热轧无缝钢管缺陷及产生原因
轧制无缝钢管常见缺陷和控制措施

轧制无缝钢管常见缺陷和控制措施广东省广州市 510700摘要:无缝钢管是用钢锭或实心管坯穿孔制成毛管,然后经热轧、冷轧或冷拔制成,一般用外径*壁厚毫米数表示。
主要用来输送流体,如输送石油、天然气、煤气、水及某些固体物料。
无缝钢管的用途非常广泛,涉及建筑、石油化工、电力、机械加工、电信、消防、汽车、船舶等行业。
随着使用范围的推广,无缝钢管自身或加工过程中出现的缺陷对安全生产影响也越来越大,本文结合常见缺陷浅析控制措施。
关键词:无缝钢管;常见缺陷;控制措施引言:我国无缝钢管从无到有经过近70年的发展,无缝钢管在产品结构、质量水平、技术装备等方面有了很大的提升,已成为世界钢管制造大国,总产量占全世界60%左右。
同时,因各种缺陷引起的安全事故也是频繁发生,现就无缝钢管缺陷产生的进行思考,进而提出控制措施,以便促进我国钢管行业的发展。
轧制无缝管常见缺陷产生的原因常见缺陷:裂纹、折叠、结巴、扎折、离层、划伤、内翘皮、夹渣等缺陷。
这些缺陷有时会同时出现,原因也是多方面的。
裂纹产生的原因:环形加热炉中管坯或毛管加热温度较高,加热时间较长,从而导致坯料表面氧化脱碳严重,且基体晶粒相对粗大。
由于脱碳层组织成分为强度较低的铁素体,在轧制过程中使管子表面严重脱碳的薄弱环节产生裂纹。
坯料本身存在夹渣、砂眼等缺陷,在轧制过程中使原有缺陷延伸细化进而形成裂纹。
折叠、夹层产生的原因:当管坯存在非金属夹杂、偏析时,有气孔存在夹杂物周边,在穿孔轧制时不能焊合形成内折叠。
管头切飞边残留物(钢屑)带到内壁形成夹层。
划痕、内翘皮产生的原因:在穿孔阶段,顶头变形在内壁形成划痕、凹坑、离层缺陷等缺陷。
钢管退火温度和冷拉余量的控制是否合理,也是形成内翘皮的原因缺陷形成的原因还包含:原材料管胚炼钢水平高低、管胚加工过程控制。
加工制造过程造成包括工艺加工设备落后原因、检测设备设置原因、工作人员工作态度原因。
常见缺陷无损检测手段主要无损检测手段及检测特点:涡流探伤、磁粉探伤、超声波探伤、水压试验。
无缝钢管生产缺陷与预防

无缝钢管生产缺陷与预防1. 引言无缝钢管是一种重要的工业材料,广泛应用于石油、化工、电力、航空、航天等领域。
然而,在无缝钢管的生产过程中存在一些缺陷问题,例如内外壁裂缝、折叠、夹层等。
这些缺陷不仅会降低无缝钢管的质量、性能,还可能导致管道泄漏、事故等安全问题。
因此,如何预防无缝钢管的生产缺陷是非常重要的。
本文将首先介绍无缝钢管生产过程中常见的缺陷问题,然后讨论预防无缝钢管生产缺陷的方法与措施,旨在提高无缝钢管的质量和安全性。
2. 无缝钢管生产过程中常见的缺陷问题2.1 内外壁裂缝内外壁裂缝是无缝钢管生产过程中最常见的缺陷问题之一。
这种裂缝可能是由于原料质量不佳、加工过程中的应力超过了材料的承受范围等原因引起的。
内外壁裂缝会导致无缝钢管在使用过程中易发生断裂,从而造成事故。
2.2 折叠折叠缺陷是指无缝钢管的内外壁出现弯曲、折叠痕迹。
这种缺陷可能是由于轧制过程中的辊形有问题、轧机调整不当等原因引起的。
折叠会使无缝钢管的强度和密封性降低,增加管道泄露的风险。
2.3 夹层夹层是指无缝钢管内外壁之间出现分层或夹杂物。
这种缺陷可能是由于材料不纯、熔炼和浇铸过程中的夹杂物等原因引起的。
夹层会降低无缝钢管的强度和耐腐蚀性,导致管道泄漏和腐蚀。
3. 预防无缝钢管生产缺陷的方法与措施3.1 严格选材要预防无缝钢管生产缺陷,首先需要严格选材。
