碟形弹簧疲劳失效
碟形弹簧设计手册
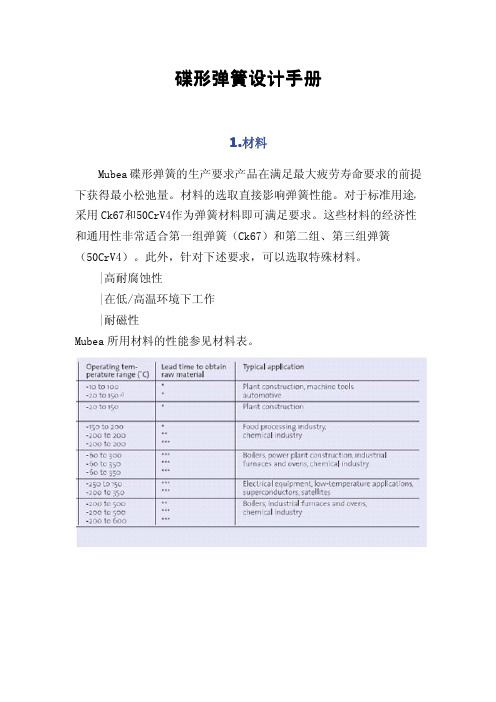
碟形弹簧设计手册1.材料Mubea碟形弹簧的生产要求产品在满足最大疲劳寿命要求的前提下获得最小松弛量。
材料的选取直接影响弹簧性能。
对于标准用途,采用Ck67和50CrV4作为弹簧材料即可满足要求。
这些材料的经济性和通用性非常适合第一组弹簧(Ck67)和第二组、第三组弹簧(50CrV4)。
此外,针对下述要求,可以选取特殊材料。
|高耐腐蚀性|在低/高温环境下工作|耐磁性Mubea所用材料的性能参见材料表。
2.材料与防腐蚀2.1标准材料Ck67(DIN1.1231)Ck67是碟形弹簧低应力应用情况下的经济型钢种,按DIN2093标准规定,该材料只适用于第一组弹簧(厚度<1.25mm)。
特殊情况下,也可用于厚度小于4mm的弹簧。
50CrV4(DIN1.8159)50CrV4是碟形弹簧最常用的材料。
由于其高合金成分,在-15℃至+150℃温度范围时,可使弹簧具有最佳性能。
如可降低弹簧耐久性,该材料最低应帮温度可达成-25℃,如采用热强压处理,其最高应用温度+200℃。
该材料抗松驰性能优于非合金钢。
51CrMoV4(DIN1.7701)51CrMoV4(DIN1.7701)性能与50CrV41(8159)相似。
由于加入了钼合金元素,材料厚度在40mm以下的工件均具有良好的淬透性。
由于其韧性优于50CrV4。
因此该材料更适用于0℃至-20℃温度范围。
2.2耐磨性材料由于较高的镍合金含量,耐腐性材料在初始状态下具有奥氏体晶格,因此不能象常规材料那样采用奥氏体或马氏体等温淬火。
而腐蚀弹簧钢通过混合晶体变形、冷轧加工硬化(见DIN17224)和沉淀硬化(х7CrNiAl177)来获得强度。
一定程度的冷扎加工硬化可使碟型弹簧获得足够的强度。
因此,对该种材料的最大厚度有严格的限制。
耐腐蚀材料碟型弹簧可以在极低温度下使用,但其通过冷轧过程获得的强度会在温度高于+200℃时消失。
х12CrNi177(DIN1.4310)DIN17224标准的镍铬金х12CrNi177通常用于耐腐的碟型弹簧。
碟簧的疲劳曲线
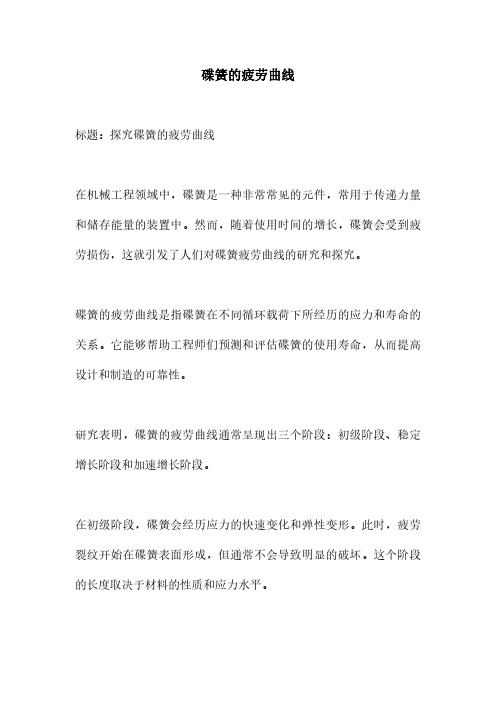
碟簧的疲劳曲线标题:探究碟簧的疲劳曲线在机械工程领域中,碟簧是一种非常常见的元件,常用于传递力量和储存能量的装置中。
然而,随着使用时间的增长,碟簧会受到疲劳损伤,这就引发了人们对碟簧疲劳曲线的研究和探究。
碟簧的疲劳曲线是指碟簧在不同循环载荷下所经历的应力和寿命的关系。
它能够帮助工程师们预测和评估碟簧的使用寿命,从而提高设计和制造的可靠性。
研究表明,碟簧的疲劳曲线通常呈现出三个阶段:初级阶段、稳定增长阶段和加速增长阶段。
