拉深模设计实例
拉深模具的设计拉深模具的分类及典型结构拉深模按其工序顺序可分...
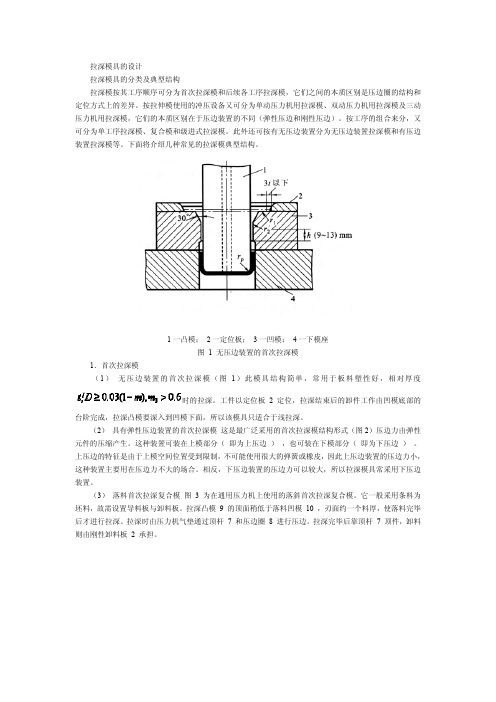
拉深模具的设计拉深模具的分类及典型结构拉深模按其工序顺序可分为首次拉深模和后续各工序拉深模,它们之间的本质区别是压边圈的结构和定位方式上的差异。
按拉伸模使用的冲压设备又可分为单动压力机用拉深模、双动压力机用拉深模及三动压力机用拉深模,它们的本质区别在于压边装置的不同(弹性压边和刚性压边)。
按工序的组合来分,又可分为单工序拉深模、复合模和级进式拉深模。
此外还可按有无压边装置分为无压边装置拉深模和有压边装置拉深模等。
下面将介绍几种常见的拉深模典型结构。
1一凸模;2一定位板;3一凹模;4一下模座图 1 无压边装置的首次拉深模1.首次拉深模(1)无压边装置的首次拉深模(图1)此模具结构简单,常用于板料塑性好,相对厚度时的拉深。
工件以定位板 2 定位,拉深结束后的卸件工作由凹模底部的台阶完成,拉深凸模要深入到凹模下面,所以该模具只适合于浅拉深。
(2)具有弹性压边装置的首次拉深模这是最广泛采用的首次拉深模结构形式(图2)压边力由弹性元件的压缩产生。
这种装置可装在上模部分(即为上压边),也可装在下模部分(即为下压边)。
上压边的特征是由于上模空间位置受到限制,不可能使用很大的弹簧或橡皮,因此上压边装置的压边力小,这种装置主要用在压边力不大的场合。
相反,下压边装置的压边力可以较大,所以拉深模具常采用下压边装置。
(3)落料首次拉深复合模图 3 为在通用压力机上使用的落斜首次拉深复合模。
它一般采用条料为坯料,故需设置导料板与卸料板。
拉深凸模 9 的顶面稍低于落料凹模 10 ,刃面约一个料厚,使落料完毕后才进行拉深。
拉深时由压力机气垫通过顶杆 7 和压边圈 8 进行压边。
拉深完毕后靠顶杆 7 顶件,卸料则由刚性卸料板 2 承担。
1一凸模;2一上模座;3一打料杆;4一推件块;5一凹模;6一定位板;7一压边圈;8一下模座;9一卸料螺钉图 2 有压边装置的首次拉深模(4)双动压力机上使用的首次拉滦模(图4)因双动压力机有两个滑块,其凸模 1 与拉深滑块(内滑块)相连接,而上模座2(上模座上装有压边圈3)与压边滑块(外滑块)相连。
冲裁弯曲拉深设计案例DOC
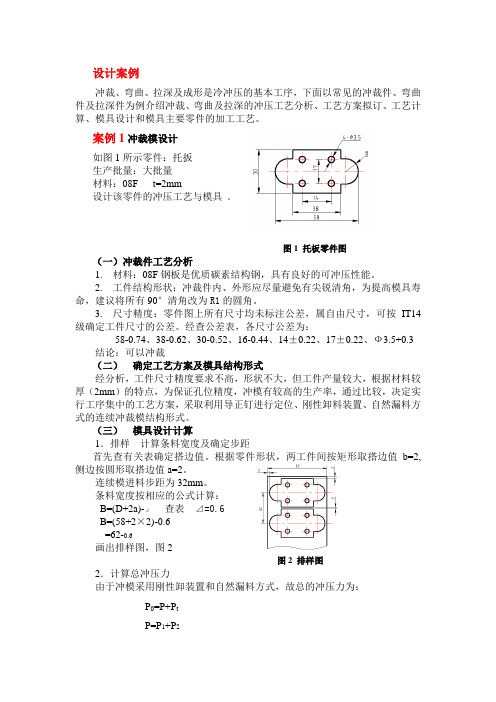
设计案例冲裁、弯曲、拉深及成形是冷冲压的基本工序,下面以常见的冲裁件、弯曲件及拉深件为例介绍冲裁、弯曲及拉深的冲压工艺分析、工艺方案拟订、工艺计算、模具设计和模具主要零件的加工工艺。
案例1冲裁模设计如图1所示零件:托扳生产批量:大批量材料:08F t=2mm设计该零件的冲压工艺与模具。
图1 托板零件图(一)冲裁件工艺分析1. 材料:08F钢板是优质碳素结构钢,具有良好的可冲压性能。
2. 工件结构形状:冲裁件内、外形应尽量避免有尖锐清角,为提高模具寿命,建议将所有90°清角改为R1的圆角。
3. 尺寸精度:零件图上所有尺寸均未标注公差,属自由尺寸,可按IT14级确定工件尺寸的公差。
