商用车车架孔位标准化设计
车身孔位设计经验 同济同捷标准 汽车设计技术
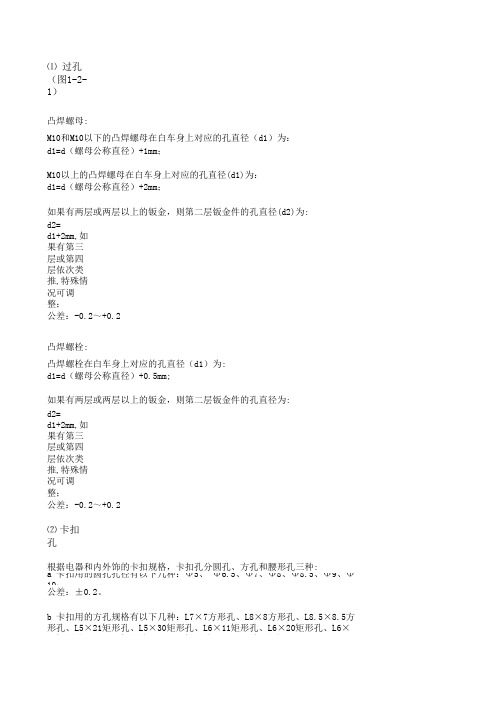
b 卡扣用的方孔规格有以下几种:L7×7方形孔、L8×8方形孔、L8.5×8.5方 形孔、L5×21矩形孔、L5×30矩形孔、L6×11矩形孔、L6×20矩形孔、L6× 21矩形孔、L8×13矩形孔、L8×25矩形孔、L10×12矩形孔; 公差:±0.2。
⑴ 过孔 (图1-21)
凸焊螺母:
M10和M10以下的凸焊螺母在白车身上对应的孔直径(d1)为: d1=d(螺母公称直径)+1mm;
M10以上的凸焊螺母在白车身上对应的孔直径(d1)为: d1=d(螺母公称直径)+2mm;
如果有两层或两层以上的钣金,则第二层钣 果有第三 层或第四 层依次类 推,特殊情 况可调 整; 公差:-0.2~+0.2
腰形孔:根据线束大小和护套尺寸,腰形孔孔径大小取φ7×10、φ7×12、 φ18×35、φ21×38、φ30×60、φ33×57、φ34×21、φ50×25、φ63× 82 ; 公差:±0.4。
⑹ 自攻 螺钉孔
在数模上用Φ5×3.5的圆锥面表示Φ4.2的孔。
⑺ 安装工艺孔、焊接过孔、减重孔、避让孔等,根据实际情况,考虑 强度、焊枪规格等,经过校核,确认其可行性。
c 卡扣用的腰形孔规格有以下几种:φ5×7、Φ5×8、φ6×8、φ6×11、φ 7×10、φ7×11、φ7×12、φ9×14; 公差:±0.2、±0.4,根据安装件的装配精度要求选择公差。
⑶ 焊装 定位孔
焊接定位孔借用其他孔时,孔径即为该孔孔径;当该孔仅为焊接定位用时, 根据孔的位置和结构,孔径选取φ6、φ8、φ10、φ12、φ16、φ20、φ26 、φ32、φ40的尺寸; 公差:0~+0.2
车身孔位设计经验

⑴ 过孔(图1-2-1)凸焊螺母:d2= d1+2mm,如果有第三层或第四层依次类推,特殊情况可调整;凸焊螺栓:d2= d1+2mm,如果有第三层或第四层依次类推,特殊情况可调整;⑵ 卡扣孔⑶ 焊装定位孔⑷ 涂装工艺孔d1=d(螺母公称直径)+0.5mm;如果有两层或两层以上的钣金,则第二层钣金件的孔直径为:根据电器和内外饰的卡扣规格,卡扣孔分圆孔、方孔和腰形孔三种:公差:-0.2~+0.2M10和M10以下的凸焊螺母在白车身上对应的孔直径(d1)为:d1=d(螺母公称直径)+1mm;M10以上的凸焊螺母在白车身上对应的孔直径(d1)为:如果有两层或两层以上的钣金,则第二层钣金件的孔直径(d2)为:d1=d(螺母公称直径)+2mm;凸焊螺栓在白车身上对应的孔直径(d1)为:公差:0~+0.2地板漏液孔取φ32、φ35、φ50三种规格的孔,根据车型尺寸选取;涂装夹持孔取φ30(0~+0.2),3.2㎜的翻边;其他部件的涂装工艺孔,根据实际状态确定。
公差:0~+0.2、±0.4,当涂装工艺孔用作焊接工艺孔时公差取0~+0.2,其他取±0.4 。
a 卡扣用的圆孔孔径有以下几种:Φ5、 Φ6.5、Φ7、Φ8、Φ8.5、Φ9、Φ10;公差:±0.2。
公差:±0.2。
公差:±0.2、±0.4,根据安装件的装配精度要求选择公差。
