c=0抽样计划介绍
C=0抽样计划表

“C=0抽样计划”资料AQL 0.010 0.015 0。
025 0。
040 0。
065 0。
10 0.15 0.25 0.40 0。
65 1。
0 1.5 2。
5 4。
0 6。
5 10。
0 批量样本2—8 **** *** ***** 5 3 2 2 9-15 * *** * ** * ** 13 8 5 3 2 2 16—25 ******* **20 13 8 5 3 2 2 26-50 * **** ** * 32 20 13 8 5 5 5 3 51—90 **** **80 50 32 20 13 8 7 6 5 4 91-150 *** * *125 80 50 32 20 13 12 11 7 6 5 151—280 * ***200 125 80 50 32 20 20 19 13 10 7 6 281-500 ** *315 200 125 80 50 48 47 29 21 16 11 9 7 501—1200 *800 500 315 200 125 80 75 73 47 34 27 19 15 11 8 1201-3200 1250 800 500 315 200 125 120 116 73 53 42 35 23 18 13 9 3201—10000 1250 800 500 315 200 192 189 116 86 68 50 38 29 22 15 9 10001—35000 1250 800 500 315 300 294 189 135 108 77 60 46 35 29 15 9 35001-150000 1250 800 500 490 476 294 218 170 123 96 74 56 40 29 15 9 150001—500000 1250 800 750 715 476 345 270 200 156 119 90 64 40 29 15 9 500000and over 1250 1200 1112 715 556 435 303 244 189 143 102 64 40 29 15 9零缺陷抽样(C=0)使用的理解(C=0抽样计划不是国标、国际标准)国际标准, 国标, 缺陷零缺陷抽样(C=0)使用的理解(C=0抽样计划不是国标、国际标准)1)是以105E为基础,把抽样数减少,只是缺点数为“0",AQL值同样有从0。
C=0抽样方案

和抽样有关的几个分布
• 二项分布:二项分布是n个独立的是/非试验中成功的次数 的概率分布,其中每次试验的成功概率一样。(二项分布 的计算方式如何推导?)
• 超几何分布:由有限个物件中抽出n个物件,成功抽出指 定种类的物件的次数(不归还)。前述案例中已给出超几 何分布计算的案例。
• 泊松分布:当二项分布的n很大而p很小时,泊松分布可作
为二项分布的近似。事实上,泊松分布是由二项分布导出
的。
– 概率密度 – 累积概率
f
(
x
)
(
np
)
x
e
np
x!
r
F (x) f (x)
x0
OC曲线
• 案例:有N=10000个产品, 不良率为P,我们抽取n=100 个,1收2退。分别计算 P=1%,2%,3%时的接收概率 Pa
– 根据泊松分布,Pa分别为:
13
3201-10000 1250 800 500 315 200 192 189 116 86 68 50 38 29 22 15
10001-35000 1250 800 500 315 300 294 189 135 108 77 60 46 35 29 15
35001-150000 1250 800 500 490 476 294 218 170 123 96 74 56 40 29 15
*
*
* 315 200 125 80 50 48 47 29 21 16 11
9
501-1200
* 800 500 315 200 125 80 75 73 47 34 27 19 15 11
1201-3200
1250 800 500 315 200 125 120 116 73
C=0抽样方案
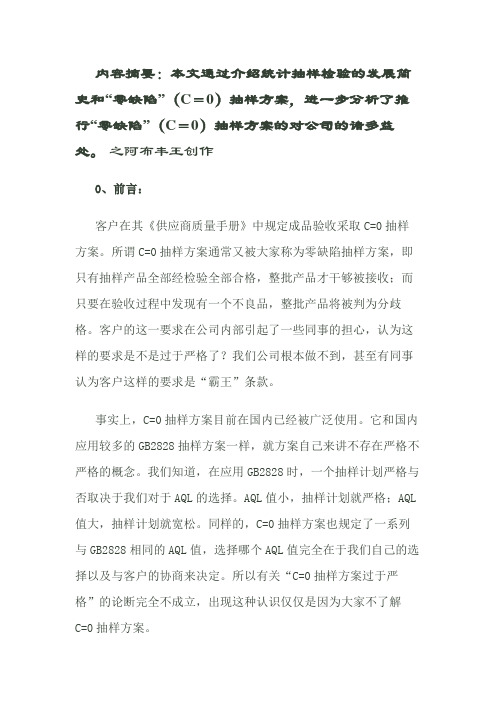
内容摘要:本文通过介绍统计抽样检验的发展简史和“零缺陷”(C=0)抽样方案,进一步分析了推行“零缺陷”(C=0)抽样方案的对公司的诸多益处。
之阿布丰王创作0、前言:客户在其《供应商质量手册》中规定成品验收采取C=0抽样方案。
所谓C=0抽样方案通常又被大家称为零缺陷抽样方案,即只有抽样产品全部经检验全部合格,整批产品才干够被接收;而只要在验收过程中发现有一个不良品,整批产品将被判为分歧格。
客户的这一要求在公司内部引起了一些同事的担心,认为这样的要求是不是过于严格了?我们公司根本做不到,甚至有同事认为客户这样的要求是“霸王”条款。
事实上,C=0抽样方案目前在国内已经被广泛使用。
它和国内应用较多的GB2828抽样方案一样,就方案自己来讲不存在严格不严格的概念。
我们知道,在应用GB2828时,一个抽样计划严格与否取决于我们对于AQL的选择。
AQL值小,抽样计划就严格;AQL 值大,抽样计划就宽松。
同样的,C=0抽样方案也规定了一系列与GB2828相同的AQL值,选择哪个AQL值完全在于我们自己的选择以及与客户的协商来决定。
所以有关“C=0抽样方案过于严格”的论断完全不成立,出现这种认识仅仅是因为大家不了解C=0抽样方案。
需要说明的是,该客户的《供应商质量手册》是根据ISO/TS16949(即GB/T18305)建立的,而ISO/TS16949在7.1.2 条款中明确要求接收水平必须是零缺陷。
(ISO/TS16949 7.1.2接收准则:组织应规定接收准则,要求时,由顾客批准。
对于计数型数据抽样,接收水平应是零缺陷。
)所以,客户的要求是根据的,不存在任何“霸王”要求。
1、抽样检验简介抽样检验又称为统计抽检检验,是指从交验的一批产品中,随机抽取若干单位产品组成样本进行检验,通过对样本的检验结果对整批产品做出质量判定的过程。
我们知道,检验是不发生价值的工作,因此如何更经济、快捷的进行检验就直接关系到生产的成本和效率。
零缺陷(C=0)抽样方案

