焦化厂焦炉煤气一级加氢转化、一级脱硫工艺分析与设计技术实施方案
焦化厂脱硫工艺流程

焦化厂脱硫工艺流程一、背景介绍焦化厂是一种能源生产企业,其主要产品为焦炭和煤气。
但是,焦化过程中会产生大量的二氧化硫等有害气体,对环境和人体健康造成威胁。
因此,在焦化厂中必须采取脱硫措施。
二、脱硫工艺分类目前,常用的焦化厂脱硫工艺主要包括湿法脱硫法和干法脱硫法两种。
三、湿法脱硫工艺流程1. 燃烧前处理:将原料煤进行粉碎、筛分等处理,以提高其燃烧效率。
2. 燃烧过程:将经过预处理的原料煤放入高温反应器中进行燃烧,产生大量二氧化硫等有害气体。
3. 熄火后处理:将产生的废气通过喷淋装置喷洒液体吸收剂(如碳酸钠溶液),使其中的二氧化硫被吸收。
4. 液体再生:将吸收剂中所含有的二氧化碳等物质去除,并将其回收再利用。
5. 废水处理:将吸收剂中所含有的废水进行处理,以达到排放标准。
四、干法脱硫工艺流程1. 燃烧前处理:同湿法脱硫工艺。
2. 燃烧过程:同湿法脱硫工艺。
3. 干法脱硫:将产生的废气通过干式吸附剂(如活性炭、氧化钙等)进行吸附,使其中的二氧化硫被吸附。
4. 再生:将已经饱和的吸附剂进行再生,以去除其中的二氧化硫等物质,并回收再利用。
5. 废物处理:将已经使用过的吸附剂进行处理,以达到排放标准。
五、两种工艺比较1. 湿法脱硫工艺具有脱除效率高、适应性强等优点,但是会产生大量废水和废渣,需要进行额外的处理。
2. 干法脱硫工艺具有节能、环保等优点,但是其脱除效率相对较低。
六、结论在选择焦化厂脱硫工艺时,需要根据实际情况进行综合考虑,选择适合自己企业的工艺。
同时,需要加强废水、废渣等废物的处理,以达到环保标准。
焦化化产车间焦炉煤气的脱硫工艺及优化改造

焦化化产车间焦炉煤气的脱硫工艺及优化改造【摘要】:本论文旨在研究焦化化产车间焦炉煤气的脱硫工艺及其优化改造。
详细分析了目前常用的脱硫工艺,包括湿法脱硫、干法脱硫,并对它们的原理、特点和工艺进行了比较,表明了MEA法+氧化铁法干法脱硫工艺具有流程短、方法简单、环保效益显著、经济效益好等特点。
针对焦炉煤气脱硫存在的问题,提出了一系列的优化改造方案,包括工艺改进、设备升级和运行管理等方面。
希望可以通过本文的研究,促进生产工艺的发展和进步。
【关键词】:焦化焦炉煤气;脱硫工艺;优化改造引言焦炉煤气脱硫是化产车间的重要作用之一。
因焦炉煤气中含有硫化氢、氰化氢等杂质,对煤气净化设备及煤气输送设施造成严重腐蚀,因H2S在燃烧后产生的SO2会造成烟气SO2超标,因此,必须对焦炉煤气进行脱硫。
焦炉煤气脱硫不仅可以提高煤气质量,还可以有效降低对环境的伤害。
对焦炉煤气进行脱硫工艺的研究和优化改造,实现车间的清洁生产、减少污染物排放、提高环境质量具有重要的现实意义和应用价值。
1、焦化厂焦炉煤气脱硫工艺分析1.1湿法脱硫工艺焦炉煤气中的硫化物主要包括硫化氢(H2S)和氰化氢(HCN)。
脱硫的目的是减少硫化物对环境和设备的腐蚀作用,保护环境和提高设备的使用寿命。
湿法脱硫工艺是指在脱硫过程中使用液体吸收剂与煤气直接进行接触,将硫化物溶解或转化为易于处理的形式。
湿法脱硫工艺有HPF 法、TH 法、FRC 法、改良ADA 法、AS法、真空碳酸钾法、MEA法等。
AS法、HPF法、真空碳酸钾法和MEA法脱硫最为常用。
