商用车车架工艺技术与材料开发
浅谈商用车总装配工艺技术现状及发展趋势
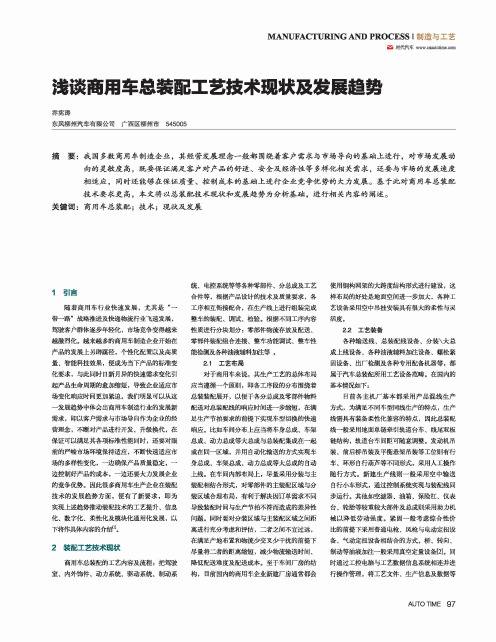
MANUFACTURING AND PROCESS I_造与工艺D时代汽车 浅谈商用车总装配工艺技术现状及发展趋势乔宪涛东风柳州汽车有限公司广西区柳州市545005摘要:我国多数商用车制造企业,其经营发展理念一般都围绕着客户需求与市场导向的基础上进行,对市场发展动向的灵敏度高,既要保证满足客户对产品的舒适、安全及经济性等多样化相关需求,还要与市场的发展速度相适应,同时还能够在保证质量、控制成本的基础上进行企业竞争优势的大力发展。
基于此对商用车总装配技术要求更高,本文将以总装配技术现状和发展趋势为分析基础,进行相关内容的阐述。
关键词:商用车总装配;技术;现状及发展1引言随着商用车行业快速发展,尤其是“一带一路”战略推进及快递物流行业飞速发展,驾驶客户群体逐步年轻化,市场竞争变得越来越激烈化。
越来越多的商用车制造企业开始在产品的发展上另辟蹊径,个性化配置以及高质量、智能科技效果,便成为当下产品的标准变化要求,与此同时日新月异的快速需求变化引起产品生命周期的愈加缩短,导致企业适应市场变化响应时间更加紧迫。
我们明显可以从这一发展趋势中体会出商用车制造行业的发展新需求,即以客户需求与市场导向作为企业的经营理念,不断对产品进行开发、升级换代,在保证可以满足其各项标准性能同时,还要对眼前的严峻市场环境保持适应,不断快速适应市场的多样性变化,一边确保产品质量稳定,一边控制好产品的成本,一边还要大力发展企业的竞争优势。
因此很多商用车生产企业在装配技术的发展趋势方面,便有了新要求,即为实现上述趋势推动装配技术的工艺提升、信息化、数字化、柔性化及模块化通用化发展,以下将作具体内容的介绍%2装配工艺技术现状商用车总装配的工艺内容及流程:把驾驶室、内外饰件、动力系统、驱动系统、制动系统、电控系统等等各种零部件、分总成及工艺合件等,根据产品设计的技术及质量要求,各工序相互衔接配合,在生产线上进行组装完成整车的装配、调试、检验。
浅述汽车车架焊接工艺技术 谢禹 鄢鹤鹏
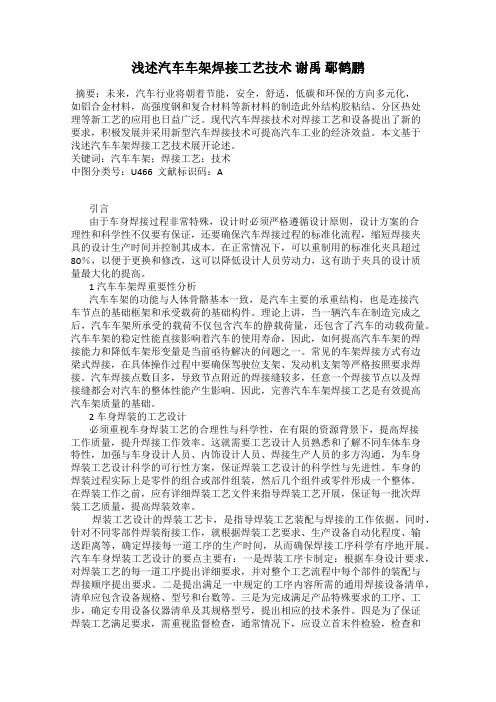
浅述汽车车架焊接工艺技术谢禹鄢鹤鹏摘要:未来,汽车行业将朝着节能,安全,舒适,低碳和环保的方向多元化,如铝合金材料,高强度钢和复合材料等新材料的制造此外结构胶粘结、分区热处理等新工艺的应用也日益广泛。
现代汽车焊接技术对焊接工艺和设备提出了新的要求,积极发展并采用新型汽车焊接技术可提高汽车工业的经济效益。
本文基于浅述汽车车架焊接工艺技术展开论述。
关键词:汽车车架;焊接工艺;技术中图分类号:U466 文献标识码:A引言由于车身焊接过程非常特殊,设计时必须严格遵循设计原则,设计方案的合理性和科学性不仅要有保证,还要确保汽车焊接过程的标准化流程,缩短焊接夹具的设计生产时间并控制其成本。
在正常情况下,可以重制用的标准化夹具超过80%,以便于更换和修改,这可以降低设计人员劳动力,这有助于夹具的设计质量最大化的提高。
1汽车车架焊重要性分析汽车车架的功能与人体骨骼基本一致,是汽车主要的承重结构,也是连接汽车节点的基础框架和承受载荷的基础构件。
理论上讲,当一辆汽车在制造完成之后,汽车车架所承受的载荷不仅包含汽车的静载荷量,还包含了汽车的动载荷量。
汽车车架的稳定性能直接影响着汽车的使用寿命,因此,如何提高汽车车架的焊接能力和降低车架形变量是当前亟待解决的问题之一。
常见的车架焊接方式有边梁式焊接,在具体操作过程中要确保驾驶位支架、发动机支架等严格按照要求焊接。