c 卡扣用的腰形孔规格有以下几种:φ5×7、Φ5×8、φ6×8、φ6×11、φ7×10、φ7×11、φ7×12、φ9×14;公差:-0.2~+0.2b 卡扣用的方孔规格有以下几种:L7×7方形孔、L8×8方形孔、L8.5×8.5方形孔、L5×21矩形孔、L5×30矩形孔、L6×11矩形孔、L6×20矩形孔、L6×21矩形孔、L8×13矩形孔、L8×25矩形孔、L10×12矩形孔;焊接定位孔借用其他孔时,孔径即为该孔孔径;当该孔仅为焊接定位用时,根据孔的位置和结构,孔径选取φ6、φ8、φ10、φ12、φ16、φ20、φ26、φ32、φ40的尺寸;⑸ 线束过孔⑹ 自攻螺钉孔根据线束形状和护套尺寸,线束过孔的形状分圆孔和腰形孔两种。
汽车设计-车身前副车架安装点设计规范模板
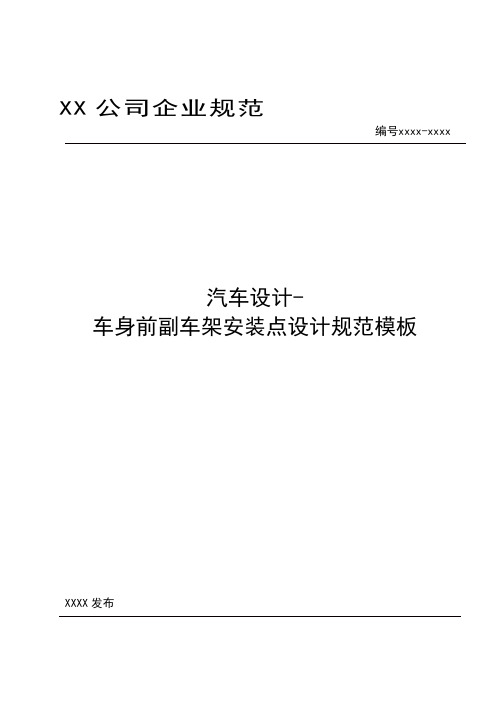
汽车设计-车身前副车架安装点设计规范模板XXXX发布1 范围本规范规定了车身前副车架安装点设计要点及其判断标准等。
本规范适用于新开发的M1类和N1类汽车车身前副车架安装点设计。
2 规范性引用文件下列文件对于本文件的应用是必不可少的,凡是注日期的引用文件,仅注日期的版本适用于本文件。
凡是不注日期的引用文件,其最新版本(包括所有的修改单)适用于本文件。
《GB 11566-2009 乘用车外部凸出物》《GB/T19234-2003 乘用车尺寸代码》《GB/T 709-2006 热轧钢板和钢带的尺寸、外形、重量及允许偏差》《GB/T 710-2008 优质碳素结构钢热轧薄钢板和钢带》《GB/T4780-2000 汽车车身术语》《整车车身设计公差与装配尺寸链分析》《螺栓连接的装配质量控制》3 术语和定义3.1 车身结构3.1.1车身结构是各个零件的安装载体。
3.2 副车架3.2.1副车架最早的应用原因是可以降低发动机舱传递到驾驶室的振动和噪音。
副车架与车身的连接点就如同发动机悬置一样。
通常一个副车架总成需要由四个悬置点与车身连接,这样既能保证其连接刚度,又能有很好的震动隔绝效果。
副车架能分5级减小震动的传入,对副车架来说,在性能上主要目的是减小路面震动的传入,以及提高悬挂系统的连接刚度,因此装有副车架的车驾驶起来会感觉底盘非常扎实,非常紧凑。
而副车架悬置软硬度的设定也面临着像悬挂调校一样的一个不可规避的矛盾。
所以工程师们在设计和匹配副车架时通常会针对车型的定位和用途选择合适刚度的橡胶衬垫。
由于来自发动机和悬挂的一部分震动会先到达副车架然后再传到车身,经过副车架的衰减后振动噪声会有明显改善。
副车架发展到今天,可以简化多车型的研发步骤。
这是因为悬挂、稳定杆、转向机等底盘零件都可以预先安装在一起,形成一个所谓的超级模块,然后再一起安装到车身上。
3.3前副车架安装点3.3.1前副车架安装点指安装在车身的安装孔中心线与安装面下平面交点的位置(XYZ 坐标)及装配孔公称尺寸。
大中型客车车架总成设计规范
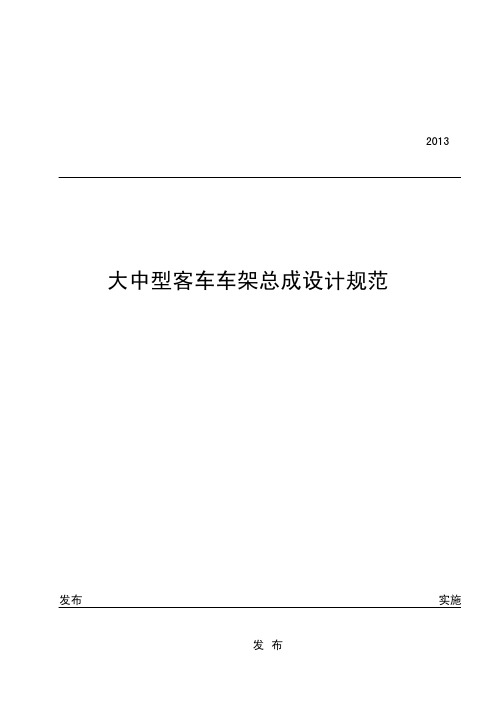
a) 纵向弯曲
b) 侧向弯曲
c) 纵向受力
d) 整体扭转
e) 纵向受力
图2 车架的受力和变形
由于车架所承受的动负荷无规律且不断变化,因此车架变形形式和状况是随机的。车架实际上是一 个承受空间力系的平面框架,而且车架纵梁与横梁的截面形状和连接接头又是各式各样的,更导致问题
3
