数控编程车削螺纹进刀的几种方法比较
数控车床螺纹加工编程指令的应用

数控车床螺纹加工编程指令的应用济宁职业技术学院(山东)张玉香在目前的FANUC 和广州数控系统的车床上,加工螺纹一般可采用3 种方法:G32 直进式切削方法、G92直进式固定循环切削方法和G76 斜进式复合固定循环切削方法。
由于它们的切削方式和编程方法不同,造成的加工误差也不同,在操作使用时需仔细分析,以便加工出高精度的零件。
1.编程方法(1)G32 直进式螺纹切削方法指令格式:图1G32直进式螺纹切削方法指令格式:G32 X(U )_ Z(W )_ F_ ;该指令用于车削圆柱螺纹、圆锥螺纹、端面螺纹。
其编程方法与G01 相似,如图1所示。
使用说明:①式中(X ,Z )和(U ,W )为螺纹的终点坐标,即图1 中B 点的坐标值;F 后的数值为导程(单线时为螺距)。
②当α=0°时,作直螺纹加工,编程格式为G32 Z_F_或G32 W_F_ ;当α<45°时加工锥螺纹,螺距以Z轴方向的值指定;当α>45°时螺距以X 轴方向的值指定;当α=90°时,加工端面螺纹,编程格式为G32 X_ F_或G32 U_ F_ 。
③螺纹切削中进给速度倍率开关无效,进给速度被限制在100% ;螺纹切削中不能停止进给,一旦停止进给切深便急剧增加,非常危险。
因此,进给暂停在螺纹加工中无效。
④在螺纹切削程序段后的第一个非螺纹切削程序段期间,按进给暂停键时刀具在非螺纹切削程序段停止。
⑤主轴功能的确定。
在编写螺纹加工程序时,只能使用主轴恒转速控制功能(程序中编入G97 ),由于进给速度的最大值和最小值系统参数已设定,在加工螺纹时为了避免进给速度超出系统设定范围,所以主轴转速不宜太高,一般用如下公式计算:(取)且从粗加工到精加工,主轴转速必须保持恒定。
否则,螺距将发生变化,会出现乱牙。
⑥螺纹起点和终点轴向尺寸的确定。
螺纹加工时应注意在有效螺纹长度的两端留出足够的升速段和降速段,以剔除两端因进给伺服电动机变速而产生的不符合要求的螺纹段,通常:δ=(2~3 )螺距δ=(1~2 )螺距⑦螺纹起点和终点径向尺寸的确定。
梯形螺纹的数控车削
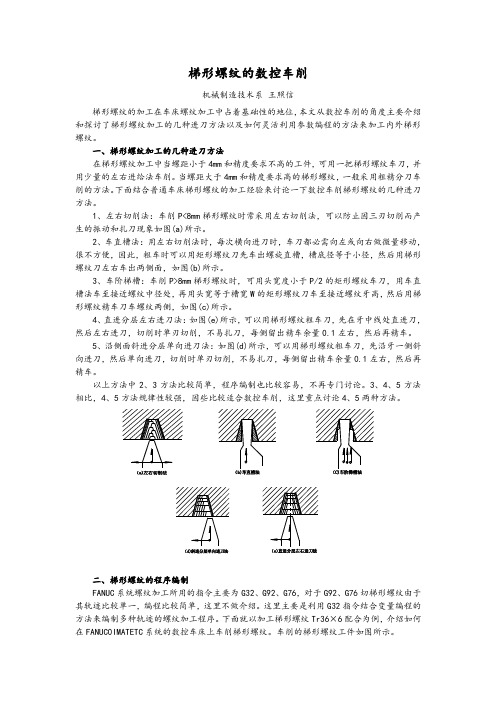
梯形螺纹的数控车削机械制造技术系王照信梯形螺纹的加工在车床螺纹加工中占着基础性的地位,本文从数控车削的角度主要介绍和探讨了梯形螺纹加工的几种进刀方法以及如何灵活利用参数编程的方法来加工内外梯形螺纹。
一、梯形螺纹加工的几种进刀方法在梯形螺纹加工中当螺距小于4mm和精度要求不高的工件,可用一把梯形螺纹车刀,并用少量的左右进给法车削。
当螺距大于4mm和精度要求高的梯形螺纹,一般采用粗精分刀车削的方法。
下面结合普通车床梯形螺纹的加工经验来讨论一下数控车削梯形螺纹的几种进刀方法。
1、左右切削法:车削P<8mm梯形螺纹时常采用左右切削法,可以防止因三刃切削而产生的振动和扎刀现象如图(a)所示。
2、车直槽法:用左右切削法时,每次横向进刀时,车刀都必需向左或向右做微量移动,很不方便,因此,粗车时可以用矩形螺纹刀先车出螺旋直槽,槽底径等于小径,然后用梯形螺纹刀左右车出两侧面,如图(b)所示。
3、车阶梯槽:车削P>8mm梯形螺纹时,可用头宽度小于P/2的矩形螺纹车刀,用车直槽法车至接近螺纹中径处,再用头宽等于槽宽W的矩形螺纹刀车至接近螺纹牙高,然后用梯形螺纹精车刀车螺纹两侧,如图(c)所示。
4、直进分层左右进刀法:如图(e)所示,可以用梯形螺纹粗车刀,先在牙中线处直进刀,然后左右进刀,切削时单刃切削,不易扎刀,每侧留出精车余量0.1左右,然后再精车。
