全氧燃烧、纯氧助燃及富氧燃烧节能技术比较#优选、
富氧燃烧的资料
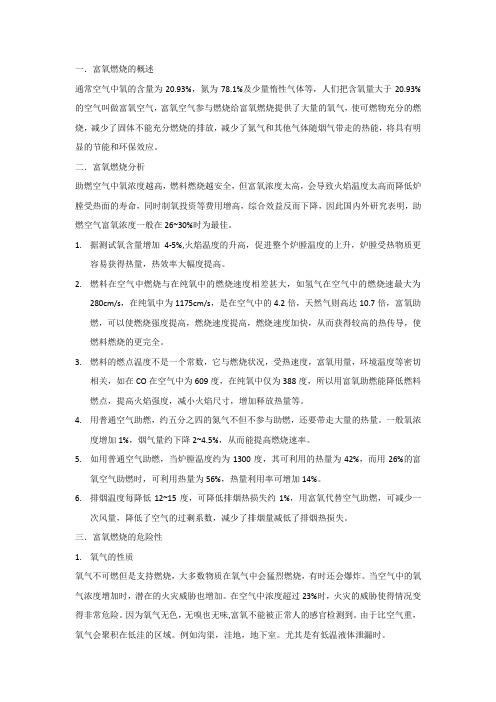
一.富氧燃烧的概述通常空气中氧的含量为20.93%,氮为78.1%及少量惰性气体等,人们把含氧量大于20.93%的空气叫做富氧空气,富氧空气参与燃烧给富氧燃烧提供了大量的氧气,使可燃物充分的燃烧,减少了固体不能充分燃烧的排放,减少了氮气和其他气体随烟气带走的热能,将具有明显的节能和环保效应。
二.富氧燃烧分析助燃空气中氧浓度越高,燃料燃烧越安全,但富氧浓度太高,会导致火焰温度太高而降低炉膛受热面的寿命,同时制氧投资等费用增高,综合效益反而下降,因此国内外研究表明,助燃空气富氧浓度一般在26~30%时为最佳。
1.据测试氧含量增加4-5%,火焰温度的升高,促进整个炉膛温度的上升,炉膛受热物质更容易获得热量,热效率大幅度提高。
2.燃料在空气中燃烧与在纯氧中的燃烧速度相差甚大,如氢气在空气中的燃烧速最大为280cm/s,在纯氧中为1175cm/s,是在空气中的4.2倍,天然气则高达10.7倍,富氧助燃,可以使燃烧强度提高,燃烧速度提高,燃烧速度加快,从而获得较高的热传导,使燃料燃烧的更完全。
3.燃料的燃点温度不是一个常数,它与燃烧状况,受热速度,富氧用量,环境温度等密切相关,如在CO在空气中为609度,在纯氧中仅为388度,所以用富氧助燃能降低燃料燃点,提高火焰强度,减小火焰尺寸,增加释放热量等。
4.用普通空气助燃,约五分之四的氮气不但不参与助燃,还要带走大量的热量。
一般氧浓度增加1%,烟气量约下降2~4.5%,从而能提高燃烧速率。
5.如用普通空气助燃,当炉膛温度约为1300度,其可利用的热量为42%,而用26%的富氧空气助燃时,可利用热量为56%,热量利用率可增加14%。
6.排烟温度每降低12~15度,可降低排烟热损失约1%,用富氧代替空气助燃,可减少一次风量,降低了空气的过剩系数,减少了排烟量减低了排烟热损失。
三.富氧燃烧的危险性1.氧气的性质氧气不可燃但是支持燃烧,大多数物质在氧气中会猛烈燃烧,有时还会爆炸。
全氧燃烧技术

全氧燃烧技术我们日常生活中,随处可见药用玻璃瓶的身影。
无论是饮料、药品,还是化妆品等等,药用玻璃瓶都是它们的好伙伴。
这些玻璃包装的容器,因其透明的美感,化学稳定性好,对内容物无污染,可以高温加热,旧瓶可回收再生利用等优点,一直被认为是最好的包装材料。
尽管如此,为了与金属罐、塑料瓶等包装材料竞争,药用玻璃瓶也在不断地提高其生产技术,使产品质量更好、外观更美、成本更低。
在蓄热式玻璃窑的建造技术之后,玻璃熔化技术迎来了第二次革命,这就是全氧燃烧技术。
在过去十年里,世界各国在玻璃熔窑上进行该技术改造的实践表明,全氧燃烧技术具有低投资、低能耗、低污染物排放等显著的优越性。
在美国、欧洲,轻量化的瓶罐已是玻璃瓶罐的主导产品,小口压吹技术(NNPB)、瓶罐的冷热端喷涂技术等,都是轻量化生产的先进技术。
德国公司已能生产出1公升的浓缩果汁瓶,仅重295克,瓶壁表面涂覆了有机树脂,可提高瓶子压力强度20%。
在现代工厂里,生产玻璃瓶可不是容易的事,有很多的科学难题需要解决。
全氧燃烧技术在玻璃熔炉的应用一、概论:改革开放以来, 国民经济迅速发展举世瞩目。
