智能称重系统的制作方法
汽车衡智能称重系统方案设计
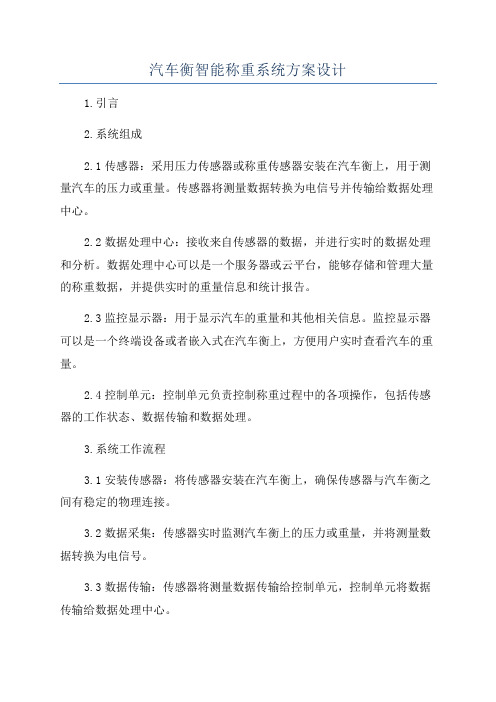
汽车衡智能称重系统方案设计1.引言2.系统组成2.1传感器:采用压力传感器或称重传感器安装在汽车衡上,用于测量汽车的压力或重量。
传感器将测量数据转换为电信号并传输给数据处理中心。
2.2数据处理中心:接收来自传感器的数据,并进行实时的数据处理和分析。
数据处理中心可以是一个服务器或云平台,能够存储和管理大量的称重数据,并提供实时的重量信息和统计报告。
2.3监控显示器:用于显示汽车的重量和其他相关信息。
监控显示器可以是一个终端设备或者嵌入式在汽车衡上,方便用户实时查看汽车的重量。
2.4控制单元:控制单元负责控制称重过程中的各项操作,包括传感器的工作状态、数据传输和数据处理。
3.系统工作流程3.1安装传感器:将传感器安装在汽车衡上,确保传感器与汽车衡之间有稳定的物理连接。
3.2数据采集:传感器实时监测汽车衡上的压力或重量,并将测量数据转换为电信号。
3.3数据传输:传感器将测量数据传输给控制单元,控制单元将数据传输给数据处理中心。
3.4数据处理:数据处理中心接收到来自控制单元的数据,并进行实时的数据处理和分析。
数据处理中心可以将数据存储在数据库中,以备后续查询和分析。
3.5结果显示:将实时的汽车重量信息和统计报告显示在监控显示器上,方便用户查看。
4.系统特点4.1自动化:传感器实时监测汽车的重量,整个称重过程无需人工干预。
这样不仅提高了称重的效率,还减少了人为误差。
4.2精确性:传感器采用高精度的压力传感器或称重传感器,能够实时测量车辆的重量,并提供准确的数据和报告。
4.3实时性:数据处理中心能够及时接收并处理来自传感器的数据,实现实时监测和报告功能。
用户可以随时了解车辆的重量情况。
4.4数据管理:数据处理中心可以对大量的称重数据进行存储和管理,便于后续查询和分析。
5.总结汽车衡智能称重系统是一种能够解决汽车运输行业中称重不便捷和不准确问题的先进设备。
通过利用传感器和数据处理技术,该系统能够实时测量车辆的重量,并提供准确的数据和报告。
智慧车载称重系统设计方案
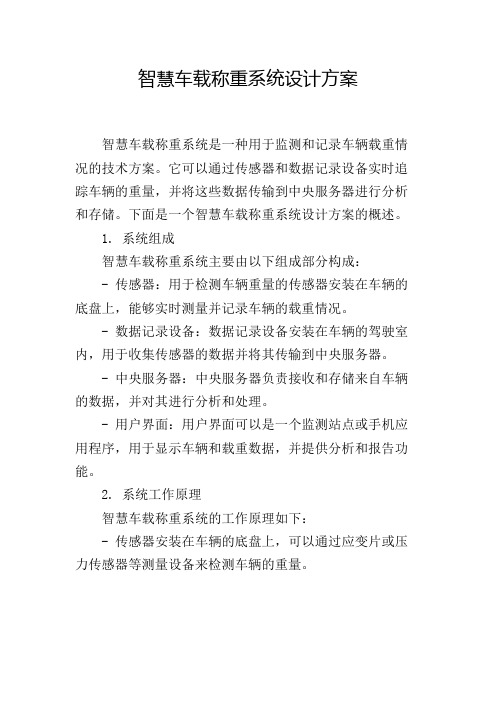
智慧车载称重系统设计方案智慧车载称重系统是一种用于监测和记录车辆载重情况的技术方案。
它可以通过传感器和数据记录设备实时追踪车辆的重量,并将这些数据传输到中央服务器进行分析和存储。
下面是一个智慧车载称重系统设计方案的概述。
1. 系统组成智慧车载称重系统主要由以下组成部分构成:- 传感器:用于检测车辆重量的传感器安装在车辆的底盘上,能够实时测量并记录车辆的载重情况。
- 数据记录设备:数据记录设备安装在车辆的驾驶室内,用于收集传感器的数据并将其传输到中央服务器。
- 中央服务器:中央服务器负责接收和存储来自车辆的数据,并对其进行分析和处理。
- 用户界面:用户界面可以是一个监测站点或手机应用程序,用于显示车辆和载重数据,并提供分析和报告功能。
2. 系统工作原理智慧车载称重系统的工作原理如下:- 传感器安装在车辆的底盘上,可以通过应变片或压力传感器等测量设备来检测车辆的重量。
- 传感器将检测到的重量数据发送给数据记录设备,数据记录设备将数据进行处理和存储,并通过无线网络传输到中央服务器。
- 中央服务器接收和存储来自多个车辆的数据,并进行分析和处理。
- 用户可以通过监测站点或手机应用程序访问中央服务器,查看车辆和载重数据,以及获取分析和报告。