1.1.1 常用湿法脱硫工艺原理AS法煤气脱硫工艺是以焦炉煤气中的氨为碱源,用洗氨后的富氨水吸收煤气中的硫化氢;HPF法脱硫工艺是以煤气中的氨为碱源、HPF为催化剂来脱除煤气中的硫化氢;真空碳酸钾法煤气脱硫是利用碳酸钾溶液吸收焦炉煤气中的硫化氢和氰化氢;MEA法脱硫工艺是采用15%的MEA溶液与焦炉煤气逆向接触,吸收煤气中的H2S、HCN等气体,之后焦炉煤气从吸收塔顶排出。
焦化厂脱硫脱销工程方案

焦化厂脱硫脱销工程方案一、前言随着环境保护意识的不断提高和环境监管政策的日益严格,各类工业企业纷纷加大对废气、废水、废渣等废物的治理力度,焦化厂作为一个重要的重工业企业,其生产中排放的废气中含有大量的二氧化硫和颗粒物等有害物质,对环境造成了严重的污染。
为了减少这些有害物质对环境的影响,降低其排放浓度,保护环境,必须进行脱硫脱销处理。
因此,本方案旨在设计一套适合焦化厂的脱硫脱销工程方案,以满足环保要求,提高企业的环保形象。
二、现状分析在燃料燃烧过程中,产生的不完全燃烧和硫化物等物质,是造成大气污染的主要原因之一。
目前,我国焦化企业的脱硫脱销措施主要是采用喷淋塔、活性炭吸附等方法进行处理。
然而,这些方法存在成本高、处理效率低、难以运维等问题。
必须有一种更加高效、成本更低的方法去替代。
三、目标1. 降低焦化厂废气中二氧化硫排放含量,符合国家排放标准。
2. 降低焦化厂废气中颗粒物排放含量,符合国家排放标准。
四、脱硫脱销工程方案设计1. 技术选型在脱硫脱销工程的设计中,需要选择合适的脱硫脱销设备。
本工程将采用湿法脱硫技术和布袋除尘技术,结合吸附剂进行脱硫脱销处理。
湿法脱硫是目前应用最广泛的脱硫技术之一,其原理是将燃料燃烧后产生的含硫烟气与氧化剂和水反应生成硫酸溶液,再通过降温、粉尘分离和脱水处理等流程得到脱硫后的烟气。
布袋除尘技术是通过在烟气通道中设置滤袋,将含尘烟气通过布袋,在滤袋上堆积下来。
当布袋上的尘埃多了后,即可通过清灰系统进行清灰,使布袋除尘器能够恢复除尘的工作。
2. 工艺流程(1)烟气预处理首先应对燃料进行预处理,采用低硫煤或者其他无硫燃烧,减少燃烧后烟气中的二氧化硫排放。
同时还需要对烟气进行预处理,通过除尘工程,减少颗粒物的排放。
对与处理后的烟气需要经过冷凝、洗涤等过程,降低烟气温度,并去除大部分的颗粒物和部分的二氧化硫。
(2)脱硫工程脱硫工程采用湿法脱硫技术,运用氧化剂与含硫烟气进行反应,产生大量的二氧化硫并与氢氧化物生成硫酸。
煤化工(焦化厂)焦炉煤气6大脱硫技术详解与脱硫工艺选择
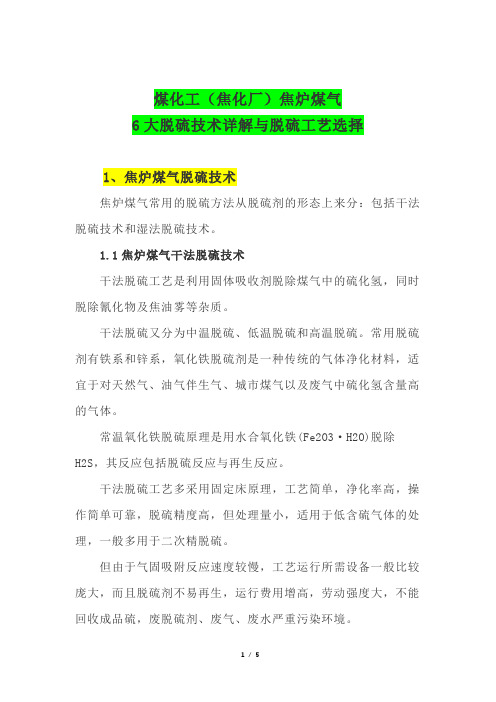
煤化工(焦化厂)焦炉煤气6大脱硫技术详解与脱硫工艺选择1、焦炉煤气脱硫技术焦炉煤气常用的脱硫方法从脱硫剂的形态上来分:包括干法脱硫技术和湿法脱硫技术。
1.1焦炉煤气干法脱硫技术干法脱硫工艺是利用固体吸收剂脱除煤气中的硫化氢,同时脱除氰化物及焦油雾等杂质。
干法脱硫又分为中温脱硫、低温脱硫和高温脱硫。
常用脱硫剂有铁系和锌系,氧化铁脱硫剂是一种传统的气体净化材料,适宜于对天然气、油气伴生气、城市煤气以及废气中硫化氢含量高的气体。
常温氧化铁脱硫原理是用水合氧化铁(Fe2O3·H2O)脱除H2S,其反应包括脱硫反应与再生反应。
干法脱硫工艺多采用固定床原理,工艺简单,净化率高,操作简单可靠,脱硫精度高,但处理量小,适用于低含硫气体的处理,一般多用于二次精脱硫。
但由于气固吸附反应速度较慢,工艺运行所需设备一般比较庞大,而且脱硫剂不易再生,运行费用增高,劳动强度大,不能回收成品硫,废脱硫剂、废气、废水严重污染环境。
1.2焦炉煤气湿法脱硫技术湿法工艺是利用液体脱硫剂脱除煤气中的硫化氢和氰化氢。