5、沿侧面斜进分层单向进刀法:如图(d)所示,可以用梯形螺纹粗车刀,先沿牙一侧斜向进刀,然后单向进刀,切削时单刃切削,不易扎刀,每侧留出精车余量0.1左右,然后再精车。
4、5方法相比,4、5二、梯形螺纹的程序编制FANUC系统螺纹加工所用的指令主要为G32、G92、G76,对于G92、G76切梯形螺纹由于其轨迹比较单一,编程比较简单,这里不做介绍。
这里主要是利用G32指令结合变量编程的方法来编制多种轨迹的螺纹加工程序。
下面就以加工梯形螺纹Tr36×6配合为例,介绍如何在FANUC0IMATETC系统的数控车床上车削梯形螺纹。
数控车床加工螺纹尺寸计算方法【干货经验】

在数控车床上进行螺纹切削的方法称为使用可转位螺纹刀片的单点螺纹。
由于攻丝操作既是切削操作又是成型操作,因此攻丝刀片的形状和尺寸必须与成品螺纹的形状和尺寸相对应。
根据定义,单点螺纹加工是切削特定形状的螺旋槽的加工过程,该螺旋槽每主轴旋转均匀地前进。
螺纹的均匀性由编程的每转进给速度中的进给速度控制。
螺纹的进给速度始终是螺纹的导程,而不是螺距。
对于单头螺纹,导程和螺距是相同的。
由于单点螺纹加工是多次加工,因此CNC系统为每个线程通过提供主轴同步。
数控车床加工螺纹尺寸计算方法(方式)-数控车床加工螺纹尺寸如何计算首先,是需要知道该百度1/2锥管螺纹的大径,小径,螺距,才能加工出来。
查锥管螺纹标准,可以知道其牙数14,螺距为,牙高为,大径为,小径为,基准距离的基本值为,(最大为10,最小为),如果是外锥螺纹时,还需要知道它的有效螺纹长度应不小于(最长为15,最短为)如何应用以上查得的参数,来应用于数控加工编程以外锥管螺纹1/2为例,把外锥螺纹想象成一个梯形,底朝左,顶朝右。
底端即为大端直径,记为D,顶端即为小端直径,记为d,大径在距离小端的地方。
因为管螺纹锥度比=1:16 =(大D-小d)/锥轴线长,所以可以得到()/=1/16,计算得到d=;同理,有()/=1/16,计算得到D=)利用计算得到的D,d,加工出螺纹的外锥,“梯形”的高暂定为;计算出螺纹锥度R=(D-d)/2=下面开始编程G92和G76均可以以G92为例进行说明编程如下(此处以广数980T 为例,T0101M3 S300 G0Z5M8 X24数控车床数控小径数控车床怎样计算螺纹牙高…大径…小径…d的算法有很多种,根据不同的罗纹有不同的值。
下面我给你具体分开来算: 1:公制螺纹d=乘P;2:55度英制螺纹d=乘P; 3:60度圆锥管螺纹d=乘P; 4:55度圆锥管螺纹d=乘P; 5:55度圆柱管螺纹d=乘P; 6:60度米制锥螺纹d=乘P;注:d=螺纹小径,D=螺纹大径,P=螺距,H就是牙形高度粗牙就是M+公称直径(也就是螺纹大径)。
数控车床多种螺纹加工技巧
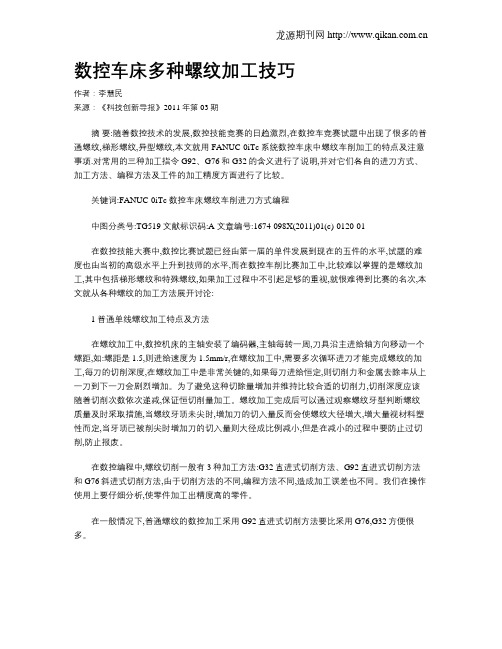
数控车床多种螺纹加工技巧作者:李慧民来源:《科技创新导报》2011年第03期摘要:随着数控技术的发展,数控技能竞赛的日趋激烈,在数控车竞赛试题中出现了很多的普通螺纹,梯形螺纹,异型螺纹,本文就用FANUC-0iTc系统数控车床中螺纹车削加工的特点及注意事项.对常用的三种加工指令G92、G76和G32的含义进行了说明,并对它们各自的进刀方式、加工方法、编程方法及工件的加工精度方面进行了比较。