3. 系统功能智慧车载称重系统具有以下主要功能:- 实时监测:系统能够实时监测车辆的载重情况,包括当前重量和历史记录。
- 数据分析:系统可以对车辆的载重数据进行分析和处理,提供统计信息和趋势分析,以帮助用户优化车辆的装载计划。
- 报警功能:系统可以设置是否超过允许的载重限制,并在超过限制时发出警报,以防止车辆超载。
- 远程访问:用户可以通过监测站点或手机应用程序远程访问系统,随时随地查看车辆和载重数据。
- 数据存储:系统能够长期存储车辆和载重数据,并提供数据备份和恢复功能。
4. 系统优势智慧车载称重系统相比传统的手动称重方式具有以下优势:- 自动化:系统能够自动记录和传输车辆的载重数据,减少人工干预和错误。
基于单片机的智能电子秤控制系统的设计
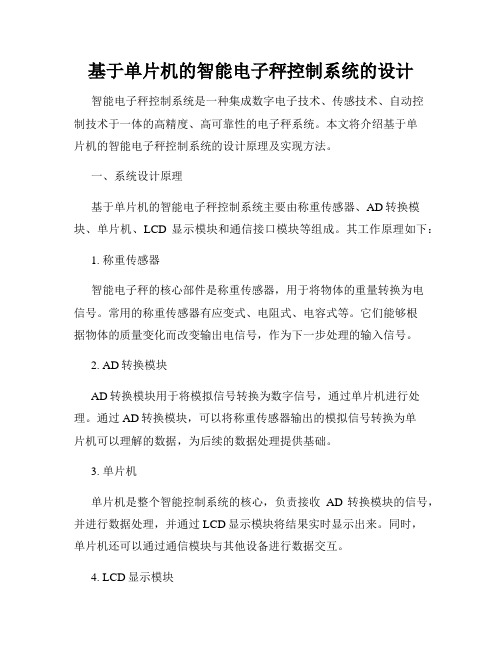
基于单片机的智能电子秤控制系统的设计智能电子秤控制系统是一种集成数字电子技术、传感技术、自动控制技术于一体的高精度、高可靠性的电子秤系统。
本文将介绍基于单片机的智能电子秤控制系统的设计原理及实现方法。
一、系统设计原理基于单片机的智能电子秤控制系统主要由称重传感器、AD转换模块、单片机、LCD显示模块和通信接口模块等组成。
其工作原理如下:1. 称重传感器智能电子秤的核心部件是称重传感器,用于将物体的重量转换为电信号。
常用的称重传感器有应变式、电阻式、电容式等。
它们能够根据物体的质量变化而改变输出电信号,作为下一步处理的输入信号。
2. AD转换模块AD转换模块用于将模拟信号转换为数字信号,通过单片机进行处理。
通过AD转换模块,可以将称重传感器输出的模拟信号转换为单片机可以理解的数据,为后续的数据处理提供基础。
3. 单片机单片机是整个智能控制系统的核心,负责接收AD转换模块的信号,并进行数据处理,并通过LCD显示模块将结果实时显示出来。
同时,单片机还可以通过通信模块与其他设备进行数据交互。
4. LCD显示模块LCD显示模块用于将称重结果以数字形式显示出来,提供直观的测量结果给用户。
5. 通信接口模块通信接口模块允许智能电子秤与其他设备进行数据交互,如与计算机进行连接,实现数据的上传和下载。
二、系统设计方法基于单片机的智能电子秤控制系统的设计可以按照以下步骤进行:1. 硬件设计根据系统的功能需求,选择适当的称重传感器和AD转换模块,并通过电路设计将其与单片机和LCD显示模块进行连接。
此外,根据实际需求选择合适的通信接口模块。
2. 软件设计编写单片机的控制程序,包括AD转换的初始化和读取、数据处理、LCD显示等功能。
根据实际需求,可以添加一些额外的功能,如单位选择、重量校准等。
3. 系统测试将硬件和软件进行组装后,进行系统测试。
通过放置不同重量的物体进行秤量,检查显示结果的准确性和稳定性。
同时,测试通信功能是否正常工作。
《汽车衡全自动智能称重系统》设计方案

《汽车衡全自动智能称重系统》设计方案设计方案:汽车衡全自动智能称重系统1.系统背景随着城市交通的发展和物流行业的不断壮大,汽车衡作为一种重要的物流设备,被广泛应用于货物称重的过程中。
然而,传统的汽车衡需要人工操作,效率低下且易受人为因素的影响,不符合现代物流行业对高效、准确、智能化操作的要求。
因此,设计一种全自动智能称重系统,将提高物流行业的效率,并减少因人为操作造成的错误。
