机加工危险源辨识
机械加工行业危险源辨识与控制清单
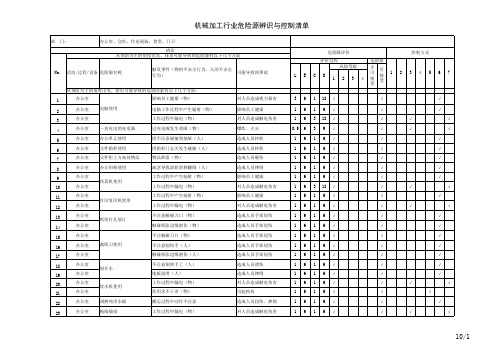
对人员造成伤害
作业现场 79
80
作业现场
清理金属切屑时用手拉或用嘴吹(人) 对人员造成伤害
没戴护目镜(人)
辐射
危险源评价
控制方式
评价过程
危险级
L
E
C
D
风险等级 1234
不 可 接 受
可 接 受
1
2
3
4
5
6
7
1 6 3 18 √ 1 6 3 18 √ 1 6 3 18 √ 1 6 3 18 √ 1 6 3 18 √ 1 6 3 18 √
造成职业病
造成人员伤害及财产损失 发生紧急情况增大损失与 应急救援难度 发生火灾时增加灭火难度 发生火灾时无法确保及时 灭火 造成人员滑倒伤害
造成人员砸伤
作业现场 50
设备接地不良,漏电,发生触电(物) 造成人员伤害
作业现场 51
转动部位楔子突出,无防护罩(物)
绞伤人体
作业现场 52
清洗铁屑无专用工具,操作者未戴护目镜 造成人员眼睛伤害
√
1 6 4 24
√
1 3 1 3√
1 6 1 6√
1 6 7 42
√
1 6 7 42
√
3 6 3 54
√
1 6 7 42
√
1 6 7 42
√
1 6 7 42
√
1 6 7 42
√
1 6 7 42
√
1 6 7 42
√
1 6 3 18 √
√ √ √ √ √ √ √ √ √
√
√
√
√ √ √ √ √ √
√
√
√
√
√
√
√
危险源辨识和风险评价清单(机加)
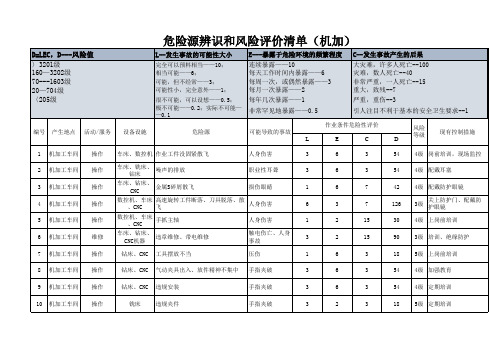
物品掉落 搬运撞伤 搬运撞伤 搬运撞伤 伤人
3
6
3
6
3
6
3
6
0.2
6
33 装配车间
操作
流水线 流水线接口处
易伤手
3
6
34 装配车间 35 装配车间 36 装配车间
操作 操作 操作
流水线 输送带变形 包装机 包装机堵塞时员工用手排除 打包机 打包机漏电
伤人,损坏产品 0.5
1
包装机温度很 高,易伤手
0.1
刀片
使用戒刀片、飞鹰刀片造成人员割 伤
锋利物切割伤
6
6
55 各车间 车间环境
地面
车间地面不平整、有杂物或较滑造 成人员摔倒
摔伤
3
6
56 各车间 车间环境
噪音
车间内机器设备产生的噪音造成听 力下降
噪音
3
6
57
各车间
车间环境
设备设施
车间内摆放的机器设备、办公设施 造成碰伤
碰伤
3
6
58 各车间 车间环境
化学品 使用饮料瓶装化学品
损伤眼睛
15
物品搬运
物料内部转 移
人工搬运
新上架的5G产品过重,搬运时会造 成身体损伤
职业病
16
物品搬运 出入库搬运
机动叉车
机动叉车行駛过快或超重驾驶;叉 运时未看清周边人及物
车辆伤害
17
物品搬运 出入库搬运
机动叉车
机动叉车所叉运物料未作防护,升 降时滑落
车辆伤害
18
物品搬运 出入库搬运
机动叉车
机动叉车驾驶人员没有驾驶证操作 不当
引人注目不利于基本的安全卫生要求--1
车工危险源辨识

检查和维护。
违规操作电气设备
危险源描述
未按照操作规程操作电气设备,如带电插拔插头、用湿手触摸电 器开关等,可能引发触电事故。
可能后果
人员触电伤亡,设备损坏,引发火灾等。
预防措施
