管道弯管加工记录
1GB50235—2019工业金属管道工程施工规范详解

2019/10/17
5
2.1.11 附着件 structural attachments
用焊接、螺栓连接或夹紧等方法附装在管子 上的零件。它包括管吊、吊(支)耳、圆环、 夹子、吊夹、紧固夹板和裙式管座等。
1 设计压力<10MPa,且设计温度<400℃,工作温度不高于标准沸点的 高度危害液体介质的管道 2 毒性程度为中度、轻度危害流体介质的下列管道: 1) 设计压力<10MPa、≥4MPa,且设计温度<400℃; 2) 设计压力<4MPa。 3 设计压力<10MPa、≥4MPa,且设计温度<400℃的乙、丙类可燃液体 介质的管道。 4 设计压力<4MPa的可燃流体介质的管道 5 下列情况的无毒、非可燃流体介质的管道: 1) 设计压力<10MPa、≥4MPa,且设计温度<400℃; 2) 设计压力<4MPa、>1MPa; 3) 设计压力≤1MPa,且设计温度≤-20℃或>185℃。
2019/10/17
21
4.1.7 防腐衬里管道的衬里质量应按现行国家标准 《工业设备、管道防腐蚀工程质量验收规范》规定 进行检查验收。
4.1.8 检查不合格的管道元件不得使用,并应作好标 识和隔离。
4.1.9 管道元件在施工过程中应妥善保管,不得混淆 或损坏,其标记应明显清晰。材质为不锈钢、有色 金属的管道元件,在运输和储存期间不得与碳素钢 接触。
4.2.5 阀门液体压力试验和上密封试验应以洁净水为介质。不锈 钢阀门液体压力试验时,水中的氯离子含量不得超过100×10 -6(25ppm)。当有特殊要求时,试验介质应符合设计文件 的规定。试验合格后应立即将水渍清除干净。
GB_5025—2010工业金属管道工程施工及验收规范

2019/9/15
20
4.1.3 当对管道元件性能数据有异议时,在异议 未解决前,该批管道元件不得使用。
2019/9/15
21
4.1.7 防腐衬里管道的衬里质量应按现行国家标准 《工业设备、管道防腐蚀工程质量验收规范》规定 进行检查验收。
4.1.8 检查不合格的管道元件不得使用,并应作好标 识和隔离。
4.1.9 管道元件在施工过程中应妥善保管,不得混淆 或损坏,其标记应明显清晰。材质为不锈钢、有色 金属的管道元件,在运输和储存期间不得与碳素钢 接触。
dimension adjustment 在管道预制过程中,按照单线图选择确定的、
经实测安装尺寸后再行加工的管段。
2019/9/15
9
Dm ax
2.2 符号
[σ]1——试验温度下,管材的许用应力; [σ]2——设计温度下,管材的许用应力; D——管子外径; D2——弯管褶皱凸出处外径; D3——弯管褶皱凹进处外径; D4——弯管相邻褶皱凸出处外径; ——弯管截面最大实测外径; ——弯管截面最小实测外径;
2019/9/15
12
3 管道施工的基本规定 3.1 一般规定
3.1.1 承担工业金属管道工程的施工单位 应取得相应的资质,并在资质许可范围内 从事相应的管道施工。
检验机构应取得相应的检验资质,且应在 资质许可范围内从事相应的管道工程检验 工作。
2019/9/15
13
3.1.2 施工单位应建立管道施工现场的质量 管理体系,具有健全的质量管理制度和相应 的施工技术标准,实施管道施工全过程的质 量控制。
弯管加工工艺

3弯管3.1弯管宜采用壁厚为正公差的管子制作。
