反应釜文献
基于聚酰胺酸聚合物反应热分析及反应釜设计优化分析

基于聚酰胺酸聚合物反应热分析及反应釜设计优化分析发布时间:2022-04-18T02:32:31.808Z 来源:《新型城镇化》2022年6期作者:马爱华[导读] 本文围绕聚酰胺酸聚合物反应热分析以及反应釜设计优化问题展开分析与探讨,首先对高分子聚合物反应热进行计算,然后对聚合物反应釜常规设计方法进行研究,最后侧重分析聚合物反应釜设计优化的基本思路,希望通过相关分析能够进一步提高对聚酰胺酸聚合物反应热以及反应釜设计方法的研究水平,仅供参考南京合创工程设计有限公司江苏南京 210012摘要:本文围绕聚酰胺酸聚合物反应热分析以及反应釜设计优化问题展开分析与探讨,首先对高分子聚合物反应热进行计算,然后对聚合物反应釜常规设计方法进行研究,最后侧重分析聚合物反应釜设计优化的基本思路,希望通过相关分析能够进一步提高对聚酰胺酸聚合物反应热以及反应釜设计方法的研究水平,仅供参考。
关键词:聚酰胺酸聚合物;反应热;反应釜;设计优化以聚酰胺酸为代表的高分子聚合物是纺织化纤领域以及工程树脂领域应用作为广泛的材料之一,小分子单体原料在溶剂环境中产生聚合反应,以此种方式生成具有高分子量的聚合原液,整个过程会产生大量反应热,溶液温度升高进而对聚合进行产生影响。
除此以外,若分子量分布范围过款,还会降低原液黏度,影响其在纺织化纤领域的应用。
本文以下分析中即对聚酰胺酸聚合物反应热进行分析,并探讨反应釜设计优化的关键思路,以最大限度确保聚合反应的正常进行,同时将聚合体分子量控制在合理范围内。
1 高分子聚合物反应热计算对于高分子聚合物而言,其分子量分布范围通常在104~107以内。
实验室条件与工业生产环境条件存在比较明显的差异性,必须在设计过程中加以区分。
对于聚酰胺酸原液而言,工业生产条件下聚酰胺酸分子量为2~5万,远远高于1.0mol剂量DOA与1.0mol计量PMDA聚合所产生对应量级,基于此,高分子聚酰胺酸原液能够更好的满足纺丝生产以及树脂生产工艺需求。
用于反应釜正常安全排气的管路布置
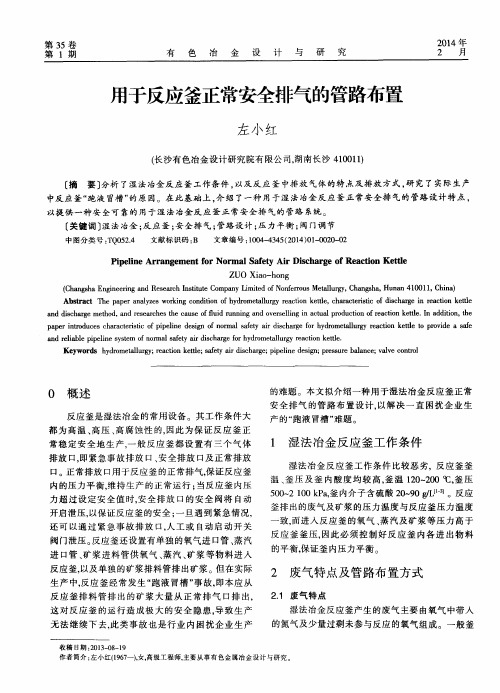
夹套 管结 构 , 管道 中间排 气 , 外 壁 蒸 汽加 温 或保 温。 夹
套管 结构 为保 证排 气 管顺 畅提供 了有 力保 证 。 5 1 合理设 置 排气 口的大小 , 排 气 口不 宜过 大 。根
据反 应 釜 的容 积 , 物 料加 入 量 、 温度 、 压力, 计算 排 气
口规 格, 一般 排 气 口为 D N 4 0 ~ 8 0 , 排 气 口过 大是 造 成
1 4 5 1 5 5 o C 。 压力 1 1 0 0 ~ 1 3 0 0 k P a , 此 时, 正 常 排 气 调
节 阀进 入 在 线 控 制程 序进 行 调 节 , 阀 门开 启 度 由大 至小, 维持 反 应釜 的压 力平衡 , 保 证 正 常安全 排气 。
图 1 反 应 釜 正 常 安 全 排 气 的 管 路 布 置 示 意
反 应釜 “ 跑 液 冒槽 ” 事 故 的重要 原 因 。
6 ) 合理 调 节物 料加 入 量, 如 氧 气量 、 蒸 汽 量, 并 合