关键词:FANUC-0iTc数控车床螺纹车削进刀方式编程中图分类号:TG519 文献标识码:A 文章编号:1674-098X(2011)01(c)-0120-01在数控技能大赛中,数控比赛试题已经由第一届的单件发展到现在的五件的水平,试题的难度也由当初的高级水平上升到技师的水平,而在数控车削比赛加工中,比较难以掌握的是螺纹加工,其中包括梯形螺纹和特殊螺纹,如果加工过程中不引起足够的重视,就很难得到比赛的名次,本文就从各种螺纹的加工方法展开讨论:1 普通单线螺纹加工特点及方法在螺纹加工中,数控机床的主轴安装了编码器,主轴每转一周,刀具沿主进给轴方向移动一个螺距,如:螺距是1.5,则进给速度为1.5mm/r,在螺纹加工中,需要多次循环进刀才能完成螺纹的加工,每刀的切削深度,在螺纹加工中是非常关键的,如果每刀进给恒定,则切削力和金属去除率从上一刀到下一刀会剧烈增加。
为了避免这种切除量增加并维持比较合适的切削力,切削深度应该随着切削次数依次递减,保证恒切削量加工。
螺纹加工完成后可以通过观察螺纹牙型判断螺纹质量及时采取措施,当螺纹牙顶未尖时,增加刀的切入量反而会使螺纹大径增大,增大量视材料塑性而定,当牙顶已被削尖时增加刀的切入量则大径成比例减小,但是在减小的过程中要防止过切削,防止报废。
在数控编程中,螺纹切削一般有3种加工方法:G32直进式切削方法、G92直进式切削方法和G76斜进式切削方法,由于切削方法的不同,编程方法不同,造成加工误差也不同。
数控加工工艺及编程 项目3螺纹轴加工工具刀具选择

螺纹轴加工刀具和工具选择一、车刀选择外圆车刀选择原则与短轴加工时的外圆车刀相同用90度外圆车刀,这里就不在赘述。
分析该螺纹零件。
螺纹为M12的三角外螺纹,我选择三角形外螺纹车刀,刀尖角60度。
割槽刀选用3mm宽的外割槽刀。
二、螺纹车刀特点螺纹车刀是成形刀具,其切削部分的形状应和螺纹牙型轴向剖面的形状相符合,车刀的刀尖角应该等于牙型角。
三角形螺纹的牙型角是60°,理论上三角形螺纹车刀的刀尖角也应该是60°。
但实际生产中,只有高速工具钢三角形螺纹车刀的刀尖角是60°,硬质合金三角形螺纹车刀的刀尖角则应为59°30’左右。
这是因为用硬质合金车刀高速切削时,工件材料受到较大的挤压力,会使牙型角增大约0.5°。
三、螺纹车刀种类1.高速工具钢三角形螺纹车刀(图1)的前角一般取5°~15°,粗车刀的纵向前角一般取15°左右,精车刀的前角一般取6°~10°。
2.硬质合金三角形螺纹车刀(图2)的前角和纵向前角一般都取0°,为了增加切削刃的强度,在车削较高硬度的材料时,两切削刃上可磨出负倒棱。
a)粗车到b)精车刀图1高速钢三角螺纹车刀c)焊接式d)机加式图2 硬质合金三角螺纹车刀三、刀具的刃磨三角螺纹车刀刃磨要求:①根据粗、精车的要求,刃磨出合理的前、后角。
粗车刀前角大、后角小,精车刀则相反;②车刀的左右刀刃必须是直线,无崩刃;③刀头不歪斜,牙型半角相等;④内螺纹车刀刀尖角平分线必须与刀杆垂直;⑤内螺纹车刀后角应适当大些,一般磨有两个后角。
四、割槽刀1)高速工具钢槽刀如图3所示1)前角ϒ0:前角增大能使车刀刃口锋利,切削省力并排屑顺畅,ϒ0=5°~20°;2)主后角α0:可减少车槽刀主后刀面和工件过渡表面间的摩擦,α0=6°~8°;3)副后角α0’:可减少车槽刀两个副后刀面和工件已加工表面间的摩擦,α0'=1~3°。
数控车螺纹加工指令编程

用G92进行圆柱螺纹加工
X Z
45°
3(F)
W 4(R)
1(R)
2(F)
2
XU
2
O
Z
格式:G92 X(U)_Z(W)_F_;
用G92进行圆锥螺纹加工
45°
X
Z
W
4(R)
3(F) 2(F)
R
1(R)
2
XU
2
O
Z
格式:G92 X(U)_Z(W)_R_F_;