汽车焊接点数目多,导致节点附近的焊接缝较多,任意一个焊接节点以及焊接缝都会对汽车的整体性能产生影响。
因此,完善汽车车架焊接工艺是有效提高汽车架质量的基础。
2车身焊装的工艺设计必须重视车身焊装工艺的合理性与科学性,在有限的资源背景下,提高焊接工作质量,提升焊接工作效率。
这就需要工艺设计人员熟悉和了解不同车体车身特性,加强与车身设计人员、内饰设计人员、焊接生产人员的多方沟通,为车身焊装工艺设计科学的可行性方案,保证焊装工艺设计的科学性与先进性。
车身的焊装过程实际上是零件的组合或部件组装,然后几个组件或零件形成一个整体。
汽车车架焊接工艺分析及工装设计
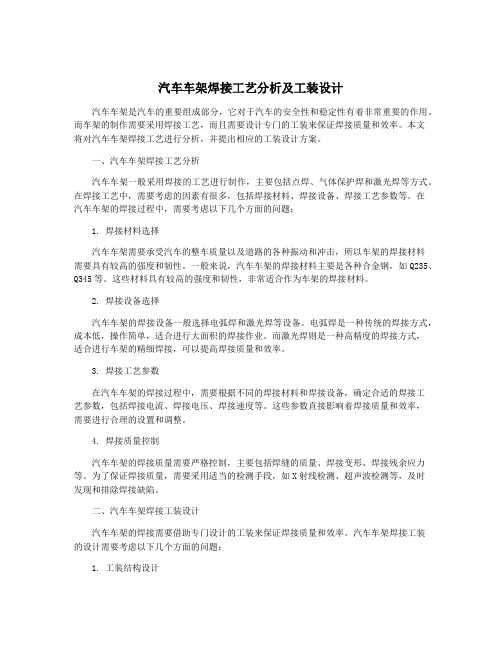
汽车车架焊接工艺分析及工装设计汽车车架是汽车的重要组成部分,它对于汽车的安全性和稳定性有着非常重要的作用。
而车架的制作需要采用焊接工艺,而且需要设计专门的工装来保证焊接质量和效率。
本文将对汽车车架焊接工艺进行分析,并提出相应的工装设计方案。
一、汽车车架焊接工艺分析汽车车架一般采用焊接的工艺进行制作,主要包括点焊、气体保护焊和激光焊等方式。
在焊接工艺中,需要考虑的因素有很多,包括焊接材料、焊接设备、焊接工艺参数等。
在汽车车架的焊接过程中,需要考虑以下几个方面的问题:1. 焊接材料选择汽车车架需要承受汽车的整车质量以及道路的各种振动和冲击,所以车架的焊接材料需要具有较高的强度和韧性。
一般来说,汽车车架的焊接材料主要是各种合金钢,如Q235、Q345等。
这些材料具有较高的强度和韧性,非常适合作为车架的焊接材料。
2. 焊接设备选择汽车车架的焊接设备一般选择电弧焊和激光焊等设备。
电弧焊是一种传统的焊接方式,成本低,操作简单,适合进行大面积的焊接作业。
而激光焊则是一种高精度的焊接方式,适合进行车架的精细焊接,可以提高焊接质量和效率。
3. 焊接工艺参数在汽车车架的焊接过程中,需要根据不同的焊接材料和焊接设备,确定合适的焊接工艺参数,包括焊接电流、焊接电压、焊接速度等。
这些参数直接影响着焊接质量和效率,需要进行合理的设置和调整。
4. 焊接质量控制汽车车架的焊接质量需要严格控制,主要包括焊缝的质量、焊接变形、焊接残余应力等。
为了保证焊接质量,需要采用适当的检测手段,如X射线检测、超声波检测等,及时发现和排除焊接缺陷。
二、汽车车架焊接工装设计汽车车架的焊接需要借助专门设计的工装来保证焊接质量和效率。
汽车车架焊接工装的设计需要考虑以下几个方面的问题:1. 工装结构设计汽车车架焊接工装的设计需要充分考虑车架的形状和结构,采用合适的夹具和模具来固定和支撑车架,在焊接过程中保证车架的稳定性和一致性。
工装的结构设计还需要考虑操作方便、维修方便等因素。
钢铝结合商用车车架轻量化技术综述

钢铝结合商用车车架轻量化技术综述李舜酩; 张凯成; 丁瑞; 孙明杰【期刊名称】《《重庆理工大学学报(自然科学版)》》【年(卷),期】2019(033)010【总页数】8页(P1-8)【关键词】轻量化; 钢铝结合车架; 结构优化设计; 连接工艺【作者】李舜酩; 张凯成; 丁瑞; 孙明杰【作者单位】南京航空航天大学能源与动力学院南京210016【正文语种】中文【中图分类】U463.32目前,商用车保有量占汽车总量的10%左右,但总体燃料消耗量占汽车燃料总消耗量的55%~60%,百公里排放量约为乘用车排放量的3~4倍[1]。
而轻量化技术作为提高汽车燃油经济性和减少尾气排放的有效手段,对商用车来说,在减轻了自身质量的同时,还提高了载质量利用系数[2]。
