车削螺纹的计算
车螺纹的方法

车螺纹简介(图)将工件表面车削成螺纹的方法称为车螺纹。
螺纹按牙型分有三角螺纹、梯形螺纹、方牙螺纹等(图1)。
其中普通公制三角螺纹应用最广。
图1 螺纹的种类1. 普通三角螺纹的基本牙型普通三角螺纹的基本牙型如图2所示,各基本尺寸的名称如下:图2 普通三角螺纹基本牙型D—内螺纹大径(公称直径);d—外螺纹大径(公称直径);D2 —内螺纹中径;d2—外螺纹中径;D1 —内螺纹小径;d1—外螺纹小径;P—螺距;H-原始三角形高度。
决定螺纹的基本要素有三个:牙型角α 螺纹轴向剖面内螺纹两侧面的夹角.公制螺纹α=60o,英制螺纹α=55o。
螺距P 它是沿轴线方向上相邻两牙间对应点的距离.螺纹中径D2(d2)它是平螺纹理论高度H的一个假想圆柱体的直径。
在中径处的螺纹牙厚和槽宽相等。
只有内外螺纹中径都一致时,两者才能很好地配合.从图上可以看出:车削外螺纹时,应该将外径车削为:车削外螺纹外径=公称直径-2*H/8其中H为螺纹原始三角形高度,计算公式为H=0.866*P(P为螺距,根据手册可以查出)车削内螺纹时,孔径应为:车削内螺纹孔径=公称直径-2*5/8H *5/8=0。
625 1/8=0。
125以车削方式制作M20X2.5的粗牙螺纹为例:螺栓坯料外径=20—2*((0。
866*2.5)/8)=19.46螺母坯料内径=20-2*((0。
866*2.5)*5/8)=17。
29这样车制出来的螺纹仅仅是牙面配合,不会出现牙顶与牙底干涉的情况。
使用板牙、丝锥做作螺纹时,由于加工时的挤压作用,因此上述公式不能适合(根据材料不同而选择另外的公式2. 车削外螺纹的方法与步骤(1)准备工作1)安装螺纹车刀时,车刀的刀尖角等于螺纹牙型角α=60o,其前角γo=0o才能保证工件螺纹的牙型角,否则牙型角将产生误差。
只有粗加工时或螺纹精度要求不高时,其前角可取γo=5o~20o。
安装螺纹车刀时刀尖对准工件中心,并用样板对刀,以保证刀尖角的角平分线与工件的轴线相垂直,车出的牙型角才不会偏斜。
车螺纹进刀深度计算公式

车螺纹进刀深度计算公式车螺纹是一种常见的机械连接元件,广泛应用于汽车、机械设备等领域。
在车螺纹加工过程中,进刀深度的计算是十分重要的,它直接影响到车螺纹的质量和工作性能。
本文将介绍车螺纹进刀深度的计算公式及其相关知识。
一、车螺纹进刀深度的定义车螺纹进刀深度是指车刀相对于螺纹轴线的进刀距离,也就是车刀在车削过程中与工件表面的接触深度。
进刀深度的选择要根据螺纹的形状、尺寸、材料等因素进行合理的计算和确定,以确保螺纹的加工质量。
二、车螺纹进刀深度计算公式车螺纹进刀深度的计算公式可以根据螺纹的类型和标准进行选择。
下面以常见的ISO标准螺纹为例,介绍车螺纹进刀深度的计算公式。
1. 内螺纹进刀深度计算公式:对于内螺纹,其进刀深度计算公式为:进刀深度= (0.5 × P) + C其中,P为螺距,C为余量。
螺距是指螺纹的一个周期所包含的螺纹数量,它是螺纹的一个重要参数。
余量是为了确保内螺纹的质量和配合要求而设置的,一般为正值。
2. 外螺纹进刀深度计算公式:对于外螺纹,其进刀深度计算公式为:进刀深度= (0.5 × P) + C其中,P和C的含义同上。