玻璃工业(平板玻璃、电子玻璃、玻璃纤维、日用玻璃、光学玻璃等)相应得到迅速发展,仅以浮法玻璃为例,截止2004年底,已建成投产126条浮法线(总产量已达到3亿重量箱,日熔量52930T),还有51条线在建、拟建。
熔化玻璃采用煤、煤焦油、重油、烊黄 ⒒虻?少量)作燃料。
目前我国熔化一公斤玻璃液(平板玻璃)平均指标在1500-1800大卡。
按此单位能耗测算,玻璃工业无疑是重要能耗大户之一。
当今世界石油价格上涨,我国进口石油逐年增加(中国生产力发展研究报告研究表明;中国石油进口率测算到2010、2015和2020年进口率下限将分别达到55.4%、57.4%、59.7%。
大大超过30%理论上控制指标,按国际能源组织今年预测2030年中国石油对外依存度将达到74%的进口率)。
玻璃熔窑大部分采用重油做燃料,因此,对于玻璃工业的总量控制,尤其是高能耗玻璃熔窑的能耗限制,从节能、成本考虑采用新燃烧技术已是当务之急。
水泥生产制备全氧燃烧、富氧燃烧技术推广方案(一)

水泥生产制备全氧燃烧、富氧燃烧技术推广方案一、实施背景水泥行业是全球最大的二氧化碳排放源之一,其碳排放量约占全球总排放量的7%。
在全球气候变化的背景下,减少水泥行业的碳排放量已成为当务之急。
另一方面,随着我国经济发展的转型和升级,水泥行业的产业结构也需要进行调整和优化。
因此,推广水泥生产制备全氧燃烧、富氧燃烧技术,已成为我国水泥行业产业结构改革的重要方向。
全氧燃烧、富氧燃烧技术是一种新型的燃烧技术,相比传统的空气燃烧技术,具有更高的燃烧效率和更低的二氧化碳排放量。
全氧燃烧技术采用纯氧作为氧化剂,燃烧过程中产生的烟气主要为水蒸气,几乎不产生氮气,因此烟气中的二氧化碳浓度较高,便于进行捕获和利用。
富氧燃烧技术则采用氧气浓度高于空气的富氧空气作为氧化剂,能够减少烟气中氮气的含量,提高二氧化碳的浓度,同样有利于二氧化碳的捕获和利用。
全氧燃烧、富氧燃烧技术已在一些发达国家的水泥企业中得到了应用,并取得了一定的减排效果。
在我国,一些水泥企业也开始进行试点应用,但由于技术、资金、政策等方面的限制,尚未得到广泛应用。
因此,本次推广方案旨在通过产业结构改革的角度,加快水泥行业全氧燃烧、富氧燃烧技术的推广应用,促进水泥行业的绿色转型和升级。
二、工作原理1. 全氧燃烧技术全氧燃烧技术是指采用纯氧作为氧化剂,将燃料和纯氧在高温下进行燃烧,产生的水蒸气和二氧化碳为主要烟气的燃烧方式。
其工作原理如图1所示。
在全氧燃烧过程中,燃料和纯氧在高温下发生氧化还原反应,生成水和二氧化碳。
由于采用纯氧作为氧化剂,燃烧过程中几乎不产生氮气,因此烟气中的二氧化碳浓度较高,一般可达到80%以上。
同时,由于烟气中水蒸气的含量也较高,可以采用冷凝的方法将水蒸气转化为液态水进行回收利用,进一步减少二氧化碳的排放量。
2. 富氧燃烧技术富氧燃烧技术是指采用氧气浓度高于空气的富氧空气作为氧化剂,将燃料和富氧空气在高温下进行燃烧,产生的烟气中二氧化碳浓度较高的燃烧方式。
富氧燃烧技术富氧燃烧技术与污染物排放

富氧燃烧技术富氧燃烧技术与污染物排放富氧燃烧是一种新兴的燃烧技术。
富氧燃烧能够显著提高燃烧效率和火焰温度,但由于制氧成本较高的问题,在上世纪80年代经历黄金成长期之后,发展速度放缓。