选择质量优良的原材料可以避免原料本身存在的缺陷问题,降低无缝钢管的生产缺陷风险。
同时,进行严格的材料检测和评估,确保原材料达到相关标准和要求。
3.2 完善加工工艺加工工艺是影响无缝钢管质量的关键因素之一。
应根据钢管的不同用途和要求,制定完善的加工工艺流程。
在轧制、冷拔和热处理等工艺中,要严格控制工艺参数,确保钢管的形状、尺寸和性能达到要求,避免产生裂缝、折叠和夹层等缺陷。
3.3 质量控制与检测质量控制与检测是预防无缝钢管生产缺陷的重要手段。
应建立健全的质量管理体系,从源头控制,严格遵守相关标准和规范。
热轧质量缺陷及产生原因
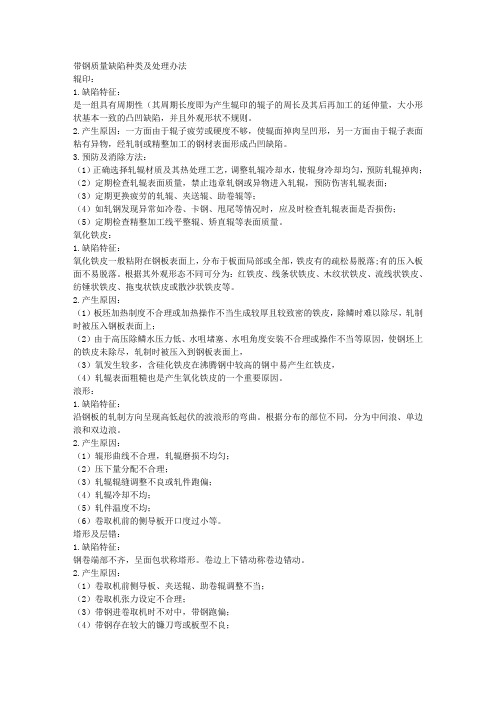
带钢质量缺陷种类及处理办法辊印:1.缺陷特征:是一组具有周期性(其周期长度即为产生辊印的辊子的周长及其后再加工的延伸量,大小形状基本一致的凸凹缺陷,并且外观形状不规则。
2.产生原因:一方面由于辊子疲劳或硬度不够,使辊面掉肉呈凹形,另一方面由于辊子表面粘有异物,经轧制或精整加工的钢材表面形成凸凹缺陷。
3.预防及消除方法:(1)正确选择轧辊材质及其热处理工艺,调整轧辊冷却水,使辊身冷却均匀,预防轧辊掉肉;(2)定期检查轧辊表面质量,禁止违章轧钢或异物进入轧辊,预防伤害轧辊表面;(3)定期更换疲劳的轧辊、夹送辊、助卷辊等;(4)如轧钢发现异常如冷卷、卡钢、甩尾等情况时,应及时检查轧辊表面是否损伤;(5)定期检查精整加工线平整辊、矫直辊等表面质量。
氧化铁皮:1.缺陷特征:氧化铁皮一般粘附在钢板表面上,分布于板面局部或全部,铁皮有的疏松易脱落;有的压入板面不易脱落。
根据其外观形态不同可分为:红铁皮、线条状铁皮、木纹状铁皮、流线状铁皮、纺锤状铁皮、拖曳状铁皮或散沙状铁皮等。
2.产生原因:(1)板坯加热制度不合理或加热操作不当生成较厚且较致密的铁皮,除鳞时难以除尽,轧制时被压入钢板表面上;(2)由于高压除鳞水压力低、水咀堵塞、水咀角度安装不合理或操作不当等原因,使钢坯上的铁皮未除尽,轧制时被压入到钢板表面上,(3)氧发生较多,含硅化铁皮在沸腾钢中较高的钢中易产生红铁皮,(4)轧辊表面粗糙也是产生氧化铁皮的一个重要原因。
浪形:1.缺陷特征:沿钢板的轧制方向呈现高低起伏的波浪形的弯曲。
根据分布的部位不同,分为中间浪、单边浪和双边浪。
2.产生原因:(1)辊形曲线不合理,轧辊磨损不均匀;(2)压下量分配不合理;(3)轧辊辊缝调整不良或轧件跑偏;(4)轧辊冷却不均;(5)轧件温度不均;(6)卷取机前的侧导板开口度过小等。
塔形及层错:1.缺陷特征:钢卷端部不齐,呈面包状称塔形。
卷边上下错动称卷边错动。
2.产生原因:(1)卷取机前侧导板、夹送辊、助卷辊调整不当;(2)卷取机张力设定不合理;(3)带钢进卷取机时不对中,带钢跑偏;(4)带钢存在较大的镰刀弯或板型不良;(5)卷取机卸卷时将钢卷头部拽出。
钢管“内六方”缺陷的产生原因及优化
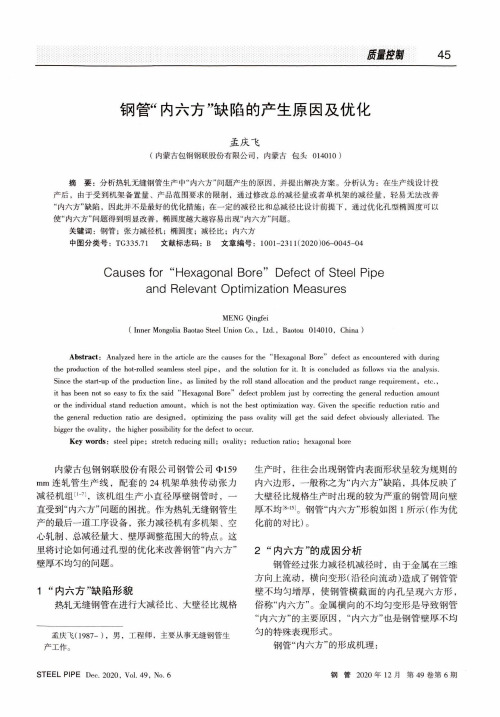
钢管“内六方”缺陷的产生原因及优化孟庆飞(内蒙古包钢钢联股份有限公司,内蒙古包头014010)摘要:分析热轧无缝钢管生产中“内六方”问题产生的原因,并提出解决方案。
分析认为:在生产线设计投产后,由于受到机架备置量、产品范围要求的限制,通过修改总的减径量或者单机架的减径量,轻易无法改善“内六方”缺陷,因此并不是最好的优化措施;在一定的减径比和总减径比设计前提下,通过优化孔型椭圆度可以使“内六方”问题得到明显改善,椭圆度越大越容易出现“内六方”问题。