一般重型商用车整备质量为8~18 t,车架质量为500~1 200 kg,车架占商用车整备质量的5%~10%[3],因此车架轻量化对整车轻量化的贡献非常可观。
车架承受着整车的簧载质量,同时还要受到来自不平度路面、行驶速度和方向改变而产生的外部激励,以及动力传动系统等产生的内部激励,所以车架要求足够的刚度、强度和可靠性。
目前车架轻量化主要依靠3个方面进行[4]:① 结构优化设计,包括尺寸优化、形貌优化和拓扑优化等,并结合多学科手段使得优化结果满足所有学科的要求,目前车架优化考虑的性能主要有刚度、强度和模态,而大多数研究在优化过程中未将疲劳考虑在内;② 轻量化材料的应用,包括高强度钢和铝合金等,目前钢铝结合和全铝在车身上的应用较为常见,而在车架上的使用相对较少;③ 先进制造工艺,包括热冲压成形和激光焊等。
生产超高强度钢和超强度铝需要更高要求的制造工艺,而且保证钢铝材料能够在车上正常使用,需要设计相应的钢铝异种材料的连接工艺。
因此,基于传统的车架钢制结构,采用铝合金材料制作部分零件,根据性能模拟、优化设计等方式,综合考虑刚度、强度、模态和疲劳性能,对铝替代钢的零件加以确定,并配合相应的连接工艺是今后实现商用车架轻量化的一个重要方向。
“U”形横梁生产工艺及其发展

针对如何实现“U”形横梁多品种、小批量、快速低成本生产的课题,本文通过横梁结构特征的分析和横梁生产工艺的发展现状与对比,提出了应用数控柔性化生产工艺解决课题的方案,并总结了三种横梁生产工艺的特点和优劣,及其所适合的生产模式。
最后,提出了要从研发开始进行横梁标准化,以从根本上解决本课题的建设性意见。
引言横梁是卡车车架重要的组成零部件,车架就是通过若干根横梁用铆接法或焊接法将两根纵梁连接成坚固的刚性构架。
横梁不仅用来连接左右纵梁保证车架的扭转刚度和承受纵向载荷,而且还可以支撑安装在汽车底盘上的其他零部件,如:传动轴吊架、贮气筒、各类管阀等等。
根据截面形状,横梁主要有“U”形、“Z”形、“工”字形、箱形等几种结构形式。
其中“U”形横梁不仅能满足车架的扭转刚度和强度的要求,而且生产工艺相比其他几种形式的横梁要更加简单,同时与纵梁等其他零部件的装配紧固,比其他几种形式的横梁更为方便,因此车架横梁通常采用“U”形结构(图1)。
“U”形横梁虽然结构简单,但由于其在车架不同位置以及装配不同零部件的需要,其开口、孔位以及外形尺寸均不同,同时这些尺寸随着车形的变化而变化,车形越多横梁的品种也越多。
随着卡车市场竞争日趋激烈,卡车行业正逐步形成个性化细分设计、快速小批量生产模式,以满足客需求。
因此,如何实现横梁多品种、小批量、快速低成本生产,是横梁生产工艺要解决的课题。
“U”形横梁的结构特征及其技术要求“U”形横梁通常设计成直线形,材料根据其功能主要选用料厚3~8mm,抗拉强度370~700MPa的低合金高强度热轧中厚钢板。
其结构分为腹面和上、下翼面。
腹面上设计布置有不同孔径的孔,大孔主要为减重孔和各类管线的通过孔,小孔为装配各类管阀等零部件的装配组孔。
上、下翼面上设计布置与纵梁连接的装配组孔以及在横梁本体上装配传动轴吊架、各类管阀等组孔,为了避让底盘装配空间和减重的需要,部分横梁的上、下翼面设计有弧形缺口。
为了便于底盘各类管、线的通过,横梁的两端通常设计半圆形或矩形缺口,如图1所示。
浅析重型商用车车架轻量化技术的发展及应用

浅析重型商用车车架轻量化技术的发展及应用东风柳州汽车有限公司 姓名:周友明 学号:P12020121 0 引言随着经济的快速发展,环境污染和能源短缺问题越来越明显,而汽车数量的增加更使这些问题日益严重。