经查公差表,各尺寸公差为:58-0.74、38-0.62、30-0.52、16-0.44、14±0.22、17±0.22、Ф3.5+0.3 结论:可以冲裁(二)确定工艺方案及模具结构形式经分析,工件尺寸精度要求不高,形状不大,但工件产量较大,根据材料较厚(2mm)的特点,为保证孔位精度,冲模有较高的生产率,通过比较,决定实行工序集中的工艺方案,采取利用导正钉进行定位、刚性卸料装置、自然漏料方式的连续冲裁模结构形式。
(三)模具设计计算1.排样计算条料宽度及确定步距首先查有关表确定搭边值。
根据零件形状,两工件间按矩形取搭边值b=2,侧边按圆形取搭边值a=2。
连续模进料步距为32mm。
条料宽度按相应的公式计算:B=(D+2a)-⊿查表⊿=0.6B=(58+2×2)-0.6=62-0.6画出排样图,图2图2 排样图2.计算总冲压力由于冲模采用刚性卸装置和自然漏料方式,故总的冲压力为:P0=P+P tP=P1+P2而式中 P 1--------落料时的冲裁力P 2--------冲孔时的冲裁力 按推料力公式计算冲裁力:P 1=KL t τ 查τ=300MPa=2.2[2(58-16)+2(30-16)+16π]*2*300/10000 =12.6 (t )P 2=2.2*4π*3.5*2*300/10000 =3.4(t)按推料力公式计算推料力P t :P t =nK t P 取n=3,查表2-10,K t =0.055 P t =3*0.055*(12.6+304)=2.475(t) 计算总冲压力P Z : P Z =P 1+P 2+P t=12.6+3.4+2.475 =18.475(t)3.确定压力中心:根据图3分析,因为工件图形对称,故落料时P 1的压力中心在O 1上;冲孔时P 2的压力中心在O 2上。
拉深模设计与制造实例

拉深模设计与制造实例实例五:拉深模设计与制造实例设计步骤设计内容1(冲压件工艺性分析2(冲压工艺方案的确定3(主要设计计算 (1)毛坯尺寸计算(2)排样及相关计算(3)成形次数的确定(4)冲压工序压力计算(5) 工作部分尺寸计算4(模具总体设计5(主要零部件设计 (1)工作零件的结构设计(2)其它零部件设计6(模具总装图7(冲压设备的选定8(模具零件加工工艺9(模具的装配零件简图:如图所示。
生产批量:大批量材料:镀锌铁皮材料厚度:1mm图1 工件简图 1(冲压件工艺性分析返回该工件属于较典型圆筒形件拉深,形状简单对称,所有尺寸均为自由公差,对工件厚度变化也没有作要求,只是该工件作为另一零件的盖,口部尺寸φ69可稍作小些。
而工件总高度尺寸14mm可在拉深后采用修边达要求。
2(冲压工艺方案的确定返回该工件包括落料、拉深两个基本工序,可有以下三种工艺方案:方案一:先落料,后拉深。
采用单工序模生产。
方案二:落料-拉深复合冲压。
采用复合模生产。
方案三:拉深级进冲压。
采用级进模生产。
方案一模具结构简单,但需两道工序两副模具,生产效率低,难以满足该工件大批量生产的要求。
方案二只需一副模具,生产效率较高,尽管模具结构较方案一复杂,但由于零件的几何形状简单对称,模具制造并不困难。
方案三也只需一副模具,生产效率高,但模具结构比较复杂,送进操作不方便,加之工件尺寸偏大。