的复杂化。车架的损坏主要是疲劳破坏,其主要形式是断裂,而疲劳裂纹则位于纵梁或横梁的边缘或应 力集中处。通过有限元计算法的应用,使车架的强度及结构设计更趋于合理。
a) 提高弯曲强度: 1) 选定较大的断面尺寸和合理的断面形状(槽形梁断面高宽比一般为 3:1); 2) 将上、下翼缘加厚或在其上贴加强板; 3) 将受拉力翼缘适当加宽。
b) 提高局部扭转强度: 1) 注意偏心载荷的布置,使相近的几个偏心载荷尽量接近纵梁断面的弯曲中心,并使合成量 较小; 2) 在偏心载荷较大处设置横梁,并根据载荷大小及分散情况确定连接强度和宽度; 3) 将悬置点布置在横梁的弯曲中心上; 4) 当偏心载荷较大且偏离横梁较远时,可采用 K 形梁,或将该段纵梁形成封闭断面; 5) 当偏心载荷较大且分散时,应采用封闭断面梁,横梁间距也应缩小; 6) 选用较大的断面; 7) 限制制造扭曲度,减小装配应力。
5
为了解决以上两个方案的不足,可以在槽形横梁的上下方各采用一个连接板,或仅在其下方采用一 个连接板。 6.4.2.2 鳄鱼式横梁
鳄鱼式横梁通常由帽形截面在其两端加接头构成,如图4所示:
a) 翼板连接
b)腹板连接
图4 鳄鱼式横梁
鳄鱼式横梁优点如下: a) 有较大的连接宽度,使主、副簧支架都可得到支撑; b) 截面高度较低,可以让开下部空间,使某些汽车的传动轴自由穿过; c) 可用矩形胚料直接压制; 鳄鱼式横梁的不足之处是:其弯曲刚度不如槽形横梁大,车架扭转时纵梁的应力偏大。因此,可将 将翼缘连接改为腹板连接。 鳄鱼式横梁也可由两个帽形截面组成封闭的箱形截面,其扭转刚度较大,弯曲刚度比其它两种大。
浅谈重卡车架纵梁制孔精度控制

就目前汽车市场竞争形式日趋严峻的现状,用户对汽车质量要求不断提高。
分析影响重卡车架纵梁孔位精度的各种因素,旨在减少车架纵梁孔位偏差,提高车架总成整体质量水平。
这对于提高车架纵梁的质量有着非常重要的现实意义。
近年来,随着我国经济的飞速发展,轻、重型汽车需求量也随之迅速攀升。
国内众多汽车制造商都积极采用新设备,不断革新现有加工方法,提升产品质量。
提高车架纵梁孔位精度是保证车架总成合格的前提,是制造一个完美汽车的重要因素。
为顺应汽车产业快速发展的趋势,车架纵梁质量的必要控制不容忽视。
图1 边梁式车架1-保险杠2-挂钩3-前横梁4-发动机前悬置横梁5-发动机后悬置左右支架和横梁6-纵梁7-驾驶室后悬置横梁8-第四横梁9-后钢板弹簧前支架横梁10-后钢板弹簧后支架横梁11-角撑横梁组件12-后横梁13-脱钩组件市场现状分析公司车架在结构上属于边梁式车架(图1),车架总成基本构造是由两根纵梁和数件横梁及相关零件(加强板和支撑板)组成。
如果纵梁孔位加工精度无法保证所需尺寸公差则会直接影响其车架质量。
影响的方面有:车架宽度难以保证;车架长度无法统一;车架尾端纵梁不平齐;零部件装配位置偏移;甚至可能导致部分零部件无法装配以及给使用性能带来诸多不良的影响。
所以控制纵梁孔位精度至关重要。
图2 STPK120-12开式纵梁平板数控冲加工工艺流程由于设备的更新使用,公司的纵梁总成加工工序存在以下两种工艺流程:流程1:开平纵剪→平板制孔(数控冲+摇臂钻)→切割外形(数控等离子切割机)→压制成形(汽车纵梁液压机)→合梁→透孔。
流程2:开平纵剪→纵梁冷弯成形→U形梁冲孔(纵梁三面冲)→切割外形(数控等离子切割机)→合梁→透孔(摇臂钻)。
