梯形螺纹加工新解
梯形螺纹加工工艺分析
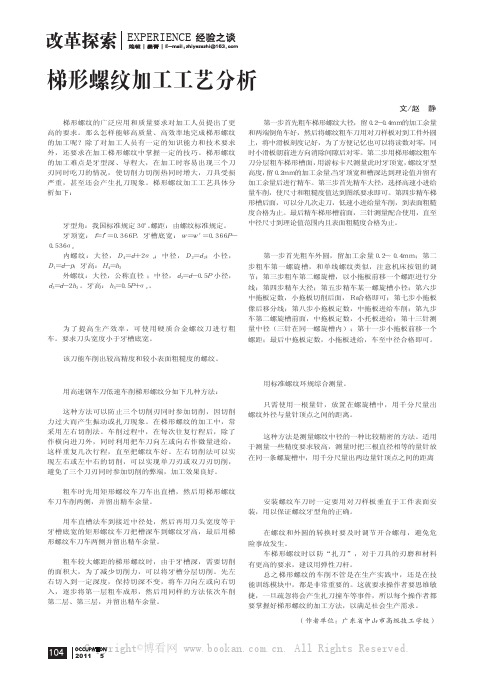
OCCUPATION2011 5104梯形螺纹加工工艺分析文/赵 静梯形螺纹的广泛应用和质量要求对加工人员提出了更高的要求。
那么怎样能够高质量、高效率地完成梯形螺纹的加工呢?除了对加工人员有一定的知识能力和技术要求外,还要求在加工梯形螺纹中掌握一定的技巧。
梯形螺纹的加工难点是牙型深、导程大,在加工时容易出现三个刀刃同时吃刀的情况,使切削力切削热同时增大,刀具受损严重,甚至还会产生扎刀现象。
梯形螺纹加工工艺具体分析如下:一、参数计算标准牙型角:我国标准规定30°。
螺距:由螺纹标准规定。
牙顶宽:f=f′=0.366P。
牙槽底宽:w=w′=0.366P-0.536αc内螺纹:大径,D4=d+2αc;中径,D2=d2;小径,D1=d-p;牙高:H4=h3外螺纹:大径,公称直径 ;中径,d2=d-0.5P 小径,d3=d-2h3 。
牙高:h3=0.5P+αc 。
二、刀具准备1.硬质合金梯形螺纹粗车刀为了提高生产效率,可使用硬质合金螺纹刀进行粗车。
要求刀头宽度小于牙槽底宽。
2.高速钢梯形螺纹精车刀该刀能车削出较高精度和较小表面粗糙度的螺纹。
三、加工方法用高速钢车刀低速车削梯形螺纹分如下几种方法:1.左右切入法 这种方法可以防止三个切削刃同时参加切削,因切削力过大而产生振动或扎刀现象。
在梯形螺纹的加工中,常采用左右切削法。
车削过程中,在每次往复行程后,除了作横向进刀外,同时利用把车刀向左或向右作微量进给,这样重复几次行程,直至把螺纹车好。
左右切削法可以实现左右或左中右的切削,可以实现单刀刃或双刀刃切削,避免了三个刀刃同时参加切削的弊端,加工效果良好。
2.车直槽法粗车时先用矩形螺纹车刀车出直槽,然后用梯形螺纹车刀车削两侧,并留出精车余量。
3.车台阶槽法用车直槽法车到接近中径处,然后再用刀头宽度等于牙槽底宽的矩形螺纹车刀把槽深车到螺纹牙高,最后用梯形螺纹车刀车两侧并留出精车余量。
4.分层切削法粗车较大螺距的梯形螺纹时,由于牙槽深,需要切削的面积大,为了减少切削力,可以将牙槽分层切削。
浅谈车工实训项目梯形螺纹的加工
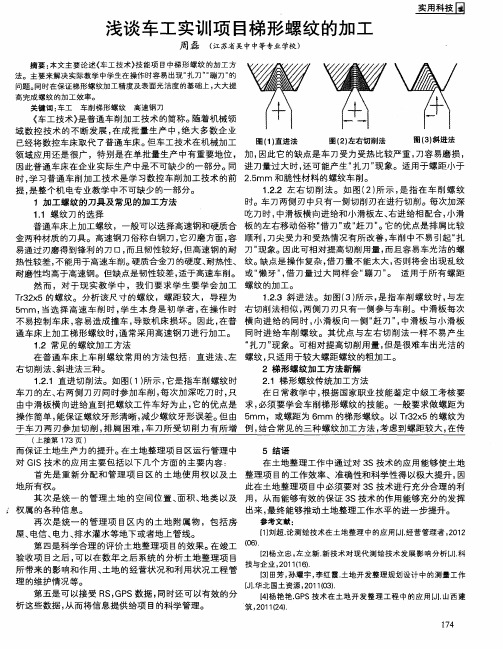
摘要: 本文主要论述 《 车工 技术》 技能项 目中梯 形螺纹 的加工方 法。主要来解决实际教学 中学生在操作时容易 出现“ 扎刀” “ 蹦刀” 的 问题。 同时在保证梯形螺纹a n T精度及表面光洁度的基础上 , 大 大提 高完成螺纹 的加工效率。 关键词 : 车工 车削梯形螺纹 高速钢刀