三、车螺纹进刀深度计算实例下面以M12×1.5的内螺纹为例,介绍车螺纹进刀深度的具体计算过程。
1. 计算螺距:根据M12×1.5的规格,可知其螺距为1.5mm。
2. 计算余量:根据螺纹的配合要求和加工经验,假设余量为0.1mm。
3. 计算进刀深度:根据内螺纹进刀深度计算公式,可知进刀深度= (0.5 × 1.5) + 0.1= 0.85mm。
因此,M12×1.5的内螺纹进刀深度为0.85mm。
四、进刀深度的影响因素车螺纹的进刀深度不仅与螺纹的规格有关,还受到以下因素的影响:1. 工件材料:不同材料的工件对进刀深度有不同的要求,如硬度大的材料要求进刀深度小。
2. 切削刃形状:车刀的切削刃形状也会对进刀深度产生影响,不同刃形的车刀对进刀深度的要求不同。
普通车床螺纹车削加工讲义

3 ) 车螺纹大径φ24
0 -0.23
4 ) 切槽
三.典型普通螺纹零件的车削加工
2. 确定加工步骤
5 ) 倒角
6 ) 车螺纹
三、典型普通螺纹零件的车削加工
3.选择刀具及切削用量
序 号
加工内容
刀具 名称
1 端面 端面刀
2
φ 24、φ 30外 圆
外圆刀
3
退刀槽
4×φ21.5
切槽刀
螺纹
4 M24X1.5— 螺纹刀
合理分配螺纹加工余量
(一般粗车ap:0.10~0.50;精车ap:0.01~0.10 。)
进刀次数 第一次进刀 第二次进刀 第三次进刀 第四次进刀 第五次进刀 第六次进刀
背吃刀量 ap=0.50mm ap=0.15mm ap=0.10mm ap=0.03mm ap=0.02mm ap=0.01mm
加工步骤 粗加工
三、典型普通螺纹零件的车削加工
7. 螺纹车削操作方法与步骤
1)正反车车削法
开车,对刀
合闸,车螺纹
横向退刀,停车, 反转,纵向回起点
快速退出
开车切削 开反车返回
多刀循环加工
进刀
三、典型普通螺纹零件的车削加工
7. 螺纹车削操作方法与步骤
2)抬闸法 利用开合螺母的压下和抬起来车削螺纹。
控制手柄
正反车车削法
车端面 车螺纹大径 车退刀槽 倒角 车螺纹
d<公称直径 <螺纹小径
多刀车削
三.典型普通螺纹零件的车削加工
1. 分析零件图
查表或计算 d=φ 24 0 -0.23
d2=d-0.6495P=φ 23.026-00.19
三.典型普通螺纹零件的车削加工
车削螺纹
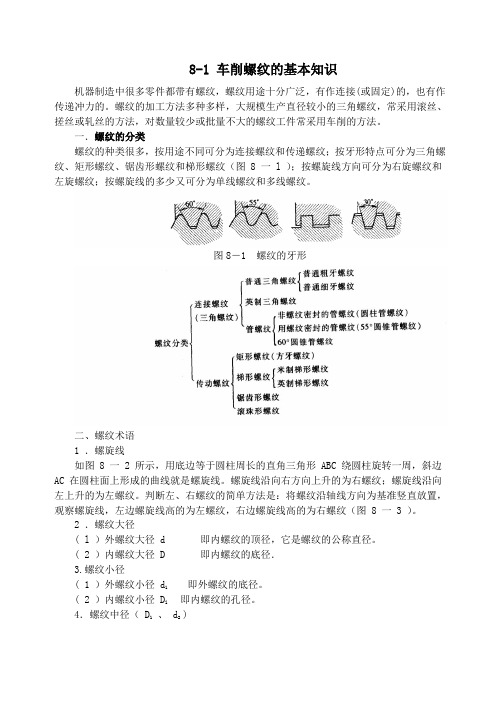
8-1 车削螺纹的基本知识机器制造中很多零件都带有螺纹,螺纹用途十分广泛,有作连接(或固定)的,也有作传递冲力的。
螺纹的加工方法多种多样,大规模生产直径较小的三角螺纹,常采用滚丝、搓丝或轧丝的方法,对数量较少或批量不大的螺纹工件常采用车削的方法。
一.螺纹的分类螺纹的种类很多,按用途不同可分为连接螺纹和传递螺纹;按牙形特点可分为三角螺纹、矩形螺纹、锯齿形螺纹和梯形螺纹(图 8 一 l );按螺旋线方向可分为右旋螺纹和左旋螺纹;按螺旋线的多少又可分为单线螺纹和多线螺纹。
图8-1 螺纹的牙形二、螺纹术语1 .螺旋线如图 8 一 2 所示,用底边等于圆柱周长的直角三角形 ABC 绕圆柱旋转一周,斜边AC 在圆柱面上形成的曲线就是螺旋线。
螺旋线沿向右方向上升的为右螺纹;螺旋线沿向左上升的为左螺纹。