在初级阶段,碟簧会经历应力的快速变化和弹性变形。
此时,疲劳裂纹开始在碟簧表面形成,但通常不会导致明显的破坏。
这个阶段的长度取决于材料的性质和应力水平。
随着循环载荷的增加,碟簧进入稳定增长阶段。
在这个阶段,疲劳裂纹逐渐扩展,但扩展速率相对较慢。
碟簧的寿命在此阶段内可以预测和估计。
然而,当循环载荷进一步增加时,碟簧将进入加速增长阶段。
在这个阶段,疲劳裂纹扩展速率急剧增加,导致碟簧的使用寿命迅速减少。
此时,碟簧可能会发生破裂和失效。
为了减少碟簧的疲劳损伤,工程师们采取了一系列的措施。
首先,合理选取材料,使用高强度和耐久性的合金材料可以延长碟簧的使用寿命。
其次,优化设计,减少应力集中和边缘效应,有助于降低疲劳裂纹的形成和扩展。
此外,定期检查和维护碟簧,及时更换疲劳严重的元件,也是确保碟簧正常运行的重要步骤。
总之,了解和研究碟簧的疲劳曲线对于设计和制造工程师来说至关重要。
通过预测和评估碟簧的使用寿命,可以提高机械装置的可靠性和安全性。
然而,在使用碟簧时,也需要注意适当的材料选择、设计优化和定期维护,以减少疲劳损伤的发生。
这样才能保证碟簧在工作过程中始终保持稳定和可靠的性能。
碟簧的许用应力和疲劳极限

通用计算
h0t^3/(K1D^2) 0.004840567 计算压并负荷Fc4572.341136 N 905494.5055 4E/(1-u²) t^4/(K1*D²) 0.002862594 f/t(K4^2(h0/t-f/t)(h0/t-f/2t)+1) 1.86727075 计算负荷F1 5049.047375 N -0.797296971 (h0/t)²-3h0f/t²+1.5*(f/t)² 0.000993956 t³/(K1*D²) 碟簧刚度F` 157.9954661 N/mm 452747.2527 2E/1-u² t^5/(K1*D²) 0.008244272 2.428339214 K4²(h0/t-f/2t)²+1 碟簧变形能U 10259.62603 N.mm 905495 4E/(1-u²) 0.00035 t²/(K1D²) 计算应力σ OM -317.66 N/mm² K4K2(ho/t-f/2t) 1.3257 计算应力σ Ⅰ -838.09 N/mm² 计算应力σ Ⅱ -43.444 N/mm² K4(K2-2K3)(h0/t-f/2t) -1.5307 计算应力σ Ⅲ 588.339 N/mm² 计算应力σ Ⅳ 72.4604 N/mm²
碟簧通用计算