常用的方法有氨水法、单乙醇胺法、砷碱法、VASC脱硫法、改良 ADA法、TH 法、苦味酸法、对苯二酚法、HPF 法以及一些新兴的工艺方法等。
1.2.1 氨水法(AS法):氨水法脱硫是利用焦炉煤气中的氨,在脱硫塔顶喷洒氨水溶液(利用洗氨溶液)吸收煤气中 H2S,富含 H2S 和 NH3的液体经脱酸蒸氨后再循环洗氨脱硫。
在脱硫塔内发生的氨水与硫化氢的反应是:H2S+2NH3·H2O →(NH4)2S+2H2O。
AS 循环脱硫工艺为粗脱硫,操作费用低,脱硫效率在 90 %以上,脱硫后煤气中的 H2S 在200~500 mg·m-3。
1.2.2 VASC法:VASC法脱硫过程是洗苯塔后的煤气进入脱硫塔,塔内填充聚丙烯填料,煤气自下而上流经各填料段与碳酸钾溶液逆流接触,再经塔顶捕雾器出塔。
煤气中的大部分 H2S 和 HCN 和部分 CO2被碱液吸收,碱液一般主要是 Na2CO3或 K2CO3溶液。
焦炉煤气脱硫工艺分析与优化

焦炉煤气脱硫工艺分析与优化摘要:随着工业化进程的加快,大量的焦炉煤气被排放到大气中,其中含有大量的二氧化硫等有害气体,对环境和人类健康造成了严重的影响。
因此,煤气脱硫技术的研究和应用变得越来越重要。
关键词:焦炉煤气;脱硫;工艺优化1常用焦炉煤气脱硫的工艺1.1HPF法脱硫工艺HPF法脱硫工艺是一种常用的焦炉煤气脱硫方法,其全称为高压催化氧化法脱硫工艺。
该工艺主要通过高压催化氧化反应将煤气中的硫化氢转化为硫酸,从而达到脱硫的目的。
HPF法脱硫工艺的主要步骤包括:煤气预处理、催化氧化反应、吸收塔脱硫和尾气处理等。
具体来说,煤气预处理主要是通过除尘、除水和降温等措施,将煤气中的杂质去除,为后续的催化氧化反应提供良好的条件。
催化氧化反应则是将煤气中的硫化氢与氧气在高压催化剂的作用下进行反应,生成硫酸。
吸收塔脱硫则是将催化氧化反应后的煤气通过吸收塔进行吸收,将硫酸吸收下来,从而实现脱硫。
尾气处理则是将吸收塔中的尾气进行处理,将其中的二氧化硫等有害物质去除,达到环保要求。
该工艺具有脱硫效率高、操作简单、设备投资少等优点,因此在焦化、化工等行业得到广泛应用。
但是,该工艺也存在一些缺点,如催化剂易失活、催化剂寿命短、对煤气中的氧气要求高等,需要在实际应用中加以注意。
1.2湿法脱硫湿法脱硫是一种常见的焦炉煤气脱硫工艺,其主要原理是利用化学反应将煤气中的二氧化硫转化为硫酸盐(如CaSO3、CaSO4等)或硫酸,从而达到脱硫的目的。
湿法脱硫的主要步骤包括:喷雾吸收、氧化还原、沉淀和过滤等。
首先,将煤气通过喷雾器喷入吸收液中,吸收液通常是一种碱性溶液,如氢氧化钠或碳酸钠溶液。
煤气中的SO2会与吸收液中的碱性物质发生反应,生成硫代硫酸盐或硫酸。
接着,将生成的硫代硫酸盐或硫酸通过氧化还原反应转化为硫酸盐。
这一步通常需要加入一些氧化剂,如氯化钙或过氧化氢,使硫代硫酸盐或硫酸被氧化为硫酸盐或硫酸。
然后,将生成的硫酸盐通过沉淀反应沉淀下来。
焦化厂焦炉煤气脱硫工段的设计(1)

本科生毕业设计100万吨/年焦化厂焦炉煤气脱硫工段的设计摘要本设计为100万t/a焦化厂焦炉煤气脱硫工段的设计,采用的煤气脱硫方法为湿法脱硫的改良A.D.A.法。
本设计的主要任务是脱除焦炉煤气中的硫化氢,同时要使生产出来的煤气各项指标能满足要求,达到民用煤气的标准。
设计的主要内容包括:1、煤气脱硫方法的概述和意义;2、工艺流程的选择与论证,选用改良A.D.A法;3、主要设备的计算、选型和布置;4、保障生产正常进行所必须的非工艺部分,包括供水、供电、采暖、设备维修、仪表自动化等;5、经济核算,每生产一吨焦炭该设计工段亏损7.0元。