判断左、右螺纹的简单方法是:将螺纹沿轴线方向为基准竖直放置,观察螺旋线,左边螺旋线高的为左螺纹,右边螺旋线高的为右螺纹(图 8 一 3 )。
2 .螺纹大径( l )外螺纹大径 d 即内螺纹的顶径,它是螺纹的公称直径。
( 2 )内螺纹大径 D 即内螺纹的底径.3.螺纹小径( 1 )外螺纹小径 d1即外螺纹的底径。
( 2 )内螺纹小径 D l 即内螺纹的孔径。
4.螺纹中径( D1、 d2 )图8-2 螺旋线的简单形成原理图8-3 三角形螺纹各部分名称中径是螺纹的重要尺寸,螺纹配合时就是靠在中径线上内、外螺纹中径接触来实现传递动力或紧固作用。
螺纹中径是一个假想圆柱的直径,该圆柱的母线通过螺纹的牙宽和槽宽正好相等时,这个假想圆柱的直径就是螺纹的中径。
外螺纹和内螺纹的中径相等,即 D2 = d2。
5 .螺纹直径螺纹直径是指代表螺纹尺寸的直径,即公称直径。
6 .螺距 P相邻两牙在中径线上对应两点间的轴向距离。
7 .导程 L在同一螺旋线上,相邻两牙在中径线上对应两点间的轴向距离。
多线螺纹导程和螺距的关系是:L = nP ( 8 一 1 ) 式中: L 一螺纹的导程, mm ;n 一多线螺纹的线数;P 一螺距, mm 。
多线梯形螺纹的车削
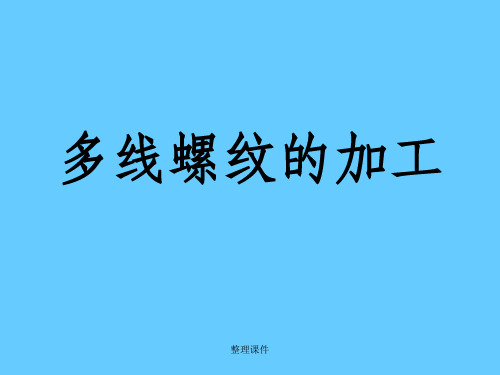
整理课件
七、加工步骤
1、车削工件端 面,车出即 可。
整理课件
2、打中心孔 φ3A。
整理课件
3、车螺纹外圆 φ控4制0 长0 0度.375至及 65。
整理课件
整理课件
4、按图纸要求
切出 3215
退刀槽(保证 螺纹外圆长
50),螺纹外 圆两边倒
角445。
5、按导程 (12mm)调整 走刀箱各手柄位 置。
• 导程L:同一螺旋 线上相邻两牙在中 径线上对应两点间 的轴向距离L。
• 导程L= 线数n×螺 距P。
整理课件
• 螺旋升角ψ : 由于多线螺纹的导程增
大一般应考虑其螺旋升角的 影响。螺纹升角对车刀工作 角度有较大的影响,即在车 右螺纹时左侧的后角等于工 作后角加上螺纹升角,而右 侧后角等于工作后角减去螺 纹升角。 tanψ=L/πd2=nP/πd2
多线螺纹的加工
整理课件
一、多线螺纹练习图
4×15°
I
4×15°
1.6
全部
Tr40×12(P6)-8e
32
12
I
6
15° ±15′ 15° ±15′ 2:1
50 65
40 -00.375
37 --00..519148
33 -00.649
练习内容 多线螺纹加工
材料 规格 5# φ45×150
件数 工时(min)
注意底径的的深度要 符合图
2)第一条螺旋线侧面 1(见图)加工完,将 车刀向前移动一个螺 距,加工第二条螺旋 线的同一侧面2(见 图)。注意小滑板向 前移动一个螺距,中 滑板刻线读数与前条 螺旋槽加工成一致。 这是为了保证第一条 螺纹深度与第二条的 螺纹深度一致。
车螺纹
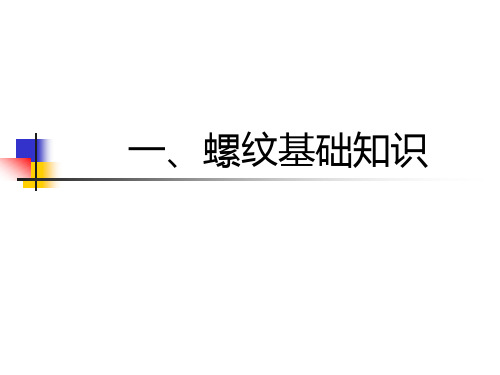
例:
T0202;(退刀槽加工) S400; G00 X22.0 Z-19.0; G75 R0.5; G75 X16.0 Z-20.0 P1000 Q1000