严格遵守电气设备操作规程,禁止违规操作;加强员堆放不规范
安全隐患
操作人员对安全生产的重要性认识不足,缺乏必要 的安全意识和风险防范意识。
违规操作
操作人员违反安全操作规程,如未佩戴防护用品、 擅自离开工作岗位、随意调整设备参数等。
忽视安全警示
操作人员忽视设备或环境的安全警示标识,冒险进 行操作。
疲劳驾驶或酒后上岗
01
疲劳驾驶
操作人员长时间连续工作,导致 身体疲劳、注意力不集中,影响 判断和操作能力。
原材料堆放过高、不稳或堆放区域不 合理,可能导致材料倒塌、滑落或碰 撞,引发伤害事故。
预防措施
严格遵守物料堆放规定,确保原材料 堆放整齐、稳定,高度适中,远离通 道和设备,及时清理散落物料。
切削液使用不当
安全隐患
切削液使用不当可能导致皮肤、眼睛接触引起刺激或过敏,长时间吸入切削液 雾气还可能对呼吸系统造成危害。
粉尘堆积
长期通风不良会导致粉尘在车间内堆积,不仅影响设备的正常运行,还可能引发火灾或爆炸等安全事故。
温度过高或过低影响操作
温度过高
高温环境可能导致车工中暑、疲劳和注意力不集中,同时也会影响机械设备的正常运行 和寿命。
温度过低
低温环境可能使车工的手部僵硬、不灵活,从而降低操作的准确性和效率,同时低温还 可能对机械设备的性能产生不良影响。
05
环境因素类危险源
照明不足或眩光
照明不足
当工作区域的照明度不足时,车工可能无法清晰地看到工件和刀具的细节,从而增加操作失误的风险 。
立式车床危险源辨识及安全措施
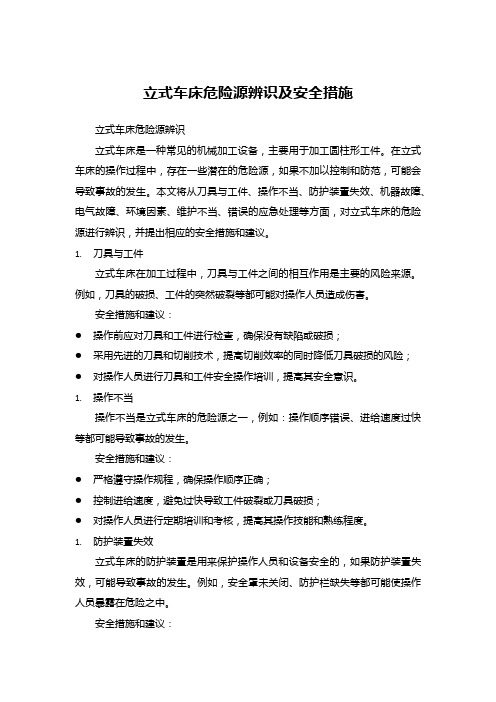
立式车床危险源辨识及安全措施立式车床危险源辨识立式车床是一种常见的机械加工设备,主要用于加工圆柱形工件。
在立式车床的操作过程中,存在一些潜在的危险源,如果不加以控制和防范,可能会导致事故的发生。
本文将从刀具与工件、操作不当、防护装置失效、机器故障、电气故障、环境因素、维护不当、错误的应急处理等方面,对立式车床的危险源进行辨识,并提出相应的安全措施和建议。
1.刀具与工件立式车床在加工过程中,刀具与工件之间的相互作用是主要的风险来源。
例如,刀具的破损、工件的突然破裂等都可能对操作人员造成伤害。
安全措施和建议:●操作前应对刀具和工件进行检查,确保没有缺陷或破损;●采用先进的刀具和切削技术,提高切削效率的同时降低刀具破损的风险;●对操作人员进行刀具和工件安全操作培训,提高其安全意识。
1.操作不当操作不当是立式车床的危险源之一,例如:操作顺序错误、进给速度过快等都可能导致事故的发生。
安全措施和建议:●严格遵守操作规程,确保操作顺序正确;●控制进给速度,避免过快导致工件破裂或刀具破损;●对操作人员进行定期培训和考核,提高其操作技能和熟练程度。
1.防护装置失效立式车床的防护装置是用来保护操作人员和设备安全的,如果防护装置失效,可能导致事故的发生。
例如,安全罩未关闭、防护栏缺失等都可能使操作人员暴露在危险之中。
安全措施和建议:●定期检查防护装置,确保其完整性和可靠性;●操作前应确认防护装置已经正确使用;●对防护装置进行定期维护和更新,确保其正常运转。
1.机器故障立式车床机器故障可能会导致设备损坏或产品质量下降,甚至可能引发事故。
例如,传动系统故障、轴承损坏等都可能影响设备的正常运行。