理 调节 排气 管 的阀 门开度 , 根 据 反应 釜 的温度 、 压力, 及 时调 节排 气管 的排 气量 。 实际 生产 中采 用在 线 控 制 调 节, 原 则 上 排 气 管 的阀 门尽 量 要 小 开启 , 以防 止 矿浆 从 排气 管外 排 。
中反 应 釜“ 跑 液 冒槽 ” 的原 因。在 此基 础 上 , 介 绍 了一 种 用 于湿 法冶金 反应 釜 正 常安全 排 气 的管路 设 计特 点 ,
以提供 一 种安 全可 靠 的用 于湿 法冶金 反应 釜 正常安 全排 气 的管路 系统 。
[ 关键 词 ] 湿法 冶金 ; 反应 釜 ; 安全 排 气 ; 管路 设 计 ; 压 力 平衡 ; 阀 门调 节
新型电磁加热实验室用磁力驱动反应釜的研究与设计

新型电磁加热实验室用磁力驱动反应釜的研究与设计作者:甄继夏马文启来源:《山东工业技术》2015年第04期摘要:实验室用磁力驱动反应釜的加热方式主要采用电阻加热,加热效率低、时间长,温度控制精度差,保温效果差。
通过对多种加热方式的比对研究,确定电磁加热的可行性,研究设计开发一种新型的电磁加热磁力驱动反应釜,除了具有磁力驱动反应釜承压能力高、釜盖开启方便、操作维护简单、无泄漏的优点,还具有加热效率高,升温速度快,温度控制精确等特点。
关键词:电磁加热;磁力驱动;反应釜;设计1 引言实验室用磁力驱动反应釜是化工企业、科研院校、研究所进行化学实验的主要反应设备之一,它具有承压能力高、釜盖开启方便、操作维护简单、无泄漏的优点。
到目前为止,国内外关于实验室用的反应釜种类很多,实验釜主要由承压釜体(承压容器)、釜盖、加热装置、冷却装置、搅拌装置、磁力传动装置以及安全附件、阀门等组成,见下图。
常规实验室用反应釜的加热装置主要采用电加热的结构对反应介质进行加热,以促进化学反应的进行,也有采用导热油加热以及蒸汽加热的方式对介质进行加热的,但是在实际操作过程中,普遍反映加热效率低、时间长,温度控制精度差,保温效果差,直接导致实验的周期长,实验采集数据准确度降低,实验成功率降低,实验成本增加。
针对目前实验用反应釜存在缺点和问题,开发研制一种新型的实验室用磁力驱动反应釜,除了具有常规磁力驱动反应釜的特点,还能具有加热效率高,温度控制精确等特点,成为各大企业院校的迫切需求。
2 反应釜加热方式选择目前国内传统反应釜普遍采用的加热方式均为介质传热,包括电炉加热以及导热油、蒸汽等介质传热。
但无论是哪种方式都存在效率不高、热量散失严重的问题,这对能源是一种浪费,也极大地使用单位的生产效率,严重地影响了经济效益。
行业内迫切需求对反应釜的加热方式进行改进,改变目前耗能高、效益低的尴尬现状。
而电磁加热方式作为一种相当成熟的技术,已成功应用在电磁炉、化纤注塑等行业,并取得了非常好的效果。
石墨反应釜的现状及一种高效传热形式

石墨反应釜的现状及一种高效传热形式发布时间:2022-09-02T06:44:21.161Z 来源:《科学与技术》2022年9期作者:章钱[导读] 本文通过设计了一种新的反应釜,即石墨反应釜,介绍了石墨反应釜的结构和特性,并将石墨反应釜与搪瓷反应釜进行了对比分析章钱南通三圣石墨设备科技股份有限公司摘要:本文通过设计了一种新的反应釜,即石墨反应釜,介绍了石墨反应釜的结构和特性,并将石墨反应釜与搪瓷反应釜进行了对比分析,证明了石墨反应釜比搪瓷反应釜更广的应用领域,更优的结构性能和经济性能。
