冷拔管常见缺陷、产生原因及预防和消除方法
冷拔钢管产品缺陷一览表
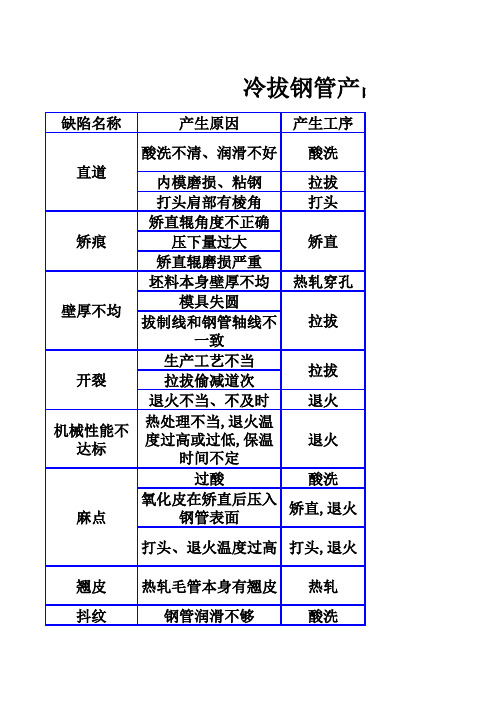
冷拔钢管产品缺缺陷名称
产生原因产生工序酸洗不清、润滑不好酸洗内模磨损、粘钢拉拔
打头肩部有棱角打头
矫直辊角度不正确
压下量过大
矫直辊磨损严重
坯料本身壁厚不均热轧穿孔
模具失圆拔制线和钢管轴线不
一致
生产工艺不当拉拔偷减道次
退火不当、不及时退火机械性能不达标热处理不当,退火温度过高或过低,保温时间不定
退火过酸酸洗
氧化皮在矫直后压入钢管表面
矫直,退火打头、退火温度过高打头,退火翘皮
热轧毛管本身有翘皮热轧抖纹钢管润滑不够酸洗
直道矫痕壁厚不均开裂麻点矫直拉拔拉拔
配模错误模具磨损严重老头管
管头尾切不净切管切管工责任心不够切管拉车衬内模过后拉拔
成品长度达
不到要求拉拔尺寸超差
产品缺陷一览表
预防措施及解决方法备注加强酸洗管理,保证酸洗质量
经常检查模具,及时更换
打头时要保证肩部圆滑
认真调整矫直机,经常检查、修磨辊面
严格按工艺要求控制壁厚
经常检查模具,及时更换
调整拔管机
合理安排工艺,严格按工艺生产
严格执行热处理工艺制度
严格执行热处理工艺制度
控制酸洗温度和时间
减少氧化铁皮的厚度
控制打头退火温度,不得过烧
投料时加强检查,及时修磨
掌握好酸洗磷化皂化时间和成分调整
加强责任心,认真检查模具,及时更换
加强切管工的责任心
加强切管工的责任心,提高自身的水平
保证衬芯到位。
冷拔轴承钢管生产质量缺陷分析与预防

第14卷第3期重庆科技学院学报(自然科学版)2012年6月收稿日期:2011-11-07基金项目:重庆科技学院横向科研项目(1911-003)作者简介:任蜀焱(1973-),男,四川南部人,硕士,讲师,研究方向为材料加工。
采用管坯+加热+二辊斜轧穿孔+控冷+球化+多道次冷拔生产GCr15轴承钢管,常常会出现内外裂纹、离层、内折、外折、壁厚不均、不圆度过大、尺寸偏差过大、球化组织不合格、矫凹等缺陷。
依据钢管质量检验标准做好缺陷的预防工作,是提高冷拔轴承管质量和经济效益的关键。
1冷拔轴承管生产过程缺陷分析1.1圆管坯加热缺陷分析圆管坯加热要防止加热不均、过热、过烧、黑头、白头等缺陷。
如果测温设备不准确,操作工控温不严,造成钢温过高引起过热或过烧,排料长短不齐引起白头,均会使管坯塑性降低,出现穿孔破裂。
煤气质量差、二次风调节不当,产生炉气负压,引起炉门吸入冷空气圆钢黑头或表面严重氧化。
翻钢不及时、出钢过早,受料槽待穿时间过长产生阴阳面。
炉子加热能力小于穿孔能力,保温时间不足,穿孔过程管坯中心温度远低于表面温度时(硬心钢)都会造成穿孔毛管偏心、表面麻毛、内翘皮、离层等缺陷。
1.2穿孔缺陷分析穿孔要防止毛管出现裂纹、内折、外折、离层和壁厚不均等缺陷。
管坯在穿孔过程中受交变切应力和拉应力作用,管坯在接触顶头前,如果中心部分的金属在应力的作用下有微小的疏松,可以减小穿孔时的能量消耗,使穿孔过程易于进行。