本设计的工艺部分包括煤气脱硫和脱硫液再生以及硫磺回收。
脱硫采用了脱硫塔,再生部分用再生塔,对于其基本原理,文中有着详细的论述,回收硫部分采用了真空过滤机。
在设计过程中,参考了焦化厂的焦炉煤气净化工艺,并在其基础上将国内外一些新的、成熟的工艺进行了比较、引用。
关键词:焦炉煤气;脱硫;改良A.D.A法AbstractThis is a design of 100 million t / a coking plant coke oven gas desulfurization section, the method for gas desulfurization is the improved ADA law. The main task of this design is the removal of hydrogen sulfide in coke oven gas, and the gas produced to make the indicators to meet the requirements, to civilian gas standards, at the same time.The main contents of the design are as follows:1, an overview of gas desulphurization and significance. 2, the process of selection and demonstration,select the improved of ADA Act. 3, the calculation, selection and arrangement of major equipment. 4, the security necessary for normal production of non-technology components, including water, electricity, heating, equipment maintenance, instrumentation and automation.5, the economic accounting, produce 1 ton of coke necessary to loss of 7.1442 yuan.Part of the design process including gas desulfurization and regeneration of the desulfurization solution and sulfur recovery. In zhe deign, part of desulfurization the desulfurization tower is used, recycled parts recycled tower is used. For the basic principles, the paper has a detailed discussion. Part of sulfur recovery the vacuum filter is used.In the design process, with reference to the coking plant in Xuzhou Universe