外径D 内径d 中性径D0 厚度t D/t ho`/t 已知 t`/t 条件 减薄厚度t` 单片自由高H0 压平变形量h0` 弹性模量E 泊松比υ 变形量f 变形量0.75h0` 209.8 mm 136.2 mm 170.4 mm 3 mm 69.93 1.623 0.96 2.88 mm 7.75 mm 4.87 mm 2E+05 N/mm² 0.3 3 mm 3.563 mm 直径比C 1.5404 lnC 0.432 [(C-1)/C]^2 0.1231 (C+1)/(C-1)-2/lnC 0.0718 系数K1 0.546 (C-1)/lnC-1 0.2508 系数K2 1.1092 系数K3 1.195 (1/4)*(H0/t)-t`/t+3/4 0.4358 (5/8)*(H0/t)-t`/t+3/8 1.0296 系数C1 2.0538 5/32*(H0/t-1)^2+1 1.3917 系数C2 3.2307 [(C1/2)^2+C2]^(1/2) 2.0701 系数K4 1.0214
机床主轴拉刀机构的解决方法
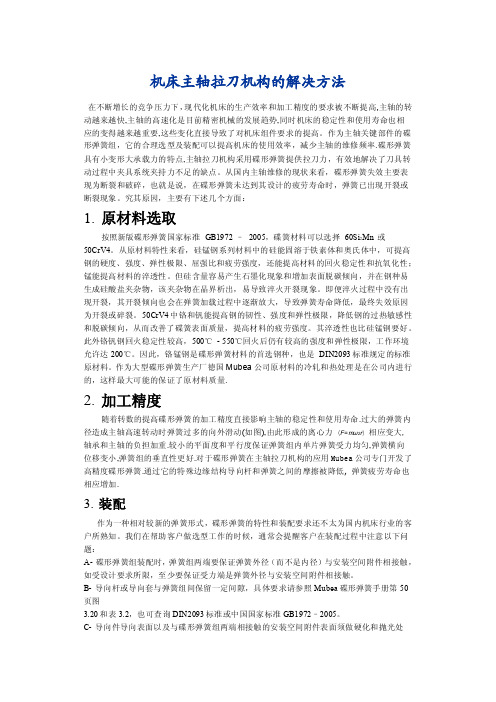
机床主轴拉刀机构的解决方法在不断增长的竞争压力下,现代化机床的生产效率和加工精度的要求被不断提高,主轴的转动越来越快,主轴的高速化是目前精密机械的发展趋势,同时机床的稳定性和使用寿命也相应的变得越来越重要,这些变化直接导致了对机床组件要求的提高。
作为主轴关键部件的碟形弹簧组,它的合理选型及装配可以提高机床的使用效率,减少主轴的维修频率.碟形弹簧具有小变形大承载力的特点,主轴拉刀机构采用碟形弹簧提供拉刀力,有效地解决了刀具转动过程中夹具系统夹持力不足的缺点。
从国内主轴维修的现状来看,碟形弹簧失效主要表现为断裂和破碎,也就是说,在碟形弹簧未达到其设计的疲劳寿命时,弹簧已出现开裂或断裂现象。
究其原因,主要有下述几个方面:1. 原材料选取按照新版碟形弹簧国家标准GB1972 –2005,碟簧材料可以选择60Si2Mn 或50CrV4。
从原材料特性来看,硅锰钢系列材料中的硅能固溶于铁素体和奥氏体中,可提高钢的硬度、强度、弹性极限、屈强比和疲劳强度,还能提高材料的回火稳定性和抗氧化性;锰能提高材料的淬透性。
但硅含量容易产生石墨化现象和增加表面脱碳倾向,并在钢种易生成硅酸盐夹杂物,该夹杂物在晶界析出,易导致淬火开裂现象。
即便淬火过程中没有出现开裂,其开裂倾向也会在弹簧加载过程中逐渐放大,导致弹簧寿命降低,最终失效原因为开裂或碎裂。
50CrV4中铬和钒能提高钢的韧性、强度和弹性极限,降低钢的过热敏感性和脱碳倾向,从而改善了碟簧表面质量,提高材料的疲劳强度。
其淬透性也比硅锰钢要好。
此外铬钒钢回火稳定性较高,500℃- 550℃回火后仍有较高的强度和弹性极限,工作环境允许达200℃。
因此,铬锰钢是碟形弹簧材料的首选钢种,也是DIN2093标准规定的标准原材料。
