基于Solidworks/Simulation的链板结构尺寸优化设计
基于SolidWorks仿真的机械零件设计优化研究

基于SolidWorks仿真的机械零件设计优化研究机械零件设计优化研究是实现高质量产品制造和生产效率提升的重要途径。
在机械设计产业中,SolidWorks仿真已经成为一个高效工具,用于验证和修改设计方案,这也成为了机械零件设计优化研究的重要工具之一。
SolidWorks是机械设计软件中最常使用的一种,同时它也是性价比最优的工具之一。
SolidWorks实现了直观的三维设计处理流程并支持详细的物理仿真,可以帮助设计师更好的发现和解决设计中存在的问题。
机械零件的设计过程往往是一个多步骤的过程,设计师需要仔细分析每一个部件的设计,以使得设计具有机械性能,达到先进的产品标准。
而SolidWorks仿真技术可以有效的帮助设计师评估物理性能,包括结构强度、耐久性、重量、摩擦力、热传导、流动和电磁性等。
在SolidWorks中进行机械零件的设计优化可以分为三个大的方面:性能仿真、元素分析和顶层设计。
在性能仿真方面,设计师可通过设置各种不同的物理属性和约束,来模拟机械零件在不同条件下的响应情况以及各个部位的应力变形情况。
根据仿真结果,设计师可以进一步了解不同方案的强度和耐久性,并进行合理的改进和调整,以便达到设计要求。
元素分析方面是通过对机械零件进行分析,了解其所包含的所有元素的互动关系、材料特性和组成等方面。
这种分析可以帮助设计师更好的了解某个零件所能承受的最大负荷等参数,进而优化设计,达到减轻重量、强化材料等效果,提升机械零件的性能。
顶层设计则是将多个零件组合设计成一个实际可行的机械部件,往往是机械零件优化研究的最后一步。
在这个阶段,设计师需要考虑整个机械的组成、设计应用环境、工艺制造以及后续维护等因素。
基于SolidWorks仿真技术,设计师可以有效的控制整个设计过程,根据每一步结果来适时调整和优化。
在机械零件设计过程中,使用SolidWorks仿真技术来进行优化研究,可以提高设计的效率和准确性,降低研究成本和缩短研究周期,提高质量和性能。
基于Solidworks的机械手连接件优化设计

第!!卷第!期锻压装备与制造技术Vol.55No.5CHINA METALFORMING EQUIPMENT&MANUFACTURING TECHNOLOGY Oct.2020基于Solidworks的机械手连接件优化设计周琦,孙移,张良,徐卫国(江阴职业技术学院机电工程系,江苏江阴214405)摘要:通过使用有限元分析的方法,对设计完成的机械手连接件零件进行静应力分析。
以此为依据开展零件的结构优化和改进,在不影响其使用性能的情况下减轻其质量,降低零件的生产成本。
同时,为保证优化后零件的性能,再次对该零件进行强度分析以验证优化结果。
结果表明,采用有限元优化的方法能够在不影响其使用性能前提下有效降低零件质量,降低了设备的研发成本,也为后续该款设备的设计研发奠定了一定的理论与实践基础。
关键词:Soli&wo()s;连接件;有限元;优化设计中图分类号:TP391.7文献标识码:AD01:10.16316/j.issn.1672—0121.2020.05.015文章编号:1672—0121(2020)05—0063—03随着计算机仿真技术的高速发展和应用,采用虚拟样机技术中的有限元分析及仿真手段,验证关键零部件结构设计的准确性和产品性能,已成为一种较为普遍的现代机械设计方法。
使用b 维软件完成零部件的结构造型设计,在此基础上模拟零部件在设备运行中的运动和受力情况,分析零部件结构设计中可能存在的问题或缺陷,及在确设性和可性的展设计,有设计方的准确性,缩短设的研发周期和成本。
激切为激光加工技术中的一种重要应用技术,运用成产中的,较的和高技术,有高和品。
研发的全自动激机,成发展的型和,用激切技术现脚溢料的完切割,使的零成为可能,高产品品和产。