5 mm, 当选 择 高 速 车 削 时 , 学生本身是初学者 , 在 操 作 时 右切 削 法相 似 , 两侧 刀 刃 只有 一侧 参 与车 削。 中滑 板 每次 不 易控 制车 床 , 容 易造 成 撞 车 , 导 致 机床 损坏 。 因此 , 在普 横 向进 给 的 同时 , 小 滑 板 向 一侧 “ 赶 刀” , 中滑板 与小 滑板 通 车床 上) J n T 梯形 螺纹 时 , 通 常采用 高速 钢 刀进 行/ J n T。 同时 进 给车 削 螺 纹 。其 优 点 与 左 右切 削 法 一 样 不 易 产 生 1 . 2 常见 的螺纹 加工 方法 “ 扎刀” 现 象。 可相 对提 高切 削用 量 , 但 是 很难 车 出光 洁 的 在普 通 车 床 上车 削 螺纹 常 用 的方 法包括 :直 进法 、 左 螺 纹 , 只 适用 于较 大 螺距 螺纹 的粗 ;  ̄ n - r - 。 右切 削 法 、 斜 进 法三 种 。 2 梯 形螺 纹加 工方 法新解 1 . 2 . 1 直进 切 削法 。如 图( 1 ) 所示 , 它是 指车 削 螺纹 时 2 . 1 梯 形螺纹 传统 加 工 方法 车 刀 的左 、 右 两侧 刀 刃 同时参 加 车 削 , 每 次 加 深吃 刀 时 , 只 在 日常教 学 中 , 根 据 国 家职 业 技 能鉴定 中级 工考 核 要 由中滑板横 向进给直N} P - . 螺纹工件车好为止 , 它的优点是 求 , 必须 要 学 会车 削梯 形 螺纹 的技 能 。一 般 要求做 螺 距 为 操作 简 单 , 能保 证 螺纹 牙形 清晰 , 减 少螺纹 牙形误 羞 。 但 由 5 mm ,或 螺距 为 6 mm 的梯 形螺 纹 。 以 T r 3 2 x 5的螺 纹 为 于 车 刀 两 刃参 加 切 削 , 排 屑 困难 , 车 刀所 受 切 削 力 有 所 增 例 , 结合 常见 的三 种 螺纹 / i n n - 方法 , 考 虑 到螺 距较 大 , 在传
梯形螺纹数控加工及问题处理
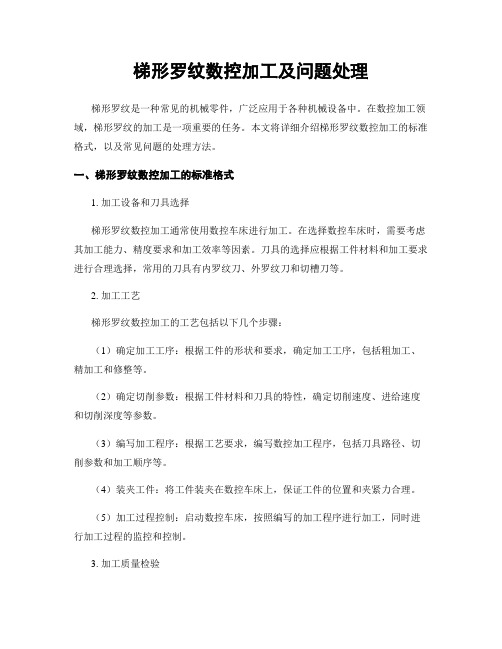
梯形罗纹数控加工及问题处理梯形罗纹是一种常见的机械零件,广泛应用于各种机械设备中。
在数控加工领域,梯形罗纹的加工是一项重要的任务。
本文将详细介绍梯形罗纹数控加工的标准格式,以及常见问题的处理方法。
一、梯形罗纹数控加工的标准格式1. 加工设备和刀具选择梯形罗纹数控加工通常使用数控车床进行加工。
在选择数控车床时,需要考虑其加工能力、精度要求和加工效率等因素。
刀具的选择应根据工件材料和加工要求进行合理选择,常用的刀具有内罗纹刀、外罗纹刀和切槽刀等。
2. 加工工艺梯形罗纹数控加工的工艺包括以下几个步骤:(1)确定加工工序:根据工件的形状和要求,确定加工工序,包括粗加工、精加工和修整等。