而后随着制氧方法的成就,一方面是富氧膜技术的进展,富氧燃烧技术近20年来逐渐推广。
而且,富氧燃烧也便于在现有锅炉设备上改造实现,拥有可预期发展前景的良好发展前景。
与普通的空气燃烧相比,富氧燃烧技术可以显著节约能源,其对环境的影响方面也具有不同特点。
其中与此相反有利的一面,也有不利的一面。
本文主要从较为常见的碳排放、粉尘污染、二氧化硫和氮氧化物的排放四个方面来讨论富氧燃烧对环境的影响。
1 富氧燃烧对碳排放的影响在对CO2排放限制越发规限严苛的当代社会,节能减排是全社会注目的焦点。
常规的燃烧方式都存在着不足之处,局部缺氧会产生不完全燃点,火焰温度偏低也会构成产生不完全燃烧,浪费燃料,而作为粉尘排放的未燃烧燃料也会造成大气污染。
母舒氏燃烧针对缺氧区,局部增氧,可或使燃料燃点降低,燃烧速度增快,燃料燃烧更彻底,而火焰温度则会不断提高。
根据维恩位移定律,各向异性辐射强度与温度的四次方比值,可促使热能的热力利用率大幅提升。
同时,富氧燃烧可以减少鼓风机进风量和高温烟气的排放量,可降低热能损失。
氧气中氧气的含量占20.94%,而不助燃的氮气占78.097%。
在燃烧过程中,氮气带走了大量热量,采用富氧燃烧后可减少凝结进风量,即减轻了热能的流失,并且由于风量的回升,可以使用功率更小的风机。
假设燃料完全挥发,空气含氧量φ=21%,理论氧气量为Vo,过量空气系数a=1.2,实际空气量为Va,则Va=a根据以上公式,设某低速理论氧气量为1 m3/s,可列表1。
对某煤种燃烧的分析,当助燃废气含氧率从21%升高至30%时,理论空气量减少30.0%,理论烟气量减少28.8%,损失减少16.3%。
据介绍,日本将23%的富氧用于化铁炉,节能高达26.7%;美国在铸造炉上使用23%~24%的富氧,平均节能44%;国内的合肥钢厂采用富氧,每年平均节省螺纹钢42万吨。
富氧燃烧技术节能机理
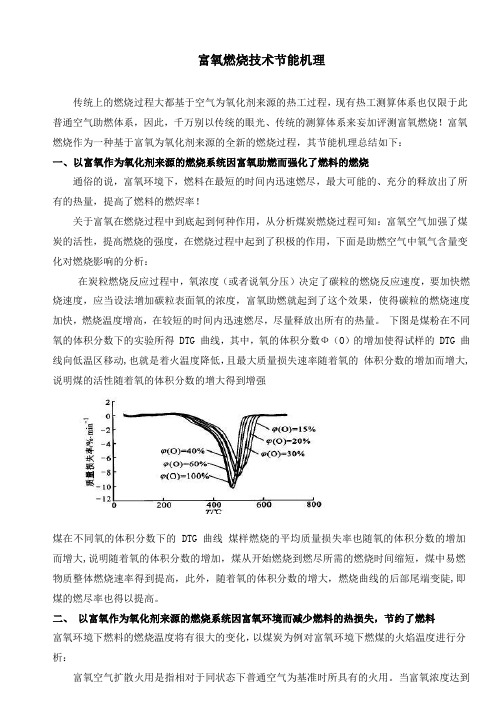
富氧燃烧技术节能机理传统上的燃烧过程大都基于空气为氧化剂来源的热工过程,现有热工测算体系也仅限于此普通空气助燃体系,因此,千万别以传统的眼光、传统的测算体系来妄加评测富氧燃烧!富氧燃烧作为一种基于富氧为氧化剂来源的全新的燃烧过程,其节能机理总结如下:一、以富氧作为氧化剂来源的燃烧系统因富氧助燃而强化了燃料的燃烧通俗的说,富氧环境下,燃料在最短的时间内迅速燃尽,最大可能的、充分的释放出了所有的热量,提高了燃料的燃烬率!关于富氧在燃烧过程中到底起到何种作用,从分析煤炭燃烧过程可知:富氧空气加强了煤炭的活性,提高燃烧的强度,在燃烧过程中起到了积极的作用,下面是助燃空气中氧气含量变化对燃烧影响的分析:在炭粒燃烧反应过程中,氧浓度(或者说氧分压)决定了碳粒的燃烧反应速度,要加快燃烧速度,应当设法增加碳粒表面氧的浓度,富氧助燃就起到了这个效果,使得碳粒的燃烧速度加快,燃烧温度增高,在较短的时间内迅速燃尽,尽量释放出所有的热量。