F20.0; G00 X100.0 Z50.0; T0303;(螺纹加工) G00 X22.0 Z2.0; G76 P020060 Q100 R300; G76 X16.75 Z-18.0 P1624 Q500 F2.5; G00 X100.0 Z50.0; T0202;(工件切断) S200; G00 X40.0 Z-53.0; G01 X2.0 F20.0; X40.0; G00 X100.0 Z50.0; M05; M30;
Z-30; N20 X35; G70 P10 Q20; G00 G40 X100 Z50;
T0202 S300;(退刀槽加工) G00 X35 Z-30; G01 X26 F30; G04 X4; G01 X35; G00 X100 Z50;
T0303; M03 S400; G00 X29.1 Z5 ; G32 Z-28 F2; G00 X31;
试用G32指令编写螺纹加工程序。
2、螺纹切削循环 G92
格式:
G92 X(U)_Z(W)_R_F_;
锥螺纹起点半径与 终点半径的差值
用G92进行圆柱螺纹加工
45°
X
Z
W
4(R)
3(F) 2(F)
R
1(R)
O
XU 22
R<0
Z
用G92进行圆锥螺纹加工
例:
T0303; M03 S400; G00 X29.1 Z5 ; G32 Z-28 F2; G00 X31;
公制螺纹 2.0
1.299 0.9 0.6 0.6
npt螺纹车削锥度算法
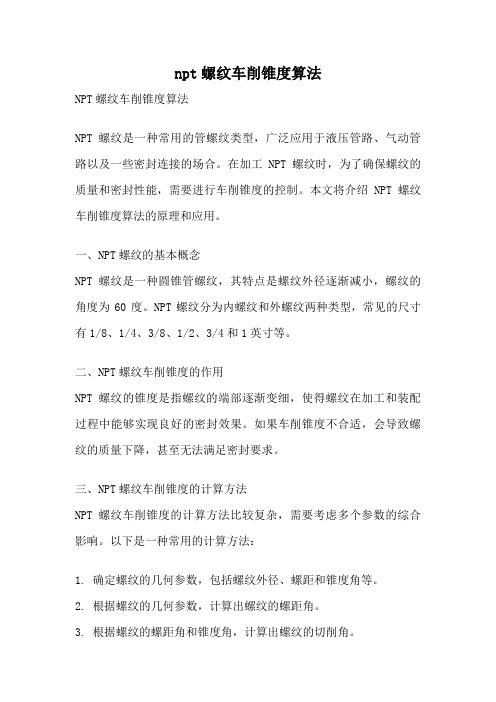
npt螺纹车削锥度算法NPT螺纹车削锥度算法NPT螺纹是一种常用的管螺纹类型,广泛应用于液压管路、气动管路以及一些密封连接的场合。
在加工NPT螺纹时,为了确保螺纹的质量和密封性能,需要进行车削锥度的控制。
本文将介绍NPT螺纹车削锥度算法的原理和应用。
一、NPT螺纹的基本概念NPT螺纹是一种圆锥管螺纹,其特点是螺纹外径逐渐减小,螺纹的角度为60度。
NPT螺纹分为内螺纹和外螺纹两种类型,常见的尺寸有1/8、1/4、3/8、1/2、3/4和1英寸等。
二、NPT螺纹车削锥度的作用NPT螺纹的锥度是指螺纹的端部逐渐变细,使得螺纹在加工和装配过程中能够实现良好的密封效果。
如果车削锥度不合适,会导致螺纹的质量下降,甚至无法满足密封要求。
三、NPT螺纹车削锥度的计算方法NPT螺纹车削锥度的计算方法比较复杂,需要考虑多个参数的综合影响。
以下是一种常用的计算方法:1. 确定螺纹的几何参数,包括螺纹外径、螺距和锥度角等。
2. 根据螺纹的几何参数,计算出螺纹的螺距角。
3. 根据螺纹的螺距角和锥度角,计算出螺纹的切削角。
4. 根据螺纹的切削角,计算出螺纹的切削量。
5. 根据螺纹的切削量,调整车床的进给量和车削速度,进行螺纹的车削加工。
四、NPT螺纹车削锥度算法的应用NPT螺纹车削锥度算法在实际生产中具有重要的应用价值。
通过合理控制车削锥度,可以提高螺纹的加工质量和密封性能,确保产品的可靠性和安全性。
1. 在加工过程中,需要根据螺纹的规格和要求,选择合适的车削工具和工艺参数。
2. 在车削过程中,要及时调整车床的进给量和车削速度,确保螺纹的切削量在合理范围内。
3. 在车削完成后,要进行螺纹的检测和测量,确保螺纹的尺寸和形状符合要求。