作为大型碟形弹簧生产厂德国Mubea公司原材料的冷轧和热处理是在公司内进行的,这样最大可能的保证了原材料质量.2. 加工精度随着转数的提高碟形弹簧的加工精度直接影响主轴的稳定性和使用寿命.过大的弹簧内径造成主轴高速转动时弹簧过多的向外滑动(如图),由此形成的离心力(F=mω2r) 相应变大,轴承和主轴的负担加重.较小的平面度和平行度保证弹簧组内单片弹簧受力均匀,弹簧横向位移变小,弹簧组的垂直性更好.对于碟形弹簧在主轴拉刀机构的应用Mubea公司专门开发了高精度碟形弹簧.通过它的特殊边缘结构导向杆和弹簧之间的摩擦被降低, 弹簧疲劳寿命也相应增加.3. 装配作为一种相对较新的弹簧形式,碟形弹簧的特性和装配要求还不太为国内机床行业的客户所熟知。
碟形弹簧标准

碟形弹簧标准一、外径(Outer Diameter)碟形弹簧的外径是指弹簧的最大直径,通常用D表示。
外径是碟形弹簧的重要参数之一,直接影响着弹簧的刚度和承载能力。
在标准中,外径的值是根据载荷和厚度计算得出的。
二、内径(Inner Diameter)碟形弹簧的内径是指弹簧的最小直径,通常用d表示。
内径的大小取决于所需安装尺寸和材料的强度。
在标准中,内径的值是根据安装尺寸和厚度计算得出的。
三、厚度(Thickness)碟形弹簧的厚度是指弹簧的直径差值,通常用t表示。
厚度是碟形弹簧的重要参数之一,直接影响着弹簧的刚度和疲劳寿命。
在标准中,厚度的值是根据载荷和外径计算得出的。
四、材料(Material)碟形弹簧的材料直接影响着其性能和使用寿命。
常用的材料有不锈钢、碳钢、合金钢等。
在标准中,应根据载荷、工作环境等因素选择合适的材料。
五、载荷(Load)碟形弹簧的载荷是指弹簧所承受的力的大小。
在标准中,载荷的值是根据使用要求和设计计算得出的。
载荷的大小直接影响着弹簧的刚度和承载能力。
六、刚度(Stiffness)碟形弹簧的刚度是指弹簧的抗变形能力。
在标准中,刚度的值是根据载荷和厚度计算得出的。
刚度的大小直接影响着弹簧的精度和使用效果。
七、疲劳寿命(Fatigue Life)碟形弹簧的疲劳寿命是指弹簧在交变载荷作用下能够维持一定性能的循环次数。
在标准中,疲劳寿命的值是根据实验测试得出的。
疲劳寿命的长短直接影响着弹簧的使用寿命和安全性。
八、安装尺寸(Installation Size)碟形弹簧的安装尺寸是指弹簧在安装过程中所需的尺寸。
在标准中,安装尺寸的值是根据实际需求和设计计算得出的。
安装尺寸的准确性直接影响着弹簧的安装和使用效果。
弹簧的分类性能要求失效形式应用常见弹簧钢弹性合金
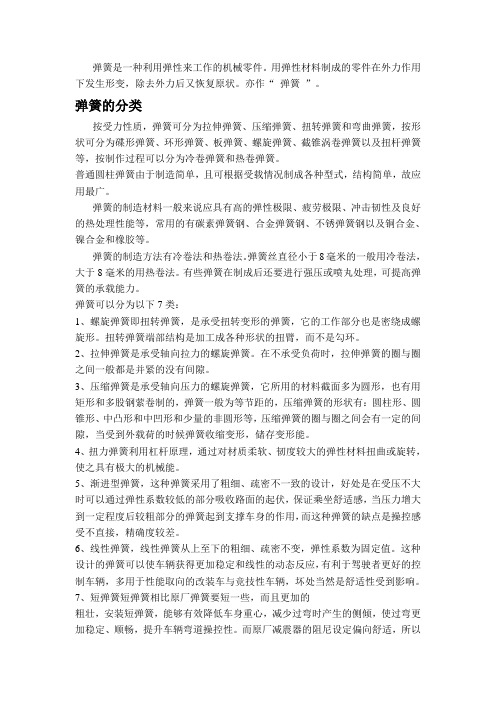
弹簧是一种利用弹性来工作的机械零件。
用弹性材料制成的零件在外力作用下发生形变,除去外力后又恢复原状。
亦作“弹簧”。
弹簧的分类按受力性质,弹簧可分为拉伸弹簧、压缩弹簧、扭转弹簧和弯曲弹簧,按形状可分为碟形弹簧、环形弹簧、板弹簧、螺旋弹簧、截锥涡卷弹簧以及扭杆弹簧等,按制作过程可以分为冷卷弹簧和热卷弹簧。
