot Qty:
样本数量/Sample Qty:
不良数/Reject Qty:
不良率 / Defect rate :
1. 问题解决团队名单 / Team Approach
2. 问题描述 / Problem Description
提报人: 审核Auditing: 3. 临时围堵行动纠正消除不良 / Interim Containment Actions(在制/库存/出货品处理方 实施日期 / Implementation Date 式)
负责人 / Verified By
4. 原因分析(以因果关系排列) / Define And Verify Root Cause
5. 问题对策及执行日期 / Corrective Actions & Implementation Date:
实施日期 /Implementation Date
负责人 / Verified By 6. 防范再发生之对策; 相关文件(号码) / Action To Prevent Re-occurrence & Supporting Document(s):
Corrective And Prevention Action Report
纠客户Customer:
日期Date:
图号/料号Drawing/part No. 品名/Description :
发生场所 / Location :
控制编号/ Control Number:
7. 效果确认 / Verification of Effectiveness (本公司或客户追踪改善效果)
签名Underwrite: 供应商异常处理流程: 异常描述(品质填写)→临时围堵措施(供应商)→原因分析(供应商)→纠正措施(供应商)→预防措施及文件修正 (供应商)→效果确认(SQE) 客户异常回复流程: 异常描述(品质填写)→临时围堵措施/原因分析(QA工程)→纠正措施(QA工程)→预防措施或文件修正(QA工程) →效果确认(客户/QA工程师)
8D报告模板
——需要有责任人和完成时间 ——需要有责任人和完成时间
96h
★说明: 原因和对策确定的原则:四不放过原则 ①原因未查清不放过 ②责任人未受到处理不放过 ③责任人和周围员工未受到教育不放过 ④制定切实可行的整改措施没有落实不放过
D6.验证纠正措施
Verify Corrective Actions
5D
24h
D3.应急措施
Containment Action(s)
风险批次
抽检排除风险
围堵措施
24h
结论
1、成品库数量及批次
抽检2K不良1k,风险极高 100%挑选使用
出厂
2、组测的数量及批次
抽检2K不良1k,风险极高 100%挑选使用
出厂
3、AA的数量及批次
正常可用
4、COB的数量及批次
正常可用
5、SMT的数量及批次
正常可用
6、原材料库的数量及批次
正常可用
7、客户端批次及数量
正常可用
8、检验点批次及数量
正常可用
小结:库存重检确认污点不良率较高,且大部分为浅污点软件不可抓,存在一定出货风险; 故厂内在制&库存品已安排全部隔离
D4.识别问题根因
Identify Root Cause of the Problem
1.1 分析流程如下: 1、头脑风暴确 定潜在原因(至 少10条)
核算质量成本
感谢您的聆听!
汇报人:XXX
结论:(措施是否有效实施)
D7.预防措施标准化
Preventive Action(s)
二、加入到LL中(必填,以附件格式插入报告中)
三、事件回溯(必填,以附件格式插入报告中) 将之前验证的3-5条发生原因和流出原因(检验工序的
品质8D报告标准模板
品质8D 报告标准模板
小组负责人:管理者代表:8D 报告对象:
客户 供应商 公司内部报告编号:品质严重性: 非常严重 严重 轻微
报告日期: 客户/ 供应商名称:
涉及报告或文件:D1:成立改善
小组
D2:问题描述问题描述问题图片
1.
2.
3.
4.