(2)确定切削参数:根据工件材料和刀具的特性,确定切削速度、进给速度和切削深度等参数。
(3)编写加工程序:根据工艺要求,编写数控加工程序,包括刀具路径、切削参数和加工顺序等。
(4)装夹工件:将工件装夹在数控车床上,保证工件的位置和夹紧力合理。
(5)加工过程控制:启动数控车床,按照编写的加工程序进行加工,同时进行加工过程的监控和控制。
3. 加工质量检验梯形罗纹数控加工完成后,需要对加工质量进行检验。
常用的检验方法包括外观检查、尺寸测量和罗纹检测等。
检验结果应符合相关标准和要求。
二、常见问题的处理方法1. 加工精度不达标如果梯形罗纹的加工精度不达标,可能会导致工件无法正常使用。
处理方法如下:(1)检查数控车床的精度:检查数控车床的定位精度、回转精度和切削精度等,确保设备的正常运行。
(2)检查刀具的磨损情况:如果刀具磨损严重,应及时更换或者修磨刀具,确保切削效果和加工精度。
(3)调整切削参数:根据实际情况,适当调整切削速度、进给速度和切削深度等参数,提高加工精度。
2. 刀具寿命过短刀具寿命过短会增加生产成本和加工周期。
处理方法如下:(1)选择合适的刀具材料:根据工件材料和加工要求,选择合适的刀具材料,提高刀具的硬度和耐磨性。
(2)优化切削参数:通过调整切削速度、进给速度和切削深度等参数,减少刀具的磨损和热变形,延长刀具的使用寿命。
数控车床加工梯形螺纹解析
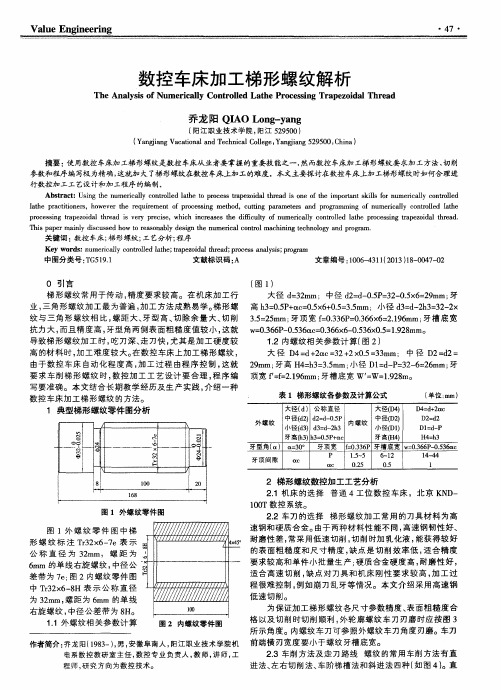
中图分类号 : T G 5 1 9 . 1
文献标识码 : A ( 图 1 )
文章编号 : 1 0 0 6 - 4 3 1 1 ( 2 0 1 3) 1 8 — 0 0 4 7 — 0 2
0 引 言
梯 形螺纹 常用于传动 , 精 度要求较高。在机床 加工行 大径 d = 3 2 m m:中 径 d 2 = d 一 0 . 5 P = 3 2 — 0 . 5 x 6 = 2 9 m m: 牙 业, 三 角 形 螺纹 加 工 最 为 普遍 , 加工方法成熟易学。 梯 形 螺 高 h 3 = 0 . 5 P + a c = 0 . 5 x 6 + 0 . 5 = 3 . 5 m m:小 径 d 3 = d 一 2 h 3 = 3 2 — 2 x 纹 与三角 形螺纹相 比 , 螺距 大、 牙型高 、 切 除余 量大 、 切削 3 . 5 = 2 5 m m: 牙顶宽 f = 0 . 3 3 6 P = 0 . 3 6 6 x 6 = 2 . 1 9 6 mm; 牙 槽 底 宽
摘要: 使用数控车床加 工梯 形螺纹是数控车床从工梯 形螺纹要 求加 工方 法、 切削
