内层干膜
HDI 制作流程
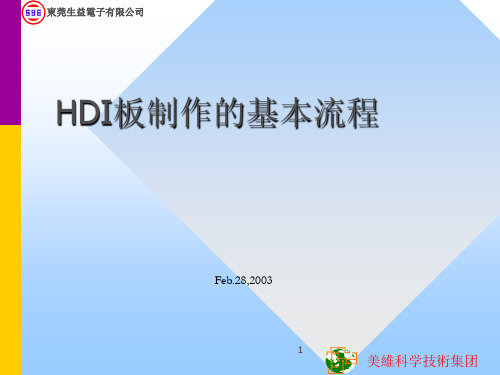
流程
26
美維科学技術集团
東莞生益電子有限公司
6.沉铜与加厚铜(孔的金属化)
概念: • 电路板的基材是由铜箔,玻璃纤维,环氧树脂组 成。在制作过程中基材钻孔后孔壁截面就是由以 上三部分材料组成。 • 孔金属化就是要解决在截面上覆盖一层均匀的, 耐热冲击的金属铜。 • 流程分为三个部分:一去钻污流程,二化学沉铜 流程,三加厚铜流程(全板电镀铜)。
前言
2
美維科学技術集团
東莞生益電子有限公司
一.概述:
HDI板,是指High Density Interconnect,即高密度互连板。是PCB行业在 20世纪末发展起来的一门较新的技术。传统的PCB板的钻孔由于受到钻刀影 响,当钻孔孔径达到0.15mm时,成本已经非常高,且很难再次改进。而HDI 板的钻孔不再依赖于传统的机械钻孔,而是利用激光钻孔技术。(所以有
内层线路做好的板子必须要经过黑化或棕化后才能进行 层压。它是对内层板子的线路铜表面进行氧化处理。一般生 成的Cu2O(氧化亚铜)为红色、CuO(氧化铜)为黑色, 所以氧化层中Cu2O为主称为棕化、CuO为主的称为黑化。
流程
19
美維科学技術集团
東莞生益電子有限公司
3. 黑化和棕化:
棕
流程
化
线
20
美維科学技術集团
流程
12
美維科学技術集团
東莞生益電子有限公司
1.开料(CUT)
开料是把我们采购回来的敷铜板切割成能在生产线上制作的板 子的过程。
首先我们来了解几个概念: 1. 2. 3. UNIT:UNIT是指客户设计的单元图形。 SET :SET是指客户为了提高效率、方便生产等原因,将多个UNIT拼 在一起成为的一个整体图形。它包括单元图形、工艺边等等。 PANEL:PANEL是指PCB厂家生产时,为了提高效率、方便生产等原 因,将多个SET拼在一起并加上工具板边,组成的一块板子。
干膜常见问题改善
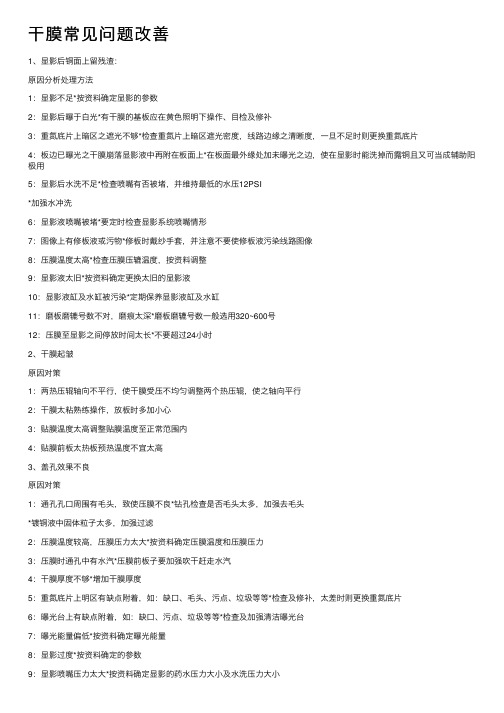
⼲膜常见问题改善1、显影后铜⾯上留残渣:原因分析处理⽅法1:显影不⾜*按资料确定显影的参数2:显影后曝于⽩光*有⼲膜的基板应在黄⾊照明下操作、⽬检及修补3:重氮底⽚上暗区之遮光不够*检查重氮⽚上暗区遮光密度,线路边缘之清晰度,⼀旦不⾜时则更换重氮底⽚4:板边已曝光之⼲膜崩落显影液中再附在板⾯上*在板⾯最外缘处加未曝光之边,使在显影时能洗掉⽽露铜且⼜可当成辅助阳极⽤5:显影后⽔洗不⾜*检查喷嘴有否被堵,并维持最低的⽔压12PSI*加强⽔冲洗6:显影液喷嘴被堵*要定时检查显影系统喷嘴情形7:图像上有修板液或污物*修板时戴纱⼿套,并注意不要使修板液污染线路图像8:压膜温度太⾼*检查压膜压辘温度,按资料调整9:显影液太旧*按资料确定更换太旧的显影液10:显影液缸及⽔缸被污染*定期保养显影液缸及⽔缸11:磨板磨辘号数不对,磨痕太深*磨板磨辘号数⼀般选⽤320~600号12:压膜⾄显影之间停放时间太长*不要超过24⼩时2、⼲膜起皱原因对策1:两热压辊轴向不平⾏,使⼲膜受压不均匀调整两个热压辊,使之轴向平⾏2:⼲膜太粘熟练操作,放板时多加⼩⼼3:贴膜温度太⾼调整贴膜温度⾄正常范围内4:贴膜前板太热板预热温度不宜太⾼3、盖孔效果不良原因对策1:通孔孔⼝周围有⽑头,致使压膜不良*钻孔检查是否⽑头太多,加强去⽑头*镀铜液中固体粒⼦太多,加强过滤2:压膜温度较⾼,压膜压⼒太⼤*按资料确定压膜温度和压膜压⼒3:压膜时通孔中有⽔汽*压膜前板⼦要加强吹⼲赶⾛⽔汽4:⼲膜厚度不够*增加⼲膜厚度5:重氮底⽚上明区有缺点附着,如:缺⼝、⽑头、污点、垃圾等等*检查及修补,太差时则更换重氮底⽚6:曝光台上有缺点附着,如:缺⼝、污点、垃圾等等*检查及加强清洁曝光台7:曝光能量偏低*按资料确定曝光能量8:显影过度*按资料确定的参数9:显影喷嘴压⼒太⼤*按资料确定显影的药⽔压⼒⼤⼩及⽔洗压⼒⼤⼩4、线路变幼或曝光区⼲膜显影时不易冲洗掉原因对策1:曝光过度*⽤21