因而,轻型、节能、环保、安全、舒适、低成本成为各汽车制造厂家追求的目标。
2009年备受世界瞩目的哥本哈根会议在全球掀起一股热烈的“哥本哈根”环保风,“低碳经济”已成为社会各界最为关注的热门词汇[1]。
近年来,得益于国家政策的扶持和国内市场的旺盛需求,我国汽车工业发展极为迅速,同时汽车也消耗了大量的不可再生能源,使一些地区出现了大面积的汽油、柴油和天然气等能源相对不足的现象,对人们的日常生活和农工业生产带来了很大的影响,对经济的发展产生了直接限制作用,所以节能减排已成为汽车工业界目前有待解决的重大问题,尤其是节能和环保更是关系到人类的可持续发展。
因此,推进汽车的节能环保显得尤为重要。
1 商用车车架轻量化的意义目前,我国商用车保有量占全部汽车保有量的23%左右,而燃油消耗占到整个汽车用油量的70%[2],其中重型商用车的耗油量又占全部商用车耗油量的70%以上。
因此,汽车节能降耗重点就是要抓重型商用车的节能降耗。
轻量化技术是提高汽车燃油经济性、减少尾气排放、节约材料消耗的有效手段。
根据国外的研究数据表明,汽车整车质量每降低100公斤,百公里油耗可降低0.3~0.6升;汽车整车质量每减重10%,油耗可降低5%~8%[3]。
国内通过试验对比分析,某典型重型商用车减轻自重的10%,可以降低油耗4.75%[4]。
另外,轻量化对环保也很有好处,车辆每减轻100公斤,CO排放量可减少约5g/km[5]。
同时,轻量化可2减少原材料消耗,降低零件成本,增加企业的收益。
因此,轻量化对于消费者、企业以及社会环境都是有益的。
对载货汽车来说,轻量化不但减轻了自身质量还提高了载质量利用系数(汽车最大承载质量与汽车整备质量之比),这是一个综合衡量轻量化的系数,也是国内外商用车设计的基本准则。
关于重型商用汽车的车架轻量化设计研究
关于重型商用汽车的车架轻量化设计研究随着物流的快速发展,载货车的载重量的标准越来越高。
而車架在汽车中的主要作用是承载货物与构件,其承受载荷来源于车的内外装置,包括连接汽车工具及车用设备。
车架的结构决定于汽车的总体布置,对车架轻量化的承载特性研究,实际上是车架结构的改进与优化,进而保证汽车的整体性能。
轻量化的设计研究,能够在一定程度上减小汽车的耗油量与废弃的排放,并在保持汽车整体性能与造价不变的条件下,降低汽车自身重量提升动力性能与可靠安全性能。
因此,轻量化对汽车运输业的发展具有重要意义。
标签:重型商用汽车;车架;轻量化;设计技术0 前言车架的轻量化实际上是从动静力学特征进行分析,结合载荷及位移边界条件,考察车架的受力分布,实现对车架架构的优化,最终使车架达到结构合理轻便,又强度可靠的效果。
本文关于重型商用汽车的车架轻量化设计研究,将以重型商用汽车为研究对象,从重型商用汽车的车架结构特点入手,分析车架进行轻量化的重要意义,进而对轻量化的设计方法与设计难点进行具体研究,通过评价车架设计的合理性,确定结构改进的可行方案。
并基于商用车车架量化的发展趋势作出展望。
希望能够为我国的物流业及汽车运输的发展提供一份参考。
1 重型商用汽车的车架轻量化意义轻量化技术可以对汽车的尾气排放与燃油量构成直接的影响,是节约材料的有效手段之一。
目前,我国重型商用车在全部车辆中的比例为23%左右,但是重型商用车在燃油消耗上占比却高达70%。
国外的有关调查数据表明,汽车的质量受汽车油耗的影响。
汽车质量每上升100kg,油耗将提升0.3-0.6L/100km,相对来说,汽车整体质量减少10%,油耗就降低7%左右。
另外,汽车的轻量化不仅能减少耗油,为降低原材料做出贡献,还能减少有害气体的排放,每辆汽车减轻100kg,二氧化碳的排放量可降低5g/km,有利于我国的保护环境基本国策的实施。