影响因素分析与质量控制纵梁冲孔(数控冲STPK120-12)对车架纵梁孔位精度的影响STPK120-12开式纵梁平板数控冲(图2),工作时由自动上料电磁吸盘将板料从移动料台上移到上料辊上。
首先选定的作为定位基准的任意两把夹钳伸出,再由推料装置的气缸运动,推动板料向钳口运动并定位,其余夹钳再伸出全部夹持板料,完成板料的定位动作。
样车关键孔位改制工艺规范
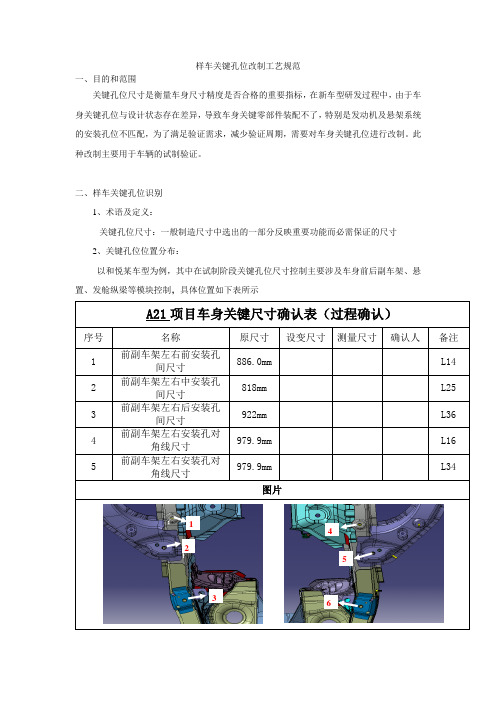
样车关键孔位改制工艺规范一、目的和范围关键孔位尺寸是衡量车身尺寸精度是否合格的重要指标,在新车型研发过程中,由于车身关键孔位与设计状态存在差异,导致车身关键零部件装配不了,特别是发动机及悬架系统的安装孔位不匹配,为了满足验证需求,减少验证周期,需要对车身关键孔位进行改制。
此种改制主要用于车辆的试制验证。
二、样车关键孔位识别1、术语及定义:关键孔位尺寸:一般制造尺寸中选出的一部分反映重要功能而必需保证的尺寸2、关键孔位位置分布:以和悦某车型为例,其中在试制阶段关键孔位尺寸控制主要涉及车身前后副车架、悬置、发舱纵梁等模块控制,具体位置如下表所示A21项目车身关键尺寸确认表(过程确认)序号名称原尺寸设变尺寸测量尺寸确认人备注1 前副车架左右前安装孔间尺寸886.0mm L142 前副车架左右中安装孔间尺寸818mm L253 前副车架左右后安装孔间尺寸922mm L364 前副车架左右安装孔对角线尺寸979.9mm L165 前副车架左右安装孔对角线尺寸979.9mm L34图片123654序号 名称原尺寸 设变尺寸 测量尺寸 确认人备注 1 发动机右悬置安装孔尺寸135.5mm L12 2 发动机左右悬置安装孔尺寸973.1mmL14 3 发动机左右悬置安装孔尺寸970.9mm L25 4 发动机左右悬置安装孔尺寸1094.4m mL36 5 发动机悬置安装孔对角线尺寸967.0mm L15 6发动机悬置安装孔对角线尺寸997.8mmL24图片序号 名称原尺寸 设变尺寸 测量尺寸 确认人备注 1 前挡风玻璃上框尺寸1143.0mm L13 2 前挡风玻璃下框尺寸1374.3mm L24 3 前挡风玻璃对角线尺寸1454.9mm L14 4前挡风玻璃对角线尺寸1454.9mmL23图片321654序号名称原尺寸设变尺寸测量尺寸确认人备注1 左右侧围开张尺寸943.9mmL132 左右侧围开张尺寸1319.2mmL243 左右侧围对角开张尺寸1249.5mmL144 左右侧围对角开张尺寸1249.5mmL23 图片序号名称原尺寸设变尺寸测量尺寸确认人备注1 左拉力杆安装孔尺寸86.6mm L122 右拉力杆安装孔尺寸86.6mm L343 左右拉力杆距离尺寸1278.2mmL2343121432序号 名称原尺寸 设变尺寸 测量尺寸 确认人 备注 1 机舱左右前纵梁开张尺寸1028.9mmL12 2 后地板左右纵梁开张尺寸1055mmL34三、样车关键孔位改制规范21434321。
商用车车架孔位标准化设计
商用车车架孔位标准化设计摘要车架孔位的标准化设计是商用车制造和维护的基础,它有助于降低制造和维护成本,提高车辆的安全性和可靠性。
本文详细介绍了商用车车架孔位的标准化设计,包括孔位的位置、大小、形状和数量等方面的标准要求,并分析了其优缺点及应用范围。