coke oven gas purification process, and on its basis , compared the home and abroad new, mature technology, and references.Key words: coke oven gas; desulfurization; improved ADA Act目录1 总论 (1)1.1 焦炉煤气脱硫的目的和意义 (1)1.2 硫化氢的性质 (1)1.5 厂址的选择 (2)1.5.1 地理条件 (3)1.5.2 资源条件 (3)1.5.3 供排水条件 (3)1.5.4 交通运输条件 (3)1.5.5 经济条件 (3)1.5.6 气候条件 (3)2 脱硫工艺论证及确定 (3)2.1 脱硫方法概述 (3)2.1.1 干法脱硫 (3)2.1.2 湿法脱硫 (3)2.2 脱硫工艺的确定 (10)2.2.1 脱硫工艺的选择 (10)2.2.2 脱硫工艺的优化 (11)3 改良A.D.A法脱硫工艺流程及操作 (11)3.1 脱硫工艺流程 (12)3.2 影响碱液对硫化氢吸收速度的因素 (13)3.3 主要工艺参数 (13)3.4脱硫工艺操作要点 (14)4 主要设计计算依据 (14)4.1 煤气量计算 (14)4.1.1 计算依据 (14)4.1.2 计算过程 (14)4.2 主要设计计算参数 (15)4.2.1 设备参数 (15)4.2.2 原材料消耗参数 (15)4.2.3 主要设计要求 (15)4.3 物料衡算 (15)4.3.1 H2S 的吸收量 (15)4.3.4 原料消耗 (16)5 主要设备的设计及计算 (17)5.1 脱硫塔 (17)5.1.1 计算参数 (17)5.1.2 脱硫塔的计算 (17)5.1.3 塔顶喷淋装置 (18)5.2 再生塔 (19)5.3 反应槽 (20)5.4 事故槽 (21)5.5 加热器 (21)5.6 循环泵 (22)5.6.1 管内的阻力损失 (23)5.6.2 换热器阻力损失 (23)5.7 空压机 (24)5.8 硫泡沫槽 (25)5.9 真空过滤机 (25)5.10 熔硫釜 (26)5.11 通风机 (27)5.12 主要管道管径 (27)5.12.1 煤气管道 (27)5.12.2 压缩空气管道 (27)5.12.3 蒸汽管道 (27)6 主要设备的选型 (28)6.1 脱硫塔 (28)6.2 再生塔 (28)6.3 循环泵 (28)6.4 空气压缩机 (28)7 工段布置及总平面布置 (29)7.1 布置原则 (29)7.4 总平面布置及说明 (30)8 非工艺部分 (31)8.1 共用设施 (31)8.1.1 供水 (31)8.1.2 供电 (31)8.1.3 蒸汽与压缩空气 (32)8.1.4 供暖与通风 (32)8.1.5 土建 (32)8.1.6 机修 (32)8.2 仪表及自动化 (32)9 生产操作和劳动定员 (34)9.1 生产操作 (34)9.1.1 泵工正常操作 (34)9.1.2 泡沫工正常操作 (35)9.1.3 过滤机工正常操作 (35)9.2 劳动定员 (36)10 经济核算 (37)10.1 核算说明 (37)10.2 投资概算 (37)10.2.1 土建部分 (37)10.2.2 设备部分 (38)10.2.3 工具费 (39)10.2.4 设备施工管理费 (39)10.2.5 化验设备费 (39)10.2.6 工艺管道和阀门 (39)10.2.7 仪表费与电气费 (40)10.2.8 设计费 (40)10.2.9 不可预见费 (41)10.3 生产成本分析 (41)10.3.3 工资及附加费 (42)10.3.4 工段经费 (42)10.4 核算 (42)参考文献 (43)附录 (44)1 设备一览表 (44)2 图纸说明 (45)1 总论1.1 焦炉煤气脱硫的目的和意义焦炉煤气由焦化企业炼焦生产时产生。