格曝光尺按资料正确曝光2:重氮底⽚上暗区之遮光不够*检查重氮底⽚上暗区遮光密度,线路边缘之清晰度,⼀旦不⾜时则更换重氮底⽚3:曝光前抽真空程度不够*检查曝光前抽真空度及碓定抽真空时间*换掉曝光上台不良的聚酯膜4:压膜之板⾯显影前曝露于⽩⾊光源*检查黄光室具有UV之⽩光情况5:压膜温度过⾼*按资料控制压膜温度6:显影不⾜,残膜冲洗不净*按资料确定显影点*更换太旧的显影液*加强⽔冲洗7:曝光时重氮底⽚药膜⾯与板上⼲膜⾯没有紧密结合*加强擦⽓及⽤导⽓条帮助抽真空或在重氮底⽚上明区位打出孔*检查重氮底⽚药膜⾯暗区及板上⼲膜⾯有⽆垃圾等杂物5、显影后⼲膜受损或发现⼲膜浮起或线路边缘不齐原因对策1:曝光不⾜*⽤21格曝光尺按资料正确曝光2:显影过度*按资料确定显影的参数3:曝光后放置时间不够*通常在撕开保护膜(Mylar)前⾄少放置要15分钟以上再显影4:显影药液温度太⾼*按资料设定正确显影温度5:压膜之前铜⾯处理不良*⽔膜测试⼤于15秒以上*保证磨痕宽度6:压膜温度不⾜,压膜压⼒不够*注意压膜速度及压膜温度、压膜压⼒7:显影喷嘴压⼒太⼤*按资料确定显影的药⽔压⼒⼤⼩及⽔洗压⼒⼤⼩6、线路镀锡铅时发现⼲膜边缘浮起⽽造成渗镀现象原因对策1:⼲膜性能不良,超过有效期使⽤*尽量在有效期内使⽤⼲膜2:压膜之前铜⾯处理不良*加强压膜前铜⾯处理控制*⽔膜测试⼤于15秒以上*保证磨痕宽度3:压膜参数条件不对*按资料确定压膜参数条件4:曝光不⾜*⽤21格曝光尺按资料正确曝光5:显影过度*按资料确定显影的参数6:电镀前处理药品及参数条件不对*按供应商资料确定参数条件7:电镀时电流密度过⼤*调整电镀层均匀性降低电流密度9:电镀液太陈旧或电镀液⾥有机杂质太多*对电镀液进⾏活性炭处理7、铜与铜之间附着⼒不良原因对策1:线路镀铜前处理及清洗不当*按供应商资料确定控制除油、微蚀、⽔洗2:压膜⾄显影之间停放时间太长*停放时间太长时,适当应加强微蚀处理使铜⾯撤底活化3:显影不⾜,暗区留有残渣*按资料确定显影的参数*更换太旧的显影液4:⽔冲洗不⾜*加强⽔冲洗8、板⾯电镀区发⽣跳镀(Skip Plating)或称漏镀现象原因对策1:在待镀区之裸铜⾯上留有⼲膜残渣或显影液中的⼲膜碎⽚⼜打回板⾯⽽重新附着*可能是棕⽚上有刮伤、缺⼝、应加修补*减少或避免⼲膜碎的产⽣2:在待镀区未曝光处显影不⾜,未撤底除尽残膜*按资料确定显影的参数*更换太旧的显影液3:电镀时板⾯受污染等问题*避免板⾯受污染,加强前处理⼯作4:电镀锡层较粗糙或剥膜⼯艺有问题*电镀锡不均匀,电流密度较⼤处较粗糙*电镀锡板放置于有污染环境处时间太长*剥膜药⽔浓度或温度太⾼或时间太长9、剥膜后发现铜⾯上尚留有残渣原因对策1:剥膜时间不⾜够*调整剥膜时间,但不宜过长2:电镀层厚度超过⼲膜厚度⽽发⽣夹膜现象*调整电镀层均匀性或⽤厚度较厚⼲膜(如2mil的⼲膜)3:电镀层厚,线路较幼剥膜较难*可以适当在剥膜药⽔中加定量3%丁基卡必醇4:剥膜液不良,剥膜液温度低,剥膜药液太旧*⼀般使⽤2~5%的苛性钾或钠的⽔溶液在50℃±2℃内操作,或更换新液5:已剥落的膜碎⽚⼜再附著上*加强冲洗的时间、压⼒及温度控制,加强过滤及溢流积渣,缩短剥膜及⽔洗间距及时间,要⽴即冲洗6:剥膜前已显影板曝露于⽩光中时间太长或显影后不当烘烤*板⾯各处被⽩光不均匀曝光延长剥膜时间*延长剥膜时间,取消烘烤10、电镀时⼲膜脱落原因对策1:前处理药⽔之温度太⾼或时间太长*按供应商资料确定参数条件2:曝光前保护膜(Mylar)被撕起或曝光后保护膜(Mylar)被过早撕起*避免保护膜(Mylar)被撕起现象3:显影后停置时间过长及放置环境不当*应放置有温度及湿度控制黄光环境中4:压膜之前铜⾯处理不良*⽔膜测试⼤于15秒以上*保证磨痕宽度5:电镀液太陈旧或电镀液⾥有机杂质太多*对电镀液进⾏活性炭处理11、线路镀⾦发现⼲膜边缘浮起⽽造成渗镀现象原因对策1:压膜之前铜⾯处理不良*加强压膜前铜⾯处理控制*⽔膜测试⼤于15秒以上*保证磨痕宽度2:压膜参数条件不对*按资料确定压膜参数条件3:曝光不⾜*⽤21格曝光尺按资料正确曝光4:显影过度*按资料确定显影的参数5:电镀前处理药品及参数条件不对*按供应商资料确定参数条件6:电镀时电流密度过⼤*调整电镀层均匀性降低电流密度7:电镀⾦缸药⽔参数条件不对*调整电镀⾦药⽔含⾦量,调整电镀层均匀性降低电流密度12蚀刻时⼲膜破坏及浮起原因对策1:压膜前铜⾯处理不良*加强压膜之前铜⾯处理控制*⽔膜测试⼤于15秒以上*保证磨痕宽度2:曝光不⾜,但不宜过⾜*⽤21格曝光尺按资料正确曝光3:蚀刻液PH太⾼,温度太⾼,喷嘴压⼒太⼤*做适当调整4:⽔洗喷嘴压⼒太⼤*降低喷嘴压⼒5:显影后停置时间过长及放置环境不当*应放置有温度及湿度控制的黄光环境中6:显影后停置⽩光区时间过长⼲膜变脆*避免放置于⽩光下1.⼲膜的介绍⼲膜(Dry film)在涂状中是相对湿膜(Wet film)⽽⾔的,⼲膜是⼀种⾼分⼦的化合物,它通过紫外线的照射后能够产和⼀种聚合反应形成⼀种稳定的物质附着于板⾯,从⽽达到阻挡电镀和蚀刻的功能。
PCB工艺流程全面介绍

路漫漫其悠远 2020/4/13
课程内容 PCB工艺流程简介及工序目的 PCB工艺流程介绍 PCB工艺流程录象
路漫漫其悠远
•2020/4/13
一 PCB工艺流程 (简图)
界料
内层干菲林
黑氧化 内层蚀板
棕化
成型
开/短路测试
包装
压板 钻孔
喷锡
镀金手指
表面处理
出货
沉铜<孔金属化> 外层干菲林
10.0 外形加工 外型加工的内容 •手锣加工 •机锣加工 •啤板加工 •V-CUT加工 •斜边加工 •阻抗测试
路漫漫其悠远
•2020/4/13
手锣加工的介绍
• 手锣的定义:
是利用由铝、FR-4基材或加强板制成的模 板。模板的尺寸与被完成的线路板尺寸一 样,其上装有定位销钉来固定线路板,人 工转动模板,利用旋转的锣头来锣板。
3.1.3. 曝光: 将黄菲林贴在板面的干膜上,然后用平行 光曝光.这样有线路的地方,其干膜被曝光定型,无线路的地 方未曝光
3.1.4. 显影: 将未曝光定型的干膜冲走,留下 来的是曝光定型的干膜,即是黄菲林上的线路图 形
3.2. 内层蚀板
3.2.1. 蚀板: 用蚀铜药水将未被干膜盖住的铜 皮蚀掉,剩下的是被干膜盖住的铜,即内层线路图 形
箔蚀掉
6.3.3. 褪铅锡层:将铅锡层去掉,露出铜层
路漫漫其悠远
•2020/4/13
7.0. 湿菲林
7.1. 磨板: 去掉板面氧化、杂物和粗化板面,加
强绿油与板面的抱合力
7.2. 印刷:
7.2.1. 制作印刷丝网:参照绿油菲林制作印刷丝 网,绿油菲林上的绿油开窗在丝网上做成不透油的挡 点.其它处均为透油的网格
干膜常见问题处理

1、显影后铜面上留残渣:原因分析处理方法1:显影不足*按资料确定显影的参数2:显影后曝于白光*有干膜的基板应在黄色照明下操作、目检及修补3:重氮底片上暗区之遮光不够*检查重氮片上暗区遮光密度,线路边缘之清晰度,一旦不足时则更换重氮底片4:板边已曝光之干膜崩落显影液中再附在板面上*在板面最外缘处加未曝光之边,使在显影时能洗掉而露铜且又可当成辅助阳极用5:显影后水洗不足*检查喷嘴有否被堵,并维持最低的水压12PSI*加强水冲洗6:显影液喷嘴被堵*要定时检查显影系统喷嘴情形7:图像上有修板液或污物*修板时戴纱手套,并注意不要使修板液污染线路图像8:压膜温度太高*检查压膜压辘温度,按资料调整9:显影液太旧*按资料确定更换太旧的显影液10:显影液缸及水缸被污染*定期保养显影液缸及水缸11:磨板磨辘号数不对,磨痕太深*磨板磨辘号数一般选用320~600号12:压膜至显影之间停放时间太长*不要超过24小时2、干膜起皱原因对策1:两热压辊轴向不平行,使干膜受压不均匀调整两个热压辊,使之轴向平行2:干膜太粘熟练操作,放板时多加小心3:贴膜温度太高调整贴膜温度至正常范围内4:贴膜前板太热板预热温度不宜太高3、盖孔效果不良原因对策1:通孔孔口周围有毛头,致使压膜不良*钻孔检查是否毛头太多,加强去毛头*镀铜液中固体粒子太多,加强过滤2:压膜温度较高,压膜压力太大*按资