普通圆柱弹簧由于制造简单,且可根据受载情况制成各种型式,结构简单,故应用最广。
弹簧的制造材料一般来说应具有高的弹性极限、疲劳极限、冲击韧性及良好的热处理性能等,常用的有碳素弹簧钢、合金弹簧钢、不锈弹簧钢以及铜合金、镍合金和橡胶等。
弹簧的制造方法有冷卷法和热卷法。
弹簧丝直径小于8毫米的一般用冷卷法,大于8毫米的用热卷法。
有些弹簧在制成后还要进行强压或喷丸处理,可提高弹簧的承载能力。
弹簧可以分为以下7类:1、螺旋弹簧即扭转弹簧,是承受扭转变形的弹簧,它的工作部分也是密绕成螺旋形。
扭转弹簧端部结构是加工成各种形状的扭臂,而不是勾环。
2、拉伸弹簧是承受轴向拉力的螺旋弹簧。
在不承受负荷时,拉伸弹簧的圈与圈之间一般都是并紧的没有间隙。
3、压缩弹簧是承受轴向压力的螺旋弹簧,它所用的材料截面多为圆形,也有用矩形和多股钢萦卷制的,弹簧一般为等节距的,压缩弹簧的形状有:圆柱形、圆锥形、中凸形和中凹形和少量的非圆形等,压缩弹簧的圈与圈之间会有一定的间隙,当受到外载荷的时候弹簧收缩变形,储存变形能。
4、扭力弹簧利用杠杆原理,通过对材质柔软、韧度较大的弹性材料扭曲或旋转,使之具有极大的机械能。
5、渐进型弹簧,这种弹簧采用了粗细、疏密不一致的设计,好处是在受压不大时可以通过弹性系数较低的部分吸收路面的起伏,保证乘坐舒适感,当压力增大到一定程度后较粗部分的弹簧起到支撑车身的作用,而这种弹簧的缺点是操控感受不直接,精确度较差。
6、线性弹簧,线性弹簧从上至下的粗细、疏密不变,弹性系数为固定值。
这种设计的弹簧可以使车辆获得更加稳定和线性的动态反应,有利于驾驶者更好的控制车辆,多用于性能取向的改装车与竞技性车辆,坏处当然是舒适性受到影响。
碟形弹簧标准
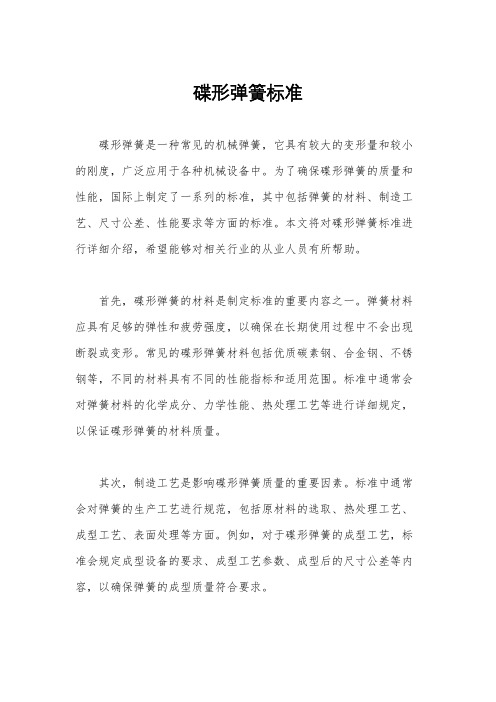
碟形弹簧标准碟形弹簧是一种常见的机械弹簧,它具有较大的变形量和较小的刚度,广泛应用于各种机械设备中。
为了确保碟形弹簧的质量和性能,国际上制定了一系列的标准,其中包括弹簧的材料、制造工艺、尺寸公差、性能要求等方面的标准。
本文将对碟形弹簧标准进行详细介绍,希望能够对相关行业的从业人员有所帮助。
首先,碟形弹簧的材料是制定标准的重要内容之一。
弹簧材料应具有足够的弹性和疲劳强度,以确保在长期使用过程中不会出现断裂或变形。
常见的碟形弹簧材料包括优质碳素钢、合金钢、不锈钢等,不同的材料具有不同的性能指标和适用范围。
标准中通常会对弹簧材料的化学成分、力学性能、热处理工艺等进行详细规定,以保证碟形弹簧的材料质量。
其次,制造工艺是影响碟形弹簧质量的重要因素。
标准中通常会对弹簧的生产工艺进行规范,包括原材料的选取、热处理工艺、成型工艺、表面处理等方面。
例如,对于碟形弹簧的成型工艺,标准会规定成型设备的要求、成型工艺参数、成型后的尺寸公差等内容,以确保弹簧的成型质量符合要求。