关键字:石墨反应釜;搪瓷反应釜;特性;高效的传热结构1.前言搅拌反应釜在工业生产中应用的范围较广, 尤其是在化学工业中, 很多的化工生产都或多或少的应用着搅拌操作。
化学工艺过程的种种化学变化,是以参加反应物质的充分混合为前提的,对于加热、冷却和液体萃取以及气体吸收等物理变化过程,也往往要采用搅拌操作才能得到好的效果。
其性能的好坏对整套生产装置的生产能力、产品质量、原材料消耗、环境保护等技术经济指标均有重大的影响。
它有使物料混合均匀,使气体在液体中很好地分散,使固体颗粒在液相中均匀悬浮,使不相容的另一液相均匀悬浮或充分乳化,加强相间传质,强化传热的功能【1】。
在防腐蚀领域搪瓷反应釜的应用非常广泛,是比较常见的反应釜,它是将含高二氧化硅的玻璃,衬在钢制容器的内表面,经高温灼烧而牢固地密着于金属表面上成为复合材料制品。
搪瓷反应釜是一种理想的耐化学腐蚀设备,在化工、医药、冶金、食品等领域都得到了很广泛的应用。
文章通过对石墨反应釜的结构设计研究,发现其更具有经济和适用性能,并提出一种高效传热的反应釜的结构形式。
2.石墨反应釜结构的说明石墨反应釜是由上封头、石墨筒体、石墨下封头、金属夹套、搅拌装置。
上封头与夹套上法兰通过螺栓紧固,上封头加装螺旋弹簧施加总装压力,充分利用了石墨材料抗压强度远远大于抗拉强度与抗弯强度的特点,并同时解决了在较大温差下石墨与钢制件间的线膨胀差异,起到热胀冷缩的自动补偿作用。
全可视化双反应釜内甲烷水合物生成与分解特征研究

开发技术及水合物开发。 通讯作者:王凯(1982—) ,男,副教授,2004 年毕业于西南石油学院油气储运工程专业,2009 年毕业于中国石油大学( 北京) 油气储运工程专业,获博士学
位,研究方向为油气流动与传热智慧管理、气体水合物、新能源油气融合。
Copyright©博看网. All Rights Reserved.
合物缓慢生成阶段;第 4 阶段为温度压力基本稳定 至实验结束,为稳定阶段。 实验结果与文献中的水 合物生成阶段划分相吻合[28] 。
成后,利用真空泵对反应釜进行抽真空操作。 打开 2. 1. 1 生成过程
恒温室,使水合物平台的温度处于恒定值。
图 3a 为上、下釜生成水合物过程。 上釜中首
(2) 打开进液阀,通过恒压恒速泵以一定的速 先在反应釜壁面的液滴处形成附着于壁面的小块
进行研究具有非常重要的科学价值以及政治经济
意义。 当前对于水合物的生成分解过程研究主要
分为生成动力学、分解动力学以及水合物稳定条件 3 个方面[2] ,主要手段为数值模拟和室内实验。 数
值模拟是分析水合物生成分解行为的重要手段, TOUGH+HYDRATE、CMG、Fluent、COMSOL 等软件
细记录观察水合物的生成分解特征,分析不同因素 对生成分解行为的影响。 在此基础上,选取了纯度 为 99. 99 %的甲烷和去离子水作为实验介质,进行 了 2 次生成分解实验,对上下釜水合物演变特征进 行分析。 然后对比 2 个反应釜内温度压力变化、气
基于CFD仿真分析的搅拌反应釜混合特性研究

[13] Birchall V S,Rocha S D F,Mansur M B,et al. A simplified mecha-
er Organic Ligands,Plenum Press,New York. p 3( 1976) .