通过应用标准化设计的方法,商用车制造企业可以有效提高生产效率和降低生产成本,为广大用户提供更加安全可靠的商用车产品。
关键词:商用车,车架孔位,标准化设计,位置,大小,形状,数量正文一、引言车架孔位是商用车制造和维护中非常重要的部件,它用于连接车身和车架上的各种零部件,如底盘、悬挂、制动和转向系统等。
车架孔位的标准化设计可以确保这些零部件的位置、大小、形状和数量等方面的一致性,从而提高车辆的安全性和可靠性,降低制造和维护成本。
二、标准要求1. 孔位位置:车架孔位的位置应符合国家标准和行业规范要求,以确保零部件的安装位置和移动范围的一致性。
孔位位置应该在车架的结构强度区域内,并且不应与其他孔位产生干扰。
2. 孔位大小:孔位的大小应该根据其作用和所需的零部件尺寸来确定,以确保安装部件的适配性和紧密度。
同时,孔位的大小应与所使用的螺栓或销的尺寸相匹配。
3. 孔位形状:孔位的形状应该简单、规则,便于制造、加工和安装。
常见的孔位形状有圆形、方形、椭圆形和CA型等,不同形状的孔位适用于不同的零部件。
4. 孔位数量:孔位的数量应该根据所需安装的零部件数量和布局来确定。
同时,孔位的数量也应考虑到车架结构的强度和刚度等因素。
三、优缺点分析1. 优点:车架孔位的标准化设计可以确保不同型号和不同批次的商用车结构一致性,降低了生产和维护成本;同时,标准化孔位设计也提高了车架的刚度和稳定性,增加了车辆的安全性和可靠性。
2. 缺点:标准化车架孔位设计可能会存在一定的限制,例如在特殊应用场景下需要添加新的孔位,这会增加设计和制造的难度和成本。
四、应用范围商用车车架孔位的标准化设计适用于各种类型的商用车,包括卡车、客车、货车、挂车等。
车架纵梁冲孔模设计
( 续) 挥发性 40℃ 黏度 / CST 100℃ 黏度 / CST 黏度指数 流动点 / ℃ 少 2. 283 1. 007 114 - 22. 5 + 30 无色、透明 无
碳氢化合物 100 第 4 类第 3 类石油 0. 762 9 少 1. 883 0. 907 138 - 10 + 30 无色、透明 无
( a) ( b)
图 2 快换凸模结构
这样也迎合了前面所谈到的必须采取有效措施降低 冲裁力的需求。 工作中通过专用套筒工具可以容易 地更换凸模,大大方便了维修和车型互换。 ( 3 ) 冲孔间隙值的确定 本冲孔模要同时冲内 梁和外梁,内梁板厚 5mm, 外梁板厚 8mm, 同时满 足这两种料厚的间隙要求是一个难题。 对于这种厚 板模具来说,冲孔间隙一般取料厚的 8% ~ 10% , 这 套模具的冲孔间隙应在 0. 5 ~ 0. 8mm 之间。 对冲孔模来说, 如间隙过大, 所冲压工件的毛 刺就比较大, 冲压质量差。 如果间隙偏小, 虽然冲 孔的质量较好, 但模具的磨损比较严重, 大大降低 模具的使用寿命, 而且容易造成冲头的折断。 为此 我们初设此套模具的间隙为 0. 63mm, 并进行 了 试 验,发现冲料厚 5mm 的内梁毛刺有点偏大, 产品质 量不好,而冲 8mm 厚的外梁得到的工件质量还可以。 最终设定此套模具的冲孔间隙为 0. 6mm。结果证实, 冲出来的产品能满足质量要求。 ( 4 ) 压力中心的确定 本纵梁冲孔模所对应的 产品是三种不同车型内梁、 外梁。 这 6 种产品冲孔 内容不完全一样, 压边中心的选择需综合考虑这 6 种产品的情况。 设计时先分别求出 6 种产品的压力 中心,发现它们的压边中心距离并不大, 折衷处理 取其中间值作为本模具的压边中心。
