旋流板式气液分离器的放大规律解读
旋流式液气分离器的设计
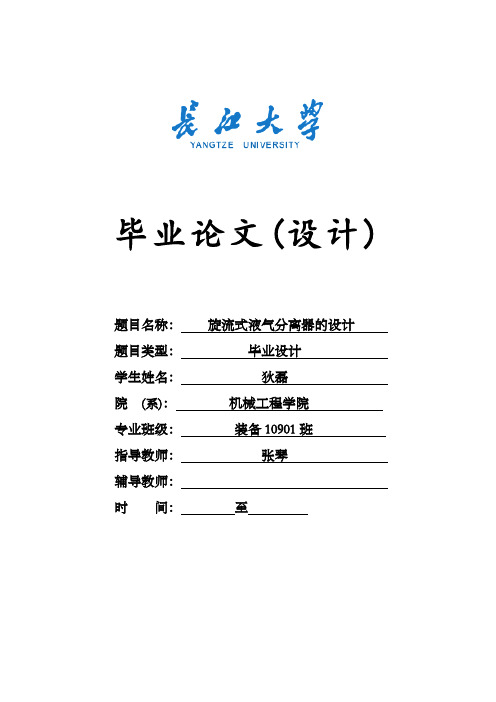
毕业论文(设计)题目名称:旋流式液气分离器的设计题目类型:毕业设计学生姓名:狄磊院(系):机械工程学院专业班级:装备10901班指导教师:张琴辅导教师:时间:至目录毕业论文(设计)任务书 (Ⅰ)开题报告 (Ⅱ)指导教师审查意见 (Ⅲ)评阅教师评语 (Ⅳ)答辩会议记录 (Ⅴ)中文摘要 (Ⅵ)外文摘要 (Ⅶ)1 绪论 (7)选择旋流式液气分离器的意义 (7)国内外现状和进展趋势 (7)国外现状和进展趋势 (7)国内现状和进展趋势 (9)2 方案论证 (9)旋流式液气分离方案的可行性 (9)旋流式分离器的结构及工作原理 (10)3 分离器的整体设计 (11)旋流器的直径和长度的计算 (11)分离器结构设计 (13)分离器整体结构设计 (13)脱气结构 (15)钻井液入口的尺寸 (15)旋流器的结构设计 (15)外筒体的设计 (17)接口管设计 (18)外部结构 (21)4、要紧零部件的设计及校核计算 (22)筒体和封头的壁厚计算 (22)外容器筒体、封头壁厚计算 (22)旋流器筒体封头壁厚计算 (24)人孔 (25)人孔选择 (25)人孔补强 (26)支座 (26)分离器的总质量 (26)支座的选用及安装要求 (28)5 分离器的安装 (28)焊接 (28)安装顺序 (29)6 壳体的有限元分析 (32)7 总结 (35)参考文献 (37)致谢 (39)附录一 (40)附录二 (43)旋流式液气分离器的设计学生:狄磊,长江大学机械工程学院指导教师:张琴,长江大学机械工程学院【摘要】旋流分离器,是一种利用离心沉降原理将非均相混合物中具有不同密度的相分离的机械分离设备。
在具有密度差的混合物以必然的方式及速度从入口进入旋流分离器后,在离心力场的作用下,密度大的相被甩向周围,并顺着壁面向下运动,作为底流排出;密度小的相向中间迁移,并向上运动,最后作为溢流排出。
如此就达到了分离的目的。
旋流分离技术可用于液液分离、气液分离、固液分离、气固分离等。
导叶式气液旋流分离器试验研究
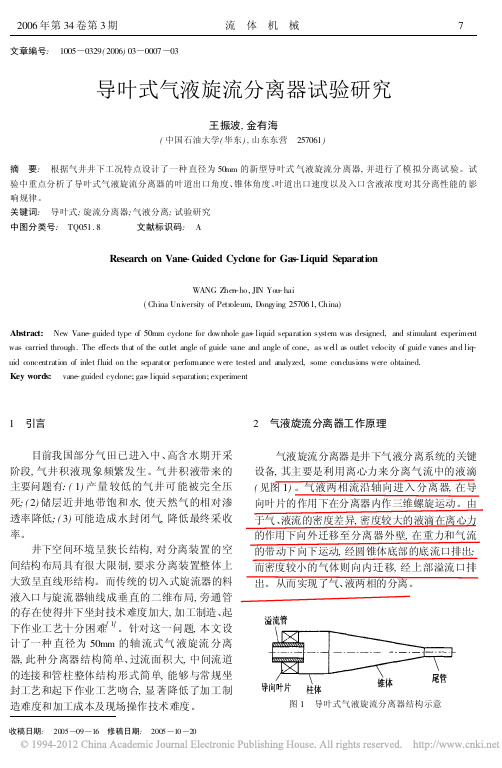
文章编号: 1005)0329(2006)03)0007)03导叶式气液旋流分离器试验研究王振波,金有海(中国石油大学(华东),山东东营 257061)摘 要: 根据气井井下工况特点设计了一种直径为50mm 的新型导叶式气液旋流分离器,并进行了模拟分离试验。
试验中重点分析了导叶式气液旋流分离器的叶道出口角度、锥体角度、叶道出口速度以及入口含液浓度对其分离性能的影响规律。
关键词: 导叶式;旋流分离器;气液分离;试验研究中图分类号: TQ051.8 文献标识码: AResearch on Vane -Guided Cyclone for Gas -Liquid SeparationWANG Zhen -bo ,JIN You -hai(China Uni versity of Petroleum,Dongying 257061,China)Abstract: New Vane -guided type of 50mm cyclone for downhole gas -liquid separation system was designed,and stimulant experiment was carried through.The effects that of the outlet angle of guide vane and angle of cone,as well as outlet velocity of guide vanes and liq -uid concentration of inlet fluid on the separator performance were tested and analyzed,some conclusions were obtained.Key words: vane -guided cyclone;gas -liquid separation;experiment收稿日期: 2005)09)16 修稿日期: 2005)10)201 引言目前我国部分气田已进入中、高含水期开采阶段,气井积液现象频繁发生。
旋流式汽水分离器
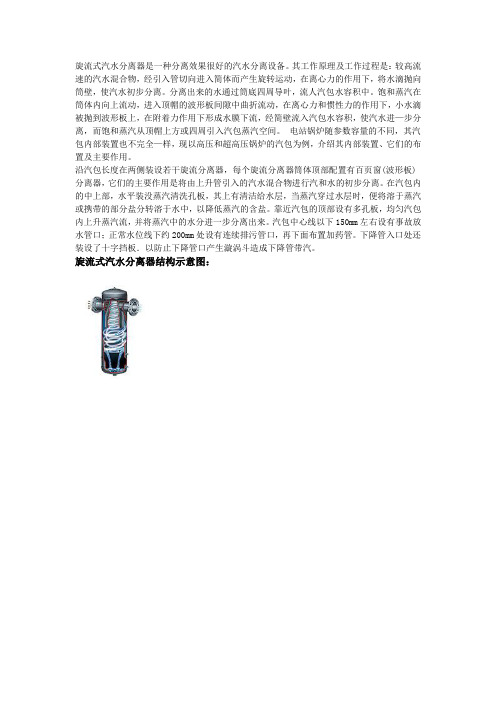