焦炉煤气精脱硫工艺分析

焦炉煤气精脱硫工艺分析一、工艺原理:焦炉煤气中的H2S主要通过煤气中的Fegl肟羧酸盐、CaS等吸收剂进行吸收。
Fegl肟羧酸盐是一种高效的硫化物吸收剂,可在较低的温度下将煤气中的H2S和COS吸收。
而CaS则可以将煤气中的剩余H2S去除。
二、工艺流程:1.气体预处理:首先对焦炉煤气进行预处理,去除其中的悬浮颗粒物和水分,以净化煤气。
2.前骤吸收:采用Fegl肟羧酸盐作为吸收剂,通过吸收剂床将煤气中的H2S、COS等硫化物吸收。
床层中的吸收剂会与煤气中的硫化氢进行反应,生成硫化铁,并将其捕集。
3.普鲁士蓝阳极液循环:将废液中的硫化铁氧化为硫酸铁,通过循环泵送到反应床顶部,实现循环利用。
4.精脱硫:采用CaS作为吸收剂,通过床层吸收煤气中剩余的硫化氢,并将其转化为CaS。
此过程需要保持一定的温度和压力,以促使吸收反应的进行。
5.再复焦炉:将经过精脱硫的煤气送入焦炉进行再加热,以提高炉内温度。
三、工艺特点:1.高效: 采用Fegl肟羧酸盐和CaS作为吸收剂,可以高效地吸收煤气中的硫化物,使硫化氢的去除率达到90%以上,保证煤气的质量。
2.安全:精脱硫过程中对温度和压力的要求较高,可以有效地防止硫化氢的泄漏,保证了生产环境的安全。
3.循环利用:工艺中的废液通过循环泵送到反应床顶部,实现了废液中的硫化铁的循环利用,减少了废液的排放,具有较好的环保效益。
总结起来,焦炉煤气精脱硫工艺通过床层吸收剂的反应,有效地去除焦炉煤气中的硫化氢等硫化物,以保证煤气的质量达到环保要求。
该工艺具有高效、安全、循环利用等特点,在焦化行业得到广泛应用。
焦炉煤气脱硫及硫回收工艺分析

焦炉煤气脱硫及硫回收工艺分析焦炉煤气脱硫工艺中常用的方法有吸收法、催化氧化法和膜法等。
其中,吸收法是一种较常用的脱硫技术,其主要原理是通过将煤气经过吸收液(如碱液或氨液)进行接触,使H2S被吸收并转化为硫化物,从而达到脱硫的目的。
催化氧化法则是利用催化剂将H2S氧化为硫,达到脱硫的效果。
膜法则是通过膜的选择性透过性,将H2S从煤气中分离出来,实现脱硫。
吸收法中较为常用的是碱液吸收法。
碱液吸收法的优点是操作简单、脱硫效果较好,但对于含有高浓度的H2S的煤气来说,在吸收液中可能会生成大量的硫化物,导致液氨浴中硫化物过多,降低硫吸收效果。
为解决这一问题,可以通过加入硝酸铁和硝酸铝等添加剂,改善液氨浴的性质,提高脱硫效果。
催化氧化法主要是通过催化剂(如氧化铁、氧化锌等)将H2S氧化为硫,其中反应产物为SO2、在焦炉煤气中,SO2含量较高,通过反应器中催化剂的作用,可以将H2S和SO2相互转化,使SO2被还原为硫,并回收利用。
这种方法适用于H2S含量较高的煤气,可以有效地将H2S转化为有价值的硫。
膜法则是利用特定的膜材料,通过选择性透过性将煤气中的H2S分离出来。
膜法具有操作简单、能耗低、脱硫效果好等优点,但因为膜材料对不同的气体有不同的透过性,所以需要选择合适的膜材料来实现脱硫。
在焦炉煤气脱硫的基础上,硫回收技术可以有效地利用焦炉煤气中的硫资源。