2.系统功能该系统的主要功能如下:(1)车辆进入自动感应区域后,系统能自动识别并记录车辆的车牌号码,与车辆信息库中的数据进行比对,确保车辆数据准确无误。
(2)车辆驶入稳定区域后,车辆传感器系统将自动测量车辆的长度、宽度和高度,并记录在数据库中。
(3)强度传感器能够准确测量车辆的重量,并将数据传输到控制系统。
(4)控制系统能自动计算车辆的总重量,并与车辆信息库中的数据进行比对,确保称重数据准确无误。
(5)称重完成后,系统将自动打印出称重信息,并显示在屏幕上。
(6)系统还具备数据分析和存储功能,可以保存车辆的称重记录,并能够对数据进行统计和分析。
3.系统组成(1)车辆识别模块:主要包括车牌识别摄像头、图像处理算法和车辆信息库。
通过拍摄车辆的车牌号码,并通过图像处理算法进行车牌号码的识别和校验,与车辆信息库中的数据进行比对,确保车辆数据准确无误。
(2)车辆测量模块:主要包括车辆传感器系统和数据库。
通过车辆传感器系统测量车辆的长度、宽度和高度,并将数据记录在数据库中。
(3)车辆称重模块:主要包括强度传感器和控制系统。
强度传感器能够准确测量车辆的重量,并将数据传输到控制系统。
控制系统能自动计算车辆的总重量,并与车辆信息库中的数据进行比对,确保称重数据准确无误。
(4)数据分析和存储模块:主要包括数据存储系统和分析软件。
数据存储系统能够保存车辆的称重记录,并可以对数据进行统计和分析。
4.系统流程(1)车辆进入自动感应区域,车牌识别摄像头自动拍摄车牌号码。
自动化称重系统400设备工艺原理
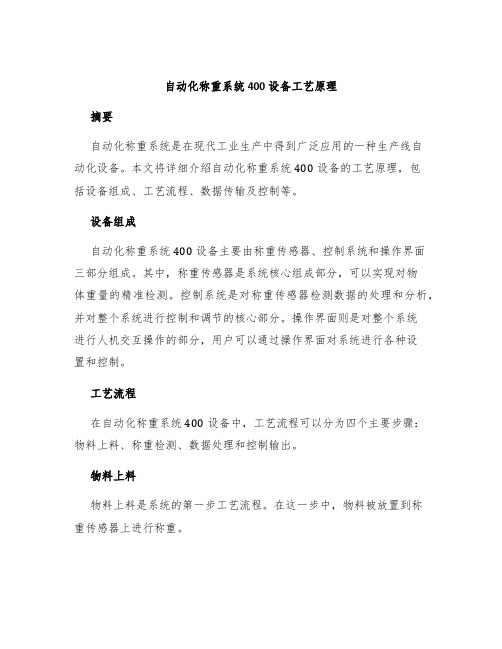
自动化称重系统400设备工艺原理摘要自动化称重系统是在现代工业生产中得到广泛应用的一种生产线自动化设备。
本文将详细介绍自动化称重系统400设备的工艺原理,包括设备组成、工艺流程、数据传输及控制等。
设备组成自动化称重系统400设备主要由称重传感器、控制系统和操作界面三部分组成。
其中,称重传感器是系统核心组成部分,可以实现对物体重量的精准检测。
控制系统是对称重传感器检测数据的处理和分析,并对整个系统进行控制和调节的核心部分。
操作界面则是对整个系统进行人机交互操作的部分,用户可以通过操作界面对系统进行各种设置和控制。
工艺流程在自动化称重系统400设备中,工艺流程可以分为四个主要步骤:物料上料、称重检测、数据处理和控制输出。
物料上料物料上料是系统的第一步工艺流程。
在这一步中,物料被放置到称重传感器上进行称重。
称重检测在物料上料完成后,自动化称重系统400设备会对物料进行称重检测。
称重传感器会对物料重量进行测量,并将测量结果传输到控制系统。
数据处理控制系统接收到称重传感器传输的数据后,会进行数据处理和分析。
该步骤的主要目的是将称重结果转换为数字数据,并进行数据比对。
控制输出在数据处理完成后,自动化称重系统400设备会根据预先设定的称重标准进行比对,并根据比对结果输出控制信号。
输出信号可以控制物料的下料或者物料数量控制。
数据传输及控制自动化称重系统400设备中的数据传输主要通过传感器进行,称重传感器会将测量的数据通过数字信号的形式传输到控制系统中。
在控制系统中,数据处理以及控制信号的输出均可以通过软件控制实现。
操作人员可以通过操作界面对系统进行控制,同时也可以通过外部设备对系统进行控制和监测。
结论自动化称重系统400设备是一种重要的工业自动化装备,可以大大提高工业生产线的效率和产能。
本文详细介绍了自动化称重系统400设备的工艺原理,包括设备组成、工艺流程、数据传输及控制等方面。