NPT螺纹车削锥度算法是一种重要的加工控制方法,对于确保螺纹的质量和密封性能具有重要意义。
在实际生产中,需要根据具体情况和要求,选择合适的车削工具和工艺参数,确保螺纹的加工质量和密封性能满足要求。
车削螺距为6的梯形螺纹
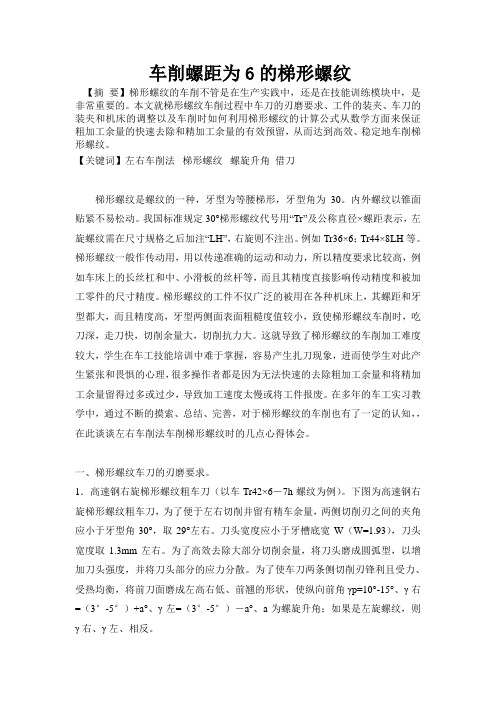
车削螺距为6的梯形螺纹【摘要】梯形螺纹的车削不管是在生产实践中,还是在技能训练模块中,是非常重要的。
本文就梯形螺纹车削过程中车刀的刃磨要求、工件的装夹、车刀的装夹和机床的调整以及车削时如何利用梯形螺纹的计算公式从数学方面来保证粗加工余量的快速去除和精加工余量的有效预留,从而达到高效、稳定地车削梯形螺纹。
【关键词】左右车削法梯形螺纹螺旋升角借刀梯形螺纹是螺纹的一种,牙型为等腰梯形,牙型角为30。
内外螺纹以锥面贴紧不易松动。
我国标准规定30°梯形螺纹代号用“Tr”及公称直径×螺距表示,左旋螺纹需在尺寸规格之后加注“LH”,右旋则不注出。
例如Tr36×6;Tr44×8LH等。
梯形螺纹一般作传动用,用以传递准确的运动和动力,所以精度要求比较高,例如车床上的长丝杠和中、小滑板的丝杆等,而且其精度直接影响传动精度和被加工零件的尺寸精度。
梯形螺纹的工件不仅广泛的被用在各种机床上,其螺距和牙型都大,而且精度高,牙型两侧面表面粗糙度值较小,致使梯形螺纹车削时,吃刀深,走刀快,切削余量大,切削抗力大。
这就导致了梯形螺纹的车削加工难度较大,学生在车工技能培训中难于掌握,容易产生扎刀现象,进而使学生对此产生紧张和畏惧的心理,很多操作者都是因为无法快速的去除粗加工余量和将精加工余量留得过多或过少,导致加工速度太慢或将工件报废。
在多年的车工实习教学中,通过不断的摸索、总结、完善,对于梯形螺纹的车削也有了一定的认知,,在此谈谈左右车削法车削梯形螺纹时的几点心得体会。
一、梯形螺纹车刀的刃磨要求。
1.高速钢右旋梯形螺纹粗车刀(以车Tr42×6-7h螺纹为例)。
下图为高速钢右旋梯形螺纹粗车刀,为了便于左右切削并留有精车余量,两侧切削刃之间的夹角应小于牙型角30°,取29°左右。
刀头宽度应小于牙槽底宽W(W=1.93),刀头宽度取1.3mm左右。
为了高效去除大部分切削余量,将刀头磨成圆弧型,以增加刀头强度,并将刀头部分的应力分散。
- 1、下载文档前请自行甄别文档内容的完整性,平台不提供额外的编辑、内容补充、找答案等附加服务。
- 2、"仅部分预览"的文档,不可在线预览部分如存在完整性等问题,可反馈申请退款(可完整预览的文档不适用该条件!)。
- 3、如文档侵犯您的权益,请联系客服反馈,我们会尽快为您处理(人工客服工作时间:9:00-18:30)。
8-2三角螺纹的计算一、三角螺纹的尺寸计算1 .普通三角螺纹的尺寸计算普通三角螺纹牙形如图、尺寸计算公式参看下表。
例:试计算三角螺纹M20 xZ 的牙形高2 .英制三角螺纹的尺寸计算英制三角螺纹的牙形如图6 一10 ,尺寸计算公式见表 6 一3 。
二、三角形螺纹车刀1 .对螺纹车刀的要求螺纹车刀属于成形刀具,要保证螺纹牙形精度,必须正确刃磨和安装车刀。
对螺纹车刀的要求主要有以下几点:( 1 )车刀的刀尖角一定要等于螺纹的牙形角。
( 2 )精车时车刀的纵向前角应等于零度;粗车时允许有5 o一15o的纵向前角。