旋流式汽水分离器是一种分离效果很好的汽水分离设备。
其工作原理及工作过程是:较高流速的汽水混合物,经引入管切向进入简体而产生旋转运动,在离心力的作用下,将水滴抛向筒壁,使汽水初步分离。
分离出来的水通过筒底四周导叶,流人汽包水容积中。
饱和蒸汽在筒体内向上流动,进入顶帽的波形板间隙中曲折流动,在离心力和惯性力的作用下,小水滴被抛到波形板上,在附着力作用下形成水膜下流,经简壁流入汽包水容积,使汽水进—步分离,而饱和蒸汽从顶帽上方或四周引入汽包蒸汽空间。
电站锅炉随参数容量的不同,其汽包内部装置也不完全—样,现以高压和超高压锅炉的汽包为例,介绍其内部装置、它们的布置及主要作用。
沿汽包长度在两侧装设若干旋流分离器,每个旋流分离器筒体顶部配置有百页窗(波形板)分离器,它们的主要作用是将由上升管引入的汽水混合物进行汽和水的初步分离。
在汽包内的中上部,水平装没蒸汽清洗孔板,其上有清洁给水层,当蒸汽穿过水层时,便将溶于蒸汽或携带的部分盐分转溶于水中,以降低蒸汽的含盐。
靠近汽包的顶部设有多孔板,均匀汽包内上升蒸汽流,并将蒸汽中的水分进一步分离出来。
汽包中心线以下150mm左右设有事故放水管口;正常水位线下约200mm处设有连续排污管口,再下面布置加药管。
下降管入口处还装设了十字挡板.以防止下降管口产生漩涡斗造成下降管带汽。
旋流式汽水分离器结构示意图:。
分析天然气净化用旋风分离器气液分离性能

分析天然气净化用旋风分离器气液分离性能摘要:为了对天然气净化用旋风分离器气液分离性能进行有效评价,应用两种方法进行了实验。
本文针对天然气净化用旋风分离器气液分离性能做出了进一步探究,对实验、实验结果进行了详细分析。
关键词:天然气净化;旋风分离器;气液分离性能天然气气质对压缩机组以及阀门等设备的有序运行非常关键,一些长输管线的上游气田特性为凝析气田等,凝析气为多元组分当中的一种气体混合物,以饱和烃组为组。
如果天然气当中,含有的重组分进入到了管道,会因为温度以及压力产生的变化,出现凝析以及反凝析的情况。
因为管道当中的内气速比较高,通常气体当中的析出来的液体,在管道当中很难构成相对稳定的连续液相,会引用微笑液滴的方式,在气相中夹带。
如果天然气当中,产生了凝析水以及凝析油,液滴以及天然气当中的氯离子以及湿气当中存在的二氧化碳等会结合在一起,这样压缩机叶片便会发生腐蚀,对其使用寿命产生影响,并影响使用安全。
此外,如果天然气当中,存在轻烃以及水滴,会使压缩机将干气密封发生失效,从而导致成燃气系统调压器发生堵塞。
1、实验1.1材料实验介质为空气,温度为室内温度,压力为大气压。
为了对天然气中存在的游离水以及轻烃进行模拟,实验应用的液体为DOS。
1.2实验装置以及分析仪器实验装置示意图,如图一所示。
雾化部分流程图,如图二所示。
图一:实验装置示意图图二:雾化部分流程图实验当中,测量的主要参数包括旋风分离器当中的入口气速、粒径分布以及进出口液滴的浓度。
旋风分离器当中入口气速,应用皮托管进行测量,进口液滴浓度,可借助液滴雾化系统进行确定,但是难以测量进口液滴的粒径分布。
由于从雾化贫嘴出口一直到旋风分离器当中的入口,存在一定的距离,所以从雾化喷嘴当中出来的液滴粒径分布不同于旋风分离器入口[1]。
旋风分离器出口液滴浓度,有两种不同的测量工作,相互印证,这样可使测量精度提升。
依照等动采样原理,可采样旋风分离器出口气体。
其一,借助高精度玻璃纤维滤膜;其二,利用光学粒子计数器Welas2000。
气液两相流的分离

气液两相流的分离方法综述摘要:本文从气液两相流分离方法出发,分析了6种最常见的气液分离方法。
研究了各种气液两相流分离方法的原理,介绍了各方法的优缺点及利用这些方法制造出的气液分离器的结构,并介绍了各种分离方法适用的领域,并针对部分方法提出了可能的改进方法。
关键字:气液两相流分离机理气液分离器引言气液两相流的分离主要在气液分离器中进行,而气液分离器采用的分离结构很多,其分离方法主要有6种,分别是:1、重力沉降;2、折流分离;3、离心分离;4、丝网分离;5、超滤分离;6、填料分离等。
但综合起来分离原理只有两种:一、利用组分质量(重量)不同对混合物进行分离(如分离方法1、2、3、6)。
气体与液体的密度不同,相同体积下气体的质量比液体的质量小。
二、利用分散系粒子大小不同对混合物进行分离(如分离方法4、5)。
液体的分子聚集状态与气体的分子聚集状态不同,气体分子距离较远,而液体分子距离要近得多,所以气体粒子比液体粒子小些。