本文动激机中机械爪的连接件开展有限元优化研究,通过使用SolidWorks 软件零件行应力分析结构收稿日期:2020—04—26;修订日期:2020—05—27基金项目:2020年江阴职业技术学院院级科研课题项目(XJ2020LG002)作者简介:周琦(1981—),男,硕士,副教授,研究方向机械创新设计、虚拟制造。
小石坝教你SolidWorks 链轮链条物理仿真教程

小石坝教你SolidWorks 链轮链条物理仿真教程
第一步:在迈迪宝或者Solidworks自带的设计库中调用出齿轮和链条,为链轮链条配合仿真做准备。
第二步:进行干涉检查,仿真计算前不能有任何干涉,否则不能成功,遇到有干涉的情况也不要紧,可将视图转换为隐藏线可见状态,然后将“皮带配合”的装配关系压缩,用鼠标轻轻拖动链轮,直接用肉眼排除干涉,然后再次干涉检查,直至没有干涉为止。
第三步:将“皮带”以及与“皮带”相关的所有装配关系全部删除掉,“皮带”只是借用来装配链条的,现在链条已经装配到位,皮带已经用不着了。
第四步:删除所有链子的所有装配关系,物理仿真是靠零件外形接触来传递运动的,装配关系过多只会起反作用,只需保留必要的装配关系:支持架以及两个链轮的装配关系。
第五步:新建运动算例,左上角的下拉框调整到“基本运动”状态。
第六步:点击“苹果”按钮,将所有零件加上引力参数,引力的大小可以保持默认的,但是一定要注意引力的方向必须是垂直向下的,窗口右下角可以查看引力方向。
第七步:任选一个链轮作为驱动轮,在其上添加一个旋转马达,旋转
方向没有要求,但是旋转速度不宜过快,一来会增加计算机的运算量,二来不利于观察仿真后的结果。
第八步:将所有参与运动的零件设置为接触状态,选上所有的链子和链轮,不要多选更不要漏选。
第九步:点击“计算”按钮进行仿真运算,直至运算结束,可将仿真
运算的结果输出成.avi 格式的视频。
这样就做好了链轮链条物理仿真,感兴趣的朋友可以自己试着去做下,当你完成时,定能感觉非常有成就的。
!!!。
Solidworks中的装配设计与优化策略

Solidworks中的装配设计与优化策略装配设计是Solidworks软件中的重要环节,它涉及到各种零部件的组装方式和优化策略。
在这篇文章中,我们将讨论Solidworks中的装配设计和一些常见的优化策略,以提高装配的效率和质量。
一、装配设计的基本原则1.合理规划构件结构:在装配设计前,需要根据产品的功能需求和结构特点,合理规划构件的结构。
这包括确定构件间的连接方式、定位方式等。
同时,还要考虑到装配过程中的加工、维修和拆卸等因素。
2.标准化设计:在设计过程中,应尽量使用标准件和标准零件,以减少设计和制造成本,并提高装配的效率。
经典的案例是使用标准螺钉和螺母代替自制螺栓。
3.组合设计与模块化设计:将装配设计分为若干个子装配图,通过各子装配图的组合,完成整个产品的装配设计。
这种方式可以提高设计的可读性和维护性,同时也便于团队协作。
二、装配优化策略1.使用 "集装箱"式设计:集装箱式设计是一种将设备、机械的各模块独立设计并单独制造的方法。
这种设计方法可以降低装配的复杂度,减少装配时间和人工成本,提高装配的精度和效率。
例如,可以将设备的控制系统和动力系统独立设计,并采用插拔式连接方式,方便维护和更换。
2.使用"约束"和"发布"功能:Solidworks软件提供了约束和发布功能,可以帮助设计人员快速完成装配设计。
约束功能可以将零件的位置和运动约束起来,确保装配的正确性和稳定性。
发布功能可以将装配中的关键信息发布到BOM(Bill of Materials)表中,方便制造和采购过程。
3.使用"替代装配体"功能:替代装配体是Solidworks中的一个非常实用的功能,可以将相似的零部件快速替换为其他零部件。
这种功能可以节省时间,提高装配的效率和灵活性。
4.使用"构件模式"进行装配设计:构件模式可以帮助设计人员分析和解决装配设计中的冲突和干涉问题。
基于SolidWorks软件的连杆有限元分析与优化设计_图文(精)