希望可以对读者对自动化称重系统有更加深入的了解。
电子秤智慧检定系统设计方案

电子秤智慧检定系统设计方案设计方案:电子秤智能检定系统1. 引言电子秤是现代生活中常用的计量工具之一,用于测量物体的重量。
然而,由于使用频繁,电子秤会出现误差,需要进行定期的检定和校准。
传统的检定方法费时费力,且可能存在人为误差。
为了解决这一问题,我们设计了一种电子秤智能检定系统,以提高检定效率和准确性。
2. 系统概述本系统通过使用传感器和微控制器,将电子秤的重量数据传输至上位机,通过上位机对数据进行分析和处理,计算出电子秤的误差,并进行相应的校准。
系统具备智能化的检定功能,能够自动识别电子秤的型号和规格,并根据不同的电子秤进行相应的检定和校准流程。
3. 硬件设计系统的硬件部分包括传感器、微控制器和通信模块。
传感器用于测量电子秤的重量数据,并将数据传输至微控制器。
微控制器负责对传感器数据进行处理和分析,并通过通信模块将数据传输至上位机。
4. 软件设计系统的软件部分包括上位机软件和微控制器嵌入式程序。
上位机软件用于接收和处理来自微控制器的数据,进行重量误差计算和校准命令下发。
微控制器嵌入式程序负责采集传感器数据、进行数据处理和通信模块控制。
5. 系统流程系统的工作流程如下:(1) 电子秤放置在检定台上,并连接到检定系统。
(2) 检定系统上位机软件自动识别电子秤型号和规格。
(3) 上位机软件发送校准命令给微控制器。
(4) 微控制器接收校准命令,并控制传感器进行测量。
(5) 传感器测量完毕后,将数据传输至微控制器。
(6) 微控制器对数据进行处理,计算出电子秤的误差。
(7) 微控制器将误差数据传输至上位机软件。
(8) 上位机软件根据误差数据进行校准计算,并发送校准命令给微控制器。
(9) 微控制器接收校准命令,并控制传感器进行校准。
(10) 校准完毕后,系统自动记录校准结果,并显示在上位机软件界面上。
6. 系统特点本系统具有以下特点:(1) 智能化:系统能够自动识别电子秤型号和规格,并根据不同电子秤进行相应的检定和校准流程。
地磅智能化无人值守智能化称重管理系统设计方案

地磅智能化无人值守智能化称重管理系统设计方案一、引言地磅智能化无人值守智能化称重管理系统是一种利用现代科技手段,对地磅进行无人值守智能化管理的系统。
该系统利用传感器、计算机技术、网络通信等技术手段,实现对地磅称重过程的自动化、智能化管理,提高地磅工作效率,减少人力成本,提高工作准确性。
本文将从系统硬件设计、软件设计和网络通信设计三个方面详细介绍地磅智能化无人值守智能化称重管理系统的设计方案。
二、系统硬件设计1.传感器选择:地磅智能化无人值守智能化称重管理系统的核心是通过传感器收集货物的重量信息,因此传感器的选择至关重要。
应选择精度高、稳定性好、响应时间快的传感器,如压力传感器或称重传感器。
2.数据采集模块:数据采集模块负责将传感器采集到的数据进行转换和处理,并将处理后的数据传送给上位机。
数据采集模块应具有较高的数据处理能力和稳定性。
3.控制模块:控制模块是地磅智能化无人值守智能化称重管理系统的核心,它负责控制传感器的工作,采集称重数据,控制显示屏的显示和控制称重过程。
控制模块应具有良好的稳定性和可靠性。
三、软件设计1.软件平台选择:根据系统的功能需求、开发人员熟悉程度和用户操作习惯等方面进行软件平台的选择。
可以选择嵌入式操作系统或PC端软件开发。