D3:临时措施序号
临时措施要点及描述责任人完成日期结果确认
12
3
4
D4:根本原因
分析序号根本原因描述与分析责任人完成日期结果确认12
3
4
D5:永久性纠正措施序号永久性纠正措施描述责任人完成日期结果确认1
2
3
4
D6:纠正措施验证
序号纠正措施实际验证情况责任人完成日期结果确认1
2
3
4
D7:预防措施序号
预防措施具体描述责任人完成日期结果确认12
3
4
D8:批量验证/
团队激励
此项目原因分析准确,制定的永久性纠正措施验证可行有效。
承认小组的集体努力,对小组工作进行总结并祝贺,同时给予必要的物质和精神奖励。
质量管理8D质量改进报告模板
质量管理8D质量改进报告模板
1D:成立小组
1、成立时间:
2、人员分工:
3、实施计划:
2D:问题说明
1、特性失效模式分析:
、市场表现: 2、原因分析 3
C、朝柴发动机故障情况 4、现生产表现: 5、相关标准要求:
(说明:国家标准、企业标准、产品图纸、工艺文件、检验指导书等) 6、改进
目标:
现状: 目标: 3D:临时措施 1、现生产临时措施:
(说明:按控制要求及要素制定临时处理措施) 2、市场处理措施(方案):
(说明:如向朝柴提供维修及故障判定的指导性材料及维修用样件等,可向朝柴
采购部提报相关材料及样件,由朝柴采购部统一向朝柴品质控制部部提供书面指导
性材料)
4D:根本原因
1、从人(人的要求)、机(工装、设备、量检具等)、料(零部件、实物等)、法
(标准、产品文件、工艺文件等)、环(环境因素等)等方面进行分析(鱼刺图):
2、可能因素分析: (说明:通过市场和现生产调查、信息分析、故障件分析等):
(说明:所占比例指按故障模式排列情况及所占百分比、重要度等情况进行综合
分析,制定可能因素改进所占的比例要求,以便有针对性地对所占比例较大的因素
做为重点进行改进;各可能因素所占比例累加和为100%,无关因素为0%)
5D:制定措施并验证 1、实施计划:
2、措施早期验证:
生产验收、第三方检验报告、市场跟踪情况、现生产跟踪情况等,要有相关书面报告等验证材料做为附件)
3、市场处理方案:
(说明:以指导市场维修、故障判定等,同时保证市场维修服务用件为改进后零部件)
4、改进措施实施日期: 首台发动机出厂编号:
6D:实施永久性纠正措施
7D:预防措施。
2019年品管8d报告范例-word范文模板 (10页)
本文部分内容来自网络整理,本司不为其真实性负责,如有异议或侵权请及时联系,本司将立即删除!== 本文为word格式,下载后可方便编辑和修改! ==品管8d报告范例篇一:8D报告范例錯誤及材質不正確;正確規格顏色為灰白色,且內圓為網狀銅絲加鐵弗龍耐磨層;實際適用錯誤規格顏色為黃色,且內圓為光滑鐵弗龍耐磨層. 2.2.不良品與良品比對圖面 :3.1.對客人提出的問題點立即展開調查問題原因及對策 3.2.對已量產之成品暫時全部隔離 (12*58=696台)3.3.對庫存及線上未使用之凸緣軸承全部隔離,不可使用(004131-A2508+6698=7206PCS,004114-A2 438+2552=2990PCS)3.4.廠商清查庫存數並進行隔離,不可使用(004131-A2 5855PCS,004114-A2 3562PCS)14.1魚骨圖- NE201X/3000凸緣干式軸承不良Man人Material料4.2 Possible factor可能因素- Method 法: 4.2.1.ECR/ECO未按照流程操作4.2.2.圖面未標註相關重要信息4.3 Possible factor 可能因素– Man 人: 4.3.1. IQC檢驗員未嚴格遵守SOP 4.3.2.線上操作人員品質意識淡薄 4.3.3.品質重點不明確4.4 Possible factor 可能因素– Material料 : 4.4.1.測試物料與量產物料不一致 4.4.2.改變廠商未獲客人同意4.4.3.