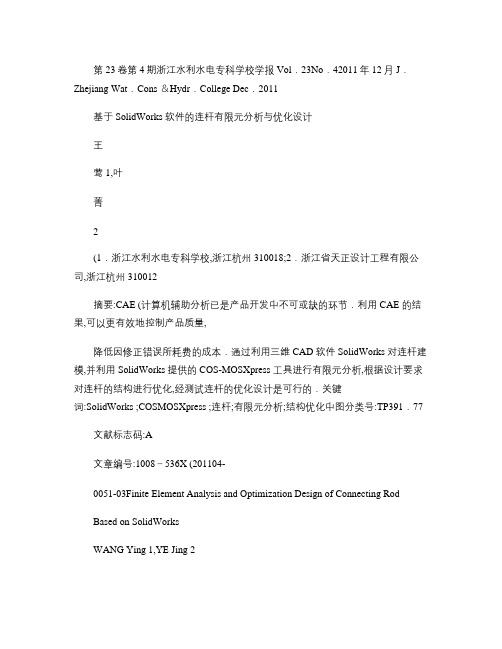
第23卷第4期浙江水利水电专科学校学报Vol.23No.42011年12月J.Zhejiang Wat.Cons &Hydr.College Dec.2011基于SolidWorks 软件的连杆有限元分析与优化设计王莺1,叶菁2(1.浙江水利水电专科学校,浙江杭州310018;2.浙江省天正设计工程有限公司,浙江杭州310012摘要:CAE (计算机辅助分析已是产品开发中不可或缺的环节.利用CAE 的结果,可以更有效地控制产品质量,降低因修正错误所耗费的成本.通过利用三维CAD 软件SolidWorks 对连杆建模,并利用SolidWorks 提供的COS-MOSXpress 工具进行有限元分析,根据设计要求对连杆的结构进行优化,经测试连杆的优化设计是可行的.关键词:SolidWorks ;COSMOSXpress ;连杆;有限元分析;结构优化中图分类号:TP391.77文献标志码:A文章编号:1008-536X (201104-0051-03Finite Element Analysis and Optimization Design of Connecting RodBased on SolidWorksWANG Ying 1,YE Jing 2(1.Zhejiang Water Conservancy and Hydropower College ,Hangzhou310018,China ;Zhejiang Titan Design and Engineering CO.LTD.,Hangzhou 310012,ChinaAbstract :CAE (computer-aided analysis is an integral part of product development.By using of CAE ,the product quality can be controlled more effectively ,while the cost of error correcting can be reduced.In this paper ,3D modeling of Con-necting Rod is set up based on SolidWork ,and finite element analysis of Connecting Rod is also made by using COSMOSX-press.The structure is optimized in order to meet design requirements ,which is proved to be feasible by test.Keywords :SolidWorks ;COSMOSXpress ;connecting rod ;finite element analysis ;structure optimization收稿日期:2011-10-14基金项目:2011年度浙江水利水电专科学校校级科研基金资助项目(XKY-201105作者简介:王莺(1978-,女,浙江杭州人,讲师.主要从事CAD /CAM 及虚拟产品设计开发的研究工作.0引言在过去,一个机械零部件设计完成后,需要加工一个样品来做简单的破坏性检测,觉得可以就去开模子了.经常等到作品完成后或在开模时,才发现大问题.所以成本高,质量也不一定牢靠.而在软件应用分析能力大幅提高的今天,CAE (计算机辅助分析已是产品开发中不可或缺的环节.利用CAE 的结果,可以更有效地控制产品质量,降低因修正错误所耗费的成本[1-2].SolidWorks 软件是一个非常方便、实用的三维建模造型软件,并且它具有强大的CAE (计算机辅助分析功能[3].而CAE 的核心计算方法就是有限元分析.用户可通过SolidWorks 提供的COSMOSX-press 工具进行有限元分析.有限元模型和产品的几何模型是相关的,经过建模和分析后,用户将得到系统计算出的结构反应(变形、应力等.