关键词:钢管;张力减径机;楠圆度;减径比;内六方中图分类号:TG335.71 文献标志码:B文章编号:1001-2311(2020)06-0045-04Causes for “Hexagonal Bore” Defect of Steel Pipeand Relevant Optimization MeasuresMENG Qingfei(Inner Mongolia Baotao Steel Union Co.,Ltd.,Baotou014010,China )Abstract: Analyzed here in the article are the causes for the**Hexagonal Bore'defect as encountered with during the production of the hot-rolled seamless steel pipe,and the solution for it.It is concluded as follows via the analysis. Since the start-up of the production line,as limited by the roll stand allocation and the product range requirement,etc., it has been not so easy to fix the said“Hexagonal Bore”defect problem just by correcting the general reduction amount or the individual stand reduction amount,which is not the best optimization way.Given the specific reduction ratio and the general reduction ratio are designed,optimizing the pass ovality will get the said defect obviously alleviated.The bigger the ovality,the higher possibility for the defect to occur.Key words:steel pipe;stretch reducing mill;ovality;reduction ratio;hexagonal bore内蒙古包钢钢联股份有限公司钢管公司中159 mm连轧管生产线,配套的24机架单独传动张力 减径机组[|-7],该机组生产小直径厚壁钢管时,一直受到“内六方”问题的困扰。
热轧工序典型质量缺陷产生原因与预防措施

预防措施
加强原材料质量检查,去除夹杂物;加强生 产过程控制,及时清除金属氧化物和其他夹 杂物。
03
热轧工序质量缺陷预防措施
提高原料质量
01
总结词:优化源头
02
详细描述:选用质量稳定的原料 ,控制原料的化学成分、物理性 能等指标,确保原料质量稳定, 为热轧工序打下良好的基础。
优化热轧工艺参数
要点一
热轧钢板内部存在气泡缺陷,影响产品质量和使用性能。
产生原因:熔炼和连铸过程控制不当、坯料加热时间过长或加热温度 过高、轧制速度过快。