nistic analysis of the hydration of magnesia [J]. Can. J. Chem.
Reactive Magnesium Oxide Using Hydration Agents,”J. Therm. A-
Japan ) 97: 683 - 689 ( 1987 ) ( In Japanese with English ab-
nal. Cal.,8[2]467 - 71( 2006) .
[19] Martell AM and Smith RM,Critical Stability Constants,Vol. 5: First
Eng.,2010,79: 507 - 511.
Supplements,Plenum Press,New York. p 418( 1982) .
[14] D. Filippou,N. Katiforis,N. Papassiopi,and K. Adam,“On the Ki- [20] Nakanishi K,Fukuda T and Nomura J,Formation mechanism of Mg
Key words: CDF simulation; Stirred tank reactor; Mixing characteristics
DOI:10.16570/ki.issn1673-6850.2019.01.005
1 前言
(完整word版)反应釜设计
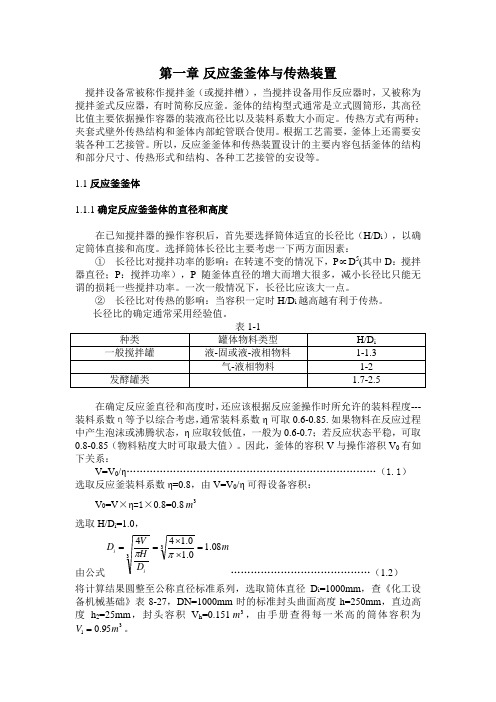
第一章 反应釜釜体与传热装置搅拌设备常被称作搅拌釜(或搅拌槽),当搅拌设备用作反应器时,又被称为搅拌釜式反应器,有时简称反应釜。
釜体的结构型式通常是立式圆筒形,其高径比值主要依据操作容器的装液高径比以及装料系数大小而定。
传热方式有两种:夹套式壁外传热结构和釜体内部蛇管联合使用。
根据工艺需要,釜体上还需要安装各种工艺接管。
所以,反应釜釜体和传热装置设计的主要内容包括釜体的结构和部分尺寸、传热形式和结构、各种工艺接管的安设等。
1.1反应釜釜体1.1.1确定反应釜釜体的直径和高度在已知搅拌器的操作容积后,首先要选择筒体适宜的长径比(H/D i ),以确定筒体直接和高度。
选择筒体长径比主要考虑一下两方面因素:① 长径比对搅拌功率的影响:在转速不变的情况下,P ∝D 5(其中D :搅拌器直径;P :搅拌功率),P 随釜体直径的增大而增大很多,减小长径比只能无谓的损耗一些搅拌功率。
一次一般情况下,长径比应该大一点。
② 长径比对传热的影响:当容积一定时H/D i 越高越有利于传热。
长径比的确定通常采用经验值。
在确定反应釜直径和高度时,还应该根据反应釜操作时所允许的装料程度---装料系数η等予以综合考虑,通常装料系数η可取0.6-0.85.如果物料在反应过程中产生泡沫或沸腾状态,η应取较低值,一般为0.6-0.7;若反应状态平稳,可取0.8-0.85(物料粘度大时可取最大值)。