高压钢管的弯曲半径宜大于外径的5倍,其他管子的弯曲半径宜大于管子外径的35倍,有缝管制作弯管时,焊缝应避开管拉(压)区。
弯曲半径与管子壁厚的关系3.2不锈钢管宜冷弯,铝锰合金管不得冷弯其他材质的管子可冷弯或热弯。
高、中合金钢管热弯时不得浇水,低台金钢管一般不宜浇水,热弯后应在5℃以上静止空气中缓慢冷却。
3.3热煨弯头常用:地炉加热煨弯,火焰弯管机,中频电热弯管机等,热煨弯管测温常热用电偶,光学高温计等。
3.4采用热弯管时,不论管径大小,一律按规定装干燥的细砂。
加热铜管应用术炭作燃料,加热铝管应先用焦炭打底,上面铺木炭以调节温度。
存加热过程中应关闭鼓风机.并不断转动管子,防止温度过高使管子熔化。
3.5采用高合金钢管或有色金属管制作弯管,宜采用机械方法,当充砂制作弯管时,不得用铁锤敲击。
铅管加热制作弯管时,不得充砂。
3.6除制作弯管温度自始至终保持在900℃以上的情况外,壁厚大于19mm的碳素钢管制作弯管后,应按规定进行热处理按规定,中、低合金钢管进行热弯时, 对公称直径大或等于是100mm或壁厚大于或等于是13mm的,应按设计文件的要求进行完全退火,正火加回火或回火处理。
中、低合金钢管进行冷弯时,对公称直径大于或等于100mm,或壁厚大于或等于13mm的,应按规定要求进行热处理。
奥氏体不锈钢管制作的弯管,可不进行热处理,当设计文件要求热处理时,应按设计文件规定进行.3.7输送剧毒流体或设计压力P大于或等于1OMPa的弯管,制作弯管前,后的壁厚之差,不得超过制作弯管前管子壁厚的10%;其它弯管,制作弯管前,后的管子壁厚之羞,不得超过制作弯管前管子壁厚的15%,且均不得小于管子的设计壁厚。
3.8输送剧毒流体或设计压力P大于或等于lOMPa的弯管,管端中心偏差值A不得超过1.5mm/m,当直管长度L人于3m时,其偏差不得超过5mm。
其他类别的弯管.管端中心偏差值Δ得超过3mm/m当直管长度L大于3m时,其偏差不得超过lOmm。
GB_50235—2010工业金属管道工程施工规范
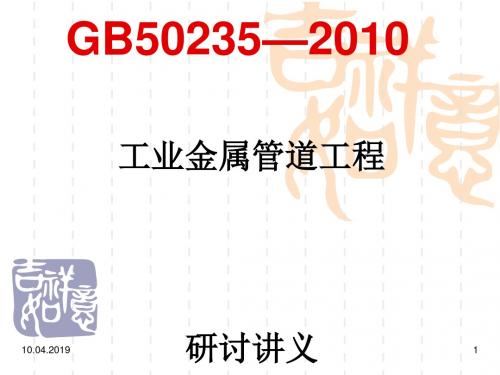
3.1.5 压力管道施工前,施工单位应向管道 安装工程所在地的质量技术监督部门办理书 面告知文件,并应接受监督检验单位的监督 检验。 3.1.6 管道施工应符合国家现行的环境保护、 安全技术和劳动保护等有关规定。
10.04.2019
16
3.2 管道分级
3.2.1 工业金属管道应按设计压力、设计温度、 介质的毒性危害程度和火灾危险性划分为 GC1、GC2、GC3三个级别。管道分级应符 合表3.2.1的规定。
10.04.2019 4
2.1.9 管道支承件 pipe-supporting elements 将管道的自重、输送流体的重量、由于操作压力和 温差所造成的荷载以及振动、风力、地震、雪载、 冲击和位移应变引起的荷载等传递到管架结构上去 的管道元件。包括管道安装件和附着件。 2.1.10 安装件 fixtures 将负荷从管子或管道附着件上传递到支承结构或设 备上的管道元件。它包括吊杆、弹簧支吊架、斜拉 杆、平衡锤、松紧螺栓、支撑杆、链条、导轨、锚 固件、鞍座、垫板、滚柱、托座和滑动支架等。
10.04.2019
17
表3.2.1 管道分级
管道级别
GC1
适用范围