目前常用的硫回收技术有硫磺回收、硫纵向深度利用和硫脱硫液回收等。
硫磺回收是将焦化炉煤气中的SO2和氢气反应生成硫磺,然后收集硫磺进行回收利用。
硫纵向深度利用是将硫经过高温和高压加工,制成硫酸、硫酸铵和硫化铵等化工产品。
硫脱硫液回收则是利用含氢气的溶液将气中的硫含量吸收,生成硫酸铵和硫化铵等化学品。
综上所述,焦炉煤气脱硫及硫回收工艺分析主要包括吸收法、催化氧化法和膜法等不同的脱硫工艺。
根据不同的情况,可以选择适合的工艺来降低煤气中的硫含量,并对焦炉煤气中的硫进行回收利用,以实现资源的可持续利用。
- 1、下载文档前请自行甄别文档内容的完整性,平台不提供额外的编辑、内容补充、找答案等附加服务。
- 2、"仅部分预览"的文档,不可在线预览部分如存在完整性等问题,可反馈申请退款(可完整预览的文档不适用该条件!)。
- 3、如文档侵犯您的权益,请联系客服反馈,我们会尽快为您处理(人工客服工作时间:9:00-18:30)。
焦化厂焦炉煤气一级加氢转化、一级脱硫工艺
分析与设计技术实施方案
1.一级加氢转化:
一级加氢转化器设计上为1台,在此焦炉煤气中大部分的有机硫在催化剂的作用下转化为硫化氢,在整个脱硫工艺中起着基础性作用。
设计上一级加氢转化器选用的催化剂是铁钼加氢转化催化剂,其活性成分是氧化钼和少量的氧化铁,使用前需预先进行升温硫化才能有较好的催化活性。
实际运行表明,只要对催化剂硫化充分,生产中温度控制合适,一级加氢转化器即能够将焦炉煤气中大部分的有机硫进行加氢转化生成硫化氢,满足生产需要。
目前存在的主要问题是,大部分的甲醇生产厂家都反映催化剂的使用寿命不够理想:
好的状况下可使用2年,一般的在使用1年后催化剂活性就会大大削弱,有机硫加氢转化能力降低甚至会消失,即使提高催化剂床层的运行温度也不会有大的改观。
如此增加了催化剂的更换频率和脱硫成本。
理论上催化剂的活性是不会下降或消失的,造成这种现象有多方面原因。
催化剂的生产厂家认为是催化剂在使用前硫化不彻底所致,
但这并非主要原因:
因为催化剂在使用过程中始终是处在一个多硫和强还原性的氛围中,即使在投用前预硫化不十分彻底,但在使用过程中也会不断地有硫化反应发生,直至硫化彻底。
因此造成催化剂活性下降较快应该有以下两个原因:
一是催化剂本身质量存在问题,如活性成分含量偏低、稳定性差;
二是焦炉煤气成分复杂,其中含有的少量焦油、萘等物质逐渐累积、附着于催化剂颗粒表面,堵塞了活性微孔使催化剂的活性大大下降,另外催化剂床层内温度的波动,尤其是超温时出现的焦炉气析碳和催化剂结块也会导致催化剂活性下降,最终使一级加氢转化器的有机硫转化能力变弱。
实际生产表明,催化剂受到污染、活性微孔被堵是造成催化活性下降的主要原因。
因此要保证一级加氢转化器入口气体的洁净度。
对此设计流程上,在一级加氢转化器之前设置了常温过滤器和预加氢转化器。
常温过滤器可以过滤除去焦炉气中的少量焦油、萘等,预加氢转化器则可以在中温条件下进一步脱除焦炉气中的焦油、萘等,同时辅助一级加氢转化器进行少量的有机硫加氢转化。
由此可见确保常温过滤器和预加氢转化器的良好运行状况对
于一级加氢转化器的稳定运行及催化剂的使用寿命有重要意义。
生产中要定期对常温过滤器进行排污,及时将过滤下的焦油等排掉以防止气体流量和温度波动时带至后系统,尤其在温度偏高时很可能会将之前过滤下的物质在相对高温下气化带入后系统。
对于预加氢转化器要充分发挥其在中温条件下的过滤作用,以保证一级加氢转化器的催化剂尽可能不被污染。