下图是煤粉在不同氧的体积分数下的实验所得 DTG 曲线,其中,氧的体积分数Ф(O)的增加使得试样的 DTG 曲线向低温区移动,也就是着火温度降低,且最大质量损失速率随着氧的体积分数的增加而增大,说明煤的活性随着氧的体积分数的增大得到增强煤在不同氧的体积分数下的 DTG 曲线煤样燃烧的平均质量损失率也随氧的体积分数的增加而增大,说明随着氧的体积分数的增加,煤从开始燃烧到燃尽所需的燃烧时间缩短,煤中易燃物质整体燃烧速率得到提高,此外,随着氧的体积分数的增大,燃烧曲线的后部尾端变陡,即煤的燃尽率也得以提高。
二、以富氧作为氧化剂来源的燃烧系统因富氧环境而减少燃料的热损失,节约了燃料富氧环境下燃料的燃烧温度将有很大的变化,以煤炭为例对富氧环境下燃煤的火焰温度进行分析:富氧空气扩散火用是指相对于同状态下普通空气为基准时所具有的火用。
当富氧浓度达到27%时,对比普通空气(含氧浓度21%),燃烧温度上升了295℃,每公斤燃料减少火用损失746KJ,相当于节约5.5%的燃料,如果富氧浓度达到30%,燃烧温度上升了438℃,减少火用损失1031kJ,相当于节约7.6%的燃料综上述分析可知:煤炭的低发热值越高,在同等的富氧率情况下,火用损失就越少,富氧燃烧节煤率也就越高,尽管实际工程应用时略有误差,结合炉窑工况的燃烧温度提高幅度也不尽相同,但显然这些都抹杀不了富氧燃烧卓越的节能效果三、以富氧作为氧化剂来源的燃烧系统因富氧环境有效的提高了燃烧系统的升温速率而节能由台湾工研院吴国光、焦鸿文、张育诚等多位博士所做的21%~30%富氧燃烧实验中所载,以燃烧后废气排放维持在5%、炉膛温度1200℃、固定瓦斯流量30.5m3/hr为测试点,到达1200℃累计所用时间定义为升温时间,由下图可明显的看出,在相同的燃烧条件下,因进风空气的氧气浓度升高,升温速度快了!下图为相同燃烧条件含氧浓度不同的锅炉升温速度图标据上图,氧气浓度到达升温目标温度所需时间分别为 :氧气纯度21% 24% 26% 28% 30%升温秒数11396 9209 8624 7688 7330由此可知,与普通空气作为氧化剂的燃烧系统比较,在含氧24%的富氧环境下的富氧燃烧系统,同样以燃烧后废气排放维持在5%、炉膛温度1200℃、固定瓦斯流量30.5m3/hr为测试点,到达1200℃累计所用时间也即升温时间自11396秒缩短到9209秒!(11396-9209)/11396*100%=19%!节能效果不言而喻!四、对可适当提高工艺温度的燃烧系统来说,因富氧环境可有效的提高炉内火焰温度,有效的改善了炉内火焰的热传递效率,显著节能!依工业炉节能技术手册实验数据显示:氧浓度于21%时,火焰温度1420℃,当氧浓度提升至23%时,火焰温度提升至1700℃,火焰温度提升280℃,下表为火焰温度与富氧空气中的氧浓度之间关系,摘录自《工业炉节能技术手册》:火焰温度o C空气过剩系数21% 23% 25% 27% 29% 31%1.0 2,120 2,250 2,350 2,400 2,415 2,4251.2 1,800 2,000 2,150 2,270 2,350 2,3801.5 1,420 1,700 1,900 2,080 2,200 2,280氧浓度(%) 21% 23%火焰温度(℃) 1420℃1700℃炉膛温度(℃) 800℃950℃依上表数据显示:1.富氧火焰温度增加,可提升炉膛内温度,使得炉膛内受热截面积受热温差大,热交换率提升,火焰温度增加,预计 23%富氧空气,富氧燃烧可降低碳的燃点,燃烧完全而强烈,火焰充满度好,提高了炉膛的整体温度,一个物体向周围辐射的热与该物体的绝对温度的四次方成正比,水冷壁获得辐射能量将大大提高,炉窑整体热效率也将得以提高,锅炉炉膛温度增加(800℃→950℃),依上述条件,23%富氧空气约可提升20%的热传导效率!节能可达10%。