参数 和程序编 写极 为精确 , 这 就加 大 了 梯形 螺纹在数控车床上加工 的难度。本文主要探讨在数控车床上加工梯 形螺纹时如何合理进
行数控加 工工艺设计和加 工程序的编制。
p r o c e s s i n g t r a p e z o i d a l t h r e a d i s v e r y p r e c i s e ,wh i c h i n c r e a s e s he t d i f f i c u l t y o f n u me r i c a l l y c o n t r o l l e d l a he t p r o c e s s i n g t r a p e z o i d a l hr t e a d .
浅谈车削梯形外螺纹的加工方法

浅谈车削梯形外螺纹的加工方法车削梯形外螺纹是机械加工中常用的一种方法,广泛应用于汽车、机械制造等行业。
本文将从加工原理、加工方法以及工艺优化等方面对车削梯形外螺纹进行讨论。
梯形外螺纹的加工原理相对简单,即利用车床进行螺纹车削。
所谓梯形外螺纹是指螺纹牙的截面形状呈梯形,具体可以分为M型和MJ型两种。
梯形螺纹的主要参数有螺距、齿顶直径、齿根直径和螺纹锥度等,加工时需要根据给定的参数进行设置。
对于梯形外螺纹的加工,常用的方法有单刀片车削法、双刀片车削法和索引盘车削法。
下面将分别介绍这三种方法的特点和应用。
首先是单刀片车削法。
单刀片车削法适用于一些中等精度的螺纹加工,加工效率较高。
它的特点是只需要一把刀具即可完成整个螺纹的加工,节约了成本。
但是由于只有一把刀具,所以无法进行深孔加工,适用于螺纹长度较短的工件。
其次是双刀片车削法。
双刀片车削法适用于一些高精度和较长长度的梯形外螺纹加工。
它的特点是可以同时进行齿顶和齿根的车削,提高了加工精度。
双刀片车削法需要两把刀具同时进行切削,因此较单刀片车削法来说,加工效率相对较低。
最后是索引盘车削法。
索引盘车削法适用于批量生产的梯形外螺纹加工,加工效率较高。
它的特点是利用索引盘进行分度,每次轮转一个螺纹牙的角度,然后进行车削。
索引盘车削法适用于螺纹长度较长的工件,但是需要专门设计制作索引盘,成本较高。
对于车削梯形外螺纹的加工过程中,有几点需要特别注意。
首先是刀具的选用和磨削。
由于梯形外螺纹的牙形较复杂,所以刀具的要求较高,需要选择质量好、刚性强的刀具。
其次是加工过程中的刀具进给和主轴转速的选择。
进给过大会导致切削力过大,加工质量下降;主轴转速过高则会增加工件的热变形。
最后是加工润滑液的选择和使用,润滑液的作用是冷却刀具和工件,减少摩擦阻力。
车削梯形外螺纹是一种常用的机械加工方法。
通过合理选择加工方法和刀具,控制加工参数和加工工艺,可以获得高精度、高效率的梯形外螺纹加工。
梯形螺纹丝杆的加工方法