而且,汽车的质量减少,零部件构造简化,可以为企业减少经济成本的投入,间接的减少消费者的支出。
商用车轻量化和高强度钢板的应用
2010年全年汽车 产量1800万辆 ,汽车保有量8000万辆
从2000年以后中国汽车工业发展进入了快车道。
中国汽车工业发展简况
汽车产量的增长情况
1000 900 800
Output of auto(*10 units)
700 600 500 400 300 200 100 0 1992 1994 1996 1998 2000 2002 2004 2006 2008 2010
2
个共性技术平台。
四种轿车产品 减轻自重8-10% 油耗降低6%以上 NCAP碰撞(安全性)达到4星级以上 商用车产品 减重10%以上 质量利用系数达到1.5以上 建立共性技术平台: 技术规范 产品开发数据库
远期 1. 全面提升我国汽车工业的 综合实力 2. 为汽车工业节能减排总目 标的实现做出贡献 3. 带动材料、装备等相关工 业的发展
中国汽车工程研究院
一、中国汽车工业发展简况
产量的增长情况
从53年建立一汽到2009年中国汽车工业走过了56年里程 1953年—1992年100万辆 1993年—2000年200万辆 2001年—2002年326万辆 2003年—445万辆,轿车高达45.4%,比例亦较合理 2005 年—570万辆,居全世界第四。 2006年—728万辆,销量居世界第二,产量居世界第三 2007年接近900万辆,如果在加农用车150-180万辆,产销均居世界第二.汽车保 有量,超过4000万辆,汽车工业已成为名符其实的支柱产业. 2008年汽车产量为938万辆,汽车保有量接近5100万辆 2009年全年产量1360万辆
热处理高强度钢板在车架上的应用1200mpa辊压整形热处理车架轻量化仓栅半挂车轻量化案例2车厢轻量化车厢开发序号原用材料现用材料减重效果4854q235dl700约200kg5862q235dl700约250kgq235dl700约300kg高强度钢自卸车车厢减重方案及效果成形性成形性回弹回弹模具磨损寿命模具磨损寿命设备吨位设备吨位焊接性能焊接性能疲劳性能疲劳性能刚性变化刚性变化高强减重应注意的问题高强减重应注意的问题项目项目普通仓栅半挂车普通仓栅半挂车配置普通钢配置普通钢轻型仓栅半挂车轻型仓栅半挂车配置高强度钢配置高强度钢普通仓栅半普通仓栅半挂车重量挂车重量轻型仓栅半轻型仓栅半挂车重量挂车重量可降低自可降低自重重1416mm1416mm88mm88mm700mpa700mpa级级8762kg8762kg4701kg4701kg4061kg4061kg腹板腹板8mm8mm5mm5mm700mpa700mpa级级7585kg7585kg4681kg4681kg2904kg2904kg地板地板3mm3mm15mm15mm1200mpa1200mpa级级6936kg6936kg3468kg3468kg3468kg3468kg1616轻型槽钢轻型槽钢3mm3mm折弯件折弯件700mpa700mpa级级3273kg3273kg1496kg1496kg1777kg1777kg立柱立柱立柱外罩立柱外罩4mm4mm带带内封板宽度内封板宽度180180立柱外罩立柱外罩3mm3mm无无内封板宽度内封板宽度120120700mpa700mpa级级2520kg2520kg1413kg1413kg1107kg1107kg合计合计29076kg29076kg15759kg15759kg13317kg13317kg减重458案例2仓栅半挂车轻量化中国汽车工程研究院九商用车轻量化和高强度钢热轧板的应用我国现阶段商用汽车8吨及以上大梁大都采用510mpa级大梁钢板制造如p510lb510lm510lw510lz510l钢板等