但是,如果顶头前伸量不足,顶头前压下量过大,管坯中心产生了严重开裂形成了孔洞,则内表面金属被氧化,在继续穿孔变形中不能被焊合而造成裂纹及内折缺陷[1]。
穿孔过程管坯离层形成因素:除管坯加热温度过高外,斜轧穿孔使内外表面层金属沿横向产生附加剪切变形。
在穿孔准备区,外层金属沿横向流动的速度大于内层,使金属纤维歪扭。
在穿孔区,毛管外表面和内表面层金属有较大的变形,故其切向流动速度大于过渡层,使金属纤维弯曲成C 形。
减壁量越大,则弯曲程度越大,金属切向流动速度不一致引起各层金属间相互的附加横向剪切变形。
冷拔过程中常见问题

1、折迭:拔制后,钢管内外表面呈现直线或螺旋方向的折迭,局部或通长的出现在钢管上。
产生的原因:管料表面有折迭或平杂物,有严重擦伤和裂纹,管料磨修处有棱角或深宽比(H/b)不够。
预防和消除方法:严格按照规程要求对管料进行修磨。
不合格管料不投产,防患于未然。
严格把好穿孔热序的质量关。
2、尺寸超差(包括壁厚超差,壁厚不均,直径超差,椭圆)直径超过了标准的偏差范围,在同一截面上管壁一边薄,厚,直径不等,长短轴之差超出标准规定。
产生的原因:1、拔制模具选择不光,或蕊棒(内模)调整不当。
2、拔模内模设计制造不合理或磨损严重,或硬度不够造成变形磨损。
3、热处理时间长,温度高。
或热处理性能不均匀。
4、空拔时增减壁的规律控制不当,拔制表编制不合理。
5、钢管矫直时被压扁,工卡量具未校零,误差大。
预防和消除方法:1、正确设计制造和选配拔管模具。
2、正确执行热处理制度,均匀加热。
3、正确调整矫直机,经常校对拔管机各部件位置和量具。
4、正确合理编制拔制表,掌握不同钢种、不同规格钢管的增减壁规律。
5、椭圆度不出格,判为合格品,椭圆度出格可重新矫直,局部椭圆度出格可切除。
3、划道:钢管表面上呈现纵向直线形的划痕称为划道。
划道长短不一,宽穿窄不等,多为沟状,可见沟底。
产生的原因:1、拔模内表不光滑,有裂纹或结金属。
2、锤头过渡部分有棱角,磨损工具。
3欠酸洗或毛管上残存氧化铁皮。
4、在涂润滑油时,磷化、皂化工序操作不当。
5、内外模已损伤或磨损严重。
6、中间退火不均,变形量不足。
预防和消除方法:1、提高拔管模具的表面质量。
2、氧化皮要酸洗,冲洗干净,涂层要均匀牢固。
3、锤头过渡部分要圆滑无棱角。
4、勤检查模具和钢管表面,发现问题及时处理。
4、抖纹:钢管表面沿长度方向呈高低不平的环形波浪或波浪逐个相同排列,局部的或通长的出现在钢管内外表面上。
产生的原因:1、热处理后的性能不均,润滑不良,皂化不均。
3、蕊杆细,拔制时蕊杆产生弹性变形引起抖动。
冷拔管常见缺陷产生原因及预防和消除方法

[选取日期]冷拔无缝钢管常见的缺陷特征产生的原因及预防和消除方法2010年10月08日孟相欣冷拔无缝钢管常见的缺陷特征产生的原因及预防和消除方法一、折迭拔制后,钢管内外表面呈现直线或螺旋方向的折迭,局部或通长的出现在钢管上。