梯形螺纹丝杆的加工方法梯形螺纹丝杆在工业生产中被广泛应用,其制造工艺也非常重要。
下面,我们将分步骤介绍梯形螺纹丝杆的加工方法。
第一步:材料准备制造梯形螺纹丝杆需要钢材作为原材料。
常用的钢材包括45#、40Cr、35CrMo等。
在选择材料时,需要根据具体使用场景和性能做出合理的选择。
在选材后,需要将钢材切割、锤打等方式加工成适合加工的工件。
此外,还需要对工件进行物理理化测试,确定其机械性能和化学成分,以确保加工品质。
第二步:车削螺纹在进行梯形螺纹丝杆的加工时,需要用到车床。
工人可以根据需要的螺距和螺纹个数,在车床上制作螺纹。
具体步骤如下:首先,安装螺距刀头,进行初始调整。
其次,根据需要的螺距和螺纹个数进行车削。
可以手动或自动调节车床的进给。
最后,进行表面处理,去除落刀油和切削屑,并检查螺纹的尺寸是否符合要求。
如果有偏差,则需要重新调整或修正。
第三步:淬火车削完成后,需要对梯形螺纹丝杆进行淬火。
淬火是指将钢材加热至临界温度以上,然后通过快速冷却获得高硬度和强度。
具体步骤如下:首先,将工件放入淬火炉,并加热至适当温度。
其次,控制冷却介质的温度和速度。
常用介质包括水、油和气体等。
最后,进行回火处理。
回火是指将淬硬材料加热至适当温度后冷却,以软化材料的硬度。
具体温度和时间的选择应根据工件的材料、形状和用途决定。
第四步:加工细节处理在完成淬火后,梯形螺纹丝杆需要进行细节加工。
具体步骤如下:首先,进行磨削和抛光,使工件表面获得较高的平滑度和光洁度。
其次,进行螺纹表面处理,通常包括打磨和喷涂螺纹防锈漆等操作。
最后,进行质量检查,确保工件的尺寸、加工表面和表面光洁度符合标准。
综上所述,梯形螺纹丝杆的加工方法包括钢材材料准备、车削螺纹、淬火和加工细节处理。
这其中每一步都必须严格按照工艺要求执行,以确保产品的质量和使用效果。
梯形多线螺纹的加工方法
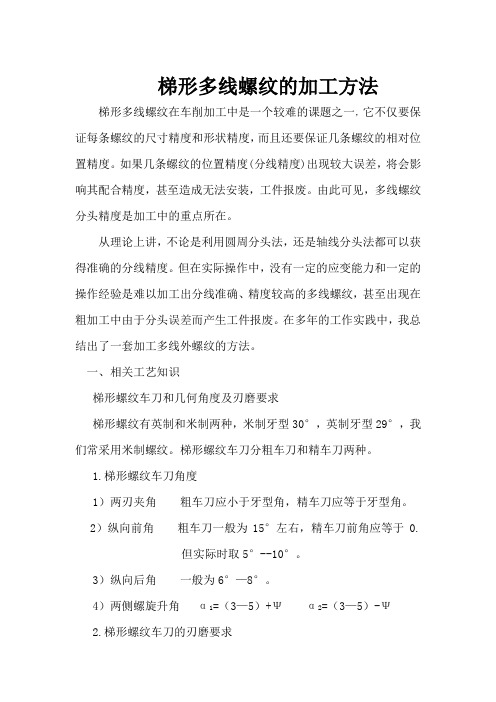
梯形多线螺纹的加工方法梯形多线螺纹在车削加工中是一个较难的课题之一,它不仅要保证每条螺纹的尺寸精度和形状精度,而且还要保证几条螺纹的相对位置精度。
如果几条螺纹的位置精度(分线精度)出现较大误差,将会影响其配合精度,甚至造成无法安装,工件报废。
由此可见,多线螺纹分头精度是加工中的重点所在。
从理论上讲,不论是利用圆周分头法,还是轴线分头法都可以获得准确的分线精度。
但在实际操作中,没有一定的应变能力和一定的操作经验是难以加工出分线准确、精度较高的多线螺纹,甚至出现在粗加工中由于分头误差而产生工件报废。
在多年的工作实践中,我总结出了一套加工多线外螺纹的方法。
一、相关工艺知识梯形螺纹车刀和几何角度及刃磨要求梯形螺纹有英制和米制两种,米制牙型30°,英制牙型29°,我们常采用米制螺纹。