预防措施:加强熔炼和连铸过程控制、合理控制坯料加热时间和温度 、降低轧制速度。
案例五:某钢厂热轧带钢表面翘曲预防措施
热轧带钢表面翘曲
产生原因:轧制温度和 冷却速度控制不当、坯 料厚度和成分不均。
案例三
01
热轧圆钢表面划痕
02
热轧圆钢表面存在划痕等缺陷, 影响产品外观和使用性能。
产生原因:轧辊表面损伤、坯料 表面质量差、冷却不均匀。
03
预防措施:检查和修复轧辊表面 损伤、加强坯料检查和加热控制
、调整冷却制度。
04
案例四:某钢厂热轧钢板内部气泡控制措施
01 02 03 04
热轧钢板内部气泡
01
02
03
04
热轧带钢表面存在翘曲 缺陷,影响产品平整度 和使用性能。
预防措施:合理控制轧 制温度和冷却速度、加 强坯料检查和控制。
THANK YOU
质量缺陷分类
根据缺陷的性质和产生原因,可 将热轧工序的质量缺陷分为材质 缺陷、工艺缺陷、设备缺陷和外 观缺陷等。
质量缺陷对产品的影响
影响使用性能
如强度、韧性等力学性能下降, 导致产品在使用过程中出现早期
热轧工序典型质量缺陷产生原因与预防措施
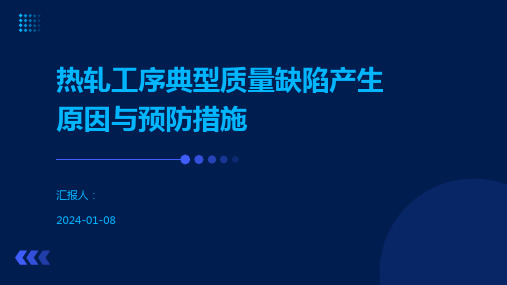
工艺参数设置不合理、工艺流程不完善等工艺因素是导致热轧工序质量缺陷的 重要原因。
详细描述
加热温度、轧制速度、道次压下量等工艺参数的设置对热轧产品的质量有显著 影响。工艺流程中的不合理之处,如冷却速度控制不当、轧制道次不足等,也 可能导致产品出现各种缺陷。
设备因素
总结词
设备故障、维护不当等设备因素是热轧工序中常见的质量缺 陷原因。
热轧工序典型质量缺陷产生 原因与预防措施
汇报人: 2024-01-08
目录
• 热轧工序简介 • 典型质量缺陷类型 • 产生原因分析 • 预防措施 • 案例分析 • 结论与展望
01
热轧工序简介
热轧工序的定义和重要性
定义
热轧工序是将金属材料在高温下 进行轧制的过程,目的是改变材 料的形状并获得所需的机械性能 。
钢材内部碳化物分布不均,导致钢材 性能不均一。
03
产生原因分析
原料因素
总结词
原料质量不均、成分偏析等原料因素 是导致热轧工序质量缺陷的主要原因 之一。
详细描述
原料的化学成分、微观组织结构、夹 杂物含量等因素可能影响热轧过程中 的流动性和变形行为,从而导致产品 出现裂纹、孔洞、夹杂等缺陷。
工艺因素
板形不良产生的原因可能是轧辊磨损严重、轧 制工艺参数设置不合理,或者是来料温度和厚 度波动过大。
厚度超差产生的原因可能是轧辊间隙调整不当 、轧制过程中张力控制不准确,或者是轧制润 滑条件不佳,导致金属流动不均匀。
预防措施实施效果评估
对于表面裂纹,通过优化轧制温 度和润滑条件,加强轧辊检查和 维护,可以显著减少裂纹的产生
2
针对这些质量缺陷,需要采取有效的预防措施, 如控制工艺参数、优化设备参数和加强质量检测 等。
热轧钢管产品缺陷一览表

热轧钢管产品缺陷一
缺陷名称产生原因
产生工序
管坯表面砸伤,管坯表面有裂
纹
来料单位轧辊表面有异物穿孔导板材质不好
供货单位导板磨损严重或粘钢穿孔导板的形状和轧辊的形状不吻合
工艺设计导向口或受料槽不光穿孔托辊、抱辊、料钩等表面不光
滑穿孔
内孔刮伤顶头或顶杆上有凸起的部分,
束节不光滑或匹配不当
穿孔钢温偏低司炉顶头冷却水太大穿孔顶头位置过后穿孔管坯剪切斜度过大剪切钢温过低、阴阳面司炉、拔料
顶头偏离中心太多
穿孔模子磨损严重打头职工操作不规范
打头尺寸超差
责任心不够,量具不齐全,取
样不及时