料确定压膜温度和压膜压力3:压膜时通孔中有水汽*压膜前板子要加强吹干赶走水汽4:干膜厚度不够*增加干膜厚度5:重氮底片上明区有缺点附着,如:缺口、毛头、污点、垃圾等等*检查及修补,太差时则更换重氮底片6:曝光台上有缺点附着,如:缺口、污点、垃圾等等*检查及加强清洁曝光台7:曝光能量偏低*按资料确定曝光能量8:显影过度*按资料确定的参数9:显影喷嘴压力太大*按资料确定显影的药水压力大小及水洗压力大小10:曝光前保护膜(Mylar)被撕起或曝光后保护膜(Mylar)被过早撕起*避免保护膜(Mylar)被撕起现象4、线路变幼或曝光区干膜显影时不易冲洗掉原因对策1:曝光过度*用21格曝光尺按资料正确曝光2:重氮底片上暗区之遮光不够*检查重氮底片上暗区遮光密度,线路边缘之清晰度,一旦不足时则更换重氮底片3:曝光前抽真空程度不够*检查曝光前抽真空度及碓定抽真空时间*换掉曝光上台不良的聚酯膜4:压膜之板面显影前曝露于白色光源*检查黄光室具有UV之白光情况5:压膜温度过高*按资料控制压膜温度6:显影不足,残膜冲洗不净*按资料确定显影点*更换太旧的显影液*加强水冲洗7:曝光时重氮底片药膜面与板上干膜面没有紧密结合*加强擦气及用导气条帮助抽真空或在重氮底片上明区位打出孔*检查重氮底片药膜面暗区及板上干膜面有无垃圾等杂物5、显影后干膜受损或发现干膜浮起或线路边缘不齐原因对策1:曝光不足*用21格曝光尺按资料正确曝光2:显影过度*按资料确定显影的参数3:曝光后放置时间不够*通常在撕开保护膜(Mylar)前至少放置要15分钟以上再显影4:显影药液温度太高*按资料设定正确显影温度5:压膜之前铜面处理不良*水膜测试大于15秒以上*保证磨痕宽度6:压膜温度不足,压膜压力不够*注意压膜速度及压膜温度、压膜压力7:显影喷嘴压力太大*按资料确定显影的药水压力大小及水洗压力大小6、线路镀锡铅时发现干膜边缘浮起而造成渗镀现象原因对策1:干膜性能不良,超过有效期使用*尽量在有效期内使用干膜2:压膜之前铜面处理不良*加强压膜前铜面处理控制*水膜测试大于15秒以上*保证磨痕宽度3:压膜参数条件不对*按资料确定压膜参数条件4:曝光不足*用21格曝光尺按资料正确曝光5:显影过度*按资料确定显影的参数6:电镀前处理药品及参数条件不对*按供应商资料确定参数条件7:电镀时电流密度过大*调整电镀层均匀性降低电流密度8:曝光前保护膜(Mylar)被撕起或曝光后保护膜(Mylar)被过早撕起*避免保护膜(Mylar)被撕起现象9:电镀液太陈旧或电镀液里有机杂质太多*对电镀液进行活性炭处理7、铜与铜之间附着力不良原因对策1:线路镀铜前处理及清洗不当*按供应商资料确定控制除油、微蚀、水洗2:压膜至显影之间停放时间太长*停放时间太长时,适当应加强微蚀处理使铜面撤底活化3:显影不足,暗区留有残渣*按资料确定显影的参数*更换太旧的显影液4:水冲洗不足*加强水冲洗8、板面电镀区发生跳镀(Skip Plating)或称漏镀现象原因对策1:在待镀区之裸铜面上留有干膜残渣或显影液中的干膜碎片又打回板面而重新附着*可能是棕片上有刮伤、缺口、应加修补*减少或避免干膜碎的产生2:在待镀区未曝光处显影不足,未撤底除尽残膜*按资料确定显影的参数*更换太旧的显影液3:电镀时板面受污染等问题*避免板面受污染,加强前处理工作4:电镀锡层较粗糙或剥膜工艺有问题*电镀锡不均匀,电流密度较大处较粗糙*电镀锡板放置于有污染环境处时间太长*剥膜药水浓度或温度太高或时间太长9、剥膜后发现铜面上尚留有残渣原因对策1:剥膜时间不足够*调整剥膜时间,但不宜过长2:电镀层厚度超过干膜厚度而发生夹膜现象*调整电镀层均匀性或用厚度较厚干膜(如2mil的干膜)3:电镀层厚,线路较幼剥膜较难*可以适当在剥膜药水中加定量3%丁基卡必醇4:剥膜液不良,剥膜液温度低,剥膜药液太旧*一般使用2~5%的苛性钾或钠的水溶液在50℃±2℃内操作,或更换新液5:已剥落的膜碎片又再附著上*加强冲洗的时间、压力及温度控制,加强过滤及溢流积渣,缩短剥膜及水洗间距及时间,要立即冲洗6:剥