工艺商用车车架纵梁加工工艺方法比较
⼯艺商⽤车车架纵梁加⼯⼯艺⽅法⽐较欢迎阅读本篇⽂章,⽂末有福利哦!商⽤车车架纵梁产品结构特点纵梁与其他冲压件对⽐,其特点有以下⼏⽅⾯:(1)外形长、板料厚。
根据车型功能不同,纵梁长度范围⼤概为5~12m,厚度范围为4~10mm。
例如,牵引车车架纵梁长度⼀般在6~8m,载货⾃卸车架纵梁长度⼀般在8~12m。
(2)孔数多。
商⽤车80%以上的重要总成和部件在车架纵梁上进⾏装配。
例如,发动机、变速箱、车桥、驾驶室及外挂件等,纵梁孔数⼀般为200~400个。
(3)结构不复杂但精度要求⾼。
以U形结构为主,由于纵梁的孔和型⾯⼤部分都是装配孔、装配⾯,所以尺⼨精度要求⾼。
(4)材料强度⾼。
钢板屈服强度δs为500~700MPa。
商⽤车车架纵梁与内加强板⼀般有单层板、双层板、三层板三种主要结构形式,⼀般内加强板厚度都不⼤于纵梁厚度。
根据不同车型承载需要,配置不同层次和不同板厚的加强板。
按截⾯分类有等截⾯和变截⾯两种,按腹⾯分类有等直和弯曲两种,具体如图1所⽰。
图1 加强板形状分类商⽤车纵梁加⼯⼯艺⽅法传统冲压⼯艺⼤型压床结合模具进⾏冷冲压加⼯是国内主要卡车制造商初期⽣产纵梁采⽤的⽣产⼯艺,这种⽣产模式适⽤于品种少批量⼤的⽣产。
在60到90年代,卡车产品种类少,⽣产批量⼤,模具冲压⽣产的效率⾼、稳定性好,解放公司卡车⼚在2004年前⼀直采⽤此⼯艺⽣产纵梁。
加⼯⼯艺流程为:倍尺钢板→酸洗→模具落料冲孔→模具压弯。
其优点是:(1)单⼀品种⼤批量⽣产效率⾼。
(2)⽣产⾯积⼩,物流环节少。
(3)落料冲孔,外形尺⼨孔位精度⾼,⼀致性好。
(4)产品适应性较强,直槽纵梁和变截⾯纵梁都能⽣产。
缺点是:(1)模具投资⼤,制造周期长。
⼀套商⽤车纵梁落料冲孔模具和压弯模具共计约需要500万左右,模具的制造周期为8~12个⽉,在新产品准备时,⽆法满⾜快速投产的需要。
(2)倍尺料封闭落料材料利⽤率低。
在封闭落料冲孔时,双侧侧搭边值为30mm,对⽐净尺料每件重15kg左右,按⽉产1万辆计算,每⽉多产⽣废料近300t。
商用车车架孔位标准化设计
商用车车架孔位标准化设计摘要:在目前商用车市场环境及其发展过程中,运用标准化的设计思想是非常重要的,一方面可以使商用车的设计和生产效率提高,另一方面降低因为车型增多而给商用车企业带来的影响,从而控制生产成本。
车架是商用车的骨架,做好纵梁孔位标准化设计,是实现整车模块化、通用化设计的基础。
本文探讨了纵梁孔位标准化的设计方法,并在这一基础之上,简要分析了车架结构和各系统连接支架的标准化。
关键词:商用车;车架孔位;标准化设计前言:现阶段,我国的汽车行业发展很快,商用车的市场形势也在不断变化着,买方市场逐渐形成。
在这种情况下,商用车企业必须与时俱进,近些年来其车型研发数量,以及生产种类都在不断增加,市场竞争愈发激烈。
采用标准化、模块化的方法进行产品设计,实现车架纵梁孔位的标准化设计有着非常重要的意义。
本文对此进行了分析和探讨,希望能够有所裨益。
1.纵梁孔位设计现状1.1纵梁孔加工工艺现状在对孔位进行设计时,纵梁孔加工工艺的限制影响很大,所以本文先对目前已有的加工工艺进行简要介绍。
