金相试样抛光机操作规程1
【管理精品】金相试样抛光机操作规程

【管理精品】金相试样抛光机操作规程金相试样抛光机操作规程一、操作规程1、取下盖、罩、套圈和抛光盘。
2、把湿润後的抛光织物张在抛光盘上,再将套圈套入,使织物紧紧地罩在抛光盘上。
3、将装了织物的抛光盘,对准锥套上的螺钉,将抛光盘套在锥套上。
将罩紧压在盘上。
4、将插头插入电源插座,开动开关即可进行抛光工作。
二、注意事项1、在装有织物的抛光盘在套入之前应进行清洁及涂油的工作2、使用时不允许对试样施加过大的压力,以免电机过载,而损坏电机。
3、不允许使用以坏的抛光织物,织物应紧张在抛光盘上。
4、由于机器部分零件,采用聚氯乙稀硬板压制而成,低温时脆性较大,在低于,3?时工作应特别注意。
5、本机经长期使用后,应及时更换电机的润滑油。
金相试样切割机操作规程1、准备工作1.1、接通进水管1.2、将插头插入电源插座,启动电机检查电机轴的旋转方向,轴旋转方向应按顺时针转动。
2、砂轮片拆卸及更换:2.1、将罩壳上的螺丝松下,取下罩壳。
2.2、旋处流水盘上的螺丝,取下流水盘。
2.3、将扳手开口处嵌入轴套的两平面上,一端搁在底座的前端。
2.4、用另一扳手逐个旋下夹紧螺母,取下砂轮片。
2.5、按照相反方法把砂轮片装上,在砂轮片的两侧应垫上两张厚纸片做成的垫片。
2.6新装的砂轮片应先空转一段时间,以保证安全工作。
3、试验的装夹:3.1、用撑板支持锯架使其不下落。
3.2、将试样放在锯架钳口的前面。
3.3、顺时针方向转动手柄,夹紧试样。
4、试样的切割:4.1、用右手将手柄抬起一些,左手将撑板向下压,使撑板前端越过流水盘上支点高度,右手握住手柄使试样逐渐接近砂轮片。
4.2、调节旋钮和冷却管,使冷却液流的方向及大小适合于切割的要求。
4.3、切割时,一定要使水流对准试样的切割位置,保持均匀进给。
4.4、切割完毕将锯架抬起到一定高度,撑板会自动落下顶住锯架,这时可以取下试样。
5、注意事项:5.1、严禁使用有裂纹的砂轮片。
5.2、不能在没冷却或冷却不充分情况下工作。
金相试样磨抛机安全操作规程

设备名称
金相试样磨抛机
设备编号
xx-xx-xx
文件编号
xx-xx-xx
所属部门
设备科
使用部门
质量部
版本
第一版
一、目的:
为了提升员工的安全防范意识,实现过程管理的可操作性及可控性,操作人员上机前必须仔细阅读安全操作规程并严格遵守。
二、作规程:
1、调节水阀旋钮让水不停地注入磨盘,但水量不宜过大,只需连续不断地流入即可;
7、磨抛机双盘可以同时使用,放入两种不同粗细的砂纸,由粗至细连续进行磨光,效率及质量均佳;
8、不要使用过钝的砂纸,否则既降低磨光效率又会使试样变形层增厚,影响试样质量;
9、本机使用的砂纸以水砂最为合适。
三、注意事项
1、不允许使用已破损的砂纸,以免影响磨光时的安全;
2、及时清除盘中的沉积物以利排水通畅,不使用时应及时盖好塑料盖;
3、长期使用后应及时更换轴承的润滑脂;
4、本机部分零件,采用硬塑料制成,低温时脆性较大,故在低于-3℃时工作应特别注意,以免损坏。
监督人:维护责任人:
批准人/日期
审核人/日期
编制人/日期
2、磨盘注入适量水后,即可放入砂纸;
3、接通开关磨盘旋转后,砂纸即可自动被吸住,这时就可进行磨光工作,但是在操作过程中不允许对试样加过大压力,以免电动机过载而损坏电动机;
4、M-2C是由转向开关来实现调速功能;
5、为了磨光效率,试样粗磨时先应在砂轮上打平;
6、停止使用时磨盘内要注满清水,使砂纸浸在水中,否则会使砂纸翘起影响下次的使用;
金相抛光机操作保养指导书

金相抛光机操作保养指导书
1.主要用途:
适用于金相试样的抛光,使金相试样表面达到后序工作要求。
2.型号及种类:
2.1 MODEL: PG-2
2.2 品牌:上海金相
3.调机操作:
3.1 把抛光机置在平整的平面上.