2.界面设计:地磅智能化无人值守智能化称重管理系统的界面设计应符合用户操作习惯,操作简单易懂。
应提供实时称重数据显示、历史数据查询等功能。
3.数据处理和记录:地磅智能化无人值守智能化称重管理系统应具备数据处理和记录功能,包括对称重数据的计算、处理和历史数据的存储。
四、网络通信设计1.硬件网络:地磅智能化无人值守智能化称重管理系统应能够与上位机进行数据通信,因此需要在硬件设计中考虑网络接口的选择和配置。
2.通信协议:系统应选择适合的通信协议,如TCP/IP协议,以实现与上位机之间的数据通信。
3.数据传输安全:考虑到数据传输的安全性,系统应采用数据加密等措施,防止数据泄露和篡改。
基于单片机的智能电子秤设计
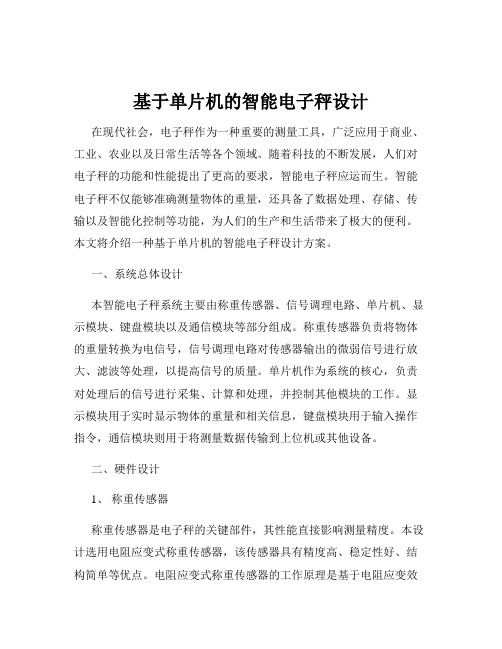
基于单片机的智能电子秤设计在现代社会,电子秤作为一种重要的测量工具,广泛应用于商业、工业、农业以及日常生活等各个领域。
随着科技的不断发展,人们对电子秤的功能和性能提出了更高的要求,智能电子秤应运而生。
智能电子秤不仅能够准确测量物体的重量,还具备了数据处理、存储、传输以及智能化控制等功能,为人们的生产和生活带来了极大的便利。
本文将介绍一种基于单片机的智能电子秤设计方案。
一、系统总体设计本智能电子秤系统主要由称重传感器、信号调理电路、单片机、显示模块、键盘模块以及通信模块等部分组成。
称重传感器负责将物体的重量转换为电信号,信号调理电路对传感器输出的微弱信号进行放大、滤波等处理,以提高信号的质量。
单片机作为系统的核心,负责对处理后的信号进行采集、计算和处理,并控制其他模块的工作。
显示模块用于实时显示物体的重量和相关信息,键盘模块用于输入操作指令,通信模块则用于将测量数据传输到上位机或其他设备。
二、硬件设计1、称重传感器称重传感器是电子秤的关键部件,其性能直接影响测量精度。
本设计选用电阻应变式称重传感器,该传感器具有精度高、稳定性好、结构简单等优点。
电阻应变式称重传感器的工作原理是基于电阻应变效应,当传感器受到外力作用时,其弹性体发生变形,从而导致粘贴在弹性体上的电阻应变片的电阻值发生变化。
通过测量电阻应变片电阻值的变化,即可得到外力的大小。
2、信号调理电路由于称重传感器输出的信号非常微弱,通常只有几毫伏到几十毫伏,且含有大量的噪声和干扰,因此需要经过信号调理电路进行放大、滤波等处理。
信号调理电路主要由放大器、滤波器和基准电源等组成。
放大器采用高精度仪表放大器,能够将传感器输出的微弱信号放大到适合单片机处理的范围。
滤波器采用低通滤波器,用于滤除信号中的高频噪声和干扰。
基准电源为整个电路提供稳定的参考电压,以保证测量精度。
3、单片机单片机是整个系统的控制核心,本设计选用 STM32F103 系列单片机。
STM32F103 系列单片机具有高性能、低功耗、丰富的外设资源等优点,能够满足智能电子秤的设计要求。
- 1、下载文档前请自行甄别文档内容的完整性,平台不提供额外的编辑、内容补充、找答案等附加服务。
- 2、"仅部分预览"的文档,不可在线预览部分如存在完整性等问题,可反馈申请退款(可完整预览的文档不适用该条件!)。
- 3、如文档侵犯您的权益,请联系客服反馈,我们会尽快为您处理(人工客服工作时间:9:00-18:30)。