例:如下图所示圆柱螺纹,螺纹导程为1.0 mm。 δ1=2 mm , δ2=1mm。 试编写螺纹加工程序
例:如下图所示圆锥螺纹,螺纹导程为1.5 mm。 δ1=2 mm , δ2=1mm。 试编写螺纹加工程序
四、简单螺纹切削循环指令G92 该指令的循环路线与前述的G90指令基本相同, 只是F后面的进给量改为螺纹导程即可。 格式:G92 X(U)_Z(W)_R_F_; 其中:X、Z为螺纹终点坐标值
U、W为螺纹起点坐标到终点坐标的增量值 R为锥螺纹大端和小端的半径差。
例:如下图所示圆锥螺纹,螺纹导程为1.5 mm。 δ1=2 mm , δ2=1mm。 试编写螺纹加工程序
五、螺纹切削循环指令G76 格式:G76 X_Z_I_K_D_F_A_P_; 其中:X为终点处的X坐标值 ;Z为终点处的Z坐标值;
I为螺纹加工起点和终点的差值; K为螺纹牙型高度,按半径值编程; D为第一次循环时的切削深度; F为螺纹导程; A为螺纹牙型顶角角度,可在0°~120°之间任意 选择; P为指定切削方式,一般省略或写成P1,表示等 切削量单边切削。
六、螺纹加工方法
螺纹加工常用切削循环方式。 两种方式:直进法(G32、G92)
数控车床加工多头螺纹
数控车床加工多头螺纹摘要:数控车床主要用来加工盘类或轴类零件,利用数控车床加工多头螺纹,能大大提高生产效率,保证螺纹加工精度,减轻操作者的劳动强度。
我通过多年的实践经验,对多头螺纹的加工要点和操作要领进行了总结,为多头螺纹的数控加工提供了理论依据。
关键词:数控车床多头螺纹编程在普通车床上进行多头螺纹车削一直是一个加工难点:当第一条螺纹车成之后,需要手动进给小刀架并用百分表校正,使刀尖沿轴向精确移动一个螺距再加工第二条螺纹;或者打开挂轮箱,调整齿轮啮合相位,再依次加工其余各头螺纹。
受普通车床丝杠螺距误差、挂轮箱传动误差、小拖板移动误差等多方面的影响,多头螺纹的导程和螺距难以达到很高的精度。
而且,在整个加工过程中,不可避免地存在刀具磨损甚至打刀等问题,一旦换刀,新刀必须精确定位在未完成的那条螺纹线上。
这一切都要求操作者具备丰富的经验和高超的技能。
然而,在批量生产中,单靠操作者的个人经验和技能是不能保证生产效率和产品质量的。
在制造业现代化的今天,高精度数控机床和高性能数控系统的应用使许多普通机床和传统工艺难以控制的精度变得容易实现,而且生产效率和产品质量也得到了很大程度的保证。
下面我将从四个方面对数控车床加工多头螺纹进行分析:一、螺纹的基本特征在机械制造中,螺纹联接被广泛应用,例如数控车床的的主轴与卡盘的联结,方刀架上螺钉对刀具的紧固,丝杠螺母的传动等。
圆柱或圆锥母体表面上制出的螺旋线形的、具有特定截面的连续凸起部分。
螺纹按其母体形状分为圆柱螺纹和圆锥螺纹;按其在母体所处位置分为外螺纹、内螺纹,按其截面形状(牙型)分为三角形螺纹、矩形螺纹、梯形螺纹、锯齿形螺纹及其他特殊形状螺纹,三角形螺纹主要用于联接,矩形、梯形和锯齿形螺纹主要用于传动;按螺旋线方向分为左旋螺纹和右旋螺纹,一般用右旋螺纹;按螺旋线的数量分为单线螺纹、双线螺纹及多线螺纹;联接用的多为单线,传动用的采用双线或多线;按牙的大小分为粗牙螺纹和细牙螺纹等,按使用场合和功能不同,可分为紧固螺纹、管螺纹、传动螺纹、专用螺纹等。
数控编程车削螺纹进刀的几种方法比较汇总
数控编程车削螺纹进刀的几种方法比较摘要螺纹是机械行业中常见的零件,螺纹的车削是机械产品质量的重要环节,在车削加工中,螺纹车削由于切削速度较快,切削力较大和作用力集中,导致毛刺较大加工难度高。
本文结合编程实例从螺纹加工几种进刀方法来编辑程序进行讨论。