汽车设计-车身前副车架安装点设计规范模板
汽车设计-车身前副车架安装点设计规范模板XXXX发布1 范围本规范规定了车身前副车架安装点设计要点及其判断标准等。
本规范适用于新开发的M1类和N1类汽车车身前副车架安装点设计。
2 规范性引用文件下列文件对于本文件的应用是必不可少的,凡是注日期的引用文件,仅注日期的版本适用于本文件。
凡是不注日期的引用文件,其最新版本(包括所有的修改单)适用于本文件。
《GB 11566-2009 乘用车外部凸出物》《GB/T19234-2003 乘用车尺寸代码》《GB/T 709-2006 热轧钢板和钢带的尺寸、外形、重量及允许偏差》《GB/T 710-2008 优质碳素结构钢热轧薄钢板和钢带》《GB/T4780-2000 汽车车身术语》《整车车身设计公差与装配尺寸链分析》《螺栓连接的装配质量控制》3 术语和定义3.1 车身结构3.1.1车身结构是各个零件的安装载体。
3.2 副车架3.2.1副车架最早的应用原因是可以降低发动机舱传递到驾驶室的振动和噪音。
副车架与车身的连接点就如同发动机悬置一样。
通常一个副车架总成需要由四个悬置点与车身连接,这样既能保证其连接刚度,又能有很好的震动隔绝效果。
副车架能分5级减小震动的传入,对副车架来说,在性能上主要目的是减小路面震动的传入,以及提高悬挂系统的连接刚度,因此装有副车架的车驾驶起来会感觉底盘非常扎实,非常紧凑。
而副车架悬置软硬度的设定也面临着像悬挂调校一样的一个不可规避的矛盾。
所以工程师们在设计和匹配副车架时通常会针对车型的定位和用途选择合适刚度的橡胶衬垫。
由于来自发动机和悬挂的一部分震动会先到达副车架然后再传到车身,经过副车架的衰减后振动噪声会有明显改善。
副车架发展到今天,可以简化多车型的研发步骤。
这是因为悬挂、稳定杆、转向机等底盘零件都可以预先安装在一起,形成一个所谓的超级模块,然后再一起安装到车身上。
3.3前副车架安装点3.3.1前副车架安装点指安装在车身的安装孔中心线与安装面下平面交点的位置(XYZ 坐标)及装配孔公称尺寸。
商用车车架打孔规程
各分组别(系统)需在车架纵梁(横梁)打孔操作规程一.新设计车型正式资料的纵梁(横梁)打孔工作:
三.变形车临时指令的纵梁(横梁)打孔工作:
四.说明:
1.新设计车型车架纵梁底盘室车架设计人员只负责车架横梁安装孔位,各分组别(系统)需用孔由各分组别(系统)
人员自行确定后,按第一条内容执行。
2.由于现在纵梁协作生产,为降低协作件价格,变形车各分系统(组别)设计时原则上尽可能借用纵梁上原有孔,减
少纵梁上打孔数量。
3.纵梁补打孔要求:
a)在车架的上下弦上(在车架尾端时除外)、在车架大梁外形有变化的区域(如拐点处)、在载荷引入点(如:直
接在钢板弹簧支架处)不能打孔;
b)需在车架大梁的腹板中钻孔,则孔中心与腹板上边或下边的距离:最小应为车架高度的20%;孔中心距最小应
为50mm;孔的最大直径:17mm
编制:段智方
审查:张长江
批准:厐建中
二零零七年十一月二十六日。
- 1、下载文档前请自行甄别文档内容的完整性,平台不提供额外的编辑、内容补充、找答案等附加服务。