通过对上述三种方案的分析比较,该件若能一次拉深,则其冲压生产采用方案二为佳。
3(主要设计计算(1) 毛坯尺寸计算返回根据表面积相等原则,用解析法求该零件的毛坯直径D,具体计算见表7。
(2)排样及相关计算返回采用有废料直排的排样方式,相关计算见表7。
查板材标准,宜选750mm×1000mm的冷轧钢板,每张钢板可剪裁为8张条料(93mm×1000mm),每张条料可冲10个工件,故每张钢板的材料利用率为68%。
(3)成形次数的确定返回该工件底部有一台阶,按阶梯形件的拉深来计算,求出h/dmin=15.2/40=0.38,根据毛坯相对厚度t/D=1/90.5=1.1,查表4.4.3发现h/dmin小于表中数值,能一次拉深成形。
冲压模具设计落料拉深复合模
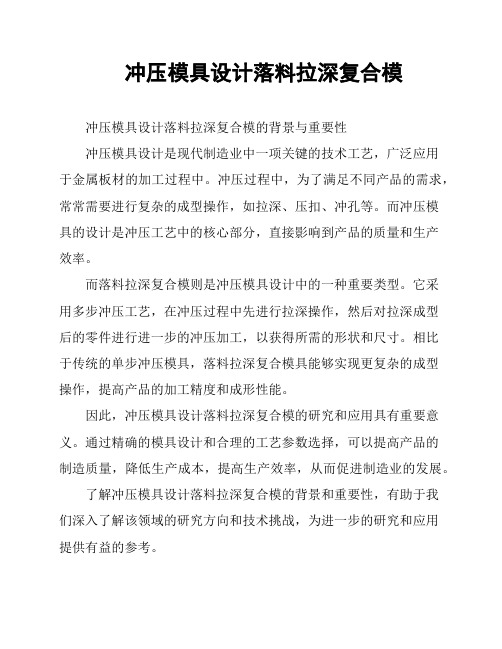
冲压模具设计落料拉深复合模冲压模具设计落料拉深复合模的背景与重要性冲压模具设计是现代制造业中一项关键的技术工艺,广泛应用于金属板材的加工过程中。
冲压过程中,为了满足不同产品的需求,常常需要进行复杂的成型操作,如拉深、压扣、冲孔等。
而冲压模具的设计是冲压工艺中的核心部分,直接影响到产品的质量和生产效率。
而落料拉深复合模则是冲压模具设计中的一种重要类型。
它采用多步冲压工艺,在冲压过程中先进行拉深操作,然后对拉深成型后的零件进行进一步的冲压加工,以获得所需的形状和尺寸。
相比于传统的单步冲压模具,落料拉深复合模具能够实现更复杂的成型操作,提高产品的加工精度和成形性能。
因此,冲压模具设计落料拉深复合模的研究和应用具有重要意义。
通过精确的模具设计和合理的工艺参数选择,可以提高产品的制造质量,降低生产成本,提高生产效率,从而促进制造业的发展。
了解冲压模具设计落料拉深复合模的背景和重要性,有助于我们深入了解该领域的研究方向和技术挑战,为进一步的研究和应用提供有益的参考。
冲压模具设计是指根据工件的形状、尺寸和加工要求,设计出能够完成冲裁、拉深等工艺过程的模具。
冲压模具设计的目标是使模具能够高效、精确地完成工件的加工,提高生产效率和质量。
冲压模具设计的原理是根据工件的形状和尺寸要求,确定模具的结构和工作方式。
冲压模具一般包括上模(上模板、上模座)、下模(下模板、下模座)、顶针、导向柱等部分。
通过上模和下模的配合运动,完成对工件的冲裁、拉深等加工过程。
分析工件:对要加工的工件进行形状、尺寸和材料等方面的分析,确定加工要求。
确定模具结构:根据工件的形状和加工要求,设计出合适的模具结构,包括上模、下模、顶针等部分。
绘制模具图纸:根据模具结构设计,进行模具构造的绘制,绘制各零部件的图纸和总装图纸。
制作模具:根据图纸制作模具的各零部件,并进行装配、调试。
试模与调试:进行模具的试模、调整和修正,保证模具能够正常运行。
批量生产:模具调试通过后,可以进行批量生产工件。
球壳正反拉深复合模设计

头 3 出工件 ,上模 完全抬起 ,一次工作循环结束 。 退
4 .工艺改进方案