冲压成型,还有辊型,是现阶段国内常用的两种商用车纵梁加工方法,而辊型是比如东风和一汽等大部分厂商会采用的主要工艺方法,其具有的优点有很多,比如生产效率高,以及材料利用率高等,但是也有很多限制存在,如下:1.1.1纵梁孔距上下翼面必须大于一定距离在辊型工艺中,一般情况下会采用数控冲孔设备,对纵梁孔进行加工,但是加工范围容易受到冲压模具结构的制约。
如果60毫米是数控冲孔机下模外径,如图1所示,那么当加工与翼面距离小于30毫米的孔时,会与翼面产生干涉作用,从而导致后续工作没有办法继续。
因为设计值通常会比实际滚压后圆角的尺寸稍小一些,并且在滚压工艺过程中,经常会产生“喇叭口”的现象,所以现在普遍要求纵梁孔距在生产时,其翻边都要大于36毫米。
图1 纵梁数控冲孔示意图1.1.2孔径选用范围有限在设计纵梁孔孔径大小时,需要结合目前已有的冲孔模具规格进行,不然没有办法进行加工。
- 1、下载文档前请自行甄别文档内容的完整性,平台不提供额外的编辑、内容补充、找答案等附加服务。
- 2、"仅部分预览"的文档,不可在线预览部分如存在完整性等问题,可反馈申请退款(可完整预览的文档不适用该条件!)。
- 3、如文档侵犯您的权益,请联系客服反馈,我们会尽快为您处理(人工客服工作时间:9:00-18:30)。
商用车车架工艺技术与材料开发
发表时间:2017-04-11T16:12:15.410Z 来源:《基层建设》2017年1期作者:蓝军
[导读] 本文主要对商用车车架工艺技术与材料开发进行分析探讨。
东风柳州汽车有限公司广西柳州 545001
摘要:近年来,得益于国家政策的扶持和国内市场的旺盛需求,我国汽车工业发展极为迅速,同时汽车也消耗了大量的不可再生能源。
因此,减少能源消耗,降低制造及使用成本成为了各汽车制造厂家的重点研究课题。
汽车发展要求的轻量化、智能化、节能、舒适、安全和环保等离不开汽车新材料的开发,而汽车材料的开发又与汽车工艺技术的发展是密不可分的。
基于此,本文主要对商用车车架工艺技术与材料开发进行分析探讨。
关键词:商用车车架;工艺技术;材料开发
1、前言
虽然这几年国内的钢铁行业也推出了一些适用于商用车车架高强度钢板如590、610、700MPa和超细晶粒钢等钢种,但并未在汽车制造企业大应用,制约的不仅是新材料价格,还有钢铁企业对汽车材料品种定位与商用车车架的工艺技术发展不同步。
由此可见,钢铁企业的新材料开发必须依托汽业行业,而汽车行业也只有通过与钢铁企业合作共同开发出具有优良性能、低成本的新材料才能满足汽车高性能、轻化、低成本、节能和环保的要求。
2、商用车车架工艺技术——轻量化工艺
汽车轻量化的主要途径:一是采用比如高强度钢板、铝合金、镁合金和新型复合材料等强度更高、质量更轻的新型轻量化材料;二是应用以CAE为基础的现代结构优化技术设计汽车各零部件的结构,使结构部件薄壁化、中空化、小型化以及对零部件进行结构形状变更等,以实现最大限度地减轻零部件的质量。
2.1高强度材料替代轻量化
采用高强度材料替代进行轻量化是最简单的也是大家最容易想到的轻量化方法,它仅需将原有普通材料更换为高强度材料,同时减薄或减小零件尺寸,在保证强度等同于原结构的前提下实现轻量化设计。
商用车车架因整车布置及各系统零部件安装的需要,目前采用的基本是边梁式梯形结构车架,另外为了减少工艺生产难度,所以其各零部件的结构也会设计得尽可能简单。
因此在车架纵梁和车架整体结构方面,商用车车架无法像乘用车那样可以设计为中空或其他更有利于轻量化的结构。
更多的便是通过将车架总成上的各零部件采用高强度钢板替代原来的普通钢板进行减薄设计实现轻量化。
2.2优化车架结构轻量化
优化车架结构进行轻量化,是指在不更换原有零件的材料,通过以CAE为基础的现代结构优化技术设计手段,在保证车架强度和刚度的前提下,对车架的结构形状进行改变,取消对车架强度和刚度无贡献或贡献小的零件,减薄或缩小尺寸实现轻量化。