本技术新型提供了一种智能称重系统,包括储料仓、机器视觉摄像头、机械臂、机械铲、称重传感器、远程终端、中控模块和搅拌装置,所述机械臂的一端固定于所述称重传感器的顶部,所述机械臂的另一端连接所述机械铲和所述机器视觉摄像头,所述储料仓设置有多个用于储粉料的料仓,多个所述料仓相互独立地设置有位置标示,所述机器视觉摄像头用于识别所述料仓的位置标示以及所述料仓中的物料种类,所述储料仓和所述搅拌装置位于所述机械臂上机械铲的运动范围之内,所述机器视觉摄像头、所述称重传感器和所述机械臂均电连接所述中控模块,所述远程终端与所述中控模块有线或无线通讯。
本技术新型提供的智能称重系统能够实现混凝土的自动化称重搅拌,有效避免人为失误,同时降低了人工成本。
权利要求书1.一种智能称重系统,其特征在于,包括储料仓、机器视觉摄像头、机械臂、机械铲、称重传感器、远程终端、中控模块和搅拌装置,所述机械臂的一端固定于所述称重传感器的顶部,所述机械臂的另一端连接所述机械铲和所述机器视觉摄像头,所述储料仓设置有多个用于储粉料的料仓,多个所述料仓相互独立地设置有位置标示,所述机器视觉摄像头用于识别所述料仓的位置标示以及所述料仓中的物料种类,所述储料仓和所述搅拌装置位于所述机械臂上机械铲的运动范围之内,所述机器视觉摄像头、所述称重传感器和所述机械臂均电连接所述中控模块,所述远程终端与所述中控模块有线或无线通讯。
2.根据权利要求1所述的智能称重系统,其特征在于,所述远程终端为电脑。
3.根据权利要求1所述的智能称重系统,其特征在于,所述智能称重系统还包括有触摸显示屏,所述触摸显示屏电连接所述中控模块。
4.根据权利要求1所述的智能称重系统,其特征在于,所述机器视觉摄像头选自OpenMV摄像头。
5.根据权利要求1所述的智能称重系统,其特征在于,所述称重传感器选自LC401称重传感器。
6.根据权利要求1所述的智能称重系统,其特征在于,所述中控模块包括STM32F103芯片。
7.根据权利要求1所述的智能称重系统,其特征在于,所述机械臂包括多个臂体和多个舵机,相邻两个所述臂体之间由单个所述舵机连接。
技术说明书一种智能称重系统技术领域本技术新型属于工业智能设备技术领域,具体涉及一种智能称重系统。
背景技术随着社会科技的快速发展,科学技术的不断创新,工业生产领域的模式发生了翻天覆地的变化。
人工制造成本不断攀升,传统的制造模式已经无法适应现有的工业生产形式。
工业机器人创造更加优质的条件来提高工业产品的质量和产量,工业机器人的突出优势在于工作效率高,能够承受非常大工作强度,并且精准度高,能够完成许多人力无法完成或者较难完成的工作,操作简单大大减少了人类的工作量,提高工作效率,加快人类社会文明的进步。
混凝土主要由粉体材料加水和外加剂拌合而成,在传统的混凝土拌合试验中,一般由人力来完成,这样就会存在很多的弊端,例如:粉体材料的颗粒粒径非常小,如果由人来完成,这样会危害到人的身体健康;拌合混凝土的工作强度非常高,尤其是高强混凝土黏性更高,这样就会消耗大量的大力和物力;人在完成试验的时候会造成人为误差,这样会使试验数据不精准等。
实用新型内容针对现有混凝土搅拌存在人工成本高以及粉料称重人为误差大的问题,本技术新型提供了一种智能称重系统。
本技术新型提供了一种智能称重系统,包括储料仓、机器视觉摄像头、机械臂、机械铲、称重传感器、远程终端、中控模块和搅拌装置,所述机械臂的一端固定于所述称重传感器的顶部,所述机械臂的另一端连接所述机械铲和所述机器视觉摄像头,所述储料仓设置有多个用于储粉料的料仓,多个所述料仓相互独立地设置有位置标示,所述机器视觉摄像头用于识别所述料仓的位置标示以及所述料仓中的物料种类,所述储料仓和所述搅拌装置位于所述机械臂上机械铲的运动范围之内,所述机器视觉摄像头、所述称重传感器和所述机械臂均电连接所述中控模块,所述远程终端与所述中控模块有线或无线通讯。