【关键词】螺纹直进法斜进法左右借刀法1. 螺纹分类介绍1.1.按连接可分为内螺纹和外螺纹1.2.按用途可分为⑴紧固螺纹:例如车床刀架上的螺钉⑵密封螺纹:例如管接头⑶传动螺纹:例如车床的丝杠1.3 按牙型可分为⑴三角形螺纹⑵矩形螺纹⑶圆形螺纹⑷梯形螺纹⑸锯齿形螺纹1.4 按螺旋线方向分为⑴右旋螺纹(顺时针旋入的螺纹为右旋螺纹)⑵左旋螺纹(逆时针旋入的螺纹为左旋螺纹)它们的判别方法:将螺纹竖直放置,螺旋线左边高为左旋反之则是右旋。
左旋螺纹右旋双线螺纹1.5按螺旋线可分为单线螺纹和多线螺纹1.6按母体形状可分为圆柱螺纹和圆锥螺纹2、螺纹的基本要数2.1 螺纹大径:是指螺纹的最大直径,是与外螺纹牙顶或内螺纹牙底相切的假想圆柱或圆锥的直径,通常我们用d/D表示。
2.2螺纹公称直径:它是代表螺纹尺寸的直径,一般是指螺纹大径的基本尺寸2.3螺纹小径:即螺纹的最小直径,是与外螺纹牙底或内螺纹牙顶相切的假想圆柱或圆锥的直径,通常我们用d1/D1表示。
2.4螺纹中径:是介于螺纹大径与小径之间,中径上牙型沟槽和凸起宽度相等,通常我们用d2/D2表示。
2.5螺距P:相邻两牙在中径线上对应两点间的轴向距离。
2.6导程:同一条螺旋线上相邻两牙在中径线上对应两点间的轴向距离。
2.7牙型高度:在螺纹牙型上牙顶到牙底在垂直于螺纹轴线方向上的距离。
2.8牙型角:在螺纹牙型上,相邻两牙侧间的夹角3.走刀路线的确定在数控车床上车螺纹时,沿螺距方向的, 向进给应和车床主轴的旋转保持严格的速比关系,考虑到刀具从停止状态到达指定的进给速度或从指定的进给速度降为零,驱动系统必有一个过渡过程,因此沿轴向进给的加工路线长度,除保证螺纹长度外,还应增加刀具引入距离和超越距离,引入距离和超越距离的数值与车床拖动系统的动态特性、螺纹的螺距和精度有关。
cnc数控加工常用的几种螺纹加工方法
螺纹加工是cnc数控加工非常重要的技术之一,螺纹的加工质量和效率将直接影响零件的加工质量及加工中心的生产效率。
随着cnc数控加工性能的提高及切削刀具的改进,螺纹加工的方法也在不断改进,螺纹加工的精度和效率也在逐渐提高。
为了使工艺人员能够在加工中合理选择螺纹加工方法,提高生产效率,避免质量事故,现将在实际中cnc数控加工常用的几种螺纹加工方法总结如下:首先来说:丝锥加工的分类及特点采用丝锥加工螺纹孔是最常用的加工方法,它主要适用于直径较小(D<30),孔位置精度要求不高的螺纹孔。
最早时期的技术师傅们,大多是用柔性攻丝方法来做的,不过柔性攻丝夹头结构复杂,成本较高,容易损坏,加工效率较低。
近年来,cnc数控加工的技术的逐步提高,刚性攻丝功能成为cnc数控加工的基本配置。
所以,之后刚性攻丝逐渐成为了螺纹加工的主要方法(刚性弹簧夹头夹持丝锥,主轴进给与主轴转速由机床控制保持一致)弹簧夹头相对于柔性攻丝夹头来说,结构简单,价格便宜,用途广泛,除夹持丝锥外,还可夹持立铣刀、钻头等刀具,可以降低刀具成本。
同时,采用刚性攻丝,可以进行高速切削,提高加工的效率,而且降低制造成本。
攻丝前螺纹底孔的确定螺纹底孔的加工对于丝锥的寿命、螺纹加工的质量等方面有较大影响。
通常,螺纹底孔钻头直径选择接近螺纹底孔直径公差的上限,例如,M8螺纹孔的底孔直径为Ф6.7+0.27mm,选择钻头直径为Ф6.9mm。
这样,可减少丝锥的加工余量,降低丝锥的负荷,提高丝锥的使用寿命。
关于丝锥的选择选择丝锥时,首先,必须按照所加工的材料选择相应的丝锥,刀具公司根据加工材料的不同生产不同型号的丝锥,选择时要特别注意。
因为丝锥相对于铣刀、镗刀来说,对被加工材料非常敏感。