此外,尺寸公差是衡量碟形弹簧质量的重要指标之一。
标准中通常会对碟形弹簧的尺寸公差进行严格规定,以确保弹簧在装配时能够达到预期的功能要求。
尺寸公差包括弹簧的外径、内径、厚度、圈数等方面,标准中通常会规定不同工作条件下的尺寸公差范围,以满足不同需求。
最后,性能要求是衡量碟形弹簧质量的关键指标之一。
标准中通常会对碟形弹簧在使用过程中的性能要求进行详细规定,包括弹簧的载荷-变形特性、疲劳寿命、表面状态、耐腐蚀性能等方面。
这些性能要求是确保碟形弹簧在实际使用中能够可靠工作的重要保障。
综上所述,碟形弹簧标准涉及到弹簧材料、制造工艺、尺寸公差、性能要求等多个方面,对于保证碟形弹簧的质量和性能具有重要意义。
遵循标准制定的要求,能够帮助企业提高产品质量,确保用户的安全和可靠性。
因此,对于从事碟形弹簧生产和应用的相关行业人员来说,熟悉并遵循碟形弹簧标准是至关重要的。
希望本文能够对大家有所帮助,谢谢阅读。
绞车的检查维护及常见故障
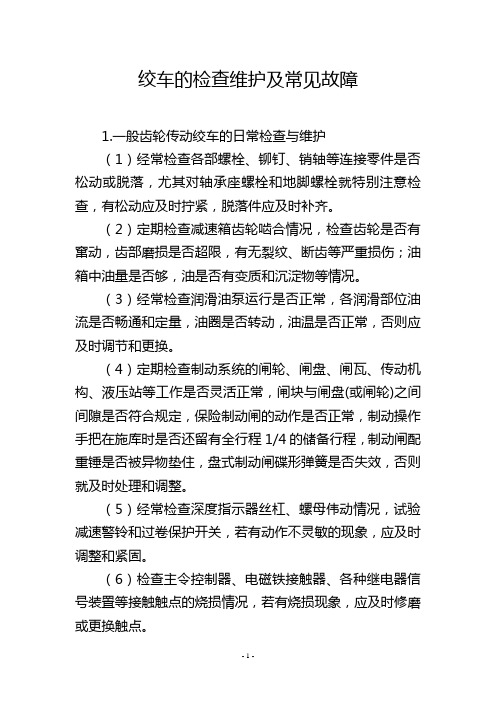
绞车的检查维护及常见故障1.一般齿轮传动绞车的日常检查与维护(1)经常检查各部螺栓、铆钉、销轴等连接零件是否松动或脱落,尤其对轴承座螺栓和地脚螺栓就特别注意检查,有松动应及时拧紧,脱落件应及时补齐。
(2)定期检查减速箱齿轮啮合情况,检查齿轮是否有窜动,齿部磨损是否超限,有无裂纹、断齿等严重损伤;油箱中油量是否够,油是否有变质和沉淀物等情况。
(3)经常检查润滑油泵运行是否正常,各润滑部位油流是否畅通和定量,油圈是否转动,油温是否正常,否则应及时调节和更换。
(4)定期检查制动系统的闸轮、闸盘、闸瓦、传动机构、液压站等工作是否灵活正常,闸块与闸盘(或闸轮)之间间隙是否符合规定,保险制动闸的动作是否正常,制动操作手把在施库时是否还留有全行程1/4的储备行程,制动闸配重锤是否被异物垫住,盘式制动闸碟形弹簧是否失效,否则就及时处理和调整。
(5)经常检查深度指示器丝杠、螺母伟动情况,试验减速警铃和过卷保护开关,若有动作不灵敏的现象,应及时调整和紧固。
(6)检查主令控制器、电磁铁接触器、各种继电器信号装置等接触触点的烧损情况,若有烧损现象,应及时修磨或更换触点。
(7)检查钢丝绳在滚筒上缠绕是否整齐,绳头固定是否牢固,查看钢丝绳断和磨损的检查记录。
(8)检查联轴器是否松旷、变形和缺件,检查联轴器轴向窜量和间隙,径向位移和端面倾斜是否符合要求,更换损坏的弹性胶圈,补齐已脱落的销子、螺母、垫圈等紧固件。
(9)经常擦试设备,清扫浮尘杂物,保持机亮地净。
2.防爆液压绞车的日常检查与维护(1)认真检查绞车各部螺栓、销子、螺母等连接件是否有松动、脱落现象,发现问题及时处理。
(2)在无提升负荷时检查盘形制动闸松闸均匀程度,保证间隙基本相同,并且不超过规定值;检查试验脚踏紧急制动关动作是否正常。