膜前已显影板曝露于白光中时间太长或显影后不当烘烤*板面各处被白光不均匀曝光延长剥膜时间*延长剥膜时间,取消烘烤10、电镀时干膜脱落原因对策1:前处理药水之温度太高或时间太长*按供应商资料确定参数条件2:曝光前保护膜(Mylar)被撕起或曝光后保护膜(Mylar)被过早撕起*避免保护膜(Mylar)被撕起现象3:显影后停置时间过长及放置环境不当*应放置有温度及湿度控制黄光环境中4:压膜之前铜面处理不良*水膜测试大于15秒以上*保证磨痕宽度5:电镀液太陈旧或电镀液里有机杂质太多*对电镀液进行活性炭处理11、线路镀金发现干膜边缘浮起而造成渗镀现象原因对策1:压膜之前铜面处理不良*加强压膜前铜面处理控制*水膜测试大于15秒以上*保证磨痕宽度2:压膜参数条件不对*按资料确定压膜参数条件3:曝光不足*用21格曝光尺按资料正确曝光4:显影过度*按资料确定显影的参数5:电镀前处理药品及参数条件不对*按供应商资料确定参数条件6:电镀时电流密度过大*调整电镀层均匀性降低电流密度7:电镀金缸药水参数条件不对*调整电镀金药水含金量,调整电镀层均匀性降低电流密度12蚀刻时干膜破坏及浮起原因对策1:压膜前铜面处理不良*加强压膜之前铜面处理控制*水膜测试大于15秒以上*保证磨痕宽度2:曝光不足,但不宜过足*用21格曝光尺按资料正确曝光3:蚀刻液PH太高,温度太高,喷嘴压力太大*做适当调整4:水洗喷嘴压力太大*降低喷嘴压力5:显影后停置时间过长及放置环境不当*应放置有温度及湿度控制的黄光环境中6:显影后停置白光区时间过长干膜变脆*避免放置于白光下1.干膜的介绍干膜(Dry film)在涂状中是相对湿膜(Wet film)而言的,干膜是一种高分子的化合物,它通过紫外线的照射后能够产和一种聚合反应形成一种稳定的物质附着于板面,从而达到阻挡电镀和蚀刻的功能。
干膜讲义
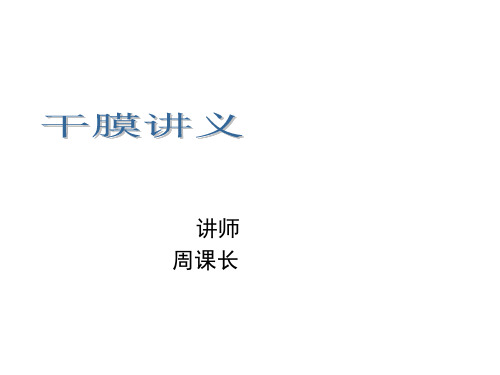
• 大批量生产时,在所要求的传送速度下, 热压辊难以提供足够的热量,因此需给要 贴膜的 板子进行预热,即在烘箱中干燥处 理后稍加冷却便可贴膜。 • 为适应生产精细导线的印制板,又发展了 湿法贴膜工艺,此工艺是利用专用贴膜机 在贴干 膜前于铜箔表面形成一层水膜,该 水膜的作用是:提高干膜的流动性;
• 驱除划痕、砂眼、凹坑和 织物凹陷等部位上 滞留的气泡;在加热加压贴膜过程中,水对 光致抗蚀剂起增粘作用,因而可 大大改善干 膜与基板的粘附性,从而提高了制作精细导 线的合格率,据报导,采用此工艺精细 导线 合格率可提高1—9%。 • 完好的贴膜应是表面平整、无皱折、无气泡、 无灰尘颗粒等夹杂。 • 为保持工艺的稳定性,贴膜后应经过15分钟 的冷却及恢复期再进行曝光。
• 贴膜通常在贴膜机上完成,贴膜机型号繁多,但基本结构 大致相同: 贴膜可连续贴,也可单张贴。 连续贴膜时要注意在上、下干膜送料辊上装干膜时要对齐, 单张贴时,膜的尺寸要稍小于板面,以防抗蚀剂粘到热压 辊上。连续贴膜生产效率高,适合于 大批量生产,小批 量生产可采用单张贴法,以减少干膜的浪费。 贴膜时要掌握好的三个要素为压力、温度、传送速度。
讲师 周课长
目录
一 、干膜成份的简介 二、干膜的流程
一 干膜成份的简介
1.干膜的介绍:
干膜是一种高分子的化合物,它通过紫外 线的照射后能够产生一种聚合反应形成一种稳 定的物质附着于板面,从而达到阻挡电镀和蚀 刻的功能。
2.干膜的分类
依据厚度的不同干膜可以分为三类:
1.2mil、1.5mil、2.0mil 1.2mil干膜主要 用于内层板作业 1.5mil、干膜主要用于外 层板作业当然也 可以用于内层板作业但由 于较厚在蚀刻的 过程中容易造成侧蚀而且成本相对较高,所 以 一般不使用其作内层。
PCB工艺流程课件(PPT 42张)
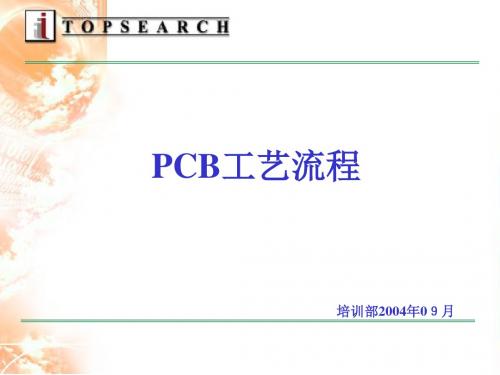
7.3. 预局:将湿菲林局至板面干爽
7.4. 曝光:图形转移
7.4.1. 将绿油菲林上的图形转移到黄菲林上.