在一级加氢转化器的催化剂后期活性下降时,其有机硫加氢转化的辅助作用也很重要。
设计上常温过滤器为2台,可以倒换使用。
对于预加氢转化器,设计上有两台或是单台加副线流程,可在开车过程更换催化剂而不影响生产。
鉴于一级加氢转化器在整个脱硫工艺中的重要作用和催化剂使用寿命偏低的现状,近来有些厂家将一级加氢转化器设计为两台,如此虽然增加了部分前期固定资产投资,但作用还是明显的:
一是可以在不停车、不影响生产的情况下更换催化剂;
二是可以随时对催化剂进行再生操作,以尽量延长催化剂的使用寿命。
2.一级脱硫:
一级脱硫槽负责将一级加氢转化器生成的硫化氢脱除。
由于其脱硫负荷较大,设计上为3台,正常生产时开2备1或3台串
联使用。
一级脱硫槽的脱硫剂是以氧化锰为主要脱硫组分的铁锰脱硫剂,使用前需进行预升温还原。
生产实践表明其投用初期的脱硫精度和硫容均比较理想,只是由于其在脱硫过程中有一定的反应热,调节不当时易使脱硫槽出口超温并进一步导致二级加氢转化器及二级脱硫槽等超温。
因此有部分厂家试用了中温氧化铁脱硫剂在一级脱硫槽,据脱硫剂的生产厂家讲中温氧化铁的性能要优于铁锰脱硫剂:硫容较高,反应热较小脱硫剂床层温度稳定且更易控制,生产成本相对较低。
然而实践证明其饱和硫容要差些,在相同的工况下,中温氧化铁脱硫剂的使用时间仅约为铁锰脱硫剂的一半,即硫容仅为铁锰脱硫剂的一半。
实际上对于氧化铁脱硫剂,其在常温状态下的脱硫效果还是十分理想的,脱硫精度和硫容都比较高。
而中温氧化铁的脱硫效果目前来说还不是很理想,需进一步改进。
一种新型氧化铁脱硫材料:无定型羰基氧化铁,硫容可达60%以上,以此为活性成分所生产的脱硫剂的硫容可达 45%,且脱硫剂可再生循环使用。
若能投入生产运行,将会减少脱硫剂的用量,大大降低中温干法脱硫工艺的脱硫成本。
近来,也有厂家尝试选用中温氧化锌作为一级脱硫槽的脱硫剂。
对于氧化锌脱硫剂其硫容受温度的影响比较大,据资料介绍,其脱硫温度在<100 ℃时,即常温氧化锌的硫容为10%左右;脱硫温度在 200~300 ℃时,其硫容可达20%左右;脱硫温度在 300~450 ℃时,硫容可达30%左右。
理论上在中温状态下氧化锌脱硫剂的硫容要优于铁锰脱硫剂,而在成本方面,中温氧化锌脱硫剂的成本要高于铁锰脱硫剂,大约是后者的2倍。
因此,针对一级脱硫槽脱硫负荷大、脱硫剂用量大的特点,宜选用硫容大、生产成本相对低的脱硫剂。
脱硫剂和催化剂不同,其中的活性成分会直接参与反应,与硫化氢反应生成相应的硫化物,直至达到吸硫饱和,最终会彻底失去脱硫作用,所以一级脱硫槽的使用时间取决于脱硫剂的硫容和入口气体的总硫含量。
对于脱硫剂,饱和后需尽快更换,以满足生产需要。
在生产中也有一个现象:即铁锰脱硫剂在使用一段时间后,会逐渐具备有机硫加氢催化转化的作用,且吸硫越多转化作用越明显,这是由于在脱硫过程中硫化氢和金属氧化物生成越来越多的金属硫化物在发挥作用。
对于这一现象,曾有厂家做了相关的运行试验,在一级加氢转化催化剂后期或活性较差时,没有立即更换催化剂而是用即将饱和的铁锰脱硫剂作为有机硫加氢转化催化剂辅助生产,实际运行证明效果还是比较良好的。
而中温氧化锌脱硫剂在使用中对有机硫的加氢转化作用却不是很明显,据此若选用中温氧化锌脱硫剂在一级脱硫槽,则对一级加氢转化器的要求较高:
其催化剂的活性需始终保持良好,否则很可能会导致脱硫负荷后移,进一步影响整体脱硫效果。
因此对于一级脱硫的脱硫剂,目前铁锰脱硫剂是合理的选择。
选用中温氧化锌脱硫剂在一级脱硫槽,其经济性和稳定性还需进一步观察。