2.安全措施和建议:●定期对机器进行巡检和维护,确保其正常运行;●操作人员应熟悉立式车床常见故障识别和排除方法,以便及时处理问题;●建立机器故障报告制度,对故障进行记录和分析,及时采取预防措施。
1.电气故障立式车床的电气故障可能会导致设备损坏或操作人员触电等危险情况。
机加工区域危险源辨识与风险评价表

金工工段
C
金工工段现场
旋转设备、绞伤、划伤、撞伤
穿戴劳保用品、严格按操作规程操作,提高自身安全防护意识、加强检查、加强管理,发现隐患立即整改
3
金工工段
B
金工工段现场
行车吊物、撞伤
穿戴劳保用品、严格按操作规程操作,提高自身安全防护意识、加强特种设备的点巡检工作、加强管理,发现隐患、立即整改。
机加工区域危险源辨识与风险评价
机加工危险源点、单位:
编号:Q/DS JL51—2014
序号
危险源点名称
级别
危险源所在位置
存在的主要危害
主要控制措施
工段责任人
班组责任人
备注
1
油库
C
油库房
火灾、爆炸
配备灭火器材。油库内严禁烟火、明火,无关人员禁止入内。加强检查防止柴油、润滑油跑、冒、滴、漏。加强安全培训、严格检查,严格管理,发现隐患、立即整改。
机械车间危险因素识别、风险评估记录

机械车间危险因素识别、风险评估记录1. 引言本文档旨在识别和评估机械车间存在的危险因素,以便采取适当的措施来保障工人的安全和健康。
通过详细评估危险因素,我们可以有效地减少事故和伤害事件的发生。
2. 危险因素识别2.1 机械设备对机械车间的机械设备进行分析,识别潜在的危险因素,如旧化设备、缺乏安全保护装置、容易发生故障等。
2.2 作业环境评估机械车间的作业环境,考虑因素包括但不限于噪音、振动、有害化学物质、高温环境等。
确保作业环境符合相关安全标准,避免对工人的健康造成不良影响。
2.3 人为因素分析机械车间中的人为因素,包括工人的行为、培训水平、安全意识等。
识别潜在的不安全操作行为和行为惯,采取必要的培训和教育措施,提高工人的安全意识。
3. 风险评估3.1 风险辨识基于危险因素的识别结果,对每个危险因素评估其潜在风险。
根据可能性和严重性分级,确定高风险和低风险因素,以便优先处理高风险因素。
3.2 风险评估对高风险因素进行进一步的风险评估,考虑控制措施的有效性和成本效益。
制定风险管理计划,明确控制措施和责任分工。
3.3 监测和审查建立监测和审查机制,定期检查机械车间的危险因素和风险控制措施的有效性。
根据监测结果对控制措施和风险管理计划进行调整和改进。
4. 结论机械车间危险因素识别、风险评估记录是保障工人安全和健康的重要工作。
通过识别危险因素并采取适当的控制措施,我们能够预防事故的发生,并创造一个安全的工作环境。
> 注:本文档旨在提供指导和建议,并不涉及具体法律问题。
在制定和实施相关措施时,请遵守当地的法律法规。
机加工行业危险源辨识与风险评价清单

机加工行业危险源辨识与风险评价清单机加工作为制造业的重要产业之一,在工业生产中起着至关重要的作用。
机加工涉及到多种机器和设备的使用,所以危险源的出现是不可避免的。
机加工行业的从业人员在日常工作中需要对危险源进行辨识和评价,以保证自身安全和生产环境的安全。
本文将详细介绍机加工行业常见危险源和相应的辨识与评价方法。