下面就每种方法的原理进行介绍。
1.重力沉降1.1 重力沉降原理气液重力沉降分离是利用气液两相的密度差实现两相的重力分离,即液滴所受重力大于其气体的浮力时,液滴将从气相中沉降出来,被分离。
由于气体与液体的密度不同,液体在与气体一起流动时,液体会受到重力的作用,产生一个向下的速度,而气体仍然朝着原来的方向流动,也就是说液体与气体在重力场中有分离的倾向,向下的液体附着在壁面上汇聚在一起通过排放管排出。
1.2 重力沉降式气液分离器图1 立式和卧式重力沉降气液分离器简图重力沉降分离器一般有立式和卧式(图1)两类,它结构简单、制造方便、操作弹性大,但操作需要较长的停留时间,分离器体积大,笨重,投资高,分离效果差,只能分离较大液滴,其分离液滴的极限值通常为100μm,主要用于地面天然气开采集输。
1.3 发展现状经过几十年的发展,该项技术已基本成熟。
当前研究的重点是研制高效的内部填料以提高其分离效率。
此类分离器的设计关键在于确定液滴的沉降速度,然后确定分离器的直径。
丙烯腈气液分离器放大规律研究及工业应用
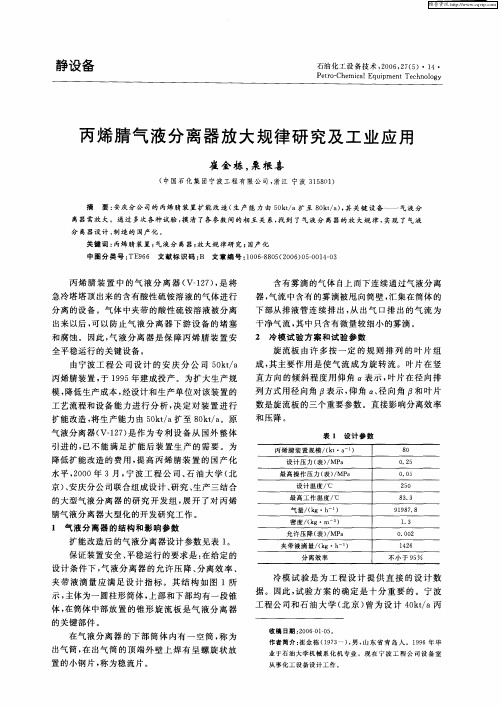
表 1 设 计 参 数
丙 烯 腈 装 置 规 模 / k a1 (t・ - ) 设 计 压 力 ( ) MP 表 / a 8 0 0 2 .5
最 高 操 作 压 力 ( ) MP 表 / a
设计温度/ ℃
0 0 .5
20 5
最高工作温度/ ℃ 气量/k (g・h1) - 密 度 /k ( g・m ) 允 许 压 降 ( ) MP 表 / a
夹 带 液滴 量 /k (g・h1 -) 分 离 效 率
8 . 33 9978 18 . 13 . 002 . 0
1 2 46 不 小 于 9 5
腈气 液分离 器 大型化 的开 发研 究工 作 。
1 气 液分 离器 的 结构和 影响 参数 扩能 改造后 的气 液分 离器 设计 参数 见表 1 。
业 于石 油 大 学 机 械 系 化 机 专 业 。现 在 宁 波 工 程 公 司 设 备 室 从事化工设备设计工作 。
维普资讯
第 2 卷第 5 7 期
崔 金栋等.丙烯腈气 液分 离器 放大规律研究及: 业应 用 】 二
烯 腈装 置用 的气 液 分 离 器 做 过 冷 模试 验 , 题 组 课
( 国石 化集 团 宁 波工 程 有 限公 司 , 江 宁 波 3 5 0 ) 中 浙 18 1
摘
要 : 庆 分 公 司 的 丙烯 腈 装 置 扩 能 改 造 ( 产 能 力 由 5 k/ 安 生 0 ta扩 至 8 k/ ) 其 关 键 设 备 试验 , 摸清 了各参数 间的相互 关 系, 找到 了气液 分 离器的放 大规律 , 实现 了气液
丙 烯腈 装 置 中 的气 液 分 离 器 ( 1 7 , 将 V一2 ) 是 急冷塔 塔顶 出来 的含有 酸性硫 铵溶 液 的气体进 行 分 离 的设 备 。气体 中夹 带 的酸性硫 铵溶 液被 分离 出来 以后 , 以防止 气 液 分离 器 下 游设 备 的堵 塞 可
旋液分离器
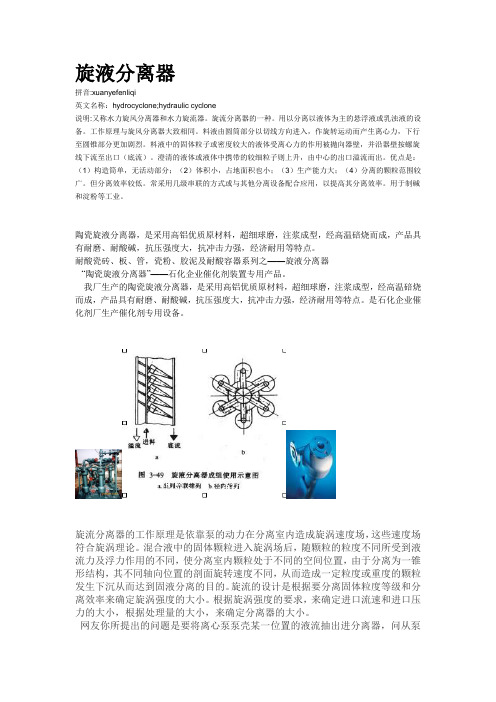
旋液分离器拼音:xuanyefenliqi英文名称:hydrocyclone;hydraulic cyclone说明:又称水力旋风分离器和水力旋流器。
旋流分离器的一种。
用以分离以液体为主的悬浮液或乳浊液的设备。
工作原理与旋风分离器大致相同。
料液由圆筒部分以切线方向进入,作旋转运动而产生离心力,下行至圆锥部分更加剧烈。
料液中的固体粒子或密度较大的液体受离心力的作用被抛向器壁,并沿器壁按螺旋线下流至出口(底流)。
澄清的液体或液体中携带的较细粒子则上升,由中心的出口溢流而出。
优点是:(1)构造筒单,无活动部分;(2)体积小,占地面积也小;(3)生产能力大;(4)分离的颗粒范围较广。
但分离效率较低。
常采用几级串联的方式或与其他分离设备配合应用,以提高其分离效率。
用于制碱和淀粉等工业。
陶瓷旋液分离器,是采用高铝优质原材料,超细球磨,注浆成型,经高温碚烧而成,产品具有耐磨、耐酸碱,抗压强度大,抗冲击力强,经济耐用等特点。
耐酸瓷砖、板、管,瓷粉、胶泥及耐酸容器系列之——旋液分离器“陶瓷旋液分离器”——石化企业催化剂装置专用产品。
我厂生产的陶瓷旋液分离器,是采用高铝优质原材料,超细球磨,注浆成型,经高温碚烧而成,产品具有耐磨、耐酸碱,抗压强度大,抗冲击力强,经济耐用等特点。
是石化企业催化剂厂生产催化剂专用设备。