浮法玻璃窑炉的有效节能三种途径
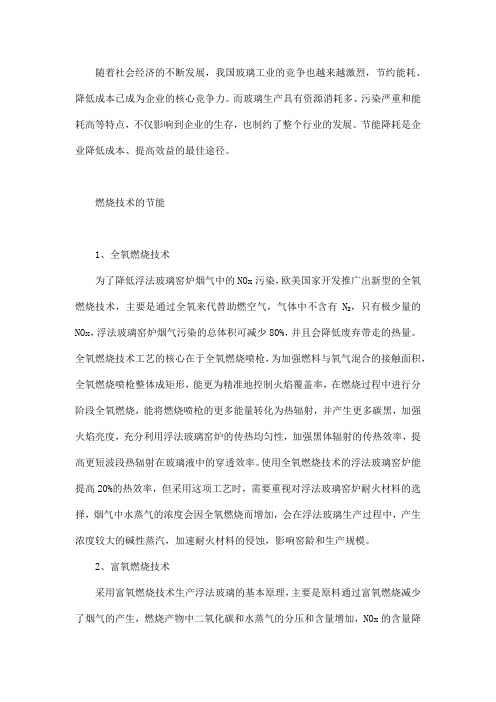
随着社会经济的不断发展,我国玻璃工业的竞争也越来越激烈,节约能耗、降低成本已成为企业的核心竞争力。
而玻璃生产具有资源消耗多、污染严重和能耗高等特点,不仅影响到企业的生存,也制约了整个行业的发展。
节能降耗是企业降低成本、提高效益的最佳途径。
燃烧技术的节能1、全氧燃烧技术为了降低浮法玻璃窑炉烟气中的NOx污染,欧美国家开发推广出新型的全氧燃烧技术,主要是通过全氧来代替助燃空气,气体中不含有N₂,只有极少量的NOx,浮法玻璃窑炉烟气污染的总体积可减少80%,并且会降低废弃带走的热量。
全氧燃烧技术工艺的核心在于全氧燃烧喷枪,为加强燃料与氧气混合的接触面积,全氧燃烧喷枪整体成矩形,能更为精准地控制火焰覆盖率,在燃烧过程中进行分阶段全氧燃烧,能将燃烧喷枪的更多能量转化为热辐射,并产生更多碳黑,加强火焰亮度,充分利用浮法玻璃窑炉的传热均匀性,加强黑体辐射的传热效率,提高更短波段热辐射在玻璃液中的穿透效率。
使用全氧燃烧技术的浮法玻璃窑炉能提高20%的热效率,但采用这项工艺时,需要重视对浮法玻璃窑炉耐火材料的选择,烟气中水蒸气的浓度会因全氧燃烧而增加,会在浮法玻璃生产过程中,产生浓度较大的碱性蒸汽,加速耐火材料的侵蚀,影响窑龄和生产规模。
2、富氧燃烧技术采用富氧燃烧技术生产浮法玻璃的基本原理,主要是原料通过富氧燃烧减少了烟气的产生,燃烧产物中二氧化碳和水蒸气的分压和含量增加,NOx的含量降低,火焰黑度加大,火焰温度提升,加快了原料的燃烧过程,提高了火焰在配合料与玻璃液之间的传热效率,从而提高了浮法玻璃窑炉的熔化效率。
富氧燃烧技术对燃烧设备具有更高要求。
燃料在燃烧过程中需要氧气,这些氧气通常来源于空气,但氧气在助燃空气中仅占21%的比重,而空气中其余的氮气并不会参加燃烧,反而会吸收大量的热量,阻碍燃烧效率的提高,增加燃料消耗。
因此提高空气中的氧气含量,可以更好地保持热量,提高燃料利用效率。
用28%的富氧空气进行燃烧试验时,热量损失减少25%,热量损失的减少也降低了燃料消耗。
(定)磁能富氧燃烧简介
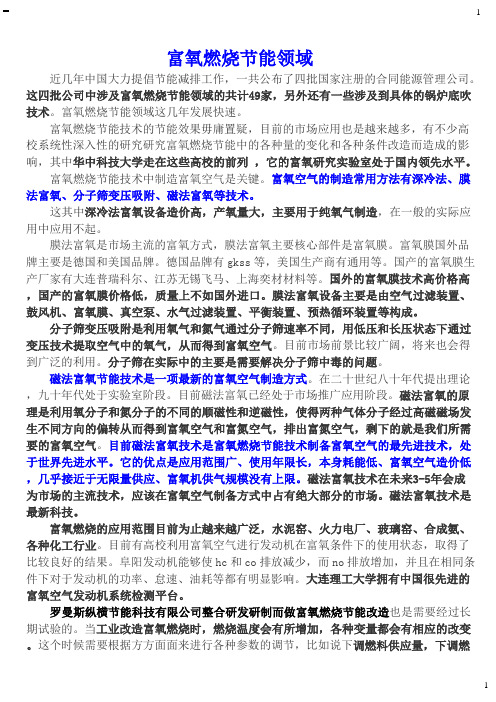
富氧燃烧节能领域近几年中国大力提倡节能减排工作,一共公布了四批国家注册的合同能源管理公司。
这四批公司中涉及富氧燃烧节能领域的共计49家,另外还有一些涉及到具体的锅炉底吹技术。
富氧燃烧节能领域这几年发展快速。
富氧燃烧节能技术的节能效果毋庸置疑,目前的市场应用也是越来越多,有不少高校系统性深入性的研究研究富氧燃烧节能中的各种量的变化和各种条件改造而造成的影响,其中华中科技大学走在这些高校的前列,它的富氧研究实验室处于国内领先水平。
富氧燃烧节能技术中制造富氧空气是关键。
富氧空气的制造常用方法有深冷法、膜法富氧、分子筛变压吸附、磁法富氧等技术。