例如,用加工铸铁的丝锥来加工铝件,容易造成螺纹掉牙、乱扣甚至丝锥折断,导致工件报废。
其次,应注意通孔丝锥与盲孔丝锥的区别,通孔丝锥前端引导较长,排屑为前排屑。
盲孔前端引导较短,排屑为后排屑。
数控车床中梯形螺纹(蜗杆)加工方法
数控车床中梯形螺纹(蜗杆)加工方法作者:李俊来源:《文理导航》2011年第20期通常车削梯形螺纹时,采用高速钢材料刀具进行低速车削,一般采用图1四种进刀方法:直进法、左右切削法、车直槽法和车阶梯槽法。
直进法适用于车削螺距较小(P4mm)的梯形螺纹常采用左右切削法、车直槽法和车阶梯槽法。
在这四种切削方法中,除直进法外,其他三种车削方法都能不同程度地减轻或避免三刃同时切削,使排屑较顺畅,刀尖受力、受热情况有所改善,从而不易出现振动和扎刀现象,还可提高切削用量,改善螺纹表面质量。
所以,左右切削法、车直槽法和车阶梯槽法获得了广泛的应用。
在数控车床上车削三角螺纹时一般可选用标准机夹刀具,利用螺纹循环指令完成加工。
但由于梯形螺纹较之三角螺纹,其螺距和牙型都大,而且精度高,牙型两侧面表面粗糙度值较小,致使梯形螺纹车削时,吃刀深,走刀快,切削余量大,切削抗力大,加之有些数控车床刚性较差,如果在切削过程中参数选择不合理就容易产生“扎刀”和“爆刀”现象。
采用斜进法对标准螺纹来说,由于有固定循环指令,较为方便,但对异型螺纹加工就不太方便。
下面介绍利用宏程序采用“分层法”切削加工梯形螺纹,该方法切削状况好,对刀具要求不高,尺寸由程序中相应数值保证,当牙顶宽和螺纹底径达到尺寸要求时,螺纹中径等其他各项尺寸也相应达到尺寸要求,尺寸精度易于控制,螺纹表面质量好,甚至蜗杆和其它异型螺纹的加工也可套用该方法的编程思路。
这里讲的“分层法”车削梯形螺纹实际上是直进法和左右切削法的综合应用。
在车削较大螺距的梯形螺纹时,“分层法”通常不是一次性就把梯形槽切出来,而是把牙槽分成若干层,每层深度根据实际机床情况可转化成若干个较浅的梯形槽来进行切削。
每一层的切削都采用左右交替车削的方法,背吃刀量很小,刀具只需沿左右牙型线切削,梯形螺纹车刀始终只有一个侧刃参加切削,从而使排屑比较顺利,刀尖的受力和受热情况有所改善,因此能加工出较高质量的梯形螺纹。
- 1、下载文档前请自行甄别文档内容的完整性,平台不提供额外的编辑、内容补充、找答案等附加服务。
- 2、"仅部分预览"的文档,不可在线预览部分如存在完整性等问题,可反馈申请退款(可完整预览的文档不适用该条件!)。
- 3、如文档侵犯您的权益,请联系客服反馈,我们会尽快为您处理(人工客服工作时间:9:00-18:30)。
数控编程车削螺纹进刀的几种方法比较
摘要
螺纹是机械行业中常见的零件,螺纹的车削是机械产品质量的重要环节,在车削加工中,螺纹车削由于切削速度较快,切削力较大和作用力集中,导致毛刺较大加工难度高。
本文结合编程实例从螺纹加工几种进刀方法来编辑程序进行讨论。
【关键词】螺纹直进法斜进法左右借刀法
1. 螺纹分类介绍
1.1.按连接可分为内螺纹和外螺纹
1.2.按用途可分为⑴紧固螺纹:例如车床刀架上的螺钉
⑵密封螺纹:例如管接头
⑶传动螺纹:例如车床的丝杠
1.3 按牙型可分为⑴三角形螺纹
⑵矩形螺纹
⑶圆形螺纹
⑷梯形螺纹
⑸锯齿形螺纹
1.4 按螺旋线方向分为
⑴右旋螺纹(顺时针旋入的螺纹为右旋螺纹)
⑵左旋螺纹(逆时针旋入的螺纹为左旋螺纹)
它们的判别方法:将螺纹竖直放置,螺旋线左边高为左旋反之则是右旋。
左旋螺纹右旋双线螺纹
1.5按螺旋线可分为单线螺纹和多线螺纹
1.6按母体形状可分为圆柱螺纹和圆锥螺纹
2、螺纹的基本要数