如果计算的结果不符预期,那么用户就可修改参数再次分析,直到达到可接受的设计值为止[4].连杆是机械传动中应用比较广泛的零件.本文主要介绍如何通过SolidWorks 软件对连杆三维建模并进行有限元分析及优化设计,以满足设计要求.1连杆的设计要求连杆的结构尺寸见图1,材料为1060铝合金,若施加垂直于大圆内圆面的力9800N ,则连杆的最大位移变形不得超过0.005mm.2连杆的几何建模根据图1连杆的尺寸要求,用SolidWorks 软件的拉伸、切除、圆角等命令创建连杆的三维模型,见图2.3连杆应力分析条件的设置应力分析条件主要是定义材质、约束、载荷等.3.1指定零件的材料我们进入SolidWorks 下的COSMOSXpress 应力分析界面,根据设计要求,从数据库中选取连杆的材料为1060铝合金,见图3.图3定义材料界面3.2定义约束和载荷因为连杆是以双空心圆头来圈连其他零件,所以先假设固定小圆端(即对小圆这端加约束,约束的面在所有方向都受到约束.点取小圆端轴孔的两个半圆柱面,表示该处是固定面.而在大圆那端加载荷.点取大圆轴孔的内圆面,表示该处是载荷面,应用力9800N 垂直于所选的内圆面,使用统一分布,见图4、图5.4连杆有限元分析在定义了材质、约束和载荷后,就可进行应力分析.系统会对实体模型进行网格化.实体模型的网格化包含两个基本的阶段过程.在第一阶段中,网格生成器将节点放置在边界上.此阶段称为“曲面网格化”.如果第一阶段成功,那么网格生成器会开始第二阶段,即在零件内部生成节点,使用四面体元素来填补体积并在边在线放置边中间的节点.随后系统会自动进行有限元分析[5].4.1应力及变形结果连杆的应力和位移分布见图6、图7,并可通过按钮观看应力变形和位移变形的动态效果,从图中可知,最大应力为1.402ˑ107N /m 2,最大位移变形为0.007523mm.25浙江水利水电专科学校学报第23卷4.2分析结果根据所指定的参数,在连杆的分析及计算中,得到最低安全系数值为1.96741,连杆的安全系数>1.0,就表示使用的材料是安全的.5结构优化设计设计要求施力后的变形量不得超过0.005mm,分析结果为0.007523mm.因此我们需要在载荷、材料和约束条件不变的情况下,对其结构进行优化,使之满足要求.修正大圆外直径值尺寸,将Φ76改为Φ70.系统将会自动对其结构重新进行有限元分析和检查,应力及变形结果见图8、9.从图中可看出改变结构后最大应力为1.574ˑ107N/m2,最大位移变形为0.002772mm.从分析结果看,应力情况结构改变前后变化不大,而位移满足设计要求.连杆的最低安全系数为17.5233,连杆的安全系数>1.0.说明此次结构的优化设计是成功的.可多次对连杆的结构参数进行优化,以获得满足设计条件的最优值.基于篇幅原因,本文在此不再赘述.6结论三维软件SolidWorks中的有限元分析工具COSMOSXpress让用户可直接在计算机上测试产品,而不需要进行昂贵又费时的实物测试,这就可以大大缩短产品的开发周期.本文利用SolidWorks 提供的COSMOSXpress工具对连杆进行有限元分析、计算,并根据设计要求对连杆的结构进行优化,经测试连杆的优化设计是可行的.参考文献:[1]曹岩,李建华.SolidWorks2004产品设计实例精解[M].北京:机械工业出版社,2004.[2]博嘉科技.SolidWorks设计与应用[M].北京:电子工业出版社,2004.[3]SolidWorks公司.SolidWorks装配体建模[M].北京:机械工业出版社,2009.[4]谭雪松,唐小虎,钟廷志,等.SolidWorks中文版机械设计[M].北京:人民邮电出版社,2008.[5]刑启恩.SolidWorks工业设计与案例精粹[M].北京:机械工业出版社,2007.35第4期王莺等:基于SolidWorks软件的连杆有限元分析与优化设计。
基于Solidworks平台的链条的三维造型及装配.