梯形螺纹车刀分粗车刀和精车刀两种。
1.梯形螺纹车刀角度1)两刃夹角粗车刀应小于牙型角,精车刀应等于牙型角。
2)纵向前角粗车刀一般为15°左右,精车刀前角应等于0.但实际时取5°--10°。
3)纵向后角一般为6°—8°。
4)两侧螺旋升角α1=(3—5)+Ψα2=(3—5)-Ψ2.梯形螺纹车刀的刃磨要求1)用样板校对刃磨两刀刃夹角。
2)车刀刃口要光滑、平直、无虚刃,两侧副刀刃必须对称刀头不能歪斜。
3)用油石研磨去各刀刃的毛刺。
二、梯形多线螺纹的车削方法(以Tr36×12 P6为例)车削梯形螺纹与三角螺纹相比,螺距大、牙型角大、切削余量大、切削抗力大,而且精度要求高,加之工件一般都比较长,所以加工难度较大。
一般车削梯形螺纹我们用以下几种方法。
1.直进法即每一刀都在X向进给,直至牙底处。
采用此方法加工梯形螺纹时,螺纹车刀的三个切削刃都要参与切削,导致加工排屑艰苦,切削力和切削热增长,刀头磨损严重,容易产生“扎刀”和“崩刃”现象,因此这种方法不合适大螺距螺纹的加工。
数控车床梯形螺纹的加工方法及改进研究

科学技术创新2020.29梯形螺纹主要应用于传动机构中作为传导螺纹,梯形外螺纹与内螺纹以成对方式呈现,具有牙型深、螺距较大等特征,在采用数控车床进行加工时易产生较大的切削力与振动问题,加剧刀尖磨损程度、易引发扎刀事故,影响到工件的质量与加工生产进度。
基于此,本文拟针对梯形螺纹的常规加工工艺进行改进,并通过程序调试确保工艺具备可行性。
1梯形螺纹结构与加工方法1.1梯形螺纹。
1.1.1基本结构。
选取一对典型梯形螺纹副作为参照,在该梯形螺纹副的左上方、右上方分别设有螺杆和螺套,两类零件的外形、尺寸与螺纹精度将直接决定零件能否正常旋合。
以梯形螺纹Tr36×6为例(各结构的参数如表1所示),其牙型呈等腰梯形、牙型角为30°,相较于其他螺纹在牙根强度、对中性上占据良好性能优势,其公称直径为36mm 、螺距为6mm 。
左旋螺纹需在尺寸规格后加注“LH ”,右旋螺纹则不标出。
为保障梯形螺纹质量达标,应在加工环节确保牙型的准确度,使螺纹中径与基准轴保持同轴,以中径尺寸定心,在车削加工环节注意控制好中径的尺寸公差与两侧表面粗糙度[1]。
表1梯形螺纹的结构及计算公式1.1.2车刀材料。
在车刀材料选取上,主要选用硬质合金刀片进行梯形螺纹的高速车削,考虑到数控车床存在较严格的加工标准,因此选用材质为YT15硬质合金的可转位机夹刀片,保障刀片在硬度、耐磨性与使用寿命等方面具备良好的性能优势。
在车削加工环节,应注重选用标准刀片,在安装刀具时控制主切削刃与工件轴线保持等高且平行,利用样板进行找正与纠偏处理,使刀头角平分线与工件轴线呈垂直关系,并且将车削深度控制在与牙型高度一致的位置,确保中径尺寸达标。