因此,釜体的容积V 与操作溶积V 0有如下关系:V=V 0/η…………………………………………………………………(1.1) 选取反应釜装料系数η=0.8,由V=V 0/η可得设备容积:V 0=V ×η=1×0.8=0.83m 选取H/D i =1.0,由公式m D H V D ii 08.10.10.14433=⨯⨯==ππ……………………………………(1.2)将计算结果圆整至公称直径标准系列,选取筒体直径D i =1000mm ,查《化工设备机械基础》表8-27,DN=1000mm 时的标准封头曲面高度h=250mm ,直边高度h 2=25mm ,封头容积V h =0.1513m ,由手册查得每一米高的筒体容积为3195.0m V =。
国内外反应釜技术研究现状
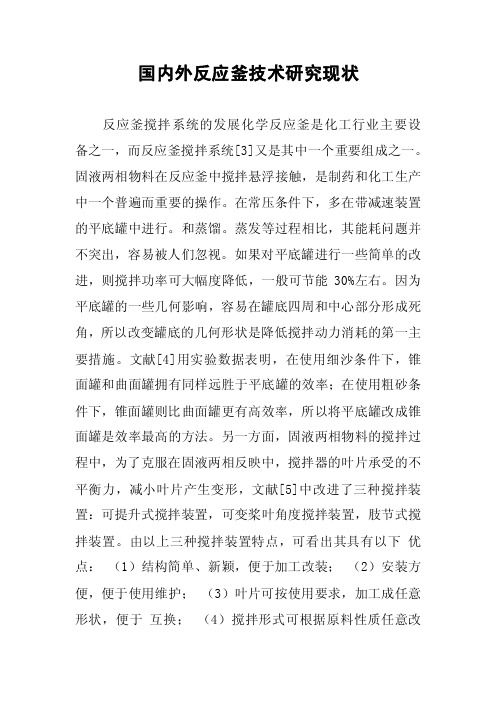
国内外反应釜技术研究现状反应釜搅拌系统的发展化学反应釜是化工行业主要设备之一,而反应釜搅拌系统[3]又是其中一个重要组成之一。
固液两相物料在反应釜中搅拌悬浮接触,是制药和化工生产中一个普遍而重要的操作。
在常压条件下,多在带减速装置的平底罐中进行。
和蒸馏。
蒸发等过程相比,其能耗问题并不突出,容易被人们忽视。
如果对平底罐进行一些简单的改进,则搅拌功率可大幅度降低,一般可节能30%左右。
因为平底罐的一些几何影响,容易在罐底四周和中心部分形成死角,所以改变罐底的几何形状是降低搅拌动力消耗的第一主要措施。
文献[4]用实验数据表明,在使用细沙条件下,锥面罐和曲面罐拥有同样远胜于平底罐的效率;在使用粗砂条件下,锥面罐则比曲面罐更有高效率,所以将平底罐改成锥面罐是效率最高的方法。
另一方面,固液两相物料的搅拌过程中,为了克服在固液两相反映中,搅拌器的叶片承受的不平衡力,减小叶片产生变形,文献[5]中改进了三种搅拌装置:可提升式搅拌装置,可变桨叶角度搅拌装置,肢节式搅拌装置。
由以上三种搅拌装置特点,可看出其具有以下优点:(1)结构简单、新颖,便于加工改装;(2)安装方便,便于使用维护;(3)叶片可按使用要求,加工成任意形状,便于互换;(4)搅拌形式可根据原料性质任意改装,使用范围广泛,便于推广使用。
三种新型搅拌装置已分别取得国家级专利。
29308在现代化工业生产中,为了使设备能更好的发挥尽它的功效,在搅拌系统的内部结构中,也有了更进一步的研究发展。
文献[6]中,用fluent软件分别在其他条件不变的情况下改变搅拌反应罐的浆间距和罐浆径比,实验发现,桨间距d,取4.0m~4.5m为佳;同时上桨距离液面的最小距离不能小于2.0m并适当地减小罐桨径比。
通过实验的方法证明,得出的改进方向和措施使搅拌反应罐内的流体更为符合流体动力学,使流体在罐内能充分、自由地流动,不存在任何的流动死角;而且流体的流动方式多以以湍流为主,从而使液体在罐内充分地进行接触和反应,最终使搅拌反应罐内的反应更为完全,从而提高于设备的处理能力和效率。
- 1、下载文档前请自行甄别文档内容的完整性,平台不提供额外的编辑、内容补充、找答案等附加服务。