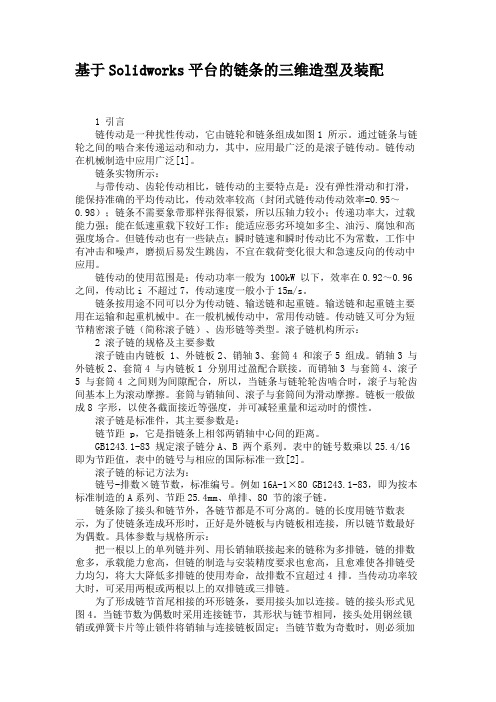
基于Solidworks平台的链条的三维造型及装配1 引言链传动是一种扰性传动,它由链轮和链条组成如图1 所示。
通过链条与链轮之间的啮合来传递运动和动力,其中,应用最广泛的是滚子链传动。
链传动在机械制造中应用广泛[1]。
链条实物所示:与带传动、齿轮传动相比,链传动的主要特点是:没有弹性滑动和打滑,能保持准确的平均传动比,传动效率较高(封闭式链传动传动效率=0.95~0.98);链条不需要象带那样张得很紧,所以压轴力较小;传递功率大,过载能力强;能在低速重载下较好工作;能适应恶劣环境如多尘、油污、腐蚀和高强度场合。
但链传动也有一些缺点:瞬时链速和瞬时传动比不为常数,工作中有冲击和噪声,磨损后易发生跳齿,不宜在载荷变化很大和急速反向的传动中应用。
链传动的使用范围是:传动功率一般为 100kW 以下,效率在0.92~0.96 之间,传动比i 不超过7,传动速度一般小于15m/s。
链条按用途不同可以分为传动链、输送链和起重链。
输送链和起重链主要用在运输和起重机械中。
在一般机械传动中,常用传动链。
传动链又可分为短节精密滚子链(简称滚子链)、齿形链等类型。
滚子链机构所示:2 滚子链的规格及主要参数滚子链由内链板 1、外链板2、销轴3、套筒4 和滚子5 组成。
销轴3 与外链板2、套筒4 与内链板1 分别用过盈配合联接。
而销轴3 与套筒4、滚子5 与套筒4 之间则为间隙配合,所以,当链条与链轮轮齿啮合时,滚子与轮齿间基本上为滚动摩擦。
套筒与销轴间、滚子与套筒间为滑动摩擦。
链板一般做成8 字形,以使各截面接近等强度,并可减轻重量和运动时的惯性。
滚子链是标准件,其主要参数是:链节距 p,它是指链条上相邻两销轴中心间的距离。
GB1243.1-83 规定滚子链分A、B 两个系列。
表中的链号数乘以25.4/16 即为节距值,表中的链号与相应的国际标准一致[2]。
滚子链的标记方法为:链号-排数×链节数,标准编号。
如何使用SOLIDWORKS进行结构优化设计

如何使用S O L I D W O R K S 进行结构优化设计-CAL-FENGHAI-(2020YEAR-YICAI)_JINGBIAN如何使用SOLIDWORKS进行结构优化设计1.建模完成后在“注解”处右键勾选“显示特征尺寸”(无需优化的尺寸可直接隐藏,剩余需优化的尺寸),本例以以下零件为例,分析不同筋板数量下的总质量最小值。
2.在Simulation中“算例顾问点击“新算例”,进入静应力分析1,名称可修改。
3.完成模拟算例,具体操作如下:3.1选中“零件名称”,选择材料;3.3施加载荷;3.4点击“网格”,自动划分网格;3.5点击“运行”,求解该算例。
4.完成以上模拟算例后,右键选中屏幕左下方模拟算例的标签栏,点击“生成新设计算例”,在该新设计算例中定义变量、约束与目标。
4.1在模拟算例中,右键“参数”,点击“编辑/定义”,增加变量。
注意:不同名称的类别不同,选择时注意,本例纯属举例,以一个力和角度作为变量:角度属于模型中的尺寸,可直接选中模型中的尺寸,而力属于仿真,则需手动键入数值;4.2在新设计算例中,在变量中输入需要优化的变量数值,输入最小值、最大值及步长(也可输入离散值);4.3约束本例未定,目标可取质量最小值(受版本限制,本次应用SOLIDWORKSPREMIUM 2014,目标值无法使用数值,例如目标取应力最小值等)。
5.将变量值与模拟算例中对应值相关联。
打开模拟算例的对应项,右键编辑定义,在数值一栏点击“链接数值”,确定。
(例如本例中,力需要此法进行关联)6.点击运行。
系统将针对每一种情形重新修改模型进行有限元仿真,并自动筛选出符合目标值的最优方案。
基于solidworks对结构架的分析和优化