产生的原因:管料表面有折迭或夹杂物,有严重擦伤和裂纹,管料磨修处有棱角或深宽比(H/b)不够。
预防和消除方法:严格把好穿孔热轧质量关。
二、尺寸超差(包括壁厚超差,壁厚不均,直径超差,椭圆偏心)直径超过了标准的偏差,在同一截面上管壁一边薄,一边厚,直径不等,长短轴之差超出标准规定。
产生的原因:1、拔制模具选择不当,或芯棒(内模)调整不当。
2、内外模设计制造不合理或磨损严重,或硬度不够造成变形磨损。
3、热处理时间长,温度高,或热处理性能不均匀。
4、增减壁的规律控制不当。
5、拔制表编制不合格。
6、钢管矫直时被压扁,造成误差较大。
预防和消除方法:1、正确设计和选配拔管模具。
2、正确执行热处理制度,均匀加热。
3、正确调制矫直机,经常校对拔管机各部件和量具。
4、掌握不同钢种、不同规格钢管的增减壁规律。
5、正确合理编制拔制表。
6、椭圆度出格可重新矫直,局部椭圆度出格可切除。
三、划道钢管表面上呈现纵向直线的划痕称为划道,划道长短不一,宽窄不等,多为沟状,可见沟底。
产生的原因:1、拔模表面不光滑,有裂纹或粘结金属。
2、锤头过度部分有棱角,工具磨损。
3、欠酸洗或毛管上残存氧化铁皮。
4、磷化、皂化工序操作不当。
5、内外模以损坏或磨损严重。
6、中间退火不均,变形量不足。
预防和消除方法:1、提高拔管模具的表面质量。
2、钢管酸洗后,氧化铁皮要冲洗干净。
3、锤头过度部分要圆滑无棱角。
4勤检查模具和钢管的表面,发现问题及时处理。
四、斗纹钢管表面沿长度方向呈高低不平的环形波浪或波浪逐个相同排列,局部或通长出现在钢管内外表面上。
产生的原因:1、热处理后的性能不均,热轧时低温钢造成性能不均。
2、酸洗后冲洗不干净,磷化不良导致皂化不均。
冷拔质量缺陷与解决办法

冷拔质量缺陷与解决办法冷拔质量缺陷与解决办法划道和擦伤:划道和擦伤缺陷的特征是,在钢管的内外表面上呈现纵向宜线形的长短不一的划痕,多为沟状,但也可能是凸起的条纹。
产生划道和擦伤的主要原因是:在管料上有内划道在拔制时未能消除,钢管上残留着氧化铁皮,模具粘钢,模具强度和硬度不够或不均,模具出现碎裂和磨损,锤头不良,锤头过渡部分的尖锐梭角损伤了模具等。
为了防止产生划道和擦伤应该提高拔制前各准备工序的质量和使用强度及硬度高、光洁度好的模具1.表面铸造缺陷1 拉伤(1)特征:①沿开模方向铸件表面呈线条状的拉伤痕迹,有一定深度,严重时为整面拉伤;②金属与模具表面粘和,导致铸件表面缺料。
(2)产生原因:①模具型腔表面有损伤;②出模方向无斜度或斜度过小;③顶出不平衡;④模具松动:(3)处理方法:①修理模具表面损伤;(修理后光洁度一定要好)②修正斜度,提高模具表面光洁度;③调整顶杆,使顶出力平衡;④紧固模具;2.锤头原因;(1)产生原因:毛管上残存氧化皮(2)处理方法:锤头过度部分要圆滑无棱角。
2.打头不足原因:要求对φ60的无缝钢管进行打头时的推进翻转设计,要求要有动力系统有关参数选择和相关计算以及结构参数设计计算,才能减少缺陷,保持正常生产工艺。