1.2加工方法。
1.2.1直进法和斜进法。
直进法指车刀沿水平方向间歇进给至牙深部位,考虑到在车削梯形螺纹需利用车刀三刃同时切削,由此将产生较大的切削力、加剧刀具的磨损情况,并且无法保障及时排屑,易出现扎刀问题。
- 1、下载文档前请自行甄别文档内容的完整性,平台不提供额外的编辑、内容补充、找答案等附加服务。
- 2、"仅部分预览"的文档,不可在线预览部分如存在完整性等问题,可反馈申请退款(可完整预览的文档不适用该条件!)。
- 3、如文档侵犯您的权益,请联系客服反馈,我们会尽快为您处理(人工客服工作时间:9:00-18:30)。
一.传统车削方法的弊端
在教梯形螺纹和蜗杆的车削中,我们常用“直进法”和“左右切削法”,但这两种方法由于学生的接受能力有高低,因而产生了以下普遍的一系列问题:
1.“直进法”在车削中,车刀的左右两侧刀刃都参与切削,排屑比较困难,同时车刀所受的总切削力比较大,因此,车刀的受力和散热条件比较差,车刀容易磨损,当进刀量过大时还能产生“扎刀”,把牙形表面镂去一块,甚至于折断车刀。
2.左右切削法相对直进法而言,只有一侧刀刃参与切削,但不如直进法简单,牙形也不易边不易车的清晰,同时车刀受单向轴向切削分力的影响,将会增加大螺纹牙形的误差。
3.学生在使用“直进法”与“左右切削法“车削梯形螺纹和蜗杆的过程中,由于技术不够成熟,加上在切削过程中,切削量掌握不好,时大时小,没有一个恒定的进刀量,很容易造成车刀“烧怀”退火,另外,掌握不好加工余量的多少,容易在粗车的过程中就把螺纹的中径车小,成为废品。
二.“分层切削法”的原理
如图一,通过计算所要切削的槽宽,留光刀余量,在要所切削的槽宽行程内,通过一个合理的进刀比。
小拖板进刀量与中拖板进刀量的数量比,把需要切削掉的量,平均的分配到每一刀。
在小拖板与中拖板不断进刀,左右来回一层一层切削,最终形成一个30°或40°的梯形槽,从而切削出梯形螺纹或蜗杆。
(图一)
在梯形螺纹和蜗杆的车削过程中,要切削掉的是一个梯形槽。
梯形螺纹与蜗杆只不过在角度上有所区别,一个是30°,一个是40°,为了保证车刀不三面同时参与切削,要保证在所要切削掉的梯形槽内进行左右分层切削。
槽宽的计算公式可根据梯形螺纹与蜗杆的计算公式分别求出:
梯形螺纹槽宽= P – 0.366P
蜗杆的槽宽= P -0.843mx
梯形螺纹和蜗杆的轴向剖面形状是一个等腰梯形,而我们使用的车刀也是一个梯形成型刀。
如何使车刀沿这个等腰梯形的腰向下延伸,形成一个15°或20°的角呢?在这里就要运用三角函数算一个进刀比。