7.4.2. 曝光:将黄菲林对准板面上的线路图形放 在板面上,然后曝光
7.5. 显影:将未经曝光的湿菲林冲走 7.6. 后局:将湿菲林烘干到要求的硬度
8.0. 白字
8.1. 网印:将文字印刷到板面上
PCB工艺流程
培训部2004年09月
课程内容
PCB工艺流程简介及工序目的 PCB工艺流程介绍 PCB工艺流程录象
一 PCB工艺流程 (简图)
界 料 内层干菲林 内层蚀板 棕化 黑氧化 压板 钻 孔 沉铜<孔金属化> 喷锡
表面处理
成 型
开/短路测试
镀金手指
包 装
出 货
外层干菲林 绿油<湿菲林> 外层蚀板 图形电镀
4.0. 钻孔
根据钻孔加工方式,大致可分为以下两 种:
一种是机械钻孔,另一种是激光钻孔
根据钻孔加工类型,大致可分为以 下两类: 1.一次钻加工 2.分步钻加工
主轴 钻嘴
销钉 线路板 台板
销钉 盖板 底板
主轴 销钉 线路板 台板 钻嘴 销钉 盖板
底板
主轴 钻嘴
销钉 线路板 台板
销钉 盖板 底板
白 字
二 制作流程 1. 界料:
界料就是按照ME制作的工作指示,将大面积 的原状始材料切割成生产所需的尺寸.
2. 局板:
将板材放在局炉内烘烤,降低板内湿度,消除内应力
3. 内层
3.1. 内层干膜
3.1.1. 磨板:
粗化铜板表面,以利于增加板面与药膜的结合
力
清洁板面,除掉板面杂物
除去铜板表面的防氧化层
PCB流程简介-内层工艺介绍

Version 1 Date: Jun.25th.2020
1 of 36
内容
1. 专业用语 ……………………………………………………………….. 3 2. 流程概述 …………………………….…………………..…................. 12 3. 制程介绍 ………………………………………………………………... 14 4. 制程缺点 ………………………………………………………………... 32
PCB
涂布滚轮
因为涂布的湿膜是液体,所以,还需要有烘烤流程,把 油墨烤干,这样才能和其他治工具(底片)进行接触。
因湿膜很薄,所以,需尽可能减少搬运涂布后的基板, 避免湿膜被刮伤。
涂布后的基板
17 of 36
3. 流程介绍
3.4 曝光
UV光通过底片照射到干膜上,使干膜发生一系列化学反应,从而使被光照部分 干膜发生聚合。反应后形成不溶于稀碱溶液的体型大分子结构,从而达到影像转 移效果。
蚀刻点通常管控70%±5%; 未达到标准时,检查时刻草的喷 嘴、喷压、速度、药液等,如有 异常进行调整。
8 of 36
1. 专业用语
1.7 喷嘴 Cone Spray 锥形喷洒-- 是指高压喷液的一种立体造型的水体(又分为空心及实心两种),可形 成强力冲打细小水点的漏斗形雾状水体,以方便各种输送式湿制程的工 件。
抗蚀阻剂 B
C
C
Undercut/Side(C)=(B-A)/2
D Etch Factor (U.S.A)=D/C
Etch Factor (Europe)=C/D
A
IPC-A-600H之定义
蚀刻因子主要和以下因子相关 : • 线路品质 • 电镀均匀性(外层) • 板面清洁度 • 铜箔结构 • 蚀刻设备(药水循环系统、喷
内层D.E.S(干膜)工序药液检验指导书

文件名称
内层D.E.S(干膜)工序药液检 验指导书
文件编号
Q/II-028
版本
A/0
页:15/15
显影流程分析手册
项目
A.浓度测试
1. 使用化学药品
1. 0.1N盐酸溶液(已经标定的标准溶液)
2. 甲基橙指示剂
2. 分析方法 250ml三角烧瓶
使用刻度吸管吸取2ml药液。
加入100ml纯水。
加入3-5滴甲基橙指示剂。(溶液颜色:黄色)
1. 0.1M EDTA溶液(已经标定的标准溶液)
2. PH=10的缓冲溶液
3. PAN指示剂
4. 无水乙醇溶液
2. 分析方法
250ml三角烧瓶
使用刻度吸管吸取1ml药液。 加入75ml纯水。
加入25ml PH=10缓冲溶液 加入20ml 无水乙醇溶液 加入3-5滴PAN指示剂。(溶液颜色:蓝紫色)
2. 分析方法 250ml三角烧瓶
使用刻度吸管吸取1ml药液。
加入100ml纯水。
加入1-2滴甲基橙指示剂。(溶液颜色:橙红色)
滴定 终点
0.5N 氢氧化钠溶液
橙红色
黄色
3. 计 算
4. 规格范围 5. 添加公式
硫酸(g/l)=K × V × 24.5 K:滴定系数。 即实际使用标准液浓度与分析方法中要求
2. 溴酚蓝指示剂
2. 分析方法 250ml三角烧瓶
使用刻度吸管吸取5ml药液。
加入100ml纯水。
加入1-2滴溴酚蓝指示剂。(溶液颜色:黄色)
滴定
0.1N 盐酸溶液
终 Hale Waihona Puke 黄色蓝色3. 计 算
4. 规格范围 5. 添加公式
- 1、下载文档前请自行甄别文档内容的完整性,平台不提供额外的编辑、内容补充、找答案等附加服务。
- 2、"仅部分预览"的文档,不可在线预览部分如存在完整性等问题,可反馈申请退款(可完整预览的文档不适用该条件!)。
- 3、如文档侵犯您的权益,请联系客服反馈,我们会尽快为您处理(人工客服工作时间:9:00-18:30)。