3、冷拔钢管退火:常见的退火工艺有:再结晶退火,去应力退火,球化退火,完全退火等。
退火的目的:主要是降低金属材料的硬度,提高塑性,以利切削加工或压力加工,减少残余应力,提高组织和成分的均匀化,或为后道热处理作好组织准备等。
拔断出现拔断的主要原因是:中间退火不均,变形量不足。
润滑的质量不好,锤头不合乎要求,在锤头前的加热时产生了过热或过烧。
冷拔钢管的主要缺陷

冷拔钢管的主要缺陷、产生原因和消除办法1.折叠存在于钢管的外表面或内表面,呈直线或螺旋状、连续的或不连续的。
产生折叠的主要原因是管料质量不好,本身存在折叠,或者表面有夹杂、严重的刮伤和裂缝,在修磨处有棱角,拔制后经延伸而出现折叠。
为了避免折叠的产生,应提高管料质量并注意检查和修磨。
2.裂缝(包括裂纹、发纹)指钢管内外表面上呈直线或螺旋线分布的细小裂纹,深度在1毫米或1毫米以上,有连续的和不连续的。
产生的原因是:热轧管坯有皮下气泡和皮下夹杂物,拔制前钢管上有裂纹或较深的麻点,在热轧时或冷拔各工序操作中产生了纵向划道或擦伤。
防止裂纹的形成也在于提高管料质量,加强管料的检查和修磨。
同时应避免管子在冷拔生产过程中产生麻点、划道和擦伤。
3.凹坑即分布在钢管表面上的面积不一的局部凹陷,分布有的呈周期性,有的无规律。
凹坑的产生是由于氧化铁皮或其它质硬的污物在拔制或矫直过程中压入了钢管表面,或者是原来存在于钢管表面的翘皮剥落。
防止出现凹坑的措施是仔细地检查管料并去除翘皮等缺陷,保持工作场地、工具和润滑剂等的清洁,防止氧化铁皮和污物落到钢管表面。
4.直径超差造成直径超差的主要原因是配模不当或者忽视了拔管模具尺寸由于磨损而引起的变化。
矫直过程中矫直辊压下量过大也会造成钢管的直径变小。
5.壁厚超差造成壁厚超差的主要原因是配模不当,或者忽视了模具尺寸由于磨损而引起的变化,对定壁后空拔道次中的壁厚变化量估计不正确,使用弧形外模和锥形芯棒进行短芯棒拔制时芯棒位置调整不当——过前或过后。
为了防止壁厚超差,应正确配模、正确调整芯棒位置。
空拔道次中钢管的壁厚变化应估算准确。
6.椭圆即钢管的横截面呈椭圆形。
在拔制过程中使用了模孔是椭圆形的拔管模或者在矫直时钢管两端弯曲过大,在矫直过程中上下窜动、钢管外径过大推入时卡住、钢管尾部甩动过大以及各对矫直辊之间压下量分配不均等均会产生这种缺陷。
如果由于模孔椭圆而产生缺陷应更换管模。
若椭圆是在矫直过程中形成的,应消除矫直时造成椭圆的有关原因。
冷拔钢管表面质量缺陷
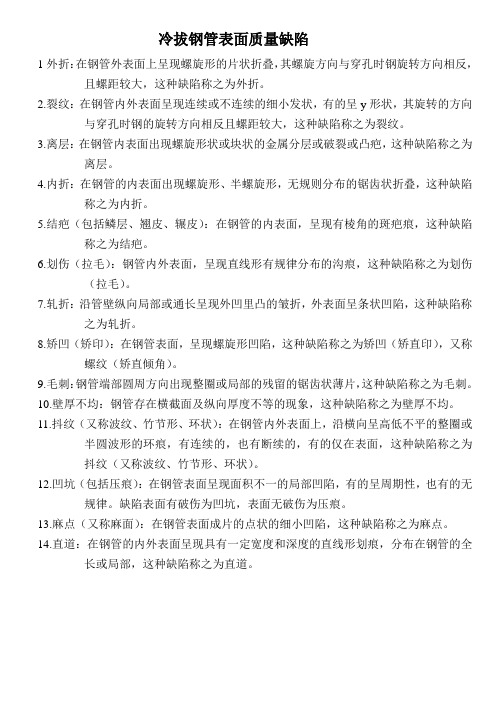
冷拔钢管表面质量缺陷1外折:在钢管外表面上呈现螺旋形的片状折叠,其螺旋方向与穿孔时钢旋转方向相反,且螺距较大,这种缺陷称之为外折。
2.裂纹:在钢管内外表面呈现连续或不连续的细小发状,有的呈y形状,其旋转的方向与穿孔时钢的旋转方向相反且螺距较大,这种缺陷称之为裂纹。
3.离层:在钢管内表面出现螺旋形状或块状的金属分层或破裂或凸疤,这种缺陷称之为离层。