1 毒性程度为极度危害介质的管道。 2 毒性程度为高度危害气体介质的管道 3 工作温度高于标准沸点的高度危害液体介质的管道。 4 设计压力≥4MPa,火灾危险性为甲、乙类可燃气体介质的管道 5 设计压力≥4MPa,火灾危险性为甲类可燃液体和液化烃介质的管道。 6 设计压力≥10MPa的管道。 7 设计压力≥4MPa,且设计温度≥400℃的管道。 1 设计压力<10MPa,且设计温度<400℃,工作温度不高于标准沸点的 高度危害液体介质的管道 2 毒性程度为中度、轻度危害流体介质的下列管道: 1) 设计压力<10MPa、≥4MPa,且设计温度<400℃; 2) 设计压力<4MPa。 3 设计压力<10MPa、≥4MPa,且设计温度<400℃的乙、丙类可燃液体 介质的管道。 4 设计压力<4MPa的可燃流体介质的管道 5 下列情况的无毒、非可燃流体介质的管道: 1) 设计压力<10MPa、≥4MPa,且设计温度<400℃; 2) 设计压力<4MPa、>1MPa; 3) 设计压力≤1MPa,且设计温度≤-20℃或>185℃。 设计压力≤1MPa,设计温度>-20℃但≤185℃的无毒、非可燃流体介质的 管道
压力管道压力试验通用工艺规程
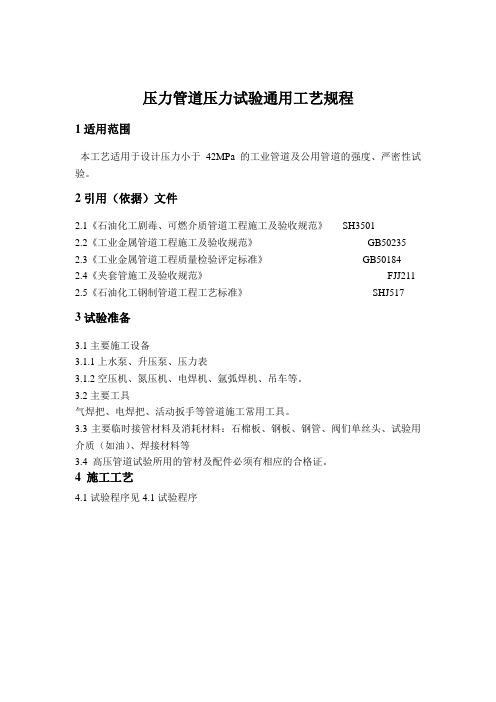
压力管道压力试验通用工艺规程1适用范围本工艺适用于设计压力小于42MPa的工业管道及公用管道的强度、严密性试验。
2引用(依据)文件2.1《石油化工剧毒、可燃介质管道工程施工及验收规范》SH35012.2《工业金属管道工程施工及验收规范》GB50235 2.3《工业金属管道工程质量检验评定标准》GB50184 2.4《夹套管施工及验收规范》FJJ211 2.5《石油化工钢制管道工程工艺标准》SHJ5173试验准备3.1主要施工设备3.1.1上水泵、升压泵、压力表3.1.2空压机、氮压机、电焊机、氩弧焊机、吊车等。
3.2主要工具气焊把、电焊把、活动扳手等管道施工常用工具。
3.3主要临时接管材料及消耗材料:石棉板、钢板、钢管、阀们单丝头、试验用介质(如油)、焊接材料等3.4 高压管道试验所用的管材及配件必须有相应的合格证。
4 施工工艺4.1试验程序见4.1试验程序4.2试压方案的确定4.2.1管道系统的划分技术人员根据施工平面布置图、设计变更单及管道说明等设计文件,来划分管道系统,把压力相近(压力差不宜超过1MP a )、现场分布临近、流程相贯通的两条或多条管线组合为系统。
4.2.2管道系统试压流程图的绘制1.管道系统试压时应有试压流程图,试压流程图根据设计部门的施工图或单线图绘制。
对于特殊的小型管道工程可直接用单线图或施工图作试压流程图。
2.试压流程图应包括以下内容:a.管号b.介质流向c.设计压力、设计温度、试验压力d.系统内空气排放点e.临时盲板位置f.试验介质进口g.临时管线h.压力表位置 图4.1试验程序 试验准备 试验条件的确认 灌注介质、升压至强度试验压力 稳压检查压力 泄压返修 降压至设计压力 泄压 稳压检查渗漏 管道系统复位i.试验介质j.试验介质临时排放点4.2.3试压参数的确定1.试验介质:管道系统压力试验用介质应根据设计文件的规定进行,如水或空气等。
如设计文件无规定时,应用液体(主要指洁净水)进行。
压力容器压力管道竣工资料