3.2 取下盖、罩、套圈及抛光盘。
3.3 把润湿后的抛光织物装在抛光盘上,再将套圈套入,应使织物紧贴在抛光盘上。
3.4装上抛光织物的抛光盘,对准锥套上的螺丝,就可套在锥套上,套入时应进行清洁
及涂油工作。
3.5 将罩紧压在盘内。
3.6在排水管出口放置一个容器,使废液排出。
3.7插入电源,打开开关,打开水源开关,把要抛光的试验件平稳放在抛光机上抛光。
4.维护和保养:
4.1使用时不允许对试样加大压力,以免损坏电动机。
4.2 电动机最高温度升为80℃。
4.3抛光织物应紧贴在抛光盘上,不允许使用已破坏的织物。
4.4对织物进行抛光时要放水进行清洗及降温,清洗后的废水安装管道进行清除。
4.5电源可靠的接地装置。
4.6 电动机的润滑脂每一年更换一次。
变频金相研磨抛光机安全操作及保养规程
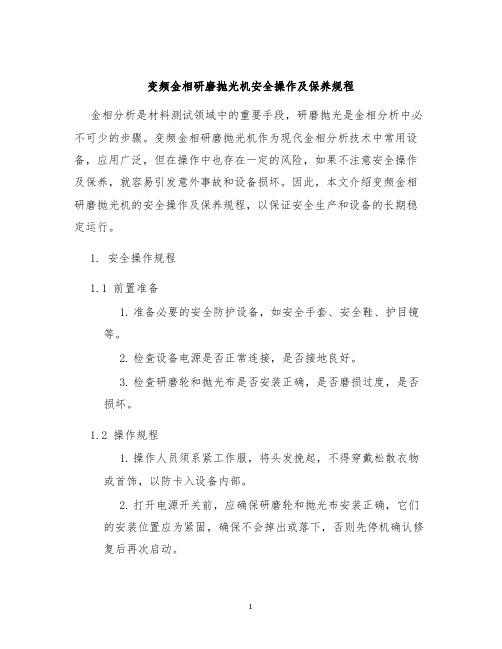
变频金相研磨抛光机安全操作及保养规程金相分析是材料测试领域中的重要手段,研磨抛光是金相分析中必不可少的步骤。
变频金相研磨抛光机作为现代金相分析技术中常用设备,应用广泛,但在操作中也存在一定的风险,如果不注意安全操作及保养,就容易引发意外事故和设备损坏。
因此,本文介绍变频金相研磨抛光机的安全操作及保养规程,以保证安全生产和设备的长期稳定运行。
1. 安全操作规程1.1 前置准备1.准备必要的安全防护设备,如安全手套、安全鞋、护目镜等。
2.检查设备电源是否正常连接,是否接地良好。
3.检查研磨轮和抛光布是否安装正确,是否磨损过度,是否损坏。
1.2 操作规程1.操作人员须系紧工作服,将头发挽起,不得穿戴松散衣物或首饰,以防卡入设备内部。
2.打开电源开关前,应确保研磨轮和抛光布安装正确,它们的安装位置应为紧固,确保不会掉出或落下,否则先停机确认修复后再次启动。
3.操作时,双手应握住操作手柄,才可打开操作开关进行操作,一手握持锁扣,另一手才可握柄。
使用手柄时,操作人员应明确方向和力度,以免造成事故或设备损伤。
4.研磨和抛光时,为了避免研磨轮、抛光布和样品间发生相互阻挡和碰撞,应先将样品固定稳定,切忌在相互作用的过程中进行力度过大或过度推挤样品操作。
5.在操作过程中,如遇到电源异常、切削异常、机器发生异响等异常情况,应立即停机,检查。
如情况严重,需停止使用后联系机器维修人员进行维护,恢复正常操作状态。
1.3 停机后的操作1.停止操作后,应立即关闭设备电源开关。
2.清理工作区域,并清洁设备表面,防止灰尘、脏物附着或损伤。
3.卸下研磨轮和抛光布,清洁并妥善存放,以免受损和过度磨损,影响下一次使用。
2. 保养规程2.1 设备保养1.定期清理设备表面、滚轴、传动部分等,使用低压空气枪等非腐蚀性工业气体将残留的金属颗粒、氧化物等污垢清除干净。