內層干膜•流程圖•烤板→砂紙打磨→前处理→压膜→静置→曝光→静置→显影→检验→蚀刻→检查→去膜→检查→IPQC检查→转下工序.•制程能力:•线经:3-3mil•板厚:0.1-1.6mm•基板尺寸:533*610mm•干膜的作用:干膜的作用主要是通过前处理等一系列工序,在已经镀好铜的板盖上一层干膜,并通过对板曝光显影从而得到一层抗电镀以及蚀刻所需要的光阻图像。
•前处理(去除表面异物平整板面增加表面附着力)•流程:入料→微蚀→水洗→酸洗→水洗→干燥→出料•制程能力:•基板尺寸:325 *310mm-600*500mm•板厚:0.1-2.0mm•线宽:3mil•压膜:•压膜线含有:斜立放板机+粘尘机+濕壓裝置+压膜机+太阳式冷却翻板机+立式收板機。
必須確認壓膜線設備傳動正常•曝光:•曝光操作原理:干膜的各化学成份,利用光能量进行一系列的化学反应,干膜在曝光过程中主要发生架桥聚合反应和变色反应.•设备:放板机+粘尘机+曝光机+收板机•制程能力:•基板尺寸:300*330-533*610mm•板厚:0.1-1.6mm•DES连线•流程:入料→显影*2→水洗*7→水洗→蚀刻*3→水洗*6→去膜*2→水洗*2→抗氧化→水洗*2→烘干→出料•显影:将未曝光的部分用药水将其去除掉,露出所需要的要被去掉的铜或者是应该被留下来的铜。
•蚀刻:将未被干膜所盖住的部分非线路处的铜箔去除掉,留下需要的被干膜所覆盖的线路部分,从而达到完成图像转移的过程。
•显像: Na2CO3:0.75-1.0% K2CO3:1.0土0.2%•蚀刻:NaCLO HCl•去膜: NaOH 0.4-0.6N 第二段NaOH 0.4-0.6N•流程说明:•流程1:适用于内层需AOI扫描之板,内层板冲AOI定位孔及识别孔,六层板冲铆合孔及识别孔,铆合孔兼作AOI定位孔.•流程2:适用于内层需电测之板,由钻孔钻出电测治具PIN孔.•流程3:适用于内层需AOI及电测之板,多用于对比测试.•注:部分板因内层线路方面原因,一面线路需过AOI或电测,另一面为Power Ground层只需目检•AOI制程能力:•基板尺寸:300*330-533*610mm•板厚:0.1-3.7mm•线径线距:3.8-10mil●壓合原理:1.压合是通过高温高压将粘结片(PP)熔化与内层及外层铜箔结合在一起,形成一个整体。
从而得到不同层次的多层板。
2.压合制程可分三部分:内层铜面处理(黑/棕化)、压合(PP分条、切张、冲孔,组合、铆合、叠合,热压、冷压)、压合后处理(下料、分板、钻靶、捞边、磨边)。
•1、流程:•黑化/棕化•(P.P)分条、切张组合(四層板用雙張(四層板用雙張↓→↓→预叠→上热压→冷压→下料→割廢PP和六層以上) 冲孔铆合PP和六層以上)銅皮→檢測→X-Ray钻靶→CNC撈邊→磨邊、清洗→轉下制程黑化●黑化流程:上料→清洁→熱水洗→雙聯水洗→微蝕→雙聯水洗→預浸→黑化→熱水洗→交換→雙聯水洗→熱純水洗→熱風→烘干→下料●黑化作用:在內層銅表面形成氧化銅之絨毛狀物體,使表面積增大,提高內層與粘結片之間的粘結強度。
棕化●棕化流程:入料→酸洗→循環水洗*2→市水洗→清洁→循環水洗*3→純水洗→吸干→中檢→預浸→棕化→循環水洗*5→純水洗→吸干→吹干→烘干→出料●棕化作用:在內層銅表面形成氧化亞銅之絨毛狀物體,使表面積增大,提高內層與粘結片之間的粘結強度。
压板的目的:利用B-Stage树脂受高温高压而完全固化使多层板各层结合在一起,保证多层板的电气性能和机械性能。
压板生产步骤:A、排板-----将内层板与半固化片及铜箔以钢板分隔排好。
B、压合-----通过压合机将排好的多层板(book)压合成整体。
常见四层板结构外压铜箔结构(Foil Construction)——Foil——Prepreg——Core(C/C)——Prepreg——Foil工艺流程特征常见六层板结构外压铜箔结构(Foil Construction)——Foil——Prepreg——Prepreg——Foil压机Opening 示例Prepreg即半固化片,由玻璃纤维布和树脂组成。
其中的树脂呈半固化状态-----称 B-Stage 。
※ Prepreg 由Pre-impregnancy (使预先孕合)组合而成,字典尚未收录,业界常称“树脂片”,“半硬化材料”,“半固化片”等。
基本类型a 、按玻璃布分类,如 1080,2116,7628 等b 、按树脂分类,如酚醛树脂(Phenolic Resin) 环氧树脂(Epoxy Resin)——Core(C/C) ——Prepreg——Kraft Paper Heat Plate ——Cover——Kraft Paper——Separator——Multilayer ——Separator——Cover ——Heat PlateE 表示E-GLASS ,C 表示连续式的玻纤丝,D 表示玻纤丝的直径5μm ,G 表示9μm ,后面数值表示一股纱其重量一磅时的长度(单位为百英尺)牛皮纸------利用牛皮纸的热阻及可压缩性来控制升温速率及平衡压力。
------对使用次数无特定要求,但最好只用一次,因其热阻及可压缩性已大大变小。