( 3 )因受螺纹升角的影响,车刀两侧面的静止后角应刃磨得不相等,进给方向后面的后角较大,一般应保证两侧面均有3o一5o的工作后角。
( 4 )车刀两侧刃的直线性要好。
2 .普通三角螺纹车刀车刀从材料上分有高速钢螺纹车刀和硬质合金螺纹车刀两种。
( l )高速钢螺纹车刀高速钢螺纹车刀刃磨方便、切削刃锋利、韧性好,能承受较大的切削冲击力,车出螺纹的表面粗糙度小。
但它的耐热性差,不宜高速车削,所以常用来低速车削或作为螺纹精车刀。
高速钢螺纹车刀的几何形状如图8-10所示。
高速钢三角螺纹车刀的刀尖角一定要等于牙形角。
当车刀的纵向前角0o时,车刀两侧刃之间夹角等于牙形角;若纵向前角不为O o时,车刀两侧刃不通过工件轴线,车出螺纹的牙形不是直线而是曲线。
当车削精度要求较高的三角螺纹时,一定要考虑纵向前角对牙形精度的影响。
为车削顺利,纵向前角常选在5 o一15o之间,这时车刀两侧刃的夹角不能等于牙形角,而应当比牙形角小30 ’一1o30’。
应当注意.纵向前角不能选得过大,若纵向前角过大,不仅影响牙形精度,而且还容易引起扎刀现象。
车螺纹时,由于螺纹升角的影响,造成切削平面和基面的位置变化,从而使车刀工作时的前角和后角与车刀静止时的前角和后角不相等。
螺纹升角越大,对工作时的前角和后角影响越明显。
当车刀的静止前角为零度时,螺纹升角能使进给方向一侧刀刃的前角变为正值,而使另一侧前角变为负值,使切削不顺利、排屑也困难。
为改善切削条件,应采取垂直装刀方法,即让车刀两侧刃组成的平面和螺旋线方向垂直,使两侧刃的工作前角均为零度;或在车刀前刀面上沿两侧切削刃方向磨出较大前角的卷屑槽。
螺纹升角能使车刀沿进给一方的工作后角变小,而使另一面的工作后角增大,为切削顺利,保证车刀强度,车刀刃磨时,一定要考虑螺纹升角的影响,把进给方向一面的后角磨成工作后角加上螺纹升角,即(3o一5o )+Ψ;另一面的后角磨成工作后角减去一个螺纹升角,即(3o一5o )-Ψ。
( 2 )硬质合金螺纹车刀硬质合金螺纹车刀的硬度高、耐磨性好、耐高温,但抗冲击能力差。
车削硬度较高的工件时,为增加刀刃强度,应在车刀两切削刃上磨出宽度为0 . 2 mm 一0 . 4 mm 的负倒棱。
高速车削螺纹时,因挤压力较大会使牙形角增大,所以车刀的刀尖角应磨成59o30 ' ,硬质合金车刀的几何形状如图8一12 所示。
8-11 高速钢外螺纹车刀三、车螺纹时交换齿轮的计算车削螺纹时,一般都是根据图样上工件的螺距(或导程),在进给箱的铭牌上查出和工件螺距相同的数值,然后把几个手柄扳置在对应的位置上即可开始车削。
但是,在车削非标准螺距螺纹、精密螺纹或铭牌上没有螺距的螺纹时,都必须计算交换齿轮,正确安装交换齿轮才能满足车削的需要。
1 .直联丝杠时交换齿轮的计算图8-12硬质合金三角螺纹车刀车削螺纹时的传动过程如图8-13所示,其具体传递步骤是:主轴三星齿轮(如图8-13所示,不改变传动比,只改变丝杠转向)交换齿轮(改变传动比)进给箱(直联丝杠)经开合螺母至床鞍刀架(车螺纹)图8-13直联丝杠车螺纹传动过程示意图车削螺纹时,车刀的进给量必须等于工件的螺距(或导程),即工件转一圈车刀沿纵向移动的距离正好等于工件的螺距(或导程)。