进一步的,所述远程终端为电脑。
进一步的,所述智能称重系统还包括有触摸显示屏,所述触摸显示屏电连接所述中控模块。
进一步的,所述机器视觉摄像头选自Open MV摄像头。
进一步的,所述称重传感器选自LC401称重传感器。
进一步的,所述中控模块包括STM32F103芯片。
进一步的,所述机械臂包括多个臂体和多个舵机,相邻两个所述臂体之间由单个所述舵机连接。
本技术新型提供的智能称重系统在进行混凝土配比搅拌时,可通过远程终端输入需要配比的物料和各物料的添加量,进而通过所述中控模块控制所述机器视觉摄像头对储料仓中各个料仓进行粉料识别,获得目标粉料后,通过机械臂控制所述机械铲进行取料,称重传感器称取机械臂取得的粉料的重量,并将重量信息传输至中控模块与目标重量对比,根据中控模块根据目标重量控制机械臂进行增加粉料或减少粉料,得到目标重量的粉料后,通过所述机械臂将粉料输送至搅拌装置中,从而实现混凝土的自动化称重搅拌,有效避免人为失误,同时降低了人工成本。
附图说明图1是本技术新型提供的智能称重系统其部分结构示意图;图2是本技术新型提供的智能称重系统其储料仓的结构示意图;图3是本技术新型提供的智能称重系统其搅拌装置的结构示意图;图4是本技术新型提供的STM32最小系统。
图5是本技术新型提供的PWM脉冲信号的驱动电路。
图6是本技术新型提供的无线串口通信电路。
图7是本技术新型提供的电源缓启电路。
具体实施方式为了使本技术新型所解决的技术问题、技术方案及有益效果更加清楚明白,以下结合附图及实施例,对本技术新型进行进一步详细说明。
应当理解,此处所描述的具体实施例仅仅用以解释本技术新型,并不用于限定本技术新型。
如图1-图3所示,本技术新型提供了一种智能称重系统,包括储料仓、机器视觉摄像头3、机械臂、机械铲1、称重传感器6、远程终端、中控模块7和搅拌装置12,所述机械臂的一端固定于所述称重传感器6的顶部,所述机械臂的另一端连接所述机械铲1和所述机器视觉摄像头3,所述储料仓设置有多个用于储粉料的料仓,多个所述料仓相互独立地设置有位置标示,所述机器视觉摄像头3用于识别所述料仓的位置标示以及所述料仓中的物料种类,所述储料仓和所述搅拌装置12位于所述机械臂上机械铲1的运动范围之内,所述机器视觉摄像头3、所述称重传感器6和所述机械臂均电连接所述中控模块7,所述远程终端与所述中控模块7有线或无线通讯。
本技术新型提供的智能称重系统在进行混凝土配比搅拌时,可通过远程终端输入需要配比的物料和各物料的添加量,进而通过所述中控模块7控制所述机器视觉摄像头3对储料仓中各个料仓进行粉料识别,获得目标粉料后,通过机械臂控制所述机械铲1进行取料,称重传感器6称取机械臂取得的粉料的重量,并将重量信息传输至中控模块7与目标重量对比,根据中控模块7根据目标重量控制机械臂进行增加粉料或减少粉料,得到目标重量的粉料后,通过所述机械臂将粉料输送至搅拌装置中,从而实现混凝土的自动化称重搅拌,有效避免人为失误,同时降低了人工成本。
所述远程终端为电脑。
所述智能称重系统还包括有触摸显示屏2,所述触摸显示屏2电连接所述中控模块7。
所述机器视觉摄像头3选自Open MV摄像头。
所述称重传感器6选自LC401称重传感器。
所述中控模块7包括STM32F103芯片。
所述机械臂包括多个臂体4和多个舵机5,相邻两个所述臂体4之间由单个所述舵机5连接。