这其中深冷法富氧设备造价高,产氧量大,主要用于纯氧气制造,在一般的实际应用中应用不起。
膜法富氧是市场主流的富氧方式,膜法富氧主要核心部件是富氧膜。
富氧膜国外品牌主要是德国和美国品牌。
德国品牌有gkss等,美国生产商有通用等。
国产的富氧膜生产厂家有大连普瑞科尔、江苏无锡飞马、上海奕材材料等。
国外的富氧膜技术高价格高,国产的富氧膜价格低,质量上不如国外进口。
膜法富氧设备主要是由空气过滤装置、鼓风机、富氧膜、真空泵、水气过滤装置、平衡装置、预热循环装置等构成。
分子筛变压吸附是利用氧气和氮气通过分子筛速率不同,用低压和长压状态下通过变压技术提取空气中的氧气,从而得到富氧空气。
目前市场前景比较广阔,将来也会得到广泛的利用。
分子筛在实际中的主要是需要解决分子筛中毒的问题。
磁法富氧节能技术是一项最新的富氧空气制造方式。
在二十世纪八十年代提出理论,九十年代处于实验室阶段。
目前磁法富氧已经处于市场推广应用阶段。
磁法富氧的原理是利用氧分子和氮分子的不同的顺磁性和逆磁性,使得两种气体分子经过高磁磁场发生不同方向的偏转从而得到富氧空气和富氮空气,排出富氮空气,剩下的就是我们所需要的富氧空气。
目前磁法富氧技术是富氧燃烧节能技术制备富氧空气的最先进技术,处于世界先进水平。
它的优点是应用范围广、使用年限长,本身耗能低、富氧空气造价低,几乎接近于无限量供应、富氧机供气规模没有上限。
★间歇法、富氧法、纯氧法气化技术的特点及优缺点比较

固定床间歇、富氧、纯氧气化技术的特点及优缺点比较田守国江西昌昱实业有限公司注1:根据贵公司的要求,对照分析三种固定床气化工艺的经济性、可行性。
注2:因贵公司生产工艺需求无氮水煤气,下面只重点介绍固定床煤气炉生产水煤气的工艺比较。
注3:工艺比较的条件;∮2800煤气炉(截面积6.2㎡)、质量比较好的无烟块煤。
一、普通间歇法、富氧法、纯氧法煤气的组分?H2、CO、CO2的组分比例?有效气比例?单台炉产气量?1.固定床间歇气化生产水煤气:煤气成份:CO2=7—9%、O2=0.4-0.5%、CO=38-39%、H2=43—46%、N2=4—6%、DH4=1-2%。
有效气体含量80%左右。
固定床煤气炉间歇气化生产水煤气,是最不经济的气化工艺。
单位面积的气化强度仅为650—750m3/㎡.h。
而且,吹风过程前后都要有排除氮气的过程,氮气是由煤气带出去的,排氮过程伴有大量煤气浪费。
间歇气化生产水煤气,煤气中氮气含量控制越低,煤耗越高、发气量越小,如果氮气含量控制小于4%单位面积的气化强度仅为650m3/㎡.h。
而且出气温度高,显热损失大,灰渣残炭量≥20%,吹风带出物达到了10%左右,型煤气化能达到15—20%。
因此,间歇气化生产水煤气原料转化利用率仅为65%左右,吨醇原料煤消耗2吨左右。
而且吹风过程有大量烟气排放,不但降低了煤气炉的热效率,更不符合国家洁净煤气化的产业政策。
2.固定床富氧连续气化生产半水煤气:半水煤气成份:CO2=16-19%、O2=0.2-0.5%、CO=28-32%、H2=36-39%、N2=10—14%、DH4=1-3%。
有效气体含量70%左右。
入炉富氧气中氧浓度50—58%单位面积的气化强度仅为1200—1300m3/㎡.h。
富氧连续气化只能生产半水煤气,不适应醇类产品生产。