基于solidworks对结构架的分析和优化摘要旋转平台结构架由多种型材焊接而成,对其进行受力分析较复杂,借助solidworks的有限元分析软件对平台结构架进行受力分析,提高了工作效率,同时在满足使用性能的前提下对结构架的尺寸进行了优化设计,降低产品成本,提高了企业的效益。
关键词solidworks2010;有限元;建模;网格化旋转平台的结构架是整个旋转设备中主要承载的部件,它的强度和刚性情况直接决定了旋转平台设备的使用性能,平台的结构和受力情况如图1所示。
图1如果对单根梁进行受力分析显然很容易,但这个结构架为若干不同规格的结构架焊接而成,分析则比较复杂。
每个转台台面钢架由8个扇形钢架组成,单件结构架由三种不同规格的矩形管焊接而成,整个转台的承载能力要求为60 KN,结构架为8个,受力按均布载荷处理,这样每个结构架的受力按8 KN计算。
扇形钢架是由80×60×5、60×60×5和40×20×2.5的矩形管焊接而成。
1 有限元模型的建立及分析首先我们先用solidworks2010建模。
新建一个零件文件,点击绘制草图,选择一个基准面。
用相关的草图命令勾勒出线条,用尺寸进行约束。
草图做好后,添加型钢。
利用solidworks的焊接功能建模,点结构构件工具图标,选取边缘的线段做路径,材料规格选择方管管60×60×5。
同理做出中间的大梁和其余的小梁,规格分别为80×60×5、40×20×2.5。
然后利用剪裁命令处理掉多余的部分,建好的模型如图2。
通过属性设置好材料,可知结构架的重量为82 kg。
梁的边缘都为圆角,这样分析起来会增加分析的时间。
如果我们把结构架上圆角压缩掉,这样对计算结果没有什么影响并提高计算速度,所以将圆角都压缩掉。
1)由于目前的版本不支持多实体,所以先将多实体组合成单实体。
- 1、下载文档前请自行甄别文档内容的完整性,平台不提供额外的编辑、内容补充、找答案等附加服务。
- 2、"仅部分预览"的文档,不可在线预览部分如存在完整性等问题,可反馈申请退款(可完整预览的文档不适用该条件!)。
- 3、如文档侵犯您的权益,请联系客服反馈,我们会尽快为您处理(人工客服工作时间:9:00-18:30)。
基于Solidworks/Simulation的链板结构尺寸优化设计
链条是重要的基础零部件,其中滚子链链板结构为“8”字形机构合理,在国家标准中并未对影响链板应力分布的胯部尺寸进行规定。
文章以ISO 08A型滚子链为例,利用Solidworks软件创建了08A型链条链节的三维模型,并利用Solidworks/Simulaiton对链板结构进行了应力分析,且根据其应力分布特点对其胯部尺寸进行了优化。
结果显示:链板最大应力发生在销轴孔处,胯部应力次之,二者应力差值高达59MPa,分布极不合理,优化链板胯部尺寸得到,当胯部尺寸取值为0.4375倍节距时,销轴孔与胯部应力基本相等,差值为2MPa,应力分布合理,为链板结构设计提供理论指导。
标签:滚子链;链板;应力分布;尺寸优化
滚子链作为重要的机械基础零部件,作为牵引件被广泛的应用于机械传动、输送、农机、化工等行业领域[1]。
链板是其重要的组成部分,其工作能力的优劣直接影响了链传动系统的整体性能。
文献研究表明:“8”字形结构滚子链链板结构应力分布合理,是滚子链链板的最佳结构形式[2,3,4],但是并未对最佳的“8”字形轮廓尺寸进行深入探讨。
文章以ISO 08A型滚子链为例,利用Solidworks软件创建了链节三维模型,并且利用Solidworks/simulaiton分析了链板的结构应力,并以其胯部宽度尺寸为设计变量,链板销轴孔与胯部最大应力为约束,对其胯部尺寸进行了优化,使得链板应力分布更为合理,为链板结构设计提供理论指导。
1 链节三维模型
滚子链包括A系列滚子链与B系列滚子链两类,其中A系类滚子链基本结构参数与节距P成一定比例关系[5]。