穿孔
壁厚不均
打头不好外折叠
导板印
外表碰划
伤内孔折叠
缺陷一览表
预防措施及解决方法备注
严格检查进厂的管坯质量
修磨轧辊
更换供货厂家,确保导板质量
修磨或更换导板
根据辊形设计导板的尺寸
修磨或更换导向口,受料槽,多
在尾部
修磨或更换
修磨或更换
经常观察仪表,保证炉温
把水开小点
进一点顶头位置
更换剪切刀片(头部)
保证钢温、及时拨料
正确调整抱辊,轧辊左右位
置,保证轧辊中心
堆焊或更换模子
加强锻炼,提高责任心
配备各种量具,加强职工责任
心。
无缝钢管生产缺陷与预防

尺寸检测
测量工具:游标卡尺、千分尺等 测量方法:直接测量、间接测量等 测量精度:根据生产要求选择合适的测量精度 测量结果处理:记录、分析、反馈等
壁厚检测
超声波检测:利用超声波在壁厚中的传播速度和衰减特性,测量壁厚 射线检测:利用射线穿透壁厚,测量壁厚 磁性检测:利用磁性材料在壁厚中的磁性变化,测量壁厚 涡流检测:利用涡流在壁厚中的变化,测量壁厚
无缝钢管生产缺陷与预 防
,a click to unlimited possibilities
汇报人:
目录
01 添 加 目 录 项 标 题
02 无 缝 钢 管 生 产 缺 陷
03 无 缝 钢 管 生 产 预 防
措施
05 无 缝 钢 管 生 产 缺 陷 处理方法
04 无 缝 钢 管 生 产 缺 陷 检测方法
Part Four
无缝钢管生产缺陷 检测方法
外观检测
目视检查:通过肉 眼观察无缝钢管的 外观,检查是否有 划痕、凹坑、凸起 等缺陷。
手感检查:通过触 摸无缝钢管,检查 是否有粗糙、凹凸 不平等缺陷。
测量检查:通过测 量无缝钢管的尺寸 、形状、厚度等, 检查是否符合标准 。
光学检测:通过光 学仪器,如显微镜 、放大镜等,检查 无缝钢管的表面和 内部缺陷。
壁厚不均
原因:轧制过程中,轧辊压力不均匀,导致壁厚不均 影响:影响钢管的力学性能和耐腐蚀性能 预防措施:调整轧辊压力,保证轧制过程的均匀性 检测方法:采用超声波检测或涡流检测,及时发现壁厚不均问题
内部缺陷
气孔:由于气体残留在钢管内部形成的孔洞 夹杂物:钢管内部含有的杂质或异物 裂纹:钢管内部出现的裂纹或裂缝 变形:钢管内部形状不规则或扭曲
Part Three
- 1、下载文档前请自行甄别文档内容的完整性,平台不提供额外的编辑、内容补充、找答案等附加服务。
- 2、"仅部分预览"的文档,不可在线预览部分如存在完整性等问题,可反馈申请退款(可完整预览的文档不适用该条件!)。
- 3、如文档侵犯您的权益,请联系客服反馈,我们会尽快为您处理(人工客服工作时间:9:00-18:30)。
热轧无缝钢管缺陷及产生原因
1. 离层
缺陷特征:位于钢管内表面呈纵向分布,呈凸起螺旋状,块状金属分离或破裂状夹层。
产生原因:材质不良造成有非金属夹杂物,残余缩孔或严重疏松。
2. 直道内折
缺陷特征:位于钢管内表面呈纵向分布,呈现对称或单条直线形的折迭有通长,也有局部。
产生原因:芯棒润滑不良,芯棒表面有缺陷或表面附有氧化铁皮,铁屑等使钢管内表面划成沟道,荒管在轧制过程中,在连轧机孔型内过充满。
3. 内孔不规则
缺陷特征:位于钢管内表面呈纵向分布,①有一个或二个相差180°的管壁增厚现象,或在钢管内表面与芯棒分离点处有壁厚增厚状,也称内鼓包。
②钢管内园呈六方形的壁厚不均状,也称内六方。
产生原因:内鼓色:连轧压下量分配或张力选择不当,使金属过充满芯棒选用不当。