2.定期检查设备传动部分润滑情况,适当加注微量润滑剂,防止传动部分磨损。
3.定期检查设备电源线,保证接地和外部绝缘状态,以免发生漏电、起火等安全事故。
金相试验操作规程
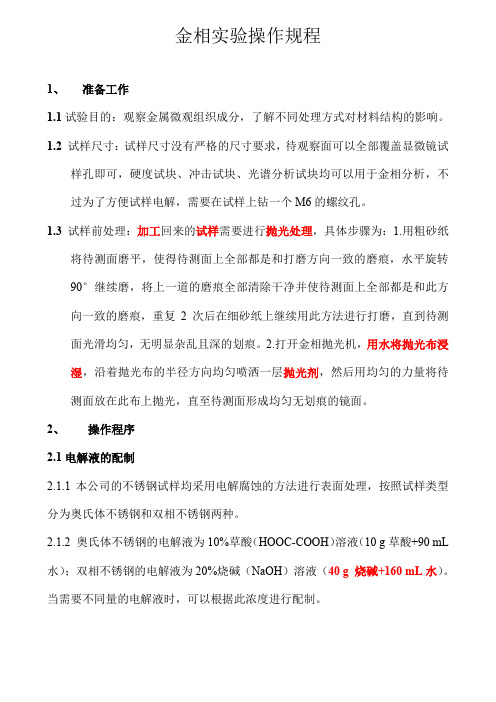
1、准备工作1.1试验目的:观察金属微观组织成分,了解不同处理方式对材料结构的影响。
1.2试样尺寸:试样尺寸没有严格的尺寸要求,待观察面可以全部覆盖显微镜试样孔即可,硬度试块、冲击试块、光谱分析试块均可以用于金相分析,不过为了方便试样电解,需要在试样上钻一个M6的螺纹孔。
1.3 试样前处理:加工回来的试样需要进行抛光处理,具体步骤为:1.用粗砂纸将待测面磨平,使得待测面上全部都是和打磨方向一致的磨痕,水平旋转90°继续磨,将上一道的磨痕全部清除干净并使待测面上全部都是和此方向一致的磨痕,重复2次后在细砂纸上继续用此方法进行打磨,直到待测面光滑均匀,无明显杂乱且深的划痕。
2.打开金相抛光机,用水将抛光布浸湿,沿着抛光布的半径方向均匀喷洒一层抛光剂,然后用均匀的力量将待测面放在此布上抛光,直至待测面形成均匀无划痕的镜面。
2、操作程序2.1电解液的配制2.1.1本公司的不锈钢试样均采用电解腐蚀的方法进行表面处理,按照试样类型分为奥氏体不锈钢和双相不锈钢两种。
2.1.2 奥氏体不锈钢的电解液为10%草酸(HOOC-COOH)溶液(10 g草酸+90 mL 水);双相不锈钢的电解液为20%烧碱(NaOH)溶液(40 g 烧碱+160 mL水)。
当需要不同量的电解液时,可以根据此浓度进行配制。
2.2 腐蚀2.2.1 将一定量的电解液装入烧杯中,把试样安装在M6的螺栓上作为阳极,放入电解液中,要求电解液完全没过试样,形成双电极电解系统(另外一边阴极为普通不锈钢)。
2.2.2将此电解系统接入到恒流电源上,正极(+)接阳极(即试样所在的电极),负极(-)接阴极(普通不锈钢所在的电极)。
2.2.3打开恒流电源,慢慢调节电流至工艺要求值,保持一定时间后将电流调回至零,关闭恒流电源后即可将试样取出清洗。
2.2.4奥氏体不锈钢电解参数:4V,55-65s;双相不锈钢电解参数:4V,25-35s(注意时间太久会过腐蚀)。
金相抛光步骤

金相抛光步骤
金相试件抛光步骤
1、打开抛光机,打开水管,水流至砂纸2/3处,在100目的砂纸
上进行抛磨,直至试件抛磨表面没有明显变化,更换至200目、400目、800目、1200目进行相同操作。
2、在1200目砂纸上操作完成后,将试件放到绒布上进行操作,
操作如下:打开水管将绒布浸湿,用刷子将绒布表面清理,关闭水管,喷涂金相抛光膏0.5S,将试件金相抛光至镜面。