交换齿轮的计算:由图8-15可以看出交换齿轮的传动比、工件螺距和和丝杠螺距、工件转数和丝杠转数之间的关系。
如丝杠螺距为6mm,车削工件的螺距也为6mm时,工件转一圈丝杠也正好转一圈,即工件螺距×工件转速=丝杠转速×丝杠螺距,也就是1×6=1×6若车削工件螺距为2mm时,工件转3转而丝杠转1转,同样有工件螺距×工件转速=丝杠转速×丝杠螺距,即:2×3=1×6;若车削工件螺距为1mm时,工件转6转而丝杠转1转,仍然是工件螺距×工件转速=丝杠转速×丝杠螺距,即1×6=1×6。
图8-14 三星齿轮图8-15 导程大小与传动比的关系(8-5)根据公式(8一5 )计算交换齿轮时,有时只需要一对齿轮就可满足传动比的称为单式轮系(图8 一16a )。
如采用单式轮系无法满足传动比时,需要用两对齿轮搭配才能获得正确传动比的称为复式轮系(图8 一16b )。
在无进给箱车床上备有的交换齿轮的齿数有:20 , 25 , 30 , 35 , 40 , 45 , 50 , 55 , 60 , 65 , 70 , 75 , 80 , 85 , 90 , 95 , 100 , 105 , 110 , 120 , 127 等。
2 .交换齿轮的搭配原则有时计算出来的复式轮系虽然速比正确,但不一定都能在交换齿轮架上正确啮合,不是一个齿轮顶在另一个齿轮的轴上,就是另一对齿轮啮合不上,因此采用复式轮系时,必须符合下列两条搭配原则:图8-16 单式轮系和复式轮系应当注意:有些车床交换齿轮架z1 的心轴距车床主轴距离较近,若:z1选得太大,很可能会使z1,顶在主轴上,或者根本装不上,因此:z1的齿数应不大于80 。
例若计算出的复式轮系z1 = 20 、z2 = 40 、z3=80 、z4=100 ,问它们能否搭配?解:20 + 40 < 80 + 1580 + 100 > 40 + 15因只符合一条搭配原则,所以不能搭配。
如果计算出的交换齿轮不符合搭配原则,应在不改变传动比的情况下,可以采用主动轮与主动轮或从动轮与从动轮互换位置,主动轮与主动轮或从动轮与从动轮之间互借倍数、主动轮与从动轮同时扩大或缩小相同的倍数等方法来解决。
例在丝杠螺距为12 mm 车床上,直联丝杠车削螺距为1 . 5 mm 的螺纹,试计算交换齿轮。
解:根据公式(8 一 5 )得:例用丝杠螺距12mm的车床,直联丝杠车削每英寸4 牙的英制螺纹,试计算交换齿轮。
例在丝杠螺距为每英寸4 牙的英制车床上,直联丝杠车削螺距为2 mm 的米制螺纹,试求交换齿轮。
根据公式(8-5)得:3 .经进给箱变速时交换齿轮的计算在普通车床上,车削铭牌上没有螺距螺纹时,应根据车床上备有的齿轮,经过计算交换齿轮并配合进给箱的变速机构,也可以满足传动比的需要,车出符合要求的螺纹,其计算公式是:(8-6)C618 车床进给箱铭牌(部分)如下表8 一10 所示。
C618 车床备有的交换齿轮的齿数有:36 , 44 , 45 , 48 , 70 , 80 , 90 , % , 120 , 127 等。
若上述齿轮仍不能满足需要,应根据计算结果再制造新的齿轮。
例在C618 车床上车削螺距为 5 . 5 mm 的螺纹,试求交换齿轮。