常见危险源1. 机器运转危险机加工中使用的设备通常包括摩托车、车床、磨床、铣床、冲床、钻床等机器,这些机器在运转时都会产生运转危险。
运转危险主要包括:•失控引起的伤害:机器在工作时可能受到突然的压力或扭矩,导致设备失控,可能会造成伤害。
•机械碰撞:机器工作时突然出现故障或不稳定,导致不同部件之间发生机械碰撞,可能会造成伤害。
•非预期操作:由于各种原因,从业人员可能会进行非预期操作,如手指、头部等进入机器运转区域,可能造成伤害。
2. 化学品危险机加工行业常常使用液态和气态化学品,如燃油、切削液、酸、碱等。
化学品在使用过程中可能产生蒸气、烟雾、溅泼等,可能会对从业人员的健康造成损害。
化学品危险主要包括:•吸入危险:吸入有毒气体、蒸汽或烟雾,可能造成呼吸系统损伤。
•皮肤接触危险:长期接触某些化学品,可能导致皮肤损伤,如过敏性皮炎等疾病。
•溅泼危险:化学品可能会不慎溅泼到身体、眼睛、呼吸器官等部位,造成损伤。
3. 物理危险机加工行业工作环境中存在着各种物理危险,如机器偏差、电击、热危险和噪声危险等。
物理危险主要包括:•电击危险:机器设备通常都带有电器组件,不慎接触可能导致触电事故。
•热危险:机器工作时可能产生高温或火源,可能会导致火灾等事故。
•声音危险:机器在工作时发出巨大的噪音,可能会对从业人员的身体造成损害。
危险源辨识与风险评价方法危险源的辨识和风险评价非常重要,其中危险源辨识是指发现环境中存在的潜在危险因素,而风险评价则是对危险源分析其可能造成的影响和概率,以确定其具体的等级和控制需求。
下面是机加工行业危险源辨识和风险评价的方法:1. 危险源辨识•做好机加工设备状态检查,保证设备在工作前已经对其进行维护和保养。
危险源辨识和风险评价记录
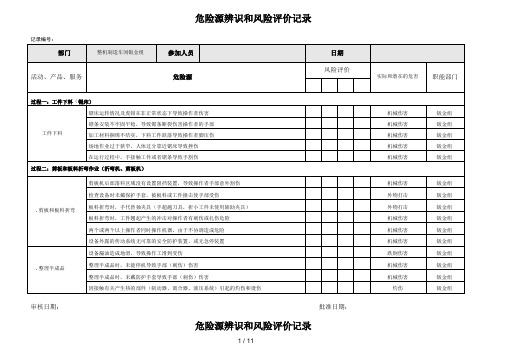
危险源辨识和风险评价记录
审核日期:批准日期:
危险源辨识和风险评价记录
1 / 11
批准日期:
危险源辨识和风险评价记录
审核日期:
批准日期:
危险源辨识和风险评价记录
记录编号:
审核日期:
批准日期:审核日期:
危险源辨识和风险评价记录
记录编号:
批准日期:
危险源辨识和风险评价记录
记录编号:
审核日期:
审核日期:批准日期:
危险源辨识和风险评价记录
记录编号:
批准日期:
危险源辨识和风险评价记录
记录编号:
审核日期:
批准日期:
危险源辨识和风险评价记录
记录编号:
审核日期:
审核日期:批准日期:
危险源辨识和风险评价记录
记录编号:
批准日期:
审核日期:
危险源辨识和风险评价记录
批准日期:审核日期:。
- 1、下载文档前请自行甄别文档内容的完整性,平台不提供额外的编辑、内容补充、找答案等附加服务。
- 2、"仅部分预览"的文档,不可在线预览部分如存在完整性等问题,可反馈申请退款(可完整预览的文档不适用该条件!)。
- 3、如文档侵犯您的权益,请联系客服反馈,我们会尽快为您处理(人工客服工作时间:9:00-18:30)。
车床危险源辨识
1、防护用品使用不当(戴手套操作,衣袖、衣襟不紧)易发生绞手,缠卷衣袖危险。
2、安全防护装置有缺陷或被拆卸产生不安全隐患。