内六方:张减孔型与张力参数选择不当,张减机单机架减经或总减径率较大。
4. 管壁收缩
缺陷特征:位于钢管内表面上,钢管横向断面最薄处钢管内表面凹陷,壁厚局部变薄,严重的收缩几乎撕破。
产生原因:连轧机延伸过大,钢管在孔型侧壁部分,局部被拉薄连轧机各机架压下调整不当和延伸系数分配不合理。
5. 内轧疤
缺陷特征:钢管内表面纵向呈指甲状结疤、凸起或块状折迭,钢管内表面压痕。
产生原因:芯棒润滑状态不良,造成芯棒局部磨损、损坏、粘金属,顶头严重磨损、粘金属、缺肉或大裂纹穿孔耳子被压在钢管的内壁上。
6. 内折迭
缺陷特征:位于钢管内表面的端部,局部或纵向呈螺旋状半螺旋状或无规律分布的片状折迭。
产生原因:穿孔过程中轧机调整不当,顶头严重磨损,管坯材质不好,芯棒严重损坏。
7. 轧折
缺陷特征:位于钢管内表面纵向管壁局部或全长上呈外凹里凸的皱折或在钢管外表面纵向通长有两道对称明显沟痕,一般为直线形,个别为斜线形。
产生原因:连轧荒管外径过大或荒管橢圆度太大,竹节控制强度不够或润滑状态不好,横移装置将连轧荒管碰瘪,连轧机转速错误。
8. 撕破
缺陷特征:位于钢管表面纵向上管体呈现不同程度的横向破裂,菱状和椭圆状穿透管体的孔洞。
产生原因:连轧来料局部有“黑斑”,过连轧时极易撕破,缺陷形式一般为菱形状。
连轧来料温度偏低,连轧张力过大,连轧机转速选择不当。
9. 双缝折迭
缺陷特征:位于钢管表面纵向上一对斜向伸入管壁纵向的裂缝,这种裂缝有时是零散地分布在管子园周上有时以对称出现。
产生原因:穿孔毛管外径过大或直径不规则引起的折迭。
10.外折迭
缺陷特征:①钢管外表上呈现规律性的折迭有三角状,双缝直线状,单缝直线状或无规律的片状折迭等。
②钢管的纵向外表上呈现一条通常连续或间断缝纫机针脚状或错开60°、120°、180°缝纫针脚状的折迭。
③钢管的纵向外表上呈现螺旋状折迭。
④钢管表面纵向呈一条通长点状或短斜线的折迭,严重时错开120°的二条或三条。
产生原因:①管坯表面有纵向裂纹或存在严重的夹杂物,缩孔等产生螺旋状折迭。
②管坯表面清理不良,有尖锐棱角或存在外翘皮。
③穿孔机导盘结瘤或穿孔机出口嘴擦伤毛管。
④连轧辊或张减辊有裂纹或碰伤。
⑤张减机辊倒角不合要求,超寿命,新旧机架搭配使用不当。
⑥张减机钢管输送过程中机械擦伤或碰伤。
⑦张减机辊冷却水小或无造成张减机辊粘钢。
11.压痕
缺陷特征:在钢管纵向表面呈现无规律或有规律局部压痕、掉肉。
形状有核状、条状、横向压伤、翘皮状、碎裂、铁屑状等。
产生原因:①张减机成品机架轧辊表面粘有金属物。
②结疤或其他异物压在钢管表面上脱落而形成。
③热态钢管碰伤或划伤。
④被横移装置或锯切装置碰伤、压印。
判断:一般管:壁厚≤8mm压痕深度不超过负偏差的90% ,壁厚>8mmm压痕深度不超过负偏差的80%最大度不得超过1.0mm。
锅炉管:不得超过壁厚负偏差之半,最大值为0.6mm。
油套管:压痕深度不得超过壁厚负偏差之半,S≥10mm时深度最大值不超过0.6mm,当S <10mm时最大深度不超过0.5mm。
12. 过热
缺陷特征:在钢管外表面呈粗糙的氧化铁皮鳞片或斑痕。
产生原因:加热时间过长或加热温度过高。
13. 矫凹
缺陷特征:在钢管外表面呈现螺旋形的凹痕。
产生原因:矫直辊角度调整不当,压下量太大,矫直辊磨损严重。
14. 凹痕
缺陷特征:在钢管外表面局部呈无规律或有规律各种形状的压痕外凹里凸,管壁壁厚无变化。
产生原因:钢管在运输过程中受到剧烈的碰撞或受到较大冲压,在锯切过程中,夹紧力调整不当。