3、试件表面甩干,放置于金相显微镜上观察有无划痕,若有重新
进行绒布抛光,若没有则进行第4步。
4、将抛光好的试件表面略倾,滴加4%硝酸酒精,旋转试件使液
体在抛好的表面全部覆盖,试件表面发雾,持续2~3秒,用流水将硝酸酒精冲洗干净,用吹风机将试件表面吹干。
全国大学生金相技能大赛制样通用操作规程

全国大学生金相技能大赛制样通用操作规程本操作规程针对全国大学生金相技能大赛比赛金相试样制样和显微组织观察而订,也可供日常金相实验教学参考使用。
一、手工预磨操作规程1. 在正式磨样前,清理工作台面的灰尘或磨料颗粒,以免影响磨样质量。
将砂纸放置合适位置 (建议如图1所示摆放,未使用的砂纸从上到下按照从细到粗的顺序叠放)。
2. 样品无标记面为磨制面。
磨制面边缘无倒角的需先行倒角 [ (0.5 ~ 1) mm 45o ,手工、机磨均可]。
3. 在砂纸上将试样的磨制面朝下,一手按住砂纸,一手握住试样 (建议用大拇指、食指和中指捏持试样),略加压力后将试样紧贴砂纸朝前推至砂纸上部边缘 (图2a,b),然后将试样提起并返回到起始位置(图2c, d ),再进行第二次磨制。
如此反复进行直至磨制面平整且磨痕方向一致为止。
在这一操作过程中,每一次后移 (返回) 也可不将试样提起,即往返过程试样均与砂纸接触。
4. 依次换上从粗到细牌号砂纸进行手工磨制。
每更换一道砂纸,试样转一个角度使上道次的磨痕与本道次的磨痕方向垂直。
每道次磨制以磨面平整、磨痕方向一致、且覆盖上道次磨痕为止。
建议在更换砂纸前用水冲、纸巾擦拭等方式清洁试样磨制面,避免把上道次磨屑颗粒 (粗) 带入下次道金相砂纸上 (细)。
5. 重复3 ~ 4步骤直至最细号砂纸。
6. 建议在更换砂纸的过程中将玻璃板打扫干净,以免前面的粗砂粒留在玻璃板上,造成后面的细磨难于完成。
7. 预磨工序结束后,清理工作台面并整齐摆放砂纸。
二、机械预磨操作规程1. 在正式磨样前,清理工作台面的灰尘或磨料颗粒,以免影响磨样质量。
将砂纸放置合适位置 (建议如图1所示摆放,未使用的砂纸从上到下按照从细到粗的顺序叠放)。
2. 检查预磨机启停、运转等情况,了解预磨机转动方向 (一般为逆时针方向),检查操作工位,消除安全隐患。
图1 磨样工位及砂纸摆放顺序示意图 图2 手工金相磨制手法示意图3. 将水磨砂纸浸湿后平放在研磨盘中。
金相抛光机操作方法
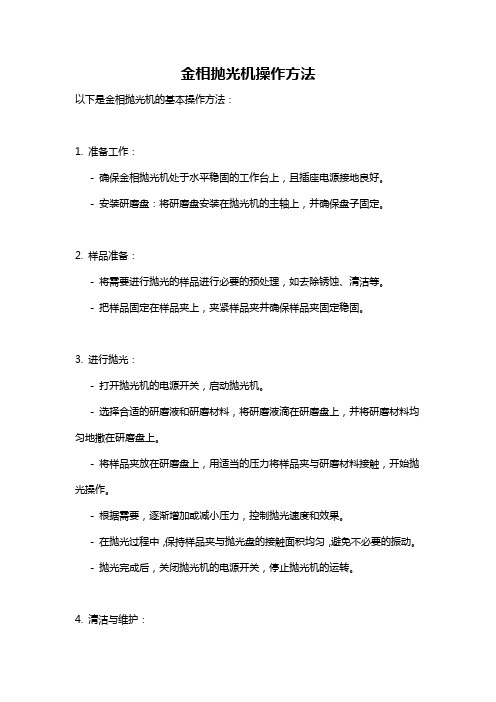
金相抛光机操作方法
以下是金相抛光机的基本操作方法:
1. 准备工作:
- 确保金相抛光机处于水平稳固的工作台上,且插座电源接地良好。
- 安装研磨盘:将研磨盘安装在抛光机的主轴上,并确保盘子固定。
2. 样品准备:
- 将需要进行抛光的样品进行必要的预处理,如去除锈蚀、清洁等。
- 把样品固定在样品夹上,夹紧样品夹并确保样品夹固定稳固。
3. 进行抛光:
- 打开抛光机的电源开关,启动抛光机。
- 选择合适的研磨液和研磨材料,将研磨液滴在研磨盘上,并将研磨材料均匀地撒在研磨盘上。
- 将样品夹放在研磨盘上,用适当的压力将样品夹与研磨材料接触,开始抛光操作。
- 根据需要,逐渐增加或减小压力,控制抛光速度和效果。
- 在抛光过程中,保持样品夹与抛光盘的接触面积均匀,避免不必要的振动。
- 抛光完成后,关闭抛光机的电源开关,停止抛光机的运转。
4. 清洁与维护:
- 清洁抛光盘和抛光机设备,清除研磨材料和研磨液的残留物。
- 定期检查抛光机的各个部件,确保设备正常工作。
- 如遇到故障或异常情况,及时停机并联系维修人员进行检修。
- 1、下载文档前请自行甄别文档内容的完整性,平台不提供额外的编辑、内容补充、找答案等附加服务。
- 2、"仅部分预览"的文档,不可在线预览部分如存在完整性等问题,可反馈申请退款(可完整预览的文档不适用该条件!)。
- 3、如文档侵犯您的权益,请联系客服反馈,我们会尽快为您处理(人工客服工作时间:9:00-18:30)。
P-1金相试样抛光机操作规程
一、准备工作
1、检查机器是否放在平整的工作台上;各部分零件是否齐全,紧固件是否有松动现象,做好清洁工作。
2、在排水管出口处放置容器或将排水管通向排水口,使废液排出;
3、检查电源是否满足工作要求(电源380V、50Hz、200W),各线路的连接及接地是否安全可靠。
二、操作
1、将织物粘贴在抛光盘上,在粘贴时必须每次先在盘面上涂上少量机油,以利再次更换织物的方便。
2、将罩紧压在盘内,并在织物表面滴上适量的抛光液或抛光膏和水。
3、将电源插头插入电源插座,将电源开关旋至“开”的位置,电动机启动,就可以进行抛光工作。
4、抛光时,要一边加水一边抛光。
5、抛光完毕,应切断电源。
三、维护与保养
1、使用时不允许对试样加过大压力,以免电动机过载而致其损坏或撕裂织物。
2、电动机最高温升为80℃。
3、电源插座的接地装置应十分可靠。
4、本机部分零件,采用硬塑料制成,低温时脆性较大,故在低于-10℃时工作,应特别注意,以免损坏。
5、抛光织物应紧贴在抛光盘上,不允许使用已破损的织物,以免在抛光时试样有飞出的危险。
6、本机不使用时应及时做好清洁保养工作,盖上塑料盖以免灰尘或其它异物落入抛光织物上而影响以后的抛光效果
7、本机长期使用后,应及时更换电动机轴承内润滑油。
-------------------------------------------------------------------------批准:审核:编制:。