4.内折:在钢管的内表面出现螺旋形、半螺旋形,无规则分布的锯齿状折叠,这种缺陷称之为内折。
5.结疤(包括鳞层、翘皮、辗皮):在钢管的内表面,呈现有棱角的斑疤痕,这种缺陷称之为结疤。
6.划伤(拉毛):钢管内外表面,呈现直线形有规律分布的沟痕,这种缺陷称之为划伤(拉毛)。
7.轧折:沿管壁纵向局部或通长呈现外凹里凸的皱折,外表面呈条状凹陷,这种缺陷称之为轧折。
8.矫凹(矫印):在钢管表面,呈现螺旋形凹陷,这种缺陷称之为矫凹(矫直印),又称螺纹(矫直倾角)。
9.毛刺:钢管端部圆周方向出现整圈或局部的残留的锯齿状薄片,这种缺陷称之为毛刺。
10.壁厚不均:钢管存在横截面及纵向厚度不等的现象,这种缺陷称之为壁厚不均。
11.抖纹(又称波纹、竹节形、环状):在钢管内外表面上,沿横向呈高低不平的整圈或半圆波形的环痕,有连续的,也有断续的,有的仅在表面,这种缺陷称之为抖纹(又称波纹、竹节形、环状)。
12.凹坑(包括压痕):在钢管表面呈现面积不一的局部凹陷,有的呈周期性,也有的无规律。
缺陷表面有破伤为凹坑,表面无破伤为压痕。
13.麻点(又称麻面):在钢管表面成片的点状的细小凹陷,这种缺陷称之为麻点。
14.直道:在钢管的内外表面呈现具有一定宽度和深度的直线形划痕,分布在钢管的全长或局部,这种缺陷称之为直道。
不锈钢无缝管冷拔管主要缺陷原因分析

不锈钢无缝管冷拔管主要缺陷原因分析不锈钢无缝管冷拔管是制造工业中常用的一种管材,具有高强度、耐腐蚀、抗高温等优点。
然而,在生产过程中,不锈钢无缝管冷拔管也会出现一些缺陷,影响其质量和使用性能。
下面将对不锈钢无缝管冷拔管主要缺陷的原因进行分析。
1.冷拔裂纹冷拔裂纹是不锈钢无缝管冷拔管中常见的缺陷。
主要原因包括:(1)超过材料的塑性变形极限,导致材料发生微裂纹;(2)冷拔过程中,不锈钢管内外表面摩擦产生热量,使不锈钢管的表面温度升高,但内部温度较低,造成不均匀变形,引起裂纹;(3)冷拔过程中,不锈钢管的表面受到过大的切削力和压力,导致表面裂纹形成。
2.冷拔皮面凹陷冷拔皮面凹陷是因为不锈钢无缝管冷拔管的表面出现深度不均匀的凹陷。
主要原因包括:(1)冷拔过程中,不锈钢管内外表面存在不一致的形变应力,导致表面凹陷;(2)冷拔过程中,冷却不均匀,使得不锈钢管的表面有热量堆积,导致凹陷。
3.管道内部气泡管道内部气泡是不锈钢无缝管冷拔管中的一种重要缺陷。
主要原因包括:(1)冷拔过程中,由于变形应力大,会产生氧化皮,氧化皮与金属表面不牢固结合,形成空鼓;(2)冷拔过程中,冷却不均匀,导致管道内部产生凝结水,形成气泡。
4.脱漆脱漆是指不锈钢无缝管冷拔管表面的涂层脱落。
主要原因包括:(1)材料的涂层质量不达标,没有很好地附着在管道表面,容易脱落;(2)不锈钢管在运输和使用过程中受到外部力的作用,使得涂层剥落。
5.尺寸偏差尺寸偏差是指不锈钢无缝管冷拔管在制造过程中的尺寸不符合要求的缺陷。