零缺陷概念的产生:被誉为“全球质量管理大师”、“零缺陷之父”和“伟大的管理思想家”的菲利浦·克劳士比(Philip B. Crosby)在20世纪60年代初提出“零缺陷”思想,并在美国推行零缺陷运动。
后来,零缺陷的思想传至日本,在日本制造业中得到了全面推广,使日本制造业的产品质量得到迅速提高,并且领先于世界水平,继而进一步扩大到工商业所有领域。
零缺陷理论核心是:“第一次就把事情做对”。
所谓"零缺陷"抽样方案,简单的说,就是不管你的批量和样本大小如何,其抽样检验的接收数Ac=0,即"0收1退"。
举例:某客户在其《供应商质量手册》中规定成品验收采用 C=0 抽样方案。
所谓 C=0 抽样方案通常又被大家称为零缺陷抽样方案,即只有抽样产品全部经检验全部合格,整批产品才能够被接收;而只要在验收过程中发现有一个不良品,整批产品将被判为不合格。
客户的这一要求在公司内部引起了一些同事的担心,认为这样的要求是不是过于严格了?公司根本做不到,甚至有同事认为客户这样的要求是“霸王”条款。
事实上,C=0 抽样方案目前在国内已经被广泛使用。
它和我们中国应用较多的GB/T2828.1-2012抽样方案一样,就方案本身来讲不存在严格不严格的概念。
在应用GB/T2828.1-2012时,一个抽样计划严格与否取决于我们对于 AQL 的选择。
AQL 值小,抽样计划就严格;AQL 值大,抽样计划就宽松。
同样的,C=0 抽样方案也规定了一系列与GB/T2828.1-2012 相同的 AQL值,选择哪个AQL 值完全在于我们自己的选择以及与客户的协商来决定。
所以有关“C=0 抽样方案过于严格”的论断完全不成立,出现这种认识仅仅是因为大家不了解C=0 抽样方案。
需要说明的是,该客户的《供应商质量手册》是根据IATF16949:2016 建立的,而IATF16949 :2016标准条款8.6.6中明确要求接收水平必须是零缺陷。
C=0抽样计划表Word版