解:已知P= 5 . 5 mm在铭牌上选取P铭二1.25mm表8-10 C618 车床进给箱铭牌(部分)应当注意:安装交换齿轮时,为了安全一定要切断电源;保证齿轮之间有0.1-0.2的啮合间隙;加注润滑脂,保证套和心轴之间的正常润滑。
四、车削三角螺纹车削三角螺纹的方法有低速车削和高速车削两种。
低速车削使用高速钢螺纹车刀,高速车削使用硬质合金螺纹车刀。
低速车削精度高,表面粗糙度值小,但效率低。
高速车削效率高,能比低速车削提高15 一20 倍,只要措施合理,也可获得较小的表面粗糙度值。
因此,高速车削螺纹在生产实践中被广泛采用。
1 .车削三角形外螺纹( l )低速车削三角形螺纹低速车削三角螺纹的进刀方法有直进法、左右车削法和斜进法(图8 一17 )三种。
①直进法车削时只用中滑板横向进给,在几次行程中把螺纹车成形(图8 一17a )。
直进法车削螺纹容易保证牙形的正确性,但这种方法车削时,车刀刀尖和两侧切削刃同时进行切削,切削力较大,容易产生扎刀现象,因此只适用于车削较小螺距的螺纹。
图8-17 车螺纹时的进刀方法②左右切削法车削螺纹时,除直进外,同时用小滑板把车刀向左、右微量进给(俗称赶刀),几次行程后把螺纹车削成形(图8 一17b )。
采用左右切削法车削螺纹时,车刀只有一个侧面进行切削,不仅排屑顺利,而且还不易扎刀。
但精车时,车刀左右进给量一定要小,否则易造成牙底过宽或牙底不平。
③斜进法粗车时为操作方便,除直进外,小滑板只向一个方向作微量进给,几次行程后把螺纹车成形(图8 一17c )。
图8-18 弹性刀杆螺纹车刀采用斜进法车削螺纹,操作方便、排屑顺利,不易扎刀,但只适应于粗车,精车时还必须用左右切削法来保证螺纹精度。
( 2 )高速车削三角螺纹高速车削三角形螺纹,只能采用直进法,而不能采用左右切削法,否则会拉毛牙形侧面,影响螺纹精度。
高速车削时,车刀两侧刃同时参加切削,切削力较大,为防止振动及扎刀现象,可使用图8 一18 所示的弹性刀杆。
高速车削的进给次数可参阅下表提供的数据。
高速车削三角螺纹时,由于车刀对工件的挤压力很大,容易使工件胀大,所以车削螺纹前工件的外径应比螺纹的大径尺寸小,当车削螺距为 1 . 5 mm 一3 . 5mm的工件时,工件外径尺寸可车小0 . 15 mm 一0 . 25 mm 。
2 .车削三角形内螺纹车削三角形内螺纹的方法和车削外螺纹的方法基本相同,只是车削内螺纹要比车削外螺纹困难得多。
( l )车螺纹前孔径的计算车削塑性材料的金属时:D孔=d 一P (8-7) 车削脆性材料的金属时:D孔=d 一1.05P(8-8)例需要在铸铁工件上车削M24 × 1 . 5 的内螺纹,试计算车削螺纹之前孔径应车成多大?解:铸铁为脆性材料,根据公式(8 一8 )得:( 2 )车削内螺纹时的注意事项①内螺纹车刀两侧刃的对称中心线应与刀杆中心线垂直,否则车削时刀杆会碰伤工件。
②车削通孔螺纹时,应先把内孔、端面和倒角车好再车螺纹,其进刀方法和车削外螺纹完全相同。
③车削盲孔螺纹时一定要小心,退刀和工件反转动作一定要迅速,否则车刀刀头将会和孔底相撞。
为控制螺纹长度,避免车刀和孔底相碰,最好在刀杆上作出标记(缠几圈线),或根据床鞍纵向移动刻度盘控制行程长度。
3 .套螺纹和攻螺纹在车床上车削数量较多、螺距较小、精度要求不太高的三角螺纹时,为提高效率,减小劳动强度,可采用套螺纹和攻螺纹的方法。