主要原因包括:(1)冷拔过程中的冷变形过程无法完全控制,导致管道尺寸偏差;(2)生产设备的精度不高,也会导致不锈钢管尺寸的偏差;(3)材料的收缩因素未考虑充分,导致材料冷拔后的尺寸偏差。
综上所述,不锈钢无缝管冷拔管的主要缺陷原因包括冷拔裂纹、冷拔皮面凹陷、管道内部气泡、脱漆和尺寸偏差等。
在生产过程中,需要加强对每个环节的控制和管理,提高生产设备的精度,采取合理的工艺措施,以减少和防止缺陷的发生,提高不锈钢无缝管冷拔管的质量和使用性能。
- 1、下载文档前请自行甄别文档内容的完整性,平台不提供额外的编辑、内容补充、找答案等附加服务。
- 2、"仅部分预览"的文档,不可在线预览部分如存在完整性等问题,可反馈申请退款(可完整预览的文档不适用该条件!)。
- 3、如文档侵犯您的权益,请联系客服反馈,我们会尽快为您处理(人工客服工作时间:9:00-18:30)。
[选取日期]
冷拔无缝钢管常见的缺陷特征产生的原因
及预防和消除方法
2010年10月08日
孟相欣
冷拔无缝钢管常见的缺陷特征
产生的原因及预防和消除方法
一、折迭
拔制后,钢管内外表面呈现直线或螺旋方向的折迭,局部或通长的出现在钢管上。
产生的原因:管料表面有折迭或夹杂物,有严重擦伤和裂纹,管料磨修处有棱角或深宽比(H/b)不够。
预防和消除方法:严格把好穿孔热轧质量关。
二、尺寸超差(包括壁厚超差,壁厚不均,直径超差,椭圆偏心)
直径超过了标准的偏差,在同一截面上管壁一边薄,一边厚,直径不等,长短轴之差超出标准规定。
产生的原因:1、拔制模具选择不当,或芯棒(内模)调整不当。
2、内外模设计制造不合理或磨损严重,或硬度不够造成变形磨损。
3、热处理时间长,温度高,或热处理性能不均匀。
4、增减壁的规律控制不当。
5、拔制表编制不合格。
6、钢管矫直时被压扁,造成误差较大。
预防和消除方法:1、正确设计和选配拔管模具。
2、正确执行热处理制度,均匀加热。
3、正确调制矫直机,经常校对拔管机各部件和量具。
4、掌握不同钢种、不同规格钢管的增减壁规律。
5、正确合理编制拔制表。
6、椭圆度出格可重新矫直,局部椭圆度出格可切除。
三、划道
钢管表面上呈现纵向直线的划痕称为划道,划道长短不一,宽窄不等,多为沟状,可见沟底。
产生的原因:1、拔模表面不光滑,有裂纹或粘结金属。
2、锤头过度部分有棱角,工具磨损。
3、欠酸洗或毛管上残存氧化铁皮。
4、磷化、皂化工序操作不当。
5、内外模以损坏或磨损严重。
6、中间退火不均,变形量不足。
预防和消除方法:1、提高拔管模具的表面质量。
2、钢管酸洗后,氧化铁皮要冲洗干净。
3、锤头过度部分要圆滑无棱角。
4勤检查模具和钢管的表面,发现问题及时处理。
四、斗纹
钢管表面沿长度方向呈高低不平的环形波浪或波浪逐个相同排列,局部或通长出现在钢管内外表面上。
产生的原因:1、热处理后的性能不均,热轧时低温钢造成性能不均。
2、酸洗后冲洗不干净,磷化不良导致皂化不均。
3、芯杆细,拔制时芯杆产生弹性变形引起抖动。
4、拔模形状不合理,入口锥角太大,使钢管与模孔的接触面积过小,使拔制拔制变形不稳定而抖动。