A-Stage Varnish B-Stage + 玻璃纤维布C-Stage 硬化树脂钻孔的目的? 導通內外層(PTH 孔) 2.制造固定孔(NPTH 孔 图解钻孔作業● 流程:1、双面板:上PIN (包括垫板)→上机台→盖铝片→贴胶带→插钻头→设定程式→加钻机台识别号→钻孔2、 多层板:上电木板→裁PIN →上板→盖铝片→贴胶吏→插钻头→设定程式→加钻机台别号→钻孔 盖铝片的作用:保持基板,不易刮伤,减少断针,散发热量,引导下钻,防止孔偏。
裁PIN 标准:多层板裁靶孔孔径为φ3.0mm 。
所有PIN 针直径为φ2.95mm ,PIN 孔钻头与PIN 针径相同。
贴胶带作用:防止孔偏,防止板子松动,防止断针,固定铝片。
● 常用物料:1钻针針 2.铝板 3.木漿板 4.电木板 5.PIN 6.单面胶铝板功能是幫助钻头定位,並可加速散发钻头的高熱。
木漿板功能是避免钻到电木板,延长电木板壽命。
當钻头钻过板底時會钻过木漿板约40mil ,藉此避免未钻穿。
木漿板厚度约100mil ,所以一片木漿板可使用兩次。
廠內目前钻头尺寸-9.8mil~250mil木漿板 铝板板子电木板目的:使钻孔后的孔金属化,使各层相互导通。
一.流程:前处理→Desmear→PTH+CUI→整平→下工序1.前处理:入料→酸洗→循环水洗→180#下刷→180#上刷→320下刷→320#上刷→中压水洗→→高压水洗→超音波水洗→市水洗→吹干*2烘干→出料a.目的:1.通过酸洗清除板面氧化物,并利用机械刷磨使板面粗糙,让基板铜与镀铜结合良好.2.去除孔口巴厘、毛刺。
b.酸洗槽浓度3-5%2.Desmear:膨松槽→除胶渣→中和●目的: 钻孔时因钻头高速旋转,在孔壁形成环氧树脂钻污,常用KMnO4法处理:去除胶渣,使内层铜环显露出与后续之镀铜紧密结合,并能粗糙环氧树脂表面,提高镀铜与基体结合力及对活化钯的吸附量,并使内外层导通.(1)膨松:使环氧树脂溶胀,利于下步高锰酸钾对其攻击,药水含膨松剂与NaOH(2)KMnO4:在高温高碱环境下利用KMnO4Q强氧化除去孔壁环氧树脂(3)中和:除去孔内残留的锰酸根3.去脂整平→微蚀→酸洗→预活化→活化→速化→化学→镀铜→整板镀铜PTH(化学铜)说明(1)去脂平整:作用:去除表面油污、指印等.在板面形成一层带正电的皮膜,利于孔壁吸附活化槽带负电的Sn,Pd胶团。
(2)微蚀:为H2SO4+H2O2蚀刻掉Cu基体表面20-40u"的Cu层,使Cu箔表面粗糙,提高板面基铜与镀铜之结合力.(3)酸洗:去除微蚀时产生的铜盐,并对板子清洁处理作用,避免污染.(4)预活化:活化前处理与活化液配套使用,减少前面之药水对活化造成毒化、污染.保护活化而设。
5)活化:活化的作用是在绝缘基体上吸附一层具有催化能力的钯,使基体表面具有还原的能力.(6)速化处理:用酸将附着在钯团外的锡壳剥掉,露出钯原子,促使铜原子吸附.(7)化学镀铜.利用化学反应方式使孔内沉积一层化学CU,厚度在15-40 u".化学沉铜速率:●⑴将10*10CM光基板经前处理后,120℃、20MIN烘烤,分析天平称重W1。
●⑵取光基板走完PTH段取下。
●⑶120℃/20MIN烘干,分析天平称重W2。
●⑷沉铜速率计算(W2-W1)*224.215(标准:≥10u〃)化学镀Cu质量的验证.a.背光试验法:化学铜Cu后的试样沿一排测试孔的中心切下,并用细砂纸打磨切口处及其背部,将制作的试样放置在灯光台上,在显影放大镜下观察孔透光的情况,将孔积Cu的完整性分为若干级,a.内层板基材铜加厚:b.双面板基材铜加厚:发料→磨边→刷磨→PTH&CUⅠ→砂带研磨→钻孔→下工序镀铜参数:PTH&CUⅠ作业时,电流密度及镀铜时间分别为:H/H→1/1:10ASF±10%,83MIN1/1→2/2:20ASF±10%,83MIN3.镀铜流程:镀Cu→水洗CuI镀层要求均匀,细致,无麻点针孔,有良好的深镀能力,与基铜结合牢固,不会出现脱皮起泡、烧焦不良现象,镀Cu机理:含有硫酸Cu,硫酸的镀液,在直流电作用下,发生电极反应:阳极:CU-2e CU2+ ,阴极:CU2++2e CU镀液的成份与浓度控制:硫酸铜:80±10g/l硫酸:200±10g/l.CL-:45-60ppm,光泽剂控制在0.5%.主要成份为CuSO4.H2S04随着溶液中H2SO4浓度提高,CuSO4的溶解度降低,但导电性会提高,溶液中CuS04浓度太低,高电流区镀层易烧焦,浓度高,分散能力下降,CuS04控制在80±10 g/l ,H2SO4控制在200±10g/l.CL-控制在30-60ppm,光泽剂控制在0.5%.b. CL-:氯离子是阳极活化剂,协同添加剂使镀层光亮,CL-浓度太低,镀层中出现粗糙镀层花斑,氯离子浓度过高使镀层,失去光泽性c. 光泽剂:溶液中光泽剂浓度太低导致.镀层粗糙,光亮度、平整度差,当添加剂过多时阳极易产生纯化。
制程能力:板面与孔内镀层厚度接近1:1,镀层厚度在800-1600u“.(依据客户要求)镀层均匀性:>85%纵横比:6:14、整平机:目的去除板面氧化物并整平因镀铜时产生高低电流区之差异。
a、刷痕宽度控制在8—12mmB、烘干温度控制在85—95℃,以使板面与孔内烘干便于品检检验。
注:此机自动化程度高,会自行侦测板厚自动调整,刷毛厚度不足时侦测后会提示;常见问题:a、镀层针孔1、添加剂不足。