- 2、"仅部分预览"的文档,不可在线预览部分如存在完整性等问题,可反馈申请退款(可完整预览的文档不适用该条件!)。
- 3、如文档侵犯您的权益,请联系客服反馈,我们会尽快为您处理(人工客服工作时间:9:00-18:30)。
文献综述
题目名称:晶化反应釜及温度控制系统
题目类别:毕业论文
专业:过程装备与控制工程
班级:08531
摘要:运用VB 语言, 编制了反应釜结构设计中相关设计参数和系数的自动查取程序, 以及反应釜结构尺寸的计算机辅助设计计算程序, 使反应釜的结构设计简单、易行, 避免了设计过程中繁琐、重复的劳动。
关键词:反应釜结构尺寸计算机辅助设计
搅拌设备广泛应用于化工、医药、农药及染料等行业。
由于其操作条件的可控范围较广,又能适用多样化的生产, 应用越来越广泛。
搅拌式反应釜是一种典型的搅拌反应设备, 由于过程换热的需要, 在一般情况下设备设有夹套及蛇管, 以满足传热要求。
釜体的设计是结构设计的第一步, 其包括反应釜的体积、直径及高度设计; 夹套的体积、直径及高度设计; 釜体及夹套的壁厚设计。
尽管其结构设计本身并不复杂, 但当涉及到外压
计算时, 设计者要做大量的重复、繁琐的查取数据、重复计算及反复试算的工作, 设计效率较低。
这种方法已不能适应设计及使用单位对产品设计质量及设计周期的要求, 且相关报道几乎没有。
所以本文尝试用计算机对其进行辅助设计计算。
1设计方法
1.1反应釜容积、内径及高度的设计
反应釜釜体的主要部分是容器, 其筒体部分为圆柱形; 筒体的内径Di和高度H是首先要设计的内容, 其值取决于工艺要求, 其中设备容积V 为主要决定参数; 而设备的容积通常是由生产能力、装料系数等工艺参数确定。
通常情况下, 可用式(1)、式(2)及式(3)求得。
1.2反应釜釜体及夹套的壁厚设计
通常情况下反应釜都存在着换热的需要。
最常见的是夹套式反应釜, 其结构简单, 能起
到一定的换热效果。
反应釜夹套的直径及高度一般由筒体的直径及高度按经验公式而定。
由
于夹套内流体往往具有一定的压力, 计算釜体及其封头壁厚时, 需同时考虑承受内、外压力
的情况。
通常是先按式(4)进行釜体及夹套壁厚的内压计算, 再按外压进行校核。
若[P ]> P
(其中, 且二者相接近, 说明按内压设计计算的壁厚合理; 否则, 需重新进行壁
厚的假设、试算, 直至满足要求为止。
然后, 取按内、外压设计所得壁厚大值为筒体的壁厚。
这个设计及校核的过程, 中间涉及了很多相关参数的查取和反复试算, 较为繁琐。
本软
件根据需要, 编制了相应的计算机程序进行相关参数的数据处理, 实现参数自动查取及计算
机辅助设计计算。
2解决方案
(1) 建立了相应的数据文件, 例如: ①公称直径为300mm~4000mm 椭圆形、球形及碟形封头高度、直边高度、内表面积及容积的数据; ②不同材料的B 值曲线基点数据; ③不同温度下的各材料的许用应力值及钢板的负偏差值等; 并编制了相应的程序, 实现这些参数的自动查取。