多个所述料仓包括第一料仓8、第二料仓9、第三料仓10和第四料仓11图4所示为STM32F103芯片最小系统电路设计,STM32F103芯片的最小系统主要有五个部分组成:电源电路、时钟源电路、BOOT启动电路、调试接口电路和复位电路,电源电压的滤波电路以及程序下载电路(本系统采用SWD下载方式)。
每一个时钟源都可以被独立地启动或关闭,从而可以降低系统功耗。
从硬件设计的角度来看,需要提供8MHz频率的时钟。
左上方的电路选用三点起振电路,三点起振电路的优势在于易起振、调节频率方便和输出波形稳定;左下方电路为复位电路,当S1按键按下时电路导通,STM32F103芯片恢复到初始状态;最上方为BOOT自举升压电路,使上下管轮流导通。
启动自举脚通过一个电容与PHASE 脚相连,电容的作用是控制上管的开启,图6中部分电路和原器件未给出。
如图5所示为PWM信号驱动电路。
PWM电路主要功能是将输入电压的振幅转换成宽度一定的脉冲,换句话说它是将振幅信号转换成脉冲宽度。
当PWM信号驱动电路中系统输入为低电平时,Q4截止,Q9导通,PUL0输出低电平;当输入为高电平时,Q4导通,Q9截止,PUL0输出为高电平。
其中R5的大小为520Ω,R5的作用是限流,防止电路的电流过大烧毁STM32F103芯片的I/O口。
本系统PWM最大输出频率为333KHZ,小于所选用的三极管的最大开关频率(1MHz),本电路满足系统的要求,增大了脉冲的驱动能力以及抗干扰能力。
STM32F103芯片的脉冲输出电压峰峰值为3.3V,而本系统所釆用的舵机的电机驱动器内部为CMOS电平,要求控制信号的峰峰值为5V,且采用光耦隔离,必须进行电平转换并提高信号的驱动能力才能控制电机的运转。
电平转换电路由三极管组合设计,利用NPN型三极管和PNP型三极管极性不同设计成电平转换电路。
二者各负责正负半周的波形放大任务,正常工作时,两个三极管始终一个处于导通状态、一个处于截止状态,可以减少导通损耗,提高效率,但必须选择两个参数相同、极性相反的三极管。
PWM电路的特点是频率高、效率高、功率密度高和可靠性高,本电路的特点是电路设计简单,可靠性高,波形失真度小,但受三极管自身数据参数的限制,无法承受高频率的脉冲。
如图6为无线串口通讯电路设计。
STM32F103芯片与远程终端采用异步串行通信方式进行数据传输,远程终端为PC机,STM32预留的10端口为TTL电平,而PC机采用的是统一的RS232电平,为了使二者能够进行数据传输,需进行电平转换。
在STM32F103芯片串口与上位机给出的RS232口之间,通过电平转换电路(MAX3232CSE芯片)实现TTL电平与RS232电平之间的转换。
串口通讯的整体流程为,开启GPIO时钟和USARTX时钟,配置TX和RX引脚,初始化USART控制器本技术新型釆用的是MAXIM公司专门为电脑的RS232标准串口设计的接口电路MAX 3232CSE芯片,它可以将单片机的TTL电平转换为RS232电平。
线路接口连接时,应将PC机和STM32F103芯片的数据发送端以及数据接收端交叉连接,但是必须共地。
如图7为电源缓启电路。
因为大多数电子器件当系统正常工作,热插拔时,连接器的机械触点在接触瞬间会出现弹跳,引起电源振荡,这个振荡过程会引起系统电源跌落,引起误码,或系统重启,也可能会引起连接器打火,引发火灾,并且热插拔时,由于系统大容量储能电容的充电效应,系统中会出现很大的冲击电流,此冲击电流可能会烧毁设备电源保险管。