3、用手直接抓砂布在工件上磨光;隔着正在加工的工件拿取物体;在加工过程中清理刀具上的铁屑、在切削过程中测量工件,擦试机床等,易发生碾、碰、割伤害事故。
4、加工细长件超过主轴后200mn没有加设防护装置,可发生甩
击伤害。
5、卡具装卡不牢或卡压方法不合理。
转动的工、卡具、工件飞出导致事故。
6、加工偏心工件时,没有做好平衡配重,致使工件飞出,造成
物体打击事故。
7、卡盘保险销子没有锁紧,工、卡具、工件飞出伤人。
8工、卡、量具摆放顺序交叉,混放不符合要求产生隐患。
9、吊卸工卡具、工件时不符合起重作业安全要求,发生起重伤害。
10、高速切削时未戴防护眼镜、工件未夹紧、用砂布光内孔时,将手指或手臂伸进工件打磨、切断小料时用手接、戴手套操作、切大料时直接切断、一手扶攻丝架(后扳牙架)一手开车会造成机械伤害。
11、机床接地不好,照明灯线裸露,照明未采用安全电压均易生触电事故。
立式车床危险源辨识
1、卡具装卡不牢或卡压方法不合理,卡盘上有浮动物件,浮动物件甩出造伤害。
2、未调整工件与刀架间距,刀架与工件相撞造成伤害。
3、卡盘爪或压板超出卡盘,发生刮衣将人绞入。
4、没有穿戴好防护用品或操作不当,易伤人。
5、防护用品使用不当(戴手套操作,衣袖、衣襟不紧)易发生绞手,缠卷衣袖危险。
6、吊卸工卡具、工件时不符合起重作业安全要求,发生起重伤害。
7、机床接地不好;照明灯线裸露,照明未采用安全电压,易发生触电伤害。
钻床危险源辨识
1、防护用品使用不当(戴手套操作,衣袖、衣襟不紧)易发生绞手,缠卷衣袖危险。
2、用手扶工件、用手清除铁屑划伤手指;
3、在旋转的刀具下,翻转、卡压或测量工件会造成机械伤害。
4、工卡具装卡不牢,飞出伤人;
5、员工操作不当或操作失误,造成设备损坏或人身伤害。
7、工件超出操作平台尺寸时支撑架要平稳牢靠,如有摆动或滑移
现象易造成重物伤害。
8机床接地不好;照明灯线裸露,照明未采用安全电压,易发生触电伤害。
龙门刨床危险源辨识
1、龙门刨行程开关,牛头刨行程限位失灵,工作台、滑枕
在运行中挤压人造成伤害。
2、牛头刨滑枕行程方向观察工件,挤压伤人。
3、刨削量过大使工件松动,刀具碎断崩人。
4、夹具、刀具有缺陷。
刀具和工件装卡不牢,刨削中工、
卡、刀具、工件飞出伤人。
5、龙门刨刀架摇把,牛头刨虎钳板子、手柄等用后未及时
取下,手柄甩击伤人。
6、工作台面上浮放工具,工件,易被碰撞坠落砸人。
7、工具、工件摆放不平稳,倾倒伤人。
&吊卸工、卡具、工件时,不符合起重作业安全要求,造成起重伤害。
9、没有穿戴好防护用品导致起重的伤害。
10、操作不当发生不安全隐患。
11、机床接地不好,照明灯线裸露,照明未采用安全电压均
易发生触电事故。
铣床危险源辨识
1、防护用品使用不当(未戴防护帽,戴手套操作,袖口未扎紧),
手拿棉纱操作,易发生铣刀绞手、缠卷衣袖,导致碾、碰、绞割伤害。
2、铣削过程中测量工件、拆卸工作,擦试机床及用手清理铁屑等,
易发生机器、工具伤害事故。
3、进刀量大,使工件松动或刀具碎断,发生工件,刀具破碎飞出造
成事故。
4、夹具、刀具有缺陷,造成工件、破碎刀具飞出伤人。
5、装卡方法不正确或卡紧力不够,使工件或刀具装卡不牢,造成坠
落伤人事故。
6、工作面上浮放工具,工件被碰撞坠落伤人。