____________________ 单位压力容器安装竣工随附文件资料压力容器安装竣工随附文件资料目录1、压力容器安装质量证明书2、特种设备安装改造维修告知书3、压力容器产品出厂文件资料审查记录4、压力容器基础验收记录5、压力容器安装找正记录6、压力容器安装系统连接施工检验记录7、压力容器安装压力试验记录8 压力容器安装压力试验报告9、压力容器静电接地测试记录压力容器安装质量证明书工程名称:容器名称:产品编号:容器类别:开工日期:竣工日期:使用单位:本压力容器安装经质量检验,符合《固定式压力容器安全技术检查规程》、设计文件和《机械设备安装工程施工及验收规范》的要求。
检验与试验责任人:日期:质量保证工程师:日期:安装单位(盖章)年月日特种设备安装许可证编号:压力容器产品随附文件资料审查记录审查人(施工质检员):日审核(检验责任人):日期:期:压力容器基础验收记录压力容器安装找正记录压力容器安装系统连接施工检验记录压力容器安装压力试验记录□水压□气压□泄漏性压力容器安装压力试验报告□水压□气压□泄漏性压力容器静电接地测试记录________________________工程压力管道安装工程竣工随附文件资料压力管道安装工程竣工随附文件资料目录1、压力管道安装质量证明书2、压力管道安装汇总表3、特种设备安装改造维修告知书4、压力管道安装安全质量监督检验报告5、施工组织设计或施工方案6、焊接工艺卡7、热处理工艺卡8、压力试验与泄漏试验方案9、管道系统吹扫与清洗方案10、管材、管件、焊材检验记录11、管材、管件、焊材产品质量证明书、合格证12、设计文件审查记录13、技术交底记录14、合金钢元件光谱复查报告15、阀门试验记录16、管道弯管加工记录17、焊材发放、回收记录18、工程焊接记录19、焊接接头表面质量检验记录20、焊接返修工艺卡21、焊缝返修及检查记录22、管道轴测图23、管道冷紧记录24、管道补偿装置安装记录25、管道支、吊架制作安装记录26、管道安装记录27、管道热处理报告及时间一一温度自动记录曲线28、硬度检测报告29、无损检测报告30、管道系统压力试验报告31、管道系统泄漏性试验报告32、管道系统吹扫与清洗记录33、管道防腐检验记录34、钢质埋地干管阴极保护调试试验记录35、管道绝热施工检查记录36、管道隐藏工程(封闭)记录37、埋地管道沟槽及回填记录38、管道静电接地测试记录39、安全阀校验报告和安全阀调试记录40、管道工程试运行记录41、管道安装工程竣工图42、设计变更及材料代用文件43、安装工程竣工交接书注:有关工程没有的项目,在对应的序号上打“ x”该有的应齐全、完整压力管道安装质量证明压力管道安装质量证明书编号:压力管道安装汇总表证明书编号:焊接工艺卡热处理工艺卡管材、管件、焊材检验记录JL0710-2012设计文件审查记录技术交底记录交底内容与要求:参加人员(施工管理人员、检验人员、特种作业人员、班组长等)会签:合金钢元件光谱复查报告阀门试验记录管道弯管加工记录焊接发放、回收记录工程焊接记录焊接接头表面质量检验记录焊接返修工艺卡编号:焊接返修及检查记录管道冷紧记录管道补偿装置安装记录管道支、吊架制作安装记录管道安装记录管道热处理报告注:附实际热处理温度——时间自动记录曲线硬度检测报告管道系统压力试验报告管道系统泄漏性试验报告管道系统吹扫与清洗记录。
3.3 工艺管道工程 检验批质量验收记录

监理
(建设)
单位
验收
结论
监理工程师
(建设单位项目代表):年 月 日
3.3.5管沟开挖检验批质量验收记录SY4203
工程名称
分项工程名称
验收部位
施工单位
专业负责人
项目经理
施工执行标准名称及编号
检验批编号
质量验收规范规定
施工单位检
查评定记录
监理(建设)
单位验收意见
主控项目
沟底被破坏(雨水浸泡等)或为岩石沟底时,应按设计规定处理,设计无规定时应超挖200mm。