“C=0抽样计划”资料AQL 0.010 0.015 0.025 0.040 0.065 0.10 0.15 0.25 0.40 0.65 1.0 1.5 2.5 4.0 6.5 10.0 批量样本2-8 * * * * * * * * * * * * 5 3 2 2 9-15 * * * * * * * * * * 13 8 5 3 2 2 16-25 * * * * * * * * * 20 13 8 5 3 2 2 26-50 * * * * * * * * 32 20 13 8 5 5 5 3 51-90 * * * * * * 80 50 32 20 13 8 7 6 5 4 91-150 * * * * * 125 80 50 32 20 13 12 11 7 6 5 151-280 * * * * 200 125 80 50 32 20 20 19 13 10 7 6 281-500 * * * 315 200 125 80 50 48 47 29 21 16 11 9 7 501-1200 * 800 500 315 200 125 80 75 73 47 34 27 19 15 11 8 1201-3200 1250 800 500 315 200 125 120 116 73 53 42 35 23 18 13 9 3201-10000 1250 800 500 315 200 192 189 116 86 68 50 38 29 22 15 9 10001-35000 1250 800 500 315 300 294 189 135 108 77 60 46 35 29 15 9 35001-150000 1250 800 500 490 476 294 218 170 123 96 74 56 40 29 15 9 150001-500000 1250 800 750 715 476 345 270 200 156 119 90 64 40 29 15 9 500000and over 1250 1200 1112 715 556 435 303 244 189 143 102 64 40 29 15 9零缺陷抽样(C=0)使用的理解(C=0抽样计划不是国标、国际标准)国际标准, 国标, 缺陷零缺陷抽样(C=0)使用的理解(C=0抽样计划不是国标、国际标准)1)是以105E为基础,把抽样数减少,只是缺点数为“0”,AQL值同样有从0.01-10;2)不存在加严、多次抽样等;3)只能用于静态的抽样,如IQC\FQC\OQC等,IPQC不适用;4)对IQC来说,对供应商要求高,但IQC的作业量减少;5)对产品检验过程中,只要有一个缺点在,即可判定,基本上不用全检完,有利于客户方;6)对供应商的品质逐渐提高和改善是不利的,往往一锤子打死;7)定义A\B\C(严重缺点(注意:C=0)、主要缺点、次要缺定)的定义要慎重,否则实际现场作业面复杂性提高,操作尴尬;8)用C=0抽样表,一般用起来不考虑它是从哪里来的,实际上与105E是“亲属”关系;9)有的公司为了避免说不清楚,干脆将C=0与105E合为一张比较表,谁问一看有出处;此表如同105E抽样计划表一样留在手边随查;10)C=0抽样计划用以来较为简单,网站有些帖子讨论的C=0复杂了,我的经验是一定要读懂105E的抽样的基本概念和其抽样技术,否则对C=0理解会偏掉;11)参考资料:《品质管理实战指南》张智勇编著,《国内企业外常用抽样技术和测量技术》陈晋美主编。
C=0-抽样方案介绍

C=0-抽样方案介绍1965年,零缺陷抽样检验方案(c=0)首次发表在国际刊物上,虽然零缺陷抽样检验方案目前还是不是国际和国家标准。
但由于“零缺陷”的品质理念已经深入人心,在加上ISO/TS16949:2002中有明确的条文要求。
所以欧美很多的企业,特别是汽车供应链相关企业普遍采用的都是零缺陷抽样检验方案。
零缺陷抽样检验方案简单的说,就是不管你的批量和样本大小如何,其抽样检验的接收数Ac=0,即“0收1退”。
在抽样检验过程中,一旦发现一个缺陷或不合格,就要实施100%的全检或退货处置。
零缺陷抽样检验方案的优点就是不存在加严、放宽与正常检验之间的转移规定。
在ISO/TS16949:2002里面的7.1.2条款里面有明确规定“7.1.2接收准则必须由组织定义,要求时,必须由顾客批准。
对于计数型数据抽样,接收水平必须是零缺陷”。
标准条文明确规定的,也就是我们要恪守的。
其实我们也一直在实用C=O的抽样检验方案。
但对其认识上可能存在一定的误区。
导致其真正的效率发挥的不够充分。
所以希望通过本文,能起抛砖引玉作用,为公司后续检验和试验活动更加顺畅的开展起到积极作用。
首先,零缺陷抽样检验方案的准则就是我们通常说的C=0,0收1退。
但其要和GB/T2828.1-2003按接收质量限(AQL)检索逐批检验抽样计划结合使用,要使用GB/T2828.1来确定其“零缺陷抽样检验方案”的样本大小。
按我们以前的经验,采用GB/T2828.1的时候,首先是确定批量大小、确定检验水平、那么它的样本大小就确定,再定义我们的接收质量限(AQL)就可以得出我们的接收准则,而现在采用零缺陷抽样检验方案的接收准则是已知的,意味着AQL值在零缺陷抽样检验方案中就失去了作用。
这就是我们认识上的一个明显误区。
试想,如果采用零缺陷抽样检验方案与AQL值无关的话,那么假设采用GB/T2828.1里面的正常检验一次抽样方案II级检验水平的话,意味着样本量是统一的。
C=0抽样方案