将原设 计 方 案 组 合 成 一 套 模 具 ,板 料 宽 度 改 为 5r ,工艺流程 :下料 ( 5m 8m a 宽 8 m,厚 3 m a r )一以弹簧 定 位销定位 ,冲孔 2 以孔 2 一 定位 ,冲第 1 的孔 1 组 和
的拉深模。
-Il 。 “I- I n d ‘| ‘ l ……l 。tt 。P 。 - 。 l ’l _ l - ¨ n ¨i ・ ・ i 。i 。… I 。 i ” ¨ i ¨ 。¨ ’ i
球形结构的曲面零件在拉深开始 时,凸模 与锻件 中 间部分仅在顶点 附近接触 ,由于接触处要承 受全 部拉深
锥度孔后 ,冲孔过程 中产生 的废料 自动落下 ,未再发生
堵塞现象 ,剪切面光亮带 超过 8% 。经 实际使用证 明 , 0 工艺及模具结构均 达到设计要求 ,生产效 率与改进前相 比大幅度提高。改进后成 品形状如图 4 所示 。
接触工件开始 冲孔 ,直到压力 机达到冲孔行程后 ,上模
力 ,将使凸模顶 点附近的材料发生较严 重的变薄 ,凸模
顶点附近的材料 处于双 向受拉 的应力状 态 ,具 有胀形 的 变形特点。另外 ,在拉深过程 中,材料在 凸模 的外缘有 很大 的一部分未被压边圈压住 ,而这部分材料在 由平面
3 模具结构及工作过程 .
该模具工作原理 与普通模具相 同,上模 采用推杆卸 料 ,冲孔废料 由凹模及下模板孔 内落下。为保证加工精 度 ,上下模均为线切割加工 ,在多功能锥度 线切割机 床 上加工锥度落料孔也很方便 。工作 时 , 将工 件放人 凹模
拉深模设计(180柴油机通风口座子)

拉深模设计零件名称:180柴油机通风口座子生产批量:大批量材料:08酸洗钢板零件简图:如图17所示图17通风口座子设计步骤按如下程序进行(一)分析零件的工艺性这是一个不带底的阶梯形零件,其尺寸精度、各处的圆角半径均符合拉深工艺要求。
该零件形状比较简单,可以采用:落料一拉深成二阶形阶梯件和底部冲孔一翻边的方案加工。
但是能否一次翻边达到零件所要求的高度,需要进行计算。
1. 翻边工序计算一次翻边所能达到的高度:按相关表取极限翻边系数K最小=0.68由相应公式计算得:H最大=D/2(1-K最小)+0.43r+0.72δ=56/2(1-0.68)+0.43*8+0.72*1.5=13.48(mm)而零件的第三阶高度H=21.5>H最大=13.48。
由此可知一次翻边不能达到零件高度要求,需要采用拉深成三阶形阶梯件并冲底孔,然后再翻边。
第三阶高度应该为多少,需要几次拉深,还需继续分析计算。
计算冲底孔后的翻边高度h(见图18):取极限翻边系数K最小=0.68拉深凸模圆角半径取r凸=2σ=3mm由相关公式得翻边所能达到的最大高度:h最大=D/2(1-K最小)+0.57r凸=56/2(1-0.68)+0.57*3=10.67(mm)取翻边高度 h=10(mm)计算冲底孔直径d:d=D+1.14r凸-2h=56+1.14×3-2×10=39.42(mm) 图18拉深后翻边实际采用Ф39mm。
计算需用拉深拉出的第三阶高度h´h´=H-h+r凸+δ=21.5-10+3+1.5=16(mm)根据上述分析计算可以画出翻边前需拉深成的半成品图,如图19所示。
2.拉深工序计算图19所示的阶梯形半成品需要几次拉深,各次拉深后的半成品尺寸如何,需进行如下拉深工艺计算。