旋流分离器的工作原理是依靠泵的动力在分离室内造成旋涡速度场,这些速度场符合旋涡理论。
混合液中的固体颗粒进入旋涡场后,随颗粒的粒度不同所受到液流力及浮力作用的不同,使分离室内颗粒处于不同的空间位置,由于分离为一锥形结构,其不同轴向位置的剖面旋转速度不同,从而造成一定粒度或重度的颗粒发生下沉从而达到固液分离的目的。
旋流的设计是根据要分离固体粒度等级和分离效率来确定旋涡强度的大小。
根据旋涡强度的要求,来确定进口流速和进口压力的大小,根据处理量的大小,来确定分离器的大小。
网友你所提出的问题是要将离心泵泵壳某一位置的液流抽出进分离器,问从泵壳何位置抽出好?关键是看你要求的分离物质的粒度及重度的分布情况和分离效率的大小,换句话讲即分离的目标是什么?不管从何位置抽水,都必须要满足分离器的工作条件及进口参数的要求,才能达到分离的效果。
旋流分离理论在气-液分离器设计中的应用
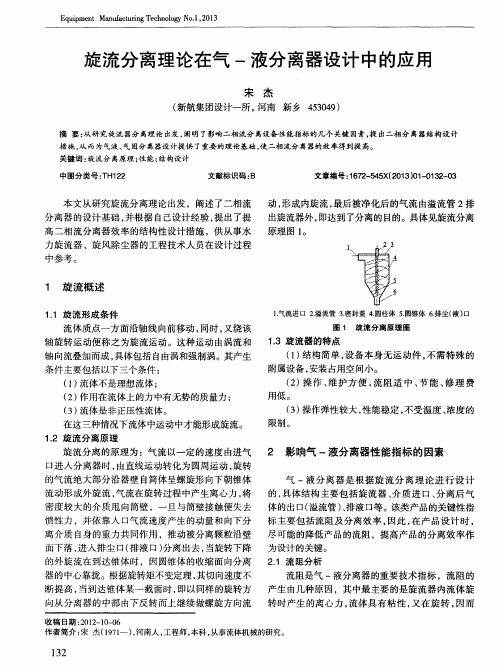
措施 , 从 而 为 气液 、 气 固分 离器设 计提 供 了 重要 的理 论 基 础 , 使 二 相 流 分 离 器的 效 率 得 到 提 高 。 关键词 : 旋 流 分 离原 理 ; 性能; 结 构 设 计
( 3 ) 操作 弹性 较 大 , 性 能 稳定 , 不受温度、 浓 度 的 限制 。
在这三种情况下流体 中运动中才能形成旋流。 1 . 2 旋 流分 离原 理
口进入分离器 时 , 由直线运动转化为圆周运动 , 旋转 的气流绝大部分沿器壁 自筒体呈螺旋形 向下朝锥体
旋流分离的原理为 :气流 以一定 的速度 由进气 2 影 响气 一液分 离器 性能指标 的因素
Eq u i p me n t Ma n u f a c t u r i n g T e c h n o l o g y No . 1 , 2 0 1 3
旋流分 离理 论在气 一液分 离器设计 中的应 用
宋 杰
( 新航集团设计一所 , 河南 新乡 4 5 3 0 4 9 )
称为半 自由旋流区 Ⅱ, 其切 向速度分布规律为 : r =常数 ( 2 ) 其 中, n为速度分布指数( 一般取 0 . 5 0 . 9 g / m 3 ;
为流速 , m / s 。
径向速度是影 响分离器性 能的重要 因素 。约在 r o 为溢流管半径 , m 。 旋流器有效高度 中点径向速度 , 为零的点称为分界 2 . 2 分 离效 率 分析 点, 在分界点上部径 向速度方向指 向筒壁 , 形成外 向 产 品的分离效率 与介质在旋 流器 内的速度分布 流 ;在分界点 以下速度方 向指向旋流器中心形成 内 及压力分布密切相关 。 旋流。在 内旋流作用下使要分离的介质 由外 向内推 2 . 2 . 1 流场 中气 流 的速度 分 布 阻止分离物的沉降 , 所 以, 径 向速度越 由于旋流器 内流体 的运动是一种复杂的三元空 至漩 涡中心 , 分离器的分离能力越差 。 间的螺旋运动 ,其 内部任一点 的速度可分为切向速 大 ,
- 1、下载文档前请自行甄别文档内容的完整性,平台不提供额外的编辑、内容补充、找答案等附加服务。
- 2、"仅部分预览"的文档,不可在线预览部分如存在完整性等问题,可反馈申请退款(可完整预览的文档不适用该条件!)。
- 3、如文档侵犯您的权益,请联系客服反馈,我们会尽快为您处理(人工客服工作时间:9:00-18:30)。
第3卷第5期过程工程学报 Vol.3 No.5 2003年10 月 The Chinese Journal of Process Engineering Oct. 2003收稿日期:2003–03–12, 修回日期:2003–05–06基金项目:中国石油化工股份有限公司科技开发资助项目(编号: 300023作者简介:魏伟胜(1962–, 男, 广东省五华县人, 硕士, 高级工程师, 主要研究催化反应工程, E-mail: weiws@.旋流板式气液分离器的放大规律魏伟胜,樊建华,鲍晓军, 石冈[石油大学(北京中国石油天然气集团公司催化重点实验室, 北京 102200]摘要:对旋流板式气液分离器在3种规模、18种旋流板结构下进行了模型实验研究,考察了旋流板结构参数(径向角、仰角和叶片数量对分离效率和压降的影响,并建立了预测分离器压降的关联式,为旋流板结构参数的确定提供了依据. 工业应用的标定结果表明分离器压降预测式是准确的,它可用于工业气液分离器的放大设计. 