抽样检的缺点
抽样检验也有如下一些固有缺点: 1、存在接受“劣质”批和拒收“优质”批
的风险。 2、增加了计划工作和文件编集工作。 3、样组所提供的产品情报一般而言较之于
全检要少。
抽样方案所规定的假定
抽样方案通常都被假定为
(实践中,这些假定并不完全靠得住) 1、检验员是按照指定的抽样方案进行工作的。 2、所做的检验是没有误差的,即在测量或鉴定产品
强的预防性 寻因性检验:在产品的设计阶段,通过充分的预测,寻找
潜在不合格的原因
2、统计抽样检验基本概念
检验分类(按检验目的):
生产检验 验收检验 监督检验 验证检验 仲裁检验
检验分类(按检验后样品状况):
非破坏性检验 破坏性检验
2、统计抽样检验基本概念
检验分类(按质量特性数据性质):
C=0零缺陷抽样计划 培训教材
制作:周亮 日期:2016-4-22
目录
一、抽样检验基础知识 二、C=0 Sampling Plan 三、MIL-STD-105E抽样与C=0抽样比 四、C=0抽样表 五、C=0抽样案例
1、统计抽样的由来与发展
1965年,美国的一位大学教授尼古拉斯•斯托格力亚发表 C=0抽样方案,几经改版,目前最新的版本为第四版。 C=0抽样方案是根据MIL-STD105 修改而成,接收准则限 定为“0收1退”,因而又被人们称为“零缺陷”抽样方案。
2、统计抽样检验基本概念
检验分类(按检验数量):
全数检验:对每个产品进行评判,接收的全是合格品, 拒绝的是少量不合格品。
抽样检验:根据对部分产品的检验结果,对一批产品做 出判断,接收的产品中可能有不合格品,拒绝的是整批 产品 (统计抽样检验、非统计抽样检验)
c=0抽样计划表优点

c=0抽样计划表优点
c=0抽样计划是一种统计抽样方法,其优点包括:
1. 明确确定了样本数量,简单易懂,易于实施和理解。
2. 具有一定的可靠性和精度,样本的代表性较高。
3. 可以有效地控制抽样误差,减小统计结果的误差。
4. 对于样本错误或不合格的数据可以很快地做出判断和处理。
5. 节约了人力、物力和时间资源,降低了统计成本,提高了效率。
6. 适用于从大样本中抽取中小样本的情况,且不需要考虑每个样本的特征或属性,适用于大多数普查、统计调查等。
总之,c=0抽样计划是一种常用的、简单有效的抽样方法,具有一定的优点和适用性。
- 1、下载文档前请自行甄别文档内容的完整性,平台不提供额外的编辑、内容补充、找答案等附加服务。
- 2、"仅部分预览"的文档,不可在线预览部分如存在完整性等问题,可反馈申请退款(可完整预览的文档不适用该条件!)。
- 3、如文档侵犯您的权益,请联系客服反馈,我们会尽快为您处理(人工客服工作时间:9:00-18:30)。
期望是生产的产品完全达到规范要求。
•
对一些非关键的特性希望用比较少的检验。
• 对所有零件的所有特性的 100%检验无法实施时。 •
问题纠正前的临时检验。
•
不同原因的审核:
库存产品的确认审核 对潜在的搬运损坏项目的审核 供应商业绩验证。
•
正常的外观检验。 零缺陷使用注意事项:
•
没有检验水平的设定;
•
没有正常、加严、放宽的区分;
•
只有正常的表格使用;
•
对消费者的保证比较大;
• 对生产者的风险比较高。
•
根据 105E 进行修改,目前已是第四版。
C=0 抽样计划和 105E 抽样计划的关系
AQL
样本数
Ac
STD-105E
1.0%
125
3
4.0%
125
10
AQL
样本数
Ac
C=0 PLAN
1.0%
42
0
4.0%
18
0
零缺陷抽样计划的原理
•
直接利用 MIL-STD-105E 修改而成;
• 表中的 ASSOCIATED A.Q.L 是一个索引值; •
运用该抽样计划可能增加判退的批数;
•
零缺陷的另外考虑:
– 如果你的质量相当差,大于 0 的允收数并没有多大的帮助; –
当你的抽样计划允收数大于零,你在授权你的检验人员接受一些可能没有用的产品;
–
零缺陷强制对任何不合格采取措施;
–
如果你正在努力迈向零缺陷,那你怎能容许你的抽样计划允许有缺陷数呢? C=0 抽样计划适用于:
零缺陷抽样计划(C=0 Single Sampling Plans)
•
零缺陷计划是由 Nicholas L. Squeglia 所开发的。
•
它和 MIL-STD-105E 相比可以以较少检验数而能提供相同或较高的消费者保障。
•
除了经济优点外,它还易于使用及管理。
•
起初是用在军方产品,后来更广泛应用于许多工业上计数型的抽样,特別强调在零缺陷的输出。