验收
结论
监理工程师
(建设单位项目代表): 年 月 日
工程名称
分项工程名称
验收部位
施工单位
专业负责人
项目经理
施工执行标准名称及编号
检验批编号
质量验收规范规定
施工单位检
查评定记录
监理(建设)
单位验收意见
主控
项目
管道材质应符合设计要求
一
般
项
目
1
管道清理时,应将坡口及其内外表面20mm范围内的油、漆、锈、毛刺等污物清除掉。
2
相邻两管道焊缝距离
当DN≤700mm时,不应小于1.5倍管道公称直径,且不应小于150mm。
5
咬边
>0.8mm或>12.5%管壁厚(取二者中的较小值),任何长度均不合格。
>6%~12.5%管壁厚或>0.4mm(取二者中的较小值),在焊缝任何300mm连续长度中不超过50mm或焊缝的1/6,取二者中的较小值。
≤0.4mm或≤6%的管壁厚(取二者中的较小值),任何长度均合格。
施工
单位
检查
GB50184培训 (2)

11、管道吹扫 与清洗
增加:污废水处理 和噪声等环保要求; 增补:管道脱脂。
12 、工程交接
增补:施工检查 记录、试验报告。
第一部分
标准概述
4、 GB50184-2011 修订
1、规范名称
调整为:工业金属 管道工程施工质量 验收规范。
2、功能调整
只验收不评定
3、术语
4、检验项目
设主控项目、一般
增加:检验批、观察 检查、100﹪检验、 项目;删除允许偏 抽样检验、局部检验。差抽检点量值规定。
增加:光谱分析、 安全阀整定等。
第一部分
标准概述
3、GB50235-2010修订
7、管道加工
增补:斜接弯头、 焊制翻边接头、支 吊架制作。
增加:主管与支管焊 增补:锆材与有色 接、法兰角焊缝要求; 金属、夹套管和阀 删减:焊接通用性要 门安装要求。 求。
8、焊接和焊后 热处理
9、管道安装
10、管道检查、 检验和试验 增加:焊缝射线和 超声波检测、压力 试验替代要求。
第二部分
标准解读
3.2.2 分部(子分部)工程质量验收应符合下列规定: 1 分部(子分部)工程所含分项工程的质量均应验收合格。 2 分部(子分部)工程所含分项工程的质量应保证资料齐全。 3.2.3 单位(子单位)工程质量验收应符合下列规定: 1 单位(子单位)工程所含分部工程的质量均应验收合格。 2 单位(子单位)工程所含分部工程的质量应保证资料齐全。
第二部分
标准解读
2 阀门的壳体试验压力应为阀门在20℃时最大允许工作压力的1.5倍;密 封试验压力应为阀门在20℃时最大允许工作压力的1.1倍;当阀门铭牌标 示对最大工作压差或阀门配带的操作机构不适宜进行高压密封试验时, 试验压力应为阀门铭牌标示的最大工作压差的1.1倍;阀门的上密封试 验压力应为阀门在20℃时最大允许工作压力的1.1倍;夹套阀门的夹套部 分试验压力应为设计压力的1.5倍。 3 在试验压力下的持续时间不得少于5min。 4 阀门壳体压力试验应以壳体填料无渗漏为合格。阀门密封试验和上密 封试验应以密封面不漏为合格。 5 检验数量:应符合下列规定: 1) 用于GC1级管道和设计压力大于或等于10MPa的C类流体管道的阀门, 应进行100%检验。 2 ) 用于GC2级管道和设计压力小于10MPa的所有C类流体管道的阀门, 应每个检验批抽查10%,且不得少于1个。 3) 用于GC3级管道和D类流体管道的阀门,应每个检验批抽查5%,且不 得少于1个。 6 检验方法:观察检查,检查阀门试验记录,检查水质分析报告。