判断:一般管:凹痕深度不得使外径超出负偏差。
锅炉管、油套管:凹痕深度不得使外径超出负偏差之半。
15. 发纹
缺陷特征:在钢管的外表面上呈连续或不连续的发状细裂纹,多为螺旋形,螺距较大,也有近似直线。
产生原因:钢质不良,有皮下夹杂物和皮下气孔,管坯表面清理不良或有发纹。
16. 麻面
缺陷特征:沿钢管表面局部通长呈现高低不平的麻坑及沟痕,有的是周期性出现。
产生原因:连轧机或张减机轧辊磨损严重,在再加热炉内加热时间过长或温度过高,在再加热炉后高压水除鳞装置压力低,个别喷嘴堵塞。
判断:一般管:麻面深度不超过壁厚负偏差之半。
锅炉锅:麻面深度不超过负偏差之半,最大值为0.6mm。
油套管:麻面深度不超过壁厚负偏差之半,当S<10mm时深度最大值不超过0.5mm,S≥10mm深度最大值不超过0.6mm。
17. 壁厚不均
缺陷特征:钢管同一截面上壁厚最大值,最小值分别超过正偏差和负偏差或分别超过公称壁厚的±8~10% (厚壁管取上限薄壁管取下限)
产生原因:穿孔来料不符合要求,管坯端面切斜,管坯热定心偏,管坯加热不均,穿孔设备调整不当,连轧机设备调整不当。
18. 壁厚超差
缺陷特征:钢管同一截面上或沿钢管长度方向壁厚超差。
产生原因:连轧机,张减机调整不当,转速选择不当,芯棒选择错误,张减增厚端设有切净。
19. 外径超差
缺陷特征:在钢管同一截面上或沿管长度方向外径超差。
产生原因:张减机孔型尺寸加工不对,张减机成品孔型磨损严重或孔型设计不对,再加热炉温度波动大。
20. 弯曲
缺陷特征:钢管沿长度方向不平直,钢管端部呈鹅头弯曲。
产生原因:张减机最后几架孔型中心线错位。
张减机精轧孔型减径量分配不合理。
张减管冷却方式不合理或锯切时温度过高,运输等原因造成。
21. 钢管开裂
缺陷特征:钢管头部或局部开裂。
产生原因:钢管局部受冷却水冷却在连轧或张减时形成开裂。
钢管头部顶在高压水除鳞设备上被浇成“黑头”张减机轧制时开裂。
22. 拉丝
缺陷特征:在钢管外表通长或出现在管子A、B段呈有规律或无规律线条状,其金属丝有脱落或粘在钢管表面上。
产生原因:张减机孔型设计不合理,穿孔毛管,连轧荒管外径与椭圆度太大,即管形不好,张减机,空减机孔型倒角不合要求。
张减机,空减机孔型不对中。
张减机新旧机架搭配不当。
23. 擦伤
缺陷特征:在钢管外表呈现螺旋形伤痕及其他有规律或无规律分布的擦伤。
产生原因:钢管停留在旋转设备上,机械设备不光滑和错位。
24. 外形不圆
缺陷特征:钢管横截面不圆。
产生原因:锯切时夹紧力调整不当,张减机成品机架和工作机架位置安装不正确,精整涡流探伤出口夹紧装置夹紧力过大,矫直辊压下量或角度调整不当。
25. 青线
缺陷特征:钢管外表呈现对称或不对称的线形轧痕,沿纵向分布。
产生原因:张减机孔型设计不合理,轧低温钢。
张减机孔型中心不对正错位。
张减机孔型超寿命使用,磨损严重。
张减机新旧孔型搭配使用不当。
26. 直道
缺陷特陷:沿钢管纵向分布的沟槽。
产生原因:当轧制温度低时,顶头粘金属划伤钢管内表面,顶头磨损严重。
芯棒润滑不良或
磨损严重。
判断:一般管:外直道深度不超过壁厚负偏差的90%最深不超过1.0mm,内直道深度不超过壁厚负偏差的70%最深不超过0.6mm。
锅炉管、油套管:直道深度不得超过壁厚的5%,最大不超过0.4mm。
钢管经贸网辛勤整理,欢迎分享!钢管经贸网为客户提供最有效的资源推广和广告服务!欢迎拨打免费热线4000-27-28-29。