计算毛坯直径及相对厚度:先作出计算毛坯分析图,如图20所示。
为了计算方便,先按分析图中所示尺寸,根据弯曲毛坯展开长度计算方法求出中性层母线的各段长度并将计算数据列于表6中。
拉深模设计案例
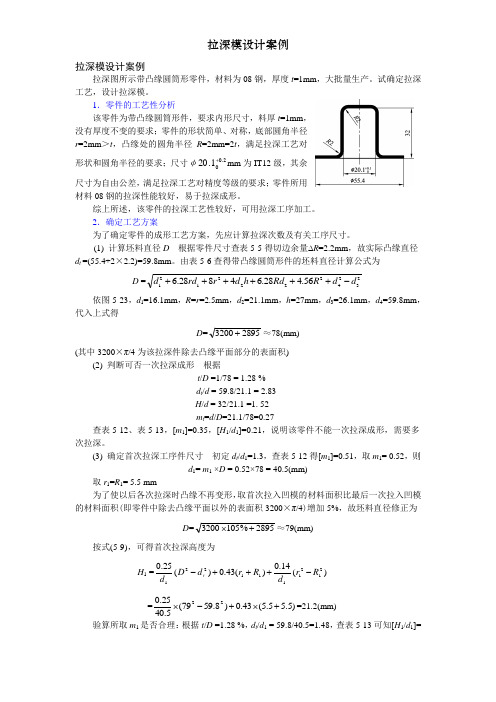
拉深模设计案例拉深图所示带凸缘圆筒形零件,材料为08钢,厚度t =1mm ,大批量生产。
试确定拉深工艺,设计拉深模。
1.零件的工艺性分析该零件为带凸缘圆筒形件,要求内形尺寸,料厚t =1mm ,没有厚度不变的要求;零件的形状简单、对称,底部圆角半径r =2mm >t ,凸缘处的圆角半径R =2mm=2t ,满足拉深工艺对形状和圆角半径的要求;尺寸φ2.001.20+mm 为IT12级,其余尺寸为自由公差,满足拉深工艺对精度等级的要求;零件所用材料08钢的拉深性能较好,易于拉深成形。
综上所述,该零件的拉深工艺性较好,可用拉深工序加工。
2.确定工艺方案为了确定零件的成形工艺方案,先应计算拉深次数及有关工序尺寸。
(1) 计算坯料直径D 根据零件尺寸查表5-5得切边余量∆R =2.2mm ,故实际凸缘直径d t =(55.4+2×2.2)=59.8mm 。
由表5-6查得带凸缘圆筒形件的坯料直径计算公式为D =2324222212156.428.64828.6d d R Rd h d r rd d -++++++依图5-23,d 1=16.1mm ,R =r =2.5mm ,d 2=21.1mm ,h =27mm ,d 3=26.1mm ,d 4=59.8mm ,代入上式得D =28953200+≈78(mm)(其中3200×π/4为该拉深件除去凸缘平面部分的表面积)(2) 判断可否一次拉深成形 根据t /D =1/78 = 1.28 % d t /d = 59.8/21.1 = 2.83 H /d = 32/21.1 =1. 52 m t =d /D =21.1/78=0.27查表5-12、表5-13,[m 1]=0.35,[H 1/d 1]=0.21,说明该零件不能一次拉深成形,需要多次拉深。
(3) 确定首次拉深工序件尺寸 初定d t /d 1=1.3,查表5-12得[m 1]=0.51,取m 1= 0.52,则d 1= m 1 ×D = 0.52×78 = 40.5(mm)取r 1=R 1= 5.5 mm为了使以后各次拉深时凸缘不再变形,取首次拉入凹模的材料面积比最后一次拉入凹模的材料面积(即零件中除去凸缘平面以外的表面积3200×π/4)增加5%,故坯料直径修正为D =2895%1053200+⨯≈79(mm)按式(5-9),可得首次拉深高度为 H 1 =)(14.0)(43.0)(25.02121111221R r d R r d D d t -+++- =)5.55.5(43.0)8.5979(5.4025.022+⨯+-⨯=21.2(mm) 验算所取m 1是否合理:根据t /D =1.28 %,d t /d 1 = 59.8/40.5=1.48,查表5-13可知[H 1/d 1]=0.58。
圆筒拉深模设计.