预防和消除方法:1、按操作规程要求进行热处理,达到软化性能均匀。
2、要把好酸洗、磷化、皂化的质量关。
3、按规定的变形量拔制。
4、正确选用芯杆尺寸。
五、拔凹
在钢管纵向上,管壁向内呈条状凹陷,其长短无规则。
产生的原因:1、无芯棒拔制(空拔)薄壁钢管时,减径量过大。
2、钢管锤头端部有棱角或过度部分有皱折且变形量过大。
3、管料局部璧薄(如修磨点)。
预防和消除方法:1、空拔薄壁管时,要合理分配减径量。
2、锤头端部应无棱角和皱折。
3、对管料表面的局部缺陷进行清理。
六、开裂(纵裂)
钢管呈现穿透管壁的纵向裂开,有通长局部裂开。
产生的原因:1、压下量过大,连拔道次过多,管料加工硬化严重,空拔尤甚。
2、热处理不当,造成管料塑性不一致或加工硬化未全部消除。
3、钢管拔制后未及时热处理。
4、塑性低的钢种较易开裂。
预防和消除方法:1、合理编制拔制表。
2、合金钢管和连拔钢管要及时进行热处理。
3、按工艺要求进行热处理,冷却速度要合理控制,使其性能均匀,消除加工硬化。
七、过酸洗(硫酸)
钢管表面呈现孔状、芝麻状裂口,轻重程度不同,一般外表面比内表面严重。
产生的原因:1、钢管表面氧化皮厚度不均,疏松与牢固程度不同。
2、酸洗时间过长。
3、酸液浓度低,硫酸亚铁含量高,在酸洗温度过高的情况下,容易过酸洗。
4、酸液浓度不均,溶液不流动,腐蚀不均。
预防和消除方法:1、正确执行酸洗技术操作规程。
2、掌握好热处理操作,防止钢管表面氧化铁皮厚薄不均。
3、严格贯彻勤吊勤看勤检查,防止过酸洗。
八、麻点(麻面、麻坑)
钢管表面成片的细点状凹坑,局部或连续的出现在钢管表面上。
产生的原因:1、热处理生成氧化皮过厚(过烧),在矫直时氧化铁皮压入或剥落后产生麻点。
2、酸洗后残留氧化铁皮或皂化液中有脏物,拔后产生麻点。
3、管子酸洗后,停放时间过长生锈腐蚀造成麻面。
4、钢管表面有油污,热处理时聚结成油点在加热时烧成麻面。
预防和消除方法:1、装炉时按钢种要求正确执行热处理制度。
2、坚持快速周转。
3、酸洗做到不过洗、不欠洗,酸洗后及时拔制。
九、拔制断裂
拔制时产生尖锐的怪叫声或间断规律的“噔噔……”声,内外模具拉毛,钢管内外表面拉伤,缺少润滑效果、拔机拔制时负荷增大等造成钢管横向断裂。
产生的原因:1、酸洗碳化(氢脆),造成钢管拔制断裂。
2、磷化不达标,磷化过度(太老)造成磷化膜脱落,失去润滑目的,即产生冷拔时怪叫不断。
3、磷化过轻,则润滑不能在钢管表面形成附着,即产生间断规律的“噔噔……”声,造成模具和钢管内外表面拉伤,拔机拔制时负荷增大。
4、润滑温度太低或太高,浓度不足润滑剂吸附不足或润滑剂被酸化失去润滑效果。
预防和消除方法:1、严格控制酸洗浓度、温度、时间,勤冲洗、换水。
2、经常检查磷化液的总酸度和游离酸度,确保磷化酸比正常。
3、控制润滑温度、浓度,保持工作液的清洁,免除酸化。
4、检查变形量、内外模具是否达标。
孟相欣
2010年10月08日。