3.纯氧+蒸汽生产水煤气成份:纯氧连续气化的水煤气成份因原煤质量、装备条件、控制条件而不同而有一定差距。
(太化)半焦(也称“兰炭”)气体成份:CO2=16.5-17%、02=0.2—0.4%、CO=38—39.8%、H2=44.4%、N2=0、CH4=≤1.0%。
- 1、下载文档前请自行甄别文档内容的完整性,平台不提供额外的编辑、内容补充、找答案等附加服务。
- 2、"仅部分预览"的文档,不可在线预览部分如存在完整性等问题,可反馈申请退款(可完整预览的文档不适用该条件!)。
- 3、如文档侵犯您的权益,请联系客服反馈,我们会尽快为您处理(人工客服工作时间:9:00-18:30)。
全氧燃烧、纯氧助燃及富氧燃烧节能技术比较
玻璃熔窑的节能降耗一直是业内关注的重大课题,在能源危机日益加重的今天,玻璃熔窑对高品质能源的过度依赖已经制约了玻璃行业的发展。
玻璃熔窑燃烧过程中,空气成分中占78%的氮气不参加燃烧反应,大量的氮气被无谓地加热,在高温下排入大气,造成大量的热量损失,氮气在高温下还与氧气反应生成NOx,NOx气体排入大气层极易形成酸雨造成环境污染。
另一方面随着高科技和经济社会的发展,要求制造各种低成本、高质量的玻璃,而全氧燃烧技术正是解决节能、环保和高熔化质量这几大问题的有效手段,被誉为玻璃熔制技术的第二次革命。
纯氧燃烧技术最早主要被应用于增产、延长窑炉使用寿命以及减少NOx排放,但随着制氧技术的发展以及电力成本的相对稳定,纯氧燃烧技术正在成为取代常规空气助燃的更好选择,这得益于纯氧燃烧技术在节能、环保、质量、投资等方面的优势。
氧气燃烧的应用分为整个熔化部使用纯氧燃烧的全氧燃烧技术、纯氧辅助燃烧技术以及局部增氧富氧燃烧技术等几种方式。
1、全氧燃烧技术的优点
1)玻璃熔化质量好。
全氧燃烧时玻璃粘度降低,火焰稳定,无换向,燃烧气体在窑内停留时间长,窑内压力稳定,有利于玻璃的熔化、澄清,减少玻璃的气泡及条纹。
2)节能降耗。
全氧燃烧时废气带走的热量和窑体散热同时下降。
研究和实践表明,熔制普通钠钙硅平板玻璃熔窑可节能约30%以上。
3)减少NOx排放。
全氧燃烧时熔窑废气中NOx排放量从2200mg/Nm3降低到500mg/Nm3以下,粉尘排放减少约80%,SO2排放量减少30%。
4)改善了燃烧,提高了熔窑熔化能力,可使熔窑产量得以提高。
玻璃熔窑采用全氧燃烧时,燃料燃烧完全,火焰温度高,配合料熔融速度加快,可提高熔化率10%以上。
5)熔窑建设费用低。
全氧燃烧窑结构近似于单元窑,无金属换热器及小炉、蓄热室。
窑体呈一个熔化部单体结构,占地小,建窑投资费用低。
6)熔窑使用寿命长。
全氧燃烧可使火焰分为两个区域,在火焰下部由于全氧的喷入,使火焰下部温度提高,而火焰上部的温度有所降低,使熔窑碹顶温度下降,减轻了对大碹的烧损,同时,火焰空间使用了优质耐火材料,窑龄可提高到1 0年以上。
7)生产成本总体下降。
举例来说,350t/d优质浮法玻璃熔窑采用全氧燃烧技术,按照目前油价3500元/吨测算,每年可为企业创造800万元的附加直接经济效益,而从长远看油价的进一步上升是必然趋势。
2、浮法玻璃熔窑纯氧辅助燃烧技术
由传热学理论可知,配合料在玻璃熔窑内熔化获得能量的主要途径是来自窑内燃烧火焰的辐射热。