2.1 螺纹大径:是指螺纹的最大直径,是与外螺纹牙顶或内螺纹牙底相切的假想圆柱或圆锥的直径,通常我们用d/D表示。
2.2螺纹公称直径:它是代表螺纹尺寸的直径,一般是指螺纹大径的基本尺寸
2.3螺纹小径:即螺纹的最小直径,是与外螺纹牙底或内螺纹牙顶
相切的假想圆柱或圆锥的直径,通常我们用d1/D1表示。
2.4螺纹中径:是介于螺纹大径与小径之间,中径上牙型沟槽和凸
起宽度相等,通常我们用d2/D2表示。
2.5螺距P:相邻两牙在中径线上对应两点间的轴向距离。
2.6导程:同一条螺旋线上相邻两牙在中径线上对应两点间的轴向距离。
2.7牙型高度:在螺纹牙型上牙顶到牙底在垂直于螺纹轴线方向上的距离。
2.8牙型角:在螺纹牙型上,相邻两牙侧间的夹角
3.走刀路线的确定
在数控车床上车螺纹时,沿螺距方向的, 向进给应和车床主轴的旋转保持严格的速比关系,考虑到刀具从停止状态到达指定的进给速度或从指定的进给速度降为零,驱动系统必有一个过渡过程,因此沿轴向进给的加工路线长度,除保证螺纹长度外,还应增加刀具引入距离和超越距离,引入距离和超越距离的数值与车床拖动系统的动态特性、螺纹的螺距和精度有关。
4.螺纹车刀的选用
螺纹车刀属于成形刀具,要保证螺纹牙型的精度,对螺纹车刀的要求主要有以下几点:
4.1螺纹车刀刀尖角一定要等于螺纹的牙型角;如普通三角螺纹为60°梯形螺纹为29°等。
4.2螺纹精车时车刀的纵向前角应等于0°;粗车时允许有5°到15°的纵向前角。
4.3因受螺纹升角的影响车刀两侧的静止后角应不相等,进给方向侧的后角较大,一般应保证两侧面均有3°到5°的工作后角。
4.4侧刃的直线性要好。
制造螺纹车刀的材料有高速钢和硬质合金两种。
高速钢螺纹车刀刃磨方便、切削刃锋利、韧性好,能承受较大的切削冲击力,加工的螺纹表面粗糙度小。
但它的耐热性差,不宜高速车削。
硬质合金螺纹车刀的硬度高、耐磨性好、耐高温,但抗冲击能力差。
数控车床一般选用硬质合金可转位车刀。
螺纹车刀刀片有全牙型刀片、泛螺距刀片、多齿刀片三种。
由于泛螺距刀片可加工刀尖角相同螺距不同的螺纹,所以应用广泛。
采用泛螺距刀片时,外螺纹的外径、内螺纹的内径须在螺纹加工前车削到正确的直径。
5.加工螺纹进刀方法
5.1直进法:一般的螺纹,小螺距,细牙螺纹都可以采用直进法。
直进法加工是在加工过程中对刀具的Z轴(轴向方向)不进行改变,分次进给(直径方向),来完成螺纹的切削。
5.2左右借刀法:对于加工大螺距的螺纹,多头螺纹等零件,由于加工面太宽,接触面大。
用直进法的话,对于机床,刀具,工件都会产生很大的影响,甚至产生打刀,蒙车等现象。
所以只有采取左右进刀法来完成加工方法为,通过改变Z轴的方向,也就是进刀起始点,来完成对螺纹一个侧面的加工,完了在加工另一侧面,最后对两侧面和底面修光。
的这种方法叫左右进刀法。
5.3斜进法:对于加工大螺距的螺纹,多头螺纹等零件,由于加工量太大,接触面大。
用直进法的话,对于机床,刀具,工件都会产生很大的影响,甚至产生打刀,蒙车等现象,采用左右进刀编程较为
复杂。
所以,采取斜向进刀法来完成比较方便,通过改变Z轴的方向,也就是进刀起始点,来完成对螺纹一个侧面的加工,完了在加工另一侧面,最后对两侧面和底面修光。
6.车削螺纹时的转速的确定
在车削螺纹时,车床的主轴转速将受到螺纹的螺距的大小、驱动电机的升降频特性及螺纹插补运算速度等多种因素影响,故对于不同的数控系统,推荐有不同的主轴转速选择范围。
例如:大多数经济型车床数控系统推荐车螺纹时的主轴转速如下:
N=1200/P-K
注:其中p是螺纹的螺距<mm>,k是保险系数,一般取为80。