因此,文章选择ISO 08A型滚子链对链板结构应力进行分析,优化胯部宽度尺寸,得到其与节距P尺寸比例关系具有一般意义。
滚子链主要由外链板、销轴、内链板、套筒以及滚子5部分构成,其中外链板与销轴过盈配合,套筒与内链板过盈配合,滚子与套筒间隙配合,如图1所示。
2 有限元模型的创建
文章利用Solidworks Simulaiton有限元设计与分析软件对链板的应力分布进行分析。
2.1 模型简化
对链节整体进行计算分析,工作量大,时间长,且数据精确程度难以保障,利用模型的对称性,选择模型结构的1/2、1/4甚至1/8部分,进行计算分析,可
以有效节省计算时间,提高计算精度。
分析链节的结构可知,链节是典型的对称结构,可以取如图2所示的结构单元,对该模型进行分析。
2.2 约束条件及载荷设置
为简化后的模型添加夹具,如图2所示,分别在面1、2、4上添加对称夹具,对分析模型三维方向进行了限制;在面3上添加力载荷600N,力方向垂直于面1。
2.3 网格划分及求解器设置
对如图2所示的模型进行网格划分,首先对模型整体按照中等精度进行网格划分,然后对链板结构面1和面5的网格进行精细控制,控制其网格单元大小为0.15mm,如图3所示。
在运行仿真程序之前,对求解器进行设置启用“使用软弹簧使模型稳定”功能,采用Direct Sparse计算方式。
运行仿真程序,得到仿真结果。
3 仿真结果分析
如图4所示为求解得到了在600N力的作用下,链板的应力分布云图。
由图4可知:链板最大应力发生在销轴孔圆柱面上为162.410MPa;胯部次之為103.727MPa,二者差值为58.683MPa,显然,应力分布不合理。
在链板高度一定的情况下,通过调节胯部宽度尺寸,来达到调节链板结构应力分布的目的。
利用Solidworks设计算例模块,设置变量参数为胯部宽度尺寸,取值5P/16至13P/16,步长P/16,监测数值为模拟数值销轴孔处最大应力及胯部最大应力。
运行设计算例,得到9种设计情形,提取设计图表,得到如图5所示的销轴孔与胯部最大应力随胯部宽度变化的变化曲线。
分析图5可得:随着胯部宽度尺寸增大,销轴孔处与胯部处最大应力均逐渐变小,且在设计情形3处,即胯部宽度为7P/16时,胯部最大应力为181.37MPa,销轴孔处最大应力为177.61MPa,二者最大应力差值最小为3.76MPa,两处应力大小基本相等,应力分布合理,可以有效增强工作链板的工作能力。
4 结束语
以08A型滚子链为例,对滚子链链板的“8”字结构进行了进一步探讨。
(1)利用Solidworks软件创建了滚子链链节的三维模型,利用Solidworks/Simulation软件对链板进行了结构静力学分析。
结果表明:现有滚子链链板的应力分布不合理,最大应力发生在销轴孔处,胯部最大应力次之,且两处最大应力差值较大,应力分布不合理。
(2)利用Solidworks设计算例模块,以胯部宽度为变量参数,提取销轴孔与胯部最大应力值,得到两处应力随胯部宽度变化的变化曲线,发现当胯部宽度为7P/16时,两处应力差值最小,应力分布合理。
文章研究成果将为滚子链链板的结构设计提供指导。
参考文献
[1]郑志峰,王义行,柴邦衡.链传动[M].机械工业出版社,1984.
[2]黄天成,王宏丽,郑强元,等.基于有限元法的链板结构设计研究[J].制造业自动化,2012(16):110-112.
[3]董华明,王雅丽,康辉.链板形状设计的新方法[J].吉林工业大学学报,1995(02):75-80.
[4]王应生.滚子链链板应力的研究[J].起重运输机械,1992(06):32-34,36.
[5]张经源.链条传动与制造[M].浙江大学出版社,1989.
作者简介:王文成(1985-),男,河北沧州人,承德石油高等专科学校机械工程系讲师,博士,主要研究方向:高速链传动技术理论及应用等。