7、工具、工件摆放不平衡致使倾倒伤人。
8吊卸工、卡具、工件时不符合起重作业安全要求,造成起重伤害。
9、没有穿戴好防护用品,致使人体防护失效,金属铁屑伤人。
10、操作不当,产生不安全隐患。
11、机床接地不好,照明灯线裸露,未采用安全电压,易造成触电伤
害。
镗床危险源辨识
1、滑块楔铁、刀杆顶丝销子松动,转动的偏心盘滑动、刃具飞出,镗杆有突出螺钉伤人。
2、工作台未开到机床中心位置,有关人员未站在安全位置,回转台转动工件时挤伤人。
3、螺栓、压板、垫铁、方箱等摆放位置不当,坠落伤人。
4、未穿防护鞋,脚的防护失效易被砸伤。
5、违反起重作业安全操作规程。
在卸工件时未用吊车吊住,就松开压板,螺栓工件,卡具工具等坠落伤人。
6、工卡刃具摆放不符合要求,倾倒伤人。
7、吊卸工卡具工件时不符起重作业安全要求。
8防护用品使用不当(戴手套操作,衣袖、衣襟不紧)易发生绞手,缠卷衣袖或人身事故危险。
10、操作不当导致的不安全隐患。
11、机床接地不好,照明灯线线裸露,照明未采用安全电压均易发
生触电。
磨床危险源辨识
1、护罩损坏或被拆除,砂轮破碎飞出易造成“物体打击”事故。
2、砂轮有裂纹、损伤,砂轮破碎飞出造成事故。
3、砂轮安装有缺陷(装夹不牢、不平衡、卡装过紧)易造成磨伤或破碎事故。
4、磨削量过大或行程速度超速易发生砂轮破碎伤人事故。
5、设备缺陷(液压系统故障、行程限位失灵、滚刀磨分度不准等)均产生不安全隐患。
6、工具,工件装卡不牢,工件飞出伤人。
7、胎具顶尖有缺陷,工件飞出伤人。
8工作台面有浮放工具、工件被碰撞坠落伤人。
9、工件摆放不平衡坠落伤人。
10、吊卸工、卡具、工件时不符合起重作业安全要求,易发生起重伤害事故。
11、机床接地不好,照明灯线裸露,照明未采用安全电压发生触
电。
插床危险源辨识
1、头部伸入滑枕行程内观察加工件,导致头部受到机器、工具的伤害。
2、用手触摸加工件、测量工件、清量切屑,使手部发生伤害事故。
3、插头有裂纹等缺陷,导致运行中插头折断发生事故。
4、插削量过大,致使插刀折断,造成事故。
5、插刀伸出刀杆过长导致伤害事故。
6、插刀装卡不牢,致使插刀飞出,造成物体打击事故。
7、工作台面上浮放的工具,工件被碰撞坠落,导致砸伤事故。
8工具、工件摆放不平稳,导致工件倾倒伤人事故。
9、吊卸工具、工件时不符合起重作业安全要求,易发生起重伤害事故。
10、没有穿戴好防护用品,导致人体防护失效,金属铁屑伤人。
11、操作不当,易发生不安全隐患。
12、机床接地不好,照明灯线裸露,照明不符安全电压,易造成触
电伤害。
砂轮机危险源辨识
1、罩与砂轮间隙不匹配,装夹砂轮片不符合要求,易夹碎砂轮,碎块飞出伤人。
2、防护装置强度不够或拆卸防护装置,一旦砂轮破碎时飞出崩伤面部及眼睛,甚至致死。
3、档板与砂轮间隙过大(间隙不超3-5毫米),磨刀时伤手。
4、站在砂轮机的正前方操作未定期更换砂轮片碎裂飞出导致人身事故。
5、未戴防护眼镜刃磨,砂轮和物料碎屑飞入眼睛,导致眼睛受伤。
6、打磨细小的、大的和不好拿的工件磨伤手指。
7、砂轮受潮、沾水后继续使用导致机械伤害。
8砂轮磨损严重或径向跳动过大、震动大时继续使用会导致机械伤害。
9、更换有裂纹或有缺陷的砂轮,破裂飞出导致人身事故。