关键词:气液分离;旋流板;分离效率;压降中图分类号:TQ028.4 文献标识码:A 文章编号:1009–606X(200305–0390–061前言旋流板式气液分离器是一种典型的基于离心分离原理的气液分离器[1,2]. 分离器的主体为一圆柱形筒体,上部和下部均有一段锥体,见图1. 在筒体中部放置的锥形旋流板是除雾的关键部件,其结构如图2所示(详细结构可参考文献[3]. 旋流板由许多按一定仰角倾斜的叶片放置一圈,当气流穿过叶片间隙时就成为旋转气流,气流中夹带的液滴在惯性的作用下以一定的仰角射出而被甩向外侧,汇集流到溢流槽内,从而达到气液分离的目的. 叶片在竖直方向的倾斜程度用仰角α表示,在径向的排列方式用径向角β表示. 叶片数量、仰角α和径向角β是旋流板的3个重要参数.图1 气液分离器结构示意图图2 旋流板结构示意图Fig.1 Mist swirl separator Fig.2 The structure of the swirl vane目前工业上广泛应用的各类旋流板式气液分离器的设计和生产技术大多为一些公司的专有或专利技术,有关其结构和设计放大方法的报道很少[4,5]. 为深入了解旋流板式气液分离器的分离机InletSwirl vaneExit tube Gas outletCylinderLiquidoutlethαβ5期魏伟胜等:旋流板式气液分离器的放大规律391理,优化旋流板式气液分离器的结构和操作参数,本文以丙烯腈装置用的旋流板式气液分离器为对象,进行了较为系统的实验研究,以期为旋流板式分离器的开发和工业应用提供必要的基础.2模型实验装置实验流程如图3所示. 旋流板的叶片数量若无特别说明,则均为36片. 实验介质为空气–稀盐水体系. 雾滴由空气辅助双流体雾化喷嘴产生. 液流:盐水, 用一小水泵增压注入,注入的盐水量先通过转子流量计进行初步的调节控制,然后再用台秤进行更准确的计量;气流:雾化所需压缩空气,由V–3/10型空气压缩机产生,压缩空气量用LZB 型转子流量计计量. 实验所需的风量较大,在实验中空气压头不需要很大,因此实验采用罗茨风机供风即可,风量用QDF–6型数字式热线风速仪进行测量. 进水和接水的两个水箱都用台秤监测水的进出量.分离效率是单位时间内捕集的雾滴质量与进入分离器的雾滴质量之比. 由于在造粒时肯定会有部分水以蒸汽形式存在,因此进入喷嘴的液体质量需去除蒸发量后才是雾滴的真实质量. 在空气–盐水系统的实验中,可通过测量进出分离器的盐水浓度来准确测定液体的蒸发量. 气流出口直接进大气,压力降由分离器气体入口处的压力计(或U 型管测得.实验中,雾滴浓度一般控制在19 g/m 3, 雾滴平均粒径一般在30 µm(它由进入双流道喷嘴的气体和液体流量来控制.3实验结果与讨论3.1分离器的最佳空速空速是指气体通过分离器最大柱体截面时的表观速度,它直接关系到设备的处理量. 空速对分离效率和总压降有明显的影响,是评价分离器操作弹性的主要依据. 图4为不同空速下的分离图3 实验装置流程示意图Fig.3 Schematic diagram of experimental apparatusDual-flow nozzleDual–flow nozzle392 过程工程学报 3卷效率,表明对于结构一定的气液分离器有一最佳空速.表1是筒径D =340 mm 规模下分离器的最佳空速,其中括号内的数是气流通过叶片之间的理论平均速度. 不难发现,对于一定筒径的分离器,当其它条件不变时,径向角或仰角增大,将造成叶片间的通气面积减小,气流的穿过速度增大,动能因子的增大使得流体的湍流脉动更加剧烈,因此径向角或仰角较大的旋流板对应的最佳气速较小,但通过叶片时的速度却增加.在3种规模下所做的实验表明,随着筒径的增加, 最佳空速稍有减少,但通过叶片之间的气流速度却增加. 因此选定空速在5~9 m/s ,通过叶片时的速度在20 m/s 左右时较为合适.表1 D =340mm 时设备各结构最佳空速Table 1 Optimal superficial gas velocity at D =340 mm (m/sElevation αRadial angl e β20o30o 40o 40o 45o50o9.0(10.79.5(14.4 9.0(15.6 8.5(17.57.5(16.7Note: Values in brackets are calculated velocity through vanes.3.2旋流板结构旋流板是气液分离器的核心部件,它决定了分离器的分离效率和压降. (1 旋流板仰角对分离效率和压降的影响表2是φ700 mm 设备在径向角为55o 时,平均分离效率和压降随仰角变化的关系. 