《塑性成形工艺》课程设计题目:圆筒拉深模设计姓名:灬焚书灬学号:211201182系别:材料工程系专业:材料成型及控制工程年级:2012级指导教师:2015年7月6日目录1 课程设计任务书 (3)2 冲压工艺分析 (3)2.1 结构与尺寸 (3)2.2 精度 (3)2.3 材料 (4)3 冲压工艺方案的确定 (4)4 必要工艺计算 (4)4.1 判断拉深次数 (4)4.1.1 确定零件修边余量 (4)4.1.2 确定坯料尺寸 (5)4.1.3 判断是否采用压边圈 (5)4.1.4 确定拉深次数 (5)4.2 凸模和凹模尺寸计算 (6)4.2.1 拉深模的间隙 (6)4.2.2 拉深模的圆角半径 (6)4.2.3 凸、凹模工作部分的尺寸和公差 (6)4.3 拉深力的计算 (7)4.3.1 拉深力的计算 (7)4.3.2 压力机的公称压力的计算 (8)4.3.3 压力中心的确定 (8)5 主要零件的计算 (9)5.1 凹模的尺寸 (9)5.2 凸模的尺寸 (9)5.3 凸模固定板的尺寸 (10)5.4 垫板的尺寸 (10)5.5 弹性元件的尺寸 (11)5.6 辅助零件与结构的设计 (11)5.6.1 螺钉的选择 (11)5.6.2 销钉的选择 (11)5.7 模架的选择 (11)5.7.1 上、下模座的选择 (11)5.7.2 导柱、导套的选择 (11)5.8 模柄的选择 (12)6 闭合高度的确定 (12)7 压力机设备的选用 (12)参考文献 (14)1 课程设计任务书设计题目:筒形件拉深模具设计工件图:如图1毛坯直径:56mm材料:1060铝合金厚度:1mm技术要求:零件公差按IT14级选取图1 零件尺寸图2 冲压工艺分析2.1 结构与尺寸该零件为无凸缘圆筒类拉深件,形状对称。
工件要求内形尺寸,对厚度变化没有要求。
1060铝合金材料被自由凸模反拉深,工件内圆角半径R为3mm最后按h =18mm进行修边。
- 1、下载文档前请自行甄别文档内容的完整性,平台不提供额外的编辑、内容补充、找答案等附加服务。
- 2、"仅部分预览"的文档,不可在线预览部分如存在完整性等问题,可反馈申请退款(可完整预览的文档不适用该条件!)。
- 3、如文档侵犯您的权益,请联系客服反馈,我们会尽快为您处理(人工客服工作时间:9:00-18:30)。
5.1拉深模设计实例——保护筒拉深模的设计5.1.1设计任务图5-3- 1所示是一金属保护筒,材料为08钢,材料厚度2mm,大批量生产。
要求设计该保护筒的冲压模具。
图5-3- 1 保护筒零件图5.1.2零件工艺性分析1.材料分析08钢为优质碳素结构钢,属于深拉深级别钢,具有良好的拉深成形性能。
2. 结构分析零件为一无凸缘筒形件,结构简单,底部圆角半径为R3,满足筒形拉深件底部圆角半径大于一倍料厚的要求,因此,零件具有良好的结构工艺性。
3. 精度分析零件上尺寸均为未注公差尺寸,普通拉深即可达到零件的精度要求。
5.1.3工艺方案的确定零件的生产包括落料、拉深(需计算确定拉深次数)、切边等工序,为了提高生产效率,可以考虑工序的复合,本例中采用落料与第一次拉深复合,经多次拉深成形后,由机械加工方法切边保证零件高度的生产工艺。
5.1.4 零件工艺计算1.拉深工艺计算零件的材料厚度为2mm ,所以所有计算以中径为准。
(1)确定零件修边余量 零件的相对高度63.230180=-=d h ,经查得修边余量mm h 6=∆,所以,修正后拉深件的总高应为79+6=85mm 。
(2)确定坯料尺寸D由无凸缘筒形拉深件坯料尺寸计算公式得mm105mm 456.043072.1853043056.072.142222≈⨯-⨯⨯-⨯⨯+=---=r dr dh d D (3)判断是否采用压边圈 零件的相对厚度9.11001052100=⨯=⨯D t ,经查压边圈为可用可不用的范围,为了保证零件质量,减少拉深次数,决定采用压边圈。
(4)确定拉深次数查得零件的各次极限拉深系数分别为[ m 1]=0.5,[ m 2]=0.75,[ m 3]=0.78,[ m 4]=0.8。