- 2、"仅部分预览"的文档,不可在线预览部分如存在完整性等问题,可反馈申请退款(可完整预览的文档不适用该条件!)。
- 3、如文档侵犯您的权益,请联系客服反馈,我们会尽快为您处理(人工客服工作时间:9:00-18:30)。
商用车车架孔位标准化设计
摘要
商用车车架孔位标准化设计是一种有效的方法,能够提高车辆的可靠性和安全性,降低制造成本和维护费用。
本文介绍了商用车车架孔位标准化设计的价值和意义,研究了车架孔位的类型和规格,以及如何实现标准化设计。
本文还探索了标准化设计的优势和挑战,并提出了解决这些挑战的建议。
最后,本文总结了商用车车架孔位标准化设计的重要性和未来发展方向。
关键词:商用车,车架孔位,标准化设计,可靠性,安全性,制造成本,维护费用
正文
1.引言
商用车是现代物流和交通运输领域中最重要的一类车辆,其安全性和可靠性对于保证企业正常运营至关重要。
车架孔位是商用车中重要的组成部分,通常用于安装车身和其他部件。
标准化设计可以为商用车车架孔位的制造和维护带来很多便利和经济效益,本文就商用车车架孔位标准化设计这一话题进行了研究与探讨。
2.商用车车架孔位的类型和规格
商用车车架孔位通常可以分为平板孔、带螺纹孔和精细型孔三
种类型,其规格常常是根据车辆的尺寸和载重等要求进行设计和制造。
例如,世界上许多国家的商用车都有统一的尺寸和规格标准,以保证它们的互换性和标准化。
3.实现标准化设计的方法和途径
实现商用车车架孔位的标准化设计可以采取多种方法和途径。
一些国际标准和惯例可以作为参考,以便车架孔位的设计符合国内外通用的标准和规范。
同时,利用先进的车辆设计软件,可以更易于实现标准化设计,提高车架孔位的精度和生产效率。
4.标准化设计的优势和挑战
商用车车架孔位标准化设计的优势在于:提高车辆的可靠性和安全性、降低制造成本和维护费用,提高生产效率和质量,提高客户满意度。
然而,标准化设计的挑战也很明显,如制定标准化标准、确定统一的测量方法和工具、提高生产和工艺的一致性等等。
5.解决挑战的建议
要克服标准化设计的挑战,需要采取一些措施和方法。
一方面,需要开发和制定适合商用车车架孔位的标准化标准,并制定完整的测试和验证程序。
另一方面,技术人员需要接受足够的培训和技术支持,以提高生产和工艺的一致性和质量。
6.总结
本文认为商用车车架孔位标准化设计是提高车辆的可靠性和安全性、降低制造成本和维护费用,提高生产效率和质量,提高客户满意度的重要方法之一。
未来,还需要更进一步的标准化工作和技术改进,以逐步推进商用车车架孔位标准化设计的深入发展。
7. 商用车车架孔位标准化设计的未来发展方向
随着商用车市场的日益发展和技术的不断创新,商用车车架孔位标准化设计也在不断发展和完善。
下面是商用车车架孔位标准化设计的未来发展方向:
(1)数字化设计和制造技术的应用
随着数字化技术的发展,越来越多的商用车辆将采用数字化设计和制造技术。
数字化技术可以提高生产效率和精度,减少制造成本,同时可以更好地满足客户需求。
(2)标准化标准的深化和升级
商用车车架孔位标准化设计需要更加深入和完善的标准体系。
尤其是在一些技术和工艺方面,如精确测量和检测、精密加工和装配等,需要制定更加严格和统一的标准和规范。
(3)全球化与区域化的创新和应用