由表可见,随着仰角的增大,平均分离效率明显提高,但同时设备压降急剧增大. 综合考虑仰角在30o 为宜.表2平均分离效率和压降随仰角的变化Table 2 Effect of elevation on separation efficiency and pressure drop (U =6.36 m/s Elevation α20o 30 o 40 o Separation efficiency (% 93.9 96.0 98.1 Pressure drop (Pa7609901580(2 旋流板径向角对分离效率和压降的影响表3是φ700 mm 设备在仰角为30o 时,平均分离效率和压降随径向角变化的关系. 由表可见,随着径向角的增大,平均分离效率明显提高. 考虑到分离器的允许压降,规模较小的分离器径向角应小一些,规模较大的气液分离器应大一些. 因此旋流板径向角可选范围为50o ~60o .表3平均分离效率和压降随径向角的变化Table 3 Effect of radial angle on separation efficiency and pressure drop (U =6.36 m/sRadi al angle β50o 55o 60o Separation efficiency (% 94.6 96.0 99.0 Pressure drop (Pa81099017004567891011121314η (%U (m/s图4 气速–效率关系图Fig.4 Influence of superficial gas velocity onseparation efficiency5期魏伟胜等:旋流板式气液分离器的放大规律393(3 旋流板叶片数对分离效率和压降的影响表4是φ700 mm 设备在仰角、径向角和空速固定时,平均分离效率和压降随叶片数变化的关系. 由表可见,随着叶片数的增大,平均分离效率和压降明显提高.表4平均分离效率和压降随叶片数的变化Table 4 Effect of vane number on separation efficiency and pressure drop (U =6.36 m/sVane number36 40 45 Separation efficiency (% 89.3 96.8 98.8 Pressure drop (Pa3805606803.3高径比气液分离器柱体直径一定时,高径比就反映了分离器的高度. 在轴向方向上,最重要的参数是出气筒与旋流板的距离h (见图1. 在D=340 mm 规模的分离器上考察了出气筒与旋流板之间距离对分离效率的影响,实验结果如图5所示. 雾滴受旋转气流的夹带,在离心力的作用下被甩向器壁,其运动可分解为向下的轴向运动和向外的径向运动. 由临界粒径关联式知,只要雾滴在分离器内的停留时间大于移动到壁面所需时间,该雾滴就可以被捕集,因此在其它条件不变的情况下,分离效率将随出气筒高度降低而升高,但事实上并非如此,出气筒高度过低时,二次夹带的负面作用将占主要地位,造成分离效率的下降,因此出气筒高度应有一最佳值. 从图5可见,在108~248 mm(32%~73%D 范围内,分离效率较高. 4分离器压降的预测从上述实验可知分离器叶片的仰角和径向角越大或者叶片越多都有利于提高分离效率,但压降也随之增加. 由于工业上对分离器压降有一限制,一般要求小于2 kPa ,因此旋流板的选用原则应该是在保证分离器压降小于2 kPa 的条件下,使分离器具有较高的分离效率.气液分离器的压降可表达为3部分之和:入口、出口的局部阻力损失(∆P i 和∆P e 和分离器内的阻力损失(∆P plate . 前两者主要是克服进气和排气的各种损失,对分离过程基本上不起任何积极作用,应尽量克服;后者主要是造成气体的旋转,给离心力提供能量,对分离过程起积极作用. 实验表明,旋流板的结构变化对压降的影响最大. 图6是D=340 mm 气液分离器在5种旋流板结构下,压降随空速变化的关系. 另一方面,气液分离器的流场特性与旋风分离器类似,参考前人对旋风分离器压降建立的关联式,因此分离器的总压降可表示为(2i e plate i e plate1(1.2P P P P u ζζζρε∆=∆+∆+∆=+++ (1 实验所用分离器进口和出口截面固定,所以ζi 和ζe 可视为定值. 