所以,每次拉深后筒形件的直径分别为mm 5.52mm 1055.0][11=⨯==D m d mm 38.39mm 5.5275.0][122=⨯==d m d mm 72.30mm 38.3978.0][233=⨯==d m d mm 30mm 58.24mm 72.308.0][344<=⨯==d m d由上计算可知共需4次拉深。
(5)确定各工序件直径调整各次拉深系数分别为 53.01=m ,78.02=m ,82.03=m ,则调整后每次拉深所得筒形件的直径为mm 65.55mm 10553.011=⨯==D m d mm 41.43mm 65.5578.0122=⨯==d m dmm 60.35mm 41.4382.0233=⨯==d m d第四次拉深时的实际拉深系数84.060.353034===d d m ,其大于第三次实际拉深系数3m 和第四次极限拉深系数][4m ,所以调整合理。
第四次拉深后筒形件的直径为mm 30φ。
(6)确定各工序件高度根据拉深件圆角半径计算公式,取各次拉深筒形件圆角半径分别为mm 81=r ,mm 5.62=r ,mm 53=r ,mm 44=r ,所以每次拉深后筒形件的高度为mm22.39mm )832.065.55(65.55843.0mm )65.5565.55105(25.0)32.0(43.0)(25.0211111121=⨯+⨯⨯+-⨯=+⨯+-⨯=r d d r d d D hmm57.55mm )5.632.041.43(41.435.643.0mm )41.4341.43105(25.0)32.0(43.0)(25.0222222222=⨯+⨯⨯+-⨯=+⨯+-⨯=r d d r d d D hmm77.70mm )532.060.35(60.35543.0mm )60.3560.35105(25.0)32.0(43.0)(25.0233333323=⨯+⨯⨯+-⨯=+⨯+-⨯=r d d r d d D h第四次拉深后筒形件高度应等于零件要求尺寸,即mm 854=h 。
拉深工序件图如图5-3- 2所示。
图5-3- 2 拉深工序图2.落料拉深复合模工艺计算(1)落料凸、凹模刃口尺寸计算根据零件形状特点,刃口尺寸计算采用分开制造法。
落料尺寸为φ087.0105-,落料凹模刃口尺寸计算如下。
查得该零件冲裁凸、凹模最小间隙mm 246.0m in =Z ,最大间隙mm 360.0m ax =Z ,凸模制造公差mm 025.0T =δ,凹模制造公差mm 035.0A =δ。
将以上各值代入A T δδ+≤m in m ax Z Z -校验是否成立。
经校验,不等式成立,所以可按下式计算工作零件刃口尺寸。
mm565.104mm 87.05.0105)(035.00035.000m ax A A+++=⨯-=-=)(δX ΔD D mm319.104mm )246.0565.104()(0025.00025.00min T T---=-=-=δZ D D A (2)首次拉深凸、凹模尺寸计算第一次拉深件后零件直径为55.65mm ,由公式Kt t Z +=m ax 确定拉深凸、凹模间隙值Z ,查得5.0=K ,所以间隙m m 3m m 25.0m m 2=⨯+=Z ,则首次拉深凹模mm 65.57mm )265.55()(08.0008.0001A +++=+=+=At d D δ。
首次拉深凸模mm 65.51mm )665.57()2(005.0005.00T ---=-=-=T Z D D A δ (3)排样计算零件采用单直排排样方式,查得零件间的搭边值为1.5mm ,零件与条料侧边之间的搭边值为1.8mm ,若模具采用无侧压装置的导料板结构,则条料上零件的步距为106.5mm ,条料的宽度应为mm6.109mm )18.12105()2(07.007.00m ax --∆-=+⨯+=++=c a D B 选用规格为2mm×1000mm×1500mm 的板料,计算裁料方式如下。
裁成宽109.6mm ,长1000mm 的条料,则每张板料所出零件数为1179135.10610006.1091500=⨯=⎥⎦⎤⎢⎣⎡⨯⎥⎦⎤⎢⎣⎡ 裁成宽109.6mm ,长1500mm 的条料,则每张板料所出零件数为1261495.10615006.1091000=⨯=⎥⎦⎤⎢⎣⎡⨯⎥⎦⎤⎢⎣⎡ 经比较,应采用第二种裁法,零件的排样图如图5-3- 3所示。