如图二,车刀的左进1mm车刀向下进多少才能形成一个15°的角,利用三角函数ctg15°=x/1,x = 3.75,进刀比为1:3.75,但是这个进刀比有小数,不是整数,在实际的操作中不方便,为了在实际的操作中方便简单,我们最好找一个整数比,在三角函数表中,我们发现ctg14°的比正好最接近整数,进刀比为1:4,沿着这
个进刀,做出的梯形槽的成形角在14°左右,双面成形角为28°多,正好有1°多一点的角度留给我们进行精车出30°的梯形槽。
(图二)
蜗杆的进刀比也按此方法在三角函数表中找ctg20°=x/1,x=2.74,进刀比为1:2.74,但不是整数比,ctg18°26‘所形成的对刀比为1:3,而且成形角为37°左右,还有几度角留给我们精车。
梯形螺纹小拖板与中拖板进刀比为1:4
蜗杆小拖板与中拖板进刀比1:3
算出进刀比后,根据要切削掉的余量,按进刀比,平均的分配到每一刀,从T40×6梯形螺纹为例,根据计算公式得出槽深就是牙高h3=0.5P+ac=3.5mm,根据梯形螺纹进刀比1:4。
如果小拖板进刀0.1mm,中拖板进刀深度为0.4mm。
需要9刀能进到3.5mm深。
左右来回18刀能切削出一个深3.5mm成形角为28°左右的梯形槽,但这个吃刀量太大,容易使车刀磨损。
我们把吃刀量缩小一倍,小拖板进0.05mm,中拖板进0.2mm,这样就需要18刀才能进刀3.5mm深,左右来回得36刀能形成一个28°左右的梯形槽,另外6140车床小拖板一格为0.05mm,中拖板一格为0.05mm,这样小拖板进一格0.05mm,中拖板进4格为0.2mm,正好跟进刀比1:4一样。
蜗杆的分层按1:3的进刀比,根据公式算出槽深进形分层计算。
在梯形螺纹与蜗杆的“分层切削”中,需算出车刀刀头的宽度,其宽度应比牙槽底宽小,在实际的操作过程中,为保证车刀不三面同时参与切削,在开头的几刀车削中,需在槽宽中间进行几次“赶刀”。
另外在车削过程中,一定要牢记小拖板与中拖板的刻度。
附图一,T=6梯形螺纹的左右分层切削图
(附图一)
附图二,m=2的蜗杆左右分层切削图
(附图二)
结论
本人在实际的教育实习中,把学生分为两组。
一组使用传统切削方法,另一组使用“分层切削法”切削T45×的梯形螺纹进行对比,发现使用“分层切削法”的一组。
在切削速度上明显要比另一组快。
在车刀的磨损上,明显没有另一组快,在螺纹的中径尺寸上,没有一个做坏,而另一组有几个同学做坏。
通过传授这种方法,学生普遍反映这种方法比传统方法简单、方便、容易掌握。
事实证明这种方法,综合了传统各种切削方法的优点,使学生在梯形螺纹和蜗杆的切削中,每一刀都格式化,机械化,由其在内螺纹的车削中更加体现出此种方法,不容易“扎刀”不容易断刀,方便简单的特点。
所以在技校的教育实习中,在车削梯形螺纹与蜗杆的过程中,应大力推广这种机床厂几位老师傅所发明的优秀的切削方法。