由于进口是一锥形渐扩体,阻力损失可忽略不计,ζi 近似为0. 出气筒直径D e 与分离器筒径D 符合以下关系:22e 14.D D = (250100150200250300949596979899η (%h (mm图5 分离效率随出气筒与旋流板间距离的变化Fig.5 Change of separation efficiency with the distance between the swirl vane and the exit tube394 过程工程学报 3卷突然缩小的局部阻力系数为0.375(以小管径气速为准[6],若以大管气速计则ζe 为6.0. 数值计算表明出口阻力系数取6.0 是合适的.当改变旋流板的径向角、仰角和叶片数量时,叶片通气面积将相应发生显著变化. 从图6可知,径向角和仰角越大,叶片的总流通面积越小,设备的总压降越大;相反叶片的总流通面积越大,设备的总压降将越小. 引入一个板结构参数B ,它等于分离器柱体截面积与叶片的总流通面积之比,因此阻力系数ζplate 与B 成正比例关系. 再引入一个与分离器规模有关的准数Ar =D 3ρ2g /µ2,假定:plate (,,f B Ar ζ= (3 用3种规模条件下的实测压降,通过优化,得到旋流板阻力系数:1.0370.052plate 2248.13 6.0,(1PB Ar u ζρε−∆==−+ (4阻力系数计算值与实验的一致性如图7所示. 从式(4就可得到分离器压降的预测模型:(1.0370.052216.048.13(1.2P B A r u ρε−∆=++ (5 我们开发的气液分离器在齐鲁丙烯腈厂和安庆石化分公司得到工业应用,工业应用标定结果及由式(5计算的结果如表5所示. 对比结果表明用式(5预算的压降与实际一致,预测压降关联式可用于放大设计.表5分离器压降的工业标定结果与计算结果的对比Table 5 Comparison between tested pressure drop and prediction by Eq.(5FactoryD (mm Temp. (o C Mass flow rate (kg/h Test ∆P (Pa Prediction ∆P (Pa η (% Qilu Acrylonitrile factory Anqing branch1520 190086 8246543 949311100 20321031 2023>96 >95Note: P =20 kPa, ε=0.0155.5结论通过对旋流板式气液分离器的模拟实验研究,得到了如下的结论: (1 气液分离器有一最佳的操作范围,最佳空速宜选取在5~9 m/s.100020003000400050006000∆P (P aU (m/s0.40.60.81.01.210203040506070ζp l a t eB1.037Ar-0.052图6 D=340 mm 分离器压降随空速的变化 Fig.6 Change of pressure drop with superficial gasvelocity at D =340 mm图7 不同结构下的旋流板阻力系数Fig.7 Drag coefficient at different swirl vanes5期魏伟胜等:旋流板式气液分离器的放大规律395 (2 旋流板与出气口之间的距离宜选取在 32%~73%D. (3 分离器叶片的仰角和径向角越大或叶片越多都有利于提高分离效率,但压降也随之增加. (4 压降预测模型:∆P = ( 6.0 + 48.13 B 1.037 A r −0.052 1 ρ (1 + ε u 2 的压降预测结果与工业应用标定 2 结果一致,它可用于气液分离器的放大设计. 符号表:Ar B g h K u α 准数, Ar=D3ρ2g/µ2 分离器柱体截面积与叶片的总流通面积之比重力加速度 (m/s2 旋流板与出气口之间的距离 (m 系数分离器的操作空速 (m/s 仰角(o β ε η µ ρ ζ 径向角 (o 气流中液气质量比分离效率 (% 气体粘度 (Pa.s 气体密度 (kg/m3 阻力系数参考文献: [1] [2] [3] [4] [5] [6] 浙江大学化工原理组. 旋流板除雾器 [J]. 化学工程, 1972,1(4: 79–84. 浙江大学化工原理组. 旋流板技术及其应用 [J]. 化学工程, 1978, 7(2: 21–23. 李樟三, 魏伟胜, 邵国华, 等. 丙烯腈装置用气液分离器 [P]. 