商用车市场正朝着全球化和区域化方向发展。
对于商用车车架孔位标准化设计的需要也越来越明显。
同时,各个区域的商用车市场和相应标准也可能存在差异,需要考虑区域化特点,制定更加适合当地市场的标准。
(4)环保和安全方面的要求不断提高
环保和安全方面的要求对商用车车架孔位标准化设计也越来越高。
这需要制定更加严密和完善的标准和规范,以确保商用车在生产和使用中不会对环境造成污染,并且具有更高的安全性和可靠性。
8. 结论
商用车车架孔位标准化设计已经成为车辆制造和维护过程中不可或缺的一部分。
标准化设计可以带来很多优势,如提高可靠性和安全性、降低制造成本和维护费用、提高生产效率和质量,以及提高客户满意度。
未来,随着技术的不断进步和市场的发展,商用车车架孔位标准化设计也将不断深入发展和创新,以更好地满足市场需求。
商用车车架孔位标准化设计的重要性越来越被人们所认识和重视。
这也为商用车辆的制造和维护提供了更现代化和高效化的解决方案。
标准化设计的理念不仅可以提高车辆生产效率和减少成本,同时还能够满足客户需要,提高车辆品质。
标准化设计可以分为两个主要方面。
首先是设计阶段的标准化,车架孔位的设计需要符合某些易用、安全、生产效率等标准,避免设计上过度复杂或不规范。
其次是生产制造阶段的标准化,车架孔位的加工、检测、以及组装需要规范化,来提高生产效率和准确性。
同时,标准化还可以使组件标准化,减少制造和维护的成本和时间。
随着商用车辆市场的不断扩大和技术的不断创新,商用车车架孔位标准化设计也在不断演进和发展。
在当前市场和技术环境下,商用车车架孔位标准化设计需要遵循以下几个方面:
首先,标准化设计需要考虑多方面因素。
车架孔位设计必须同时考虑到可靠性、安全性、生产效率、易用性等多种因素,并将它们结合在一起,以满足市场需求。
设计标准需要精确并且完整,以确保车辆能够在生产和使用中安全可靠。
其次,标准化设计需要求新。
同时,标准化设计也需要与数字化技术结合,符合时代的趋势。
在设计阶段,可以使用计算机辅助设计(CAD)和计算机辅助制造(CAM)技术来提高生
产效率和精度,并且可以大量减少错误几率。
此外,标准化设计需要遵循可持续性原则,减少对环境的污染,降低能源消耗。
在设计过程中,应该注意降低材料的使用量和浪费,同时考虑可回收和可再利用的材料。
总之,商用车车架孔位标准化设计是一个由许多不同的需求和考虑所影响的中心部分。
只有如此多方面因素的综合考虑,设计才能更贴合市场需求,以及能满足行业的未来发展趋势。
将标准化设计作为一个系统性的过程,并严格贯彻其中的要求,商用车制造可以实现更加高效、精准和经济的车辆生产和维护。
商用车车架孔位标准化设计是现代化和高效化的解决方案,逐渐被人们认识和重视。
标准化设计不仅可以提高车辆生产效率和减少成本,同时还能够满足客户需要,提高车辆品质。
标准
化设计可以分为设计阶段的标准化和生产制造阶段的标准化,两者都必须规范化。
随着商用车辆市场的不断发展,商用车车架孔位标准化设计必须考虑多方面的因素,如可靠性、安全性、生产效率、易用性等,并结合数字化技术,符合时代趋势。
同时,还要遵循可持续性原则,降低能源消耗,减少对环境的污染,考虑材料的使用量和回收利用。
只有综合考虑这些因素,才能满足市场需求,促进商用车制造业的高效、精准和经济发展。