改變廠商未送樣給各單位確認26.1.2不良物料管制及改善落實到責任人; 預計完成日期12/20 責任人:白心順6.2.1生產前2小時提供首件給品保確認; 預計完成日期12/15責任人:歲明章6.2.2.成品打包前派專人負責外觀檢驗(焊接,塗裝,塑膠件外觀). 預計完成日期12/15責任人:歲明章6.3.1.焊接廠統計殘缺SOP提供給IE,IE將SOP補全. 預計完成日期12/21責任人:翟小軍/易峰 6.4.1建立相應獎懲制度,提高人員責任心; 預計完成日期12/15責任人:歲明章/吳志幸 6.4.2制定培訓計劃,對品保人員,操作人員進行培訓. 預計完成日期12/20責任人:章偉 6.5.1上線前宣導品質重點及不良履歷; 預計完成日期12/14責任人:歲明章/吳志幸/章偉6.5.2將品質重點列入SOP,定期更新補缺. 預計完成日期12/20責任人:易峰6.6.1 使用二氧化碳與氬氣混合氣體焊接,完成日期12/14,責任人,翟小軍6.6.2 焊接氣體供給方式由瓶裝改為管道.完成日期12/14,責任人,翟小軍7.2 每批量產前確認首件檢驗執行力度,預計完成日期12/157.3 每批產品管控改善和追蹤改善:進行中.持續進行3篇二:品质七大手法及8D报告品管七大手法品管七大手法是常用的统计管理方法,又称为初级统计管理方法。
- 1、下载文档前请自行甄别文档内容的完整性,平台不提供额外的编辑、内容补充、找答案等附加服务。
- 2、"仅部分预览"的文档,不可在线预览部分如存在完整性等问题,可反馈申请退款(可完整预览的文档不适用该条件!)。
- 3、如文档侵犯您的权益,请联系客服反馈,我们会尽快为您处理(人工客服工作时间:9:00-18:30)。
A
重新制作压坡框子,配合间隙调整到0.05mm,对压坡操作工进行培训,确保操作时放到位。
XXXX
2014.12.20
良好
2
B
包装终检对该产品进行100%全检。
XXXX
2014.12.20
良好
【D6】验证长期纠正措施(以上的纠正措施是否解决了问题)
通过以上措施,可以把轴承保持架碰伤问题基本解决。
【D7】预防:(为防止类似的事情发生,对于相关的系统/工艺/策略进行必要的调整,以预防类似问题的再发生)
Tel:XXXXXXXXFax:XXXXXXXXXXXXXXe-mail:XXXXXXX
XXXXXXXXXXXX公司品管
地址:XXXXXXXXXXX邮编:XXXXXXX
关于XXXXXX8D报告
客户
XXXXXXXX
编号
XXXXXXX
客户联系人
问题发现日期
XXXXXXX
8D团队倡导者姓名
8D团队领导姓名
3.包装终检抽检没有检验出不合格产品。
1.故障件分析:
型号
25590
毛刺
31594/10
窗口外翻
2.确认根本原因:
公司已组成分析小组,小组认为:
4.A:压坡工序模具上的框子定位不准,操作工没有把产品放正。
5.B:包装终检抽检没有检验出不合格产品。
【D5】永久措施:
序
根本原因
永久措施
责任人
完成日期
完成情况
D1)团队成员:
D2)问题描述:25590保持架毛刺31594/07窗口个别外翻
客户零件号
25590、31594/07
零件名称
保持架
被拒绝的数量
(件、公斤、吨)
18800个
缺陷类型
是第一次发现
这个问题吗?
是
投诉:
客户抱怨产品出现个别问题及缺陷
D3)临时的/紧急措施:
序号
临时措施
责任人
完成日期
1
组织3名工人认真挑拣
系统性的预防建议
相关文件或内容
责任人
完成日期
完成情况
FMEA
控制计划
系统文件
标识和可追溯性程序ZC-Q-BZ01
操作指导书
附图片
图纸/规格
【D8】团:XXXXX日期:2014.12.26
备注:
XXXXX
2014.12.27
2
4人去客户工厂挑拣
XXXX
2014.1.12
描述采取的其它的行动方案:(非质量问题的行动方案)
D4)根本原因
【D4-1】原因分析(从人、机、料、法、环、测等各方面查找潜在原因并确定根本原因。可附上鱼骨刺图等分析过程)
1.压坡工序模具上的框子定位不准,间隙有0.2mm
2.操作工没有把产品放正。