由于配合料的黑度比玻璃液的黑度大得多,即配合料的吸热能力比玻璃液的吸热能力大,这样有效地增加配合料上方的热负荷,并不致产生熔窑内衬温度的显著升高。
这就是0#小炉位置增设一对全氧喷枪的原因所在。
在浮法玻璃熔窑上增设一对全氧喷枪后,不仅能达到增产增效、节能降耗、改善玻璃质量的目的,而且一定程度上还能延长玻璃窑炉的寿命。
具体来说,有以下优点:
(1)提高玻璃窑炉的拉引量5~15%;
(2)改善窑炉的热效率,节省燃料5~8%;
(3)改善玻璃质量,减少气泡和结石,提高成品率0.5~3%;
(4)增设一对全氧喷枪后,高压热气流对窑体的整体冲刷侵蚀相对减缓;而用于熔化配合料的有效热量显著增加,可能加剧窑体侵蚀的热量也就相应降低;同时配合料的快速熔化减少了配合料的飞料,从而为延长熔窑使用寿命提供了保证。
(5)减少粉尘、烟尘的排放达20%,蓄热室格子体堵塞的可能性也减小了;
(6)纯氧辅助燃烧系统与原有空气燃烧系统相互独立,操作灵活。
3、局部增氧富氧燃烧技术
局部增氧是富氧空气不足时的一种主要应用方式。
玻璃熔窑理想燃烧状态是:火焰上部为缺氧区,可保护碹顶;中部位普通燃烧区;下部为高温区,能有效将热量传给玻璃液。
本技术关键是在火焰下部通入富氧气体,火焰的下部(靠近配合料和玻璃液面)温度提高,从而改变了传统的火焰燃烧特性,使其形成梯度燃烧。
火焰下部温度的提高,可强化火焰对玻璃液的传热,有利于玻璃熔化,减少过剩的二次空气量,确保空气过剩系数达到理想数值而节约油耗。
局部增氧时火焰上部温度没有下部温度高,这不仅对大碹和胸墙的寿命有利,而且由于小炉、蓄热室格子体的热负荷降低,可减轻其烧蚀。
采用局部增氧富氧燃烧技术,可以提高燃料效率、降低燃料消耗、增加生产能力,改善玻璃质量、减少污染物(NOx、SOx、CO2和颗粒物)的排放、缩减燃烧废气的总量、提高受损熔窑运行的维护能力以及在整个窑龄期运行的可能性。
局部增氧富氧燃烧技术投入包括设备费、人工费、设备加工费及技术使用费等,实施局部增氧富氧燃烧技术可以取得约4%的节能效益,按保守节能率3.0%计算,对于500t/d浮法玻璃熔窑,每天油耗约90吨,日节油量为2.7吨,油价按3000元/吨计算,日节约0.81万元,静态回收期200天。
局部富氧燃烧技术还能提高玻璃质量,延长炉龄,减少烟尘NOx等的排放,改善环境,带来巨大的社会效益。
玻璃熔窑富氧燃烧技术前景广阔,经过合理改造,一般浮法生产线均可应用,特别对于
(2)500吨/日浮法玻璃富氧燃烧运行情况1)火焰明亮、碹顶温度下降
经过观察通入富氧气体后火焰下部明显变亮,与使用富氧前相比熔窑的碹项温度大约下降大于10~25℃。
2)玻璃熔化改善、熔化率提高
使用富氧燃烧技术以后,由于火焰特性的变化,玻璃的熔化明显改善,可在不增加油耗的基础上,适当提高玻璃产量,据测算,富氧燃烧时,熔窑熔化率可以提高5~8%;
3)熔窑总体节能评价
经过对单位产品能耗与历史数据的比较得出结论:浮法玻璃熔窑富氧燃烧技术总体节能大约在3~5%。
5、结论
采用全氧燃烧、纯氧助燃或富氧燃烧技术,不仅可以实现节能减排、显著提高玻璃质量,而且可以降低生产成本,是企业节能降耗、提高产品质量、取得良好经济效益的有效措施
最新文件仅供参考已改成word文本。
方便更改如有侵权请联系网站删除。