中国专利: 01221773.5, 2002–01–23. 陈建孟, 谭天恩. 旋流板上流场的 LDA 实验研究 [J]. 化学工程, 1996, 24(3: 59–64. 陈建孟, 谭天恩, 史小农. 旋流塔板上局部处的液滴粒径分布 [J]. 高校化学工程学报, 1995, 9(4: 319–325. 时钧, 汪家鼎, 余国琮, 等. 化学工程手册, 第二版, 上卷 [M]. 北京: 化学工业出版社, 1996. 19–32. Scale-up of Mist Swirl Separators WEI Wei-sheng, FAN Jian-hua, BAO Xiao-jun, SHI Gang (The Key Laboratory of Catalysis, China National Petroleum Co., University of Petroleum, Beijing 102200, China Abstract: Experiments were conducted in three swirl mist separators, with the internal diameters being 340, 480, and 700 mm, respectively. The separators were equipped with 18 sets of swirl vanes. The effects of superficial gas velocity and geometrical parameters, such as the elevation and the radial angle of the swirl vane, vane number, the ratio of separator body height to diameter on mist separation efficiency and pressure drop w tested. Results ere showed that the separation efficiency and pressure drop increased as elevation, radial angle and vane number were increased. An optimal superficial gas velocity exists in the range from 5 to 9 m/s and it decreases slightly with scale-up. The optimal distancebetween the swirl vane and inner exiting tube is 32%~73% of the separator diameter. The mist separator should be designed to make the separation efficiency as high as possible, with the pressure drop less than 2 kPa. The structure of the swirl vane is one of the most important parameters by which pressure drop is determined. A pressure drop correlation was established based on experimental data and theoretic analysis. A scale-up procedure was suggested for the design of industrial mist separators. Pressure drops measured from two industrial scale separators (φ1.52 m and φ1.90 m were found in good agreement with the predicted values, and the separation efficiency of greater than 95% was achieved. Key words: mist separator; swirl vane; separation efficiency; pressure drop。