7.走刀次数和背吃刀量的确定
螺纹加工中的走刀次数和背吃刀量会直接螺纹的加工质量,车削螺纹时的走刀次数和背吃刀量可常考一下表格:
普通螺纹走刀次数和背吃刀量的参考表:
三种进刀方法如图示:
8.编程方法 8.1斜进法编程: O0001;FANUC 系统程序名 T0101;刀具号
M03 S600;主轴正转600r/min
G00 X32 Z5; 快速点定位至加工起始点 #1=0;设定Z 轴参数
#2=0.1; 设定变量为切削深度
N10 G0 X[30-#1];快速定位至螺纹加工起始点
Z[5-#2/sin60°];快速定位至螺纹Z向起始点
G32 Z-15;螺纹加工
#1=#1-#2;螺纹深度变量递减
IF[#1 GE 0.975]GOTO10;条件跳转,如果#1大于或等于0.975跳转到N10段继续执行
G0X80;快速退刀X直径方向80mm处
Z100;快速退刀Z方向100mm处
M30;程序结束并返回加工起始点
8.2直进法编程:
O0001;程序名
T0101;刀具号、刀补号分别为1号
M03 S600;主轴正转,600r/min
G00 X32 Z5;快速点定位至毛坯外切削加工起始点
#1=0;设定Z轴变量
N10 G0 X[30-#1];设置每刀切削加工起始直径
G32 Z-15 F1.5;螺纹加工Z轴方向15mm,螺距为1.5
G0 X32;快速退刀点定位至毛坯外直径X向32mm
Z5;快速退刀定位至毛坯外Z向5mm
#1=#1+0.2;Z轴方向每刀切削加深0.2mm
IF [#1 LE 0.975] GOTO10;条件跳转,如果#1小于或等于0.975跳转到N10段继续执行
G0 X80;X向快速退刀80mm处
Z100; Z向快速退刀100mm处
M30;程序结束并返回加工起始点
8.3左右借刀法编程
O0001;FANUC系统程序名
T0101;刀具号
M03 S600;主轴正转,600r/min
G00 X32 Z5;快速点定位至加工起始点
#1=0;Z轴变量
G0 X[30-#1];定位到螺纹切削深度
Z[5-#2*sin15°];定位到左侧螺纹加工起始点
G32 Z-15 F1.5;螺纹加工
G0 X32;快速退刀至X32
Z[5+#2*sin15°];定位到右侧螺纹加工起始点
G32 Z-15 F1.5;螺纹加工
G0 X32 ; X向快速退刀32mm处
Z100;Z向快速退刀100mm处
M30;程序结束并返回加工起始点
通过对同一螺纹三种不同的编程方法进行分析,可以知道采用G76编程最为方便,程序段最少,但参数计算比较复杂,实际加工中
若参数设置不当,很容易造成撞刀现象,采用G32编程,程序段长,一般很少采用这个方法。
采用G92编程,条理很清晰并且走刀路线直观,又因为程序段不是太长,所以在实际加工中大多采用此种方法。
9.论文总结
在实际的加工生产中,以上措施有效地解决了经济型数控车床加工螺纹时进刀的问题,合理利用机床和刀具切削进给,提高了加工效率,减轻了车床操作者的劳动强度,提高了生产效率,保证了零件的加工质量。
总而言之,数控车床在机械制造业中的应用越来越广泛,我们要善于分析,不断总结,掌握一定的编程技巧,编制出合理、高效的加工程序,多学习先进的加工技术,使数控车床的功能得到合理的应用与充分的发挥,保证高效率、高标准的完成零件的加工。
参考文献:
1.董国成.《车工工艺与技能训练》人民邮电出版社 2009.10
2.张超英.《数控编程技术-手工编程》化学工业出版社2008.4
3.裴炳海.《数控加工工艺与编程》机械工业出版社 2008.4
4.。