如以前的商用车车架普遍采用双层大梁,通过优化分析,可以设计为单层大梁,根据不同工况需要适当对车架做局部加强,以保证车架总成的强度和刚度和原车架相当。
采用高强度材料替代和通过CAE分析优化车架结构两种方法是目前车架轻量化采用最多、也是最有效的方法,效果也是非常明显的。
这两种方法在实际工作中应该是相辅相成,共同使用才能更大地挖掘出车架轻量化的空间,才能保证优化后的车架可靠。
在上述轻量化方法的基础上,通过细化扩展,借助先进的设计优化软件,业界学者及汽车设计工程师们提出了很多的轻量化设计方法,开展了大量的车架轻量化设计工作,为车架的轻量化提供了大量的参考理论依据。
3、商用车车架材料开发分析
3.1高强度钢板的发展
目前国内已经批量生产高强度热轧钢板为700MPa级钢板,800MPa级及以上强度的高强度热轧钢板处于小批试用阶段,主要用在工程机械产品上,在商用车车架上暂时还无厂家试用。
特别是900MPa以上的材料金相组织为“贝氏体+马氏体”(900MPa以下的材料为铁素体析出强化+贝氏体),其延伸率较低,在10%左右,不适用于成型件,一般需采用焊接形式形成构件。
因目前的热轧技术已经基本做到极限,如果要再进一步提高抗拉强度,需要进行热处理,这样会导致钢材成本大幅增加。
随着钢材强度的提高,加工难度也会变大,对设备能力的要求也有所提高,因此需要调整设计方案和制造工艺,如设计上将零件厚度减薄。
3.2高强度钢的成型能力
(1)传统的车架纵梁成型工艺
传统的车架纵梁成型工艺主要为模具冲压成型,其具有生产效率高、质量稳定的特点,适用于单一品种的大批量生产,特别是可以进行双梁合压成型。
其采用的压力机吨位较大,一般在3000t以上。
压力机有油压机和机械式压力机两种,机械式压力机效率高;油压机成型过程中保压时间比机械式压力机稍长,对比同等吨位机械式压力机,具有成型后回弹少,质量更稳定的优点。
因此,过去通常采用的机械式压力机逐步被油压机所替代。
图,1为亚洲最大的6300t机械式压力机。
(2)车架纵梁的辊压成型工艺
辊压成型是与模具成型完全不同的纵梁生产工艺,辊压成型是辊轮在做旋转运动把纵梁带动向前的同时将纵梁逐步弯曲成型。
其具有生产效率高,产品质量稳定,零件长度可以随时调整等优点。
国内的辊压线在生产不同纵梁高度(即槽型宽度)时,需要更换辊轮,而更换辊轮和调试的时间较长。
目前国外的辊压成型线通过伺服电机控制可在极短时间内完成产品料厚、槽宽和长度等参数的设置转换,且成型质量稳定,但设备非常昂贵,投入较大。
如重汽采用了意大利Stam公司的辊压线。
对于高强度板,采用传统的成型工艺会因设备压力问题导致无法采用双梁合压。
因此传统的生产工艺必须要进行改造以满足高强度板的成型能力要求,如采用辊压成型或采用单压工艺(即纵梁和纵梁加强板分别成型后再组合)。
同时,冲孔和剪切设备也需要相应升级冲头和刀具,采用强度更高、耐磨性更好的材料所制作的冲头和刀具。
若采用更高强度的钢板,上述工艺问题会更为严重,所以,车架的生产工艺也将会是未来几年内制约向更高强度钢板发展的重要因素之一。
4、结语
车架的结构性能影响着整车的正常行驶,所以车架轻量化必须在满足一定的强度和刚度的条件下进行。
材料开发是现代汽车工业的重点课题,也是汽车工业长远发展的有力保障。
参考文献:
[1]乔艳军.商用车车架工艺[J].汽车工艺与材料,2008,(3):15-20
[2]周岁华.商用车车架工艺技术与材料开发[J].汽车工艺与材料,2007(8):37-38。