(3)检查轴向柱塞油泵和叶片油泵的工作是否正常,有无振动和噪声,当正反两个方向微小扳动手柄时,看其能否实现绞车滚筒正反转动。
(4)检查油箱中油位指示是否达到规定位置(或标记),油温是否符合规定要求,检查冷却器渡过的冷却水是否充足和畅通。
- 1、下载文档前请自行甄别文档内容的完整性,平台不提供额外的编辑、内容补充、找答案等附加服务。
- 2、"仅部分预览"的文档,不可在线预览部分如存在完整性等问题,可反馈申请退款(可完整预览的文档不适用该条件!)。
- 3、如文档侵犯您的权益,请联系客服反馈,我们会尽快为您处理(人工客服工作时间:9:00-18:30)。
碟形弹簧疲劳失效
碟形弹簧单位体积的变形能较大,用于吸收冲击和消散能量,在受到载荷长期冲击作用时,产生径向贯穿裂纹;碟簧工作时位于碟簧凹面内环面和端面交界处,承载最大拉应力,以下是碟簧失效分析:
1.由于材料成分不合理,成分偏析导致碟簧性能不均匀,例如,60Si2Mn作为碟簧材料时,含Si量偏低,降低碟簧屈服强度,导致零件提前发生脆变,甚至开裂;含P量偏高,则加剧钢的脆性倾向和成分偏析;而杂物的存在则分割了基体的连续性,成为裂纹敏感的区域,特别当分布于零件表面时,容易造成压力集中,为应力腐蚀开裂优先选择了通道。
2.加工产生裂纹。
碟形弹簧由热锻加工成型,淬火+高温回火调质处理,喷丸强化处理表面,整个加工过程中会出现碟簧内部微裂纹,造成应力集中,在使用过程中若负载过大会加速碟簧疲劳失效甚至开裂。
3.应力腐蚀。
碟簧工作时承受拉应力,当碟簧卸除载荷,其内部依然保持着残余拉应力,若碟簧长期工作在酸性液体或湿度较大环境,在拉应力作用下,溶液中的氢发生聚集,吸附在表面的空穴、腐蚀坑等缺陷处,使表面能或原子健的结合力降低,局部应力集中加剧,当裂纹的形核功大于裂纹尖端应力强度因子时,从而导致环境脆断微裂纹的形核和扩展,出现微裂纹,导致碟簧过早疲劳失效。
4.热处理不合理。
碟簧热处理时,调质处理,由于回火温度与回火后的冷却速度不当或出现偏差(譬如回火后的冷却速度过于缓慢),产生高温回火脆性;热处理表面出现脱碳现象,对碟簧的疲劳寿命产生不良影响,使碟簧的弹性极限和疲劳寿命恶化,有利于促成裂纹的形成。
5.使用环境使碟簧产生进一步的脆化。
碟簧长期工作在高温或低温的环境下,其组织缓慢发生变化,出现进一步脆化。
6.长时间使用产生材料脆化。
材料长时间使用,碟簧内部组织达到甚至超出其力学性能极限,造成脆化出现,过早产生疲劳失效。
以上每一种原因都会造成碟形弹簧在工作时产生疲劳失效,给生产应用带来损失,因此探究碟形弹簧承受载荷与形变之间的关系就十分具有应用价值,针对目前碟簧的计算公式都适用于中小载荷下的局限,探究碟簧在大载荷下的应力应变关系,得出精度较高的计算式就显得十分必要。