(2) 对外压校核所需系数A 、B 的图表进行数据采集及处理。
① A 值实质上是临界应变, 可由式(5)、(6)计算而得。
②B 值曲线是一组二维曲线。
由图1 可知, 其值由温度参数及A 值查出。
本文把B 值
曲线分两部分来处理:
a) 当B 处于直线段时, 先根据温度, 用差值法计算出对应的弹性模量E, 然后由式(7)计
算得B 值。
图(1)压圆筒和球壳厚度计算图(16 M nR)
b) 当B值处于曲线段时, 建立不同温度下的B 值基点数据文件, 利用文献[5]所介绍的双差值法, 编制相应的程序, 来实现B 参数的自动查取。
在B 值曲线基点数据输入准确的情况下, 其精确度明显高于人工查取。
(3) 本设计使用VB 进行编程, 使用户具有一个良好的操作界面。
在输入必要的工艺设
计参数, 如釜体及夹套的设计温度、设计压力、釜体及夹套内介质、筒体及封头材料、反应釜的年生产能力、装料系数及封头型式选择后, 即可进行相关参数及系数的自动查取, 并进行结构尺寸设计, 显示并输出设计结果。
设计计算流程图如图2 所示。
3算例
为某厂设计环氧乙烷反应生成聚醚搅拌反应釜。
反应釜的生产能力为4800 t? a, 年开工天数为300d, 生产周期为间歇操作, 每8h 投料一次; 釜内最高工作压力为115 M Pa, 操作温度为120℃; 在反应开始时, 通过夹套加入蒸汽将装置加热到120℃左右; 由于壁厚传热等因素, 拟用150℃的饱和蒸汽加热, 其饱和蒸汽压力约为015 M Pa; 装料系数取0.7.
图2 程序的流程框图
当输入以上工艺参数后, 封头型式选为椭圆形, 釜体材料选用16 M nR, 夹套材料选用Q235.利用本软件进行结构设计计算的结果如表1 所示。
4结论
(1) 本文编制相应的计算程序, 能实现反应釜设计参数的自动查取。
如(a) 常用材料不同温度下的许用应力值的查取;(b) 直径在300mm~4000mm 的椭球形封头、球形及碟形封头的直边高度、封头高度、封头体积及表面
积查取; (c) 外压设计参数A 、B 值的查取等。
这些参数的自动查取保证了反应釜结构的计算机辅助设计计算得以实现。
此外, 本程序同样适应于其它受压设备的相同参数的自动查取。
(2) 本软件以VB 为手段, 实现了反应釜釜体及夹套部分结构尺寸的计算机辅助设计计算, 操作方法简单、明了、实用, 所得设计结果经实践验证可行。
参考文献
1朱思明, 汤善莆. 化工设备机械基础. 上海: 华东理工大学出版社, 1994.
2李罡. V isualBasic 510 编程实例详解. 北京: 电子工业出版社, 1998.
3陈允中, 汪霞倩. 搅拌设备的设计与计算. 石油化工设备技术, 1997, 18 (6): 13 ~21
4彭兰平, 段光复. 大功率高黏度搅拌设备换代设计. 石油化工设备, 1998, 27 (4): 33 ~36 5於孝春等. CAD 中三维线图的处理. 南京: 南京化工大学学报, 1995, 17 (2)。