图5-3- 3 零件排样图(4)力的计算模具为落料拉深复合模,动作顺序是先落料后拉深,现分别计算落料力落F 、拉深力拉F和压边力压F 。
kN 3.274N 4.274310N 320210514.33.1≈=⨯⨯⨯⨯==τKLt F 落 kN8.111N 24.111834N 8.0400265.5514.311≈=⨯⨯⨯⨯==K t d F b σπ拉 kN7.9N 37.9672N 2.2])82265.55(105[4])2[422212≈=⨯⨯++-=++-=ππPr t d D F A (压因为拉深力与压边力的和小于落料力,即落压拉F F F <=+=+KN 5.1217.98.111,所以,应按照落料力的大小选用设备。
初选设备为J23—35。
3.第二次拉深模工艺计算(1)拉深凸、凹模尺寸计算第二次拉深件后零件直径为43.41 mm ,拉深凸、凹模间隙值仍为3mm ,则拉深凸、凹模尺寸分别为mm 41.45mm )241.43()(08.0008.0002A A +++=+=+=δt d Dmm 41.39mm )641.45()2(005.0005.00T T ---=-=-=δZ D D A(2)拉深力计算kN4.65N 55.65427N6.0400241.4322≈=⨯⨯⨯⨯==πσπK t d F b 拉 根据以上力的计算,初选设备位J23—10。
4.第三次拉深模工艺计算计算方法与第二次拉深模工艺计算相同,此处从略。
5.第四次拉深模工艺计算(1)拉深凸、凹模尺寸计算因为零件标注外形尺寸(04.032±)mm ,所以要先计算凹模,即mm 98.31mm )08.075.004.32()75.0(08.0008.000m ax A A +++=⨯-=∆-=δd D拉深凸模mm 58.27mm )4.498.31()2(005.0005.00T T ---=-=-=δZ D D A (2)拉深力计算kN2.45N 45216N 6.04002304≈=⨯⨯⨯⨯==πσπK dt F b 拉 5.1.5 冲压设备的选用1.落料拉深复合模设备的选用根据以上计算,同时考虑拉深件的高度选取开式双柱可倾压力机JH23—40,其主要技术参数如下:公称压力:4000kN 滑块行程:80mm 最大闭合高度:330 mm 闭合高度调节量:65 mm 滑块中心线到床身距离:250mm 工作台尺寸:460 mm ×700 mm 工作台孔尺寸:250 mm ×360 mm 模柄孔尺寸:φ50 mm ×70 mm 垫板厚度:65mm2.第二次拉深模设备的选用考虑零件的高度,选取开式双柱可倾压力机JH23—80,以保证拉深的顺利操作,其主要技术参数如下:公称压力:800kN 滑块行程:130mm 最大闭合高度:380 mm 闭合高度调节量:90mm 滑块中心线到床身距离:290mm 工作台尺寸:540 mm ×800 mm 模柄孔尺寸:φ60mm ×80 mm 垫板厚度:100mm5.1.6 模具零部件结构的确定1.落料拉深复合模零部件设计(1)标准模架的选用标准模架的选用依据为凹模的外形尺寸,所以应首先计算凹模周界的大小。
根据凹模高度和壁厚的计算公式得凹模高度m m 21m m 1052.0=⨯==Kb H 。
凹模壁厚mm 38mm 218.1)2~5.1(≈⨯==H C 。
所以,凹模的外径为m m 181382105=⨯+=D 。
以上计算仅为参考值,由于本套模具为落料拉深复合模,所以凹模高度受拉深件高度的影响必然会有所增加,其具体高度将在绘制装配图时确定。
另外,为了保证凹模有足够的强度,将其外径增大到200mm 。
模具采用后置导柱模架,根据以上计算结果,查得模架规格为:上模座200mm ×200mm ×45mm ,下模座200mm ×200mm ×50mm ,导柱32mm ×190mm ,导套32mm ×105mm ×43mm 。
(2)其它零部件结构拉深凸模将直接由连接件固定在下模座上,凸凹模由凸凹模固定板固定,两者采用过渡配合关系。
模柄采用凸缘式模柄,根据设备上模柄孔尺寸,选用规格为A50×100的模柄。